Физика металлов и металловедение, 2019, T. 120, № 11, стр. 1204-1209
Структурообразование и свойства эвтектического силумина, полученного селективным лазерным сплавлением
И. Г. Бродова a, b, *, О. А. Чикова b, c, А. Н. Петрова a, А. Г. Меркушев b
a Институт физики металлов УрО РАН им. М.Н. Михеева
620108 Екатеринбург, ул. С. Ковалевской, 18, Россия
b Уральский федеральный университет им. Б.Н. Ельцина
620002 Екатеринбург, ул. Мира, 19, Россия
c Уральский государственный педагогический университет
620017 Екатеринбург, пр. Космонавтов, 26, Россия
* E-mail: brodova@imp.uran.ru
Поступила в редакцию 16.05.2019
После доработки 04.06.2019
Принята к публикации 07.06.2019
Аннотация
Методом селективного лазерного сплавления, используя в качестве исходного материала опытный порошок состава АКД-12, синтезирован Al–Si сплав эвтектического состава. На основании электронно-микроскопических исследований проведена аттестация микроструктуры СЛС сплава с EDS-картированием элементов (Al и Si). Установлено, что основной структурной составляющей является Al-твердый раствор, имеющий ячеисто-дендритное строение (средний размер ячеек ~500 нм). Фаза Si, входящая в состав эвтектики, расположена по границам в виде округлых кристаллов, размером порядка десятка нанометров. Приведены результаты измерения механических и наномеханических свойств, показывающие конкурентоспособность использования опытного порошка.
ВВЕДЕНИЕ
К настоящему времени селективное лазерное сплавление (CЛC) алюминиевых сплавов широко изучается в России и за рубежом и обсуждаются вопросы, связанные с использованием аддитивных технологий вместо традиционных способов получения деталей из алюминиевых сплавов для нужд авиакосмической отрасли и машиностроения [1–4]. Наиболее подробно из литейных сплавов на основе Al исследованы Al–Si-сплавы как материалы, которые обладают высокой удельной прочностью, хорошими трибологическими свойствами и коррозионной стойкостью [3, 5–9], широко используются на практике. Как отмечается авторами [2, 3, 5–11], высокий уровень механических характеристик обусловлен модифицированной микроструктурой СЛС сплавов, сочетающей дисперсную матрицу с ультрамелкими частицами, входящими в состав (Al + Si)-эвтектики. Сплав Al–12 мас. % Si имеет эвтектический состав и наиболее пригоден для СЛС-производства из-за малого теплового расширения. Согласно [12], в СЛС-сплаве данного состава наблюдается анизотропия свойств в продольном и поперечном сечениях изделий: предел текучести изменяется от 225 до 263 МПа, а предел прочности от 260 до 365 МПа. Причиной анизотропии, по мнению авторов, является различие в плотности материала, что связано с развитием пористости. Газовая пористость является один из наиболее распространенных дефектов в СЛС алюминиевых сплавах, она может оказывать сильное влияние на усталостную прочность. Установлено, что газовые поры с объемной долей 0.2–1.6% и средним размером 20–55 мкм инициируют разрушение образцов после испытания на усталость [13, 14].
Другим часто встречающимся дефектом в СЛС-изделиях являются горячие трещины, устранить которые можно с помощью оптимизации параметров работы лазера [15], а также подбирая сплавы, не склонные к образованию горячих трещин [9]. Благодаря хорошей жидкотекучести и низкой склонности к образованию горячих трещин, в качестве наиболее распространенного материала для СЛС-изделий используют силумин системы легирования Al–Si–Mg. Высокий уровень механических свойств этого материала обусловлен твердорастворным упрочнением матрицы [12, 16–20]. В частности, в СЛС-состоянии без термической обработки предел прочности сплава составил 330–450 МПа [17, 19].
