Физика металлов и металловедение, 2019, T. 120, № 11, стр. 1187-1192
Эволюция структуры и механизм образования сварных соединений среднеуглеродистых сталей при ротационной сварке трением
Е. Ю. Приймак a, *, И. Л. Яковлева b, Н. А. Терещенко b, А. В. Степанчукова c, А. Н. Морозова b
a Оренбургский государственный университет
460048 Оренбург, пр. Победы, 13, Россия
b Институт физики металлов УрО РАН
620108 Екатеринбург, ул. С. Ковалевской, 18, Россия
c ОАО “Завод бурового оборудования”
460026 Оренбург, пр. Победы, 118, Россия
* E-mail: elena-pijjmak@yandex.ru
Поступила в редакцию 24.04.2019
После доработки 04.06.2019
Принята к публикации 07.06.2019
Аннотация
С применением металлографии и сканирующей электронной микроскопии, дополненной микрорентгеноспектральным анализом, описана микроструктура линии контакта и зоны термомеханического влияния сварных соединений среднеуглеродистых легированных сталей, полученных методом ротационной сварки трением. Приведены результаты распределения микротвердости по сечению сварного соединения. Проанализированы фазовые превращения, реализующиеся на каждом этапе технологического процесса сварки в областях, подверженных термодеформационному воздействию. Приведены результаты испытаний на одноосное растяжение и ударный изгиб, дополненные фрактографией поверхности разрушения.
ВВЕДЕНИЕ
Сварка трением – одна из наиболее прогрессивных технологий получения неразъемных соединений металлов. Она находит все более широкое применение в различных производствах. К настоящему моменту реализовано более 20 технологических решений процесса сварки, использующих нагрев трением [1–5]. Одним из первых таких решений является сварка трением вращением, или ротационная сварка трением [6].
В отечественной научной литературе основные исследования процесса ротационной сварки трением, направленные на внедрение ее в промышленное производство, относятся к 60–70-м гг. прошлого столетия и изложены в работах [7, 8]. В них представлен накопленный эмпирический опыт по промышленному применению, оборудованию и режимам сварки, которые преимущественно подбирали, исходя из результатов определения механических характеристик сварных соединений или данных неразрушающего контроля. К сожалению, в научных публикациях не представлено более современных отечественных исследований, в том числе с применением оборудования высокого разрешения для выявления механизмов образования и структурных особенностей получаемых подобным образом сварных соединений. Однако применение данной технологии на передовых отечественных машиностроительных предприятиях, в том числе для производства геологоразведочных и нефтяных бурильных труб, указывают на потребность в более глубоком понимании процесса ротационной сварки.
Анализируя зарубежные источники по данной тематике [9–15 ], можно отметить, что исследование процесса ротационной сварки трением в настоящее время актуально, что, вероятно, связано с более широким распространением данной технологии за рубежом для создания неразъемных конструкций из различных материалов.
Тем не менее в этихисследуемых публикациях не представлено прямых исследований эволюции микроструктуры и фазовых превращений, вызванных локальным термодеформационным воздействием при ротационной сварке трением. Подобные исследования получают распространение преимущественно для изучения процесса сварки трением с перемешиванием [16, 17], имеющего некоторые отличия по механизму образования сварных соединений от ротационной.
Настоящая работа посвящена изучению особенностей формирования структуры и механических свойств в зоне термомеханического воздействия сварного соединения, выполненного из среднеуглеродистых легированных сталей методом ротационной сварки трением.
МАТЕРИАЛЫ И МЕТОДЫ ИССЛЕДОВАНИЯ
Сварка трением заготовок кольцевого сечения диаметром 48 мм и толщиной стенки 4 мм осуществлена на автоматизированной машине для сварки трением “Thompson-60”. Технологический процесс образования сварного соединения происходил в несколько стадий (рис. 1). Заготовки (1) устанавливали в стационарный зажим (2), одной из них сообщали вращательное движение с частотой 900 об./мин (3), заготовки сближали и осуществлялась притирка контактных поверхностей. Далее в течение 6 с прикладывали усилие трения 40 кН, в результате чего происходил разогрев. После этого вращение быстро прекращали, и к заготовкам вдоль оси прикладывали постоянное усилие 100 кН в течение 4.5 с (4). Затем осуществляли точение сварочного грата, который представляет собой избыточный металл, выдавленный при сварке давлением (5).
