Физика и химия стекла, 2021, T. 47, № 3, стр. 257-272
Физико-химические процессы взаимодействия в системе углерод (алмаз)–кремний
В. Я. Шевченко 1, С. Н. Перевислов 1, *, В. Л. Уголков 1
1 ФГБУН Институт химии силикатов им. И.В. Гребенщикова РАН
199034 Санкт-Петербург, наб. Макарова, 2, Россия
* E-mail: perevislov@mail.ru
Поступила в редакцию 09.10.2020
После доработки 01.02.2021
Принята к публикации 05.02.2021
Аннотация
Экспериментально исследованы химические процессы, происходящие при взаимодействии углерода (алмаза) с кремнием. Проведен термический анализ взаимодействия алмаза с кремнием, что позволило определить механизм синтеза карбида кремния и последующее реакционное спекание алмазных частиц на основе реакционно-диффузионного процесса Тьюринга и формирование микроструктуры, состоящей из трижды периодических поверхностей минимальной энергии.
ВВЕДЕНИЕ
Определяющую роль в формировании свойств веществ играет их химическая природа. Однако, используя композиционные сочетания различных веществ, можно, в ряде случаев, получить оптимальные свойства соответствующих материалов. Большой практический интерес среди композитов представляют материалы на основе алмаза и гетерогенетического ему карбида кремния [1, 2].
Для получения композитов алмаз–карбид кремния используют горячее изостатическое прессование, искровое плазменное спекание и спекание в камерах высокого давления. Наиболее эффективным и практичным методом является реакционное спекание (пропитка расплавом Si пористых заготовок), приводящее к формированию плотной структуры, состоящей из алмазных частиц и карбида кремния [3–8].
Однако, несмотря на большой интерес к композитам алмаз-карбид кремния и подробное изучение их структуры, фазового состава и механических свойств, до сих пор мало изучены физико-химические особенности взаимодействия алмаза с кремнием и формирование гетеродисперсной микроструктуры.
Для создания и исследования материалов системы алмаз–карбид кремния необходимо охарактеризовать следующие основные положения:
1) Микроструктура должна быть трижды периодической структурой с минимальной энергией, что обеспечивает возможность диссипации высоких энергий поражения;
2) Shoji H. и др. [9] показали, что в результате реакции Тьюринга в материале может быть реализована трехмерная периодичность структуры.
3) В какой системе можно создать условия реакции Тьюринга – гетерогенетической (материалы близкие по кристаллической структуре, но разные по свойствам), например, алмаз и карбид кремния являются гетерогенетической парой, т.е. муассанит и алмаз сосуществуют в природных образованиях;
4) Исследовать возможность создания в таких системах условий прохождения реакции Тьюринга.
5) Ранее, в чисто неорганических системах, таких наблюдений не было.
НЕКОТОРЫЕ ФИЗИКО-ХИМИЧЕСКИЕ СВОЙСТВА
Необходимо подробно изучить химизм реакции углерод (алмаз)–кремний и образование в результате этой реакции карбида кремния на поверхности алмазных частиц, что включает рассмотрение кристаллического состояния SiC, в зависимости от условий взаимодействия углерода, графита и алмаза с кремнием.
Карбид кремния имеет 2 модификации: гексагональную (α-SiC) и кубическую (β‑SiC). Именно β-SiC образуется при взаимодействии пироуглерода или графитового слоя алмаза с жидким или газообразным кремнием в процессе реакционного спекания. Количество Si в β-SiC может колебаться от 50.0 до 52.5 ат. %.
Ковалентный характер и высокая прочность связи С–C в алмазе и Si–C в карбиде кремния определяют их энергетическую и механическую прочности. В работе [10] исходя из энергии атомизации (Ω) кристаллов (функция, которая характеризует энергетическую прочность кристалла с ковалентной решеткой) рассчитаны значения удельной полной (ε) и удельной свободной (σ) поверхностной энергии, с которыми хорошо коррелируют величины твердости (H) и ширины запрещенной зоны (ΔE) кристаллов с ковалентной связью (табл. 1). В табл. 2 приведены параметры кристаллической решетки алмаза, графита, углерода, карбида кремния и кремния.
Таблица 1.
Энергетические характеристики и свойства алмаза, карбида кремния и кремния
Вещество | hkl грани | Ω, ккал/моль | ε, эрг/см2 | σ, эрг/см2 | H, ГПа | ΔE, эВ |
---|---|---|---|---|---|---|
Алмаз | 100 | 340 | 9304 | 9100 | 100.0 | 5.3 |
β-SiC | 100 | 300 | 5450 | 5340 | 33.4 | 2.2 |
Si | 100 | 204 | 2124 | 2085 | 11.0 | 1.1 |
Таблица 2.
Параметры кристаллической решетки алмаза, графита, углерода, карбида кремния и кремния
Вещество | Сфалерит а, Å |
Вюрцит | ||
---|---|---|---|---|
а, Å | с, Å | с/а | ||
Алмаз | 3.5669 | – | – | – |
Графит* | – | 2.47 | 6.79 | 2.749 |
Углерод** | – | 2.52 | 4.12 | 1.633 |
β-SiC | 4.3596 | – | – | – |
α-SiC (2Н) | – | 3.076 | 5.048 | 1.635 |
Si | 5.4306 | – | – | – |
Малые энергетические различия между политипами позволили авторам работы [11] оценить вероятность существования того или иного политипа исходя из термодинамических зависимостей. Изменение термодинамического потенциала при фазовом превращении описывается уравнением:
Поскольку политипные переходы не сопровождаются заметными объемными изменениями, член PΔV близок к нулю. Величина ΔH также близка к нулю, так как все политипы SiC имеет одинаковую потенциальную энергию, благодаря одинаковому окружению в первой и второй координационных сферах. Таким образом изменение свободной энергии (ΔF) при политипном переходе определяется отличием в энтропии исходного и конечного состояния. Поэтому при политипном переходе:
Отсюда следует, что политип с более высоким уровнем энтропии будет более термодинамически устойчивым.
