Физика металлов и металловедение, 2019, T. 120, № 10, стр. 1109-1115
Механизмы сверхпластичекой деформации при повышенной скорости в сплаве системы Al–Mg–Zn–Fe–Ni–Zr–Sc
О. А. Яковцева a, А. Д. Котов a, М. Н. Ситкина a, А. В. Иржак b, А. В. Михайловская a, *
a НИТУ “МИСиС”
119049 Москва, Ленинский проспект, 4, Россия
b ИПТМ РАН
142432 Черноголовка, Московская обл., ул. Академика Осипьяна, 6, Россия
* E-mail: mihaylovskaya@misis.ru
Поступила в редакцию 20.03.2019
После доработки 09.04.2019
Принята к публикации 23.04.2019
Аннотация
Изучены микроструктура и действующие механизмы сверхпластической деформации в высокопрочном сплаве Al–7.0% Zn–2.7% Mg–1.0% Ni–0.9% Fe с малой добавкой Sc и Zr при температуре 480°С и скорости деформации 1 × 10–2 с–1 на стадии устойчивого течения в интервале значений истинной деформации от 1.1 до 1.6. По результатам анализа изменений структуры поверхности с предварительно нанесенными методом ионного травления маркерными сетками оценены вклады действующих механизмов сверхпластической деформации в общее удлинение. Выявлено, что зернограничное скольжение и внутризеренная деформация играют доминирующую роль, при этом вклад каждого из механизмов достигает 35–40%. Оставшиеся 25% обеспечивает механизм диффузионной ползучести/диффузионного массопереноса, что определено по размерам полосчатых зон, формирующихся на поверхности деформированного образца у поперечных границ зерен.
ВВЕДЕНИЕ
Феномен сверхпластичности применяется для формообразования материалов, трудно поддающихся деформации другими способами, или получения изделий очень сложной геометрии [1, 2]. Благодаря методу сверхпластической формовки, детали способны точно воспроизводить гравюру матрицы, при получении сложной формы из листового материала за одну технологическую операцию при определенных скорости и температуре деформации [3]. Cверхпластическая формовка промышленных листов алюминиевых сплавов (например, AA7475 [4], AA5083 [5]) реализуется при низких скоростях деформации – 10–4–10–3 с–1, и температурах 500–550°С. В связи с чем действующие механизмы деформации исследованы в большей степени в данном температурно-скоростном диапазоне [6].
Известны три действующие при сверхпластической деформации механизма, – зернограничное скольжение (ЗГС), дислокационная (ВДС) и диффузионная ползучесть (ДП) [1, 2, 7–9]. Большинство работ определяют зернограничное скольжение как основной механизм сверхпластической деформации, а остальные два считают аккомодационными. Показатели сверхпластичности зависят от структурных параметров сплава, их изменения при деформации, что в итоге влияет на вклады действующих при сверхпластической деформации механизмов. Одни авторы на близких по составу сплавах находят подтверждения тому, что дислокационная аккомодация является ключевой [10, 11], другие, что основную роль играет диффузионная ползучесть [5, 12–14]. При этом, низкий вклад ЗГС (около 10%) при доминировании диффузионной ползучести показывают сплавы системы Al–Mg–Mn–Cr [15, 16] и Al–Cu–Zr [12], в большинстве других сплавов преобладает ЗГС [2, 17]. Различия в результатах и их интерпретации может быть связано с применением отличающихся методик исследования, геометрии образцов, использования отличающихся по составу сплавов и разных температурно-скоростных и степенных условий деформации, которые могут влиять на действующие механизмы в большей или меньшей степени.
Для сверхпластической формовки производятся листы высокопрочного сплава АА7475, в котором формообразование возможно при скоростях ≤1 × 10–3 с–1. Основным механизмом сверхпластической деформации в сплаве AA7475 является зернограничное скольжение [2, 17], аккомодируемое согласно [18, 19] диффузионной ползучестью или согласно [20–22] внутризеренным дислокационным скольжением. При этом недостатком сплава является высокая остаточная пористость – 5–8%, которая считается результатом развитого ЗГС [17, 23, 24].
