Физика металлов и металловедение, 2019, T. 120, № 11, стр. 1174-1180
Структура СВС-композитов системы Fe–Ni–Ti–C–B
Н. Б. Пугачева a, *, Ю. В. Николин b, Е. И. Сенаева a, И. Ю. Малыгина a
a Институт машиноведения УрО РАН
620049 Екатеринбург, ул. Комсомольская, 34, Россия
b ООО “Солид Флэйм”
620075 Екатеринбург, пр. Ленина, 54, кор. 5, Россия
* E-mail: nat@imach.uran.ru
Поступила в редакцию 01.04.2019
После доработки 30.04.2019
Принята к публикации 08.05.2019
Аннотация
Исследованы структура, химический и фазовый состав, твердость композитов системы Fe–Ni–Ti–C–B, полученных методом самораспространяющегося высокотемпературного синтеза (СВС). Показано, что при использовании в качестве исходных материалов порошков Fe, Ni, Ti, C и B4C, засыпаемых внутрь стальной трубы, в процессе СВС и последующего горячего прессования формируется единая многослойная пластина, состоящая из стальной оболочки и композита. Матрицей композита является твердый раствор Ni и Ti в кристаллической решетке γ-Fe, упрочняющие фазы – TiC, TiB2, Fe2B, Ni3Ti и NiTi. Твердость композитов достигает значений 57–62 HRC. Внутренняя поверхность стальной оболочки прочно соединена с композитом за счет диффузии продуктов синтеза в сталь.
ВВЕДЕНИЕ
Самораспространяющийся высокотемпературный синтез (СВС) является одним из наиболее современных способов получения новых порошковых или монолитных материалов, а также покрытий с уникальными свойствами [1–5]. Известные компактные СВС-композиты отличаются высокой твердостью в сочетании с высокой хрупкостью и склонностью к образованию трещин и сколов при внешнем нагружении, особенно в случае приложения ударных нагрузок, поэтому применяются, главным образом, как режущий инструмент. Возрастающие эксплуатационные мощности машин и агрегатов выдвигают новые требования к созданию высокоизносостойких материалов с удовлетворительными показателями конструкционной прочности. С этой точки зрения перспективным направлением представляется разработка новых СВС-композитов с регулируемым содержанием наполнителя (упрочняющих фаз) и пластичной матрицей, в качестве которой могут быть использованы железо, никель, кобальт, медь, алюминий и их сплавы. При создании новых износостойких СВС-композитов основное внимание обычно уделяется упрочняющим фазам – карбидам и боридам, которые обеспечивают высокие значения твердости и износостойкости. Несмотря на то что проблема создания новых композиционных материалов с использованием метода СВС достаточно успешно решается, до сих пор не определена роль эвтектик, неизбежно появляющихся в процессе синтеза многокомпонентных систем, таких как Fe–Ni–Ti–C–B. Практически все еще не выявлено влияние содержания термореагирующих компонентов (ТРК), определяющих ход процесса СВС, в смеси исходных порошков, в формировании структуры и свойств композитов. Недостаточное внимание уделяется исследованию особенностей строения металлической матрицы. Определенные трудности до сих пор существуют в получении беспористых компактных композитов, предназначенных для изготовления деталей и элементов конструкций, испытывающих абразивное воздействие на большой площади поверхности. Традиционно для устранения пористости сразу после синтеза применяют обработку давлением, которая не только способствует схлопыванию пор, но и может упрочить связи “наполнитель–матрица” за счет протекающих адгезионно-диффузионных процессов.
Цель работы – установить влияние состава исходных порошковых материалов на структурное состояние композитов системы Fe–Ni–Ti–C–B, определить их пористость, твердость, фазовый и химический состав.
МАТЕРИАЛЫ И МЕТОДЫ ИССЛЕДОВАНИЯ
Исследована структура, пористость и твердость композиционных материалов системы Fe–Ni–Ti–C–B, получаемых в режиме безгазового твердофазного горения методом СВС при постоянной скорости перемещения фронта горения. Исходными материалами для синтеза были выбраны порошки Ti, Ni, Fe, C и В4С, которые засыпали в стальную трубу (марка Ст3), выполняющую роль реактора открытого типа и внешней оболочки будущей заготовки одновременно [6, 7]. Порошки Fe и Ni формируют металлическую матрицу будущего композита, форма частиц приведена на рис. 1. Порошки Ti, C, B4С представляют собой ТРК, поскольку именно они обеспечивают протекание экзотермических реакций, в результате которых формируются упрочняющие фазы композита.
Рис. 1.