Для образования карбида кремния при температуре 1800 К изменение энтропии синтеза α-SiC (2Н) – ΔS = 76.79 Дж/(моль К), а β-SiC – ΔS = 76.84 Дж/(моль К), поэтому при реакционном спекании при температуре ~1500°С термодинамически более вероятно образование кубического карбида кремния. При температуре 1800°С изменение энтропии образования α-SiC больше, чем ΔS образования β-SiC, что определяет фазовый β → α-SiC переход при этой температуре.
В начальный период взаимодействия алмазных частиц с кремнием, из-за избытка углеродсодержащего компонента (пироуглерода и графита на алмазных частицах), происходит синтез β-SiC не стехиометрического состава (с повышенным содержанием углерода), что подтверждается увеличением параметра решетки до 4.360–4.361 Å [12].
Растворимость углерода в расплавленном кремнии во многом определяет структурообразование карбида кремния.
Растворимость углерода в твердом кремнии очень мала и даже при температуре 1410°С не превышает 0.005 ат. %. В работе [2] показано, что сплавы кремния с углеродом (до 0.7% C) являются однофазными. Причем параметр решетки в насыщенном углеродом твердом растворе на основе кремния заметно уменьшается (а = 5.4174 Å), по сравнению с чистым кремнием (а = 5.4306 Å) [2]. Повышение содержания углерода в твердом растворе также коррелирует со значениями микротвердости.
Концентрацию углерода в твердом кремнии (РС) рассчитывали на основе определения параметров кристаллической решетки твердого раствора углерода в кремнии, исходя из факта, что углерод (алмаз) и кремний изоморфны (решетка типа сфалерита), имеют ковалентный тип химической связи и их параметры линейно связаны с концентрацией углерода. Исходя из этой зависимости растворимость углерода в кремнии можно определить по формуле:
(3)
${{Р}_{{\text{С}}}} = \left( {\Delta {{a}_{{\text{p}}}}/\left( {2{{a}_{{{\text{Si}}}}} - {{a}_{{{\text{SiC}}}}}} \right)} \right) \times 100\% ,$В образцах кремния, насыщенных углеродом, при температуре 1250–1350°C уменьшение параметра решетки составило Δap = –0.0020 Å, Pc = 0.094 ат. %. Твердый раствор углерода в кремнии в данном случае значительно пересыщен Δap = 0.0004 ± ± 0.0001 Å, что отвечает концентрации углерода Pc = 0.019 ат. %.
В результате изотермической выдержки при 1350°C в течение 18 ч Δap становится равным –0.0003 Å и при дальнейшем увеличении времени отжига до 36 ч не изменяется.
Таким образом, концентрацию Pc = 0.019 ат. %, рассчитанную по Δap = –0.0004 Å, следует считать предельной растворимой концентрацией углерода в кремнии при 1250–1350°C, сохраняющейся при медленном охлаждении до комнатной температуры.
Также обнаружено, что растворимость углерода в жидком кремнии зависит не только от температуры и времени насыщения, но и от активности исходного углерода, связанной со степенью его кристалличности. При растворении в расплавленном кремнии микронного или субмикронного, хорошо кристаллизованного природного графита (степень графитации равна 0.9) после выдержки при температуре 1700°С в течение 1 ч и охлаждения до комнатной температуры Pc = 0.052 ат. %, а при растворении углерода (степень гравитации равна 0) в тех же условиях Pc = 0.27 ат. %.
При увеличении температуры и времени взаимодействия углерода и жидкого кремния различие в растворимостях углерода и графита уменьшается (табл. 3).
Таблица 3.
Влияние вида углеродистого материала и температуры насыщения на растворимость углерода в кремнии
Добавка к кремнию | Температура насыщения, °С | Время насыщения, ч | Δap, Å | Pc, ат. % |
---|---|---|---|---|
Углерод | 1700 | 1 | –0.0058 | 0.27 |
Графит | –0.0011 | 0.05 | ||
Углерод | 2000 | 0 | –0.0065 | 0.25 |
Графит | –0.0066 | 0.20 | ||
Углерод | 2200 | 1 | –0.0096 | 0.45 |
Графит | –0.0093 | 0.43 |
ГРАФИТИЗАЦИЯ АЛМАЗНЫХ ЧАСТИЦ
Превращение алмаза в графит на воздухе начинается уже при температуре 800°С [13, 14]. При температуре ниже 800°С скорость горения превышает скорость графитизации. В результате на поверхности алмаза не образуется графитовый слой. При температурах выше 800°С скорость графитизации превышает скорость горения, и в этом случае тонкий графитовый слой образуется в результате поверхностной химической реакции с участием молекул монооксида углерода и диоксида углерода [15]. Толщина графитового слоя увеличивается с увеличением температуры и давления остаточных газов [16, 17].
Переход алмаза в графит в вакууме осуществляется при значительно более высокой температуре и объясняется взаимодействием поверхностных атомов алмаза с молекулами кислорода в вакуумной печи [18]. Термодинамический анализ показывает, что прямой переход алмаза в графит должен происходить при температуре выше 4000°С [19]. Графитизация в вакууме идеального кристалла алмаза никогда не наблюдается. Графитизация характерна для алмазов, в которых присутствуют микроскопические включения, особенно если они металлические или графитовые.
