Физика и химия стекла, 2022, T. 48, № 3, стр. 293-306
Особенности окисления коммерческих алмазных порошков
С. П. Богданов 1, *, В. Я. Шевченко 2, В. Л. Уголков 2, Н. А. Христюк 1, С. Н. Перевислов 2, М. М. Сычев 1, 2, А. В. Ножкина 3
1 Санкт-Петербургский государственный технологический институт (технический университет)
190013 Санкт-Петербург, Московский пр., 26, Россия
2 Институт химии силикатов им. И.В. Гребенщикова РАН
199034 Санкт-Петербург, наб. Макарова, 2, Россия
3 Научно-исследовательский институт природных, синтетических алмазов и инструмента
107996 Москва, ул. Гиляровского, 65, Россия
* E-mail: BogdanovSP@mail.ru
Поступила в редакцию 02.09.2021
После доработки 14.01.2022
Принята к публикации 07.02.2022
- EDN: HXABAB
- DOI: 10.31857/S0132665122030027
Аннотация
В работе изучена стойкость к окислению различных марок коммерческих порошков алмаза. Методами оптической и электронной микроскопии, микрорентгеноспектрального и термического анализов изучена кинетика окисления алмаза на воздухе. Исследована взаимосвязь размера алмазных зерен, их морфологии и примесного состава с температурой, тепловыделением и скоростью процесса. Установлено, что основной фактор, влияющий на поведение алмаза при его горении – это тип присутствующих в порошках примесей, а затем размеры зерен и их морфология. Обнаружен сложный многоступенчатый характер процесса окисления.
ВВЕДЕНИЕ
Экстремальные условия эксплуатации современных конструкционных материалов требуют от них выдающихся механических и термических свойств. Сочетание высокой твердости, модуля упругости, теплопроводности ставит алмаз среди известных в технике материалов на первое место. Однако изготовление изделий из алмаза имеет низкую технологичность, обусловленную трудностью обработки алмазных кристаллов, а высокая цена и небольшие размеры дополнительно ограничивают область применения таких изделий.
Для оптимизации этих противоречивых ограничений изучены многочисленные методы получения алмазосодержащих композитов. Необходимость высоких температур и, как следствие, термодинамической метастабильности алмаза, высоких давлений при спекании алмазосодержащих композитов методом горячего прессования, сужает возможности этого процесса [1, 2]. Перспективным приемом, позволяющим консолидировать алмазные зерна в габаритные изделия сложной формы, является метод инфильтрации пористой алмазной заготовки расплавленным кремнием [3]. Любые приемы спекания пористых дисперсных систем сталкиваются с проблемой наличия в них сорбированного воздуха. Сопутствующим процессом при спекании алмазных композиций может быть окисление порошков алмаза.
Впервые наиболее полно окисление алмаза было исследовано при его нагревании в вакуумной камере при парциальном давлении кислорода 533 Па Эвансом и Фалом [4]. Они обнаружили образование аморфного углерода и графита на поверхности алмаза при температуре нагревания выше 500°С. Авторы установили, что кислород является катализатором процесса перехода метастабильного алмаза при данных условиях температуры (T) и давлении (P) в термодинамически стабильный графит с последующим образованием СО и СО2. В работах [5, 6] по исследованию взаимодействия алмазов с металлами показано, что химически активные к углероду металлы также являются катализаторами графитизации алмазов.
Исследование кинетики окисления синтетических алмазов марок АСО и АСМ раз-личного гранулометрического состава от 2–3 до 200–250 мкм в работе [7] показало, что стойкость к окислению на воздухе в значительной степени снижается при уменьшении размера частиц. Но наиболее подробно кинетика окисления алмазных порошков от зернистости 250/200 (рис. 1в) к меньшим зернистостям 28/20 мкм (рис. 1б) и 3/2 мкм (рис. 1а) приведена авторами работы [8]. Для удобства мы представили их в виде кинетических кривых (рис. 1). Можно наблюдать, что более мелкодисперсные порошки окисляются с большей скорость, чем крупные зернистости. На основании представленных термограмм, авторы отмечают [8], что температура начала окисления зернистости 3/2 мкм равна 500°С, максимум скорости окисления при 600°С. Можно отметить, что зерна размером 3/2 мкм при температуре 500°С имеют степень окисления до 6.6%. Крупные зернистости начинают окисляться при больших температурах от 510°С для АСМ 28/20 мкм до 630°С для АС32 250/200 мкм. Соответственно сдвигаются и температуры “максимального развития окисления” от 680°С (для 28/20) до 880°С (для 250/200).