Форма частиц металлического порошка, использованного для синтеза композитов: а – Ti, б – Ni; в – Fe.
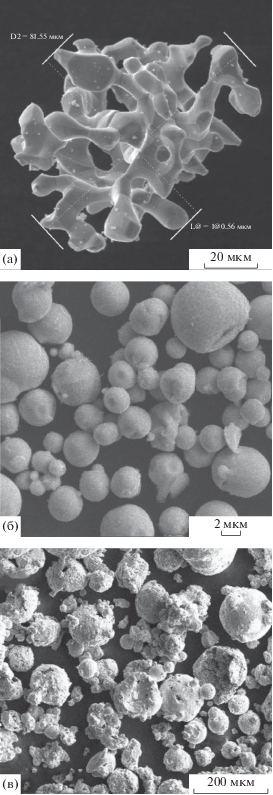
Объемное содержание ТРК варьировали от 15 до 50 об. % согласно табл. 1. Сразу после завершения процесса синтеза заготовки подвергали силовому компактированию (горячему прессованию) при температуре 1200°С под нагрузкой 250 МПа на гидравлическом прессе. Образцы для исследований вырезали из полученных заготовок.
Таблица 1.
Содержание ТРК в исходных порошковых составах (об. %) и твердость композитов
№ | ТРК (Ti + B4C + C) | HRC |
---|---|---|
1 | 50 | 21–24 |
2 | 40 | 48–55 |
3 | 30 | 58–62 |
4 | 15 | 36–38 |
Структуру композитов и зон диффузионного взаимодействия со стальной оболочкой исследовали как непосредственно после синтеза, так и после горячей пластической деформации. Проведен анализ макро- и микроструктуры композитов на оптическом микроскопе NEOPHOT 21. Были определены значения твердости по Роквеллу, замеры проводили только на участках, свободных от пор. Определен характер распределения значений микротвердости по сечению образцов и на границе со стальной оболочкой на твердомере LEICA VM HT AUTO.
Локальный химический состав фаз композитов определяли на растровом электронном микроскопе TESCAN VEGAII XMU с энергодисперсионной и волнодисперсионной (для определения содержания бора) приставками фирмы OXFORD. Фазовыйрентгеноструктурный анализ выполнен на рентгеновском дифрактометре SHIMADZU в kα-излучении хрома.
РЕЗУЛЬТАТЫ ИССЛЕДОВАНИЙ И ОБСУЖДЕНИЕ
В СВС выделяют три основные стадии: горение, образование новых фаз и охлаждение продуктов горения [1]. На стадии горения происходят экзотермические реакции, повышающие температуру порошковой смеси вплоть до температур плавления ее составляющих. Основными экзотермическими реакциями для исследованных композитов являются:
(2)
${\text{3Ti}} + {{{\text{B}}}_{{\text{4}}}}{\text{C}} \to {\text{TiC}} + 2{\text{Ti}}{{{\text{B}}}_{2}} + Q;$Следует отметить большую площадь поверхности частиц порошка титана, участвующих в синтезе (рис. 1а). В ходе протекания этих химических реакций происходит интенсивное газовыделение, поэтому получаемый композит имеет весьма пористое строение. Для устранения порообразования заготовку сразу после завершения синтеза подвергают силовому компактированию (горячему прессованию), пока температура композита еще сохраняется на уровне 1200°С. В результате происходит образование многослойной пластины (рис. 2), которая представляет собой единый конструкционный элемент.
Рис. 2.
Внешний вид поперечных резов полученных композитов: а – состав 1, б – состав 2 (стрелками отмечены цепочки пор на границе с внешней стальной оболочкой; в – состав 3; г – состав 4 (см. составы в табл. 1).
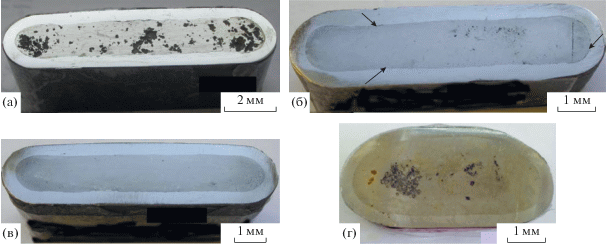
Исследования показали, что содержание ТРК в исходных порошковых смесях существенно влияет на пористость получаемых композитов: с увеличением ее объемной доли пористость существенно увеличивается. Так композит, полученный из порошковой смеси состава 1 с максимальным содержанием ТРК, характеризуется наличием множественных крупных пор размерами 0.5 мм, которые образуют скопления (рис. 2а). Очевидно, повышенная пористость в этом случае обусловлена наиболее интенсивным газовыделением, проведение горячего компактирования после синтеза не устраняет образовавшиеся поры. Более того, после компактирования в композите образуются многочисленные микротрещины как в центральной части образца, так и по границе с внешней оболочкой из стали. Невысокие значения твердости этого композита (см. табл. 1) очевидно обусловлены его пористостью.