Авторы работы [20] считают полный переход алмаза в графит довольно маловероятным. Они подчеркивают важную роль поверхностных химических реакций и предлагают двухстадийный механизм, когда атомы углерода сначала отрываются от своих участков на поверхности алмаза, образуя неупорядоченные агрегаты, которые затем преобразуются в микрокристаллы графита.
В работе [21] описано образование тригональных пирамид на естественных {111} гранях алмаза при отжиге на температуру 1800°С. Это оказался поликристаллический графит с микрокристаллами размером 10–15 нм, преимущественно ориентированными вдоль {111} алмазной грани. В работе [22] исследована скорость графитизации различных граней алмаза, обнаружено, что грань {110} графитизируется быстрее, чем {111}, хотя на поверхности плоскости {100} графитизация почти не происходила. При температурах выше 1600 °С характер графитизации меняется – он становится неоднородным, анизотропным и проникает внутрь кристалла. Образуются области интенсивной графитизации (фигуры графитизации) симметричной формы размером до 100 мкм.
В алмазе существуют некоторые “слабые” кристаллографические плоскости или направления, которые преимущественно вовлечены в процесс графитизации. На полированной поверхности алмаза фигуры графитизации имеют форму, определяемую симметрией решетки алмаза. Размер и число таких фигур увеличивается с увеличением продолжительности и температуры спекания материала. По мере развития процесса поверхность алмаза полностью покрывается черным неровным слоем графита.
Исследование неоднородной и анизотропной графитизации алмаза в интервале температур 1600–1750°C выявило различную термическую стабильность граней кристаллов, в последовательности {211}, {110}, {111}, {100}, грани {211} оказались самыми слабыми [23]. Поверхностная плотность атомов на кристаллографической грани алмаза {211} очень близка к грани графита {0001}. Напротив, грани {100} оказались чрезвычайно устойчивыми в отношении графитизации, при температурах спекания материала выше 1700°С, причем при этой температуре все остальные грани уже были покрыты сплошным слоем графита.
Фигуры графитизации формируются преимущественно на неровностях поверхности алмаза. На полированных образцах они могут образовываться в местах царапин после механической обработки.
Изображения фигур графитизации, зарегистрированные на последовательных этапах спекания свидетельствуют о том, что они растут из одной точки. Размер фигур графитизации в плоскости образца в 10 раз превышает их толщину, то есть графитизация развивается преимущественно вдоль поверхности. Для диапазона температур 1200–1600°С толщина графитового слоя определяется давлением остаточных газов в вакуумной печи: чем лучше вакуум, тем тоньше графитовый слой на поверхности алмаза. И чем тоньше слой, тем выше температура, при которой начинают формироваться фигуры графитизации.
Фактором, ограничивающим распространение графитизации внутрь кристалла, является давление, даже когда графитизация протекает по плоскостям вблизи поверхности алмаза. Поскольку плотность атомов алмаза отличается от плотности образующегося графитового слоя, преобразование сопровождается механическими деформациями сжатия или растяжения вдоль плоскости, которая стабилизирует алмазную фазу. Поскольку удельный объем графита в 1.55 раза больше, чем у алмаза, графитовые слои, которые образуются под поверхностью в процессе превращения алмаз–графит, испытывают давление со стороны поверхностного слоя алмаза, который они покрывают. Чем больше углы, под которыми алмазные плоскости {211}, превращающиеся в графит, уходят вглубь кристалла, тем большее давление со стороны покрывающего алмаза они испытывают, это давление препятствует графитизации.
Теоретическая модель графитизации, предложена в работе [24], где рассмотрены результаты первичных принципов молекулярно-динамического моделирования поверхностно-индуцированного перехода алмаз–графит, который обеспечивает микроскопическую модель для ранних стадий процесса графитизации. Проникновение графитовой фазы в алмаз и вертикальная графитизация приводит к образованию когерентной границы раздела алмаз–графит.
Можно предположить, что неоднородная и анизотропная графитизация поверхности алмаза протекает в несколько этапов:
1) Формирование графитизированного слоя на поверхности алмаза при термообработке при температуре выше 800°С за счет взаимодействия атомов алмаза с молекулами кислорода и примесями;
2) Образование ядер графита размером 5–10 нм на поверхности алмаза;
3) Миграция ядер графита на поверхности алмаза и формирование групп ядер с повышенной плотностью, размером 10–100 нм.
4) Развитие фигур графитизации из агрегированных ядер вдоль алмазных плоскостей {211}, поскольку они имеет ту же поверхностную плотность, что и плоскости графита {0001}.
ПРОЦЕСС РЕАКЦИОННОГО СПЕКАНИЯ МАТЕРИАЛОВ НА ОСНОВЕ АЛМАЗНЫХ ЧАСТИЦ
Процесс реакционного спекания практически не затрагивает всего объема алмазной частицы. Формирование контактов, заполнение пор и образование непрерывного поликристаллического каркаса (“скелета”) определяется, в данном случае, химическими реакциями на поверхности алмаза и сопровождается образованием SiC. Синтез карбида кремния из элементарных кремния и углерода возможен при температурах значительно более низких чем температура получения жидкофазно-спеченых и горячепрессованных материалов. Способ транспорта реагирующих компонентов при образовании SiC определяет условия процесса спекания и конечную структуру материала системы алмаз–карбид кремния.
Взаимодействие твердого углерода с кремниевым расплавом, диффузионный перенос растворенного углерода через жидкий кремний, взаимодействие углерода с газообразным кремнием и кристаллизация SiC из расплава – это основные механизмы, которые влияют на формирование структуры и свойства материала [2].