Важную роль в получении качественных и плотных отливок играют характеристики порошков, используемых для СЛС-силуминов, так как наличие оксидной пленки на поверхности порошков крайне нежелательно, снижает их смачиваемость расплавом и приводит к формированию пористого слоя [21]. В настоящее время в России для технологии СЛС-сплава Al–12% Si используют порошок импортного производства, стоимость которого весьма высока. В Региональном инжиниринговом центре Уральского федерального университета (УрФУ) сконструирована и изготовлена установка газового распыления расплавов металлов УР-9, на которой был получен порошок сплава Al–12% Si (аналог марки АКД-12). В работе [22] описан положительный опыт апробации полученного порошка в качестве сырья для изготовления деталей методом СЛС с целью определения возможности замены иностранных аналогов.
Данная работа является продолжением этих исследований и посвящена изучению тонкой структуры и свойств эвтектического силумина, синтезированного методом СЛС из опытного порошка.
МАТЕРИАЛЫ И ЭКСПЕРИМЕНТАЛЬНЫЕ МЕТОДЫ ИССЛЕДОВАНИЯ
Из опытного порошка силумина Al–12% Si, синтезированного в среде высокочистого азота на установке УР-9, методом селективного лазерного сплавления были получены образцы в виде цилиндров диаметром 15 мм и длиной 80 мм. Химический состав СЛС-образцов приведен в табл. 1. Установка селективного лазерного сплавления EOSINT M 280 оснащена волоконным лазером с длиной волны 1.06 мкм и максимальной номинальной мощностью 400 Вт. В процессе СЛС в рабочей камере поддерживали атмосферу аргона высокой чистоты для предотвращения окислению металла. Скорость сканирования и мощность лазера составляли 2000 мм/с и 400 Вт соответственно. Толщина слоя порошка была фиксирована – 30 мкм. Температура подложки во всех опытах – 35°С. Термическую обработку полученных СЛС-образцов не проводили.
Таблица 1.
Химический состав СЛС образцов (EDS-анализ)
Химический элемент | Вес. % | Ат. % |
---|---|---|
O | 9.48 | 15.08 |
Al | 78.37 | 73.91 |
Si | 12.15 | 11.01 |
Из СЛС-цилиндров для проведения механических испытаний на растяжение были изготовлены стандартные цилиндрические образцы с длиной рабочей части 35 мм и диаметром 4.8 мм (ГОСТ 1497–84). Ось образца совпадала с вертикальным направлением печати. Испытания СЛС-образцов на растяжение проводили на испытательной машине Shimadzu AG-50kNXD со скоростью растяжения V = 10 мм/мин. Определяли условный предел текучести (МПа), предел прочности (МПа) и относительное удлинение (%).
Исследование микроструктуры образцов проводили методами металлографического анализа, используя световой микроскоп “Neophot-32” с системой автоматического анализа изображения SIAMS 700 и аналитический автоэмиссионный растровый электронный микроскоп Merlin (CarlZeiss, Германия). Визуализацию морфологии структурных составляющих выполняли с использованием детектора вторичных электронов Эвернхарта-Торнли, а обработку и анализ полученных данных – с помощью программного средства SmartSEM (CarlZeiss, Германия). Измерения наномеханических свойств – твердости H и модуля упругости Е проводили на сканирующем нанотвердомере “НаноСкан-4D” в субмикробъеме размером 900 × 900 мкм с шагом индентирования 30 мкм. Таким образом, был получен массив из 300 значений, по которым далее построены гистограммы. Для измерения использовали динамический режим индентирования с постоянной скоростью нарастания силы. Время нагружения до достижения максимальной силы 50 мН составляло 10 с. Время выдержки материала под максимальной нагрузкой 2 с.
РЕЗУЛЬТАТЫ И ОБСУЖДЕНИЕ
Структура
На рис. 1. представлены оптические изображения типичной структуры синтезированного сплава в продольном и поперечном сечениях образца, на которых видны следы прохождения луча лазера (melt pools). На рис. 1г показано, что в разных зонах “ванны расплава” размер структурных составляющих меняется, т.е. на границах формируется несколько слоев с отличной от центральной ячеисто-дендритной структурой.
Рис. 1.