В процессе образования сварочного грата происходит осадка привариваемых материалов. Суммарная величина осадки состоящая из осадки после реализации этапа трения (9 мм) и небольшой осадки после проковки, достигла 11.5 мм. Процесс окончательного схватывания привариваемых поверхностей с образованием неразъемного соединения осуществляется на этапе проковки.
Сварке трением подвергали среднеуглеродистые стали, применяемые для изготовления геологоразведочных бурильных труб с приварными замковыми деталями, их химический состав представлен в табл. 1. Заготовки предварительно были подвержены улучшению.
Таблица 1.
Химический состав привариваемых материалов
Материал | С | Mn | Si | S | P | Cr | Ni | Cu | Mo |
---|---|---|---|---|---|---|---|---|---|
32Г2 | 0.27 | 1.19 | 0.38 | 0.002 | 0.006 | 0.03 | 0.01 | <0.01 | <0.005 |
40ХН | 0.31 | 0.53 | 0.32 | 0.006 | 0.004 | 0.51 | 1.06 | – | 0.09 |
Из металла сварного соединения изготавливали продольные образцы для металлографического анализа. Исследование структуры проводили с использованием оптического микроскопа Nicon ECLEPSEMA 10 и сканирующих микроскопов JEOL JSM-6460LV и Quanta-200, оборудованного приставкой для рентгеноспектрального анализа.
Твердость измеряли на приборе HVS-1000 при нагрузке 2 Н. Испытания на ударный изгиб осуществляли на маятниковом копре “WANCE PIT 452 С2” на образцах 4 × 10 × 55 с V-образным надрезом согласно ГОСТ 9454-78, который наносили непосредственно в стыке сварного соединения в радиальном направлении. Испытания на статическое растяжение осуществляли на разрывной машине Р-50 в соответствии с ГОСТ 10006-80 на образцах, шириной рабочей части 10 мм и начальной расчетной длиной 40 мм.
РЕЗУЛЬТАТЫ ИССЛЕДОВАНИЯ И ОБСУЖДЕНИЕ
Процесс ротационной сварки трением осуществляется в твердой фазе, и с позиций термомеханического воздействия на материал он весьма сложен и многообразен. При металлографическом исследовании сварного соединения на изображениях макро- и микроструктуры отчетливо выявляются линия стыка и зона термомеханического воздействия (ЗТМВ) протяженностью около 3.5 мм, по обе стороны от которой располагается основной металл (рис. 2).
Рис. 2.
Микроструктура сварного соединения сталей 32Г2-40ХН, выполненного ротационной сваркой трением, на различном удалении от стыка сварного шва: a, b, c, d, f, g – зона термического влияния; d, h – основной металл.
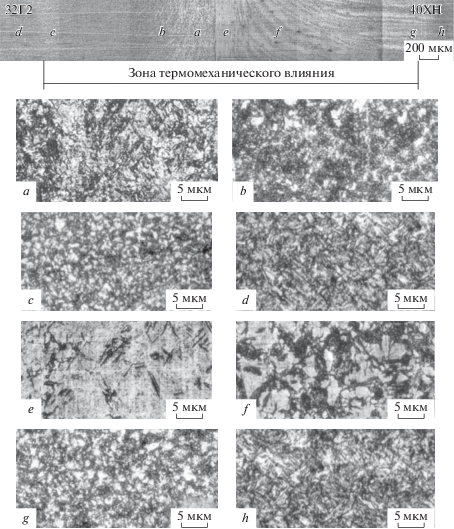
Как установлено ранее [7–15 ], вблизи свариваемых поверхностей металл испытывает локальное термодеформационное воздействие, при котором одновременно развиваются такие явления, как тепловыделение, износ поверхностей при трении; непрерывное образование и разрушение металлических связей между сопряженными поверхностями в процессе их относительного движения; мгновенный нагрев и быстрое охлаждение локальных объемов металла в присутствии высоких удельных давлений; упруго-пластические деформации приповерхностных слоев материала; наклеп и рекристаллизация металла; возможная взаимная диффузия и др. Под влиянием этих процессов в ЗТМВ формируются три характерные участка:
– участок воздействия деформаций и температур, превышающих критическую точку АС3 (зона 1, рис. 2а, 2e),
– участок воздействия деформаций и температур в интервале от Ас1 до Ас3 (зона 2, рис. 2b, 2f),
– участок рекристаллизации, в которой температура была близка к АС1 (зона 3, рис. 2c, 2g).