В недавно разработанных высокопрочных сплавах той же системы легирования с добавками никеля, железа, циркония и скандия, имеющих практически нерекристаллизованную структуру при нагреве до температур проявления сверхпластичности, сверхпластичное состояние достигается при скоростях деформации (5 × 10–3–10–1) с–1 при низкой остаточной пористости [25–28]. При этом вклады действующих механизмов и их изменение в процессе сверхпластической деформации при повышенных скоростях не изучены. При повышении скоростного диапазона проявления сверхпластичности роль действующих механизмов может меняться. Так как важнейшей технологической задачей в области сверхпластичности алюминиевых сплавов является увеличение скорости формовки, необходимо понимать, как меняются действующие механизмы при повышении скорости сверхпластической деформации. Таким образом, цель данной работы заключается в изучении вкладов действующих механизмов при сверхпластической деформации со скоростью 1 × × 10–2 с–1 в сплаве Al–Mg–Zn–Ni–Fe–Zr–Sc.
МАТЕРИАЛ И МЕТОДИКА ЭКСПЕРИМЕНТОВ
Исследуемый сплав имел следующий состав: Al–7.0% Zn–2.7% Mg–1.0% Fe–1.0% Ni–0.1% Sc–0.1% Zr [29]. Для приготовления сплава использовали алюминий марки A99, цинк марки Ц1С и магний марки Mг95, лигатуры Al–10% Fe, Al–20% Ni, Al–5% Zr, Al–5% Sc. Слиток получали в лабораторных условиях, отливая в медную водоохлаждаемую изложницу, обеспечивающую скорость охлаждения при литье около 15 К/мин. Слиток подвергали двухступенчатому гомогенизационному отжигу в печи Nabertherm N 30/65A с конвекцией по следующему режиму: 380 ± 1°C, 3 ч и 480 ± 1°C, 3 ч. Первая ступень отжига необходима для выделения дисперсных частиц Al3(Zr, Sc) и частичного растворения неравновесных фаз кристаллизационного происхождения. Вторая ступень позволяла провести сфероидизацию частиц фазы Al9FeNi. Для получения листа толщиной 1 мм гомогенизированный образец подвергали горячей прокатке при температуре 420°С с деформацией 85%, и затем прокатке при комнатной температуре с обжатием 70%. Исходную микроструктуру изучали после отжига при температуре 480°С в течение 20 мин, имитирующего нагрев и выдержку перед началом сверхпластической деформации.
Микроструктуру литых, термообработанных и холоднокатаных образцов и структуру поверхности образов после сверхпластической деформации изучали при помощи сканирующего электронного микроскопа (СЭМ) “TESCAN Vega 3 LMH”. Микрошлифы готовили при помощи механической шлифовки на абразивной (SiC) бумаге разной дисперсности и последующего полирования с использованием суспензии OP–S на основе оксида кремния на установке Struers LaboPol. Для выявления зеренной структуры дополнительно применяли оксидирование в 10% водном растворе фторборводородной кислоты при температуре примерно 10°С.
Зеренную структуру образцов изучали в поляризованном свете при помощи светового металлографического микроскопа “Neophot-30”.
Объектами электронно-микроскопического исследования при помощи просвечивающего электронного микроскопа JEOL JEM-2100 служили диски, которые готовили механическим шлифованием до толщины 0.22–0.25 мм, а затем электролитически утоняли на установке Struers TenuPol-5 до появления отверстия.
Для определения механизмов сверхпластической деформации, относительного удлинения и напряжения течения в состоянии сверхпластичности образцы подвергали одноосной деформации с постоянной скоростью 1 × 10–2 с–1 при температуре 480°С. Для данных экспериментов использовали разрывную машину Walter Bay LFM-100 и образцы с длиной рабочей части 14 мм и шириной 6 мм.