Микроструктура СЛС-образца (оптическая микроскопия): а, б – продольное сечение; в, г – поперечное сечение.
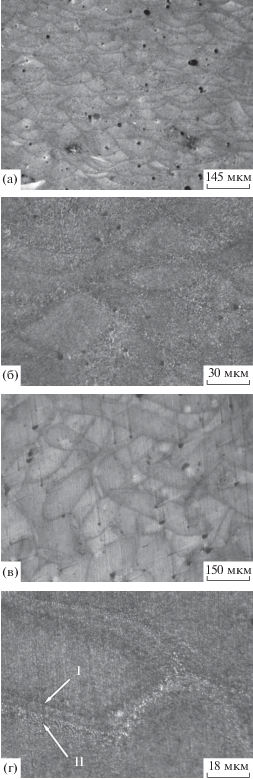
Появление таких структурных зон обусловлено разным перегревом и скоростью кристаллизации расплава в центре и по краям ванны. Так, вследствие высоких температурных градиентов, возникающих при лазерном плавлении, температура расплава в центре ванны выше, в результате происходит растворение (дезактивация) центров кристаллизации, и образуется более грубая, чем в слое I, структура (рис. 1г). Кроме того, из-за двойного переплава материала на границе двух ванн (в зоне термического влияния) возникает зона с более крупной, чем в центре, структурой (слой II, рис. 1г).
Результаты исследования микроструктуры СЛС-образца средствами растровой электронной микроскопии приведены на рис. 2. Рисунок 2а иллюстрирует изображение микроструктуры в обратно отраженных электронах, а на EDS-картах можно увидеть две структурные составляющие – Al‑твердый раствор (рис. 2б) и Si (рис. 2в). Видно, что Al-твердый раствор кристаллизуется в виде дендритоподобных ячеек размером ~500 нм, а Si-фаза, входящая в состав эвтектики (Al + Si), имеет преимущественно округлую форму и расположена по их границам. Формирование таких структур при лазерном плавлении силуминов неоднократно отмечали в работах [5–8], причем размер и форма кристаллов кремния меняется по сечению образца в зависимости от температурно-скоростных режимов затвердевания, а самые крупные кристаллы кремния формируются в слое термического влияния.
Рис. 2.
Микроструктура СЛС-образца (растровая электронная микроскопия и EDS-анализ): а – изображение в обратно отраженных электронах, распределение элементов; б – Al, в – Si.
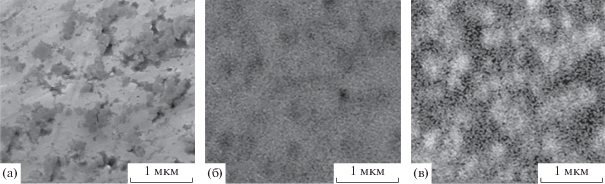
В структуре СЛС-сплава (рис. 1, 2), было обнаружено большое число пор сферической и серповидной формы с размерами от нескольких десятков до нескольких сотен микрометров. Наиболее типичной причиной их появления, как указано выше, является окисная пленка на поверхности порошка. Как следует из данных табл. 1, в составе порошка обнаружено большое количество кислорода. Согласно [13], сферическая пористость может иметь как эндогенное, так и экзогенное происхождение и возникает при свободном растекании металла, при этом оксид Al2O3 частично переходит в летучий субокисел Al2O. Поры серповидной морфологии образуются в результате неполного разрушения оксидной пленки на частице порошка, и, соответственно, затрудняют ее растекание, препятствуя формированию бездефектного материала.
Анализируя морфологические и размерные особенности СЛС-структуры, можно отметить ее подобие структурам Al–Si-композиций доэвтектического состава, полученных быстрой закалкой жидкого силумина Al–12% Si [19, 23]. Так как при СЛС-технологии скорость охлаждения расплава может достигать 105 град/с, то процесс кристаллизации осуществляется в неравновесных условиях, и формируются метастабильные субмикрокристаллические структуры. Кроме высокой скорости охлаждения расплава, кристаллизации эвтектического сплава по доэвтектическому механизму также способствует высокий перегрев расплава над температурой ликвидуса [23]. Как отмечалось в [19], основным отличием СЛС и быстрозакаленных алюминиевых сплавов при схожей морфологии их структур является разная степень легирования Al-твердого раствора, но для исследованного сплава этот фактор не играет большой роли из-за слабой растворимости Si в Al и отсутствия других легирующих добавок.
