Физика металлов и металловедение, 2019, T. 120, № 10, стр. 1058-1065
Формирование структуры и свойств при термоводородной обработке сплава на основе алюминида титана Ti2AlNb
А. Г. Илларионов a, b, *, О. Г. Хаджиева c, С. М. Илларионова a, Е. Д. Мерсон d
a ФГАОУ ВО Уральский федеральный университет
620002 Екатеринбург, ул. Мира, 19, Россия
b Институт физики металлов УрО РАН
620108 Екатеринбург, ул. С. Ковалевской, 18, Россия
c НПФ “АВЭК”
620049 Екатеринбург, ул. Первомайская, 109, Россия
d НИИ прогрессивных технологий, Тольяттинский государственный университет
445020 Тольятти, ул. Белорусская, 14, Россия
* E-mail: illarionovag@mail.ru
Поступила в редакцию 06.05.2019
После доработки 07.05.2019
Принята к публикации 15.05.2019
Аннотация
Методами электронной микроскопии, рентгенографии, микроиндентирования изучено изменение структуры, фазового состава, микротвердости и модуля упругости при термоводородной обработке сплава ВТИ4 на основе орторомбического алюминида титана Ti2AlNb, легированного водородом до 12.5 ат. %. Показано, что легирование водородом исследуемого сплава способствует снижению пиковых напряжений, повышению степени деформации до образования трещин в ходе осадки при температуре 900°С. Изучена кинетика разводороживания сплава при температурах 600 и 700°С в течение 4 ч в потоке аргона и в вакууме. Термоводородная обработка сплава ВТИ4 позволяет получить после окончательного разводороживающего отжига в вакууме при 600°С в течение 4 ч термически стабильное, с безопасным содержанием водорода состояние с преобладанием О-фазы в структуре и высокие физико-механические свойства – твердость по Виккерсу до 5300 МПа, контактный модуль упругости до 114 ГПа.
ВВЕДЕНИЕ
ВТИ4 относится к так называемым О-сплавам на основе орторомбического алюминида титана Ti2AlNb (О-фазы). Благодаря сочетанию высокой термической стабильности, удельной прочности, хорошей обрабатываемости, они являются перспективными функциональными материалами. Например, О-сплавы имеют потенциал для использования в авиационных газотурбинных двигателях и силовых установках с рабочими температурами в диапазоне 600–700°С [1, 2], в качестве альтернативы пожароопасным титановым сплавам [3], основы композитов [4], сплавов – накопителей водорода [5, 6]. Полуфабрикаты и конструкции из О-сплавов изготавливают методами литья и горячей деформации [1, 7] с возможностью получения сварных соединений [8], и порошковой металлургии [9, 10].
Введение в сплавы титана на базе систем Ti–Al, Ti–Nb, Ti–Al–Nb водорода способствует расширению области существования высокотемпературного β-твердого раствора с ОЦК-решеткой [11, 12], снижению температуры перехода сплавов в однофазное β-состояние [12, 13], оказывает положительное влияние на их технологическую пластичность [11, 13], включая О-сплавы [14, 15]. Повышение технологической пластичности титановых сплавов в ходе операций деформации за счет легирования водородом связано с так называемым эффектом водородного пластифицирования [16–18]. Данный эффект широко используется при их термоводородной обработке (ТВО) [12]. При разработке режима ТВО необходимо знание закономерностей протекания фазовых превращений в сплаве в ходе термического воздействия до и после наводороживания. Ранее нами на сплаве ВТИ4 изучено влияние температуры нагрева на фазовый состав при закалке, процессы распада метастабильных фаз при непрерывном нагреве и старении в ненаводороженном [19, 20] и наводороженном [14, 21, 22] состояниях. Однако пока нет ответа на вопрос, как поведет себя сплав ВТИ4, легированный водородом, с точки зрения формирования структуры, фазового состава, изменения комплекса технологических и физико-механических свойств в ходе ТВО, включающей процессы наводороживания, горячей пластической деформации и последующего разводороживающего отжига. Исходя из этого, целью работы является изучение влияния ТВО на структуру и свойства сплава ВТИ4.