За участком рекристаллизации следует основной металл, имеющий структуру отпущенного мартенсита для обоих привариваемых материалов (рис. 2d, 2h) с размером зерна от 6 до 8 мкм для стали 32Г2 и от 8 до 10 мкм для стали 40ХН.
Рассмотрим структурные особенности каждой из зон. В областях, примыкающих к сварному стыку зоны 1, можно наблюдать образование игольчатой мартенситной структуры с отдельными участками нижнего бейнита со стороны стали 40ХН (область e) и смешанной мартенсито-бейнитной структуры со стороны стали 32Г2 (область a). Образование закалочных структур в ЗТМВ обеих сталей связано с их локальным разогревом до температур выше температуры полиморфного превращения и дальнейшим ускоренным охлаждением за счет реализации быстрого теплообмена между узкой, нагретой в процессе трения зоной, и прилегающими областями металла. Тем самым подтверждается тот факт, что фазовые превращения в данной зоне происходили в твердом состоянии. Следует отметить, что распределение зерна по размеру и геометрии в зоне 1 имеет сложный характер. Наряду с крупными зернами имеет место и образование более мелких, а следы деформации практически отсутствуют.
При удалении от сварного стыка микроструктура претерпевает изменения. В зоне 2 обеих сталей она представляет собой волокнистое строение и состоит из чередующихся полос закалочной структуры и мелкодисперсной феррито-цементитной смеси, плавно меняющих направление от параллельного сварному стыку к перпендикулярному (области b и f). Также можно отметить, что размер зерен здесь значительно меньше, чем в зоне 1. Зона 3 (области c и g), в которой отсутствуют видимые признаки пластической деформации, характеризуется образованием равноосных мелких зерен.
Уровень микротвердости в ЗТМВ соответствует структурным изменениям, вызванным термодеформационным влиянием сварочного процесса. На рис. 3 видно, что распределение микротвердости вдоль ЗТМВ имеет немонотонный характер. Наличие мартенситной фазы со стороны стали 40ХН объясняет высокую твердость в зоне 1, близлежащей к линии контакта. При удалении от линии контакта значения микротвердости плавно снижаются, достигая минимума в зоне 3. Зона 3 в стали 32Г2 характеризуется наиболее низкими значениями твердости и большей протяженностью по сравнению со сталью 40ХН и является зоной разупрочнения по отношению к основному металлу.
Рис. 3.
Распределение микротвердости по протяженности ЗТМВ сварного соединения сталей 32Г2–40ХН. Штриховыми линиями отмечены границы зоны термомеханического влияния.
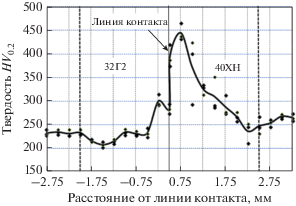
Для понимания механизмов, реализующихся на конечной стадии схватывания с последующим образованием неразъемного соединения, было проведено детальное изучение микроструктуры вдоль линии контакта с помощью растровой электронной микроскопии (рис. 4). Результаты исследования показывают, что линия соединения представляет собой ориентированную в плоскости контакта границу. На некоторых участках линии контакта видно образование общих зерен. Это позволяет считать, что при ротационной сварке взаимодействие в зоне соединения на некоторых участках не ограничивается образованием межатомных связей, а происходит взаимная объемная рекристаллизация.
Рис. 4.
Микроструктура вблизи линии контакта сварного соединения сталей 32Г2-40ХН, выполненного ротационной сваркой трением (сталь 32Г2 слева).
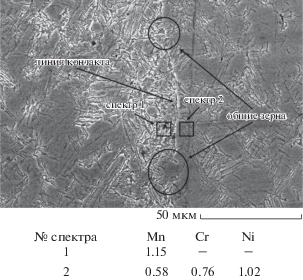
Вблизи линии контакта видны характерные морфологические особенности структуры мартенсита и нижнего бейнита. Размер образующихся игл мартенсита находится в диапазоне от 5 до 20 мкм, наблюдается разнозернистость, вызванная аномальным ростом некоторых зерен. Полученная микроструктура предполагает последовательное развитие процессов динамической и собирательной рекристаллизации в данных областях в процессе разогрева соединяемых поверхностей при приложении давления трения. Однако в узких зонах, непосредственно примыкающих к линии контакта, наблюдается измельчение зерна и фрагментация цементитных пластин в зернах бейнита, что особенно прослеживается со стороны стали 32Г2. Предположительно, такая структура в приконтактной узкой зоне могла образоваться на этапе проковки, в результате чего интенсифицировалась деформация наиболее разогретого и пластичного металла, а в некоторых участках развились процессы совместной рекристаллизации. Узкая деформированная зона с фрагментированными частицами имеет размер около 20 мкм и микротвердость несколько ниже, чем на некотором удалении в сторону основного металла (рис. 3).