Для анализа вкладов механизмов сверхпластической деформации исследовали эволюцию поверхности полированных образцов с предварительно нанесенными маркерами. Маркерами служили сетки, которые наносили при помощи ионного микроскопа STRATA FIB-205 при ионном токе 1000 пА. Использовали два вида сеток: (1) грубую сетку – с шагом линий 5 мкм для измерения вклада ЗГС, и (2) микросетку – с шагом линий 1 мкм для определения вклада ВДС. Глубина линий составляла 0.2 мкм. Исходная деформация образца, на который наносили маркеры, составляла 1.10, далее образец деформировали последовательно до 1.35 и 1.60. Деформацию проводили в атмосфере аргона для предотвращения окисления поверхности. Для определения вкладов механизмов сверхпластической деформации анализировали смещения маркерных линий, вызванные деформацией [30].
РЕЗУЛЬТАТЫ ИССЛЕДОВАНИЯ И ИХ АНАЛИЗ
Литая структура сплава до и после прокатки представлена на рис. 1. В литой структуре помимо твердого раствора на основе алюминия наблюдали частицы эвтектического происхождения равновесной фазы, богатые Ni и Fe, неравновесной фазы, богатой Zn и Mg (рис. 1а), которая практически полностью растворялась при гомогенизации, а затем выделялась в более компактной форме при охлаждении с температуры отжига и горячей прокатки в виде вторичных кристаллов (рис. 1б). Термомеханическая обработка обеспечила относительно равномерное распределение частиц вторых фаз в алюминиевой матрице (рис. 1в). Средний размер частиц Al9FeNi составил 1.8 мкм, а их объемная доля – около 9%.
Рис. 1.
Микроструктура (СЭМ) сплава после литья (а), горячей прокатки (б), холодной прокатки и отжига 480°С, 20 мин (в).
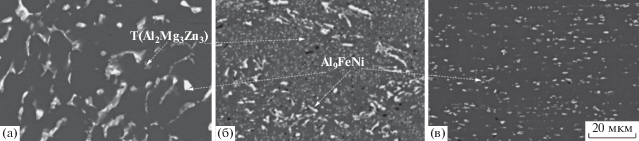
После нагрева и 20 мин выдержки при температуре 480°С в образцах наблюдали волокнистую зеренную структуру, отличающуюся от холоднодеформированного состояния наличием незначительного числа мелких, равноосных зерен. Такая структура является практически не рекристаллизованной и формируется в исследуемом сплаве благодаря дисперсоидам фазы Al3(Sc, Zr) с L12-структурой [31–33]. Мелкие равноосные рекристаллизованные зерна образуются благодаря крупным частицам фазы Al9FeNi, стимулирующим зародышеобразование при рекристаллизации [34–37].
Относительное удлинение при температуре 480°С и скорости деформации 1 × 10–2 с–1 составило ≈900% (2.2) (рис. 2). До деформации 0.4 наблюдали упрочнение на кривой напряжение-деформация с максимумом напряжения 10.8 МПа, при этом в сплаве сохранялась частично нерекристаллизованная структура. При деформации более 0.8 начиналась стадия устойчивого течения, напряжение течения уменьшалось до 9.5 МПа (рис. 2), а зеренная структура сплава становилась практически равноосной. Средний размер зерна составил 3.5 ± 0.2 мкм при деформации 1.1 и 3.9 ± ± 0.2 мкм при деформации 2.0. Очевидно, что высокотемпературная сверхпластическая деформация обеспечивает протекание динамической рекристаллизации [35], что приводит к формированию в образце равноосной микрозеренной структуры. Так же как и статическая, динамическая рекристаллизация, может ускоряться крупными частицами эвтектического происхождения, без которых высокоскоростная сверхпластичность невозможна в исследуемом сплаве [27].
Рис. 2.
Зависимость напряжения от истинной деформации при температуре 480°С и скорости деформации 1 × 10–2 с–1.