МАТЕРИАЛ И МЕТОДИКИ
Материалом для исследования служили цилиндрические образцы диаметром 20 мм, вырезанные из центральной части слитка сплава ВТИ4 состава Ti–24.3Al–24.8Nb–1.0Zr–1.4V–0.6Mo–0.3Si (ат. %). Полученные образцы были подвергнуты ТВО, включающей наводороживающий отжиг, горячую деформацию и разводороживающий отжиг (РВО). Наводороживание сплава проводили до получения в нем содержания водорода 5.2, 8.5 и 12 ат. % в установке Сивертса при давлении водорода 93 кПа путем ступенчатого медленного охлаждения с печью после предварительной выдержки при температуре 900°С в течение 30 мин. Конечное содержание водорода в сплавах определяли по разности парциальных давлений водорода в системе до и после наводороживания. В работе ненаводороженный сплав ВТИ4 обозначен как сплав 1, сплавы с 5.2, 8.5 и 12 ат. % водорода фигурирует как сплавы 2, 3, 4 соответственно.
Образцы сплавов 1, 2, 3, 4 нагревали до температуры 900°С, выдерживали 30 мин и производили горячую изотермическую деформацию осадкой на универсальной гидравлической испытательной машине Instron 300LX со скоростью 10–3 с–1, затем образцы извлекали из печи и охлаждали на воздухе. Данный вид испытаний проводили в лаборатории “Объемные наноструктурные материалы” Белгородского НИУ, г. Белгород. РВО деформированных образцов проводили в лаборатории “Физика прочности и интеллектуальные диагностические системы” ТГУ, г. Тольятти. в газоанализаторе G8 Galileo ON/H методом горячей экстракции в атмосфере проточного аргона для исключения образования окисной пленки, тормозящей процесс выхода водорода, а также в вакууме (давление 2.67 × 10–3 Па) в течение 4 ч при температурах 600 и 700°С. Оценку остаточного содержания водорода в дегазированных сплавах производили в газоанализаторе методом плавления. Исследование микроструктуры сплавов осуществляли методом просвечивающей и растровой электронной микроскопии на приборах Jeol 2100 и JSM6490LV при ускоряющем напряжении 200 и 35 кВ соответственно в ЦКП УрФУ в “Лаборатории структурных методов анализа и свойств материалов и наноматериалов”. Рентгеноструктурный фазовый анализ сплавов проводили на дифрактометре Bruker D8 Advance в CuKα-излучении. Для прецизионного определения периодов решеток О- и β-фаз использовали метод Ритвельда. Микротвердость по Виккерсу и контактный модуль упругости сплавов определяли методом микроиндентирования на приборе MHTX CSM Instruments по методике Оливера и Фарра при нагрузке 9 Н.
РЕЗУЛЬТАТЫ И ОБСУЖДЕНИЕ
Данные по изменению удельных усилий (напряжений) в ходе осадки при 900°С в зависимости от степени деформации сплава ВТИ4 с различным содержанием водорода приведены на рис. 1.
Рис. 1.
Зависимость удельного усилия осадки при 900°С сплава ВТИ4 с различным содержанием водорода от степени деформации.
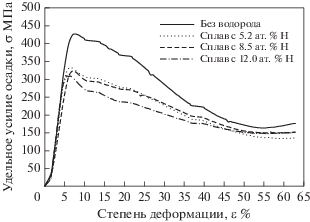
Анализ полученных зависимостей показал, что введение в сплав ВТИ4 водорода от 5.2 до 12 ат. % способствует снижению пиковых напряжений при осадке примерно в 1.4 раза от 427 до 310 МПа (рис. 2).
Кроме того, обнаружено, что максимальная степеней деформации при осадке до образования трещин на поверхности образцов за счет введения водорода в сплав ВТИ4 повышается от 40% для сплава 1 до 75% для сплава 4.
Наблюдаемые изменения являются проявлением эффекта водородного пластифицирования. В нашем случае эффект связан с увеличением при 900°С объемной доли наиболее пластичной β-фазы и подавлением образования хрупкой α2-фазы в структуре наводороженного сплава ВТИ4, зафиксированным нами [14].