Рис. 1.
Степень окисления алмазов различных марок по данным [8]: АСМ 3/2 (а), АСМ 28/20 (б), АС32 250/200 (в).
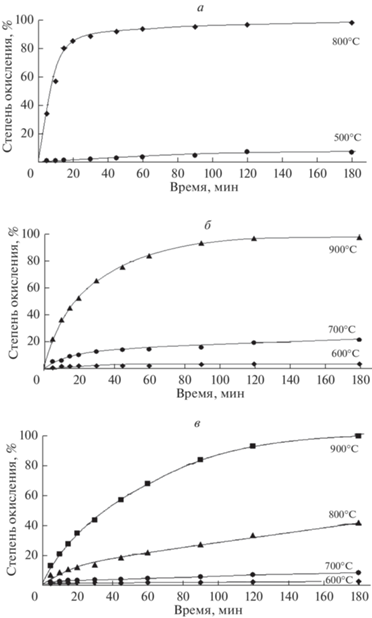
Энергия активации реакции окисления алмазного порошка также зависит от диаметра частиц – для АСМ 0.3/0 Eaкт = 19.2 кДж/моль, а для АСМ 14/10 Eaкт = 158 кДж/моль [9]. Для более мелких частиц процесс идет в диффузионной области, а для более крупных – переходит в кинетическую. Исследование окисления алмазов статического синтеза методами дифференциального термического анализа ДТА [10] и масс-спектрометрии [11] показало, что окисление начинается уже при 773 K и достигает максимальной скорости при 1073–1173 K [11]. Потеря массы при 1673 K за 2 ч составляет 63.3%, а при нагревании в токе воздуха 80 л/ч при 1323 K образец полностью окисляется [10].
Исследование взрывных алмазов АВ так же показало, что скорость окисления зависит от зернистости порошков, особенно при низких температурах [12]. Было замечено, что микропорошки из этих алмазов обладают более высокой окисляемостью, чем порошки из алмазов того же гранулометрического состава, полученные при статических давлениях. Расчеты, полученные методом ДТА, дали значения кажущейся энергии активации Ea = 257 кДж/моль, lg A = 5.73 [13] на основании которых можно предположить, что окисление взрывных алмазов идет в кинетической области (т.е. ограничено скоростью химического взаимодействия).
Для практического применения алмазных порошков и композитов на их основе не менее важно знать, как влияет на стойкость к окислению не только дисперсность алмазных зерен, но и их габитус и наличие характерных примесей. Мало изучено влияние морфологии алмазных порошков на процесс их окисления.
Цель нашей работы – исследование окисления алмаза при нагревании его в воздушной среде при атмосферном давлении.
МАТЕРИАЛЫ ИССЛЕДОВАНИЯ
Сложность выбора исходных материалов для изготовления алмазосодержащего композита связана с тем, что отечественные фирмы-поставщики алмазных порошков в большинстве случаев не являются их производителями, а порошки маркируют в соответствии с ГОСТ 9206-80 “Порошки алмазные. Технические условия” (без данных о производителе и торговой марке). В результате порошки с одинаковой маркировкой могут существенно отличаться по свойствам. Нами использованы алмазные порошки, представленные в табл. 1.
Таблица 1.