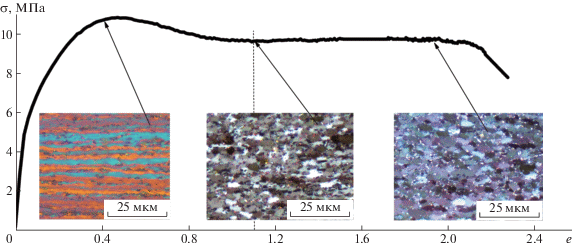
Для изучения механизмов сверхпластической деформации на установившейся стадии выбрали начальную деформацию 1.1, при которой структура полностью рекристаллизована (рис. 2). Анализ дислокационной структуры сплава после деформации 1.1 (рис. 3) выявил стенки дислокаций и отдельные дислокации в теле рекристаллизованных зерен. Частицы фазы Al3(Sc, Zr) имели средний размер 13 ± 1 нм и сохраняли L12-структуру, что подтверждается наличием сверхструктурных рефлексов на дифрактограмме (рис. 3г), т.е. частицы сохраняют кубическую структуру и когерентность матрице во время сверхпластической деформации. Размер некоторых дисперсоидов вблизи границ зерен достигал 23 нм (показаны стрелками на рис. 3б, 3в), они также сохраняли метастабильную L12 структуру. Частиц равновесной Al3(Sc, Zr) фазы с D023 типом структуры [38] не обнаружили.
Рис. 3.
Тонкая структура (ПЭМ) после деформации 1.10 при температуре 480°С и скорости деформации 1 × 10–2 с–1 в светлом поле (а, б), в темном поле (в) и связанная картина микродифракции; интенсивные рефлексы соответствуют Al, слабые рефлексы фазе Al3(Sc, Zr); ось зоны алюминиевой матрицы обозначена в правом нижнем углу (г).
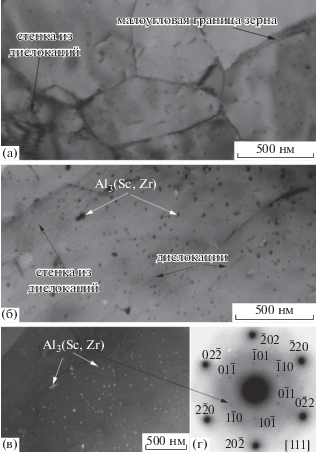
Оценку механизмов сверхпластической деформации проводили на образцах с нанесенной на полированную поверхность маркерной сеткой в интервале степени деформации 1.10–1.60 (рис. 4). На поверхности образца после деформации 1.10 + 0.25 (рис. 4) можно наблюдать характерный рельеф, видны смещения линий маркерной сетки, которые являются признаком зернограничного скольжения. Смещения увеличиваются при увеличении деформации до 1.10 + 0.50, также увеличивается угол разворота и число развернувшихся зерен. Происходит смена соседей зерен (рис. 4 зерна A, B, C, D), а также наблюдается значительная деформация некоторых зерен (зерно X на рис. 4). Наиболее значительная деформация тела зерен выявлена вблизи крупных частиц фазы Al9FeNi (показаны стрелками на рис. 4). В процессе деформации также появляются деформационные полосчатые зоны (обозначены ДП и показаны стрелками на рис. 4а, 4б), которые локализуются вдоль поперечных границ зерен, и ориентированы вдоль оси растяжения. Такие полосчатые зоны могут быть результатом действия механизма диффузионной ползучести [5, 12, 39]. Развороты зерен вероятнее всего являются следствием действия ЗГС [2, 40, 41], однако, согласно [42], разворот зерен также может быть результатом действия диффузионного массопереноса.
Рис. 4.
Эволюция поверхности образца с маркерной сеткой при температуре 480°С и скорости деформации 1 × 10–2 с–1 в режиме вторичных (а, б) и обратно-отраженных (в, г) электронов (СЭМ).