Сравнение структуры сплавов до и после деформации при 900°С (рис. 3) показало, что в ходе горячей деформации осадкой исследуемых сплавов получают развитие процессы динамической рекристаллизации в β-мартице. В результате образуются мелкие рекристаллизованные зерна с относительно невысокой плотностью дислокаций. Повышение содержания водорода в сплаве обеспечивает более полное протекание динамической рекристаллизации (рис. 3г). Очевидно, именно развитие процессов динамической рекристаллизации способствует снижению усилий при осадке после достижения максимальных пиковых напряжений (рис. 1). Такой эффект наблюдали при аналогичных температурах деформации в сплаве на основе орторомбического алюминида Ti2AlNb в работе [7].
Рис. 3.
Структура сплавов 1 (а, в) и 3 (б, г) после обработки при 900°С: а, б – после закалки (без деформации), в, г – после горячей осадки.
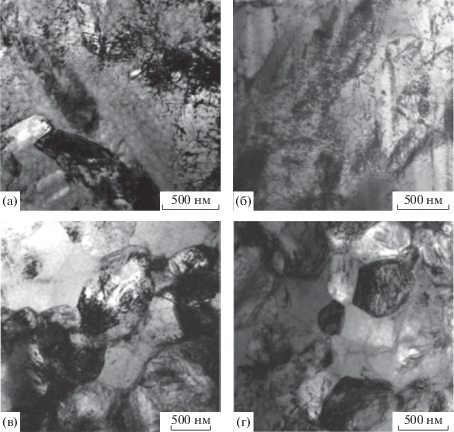
Данные по скорости и степени разводороживания в проточном аргоне горячедеформированных сплавов 2 и 4, содержащих 5.2 и 12 ат. % водорода, при температурах изохронного отжига 600 и 700°С в течение 4-х ч (240 мин) представлены на рис. 4.
Рис. 4.
Скорость (а) и степень (б) разводороживания сплава ВТИ4 при отжиге в проточном аргоне в зависимости от времени выдержки.
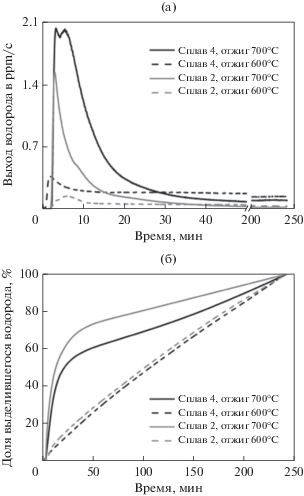
Анализ полученных зависимостей показал, что при обеих температурах отжига максимальный поток водорода из исследованных сплавов наблюдается в течение первых 5–10 мин выдержки (рис. 4а). Повышение температуры отжига от 600 до 700°С в несколько раз увеличивает скорость выхода водорода. Кривые скорости разводороживания при температуре 700°С характеризуются наличием двух характерных максимумов для сплава 4 в интервале выдержек 3–6 мин. Для сплава 2 наблюдается один интенсивный максимум после выдержки около 3-х мин и второй менее интенсивный максимум (на кривой наблюдается в виде “излома”), смещенный в сторону более длительного времени выдержки 8–12 мин (рис. 4а). Два максимума на кривых разводороживания сплавов 2 и 4, по нашему мнению, могут быть связаны с выходом водорода из различных мест. Первый интенсивный максимум отвечает выходу водорода, который находится в твердом растворе и является диффузионно-подвижным. Второй максимум соответствует выходу водорода, закрепленного на дислокациях, сгенерированных в ходе предшествующей горячей деформации. Взаимодействие водорода с дефектами кристаллического строения с образованием атмосфер на дислокациях в деформированном титановом сплаве ВТ16 было ранее обнаружено в работе [23].
Анализ кинетики разводороживания (рис. 4б) показал, что при температуре отжига 700°С зависимость доли выделившегося водорода от времени близка к логарифмической или Г-образной. При этом величина вертикального участка кривой определяется содержанием водорода в сплаве до отжига, а углы наклона пологих участков кривых примерно одинаковы для исследованных сплавов с водородом. При уменьшении температуры отжига до 600°С вид зависимости меняется на близкий к линейному: вертикальный участок практически отсутствует, а угол наклона определяется содержанием водорода в сплаве до отжига. Близкого вида кривые разводороживания при аналогичных температурах отжига ранее фиксировали в работе [24] для титанового сплава ОТ4.