Исследуемые алмазные порошки
Марка | Зернистость, мкм | Цвет | Поставщик |
---|---|---|---|
АСМ | 3/1 | Светло-серый | Intech-diamond |
АСМ | 3/2 | Темно-серый | Веневский завод алмазного инструмента |
АСМ | 7/5 | Темно-серый | |
АСМ | 14/10 | Темно-серый | |
АСМ | 28/20 | Темно-серый | |
АСМ | 28/20 | Светло-серый | Intech-diamond |
АСМ | 50/40 | Черный | ФГБНУ ТИСНУМ |
АС6 | 100/80 | Черный | |
АС160 | 250/200 | Желто-зеленый | Intech-diamond |
MBD12 | 250/215 | Желтый | ZheCheng HongXiang Superhard Material Co., Ltd. (Китай) |
МЕТОДЫ ИССЛЕДОВАНИЯ
Морфология порошков изучена с помощью сканирующего электронного микроскопа (СЭМ) Tescan Vega 3 SBH.
Состав примесей в алмазных порошках различных производителей и зернистостей определяли в два этапа: определение несгораемого остатка после окисления навески образца на воздухе при температуре 1300°С на установке комплексного термического анализа STA 429 СD немецкой фирмы NETZSCH. Анализ элементного состава золы проводили с помощью сканирующего электронного микроскопа (СЭМ) Tescan Vega 3 SBH с приставкой для микрорентгеноспектрального анализа (МРСА) AZtec X – Act.
На дифрактометре Rigaku Smartlab 3 методом полнопрофильного анализа изучены следующие характеристики кристаллической решетки исследуемых порошков из синтетических алмазов: параметр элементарной ячейки “a”, величина микронапряжений Δa/a и размер областей когерентного рассеивания L.
Термогравиметрические исследования алмазных порошков были выполнены на установке комплексного термического анализа STA 429 СD немецкой фирмы NETZSCH с использованием платино-платинородиевого держателя для образцов типа “ТГ + ДСК”. Образцы, взвешенные с точностью до ±0.01 мг, помещали в открытые алундовые тигли и подвергали комплексному термическому анализу при нагревании со скоростью 20°С в мин в потоке воздуха (50 см3/мин) в интервале от 40 до 1490°С. Продукты разложения анализировали с помощью соединенного с печью квадрупольного масс-спектрометра QMS 403 С той же фирмы, при этом анализировали все массы в интервале от 1 до 121 массо-зарядных единиц в виде записи соответствующего ионного тока (кривая IC). При анализе производили одновременное определение изменений массы образца в % от величины навески (кривая ДСК) и изменений энтальпии, сопровождающих термические трансформации, в микроваттах на миллиграмм (кривая ДСК).
РЕЗУЛЬТАТЫ И ОБСУЖДЕНИЕ
Морфология алмазных порошков. Морфология порошков приведена на рис. 2–5. Порошки производства Веневского завода алмазного инструмента представлены агломератами, сростками и монокристальными зернами осколочной формы, не имеющими четкой огранки, цвет – от темно-серого для мелких зернистостей до черного у крупных зернистостей. Грани шероховатые. Такие алмазные микропорошки – это материал, полученный отсевом мелких фракций из общего объема синтезированных алмазов методом высоких давлений и температур (НРНТ).
Микропорошок АСМ зернистости 28/20 мкм фирмы Интекс – это преимущественно монокристаллические зерна, не имеющие определенной огранки (рис. 3б). Светло серый цвет порошков говорит о том, что они выращены в иной ростовой среде, по сравнению с порошками Веневского завода.
Марка MBD12 представлена исключительно хорошо ограненными кристаллами золотистого цвета преимущественно с гранями куба {100}, октаэдра {111} и небольшими гранями ромбододекаэдра {110} (рис. 5б). Доля агрегатов не более 2%. Порошок марки АС160 представляет собой темные желто-зеленые изометрические (коэффициент формы 1–1.1) зерна размером 250/215 мкм. Доля монокристаллов не более 65%, в т. ч. с правильной огранкой, как у MBD12, только 15%. Доля сростков до 20%, доля агрегатов (рис. 5а) до 15%. В ограненных монокристаллах преобладают грани октаэдра {111} и куба {100}, встречаются грани ромбододекаэдра {110}.