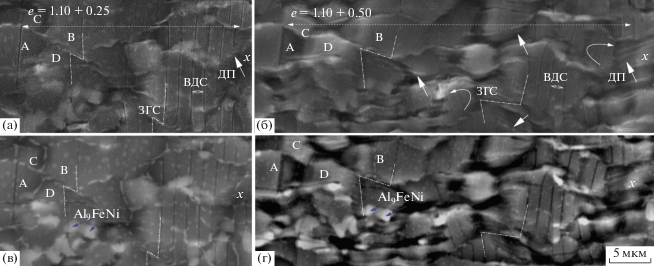
В табл. 1 представлена количественная оценка вкладов механизмов сверхпластической деформации. Как можно заметить, на установившейся стадии деформации численное значение вкладов слабо зависит от величины деформации. Вклад ЗГС и вклад ВДС близки и составляют примерно по 30–40%, а величина ДП, определенная по доле полосчатых зон составила оставшиеся ≈25%. Основное отличие высокоскоростной деформации исследуемого сплава от деформации сплава АА7475 сверхпластичного при на порядок меньшей скорости деформации, во-первых, в менее развитом ЗГС. На стадии установившегося течения в сплаве АА7475 вклад ЗГС достигал 60% [17], что практически в два раза больше, чем получено в исследуемом сплаве. Пониженное ЗГС может быть вызвано присутствием дисперсных L12-частиц, способных сдерживать перемещение границ зерен. И, во-вторых, в исследуемом сплаве значительно больше вклад внутризеренной деформации. В сплаве АА7475 деформации тела зерен не было обнаружено до значений удлинения близких к разрушению [17]. Внутризеренное дислокационное скольжение может как аккомодировать ЗГС, так и обеспечивать собственный существенный вклад в общее удлинение. Важно отметить, что сплав сохраняет практически равноосную структуру до разрушения, при этом деформация тела зерен существенна на установившейся стадии. Это означает, что сверхпластическое течение в исследуемом сплаве при повышенных скоростях деформации должно сопровождаться динамической рекристаллизацией сохраняющей равноосную структуру. Увеличение доли субзерен – динамическая полигонизация, было отмечено ранее как в аналогичных исследуемому сплавах [25, 43], так и в других сплавах на основе алюминия [15, 44], что может свидетельствовать о протекании динамической рекристаллизации в том числе по непрерывному механизму через увеличение разориентировки малоугловых границ до высокоугловых [35].
Таблица 1.
Вклады механизмов сверхпластической деформации
Деформа-ция e | Зернограничное скольжение (ЗГС) | Внутризеренная деформация (ВДС) | Деформационные зоны (ДЗ) | Макс. угол разворота, град | |||
---|---|---|---|---|---|---|---|
eЗГС | вклад, γЗГС, % | eВДС | вклад γВДС, % | eДЗ | вклад γДЗ, % | ||
1.1 + 0.25 | 0.076 ± 0.03 | 31 ± 12 | 0.09 ± 0.03 | 36 ± 12 | 0.06 ± 0.02 | 24 ± 8 | 30 |
1.1 + 0.50 | 0.183 ± 0.08 | 37 ± 16 | 0.09 ± 0.04 | 41 ± 8 | 0.13 ± 0.06 | 25 ± 12 | 35 |
В процессе деформации исследуемого сплава развивается пористость. Объемная доля пор не превышает 2% в образце, доведенном до разрушения. Полученное значение пористости примерно в 3 раза ниже, чем в сплаве AA7475 [17, 23, 24]. Поры выявлены около эвтектических частиц и в свободных от крупных частиц тройных стыках зерен. Таким образом, причиной пористости могут стать как отдельные неравноосные включения эвтектического происхождения, так и зернограничное скольжение. При этом, низкую остаточную пористость при повышенной скорости деформации в исследуемом сплаве можно объяснить пониженным вкладом ЗГС и значительной ролью дислокационного внутризеренного скольжения, механизма, который способствует протеканию динамической рекристаллизации, обеспечивая устойчивое продолжительное течение при повышенных скоростях деформации. Отметим, что аналогичный эффект, снижения пористости при малом вкладе зернограничного скольжения был обнаружен в сплавах системы Al–Mg–Mn–Cr, в которых предположено, что слабое развитие ЗГС может быть следствием присутствия по границам зерен дисперсоидов Al6(MnCr) [45, 46].