О степени разводороживания судили по остаточному содержанию водорода в сплаве ВТИ4 после отжига, которое было оценено методом плавления. Результаты приведены в табл. 1.
Таблица 1.
Содержание водорода в сплавах 2 и 4 после РВО в атмосфере аргона в течение 4 ч при различных температурах
Сплав | Содержание водорода в сплавах после разводороживания при различных температурах, мас. % | |
---|---|---|
600°С | 700°С | |
2 | 0.024 | 0.004 |
4 | 0.020 | 0.003 |
Согласно данным монографии [25, с. 113], для не сварных конструкций, выполненных из титановых сплавов, концентрация водорода не должна превышать 0.020 мас. %. Из табл. 1 видно, что получение допустимой концентрации водорода в обоих сплавах обеспечивается РВО при температуре 700°С.
Для исследования влияния атмосферы отжига (аргон, вакуум) на скорость разводороживания был проведен вакуумный отжиг сплава 2 при температуре 600°С в течение 4 ч. Остаточное содержание водорода после такой обработки составило 0.012 мас. %. Это в 2 раза меньше, чем после отжига при той же температуре в аргоне и в 1.5 раза меньше максимальной допустимой концентрации. Соответственно, для получения безопасной концентрации водорода в сплаве ВТИ4 при вакуумном отжиге в течение 4 ч его можно проводить и при температуре 600°С.
Дифрактограммы сплава ВТИ4 после РВО приведены на рис. 5. После РВО для сплава 1 интенсивность линий β-фазы, в частности {110}β выше, чем для сплавов 2 и 4. При этом с повышением температуры РВО от 600 до 700°С относительная интенсивность линий β-фазы увеличивается. По нашему мнению, в ходе разводороживающего отжига сплавов 2 и 4 присутствие в них водорода облегчает перераспределение легирующих элементов, по сравнению со сплавом 1, нелегированным водородом. Это интенсифицирует процессы распада β-фазы, как мы наблюдали при старении наводороженных сплавов [22]. В результате в сплавах 2 и 4 формируется более равновесное термически стабильное состояние с большим количеством О-фазы в структуре по сравнению со сплавом 1.
Данные о фиксируемых при РВО параметрах О- и β-фаз, полученные из расчета дифрактограмм представлены в табл. 2.
Таблица 2.
Параметры решеток О- и β-фаз и удельный объем, приходящийся на один атом в решетке О-фазы, сплавов 1, 2, 4 после отжига
Периоды решетки О-фазы, нм | V, 10–30, м3/ат | Период решетки β-фазы а, нм | |||
---|---|---|---|---|---|
а | b | с | |||
Тотж = 600°С | |||||
1 | 0.6053 | 0.9573 | 0.4660 | 16.88 | 0.3251 |
2 | 0.6055 | 0.9607 | 0.4668 | 16.97 | –* |
4 | 0.6069 | 0.9567 | 0.4664 | 16.93 | –* |
Тотж = 700°С | |||||
1 | 0.6048 | 0.9578 | 0.4655 | 16.85 | 0.3255 |
2 | 0.6039 | 0.9611 | 0.4665 | 16.92 | 0.3258 |
4 | 0.6067 | 0.9577 | 0.4665 | 16.94 | 0.3257 |
Анализ данных табл. 2 показал, что при обеих температурах отжига у разводороженных сплавов 2 и 4 удельный объем V, приходящийся на один атом в решетке О-фазы, больше, чем в ненаводороженном сплаве 1, как и период решетки β-фазы при температуре 700°С. Причиной наблюдаемых отличий является отмеченное выше более полное развитие при отжиге процессов распада β-твердого раствора в сплавах 2 и 4, исходно содержащих водород. Это способствует увеличению в них количества О-фазы и соответственно уменьшению количества β-фазы при одинаковых температурах отжига (рис. 5). В результате у сплавов 2 и 4 содержание основного β-стабилизатора ниобия в β‑твердом растворе, сохранившемся в меньшем объеме, должно быть выше, чем в сплаве 1, что, согласно [19], способствует росту периода решетки β-фазы. Кроме того, за счет фиксации в структуре сплавов 2, 4 после РВО большего количества О-фазы по сравнению со сплавом 1, среднее содержание алюминия в О-фазе (Ti2AlNb) в сплавах 2, 4 будет меньше, чем в сплаве 1. Вследствие меньшего атомного радиуса алюминия (0.143 нм) по сравнению с атомами титана и ниобия (0.146, 0.147 нм) это способствует увеличению удельного объема О-фазы. В пользу полученных зависимостей свидетельствует рост периода решетки β-фазы в сплаве 1 и преимущественное уменьшение удельного объема решетки О-фазы на 1 атом в сплавах 1, 2, 4 при повышении температуры отжига, когда в структуре также увеличивается количество нераспавшейся β-фазы и уменьшается объемная доля О-фазы.