На поперечном резе композита, полученного при содержании ТРК 40 мас. %, зафиксированы мелкие поры (максимальный размер 0.2 мм) в виде скоплений на площади поверхности, составляющей около ¼ общей площади шлифа (рис. 2б). Значение твердости, измеренное на участке без визуально наблюдаемых пор, составило 48–55 HRC. Цепочки микропор зафиксированы на границе композита со стальной оболочкой (отмечены стрелками на рис. 2б). Беспористый композит образовался при содержании ТРК 30 мас. % (рис. 2в), соответственно значения твердости гораздо выше – 58–62 HRC (табл. 1). В случае образца 4 визуально не было зафиксировано протекание экзотермических реакций в процессе спекания, поэтому заготовку не подвергали горячему компактированию, на поверхности поперечного реза наблюдали множественные поры в виде скоплений в центральной части заготовки (рис. 2г). Твердость этого композита невысока – 36–38 HRC.
Известно [8, 9], что в системе Ti–C–B при температурах, близких к температурам синтеза, возможно существование следующих фаз: β-Ti, TiC, TiB2, Ti3B4, TiB (рис. 3). Химические соединения B4C и TiC имеют достаточно широкие области гомогенности. Результаты фазового рентгеноструктурного анализа показали присутствие во всех полученных композитах γ-Ni, γ-Fe, TiC и TiB2. В композитах, полученных из составов 3 и 4, зафиксировано присутствие Fe2B, Ni3Ti и NiTi (рис. 4).
Рис. 3.
Бинарные фазовые диаграммы Ti–B, Ti–C, B–C и изотермическое сечение тройной системы Ti–B–C при 1400°С [9].
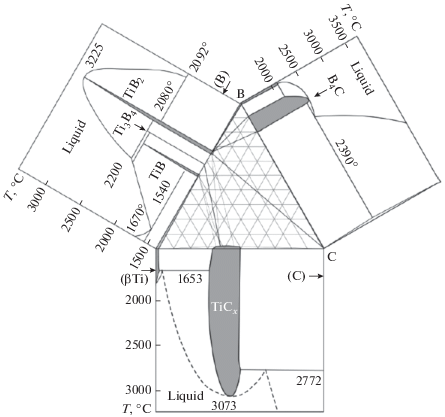
Очевидно, в процессе СВС кроме экзотермических превращений (1)–(3) протекают еще и следующие реакции:
При анализе микроструктуры композитов обнаружено присутствие продуктов эвтектических превращений характерного “скелетообразного” строения при содержании в исходной порошковой смеси ТРК 15 и 30 мас. % (рис. 5а). Вполне вероятно, что в процессе синтеза происходит распад карбида бора B4C, образовавшийся атомарный бор легирует γ-Fe и может участвовать в формировании боридов железа. При содержании бора менее 10 мас. % в соответствии с диаграммой состояния системы Fe–B возможно протекание эвтектического превращения L ↔ γ-Fe + Fe2B при температуре 1177°С [8]. В результате при охлаждении в композите образуется механическая смесь γ-Fe и Fe2B скелетообразного строения (рис. 5а). В композите, полученном при содержании ТРК 15 мас. %, синтез произошел в отдельных микрообластях, структура его крайне неоднородна, частицы упрочняющих фаз TiC и TiB2 расположены в виде отдельных строчек в твердом растворе Ni в γ-Fe.
Рис. 5.
Микроструктура СВС-композитов после горячего компактирования: а – состав 3 (стрелками отмечены участки эвтектики γ-Fe + Fe2B); б – состав 3, в – состав 2 (ограненные частицы черного цвета – TiB2, глобулярные серого – TiC).
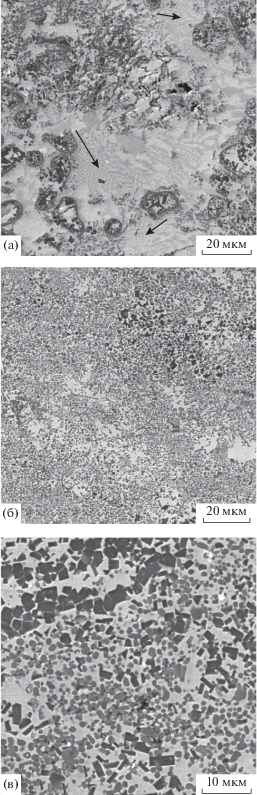
После завершения процесса СВС возможно существование отдельных микрообъемов жидкой фазы, в которых при охлаждении происходит превращение L → γ-Fe + Fe2B. Последующее горячее компактирование приводит, во-первых, к тому, что расплав под давлением заполняет поры, образовавшиеся при газовыделении, во-вторых, эвтектическая смесь скелетообразного строения γ-Fe + Fe2B измельчается, частицы борида Fe2B приобретают размеры от 2 до 4 мкм и дополнительно упрочняют композит.