Примеси в порошках алмаза. ГОСТ 9206-80 “Порошки алмазные. Технические условия” регламентирует содержание примесей только для микропорошков. Сущность метода заключается в сжигании навески микропорошка и определение масс до и после сжигания. Определяют суммарное количество несгораемых примесей без дифференциации их по элементам. В алмазных зернах крупнее 60 мкм проверка на содержание таких примесей в объеме зерен не предусмотрена. Такой подход объясняется чрезвычайно малым содержанием примесей в зернах. В микропорошках количество несгораемых примесей не превышает 2%. Однако, такие микропримеси могут оказывать существенное влияние на свойства материала.
Рис. 7.
СЭМ фото золы после сгорания алмазных порошков АСМ 28/20: “светлый” во вторичных электронах (а), “светлый” в отраженных электронах (б), “темный” во вторичных электронах (в).
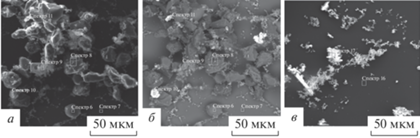
В настоящей работе определен состав примесей в алмазных порошках различных производителей и зернистостей (табл. 2).
Таблица 2.
Содержание примесей в алмазных порошках
Марка алмаза | Несгораемый остаток, вес. % | Содержание элементов в золе, вес. % | ||||||||||
---|---|---|---|---|---|---|---|---|---|---|---|---|
Ca | Na | K | Fe | Ni | Mn | Al | Cr | Zr | Nb | Ta | ||
АСМ 28/20 темный | 0.46 | 1.4 | 1.0 | 35.3 | 39.0 | 0.2 | ||||||
АСМ 28/20 светлый | 0.05 | 0.4 | 2.6 | 7.3 | 0.9 | 0.6 | 0.2 | 9.2 | 0.3 | 1.9 | 1.8 | Отдельные частицы оксида тантала |
АСМ 50/40 | 0.38 | 1.3 | 1.0 | 33.3 | 36.1 | 0.3 | ||||||
АС6 100/80 | Не опред. | 1.8 | 1.4 | 0.3 | 1.2 | 35.5 | 39.3 | 0.2 | 0.5 | |||
АС160 250/200 | 1.19 | 48.3 | 16.6 | 1.0 | ||||||||
MBD12 250/215 | 0.71 | 0.3 | 38.7 | 16.8 | 1.2 | 0.8 | 1.1 |
Обнаруженные примесные металлы можно разделить на две группы: примеси, попадающие в алмазы из контейнера, снаряженного для синтеза алмазов и помещенного в аппарат высокого давления (АВД). Это: кальций, натрий, калий, которые являются составляющими материала контейнера. Эти примеси располагаются не в кристаллах алмаза, они присутствуют в виде отдельной фазы или заключены между зернами агрегатов. Примеси, захваченные кристаллами из расплава ростовой среды. Эти примеси являются “визитной карточкой” технологии НРНТ. Наиболее распространенной средой для кристаллизации алмаза служит раствор углерода в металлах группы железа – Fe, Ni, Co.
Анализ металлов, обнаруженных в исследованных порошках, свидетельствует о том, что они были произведены по различным технологиям. Алмазные порошки и микропорошки Веневского завода алмазного инструмента выращены путем растворения графита в расплаве Ni–Mn.
Большое содержание в золе порошка АСМ 28/20 производителя “Intech-diamond” таких металлов как Al, K и практически отсутствие Fe, Ni, Mn говорит о том, что средой кристаллизации служил расплав солей щелочных и щелочноземельных металлов. Видно, что зола более легкоплавкая, чем зола от порошков, выращенных из металлических расплавов (рис. 7), что привело к образованию крупных оплавленных сферических частиц. В золе присутствуют металлы Zr, Nb не характерные для среды кристаллизации синтетических алмазов. Необычна локализация Ta – металл содержится в отдельных частицах (ярко белые частицы на рис. 7б), содержащие 66.8% тантала и 23.6% кислорода.