Структура разводороженных при 600°С сплавов 2 и 4 (рис. 6а, 6б) представлена фрагментами первичных пластин О- фазы, раздробленных при осадке и частично сфероидизированных при охлаждении от температур деформации, и мелкодисперсными вторичными О-пластинами, сформировавшимися в ходе разводороживающего отжига. Выделение дисперсных вторичных пластин О-фазы приводит к некоторому повышению дюрометрических характеристик отожженных сплавов (табл. 3), по сравнению с ненаводороженным горячедеформированным состоянием, когда твердость сплавов 1, 2 и 4 составила 4600, 4700 и 4800 МПа, соответственно. После отжига при 600°С сплав 2 имеет такую же твердость, как и сплав 1, а твердость сплава 4 выше. Последнее, вероятно, связано с большим количеством β-фазы, сохранившейся в структуре сплава 4 при охлаждении от температуры деформации, что обеспечило выделение большего количества вторичных частиц О-фазы при РВО.
Рис. 6.
Структура сплавов 2, 4 после РВО при 600°С (а, б) и 700°С (в, г): а, в – сплав 2, б, г – сплав 4.
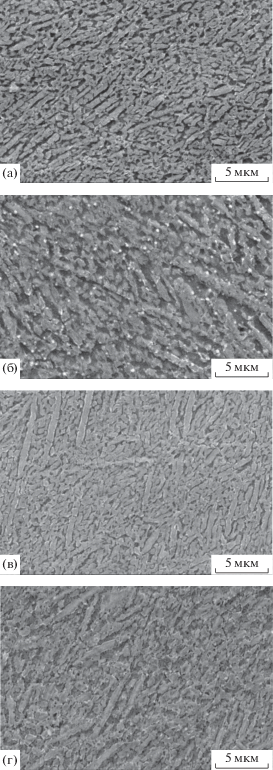
Таблица 3.
Твердость и модуль упругости сплава ВТИ4 после РВО
Сплав | Режим отжига | |||
---|---|---|---|---|
600°С, 4 ч | 700°С, 4 ч | |||
НV, МПа | Е, ГПа | НV, МПа | Е, ГПа | |
1 | 5000 | 116 | 5000 | 117 |
2 | 5000 | 108 | 4600 | 112 |
4 | 5300 | 114 | 4600 | 118 |
Повышение температуры РВО от 600 до 700°С в сплавах 2 и 4 способствует росту как размеров сфероидизированных первичных частиц, так и вторичных пластин О-фазы (рис. 6). Это приводит к получению более низких значений твердости (на 10–15%) в сплавах, отожженных при 700°С, по сравнению с отжигом при температуре 600°С (табл. 3). Кроме того, повышение температуры разводороживающего отжига от 600 до 700°С приводит к незначительному (на 1–4 ГПа) росту модуля упругости для каждого сплава (табл. 3).
Данный эффект, очевидно, связан с изменением легированности преобладающей в структуре сплавов О-фазы, а именно, с увеличением содержания в О-фазе алюминия. Это приводит к преимущественному уменьшению удельного объема на 1 атом в решетке О-фазы сплавов (табл. 2) при повышении температуры отжига от 600 до 700°С, обеспечивая рост модуля упругости в О‑сплавах [26].