ВЫВОДЫ
1. Исследованы особенности сверхпластичеcкой деформации и эволюции структуры в высокопрочном сплаве Al–7.0% Zn–2.7% Mg–1.0% Fe–1.0% Ni с малой добавкой Zr и Sc на установившейся стадии деформации. Сплав с добавками эвтектикообразующих (Fe, Ni) и дисперсоидообразующих (Zr, Sc) элементов, обеспечивающих исходную перед началом деформации практически нерекристаллизованную структуру состоящую преимущественно из субзерен, демонстрирует относительные удлинения 900% (е = 2.2) при температуре 480°С и скорости деформации 1 × 10–2 с–1.
2. Сплав показывает относительно низкое значение остаточной пористости, не превышающее 2%, при сохранении среднего размера зерна менее 4 мкм до разрушения.
3. На установившейся стадии деформации при сформированной полностью рекристаллизованной структуре изменения механизмов деформации в интервале истинной деформации 1.1–1.6 не наблюдали. Доминирующими механизмами являются зернограничное скольжение и внутризеренная деформация, обеспечивающие по ≈35–40% вклада в общее удлинение.
4. Вклад диффузионной ползучести, определенный по полосчатым зонам, формирующимся на поверхности образца при деформации, составил около 25%. Таким образом, при равном соотношении внутризеренной деформации и зернограничного скольжения, сопровождающихся диффузионной ползучестью и непрерывной динамической рекристаллизацией, высокопрочные сплавы способны к высокоскоростной сверхпластической деформации с низкой остаточной пористостью.
Работа выполнена при финансовой поддержке Российского научного фонда по гранту № 17-79-20426.
Список литературы
Pilling J., Ridley N. Superplasticity in Crystalline Solids // The Institute of Metals. London. 1989. 214 p.
Nieh T.G., Wadsworth J., Sherby. O.D. Superplasticity in metals and ceramics // Cambridge, N.Y., 1997. 273 p.
Wood R.D., Bonet J. A review of the numerical analysis of superplastic forming // J. Mater. Proces. Techn. 1996. V. 60. P. 45–53.
Buschow K.H.J., Cahn R.W., Flemings M.C., Ilschner B., Kramer E.J., Mahajan S., Veyssière P. Encyclopedia of Materials: Science and Technology (Second Edition), Chapter: Koehler W., Plege B., Sahm K.F., Metal Forming: Specialized Procedures for the Aircraft Industry. Oxford. Elsevier. 2001. P. 10388(5427–5433).
Rust M.A., Todd R.I. Surface studies of Region II superplasticity of AA5083 in shear: Confirmation of diffusion creep, grain neighbor switching and absence of dislocation activity // Acta Mater. 2011. V. 59. P. 5159–5170.
Dudina D.V., Mishra R.S., Mukherjee A.K. Superplasticity: Where the deformation mechanism is also an industry. In: Reference Module in Materials Science and Materials Engineering. Hashmi S. (Ed.). Oxford: Elsevier, 2016. P. 1–8.
Кайбышев О.А. Сверхпластичность промышленных сплавов. М.: Металлургия, 1984. 264 с.
Кайбышев О.А. Пластичность и сверхпластичность металлов. М.: Металлургия, 1975. 280 с.
Новиков И.И., Портной В.К. Особенности сверхпластической деформации некоторых алюминиевых сплавов // Изв. вузов. Цветная металлургия. 2001. № 4. С. 4–11.
Bate P.S., Humphreys F.J., Ridley N., Zhang B. Microstructure and texture evolution in the tension of superplastic Al–6Cu–0.4Zr // Acta Mater. 2005. V. 53. № 10. P. 3059–3069.
Musin F., Kaibyshev R., Motohashi Y., Itoh G. High strain rate superplasticity in a commercial Al–Mg–Sc alloy // Scripta Mater. 2004. V. 50. № 4. P. 511–516.
Sotoudeh K., Bate P.S. Diffusion creep and superplasticity in aluminium alloys // Acta Mater. 2010. V. 58. № 6. P. 1909–1920.