Представляет интерес оценка роли диффузии в механизме образования исследуемых сварных соединений. Существуют противоречивые данные о вкладе диффузии в образование соединений при сварке в твердой фазе, рассмотренные в работе [20]. Микрорентгеноспектральный анализ приконтактных областей показал отсутствие диффузионных перемещений основных легирующих элементов. Это свидетельствует о превалирующей роли рекристаллизации в образовании исследуемого сварного соединения. Полученные данные согласуются с теорией Дж. Паркса, который сделал заключение, что рекристаллизация и есть тот основной механизм, с помощью которого можно получать прочные сварные соединения [20].
Образование физического контакта и прочности межзеренных границ между свариваемыми материалами проследим на основе результатов механических испытаний на ударный изгиб и статическое растяжение.
Величина ударной вязкости находится в диапазоне от 14.3 до 18.5 Дж/см2. Такой низкий уровень значений KCV соответствует формированию хрупких закалочных структур сталей вблизи стыка сварного соединения, расположенного непосредственно под надрезом.
Анализ излома ударного образца позволяет установить, что при пересечении магистральной трещиной линии контакта привариваемых материалов образуется “ступенька” перехода, разделяющая поверхность разрушения стали 40ХН и стали 32Г2 (рис. 5а).
Рис. 5.
Поверхность разрушения сварного соединения: а – область линии контакта привариваемых материалов; б – фрактограмма стали 40ХН; в – фрактограмма стали 32Г2.
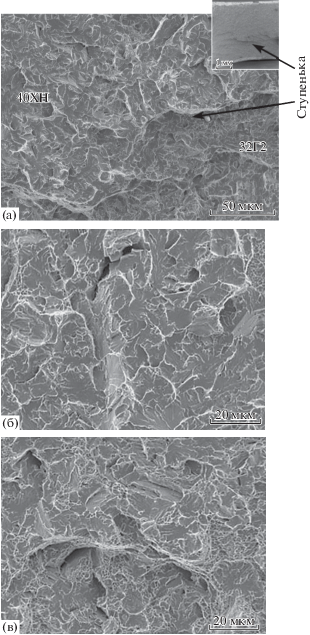
Характер разрушения всех исследуемых сталей преимущественно транскристаллитный; инициированные границами зерен вторичные трещины встречаются крайне редко (рис. 5б, 5в). Большая часть поверхности разрушения стали 40ХН занята фасетками квазискола. На фрактограммах стали 32Г2 наряду с фасетками квазискола значительную долю занимают области вязкого ямочного разрушения. Таким образом, проведенный фрактографический анализ свидетельствуют о достаточной прочности межзеренных границ вблизи линии контакта привариваемых материалов.
Испытание на статическое растяжение позволяет сделать заключение о достаточной конструктивной прочности сварного соединения в целом. В табл. 2 приведены прочностные и пластические характеристики привариваемых материалов, а также образца сварного соединения. Сопоставление этих данных показывает, что сварное соединение демонстрирует уровень механических свойств, характерный для стали 32Г2. Локализация деформации с последующим разрушением образца сварного соединения происходит на расстоянии 11 мм от стыка материалов со стороны стали 32Г2.
ЗАКЛЮЧЕНИЕ
При ротационной сварке трением металл подвергается термомеханическому воздействию; на каждом этапе образования сварного соединения в структуре приконтактных областей развивается ряд процессов. Можно предполагать, что для среднеуглеродистых легированных сталей 32Г2 и 40ХН основными являются следующие:
– на этапе разогрева при приложении давления трения в приконтактных областях одновременно развивается фазовая перекристаллизация, динамическая и собирательная рекристаллизация, происходит формирование разнозернистой структуры с аномальным ростом некоторых зерен;
– на этапе проковки происходит окончательное формирование структуры вдоль линии контакта, заключающееся в образовании межатомных связей, совместной рекристаллизации в некоторых областях и фрагментации зерен в узких примыкающих зонах;
– дальнейшее охлаждение сварного соединения приводит к образованию закалочных структур мартенсита и бейнита в зонах, где температура разогрева превысила значения критических точек.
Прочностные и пластические свойства сварного соединения сопоставимы с уровнем механических свойств стали 32Г2.