Таким образом, на основании проведенных исследований были сделаны следующие выводы:
Повышение содержания водорода в сплаве ВТИ4 от 5.2 до 12 ат. % усиливает эффект водородного пластифицирования сплава в ходе горячей осадки при 900°С, обеспечивая снижение пиковых напряжений от 427 до 310 МПа, повышение максимальных степеней деформации до образований трещин от 40% (ненаводороженный сплав) до 75% (сплав с 12 ат. % Н), интенсифицирование процесса динамической рекристаллизации. Это расширяет возможности получения деформируемых изделий сложной формы из О-сплава ВТИ4.
Процесс разводороживания в проточном аргоне сплава ВТИ4 ускоряется при повышении температуры от 600 до 700°С и может иметь 2-х стадийный характер, обусловленный различными местами выхода (твердый раствор, атмосферы на дислокациях) водорода из сплава.
Режим термооводородной обработки сплава ВТИ4, включающий наводороживание до 12 ат. % водорода, горячую деформацию осадкой при 900°С и последующий разводороживающий вакуумный отжиг при температуре 600°С в течение 4 ч, позволяет получить термически стабильное состояние сплава с преобладанием О-фазы в структуре с допустимым содержанием водорода и сохранить высокие физико-механические свойства – твердость по Виккерсу 5300 МПа, контактный модуль упругости 114 ГПа.
Работа выполнена при финансовой поддержке постановления № 211 Правительства Российской Федерации, контракт № 02.A03.21.0006 и госзаданий Минобрнауки РФ для УрФУ в рамках базовой темы № 11.8386.2017/БЧ и для ИФМ УрО РАН (шифр “Структура”).
Список литературы
Кашапов О.С., Новак А.В., Ночовная Н.А., Павлова Т.В. Состояние, проблемы и перспективы создания жаропрочных титановых сплавов для деталей ГТД // Труды ВИАМ (эл. журн.). 2013. № 3.
Skvortsova S.V., Il’in A.A., Mamonov A.M., Nochovnaya N.A., Umarova O.Z. Structure and properties of semifinished sheet products made of an intermetallic refractory alloy based on Ti2AlNb // Mater. Sci. 2016. V. 51. № 6. P. 821–826.
Ночовная Н.А., Алексеев Е.Б., Изотова А.Ю., Новак А.В. Пожаробезопасные титановые сплавы и особенности их применения // Титан. 2012. № 4. С. 42–46.
Юровских А.С., Демаков С.Л., Колосова Е.В. Особенности структуры и фазового состава слоистого материала Ti–23Al–26Nb/Al, полученного методом плазменно-искрового спекания // Металловедение и термическая обработка металлов. 2012. № 9(687). С. 35–40.
Zhang L.T., Itu K, Vasudevan V.K., Yamaguchi M. Hydrogen absorption and desorption in a B2 single-phase Ti–22Al–27Nb alloy before and after deformation // Acta Mater. 2001. V. 49. P. 751–758.
Patselov A.M., Rybin V.V., Greenberg B.A., Mushnikov N.V. Hydrogen absorption in as-cast bcc single – phase Ti–Al–Nb alloys // J. Alloys and Compounds. 2010. V. 505. P. 183–187.
Wang S., Xu W., Zong Y., Zhong X., Shan D. Effect of initial microstructure on hot deformation behavior and workability of Ti2AlNb– based alloy // Metals. 2018. V. 8. P. 382. https://doi.org/10.3390/met8060382
Jiao X., Kong B., Tao W., Liu G., Ning H. Effects of annealing on microstructure and deformation uniformity of Ti–22Al–24Nb–0.5Mo laser welded joints// Materials & Design. 2017. V. 130. P. 166–174.
Li M., Cai Q., Liu Y., Ma Z., Wang Z., Huang Y., Li H. Formation of fine B2/β + O structure and enhancement of hardness in the aged Ti2AlNb-based alloys prepared by spark plasma sintering // Metal. Mater. Trans. A. 2017. V. 48A. № 9. P. 4365–4371.