Ashby M.F., Verrall R.A. Diffusion accommodated flow and Superplasticity // Acta Metall., 1973. V. 21. P. 149–163.
Mukherjee A.K. The rate controlling mechanism in Superplasticity // Mater. Sci. Eng. 1971. V. 8. P. 83–89.
Mikhaylovskaya A.V., Yakovtseva O.A., Golovin I.S., Pozdniakov A.V., Portnoy V.K. Superplastic deformation mechanisms in fine-grained Al–Mg based alloys // Mater. Sci. Eng. A. 2015. V. 627. P. 31–41.
Yakovtseva O.A., Mikhaylovskaya A.V., Levchenko V.S., Irzhak A.V., Portnoi V.K. Study of the Acting Mechanisms of Superplastic Deformation in Al–Mg–Mn-Based Alloys. // Phys. Met. Metal. 2015. V. 116. № 9. P. 908–916.
Mikhaylovskaya A.V., Yakovtseva O.A., Sitkina M.N., Kotov A.D., Irzhak A.V., Krymskiy S.V., Portnoy V.K. Comparison between superplastic deformation mechanisms at primary and steady stages of the fine grain AA7475 aluminium alloy // Mater. Sci. Eng. A. 2018. V. 718. P. 277–286.
Langdon G.T., Grain boundary sliding revisited: Developments in sliding over four decades // J. Mat. Sci. 2006. V. 41. P. 597–609.
Hamilton C.H., Bampton C.C., Paton N.E. Superplasticity in high strength aluminium alloys // Proceedings of AIME Met. Soc. Conference on Superplastic Forming of Structural Alloys, San Diego, 1982. 173 p.
Sahraoui T., Hadji M., Bacha N., Badji R. Superplastic deformation behavior of 7075 aluminum alloy // J. Mater. Eng. Performance. 2003. V. 12. P. 398–401.
Liu J., Chakrabarti D.J. Grain structure and microstructure evolution during superplastic forming of a high strength Al–Zn–Mg–Cu alloy // Acta Mater. 1996. V. 44. P. 4641–4661.
Adabbo H.E., Gonzalez-Doncel G., Ruano O.A., Belzunce J.M., Sherby O.D. Strain hardening during superplastic deformation of Al-7475 alloy // Mat. Research Society. 1989. V. 3. P. 587–594.
Chen Z.P., Thomson P.F. A study of post-form static and fatigue properties of superplastic 7475-SPF and 5083-SPF aluminium alloys // J. Mat. Proces. Tech. 2004. V. 148. № 2. P. 204–219.
Chen C., Tan M. Cavity growth and filament formation of superplastically deformed Al 7475 Alloy//Mater. Sci. Eng. A. 2001. V. 298. P. 235–244.
Mikhaylovskaya A.V., Kotov A.D., Pozdniakov A.V., Portnoy V.K. A high-strength aluminium-based alloy with advanced superplasticity // J. Alloys and Compounds. 2014. V. 599. P. 139–144.
Mikhaylovskaya A.V., Yakovtseva O.A., Cheverikin V.V., Kotov A.D., Portnoy V.K. Superplastic behaviour of Al–Mg–Zn–Zr–Sc-based alloys at high strain rates // Mater. Sci. Eng. A. 2016. V. 659. P. 225–233.
Kotov A.D., Mikhaylovskaya A.V., Portnoy V.K. Effect of the Solid-Solution Composition on the Superplasticity Characteristics of Al–Zn–Mg–Cu–Ni–Zr Alloys // Phys. Met. Metal. 2014. V. 115. № 7. P. 730–735.
Kotov A.D., Mikhaylovskaya A.V., Borisov A.A., Yakovtseva O.A., Portnoy V.K // High-strain-rate superplasticity of the Al–Zn–Mg–Cu alloys with Fe and Ni // Phys. Met. Metal. 2017. V. 118. № 9. P. 913–921.
Cheverikin V.V., Belov N.A., Eskin D.G., Turchin A.N. Effect of Al3Ni and Mg2Si eutectic phases on casting properties and hardening of An Al–7% Zn–3% Mg alloy // Mater. Sci. Forum. 2006. V. 519–521. P. 413–418.