Монокристаллы размеров более 200 мкм обеих марок выращены из раствора углерода в металлическом расплаве Fe–Ni. После выгорания углеродной матрицы на рис. 8 хорошо видно, что частицы примесного металла в алмазных порошках MBD12 250/215 были сосредоточены компактно (вероятно, в области затравочного кристалла), а в алмазных порошках марки АС160 примеси были распределены во всем объеме.
Рис. 9.
Окисление алмазных порошков АСМ различной зернистости: 7/5 мкм (a), 14/10 мкм (б), 28/20 мкм (темный) (в). 1 – кривая ДТГ, 2 – кривая ДСК, 3 – ионный ток CO2.
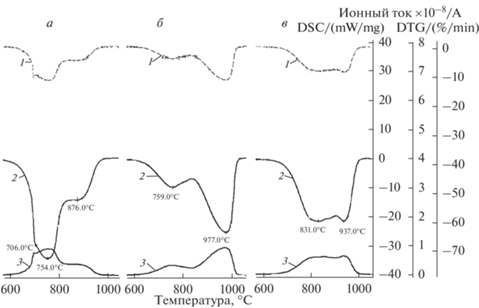
Характеристики кристаллической решетки исследуемых порошков. Результаты исследования алмазов методом полнопрофильного анализа, полученные на рентгеновском дифрактометре Rigaku Smartlab 3, подтвердили высокую чистоту всех изученных алмазных порошков. На дифрактограммах присутствовали только пики, принадлежащие алмазу, примесных фаз не обнаружено. Следовательно, содержание примесей в этих кристаллах незначительно и практически не влияет на появление неалмазного углерода на поверхности алмаза при нагревании на воздухе.
Параметр элементарной ячейки “a”, величина микронапряжений Δa/a и размер областей когерентного рассеивания L представлены в табл. 3. Полученные результаты хорошо согласуются с данными о примесях в кристаллах алмаза. Повышенное значение параметра элементарной ячейки порошков, выращенных из металлических расплавов, может быть связано с внедрением металлов катализаторов в кристаллическую решетку в процессе синтеза алмазов методом НРНТ. Значительные размеры ОКР и небольшие микронапряжения в зернах 250/200 мкм говорят о достаточном совершенстве кристаллов.
Таблица 3.
Характеристики кристаллической решетки исследуемых алмазных порошков
Образец | Зернистость, мкм | “а”, нм | Δa/a | L, нм |
---|---|---|---|---|
АСМ темный | 3/2 | 0.35659 | 0.012 | 22 |
АСМ | 7/5 | 0.35645 | 0.002 | 31 |
АСМ | 14/10 | 0.35643 | 0.007 | 36 |
АСМ темный | 28/20 | 0.35642 | 0.003 | 24 |
АСМ светлый | 28/20 | 0.35600 | –0.001 | 40 |
АСМ | 50/40 | 0.35643 | 0.032 | 27 |
АС6 | 100/80 | 0.35707 | –0.0045 | 34 |
АС160 | 250/200 | 0.35702 | 0.0006 | 700 |
MBD12 | 250/200 | 0.35702 | –0.0001 | более 900 |
Термогравиметрические исследования алмазных порошков. Полученные в результате термогравиметрического исследования алмазных порошков кривые (ионный ток, изменения массы образца (кривая ДТГ) и изменения энтальпии (кривая ДСК)) приведены на рис. 9–12.
Рис. 10.
Окисление алмазных порошков различных марок: АСМ 3/2 темный (a), АСМ 3/1 светлый (б). 1 – кривая ДТГ, 2 – кривая ДСК, 3 – ионный ток CO2.

Рис. 11.
Окисление алмазных порошков различных марок и зернистости: АСМ 28/20 мкм (светлый) (a), АСМ 50/40 мкм (б), АС6 100/80 мкм (в). 1 – кривая ДТГ, 2 – кривая ДСК, 3 – ионный ток CO2.