Рассмотрим эти процессы подробнее. Исходная пористая заготовка представляет собой смесь алмазных частиц (D) и пироуглерода (C) от пиролиза фенолформальдегидной смолы. Такое пористое трехфазное тело (D + С + поры) пропитывается расплавом кремния. Представим каналы заготовки в виде цилиндрического капилляра. Без учета химического взаимодействия между расплавом и твердой фазой, временной закон продвижения мениска жидкости в капилляре при вязком течении имеет вид [2]:
(4)
${{l}^{2}} = \frac{{{{{{\sigma }}}_{{{\text{ж}},{\text{г}}}}}{\text{cos}}\theta }}{{2{{\eta }}}}R\tau = \frac{{{{{{\sigma }}}_{{{\text{ж}},{\text{г}}}}}{\text{cos}}\theta }}{{2{{\rho \nu }}}}R\tau \,\,{\text{или}}\,\,l = k{{\tau }^{{{1 \mathord{\left/ {\vphantom {1 2}} \right. \kern-0em} 2}}}},$(5)
${\text{где}}\,\,k = \frac{{{{{{\sigma }}}_{{{\text{ж}},{\text{г}}}}}\,{\text{cos}}\theta }}{{2{{\eta }}}}R = \frac{{{{{{\sigma }}}_{{{\text{ж}},{\text{г}}}}}\,{\text{cos}}\theta }}{{2\rho \nu }}R,$Это уравнение (4) справедливо для описания кинетики пропитки пористых материалов расплавами, не взаимодействующими с твердой фазой. В табл. 4 представлены данные, характеризующие влияние концентрации углерода в кремниевом расплаве на смачиваемость карбида кремния и алмаза.
Таблица 4.
Характеристики растворимости углерода и смачиваемости алмазных частиц кремнием
Характеристики | Свойства | ||
---|---|---|---|
Температура, °С | 1420 | 1500 | 1600 |
Краевой угол θ смачивания SiC, град.: | |||
чистый Si | 37 | 32 | 27 |
Si, насыщенный углеродом | 37 | 34 | 31 |
Краевой угол θ смачивания алмаза, град.: | |||
чистый Si | 25 | 22 | 17 |
Si, насыщенный углеродом | 25 | 23 | 20 |
Растворимость углерода в Si, ат. % | 5.5 × 10–3 | 1.3 × 10–2 | 4.0 × 10–2 |
Плотность кремния ρ, г/см3 | 2.52 | 2.49 | 2.45 |
Кинетическая вязкость ν, см2/с | 0.00348 | 0.00265 | 0.00233 |
Можно вычислить глубину пропитки l пористого тела из алмазных и карбидокремниевых частиц. Поверхностное натяжение кремния в интервале температур 1420–1600°С практически не меняется и равно 860 дин/см [2]. Зависимость глубины пропитки l пористых заготовок на основе карбида кремния и алмазных частиц от времени τ представлена на рис. 1 в интервале температур 1420–1600°С, при условии радиуса пор R = 10 мкм.
Рис. 1.
Зависимость глубины пропитки пористых заготовок на основе карбида кремния и алмазных частиц от времени пропитки.
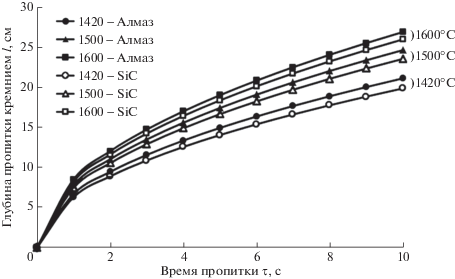
Из анализа графиков видно, что уже при температуре 1420°С заметна хорошая пропитка пористых заготовок на основе карбида кремния и алмазных частиц. Заготовки из алмазных частиц пропитываются жидким кремнием лучше, поскольку краевой угол θ смачивания алмазных частиц кремнием ниже, чем при смачивании SiC, вероятнее всего это связано с частичной графитизацией алмаза (краевой угол смачивания графита кремнием равен 0°).
С повышением температуры область между линиями пропитки карбида кремния и алмаза сужается, так как краевой угол смачивания карбида кремния и алмаза кремнием уменьшается. Скорость пропитки также зависит и от эффективного радиуса пор (в нашем расчете R = 10 мкм). При контакте пористых заготовок с жидким кремнием сразу после его плавления пропитка проходит на достаточно большую глубину за сравнительно короткое время. Поэтому даже для крупногабаритных изделий 25–30 см время пропитки составляет около 10 с.
Рассматриваемая нами система включает в себя химические взаимодействия между углеродом и кремниевым расплавом. Поэтому для анализа явлений, происходящих при пропитке двухкомпонентной пористой заготовки следует рассматривать в отдельности две частные системы С–Siж и D–Siж.
Пропитка пористого углерода (графита) химически активными расплавами рассмотрена в работах [25, 26]. В работах [27, 28] экспериментально изучена кинетика пропитки пористых графитов жидким кремнием. Установлено, что на начальной стадии процесса (0–50 с) глубина пропитки l подчиняется уравнению l = k'τ1/2, что характерно для вязкого течения жидкости.
В работе [25] показано, что в тех случаях, когда наблюдается полное смачивание и движущая сила процесса пропитки остается практически постоянной при изменении температуры, энергия активации пропитки становится соизмеримой с энергией активации вязкого течения пропитывающей жидкости.
Вязкий характер течения кремниевого расплава при пропитке графита подтверждается также и значением энергии активации, определенным в интервале температур 1410–1550°С. Энергия активации пропитки графита кремнием колеблется на начальной стадии процесса в пределах 11.5–14.2 ккал/моль для разных сортов графита, что хорошо совпадает с энергией активации вязкого течения кремния, равной для этих температур 10.3–10.6 ккал/моль [27, 28].