Во всех композитах наблюдали частицы черного цвета правильной огранки, соответствующие по химическому составу химическому соединению TiB2 (рис. 5б, 5в, табл. 2), и частицы серого цвета глобулярной формы, соответствующие соединению TiC. Наиболее равномерно эти частицы распределены в образцах 2 и 3 (рис. 5б, 5в). В композитах составов 1 и 4 частицы упрочняющих фаз TiB2 и TiC распределены полосчато. Значения микротвердости участков, обогащенных частицами TiB2, достигают значений 1000 HV 0.05, участков с наибольшим количеством частиц TiC – 950 HV 0.05. В композите 2 обнаружены скопления частиц TiN, не выявленные при рентгеноструктурном анализе, очевидно, из-за их малого содержания и малых размеров, эти частицы образуют вытянутые строчки и зафиксированы на единичных участках поверхности шлифа.
Таблица 2.
Химический состав диффузионной зоны композита состава 2 после горячего компактирования на границе со стальной оболочкой, мас. % (участки анализа обозначены на рис. 6)
№ | В | С | Ti | Fe | Ni | Cr | Si | N | Примечание |
---|---|---|---|---|---|---|---|---|---|
1 | 1.65 | 1.02 | 0 | 97.33 | 0 | 0 | 0 | 0 | α-Fe |
2 | 1.60 | 0.67 | 0 | 97.57 | 0.16 | 0 | 0 | 0 | |
3 | 1.3 | 0.54 | 0.08 | 98.09 | 0 | 0 | 0 | 0 | |
4 | 1.10 | 0.78 | 0.23 | 97.59 | 0.28 | 0 | 0 | 0 | |
5 | 4.20 | 5.68 | 12.26 | 58.91 | 18.40 | 0 | 0.56 | 0 | γ-Fe + TiC |
6 | 1.0 | 4.10 | 4.05 | 86.65 | 3.32 | 0 | 0 | 1.1 | γ-Fe + TiN |
7 | 0.72 | 1.08 | 23.67 | 47.63 | 23.29 | 0 | 3.62 | 0 | γ-Fe |
8 | 0.70 | 1.22 | 11.98 | 54.15 | 30.72 | 0.40 | 0.82 | 0 | |
9 | 1.03 | 0.80 | 11.28 | 54.72 | 31.18 | 0.43 | 0.58 | 0 | |
10 | 2.42 | 12.55 | 48.26 | 21.14 | 15.35 | 0 | 0.27 | 0 | γ-Fe + TiC |
11 | 3.87 | 12.76 | 53.98 | 18.34 | 10.73 | 0 | 0.32 | 0 | |
12 | 1.63 | 15.53 | 48.66 | 19.37 | 14.42 | 0 | 0.40 | 0 | |
13 | 25.95 | 0 | 48.33 | 17.14 | 7.88 | 0.51 | 0.18 | 0 | TiB2 |
14 | 20.23 | 8.97 | 39.30 | 20.13 | 10.75 | 0.43 | 0.20 | 0 |
На границе всех исследованных композитов со стальной оболочкой наблюдается диффузионное взаимодействие, проявившееся в образовании переходной диффузионной зоны (рис. 6). Значения микротвердости в этой зоне плавно изменяются от 950 HV 0.05 в композите до 240 HV 0.05 в стали (рис. 7).
Рис. 6.
Строение диффузионной зоны на границе композита состава 2 после горячего компактирования со стальной оболочкой (цифрами отмечены участки микрорентгеноспектрального анализа).
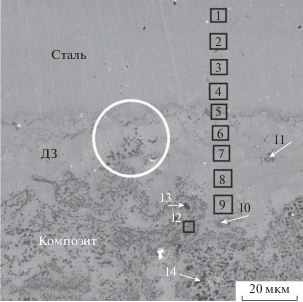
Рис. 7.
Распределение значений микротвердости на границе СВС-композита состава 2 после горячего компактирования со стальной оболочкой.