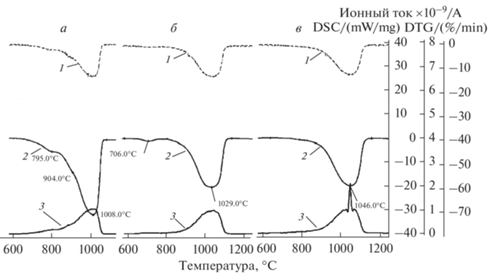
Рис. 12.
Окисление алмазных порошков различных марок: АСМ160 (a), MBD12 (б). 1 – кривая ДТГ, 2 – кривая ДСК, 3 – ионный ток CO2.

Эксперименты показали, что при нагревании порошков алмаза, выращенных из раствора углерода в металлическом расплаве Ni–Mn (Веневского завода алмазного инструмента), до температуры 1490°С наблюдается несколько экзотермических эффектов (рис. 9, 10) положение максимумов которых приведено в табл. 4. Температуры начала окисления тонких микропорошков, всех изученных зернистостей, примерно одинаковая до 504–526°С. У алмазных порошков зернистостью 50/40 и 100/80 температура начала окисления снижается, что можно объяснить их более дефектной структурой. При этом наиболее выраженный эффект, наоборот, смещается в сторону большей температуры 1029–1046°С (рис. 11).
Таблица 4.
Экзотермические эффекты при окислении углеродных материалов
№ | Материал | Температура окисления, °С | Убыль массы, % | Тепловой эффект, Дж/г | |||||
---|---|---|---|---|---|---|---|---|---|
начало | максимумы эффектов | ||||||||
1 | АСМ 3/1 светлый | 463 | 632 | 655 | 823 | 845 | 97.82 | 12 988 | |
2 | АСМ 3/2 темный | 504 | 703 | 766 | 833 | 100 | 15 267 | ||
3 | АСМ 7/5 | 504 | 706 | 754 | 876 | 99.51 | 17 251 | ||
4 | АСМ 14/10 | 526 | 759 | 977 | 100 | 13 331 | |||
5 | АСМ 28/20 темный | 574 | 833 | 937 | 99.56 | 14 810 | |||
6 | АСМ 50/40 | 380 | 706 | 1029 | 99.62 | 9480 | |||
7 | АС6 100/80 | 499 | 784 | 1046 | 100 | 9312 | |||
8 | АСМ 28/20 светлый | 532 | 795 | 904 | 1008 | 99.95 | |||
9 | MBD12 250/215 | 684 | 1089 | 99.29 | 12693 | ||||
10 | АС160 250/200 | 673 | 1005 | 1031 | 98.81 | 11748 |
Окисление светлого микропорошка зернистости 28/20, принципиально отличается от процесса в предыдущих материалах. Имеется один выраженный максимум на кривой DSC при температуре 1008°С (рис. 11).
Крупные монокристальные зерна 200–250 мкм окисляются труднее, имеют более высокую температуру начала процесса 670–680°С, а максимум скорости окисления сдвинут до 1090°С. Более качественные порошки марки MBD12 устойчивее, чем порошки АС160 (рис. 12).
Обобщая результаты комплексного термического анализа поведения алмазных порошков при окислении, следует отметить, что характер поведения материалов при нагревании сильно отличается для алмазных порошков различных зернистостей и производителей. Наблюдается существенное отличие между различными марками алмазных порошков при одинаковой зернистости. В табл. 5 представлены результаты комплексного исследования пяти марок синтетических алмазов, выполненные в данной работе.
Таблица 5.