Механические свойства
Учитывая, что размер ячеек-дендритов Al‑твердого раствора не превышает 500 нм, для аттестации его свойств и измерения твердости и модуля упругости был применен локальный метод наноиндентирования. Результаты измерений нанотвердости H (ГПа) и модуля упругости E (ГПа) ячеек Al-твердого раствора представлены в виде гистограмм на рис. 3, где N – количество определенных значений в выборке из трехсот измерений.
Плотность распределения вероятностей величин Н и Е аппроксимированы функцией Гаусса. Получены средние значения нанотвердости и модуля упругости: Н = 2.3 ± 0.4 ГПа и Е = 90 ± 31.3 ГПа. Данные результаты согласуются с литературными данными по нанотвердости СЛС-сплава AlSi7Mg (H = 1.0–3.0 ГПа) и СЛС-сплава AlSi10Mg (H = = 1.5–2.5 ГПа) [24, 25]. Приведенные в [26] значения модуля упругости E = 62.4 ГПа для СЛС-сплава AlSi10Mg также согласуются в пределах погрешности с данными настоящей работы.
Результаты механических испытаний СЛС-образцов приведены в табл. 2, где σ0.2 – условный предел текучести, σВ – предел прочности, δ – относительное удлинение. Представляет интерес сравнить механические свойства сплава, полученного из опытного порошка, с литым состоянием, а также с другими СЛС-сплавами этого же химического состава [5, 6, 8] (табл. 2).
Сравнение механических характеристик сплава, синтезированного из опытного порошка, и литого сплава Al–12% Si [8] при близких значениях предела текучести и относительного удлинения демонстрирует повышенный в 1.7 раза предел прочности. Рост прочности обусловлен диспергированием структурных составляющих сплава и сменой формы роста кристаллов эвтектического кремния с пластинчатой на округлую [23]. Анализируя результаты, полученные авторами [5, 6, 8], можно отметить, что образцы, синтезированные из опытного порошка, имеют тот же запас прочности, более высокую пластичность и заниженные в 2 раза значения условного предела текучести. Условный предел текучести является структурно-чувствительной характеристикой, поэтому появление дефектов (например, пор и несплошностей) снижает величину напряжения перехода от упругой к пластической деформации, увеличивая деформационную способность материала и его пластичность. Если считать, что в условиях проведения экспериментов по лазерному сплавлению эвтектического силумина формируются структуры, подобные указанным на рис. 1, 2, и вклады зернограничного, дисперсного и твердорастворного упрочнения в σ0.2 одинаковы, то возможной причиной указанных несоответствий является разная пористость материала.
ЗАКЛЮЧЕНИЕ
Методом селективного лазерного сплавления из опытного порошка синтезированы образцы эвтектического силумина Al–12% Si. На основании электронно-микроскопических исследований проведена аттестация микроструктуры СЛС-сплава с EDS-картированием элементов (Al и Si), и установлено, что основной структурной составляющей является Al-твердый раствор, имеющий ячеисто-дендритное строение (средний размер ячеек ~500 нм). Фаза Si, входящая в состав эвтектики, расположена по границам в виде округлых кристаллов, размером порядка десятка нанометров. Характер кристаллизации эвтектического сплава по доэвтектическому механизму свидетельствует о неравновесных условиях затвердевания при лазерном плавлении, в частности, высокой скорости охлаждения и сильном перегреве расплава над температурой ликвидуса.