Portnoy V.K., Novikov I.I. Evaluation of grain boundary sliding contribution to the total strain during superplastic deformation // Scr. Mater. 1998. V. 40. P. 39–43.
Rout P.K., Ghosh M.M., Ghosh K.S. Microstructural, mechanical and electro- chemical behavior of a7017Al–Zn–Mg alloy of different tempers // Mater. Charact. 2015. V. 104. P. 49–60.
Filatov Yu.A., Yelagin V.I., Zakharov V.V. New Al–Mg–Sc alloys // Mater. Sci. Eng. A. 2000. V. 280. P. 97–101.
Zolotorevskiy V.S., Dobrojinskaja R.I., Cheverikin V.V., Khamnagdaeva E.A., Pozdniakov A.V., Levchenko V.S., Besogonova E.S. Evolution of structure and mechanical properties of Al–4.7Mg–0.32Mn–0.21Sc–0.09Zr alloy sheets after accumulated deformation during rolling // The Phys. Met. Metal. 2016. V. 117 P. 1163–1169.
Humphreys F.J. Recrystallization mechanisms in two-phase alloys // Metal Science. 1979. V. 13. P. 136–145.
Humphreys F.J., Hatherly M. Recrystallization and related annealing phenomena. 2nd ed. Oxford. Elsevier, 2004. 658 p.
Pozdniakov A.V., Aytmagambetov A.A., Makhov S.V., Napalkov V.I. Effect of impurities of Fe and Si on the structure and strengthening upon annealing of the Al–0.2% Zr–0.1% Sc alloys with and without Y additive. // Phys. Met. Metal. 2017. V. 118. P. 479–484.
Kotov A.D., Mikhaylovskaya A.V., Golovin I.S., Portnoy V.K. Fine-grained structure and superplasticity of Al–Cu–Mg–Fe–Ni alloys // Mater. Sci. Forum. 2013. V. 735. P. 55–60.
Van Dalen M.E., Gyger T, Dunand D.C., Seidman D.N. Effects of Yb and Zr microalloying additions on the microstructure and mechanical properties of dilute Al–Sc alloys // Acta Mater. 2011. V. 59. P. 7615–7626.
Новиков И.И., Портной В.К. Сверхпластичность сплавов с ультрамелким зерном. М.: Металлургия, 1981. 168 с.
Chen C.L., Tan M.J. Effect of grain boundary character distribution (GBCD) on the cavitation behaviour during superplastic deformation of Al 7475 // Mater. Sci. Eng. 2002. V. 338. P. 243–252.
Masuda H., Tobe H., Hara T., Sato E. Three-dimensional characterization of superplastic grain boundary sliding inside Al–Zn–Mg–Cu alloy sheet // Scr. Mat. 2019. V. 164. P. 82–85.
Ford J.M., Wheeler J., Movchan A.B. Computer simulation of grain-boundary diffusion creep // Acta Mat. 2002. V. 50. P. 3941–3955.
Blackwell P.L., Bate P.S., Superplastic Deformation without Relative Grain Translation, Mater. Sci. Forum. 1999. V. 304–306. P. 189–194.
Tan J.C., Tan M.J., Superplasticity and grain boundary sliding characteristics in two stage deformation of Mg–3Al–1Zn alloy sheet, Mater. Sci. Eng. A. 2003. V. 339. P. 124–132.
Portnoy V.K., Rylov D.S., Levchenko V.S., Mikhaylovskaya A.V. The influence of chromium on the structure and superplasticity of Al–Mg–Mn alloys // JAlCom. 2013. V. 581. P. 313–317.
Kishchik A.A., Mikhaylovskaya A.V., Levchenko V.S., Portnoy V.K. Formation of microstructure and the superplasticity of Al–Mg-based alloys // Phys. Met. Metal. 2017. V. 118. P. 96–103.
Дополнительные материалы отсутствуют.
Инструменты
Физика металлов и металловедение