Работа выполнена в рамках государственного задания Минобрнауки РФ (тема “Структура” № АААА-А18-118020190116-6).
Список литературы
Вавилов А.Ф., Воинов В.П. Сварка трением. М.: Машиностроение, 1964. 156 с.
Хуснуллин А.М., Кашаев Р.М. Управление линейной сваркой трением // Письма о материалах. 2016. Т. 6. № 3. С. 227–230.
Сергеева Е.В. Сварка трением с перемешиванием в авиакосмической промышленности (обзор) // Автоматическая сварка. 2013. № 5. С. 58–62.
Friction Stir Welding and Processing / Ed. by Misha R.S., Mahoney M.W. San Francisco. 2005. 298 p.
Красильников В.В., Шагабутдинов Э.Р., Кузнецов М.Е., Бородулин И.В., Каратыш В.В. Точечная сварка трением с перемешиванием с разделением цикла сварки для нахлесточных соединений // Master’s J. 2015. № 1. С. 48–53.
Клименко Ю.В. Способ сварки металлов трением. Авт. свид. № 195846 (приоритет от 09.11.65 г.).
Виль В.И. Сварка металлов трением. М.: Машиностроение, 1970. 176 с.
Сварка трением: Справочник / В.К. Лебедев, И.А. Черненко, В.И. Вилль и др. Л.: Машиностроение, 1987. 236 с.
Sahin M. Joining with friction welding of high-speed steel and medium-carbon steel // J. Mater. Proces. Techn. 2005. V. 168. P. 202–210. https://doi.org/10.1016/j.jmatprotec.2004.11.015
Sahin M. Characterization of properties in plastically deformed austenitic-stainless steels joined by friction Welding // Mater. Design. 2009. V. 30. P. 135–144. https://doi.org/10.1016/j.matdes.2008.04.033
Sahin M. Evaluation of the joint-interface properties of austenitic-stainless steels (AISI 304) joined by friction welding // Mater. Design. 2007. V. 28. P. 2244–2250. https://doi.org/10.1016/j.matdes.2006.05.031
Zdemira N.O., Sarsılmaz F., Hascalık A. Effect of rotational speed on the interface properties of friction- welded AISI 304L to 4340 steel // Materials and Design. 2007. V. 28. P. 301–307. https://doi.org/10.1016/j.matdes.2005.06.011
Selvamani1 S.T., Umanath K., Palanikumar K., Vigneswar K. The microhardness analysis of friction welded AISI 52100 grade carbon steel joints. // Advanced Mater. Research. 2014. V. 984–985. P. 613–617. DOI 10.4028/www.scientific.net/AMR.984-985.613
Satyanarayana V.V., Madhusudhan R.G., Mohandas T. Dissimilar metal friction welding of austenitic–ferritic stainless steels. // J. Mater. Proces. Techn. 2005. V. 160. P. 128–137. https://doi.org/10.1016/j.jmatprotec.2004.05.017
Kalsi. N.S., Sharma V.S. A statistical analysis of rotary friction welding of steel with varying carbon in workpieces // Int. J. Adv. Manuf. Technol. 2011. https://doi.org/10.1007/s00170-011-3361-z
Рао Шайлеш, А. Найк Ювараджа Сравнение внешнего вида, микроструктуры и механических свойств на растяжение сварных соединений Al–Si сплавов после сварки трением с перемешиванием // ФММ. 2017. Т. 118. С. 752–760.
Чуларис А.А. Рзаев Р.А., Валишева А.Г. Эволюция механизмов пластической деформации, ответственных за формирование структуры околошовной зоны при сварке трением с перемешиванием металлов // Металловедение и термич. обр. металлов. 2019. № 1. С. 54–60.
Горелик С.С., Добаткин С.В., Капуткина Л.М Рекристаллизация металлов и сплавов. 3-е изд. М.: МИСИС, 2005. 432 с.
Дегтярев М.В. Воронова Л.М. Чащухина М.И., Пилюгин В.П., Реснина Н.Н. Эволюция структуры никеля в ходе деформации сдвигом под высоким давлением при 150°С // ФММ. 2017. Т. 118. № 3. С. 270–277.
Лариков Л.Н., Рябов В.Р., Фальченко В.М. Диффузионные процессы в твердой фазе при сварке. М.: Машиностроение, 1975. 192 с.
Дополнительные материалы отсутствуют.
Инструменты
Физика металлов и металловедение