Влияние основных характеристик алмазных порошков различных марок на процесс их окисления на воздухе
Марка алмаза | Несгораемый остаток, мас. % |
T начала окисления, °С | L, нм | Δa/a | Содержание элементов в золе, мас. % | ||||
---|---|---|---|---|---|---|---|---|---|
Fe | Ni | Mn | Al, Cr, Zr, Nb | Ta | |||||
АСМ 28/20 темный |
0.46 | 574 | 24 | 0.003 | 1.0 | 35.3 | 39.0 | Al 0.2 | |
АСМ 28/20 светлый |
0.05 | 532 | 40 | –0.001 | 0.9 | 0.6 | 0.2 | Al 9.2 Cr 0.3 Zr 1.9 Nb 1.8 |
Отдель- ные частицы оксида тантала |
АС6 100/80 |
Не определено | 499 | 34 | –0.0045 | 1.2 | 35.5 | 39.3 | Al 0.2 Cr 0.5 |
|
АС160 250/200 |
1.19 | 673 | 700 | 0.0006 | 48.3 | 16.6 | Cr 1.0 | ||
MBD12 250/215 |
0.71 | 684 | Более 900 | –0.0001 | 38.7 | 16.8 | 1.2 | Al 0.8 |
Анализ полученных комплексных результатов показал, что одним из основных факторов, влияющих на поведение алмаза при его окислении на воздухе, является метод получения, т.е. доля и природа присутствующих в порошках примесей, а также размер зерен и их морфология.
В работе обнаружен сложный многоступенчатый характер процесса окисления, который пока трудно объяснить. Авторы [14] отмечали присоединение к поверхности алмаза кислородных групп с образование поверхностных окислов. В продолжение этих исследований была определена энергия активации хемосорбции и показано ее линейное увеличение от степени заполнения поверхности кислородом, предполагается, что фиксация кислорода происходит только на поверхности {111} [15].
Изучение окисления синтетических алмазов, осажденных из газовой фазы, показало, что окисление начинается при 873 K, а при 1123 K происходит изменение механизма процесса и наряду с окислением наблюдается и графитизация алмаза [16]. Известно, что графитизацию алмаза катализируют химически активные к углероду примеси или покрытия [5, 6, 17]. Например, в работе [18] показано, что скорость окисления алмазов, синтезированных на основе железо-никель выше, чем скорость окисления алмазов, синтезированных на основе никель-марганца. На влияние примесей при окислении алмаза указывают авторы [19]. Процесс окисления алмазных поликристаллов АРК4 и влияние на него состава сплава-катализатора изучали в работе [20], где так же подтверждено влияние примесей.
Наличие граней куба у зерен порошка марки MBD12 способствует повышению температуры начала окисления, так как химическая стойкость [100] выше, чем у граней октаэдра [111]. Поэтому по сравнению с остальными порошками порошки марки MBD12 имеют преимущество в процессе нагревания на воздухе, проявляющееся в самой высокой температуре начала окисления из всех исследованных порошков.
ЗАКЛЮЧЕНИЕ
Окисление синтетических алмазов зависит от температуры нагревания, давления кислорода в системе, примесей металлов в алмазах и морфологии кристаллов.
Наблюдается существенное отличие между различными марками алмазных порошков при одинаковой зернистости.
Комплексное исследование характеристик порошков из синтетических алмазов свидетельствует об определяющем влиянии примесей на процесс окисления алмазных порошков.
Определены температуры начала окисления алмазных порошков различных марок: минимальная – 499, максимальная – 684°С. Определены две группы примесных металлов в исследуемых алмазных порошках: попадающие в алмаз из материала реакционной ячейки, находящейся в аппарате высокого давления, в котором происходит синтез алмаза, – Ca, K, Na, они присутствуют в виде отдельной фазы или заключены между зернами агрегатов; захваченные кристаллом из ростовой среды: Fe, Co, Ni, Mn.
Наибольшим совершенством обладают порошки из синтетических алмазов марки MBD12 200/250. Они имеют максимальное значение температуры начала окисления на воздухе алмазных порошков, равное 684°С.
Исследование выполнено за счет гранта Российского научного фонда (проект № 20-13-00054).
Список литературы
Поликристаллические материалы на основе алмаза / Отв. ред. Н.В. Новиков // Киев: Наукова думка, 1989. 192 с.
Shevchenko V.Ya., Perevislov S.N. Reaction–diffusion mechanism of synthesis in the diamond–silicon carbide system // Russian J. Inorganic Chemistry. 2021. V.66. № 8. P. 1107–1114.