С увеличением времени (50–180 с) глубина пропитки становится пропорциональной τ1/4, что связанно с поверхностной диффузией кремния. При этом энергия активации процесса возрастает до 45–53 ккал/моль.
Полученные результаты указывают, что на начальной стадии процесс пропитки углерода (графита) кремнием определяется вязким течением и не осложнен образованием карбида кремния, который начинает кристаллизоваться на межфазной границе после насыщения расплава углеродом.
Таким образом при реакционном спекании материалов на основе алмазных частиц предполагаются следующие элементарные процессы: смачивание и пропитка твердого пористого тела расплавленным кремнием; растворение пироуглерода и графита на поверхности алмазных частиц в расплаве кремния. Синтез карбида кремния происходит в результате гетерогенного взаимодействия (Siж + Cт = SiCт) и переноса углерода через кремниевый расплав с последующей кристаллизацией SiC на поверхности алмазных частиц в результате реакционно-диффузионного взаимодействия, т.е. реакция Тьюринга.
СПЕКАНИЕ ЧАСТИЦ АЛМАЗА И ТВЕРДОГО УГЛЕРОДА В ПРИСУТСТВИИ РАСПЛАВЛЕННОГО Si
Для рассмотрения механизма реакционного спекания материалов на основе алмазных частиц представим модель, состоящую из ансамбля сферических частиц. Например, четыре частицы алмаза, частицы углерода между ними и пространство, заполненное расплавленным кремнием (рис. 2а). Эта модель реализуется на начальном этапе процесса в результате пропитки пористых заготовок, состоящих из частиц алмаза, углерода и расплавленного Si (рис. 2а).
Рис. 2.
Модельная схема распределения фазовых составляющих на I стадии (а), II стадии (б) и III стадии (в) реакционного спекания. На схеме представлены следующие фазы: алмаз (D); графит на поверхности частиц алмаза (Gr); пироуглерод (C); жидкий кремний (Siж); образующийся в результате реакционно-диффузионного взаимодействия карбид кремния (SiC) и SiC на поверхности алмазных частиц (забор Тьюринга).
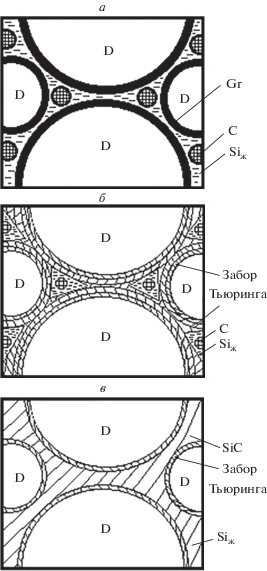
На следующем этапе происходит растворение углерода (пироуглерода), графита на поверхности алмаза, насыщение ими кремниевого расплава и кристаллизация в виде карбида кремния в местах наиболее выгодных в термодинамическом отношении, т.е. на поверхностях алмазных частиц (рис. 2б). Причем этот процесс не приводит к изменению центровых расстояний контактирующих сфер алмазных частиц. Растворяющиеся атомы углерода диффундируют на границах расплав–углерод и расплав–алмаз и непосредственно кристаллизуется из расплава виде зерен карбида кремния. Поэтому можно ожидать что концентрация углерода в кремнии не будет достигать равновесного значения вплоть до момента полного растворения частиц углерода (графита).
Образование карбида кремния на частицах алмаза, также как и на частицах SiC при реакционном спекании карбида кремния, происходит в соответствии с реакционно-диффузионным механизмом Тьюринга послойно (рис. 2), образуя таким образом трижды периодические поверхности (заборы Тьюринга) в объеме алмазного каркаса.
Таким образом, пока в материале существует в контакте с твердым углеродом жидкая кремниевая фаза, будет происходить интенсивный перенос углерода через расплав и осаждения SiC виде зерен на поверхности алмазных частиц (рис. 2в).
Коэффициент самодиффузии кремния и коэффициент диффузии углерода в жидком кремнии имеют следующий вид:
(6)
$~{{D}_{C}} \approx {{D}_{{{\text{Si}}}}} = {\text{ }}0.755 \times {{10}^{{ - 3}}}{\text{exp}}\left( { - \frac{{9150}}{{RT}}} \right).$Вычисления по этой формуле дают следующие значения коэффициента диффузии:
Коэффициент диффузии углерода через жидкий кремний на 6–7 порядков выше коэффициента диффузии углерода через слой карбида кремния и на 9–10 порядков выше коэффициента диффузии углерода через слой алмаза.
На основании данных коэффициентов диффузии в нашей работе рассчитано время полного превращения кремния при взаимодействии с углеродом (графитом) в карбид кремния при реакционном спекании, которое равно при 1700°С – 2.58 × 104 с (~7 ч), а при 2100°С ~18 мин.
РЕАКЦИОННО-ДИФФУЗИОННЫЙ МЕХАНИЗМ ТЬЮРИНГА
Фазовая диаграмма состояния Si–C (рис. 3) показывает, что в области, богатой углеродом (более 50 ат. % С) существуют только 2 фазы SiC и С, а Si полностью переходит в карбид кремния [29]. На начальной стадии пропитки жидкий Si проникает в каналы пор заготовки и взаимодействует с углеродом, количество которого превосходит Si, с образованием карбида кремния. Дальнейшая реакция взаимодействия кремния с углеродом осуществляется путем диффузии Si через слой SiC. Следовательно, процесс реакции включает диффузию атомов кремния через слой карбида кремния и реакцию между Si и углеродом. Кинетика реакции очень медленная, из-за низких коэффициентов диффузии C и Si в SiC [30], что приводит к образованию на поверхности алмазных частиц слоев SiC.