Сформированная при термо-скоростных параметрах процесса селективного лазерного сплавления тонкая микроструктура обеспечивает высокую прочность и способность к деформационному упрочнению материала за счет действия дислокационного механизма упрочнения Орована, вследствие огибания дисперсных эвтектических фаз на границе ячеек движущимися дислокациями.
Методами наноидентирования определены механические характеристики сплава, синтезированного из опытного порошка (нанотвердость и модуль упругости), а также измерены предел прочности σв = 357 МПа и относительное удлинение δ = 10.8%. Результаты показали хорошее совпадение с соответствующими характеристиками СЛС-силуминов, полученных иностранными производителями, что свидетельствует о перспективности использования опытного порошка в качестве исходного сырья для СЛС-процесса. Дополнительным резервом повышения механических свойств СЛС-изделий из опытного порошка может быть снижение их пористости за счет повышения энергетической нагрузки лазера.
Работа выполнена в рамках государственного задания МИНОБРНАУКИ России (тема “Структура”, АААА-А18-118020190116-6).
Список литературы
Каблов Е.Н. Аддитивные технологии – доминанта национальной технологической инициативы // Интеллект и технологии. 2015. № 2(11). С. 52–55.
Рябов Д.К., Антипов В.В., Королев В.А., Медведев П.Н. Влияние технологических факторов на структуру и свойства силумина, полученного с использованием технологии селективного лазерного синтеза // Авиационные материалы и технологии. 2016. № S1. С. 44–51.
Дынин Н.В., Иванова А.О., Хасиков Д.В., Оглодков М.С. Селективное лазерное сплавление алюминиевых сплавов // Электронный научный журн. Труды ВИАМ. 2017. № 8(56).https://doi.org/10.18577/2307-6046-2017-0-8-2-2
Казанцева Н.В., Ежов И.В., Виноградова Н.И., Ильиных М.В., Фефелов А.С., Давыдов Д.И., Оленева О.А., Карабаналов М.С. Влияние геометрии построения образца в методе селективного лазерного сплавления на микроструктуру и прочностные характеристики сплава Ti–6Al–4V // ФММ. 2018. Т. 119. № 11. С. 1138–1164.
Li X.P., Wanga X.J., Saunders M., Suvorova A., Zhang L.C., Liu Y.J., Fang M.H., Huang Z.H., Sercombe T.B. A selective laser melting and solution heat treatment refined Al–12Si alloy with a controllable ultrafine eutectic microstructure and 25% tensile ductility // Acta Mater. 2015. V. 95. P. 74–82.
Prashanth K.G., Scudino S., Klauss H.J., Surreddi K.B., Löber L., Wang Z., Chaubey A.K., Kühn U., Eckert J. Microstructure and mechanical properties of Al–12Si produced by selective laser melting: Effect of heat treatment // Mater. Sci. Eng. A. 2014. V. 590. P. 153–160.
Kang N., Coddet P., Dembinski L., Liao H., Coddet C. Microstructure and strength analysis of eutectic Al–Si alloy in-situ manufactured using selective laser melting from elemental powder mixture // J. Alloys Comp. 2017. V. 691. P. 316–322.
Suryawanshi J., Prashanth K.G., Scudino S., Eckert J., Prakash Om., Ramamurty U. Simultaneous enhancements of strength and toughness in an Al–12Si alloy synthesized using selective laser melting // Acta Mater. 2015. V. 115. P. 285–294.
Maskery I., Aboulkhair N.T., Aremu A.O., Tuck C.J., Ashcroft I.A., Wildman R.D., Hague R.J.M. A mechanical property evaluation of graded density Al–Si10–Mg lattice structures manufactured by selective laser melting // Mater. Sci. Eng. A. 2016. V. 670. P. 264–274.
Samuel A.M., Garza-Elizondo G.H., Doty H.W., Samuel F.H. Role of modification and melt thermal treatment processes on the microstructure and tensile properties of Al–Si alloys // Mater. Design. V. 80. 2015. P. 99–108.
Kimura T. Effect of silicon content on densification, mechanical and thermal properties of Al–xSi binary alloys fabricated using selective laser melting // Mater. Sci. Eng.: A. 2017. V. 682. P. 593–602.