Шевченко В.Я., Перевислов С.Н., Уголков В.Л. Физико-химические процессы взаимодействия в системе углерод (алмаз) – кремний // Физика и химия стекла. 2021. Т. 47. № 3. С. 257–272.
Evans T., Phaal C. The kinetics of the diamond-oxygen reaction // Conference on Carbon. 1961. V. 5. № 1. P. 147–153.
Отопков П.П., Ножкина А.В., Васильева Л.А. Влияние термообработки на физико-химические свойства алмазов. Физико-химические свойства алмазов // Тр. ВНИИАлмаз. М. 1974. С. 15–24.
Nozhkina A.V., Laptev A., Ralchenko V., Bolshakov A., Khomich A., Komlenok M., Conte G. Diamond surface graphitization by catalytic action of metal films for electric contacts // Diamond and carbon materials-2013” Riva Del Garda, Italy, 2–5 sept. 2013.
Горбачев В.М. Кинетика окисления синтетических алмазов различного гранулометрического состава // Сверхтвердые материалы. 1981. № 4. С. 16–18.
Физические свойства алмаза. Справочник / Под ред. Н.В. Новикова // Киев: Наукова думка, 1987. 192 с.
Клевцур С.А, Лохов Ю.Н., Спасский М.Р., Евко Э.И. Влияние дисперсности микропорошка алмаза на скорость его окисления // Известия АН СССР. Неорганические материалы. 1981. Т. 17. № 9. С. 1598–1602.
Ogorodnik V.V., Pugach E.A., Postolova G.S. Application of DTA-DTG-TG complex thermal analysis to study diamond oxidation processes // Thermochim. Acta. 1985. V. 93. P. 705–708.
Kozeluha V., Drexler J., Havlicek J. An evaluation of the heat stability of synthetic diamonds by means of mass spectrometer QMG 311 // High Pressures. High Temp. 1986. V. 18. № 3. P. 347–349.
Пугач Э.А., Андреев В.Д., Огородник В.В., Лукаш В.А., Филипченко С.И. Кинетика окисления алмазов АВ // Сверхтвердые материалы. 1980. № 4. С. 10–13.
Бреусов О.Н., Волко В.М., Стрижкова И.Г., Таций В.Ф. Применение ДТА для изучения кинетики окисления алмаза // Кинетика и катализ. 1977. Т. 18. № 4. С. 837–841.
Sappok R., Boehm H.P. Chemie der oberflashe des diamanten-II. Bildung, eigenschaften und structur der oberflachenoxide // Carbon. 1968. V. 6. № 5. P. 573–588.
Touhara H., Okino F. Property control of carbon materials by fluorination // Carbon. 2000. V. 38. P. 241–267.
Успенская К.С., Толмачев Ю.Н., Федосеев Д.В. Окисление и графитизация алмаза при низких давлениях // Журн. физической химии. 1982. Т. 56. № 2. С. 495–496.
Ножкина А.В. Взаимодействие алмаза с металлами и сплавами // Сб. “Вячеслав Петрович Елютин” издательский дом “Руда и металлы”. М.: МИСиС, 2005. С. 158–165.
Ильницкая Г.Д., Исонкин А.М., Зайцева И.Н. Влияние дисперсности алмазов, синтезированных в разных ростовых системах, на процесс их графитизации в воздушной среде // Прогресивні технології і системи машинобудування. 2013. Вип. 1(45)–2(46). С. 118–123.
Елютин А.В., Ермолаев А.А., Лаптев А.И., Манухин А.В. Влияние металлической фазы в поликристалле алмаза на процесс его окисления // Доклады академии наук. 2000. Т. 375. № 4. С. 457–461.
Лаптев А.И. Процессы и технологии синтеза алмазных поликристаллических композиционных материалов на основе разработанных сплавов-катализаторов Ni–X (Mo, Cr, Ti, B): автореф. дис. д-ра техн. наук: 05.16.06; М.: МИСиС, 2009. 49 с.
Дополнительные материалы отсутствуют.
Инструменты
Физика и химия стекла