Процесс образования SiC можно объяснить с точки зрения анализа реакционно-диффузионного механизма А. Тьюринга (A. Turing) [31]. Источником углерода в материалах на основе только алмазных частиц является графит, который при высокой температуре может частично, на поверхности, графитизироваться (происходит фазовый переход алмаз–графит). При анализе кинетики роста слоя SiC в результате реакционно-диффузионного взаимодействия между алмазом и кремнием [32], подтвержденным экспериментально, показано образование слоя SiC на поверхности алмазных частиц.
Соответственно, исходя из реакционно-диффузионного механизма Тьюринга на поверхности алмазных частиц формируются наноразмерные зерна SiC при диффузии газообразного Si в пористую заготовку, а при пропитке расплавом жидкого кремния частиц пироуглерода и графита на поверхности алмаза формируются микронные зерна SiC, образуя в обоих случаях “забор” Тьюринга (рис. 4).
Рис. 4.
Формирование микронных зерен SiC (“забор” Тьюринга), образующихся при взаимодействии графитового слоя на поверхности алмазной частицы с жидким Si (а, б).
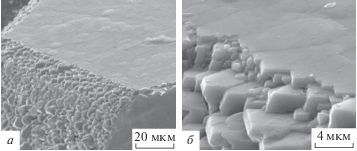
Давление насыщенного газообразного Si составляет 1 Па при температуре 1500°С [33], следовательно, Si с большой скоростью проникает в пористую заготовку и контактируя с углеродом образует карбид кремния. Как показано ранее, насыщение жидким кремнием происходит за счет капиллярной пропитки пористой заготовки.
Реакционно-диффузионное взаимодействие Si с углеродом сопровождается экзотермическим эффектом (повышением температуры системы до 2400°С), с энтальпией H0 = −117.77 кДж/моль, что устраняет градиенты температуры в заготовках [34]. В результате увеличивается скорость растворения пироуглерода и графита на частицах алмаза в жидком Si. Вязкость Si и угол смачивания им углерода снижаются, что приводит к более быстрой и легкой пропитке жидким Si пористой заготовки. Скорость диффузии Si увеличивается в несколько раз, а поры заготовки алмазного материала заполняются SiC, в соответствии с реакционно-диффузионным механизмом Тьюринга.
ТЕРМИЧЕСКИЙ АНАЛИЗ СИСТЕМЫ АЛМАЗ–КРЕМНИЙ
Для экспериментального изучения процессов взаимодействия алмаза с кремнием проведен комплексный термический анализ. Исследование ТГ и ДСК выполнено на установке комплексного термического анализа STA 429 СD фирмы NETZSCH (Германия).
Образец 1, состоящий из алмазного порошка фракции 20/28 мм, в виде диска размером Ø5 мм, h = 1 мм и пористостью 45 об. %, помещали в открытый алундовый тигель. На верхней поверхности диска укладывали частицу монокристаллического кремния (рис. 5а).
Образец подвергали комплексному термическому анализу при нагревании со скоростью 20°С/мин в динамической атмосфере Ar (поток Ar – 50 см3/мин) в интервале температур 40–1500°С и охлаждении до 1200°С. Напуск Ar производили после откачки воздуха печи до 1 × 10–4 мБар. Продукты разложения анализировали с помощью соединенного с печью квадрупольного масс-спектрометра QMS 403 С фирмы NETZSCH (Германия).
Целью исследований являлось изучение особенностей процессов, происходящих при термообработке композитов алмаз–кремний и экспериментальное подтверждение взаимодействия компонентов с образованием карбида кремния.
На рис. 6 представлены кривые ТГ, ДСК образца 1, термообработанного в интервале температур 40–1500°С со скоростью 20°С/мин в потоке Ar.
Ход кривой ТГ показывает, что масса образца уменьшается на всем протяжении нагрева от 100 до 1500°С. Потеря массы образца при температуре 1500°С составляет 0.79% (рис. 6), что говорит об отсутствии взаимодействия с образованием газообразных продуктов. При охлаждении образца в интервале температур 1500–1200°С изменений массы практически не происходит.
Кривая ДСК при нагревании (рис. 6) до температуры 1390.8°С (теплота плавления –0.3469 мВт/мг) является гладкой. При температуре 1390.8°С начинается процесс плавления кремния, сопровождаемый большим эндотермическим эффектом (удельная теплота химической реакции 42.63 Дж/г). Максимум пика наблюдается при температуре 1414.8°С (теплота плавления 0.6937 мВт/мг), чему соответствует полное расплавление кремния и проникание его в пористый алмазный образец. При этой температуре начинается растворение графита (углерода) на поверхности алмазных частиц и образование карбида кремния, сопровождаемое большим экзотермическим эффектом (удельная теплота химической реакции –106.9 Дж/г). Кривая DSC резко устремляется вниз и достигает минимума при температуре 1424.1°С (теплота кристаллизации –2.196 мВт/мг). Экзотермический эффект завершается при температуре 1444.7°С (теплота кристаллизации –0.4988 мВт/мг).
Следует отметить, что время между максимальной температурой плавления кремния (1414.8°С) и максимальной температурой кристаллизации карбида кремния (1424.1°С) составляет около 28 с. Это подтверждает корректность расчета времени пропитки пористой алмазной заготовки (рис. 1).
На рис. 7 представлены кривые DSC образца 1 (сплошная линия) и образца 2 (пунктирная линия), отожженных в интервале температур 1300–1500°С со скоростью 20°С/мин в потоке Ar – 50 мл/мин. Образец 2 состоял из алмазного порошка фракции 20/28 мм, в виде дисков размером Ø5 мм, h = 1 мм, который предварительно обрабатывали при температуре 1300°С в среде Ar. После чего на верхнюю поверхность диска укладывали частицу монокристаллического кремния, аналогично образцу 1 (рис. 5а).