Yang J.L., Wang G.F., Zhang W.C., Chen W.Z., Jiao X.Y., Zhang K.F. Microstructure evolution and mechanical properties of P/M Ti–22Al–25Nb alloy during hot extrusion // Materials Science & Engineering A. 2017. V. 699. P. 210–216.
Popov A.A., Illarionov A.G., Demakov S.L., Elkina O.A. Study of phase transformations in the titanium-niobium-hydrogen system // International J. Hydrogen Energy. 1997. V. 22. № 2/3. P. 195–200.
Ильин А.А., Колачев Б.А., Носов В.К., Мамонов А.М. Водородная технология титановых сплавов. М.: МИСиС, 2002. 392 с.
Froes F.H., Senkov O.N., J.I. Qazi Hydrogen as a temporary alloying element in titanium alloys: thermohydrogen processing // Intern. Mater. Rev. 2013. V. 49. № 3–4. P. 227–245.
Илларионов А.Г., Гриб С.В., Попов А.А., Демаков С.Л., Карабаналов М.С., Хаджиева О.Г., Елкина О.А. Влияние водорода на формирование структуры и фазового состава в сплаве на основе Ti2AlNb // ФММ. 2010. Т. 109. № 2. С. 154–164.
Скворцова С.В., Гвоздева О.Н., Пожога В.А., Слезов С.С., Ягудин Т.Г. Водородная технология как эффективный технологический способ управления структурой, механическими и технологическими свойствами сплавов на основе титана и алюминида титана //Титан. 2016. № 4(54). С. 49–53.
Zwicker U., Scheicher H. Titanium alloy deformability improvement technique durong hot pressure shaping. USA patent № 2892742, grade 148-11,5; 1959.
Колачев Б.А., Носов В.К. Водородное пластифицирование при горячей деформации титановых сплавов. М.: Металлургия. 1986. 118 с.
Ovchinnikov A. Skvortsova S., Mamonov A., Yermakov E. Influence of hydrogen on plastic flow of the titanium and its alloys// Acta metallurgica Slovaca. 2017. V. 23. № 2. P. 122–134.
Попов А.А., Илларионов А.Г., Гриб С.В., Демаков С.Л., Карабаналов М.С., Елкина О.А. Фазовые и структурные превращения в сплаве на основе орторомбического алюминида титана // ФММ. 2008. Т. 106. № 4. С. 414–425.
Хаджиева О.Г., Илларионов А.Г., Попов А.А. Влияние старения на структуру и свойства закаленного сплава на основе орторомбического алюминида титана (Ti2AlNb) // ФММ. 2014. Т. 115. № 1. С. 14–22.
Хаджиева О.Г., Илларионов А.Г., Попов А.А., Гриб С.В. Влияние водорода на структуру закаленного сплава на основе орторомбического алюминида титана и фазовые превращения при последующем нагреве // ФММ. 2013. Т. 114. № 6. С. 577–583.
Илларионов А.Г., Хаджиева О.Г., Елкина О.А. Формирование структуры и свойств при старении закаленного сплава на основе орторомбического алюминида Ti2AlNb, легированного водородом // ФММ. 2018. Т. 119. № 8. С. 844–849.
Осинцева Н.О. Фазовые и структурные превращения в водородсодержащих сплавах системы Ti–Al–V // Автореферат диссертации на соискание ученой степени кандидата технических наук. М.: МАТИ. 2000. 23 с.
Крылов Б.С. Кинетика выделения водорода в вакууме из титановых материалов / Титан и его сплавы. Вып. 10. Исследование титановых сплавов. М: Изд-во АН ССР. 1963. С. 159–167.
Колачев Б.А., Садков В.В., Талалаев В.Д., Фишгойт А.В. Вакуумный отжиг титановых конструкций. М.: Машиностроение, 1991. 224 с.
Tang F., Awane T., Hagiwara M. Effect of compositional modification on Young’s modulus of Ti2AlNb-based alloy // Scripta Mater. 2002. V. 46(2). P. 143–147.
Дополнительные материалы отсутствуют.
Инструменты
Физика металлов и металловедение