Zhao J., Easton M., Qian M., Leary M., Brandt M. Effect of building direction on porosity and fatigue life of selective laser melted AlSi12Mg alloy // Mater. Sci. Eng. A. 2018. V. 729. P. 76–85.
Khairallah S.A., Anderson A.T., Rubenchik A., King W.E. Laser powder-bed fusion additive manufacturing: Physics of complex melt flow and formation mechanisms of pores, spatter, and denudation zones // Acta Mater. 2016. V. 108. P. 36–45.
Galy C., Le Guen E., Lacoste E., Arvieu C. Main defects observed in aluminum alloy parts produced by SLM: From causes to consequences // Additive Manufacturing. 2018. V. 22. P. 165–175.
Rashida R., Masooda S.H., Ruana D., Palanisamya S., Rahman Rashida R.A., Elambasseril J., Brandt M. Effect of energy per layer on the anisotropy of selective laser melted AlSi12 aluminium alloy // Additive Manufacturing. 2018. V. 22. P. 426–429.
Fousová M., Dvorský D., Michalcová A., Vojtěcha D. Changes in the microstructure and mechanical properties of additively manufactured AlSi10Mg alloy after exposure to elevated temperatures // Mater. Characterization. 2018. V. 137. P. 119–126.
Chen B., Moon S.K., Yao X., Bi G., Shen J., Umeda J., Kondoh K. Strength and strain hardening of a selective laser melted AlSi10Mg alloy // Scripta Mater. 2017. V. 141. P. 145–149.
Takata N., Kodaira H., Sekizawa K., Suzuki A., Kobashi M. Change in microstructure of selectively laser melted AlSi10Mg alloy with heat treatments // Mater. Sci. Eng. A. 2017. V. 704. P. 218–228.
Marola S., Manfredi D., Fiore G., Poletti M. G., Lombardi M., Fino P., Battezzati L. A comparison of Selective Laser Melting with bulk rapid solidification of AlSi10Mg alloy // J. Alloys Comp. 2018. V. 742. P. 271–279.
Aboulkhai N.T., Maskery I., Tuck C. The microstructure and mechanical properties of selectively laser melted AlSi10Mg: The effect of a conventional T6-like heat treatment // Mater. Sci. Eng. A. 2016. V. 667. P. 139–146.
Olakanmi E.O. Selective laser sintering/melting (SLS/SLM) of pure Al, Al-Mg, and Al–Si powders: Effect of processing conditions and powder properties // J. Mater. Proces. Techn. 2013. V. 213. № 8. P. 1387–1405.
Fefelov A.S., Merkushev A.G., Chikova O.A. Microstructure and mechanical properties of Al–12Si produced by selective laser melting // IOP Conf. Series: Earth and Environmental Science. IPDME 2017. 2017. V. 87. P. 09201.
Бродова И.Г., Попель П.С., Барбин Н.М., Ватолин Н.А. Расплавы как основа формирования структуры и свойств алюминиевых сплавов. Екатеринбург: УрО РАН. 2005. 369 с.
Nasaba M.H., Gastaldib D., Lecisa N.F., Vedania M. On morphological surface features of the parts printed by selective laser melting (SLM) // Additive Manufacturing. 2018. V. 24. P. 373–377.
Aversa A., Lorusso M., Cattano G., Manfredi D., Calignano F., Ambrosio E.P., Biamino S., Fino P., Lombardi M., Pavese M. A study of the microstructure and the mechanical properties of an Al–Si–Ni alloy produced via selective laser melting // J. Alloys and Comp. 2017. V. 695. P. 1470–1478.
Kim D.K., Woo W., Hwang J.H., An K., Choi S.H. Stress partitioning behavior of an AlSi10Mg alloy produced by selective laser melting during tensile deformation using in situ neutron diffraction // J. Alloys Comp. 2016. V. 686. P. 281–286.
Дополнительные материалы отсутствуют.
Инструменты
Физика металлов и металловедение