Рис. 7.
Кривые DSC, полученные при термообработке образца 1 (сплошная линия) и образца 2 (пунктирная линия) в интервале температур 1300–1500°С.
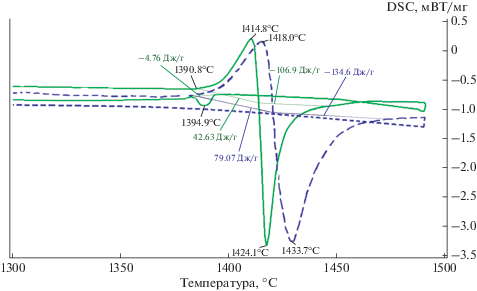
Поскольку образцы 1 и 2 практически не отличались по массе, природе и фракционному составу алмаза, кроме предварительной термообработки образца 2 при 1300°С, интересно сравнить их реакционную способность и поведение при термообработке.
Кривая ДСК образца 1 (рис. 7) повторяет результаты, приведенные на рис. 6. Процесс образования жидкого кремния и карбида кремния для образца 1 начинается немного раньше (1414.8 и 1424.1°С), чем для образца 2 (1418.0 и 1433.7°С), различие в температурах начала процесса образования карбида кремния составило 9.6°С. Выделение тепла для образца 1 прекратилось при 1444.7°С а для образца 2 при температуре 1472.2°С. Таким образом, предварительная термообработка алмазного порошка (образец 2) приводит к небольшому затормаживанию процесса образования SiC.
Если сравнить удельные теплоты химических реакций плавления кремния и кристаллизации карбида кремния: 42.63 и –106.9 Дж/г для образца 1 и 79.07 и –134.6 Дж/г для образца 2, у последнего, при кристаллизации SiC, выделяется большая энергия, что связано с образованием большего по объему количества карбида кремния.
При охлаждении образца 1 наблюдался экзотермический эффект (удельная теплота химической реакции –4.76 Дж/г) кристаллизации жидкого кремния, который не прореагировал с графитом, начинающийся при температуре 1394.9°С (теплота кристаллизации –0.4792 мВт/мг). Температура начала кристаллизации кремния (1394.9°С) практически совпадает с началом его плавления (1390.8°С).
При охлаждении образца 2 экзотермического пика не наблюдался, что также свидетельствует об образовании бóльшего слоя графита на алмазных частицах образца 2 (заранее термообработанного при 1300°С), которого, вероятнее всего, достаточно для полного прохождения реакции между графитом и кремнием с образованием карбида кремния. Поэтому на кривой ДСК образца 2 при охлаждении экзотермического эффекта не наблюдается (рис. 7).
На рис. 5 представлены микрофотографии образца (таблетки с кремнием) до термообработки при 1490°С (рис. 5а) и после термообработки (рис. 5б). После термообработки на верхней поверхности образца остается контур кремниевого кристалла. Возможно, в месте впитывания кристалла в пористую заготовку, остается тонкая пленка кремния.
АНАЛИЗ МИКРОСТРУКТУРЫ
На рис. 8 изображена микроструктура композита алмаз–карбид кремния. Темные фазы соответствуют частицам алмаза, светло-серые – β-SiC. Кристаллы алмаза правильной формы, однородно распределены в композите. Пор в материале практически нет, что говорит о прочной межфазной связи между алмазом и карбидом кремния.
ЗАКЛЮЧЕНИЕ
Исследованы физико-химические взаимодействия в системе углерод (алмаз)–кремний. Изучена природа процесса реакционного спекания углерода (алмаза) с кремнием, рассмотрены модели спекания частиц алмаза, углерода и алмаза с углеродом в присутствии расплавленного кремния, проведен термический анализ взаимодействия алмаза с кремнием, что помогло объяснить процесс взаимодействия алмазных частиц с кремнием на основе модели реакционно-диффузионного механизма Тьюринга и получения материала с микроструктурой, состоящей из трижды периодических поверхностей минимальной энергии.
Работа выполнена при финансовой поддержке гранта Российского научного фонда (№ 20-13-00054).
Список литературы
Шевченко В.Я. Стекло и керамика // XXI. Перспективы развития. СПб.: Янус. 2001. 303 с.
Knippenberg W.F. Growth phenomena in silicon carbide // Philips Res. Report. 1963. V. 18. P. 161–274.
Ekstrom T.C., Gordeev S.K. New carbide composites with extraordinary properties // Key Engineering Materials. 1999. P. 75–80.
Park J.S., Sinclair R., Rowcliffe D., Stern M., Davidson H. Orientation relationship in diamond and silicon carbide composites // Diamond and Related Materials. 2007. V. 16. № 3. P. 562–565
Liu Y., Hu C., Feng W., Men J., Cheng L., Zhang L. Microstructure and properties of diamond/SiC composites prepared by tape-casting and chemical vapor infiltration process // J. Eur. Ceram. Soc. 2014. V. 34. № 15. P. 3489–3498.
Matthey B., Kunze S., Hörner M., Blug B., van Geldern M., Michaelis A., Herrmann M. SiC-bonded diamond materials produced by pressureless silicon infiltration // J. Mater. Res. 2017. V. 32. № 17. P. 3362–3371.
Taylor A., Klimša L., Kopeček J., Remeš Z., Vronka M., Čtvrtlík R., Tomáštík J., Mortet B. Synthesis and properties of diamond-silicon carbide composite layers // J. Alloys Compd. 2019. V. 800. P. 327–333.