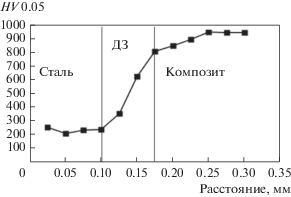
Граница между ДЗ и композитом извилистая, на некоторых участках синтезированные частицы упрочняющих фаз TiC и TiB2 образуются практически у стальной оболочки (на рис. 6 подобный
участок выделен кругом). Более светлая структурная составляющая диффузионной зоны соответствует твердому раствору на основе α-Fe (участок 6 на рис. 6), серая составляющая – твердому раствору Ni в γ-Fe (участки 7–9 на рис. 6).
ЗАКЛЮЧЕНИЕ
При СВС исходных порошков Fe, Ni, Ti, C, B4C, засыпанных в полость стальной трубы и нагретых в печи до 1200°С, формируется единая монолитная “сэндвич-пластина”, состоящая из наружной стальной оболочки, диффузионно связанной с образовавшимся композитом. Матрицей образовавшегося после СВС композита является твердый раствор никеля и титана в ГЦК решетке железа. Упрочняющие фазы – частицы TiC, TiB2 и Fe2B размерами от 1 до 4 мкм.
Содержание ТРК существенно влияет на пористость и, как следствие, твердость СВС композитов после горячего компактирования при выбранном давлении 250 МПа. При содержании ТРК 15 мас. % визуально синтез не был зафиксирован, однако продукты синтеза были обнаружены. Основу композита составил твердый раствор на основе γ-Fe, значительную часть объема композита занимают продукты эвтектического превращения L → γ-Fe + Fe2B. Частицы упрочняющих фаз TiC и TiB2 образовались в отдельных микрообъемах в виде строчек.
При содержании ТРК 50 мас. % в композите зафиксированы множественные поры размерами 0.5 мм, образующие скопления, что привело к уменьшению его твердости до 21–24 HRC. Высокое содержание ТРК в исходной порошковой смеси обусловило интенсивное протекание процесса синтеза, сопровождающегося бурным газовыделением и порообразованием.
Горячее компактирование заготовок в гидравлическом прессе при 1200°С под нагрузкой 250 МПа позволило получить беспористый композит при содержании ТРК 30 мас. %, твердость которого составила 58–62 HRC.
На границе между композитом и внутренней поверхностью стальной оболочки формируется диффузионная переходная зона с плавным изменением концентрации железа, никеля и титана, а также микротвердости. Именно диффузионное взаимодействие внешней оболочки с продуктами СВС обеспечивает формирование единой многослойной конструкции – “сэндвич-пластины”.
Работа выполнена на оборудовании ЦКП “Пластометрия” ИМАШ УрО РАН в соответствие с государственным заданием по теме № АААА-А18-118020790145-0.
Список литературы
Амосов А.П., Боровинская И.П., Мержанов А.Г. Порошковая технология самораспространяющегося высокотемпературного синтеза материалов. М.: Машиностроение-1, 2007. 472 с.
Мержанов А.Г. Твердопламенное горение. Черноголовка: ИСМАН, 2000. 224 с.
Самораспространяющийся высокотемпературный синтез: теория и практика / Сборник статей // Под ред. А.Е. Сычева. Черноголовка: Территория, 2001. 432 с.
Жевтун И.Г., Гордиенко П.С., Кульчин Ю.Н., Субботин Е.П., Ярусова С.Б., Голуб А.В. Влияние легирования композитных Ti–TiC покрытий переходными и вентильными металлами на их структуру и механические свойства // ФММ. 2019. Т. 120. № 1. С. 27–33.
Баят О., Хаванди А.Р., Гесемзаде Р. Синтез интерметаллического соединения TiCr2 из исходно механоактивированных порошков путем их совместного кальцитермического восстановления // ФММ. 2018. Т. 119. № 5. С. 469–477.
Николин Ю.В., Зяткевич В.В., Блинков О.Г. Патент на полезную модель № 150731 (Rus). Многослойная износостойкая пластина. Приоритет от 07.08.2014 до 07.08.2024.
Николин Б.В., Матевосян М.Б., Кочугов С.П., Пугачева Н.Б. Патент на изобретение № 2680489. Способ изготовления многослойной износостойкой пластины. Приоритет от 10.11.2017 до 10.11.2037.
Захаров А.М. Диаграмма состояния двойных и тройных систем. М.: Металлургия, 1990. 350 с.
Кузьма Ю.Б., Чабан Н.Ф. Двойные и тройные системы, содержащие бор. Справочник. М.: Металлургия, 1990. 318 с.
Дополнительные материалы отсутствуют.
Инструменты
Физика металлов и металловедение