Salamone S., Aghajanian M., Horner S.E., Zheng J.Q. Reaction bonded SiC/Diamond composites: Properties and impact behavior in high strain rate applications // Advances in Ceramic Armor XI. 2015. V. 600. P. 111–118.
Shoji H., Ohta T. Computer simulations of three-dimensional Turing patterns in the Lengyel-Epstein model // Phys. Rev. E. 2015. V. 91. № 3. P. 032 913.
Мюллер У., Ховив А.М. Структурная неорганическая химия. М., Интеллект, 2010. 351 с.
Belenkov E.A., Agalyamova E.N., Greshnyakov V.A. Classification and structure of silicon carbide phases // Phys. Solid State. 2012. V. 54. № 2. P. 433–440.
Falk A.L., Buckley B.B., Calusine G., Koehl W.F., Dobrovitski V.V. et al. Polytype control of spin qubits in silicon carbide // Nat. Commun. 2013. V. 4. № 1. P. 1–7.
Howes V.R. The graphitization of diamond // Proceedings of the Physical Society. 1962. V. 80. № 3. P. 648.
Harris J.W., Vance E.R. Induced graphitisation around crystalline inclusions in diamond // Contributions to Mineralogy and Petrology. 1972. V. 35. № 3. P. 227–234.
Evans T., Sauter D.H. Etching of diamond surfaces with gases // Philosophical Magazine. 1961. V. 6. № 63. P. 429–440.
Dallek S., Kabacoff L., Norr M. Oxidation kinetics of type 2A natural diamond [100] and [111] surfaces by TG // Thermochimica Acta. 1991. V. 192. P. 321–326.
Sun Q., Alam M. Relative oxidation behavior of chemical vapor deposited and type II a natural diamonds // Journal of the Electrochemical Society. 1992. V. 139. № 3. P. 933–936.
van Enckevort W.J.P., de Theije F.K. Etching of diamond / In: Nazare M.H., Neves A.J. editors // Properties, growth and application of diamond (INSPEC). London: Institution of Electrical Engineers. 2001. P. 115–124.
Bundy F.P., Bassett W.A., Weathers M.S., Hemley R.J., Mao H.U., Goncharov A.F. The pressure-temperature phase and transformation diagram for carbon; updated through 1994 // Carbon. 1996. V. 34. № 2. P. 141–153.
Davies G., Evans T. Graphitization of diamond at zero pressure and at a high pressure // Proceedings of the Royal Society of London. A. Mathematical and Physical Sciences. 1972. V. 328. № 1574. P. 413–427.
Xie H., Yin F., Yu T. Strain rate induced graphitization of cubic diamond film // Applied Physics Letters. 2014. V. 104. № 3. P. 031911.
Бутенко Ю.В., Кузнецов В.Л., Чувилин А.Л., Коломийчук В.Н., Станкус С.В., Хайрулин Р.А., Сегалл Б. Кинетика графитизации дисперсных алмазов при “низких” температурах // Журнал прикладной физики. 2000. Т. 88. № 7. С. 4380–4388.
Khmelnitsky R.A., Gippius A.A. Transformation of diamond to graphite under heat treatment at low pressure // Phase Transitions. 2014. V. 87. № 2. P. 175–192.
De Vita A., Galli G., Canning A., Car R. A microscopic model for surface-induced diamond-to-graphite transitions // Nature. 1996. V. 379. № 6565. P. 523–526.
Canham L.T., Houlton M.R., Leong W.Y., Pickering C., Keen J.M. Atmospheric impregnation of porous silicon at room temperature // J. Appl. Phys. 1991. V. 70. № 1. P. 422–431.
Lee J., Kim J., Hyeon T. Recent progress in the synthesis of porous carbon materials // Adv. Mater. 2006. V. 18. № 16. P. 2073–2094.
Sibieude F., Benezech G. Chemical vapour deposition of silicon carbide: an X-ray diffraction study // J. Mater. Sci. 1988. V. 23. № 5. P. 1632–1636.
Fleisher A., Zolotaryov D., Kovalevsky A., Muller-Kamskii G., Eshed E., Kazakin M., Popov Jr V.V. Reaction bonding of silicon carbides by Binder Jet 3D-Printing, phenolic resin binder impregnation and capillary liquid silicon infiltration // Ceram. Int. 2019. V. 45. № 14. P. 18023–18029.
Ohtaka O., Shimono M., Ohnishi N., Fukui H., Takebe H., Arima H., Yamanaka T., Kikegawa T., Kume Sh. HIP production of a diamond/SiC composite and application to high-pressure anvils // Phys. Earth and Planetary Interiors. 2004. V. 143. P. 587–591.
Zollfrank C., Sieber H. Microstructure evolution and reaction mechanism of biomorphous SiSiC ceramics // J. Am. Ceram. Soc. 2005. V. 88. № 1. P. 51–58.
Turing A. The chemical basis of morphogenesis // Philos. Trans. R. Soc. London, Ser. B. 1952. V. 237. № 641. P. 37–72.
Mlungwane K., Sigalas I., Herrmann M., Rodriguez M. The wetting behaviour and reaction kinetics in diamond–silicon carbide systems // Ceram. Int. 2009. V. 35. № 6. P. 2435–2441.
Haynes W.M. CRC handbook of chemistry and physics. CRC press, 2014. 2666 p.
Shevchenko V.Y., Koval’chuk M.V., Oryshchenko A.S. Synthesis of a new class of materials with a regular (periodic) interconnected microstructure // Glass Phys. Chem. 2019. V. 45. № 6. P. 412–418.
Дополнительные материалы отсутствуют.
Инструменты
Физика и химия стекла