Физика металлов и металловедение, 2019, T. 120, № 3, стр. 280-290
Микроструктура и кинетика формирования интерметаллической фазы в условиях твердофазной диффузионной сварки в биметаллическом Ti/Al композите
Амир Хусейн Ассари a, Бейаталла Эгхбали a, *
a Факультет материаловедения и машиностроения, Технический университет Саханда
Тебриз, Иран
* E-mail: eghbali@sut.ac.ir
Поступила в редакцию 06.06.2017
После доработки 31.05.2018
Принята к публикации 08.10.2018
Аннотация
С помощью горячего пакетного прессования и прокатки были синтезированы трехслойные композиты Ti/Al, подвергнутые затем отжигу при температурах 550–650°C в течение 2, 4 и 6 ч. Поверхности сопряжения слоев разнородного материала композита были аттестованы с помощью растровой электронной микроскопии, энергодисперсионной спектрометрии и метода рентгеновской дифракции. Изучение микроструктуры, сформированной в результате отжигов различной продолжительности при разных температурах, показало, что Al3Ti был единственным интерметаллическим соединением, наблюдавшимся в диффузионных слоях композита. Рост Al3Ti характеризовался линейной кинетикой и энергией активации 128.7 кДж моль–1. Результаты свидетельствуют, что основным диффузантом выступал алюминий, и что рост слоя Al3Ti происходил в основном по границе сопряжения Ti/Al3Ti.
1. ВВЕДЕНИЕ
Сегодня соединения алюминида титана находят широкое применение в различных высокотемпературных приложениях благодаря высоким значениям отношения прочности к весу и низкому удельному весу [1]. Наиболее предпочтительными интерметаллическими соединениями бинарной Ti–Al системы являются TiAl, Ti3Al и Al3Ti [2]. Алюминиды типа Al3X, которые являются соединениями алюминия и химических элементов из групп IV-A (Ti, Zr, Hf) и V-A (V, Ta, Nb), привлекают внимание благодаря своему легкому весу и высокому сопротивлению к окислению в условиях высоких температур [2]. Соединение Al3Ti упорядочивается по типу D022 тетрагональной кристаллической структуры, производному от типа L12 с антифазной границей 1/2 [110] (001) [3]. Атомы алюминия составляют 75% от общего числа атомов соединения Al3Ti, что приводит к величине модуля Юнга 216 ГПa, хорошему сопротивлению к окислению и удельному весу (3.3 г/см3), более низкому, чем удельный вес других алюминидов титана [4].
Для синтеза Ti/Al многослойных композитов используются различные методики, такие как сварка взрывом [5], диффузионная сварка [6] и пайка-сварка [7]. Диффузионная сварка (как процесс соединения) включает в себя этапы связывания разнородных материалов в твердом и жидком состоянии [8]. Основным механизмом твердофазной диффузионной сварки является встречная диффузия атомов через границу сопряжения, приводящая к возникновению атомной связи в результате сопряжения при повышенных температурах соединяемых поверхностей посредством их локального деформирования [9]. Тем самым, важнейшими параметрами, определяющими эффективность диффузионной сварки, являются температура, время, приложенное давление и шероховатость поверхностей сопрягаемых частей [10]. Тремя важнейшими условиями, которые необходимо соблюдать перед началом диффузионной сварки для обеспечения однородности контакта, являются механическая близость сопрягаемых поверхностей, их чистота и гладкость [10]. Преимуществами диффузионной сварки являются ее экономичность, высокая прочность и плотность сопряжения, минимальное негативное воздействие на основной материал и возможность соединения разнородных материалов [8, 10]. Более того, комбинирование методов диффузионной сварки и сверхпластичного формообразования часто находит применение при производстве конструкций сложной формы (например, слоистых конструкций с сотовым заполнением) [8].
В последнее время диффузионная сварка осуществляется в комбинации с методами горячего прессования [6, 11–13] и горячей пакетной прокатки [6, 14]. В данной работе изготовление многослойного композита Ti/Al было проведено методом диффузионной сварки с использованием как горячего прессования, так и горячей пакетной прокатки. В статье обсуждены вопросы эволюции микроструктуры и кинетики роста слоя фазы Al3Ti.
2. МЕТОДИКА ЭКСПЕРИМЕНТА
Для получения многослойного композита методом пакетной прокатки были взяты листы титана (толщиной 0.7 мм) и алюминия (толщиной 2 мм). Химических составов материалов приведен в табл. 1. Поверхность листов была первоначально обработана стальной щеткой для повышения шероховатости, затем подвергнута ультразвуковой очистке в ацетоне и, наконец, размечена на прямоугольные участки размером 130 × 30 мм под будущие заготовки. Чередующиеся листы алюминия и титана были пакетированы в последовательности: алюминиевый слой между двумя титановыми (для образования трехслойной Ti/Al/Ti заготовки так, как показано на рис. 1).
Таблица 1.
Химический состав листов Ti и Al
Лист | Элементы, вес. % | ||||||
---|---|---|---|---|---|---|---|
Ti | Zr | V | Si | Fe | Al | Другие | |
Al | 0.002 | – | 0.011 | 0.121 | – | 99.8 | 0.066 |
Ti | 99.8 | 0.01 | – | – | 0.01 | 0.1 | 0.08 |
Этапы синтезирования многослойного композита Ti/Al были следующими (рис. 2): (i) соединение горячим прессованием при давлении сжатия 40 МПа и температуре 570°C с выдержкой в течение 1 ч – для формирования горячепрессованного образца, и затем (ii) горячая пакетная прокатка, при которой горячепрессованный образец был прокатан на 30% (уменьшения в толщине) при ~450°C и рассматривался уже как синтезированный в результате горячего пакетного прессования и прокатки.
Приготовленные образцы далее проходили изотермическую термообработку при 550, 600 и 650°C в течение 2, 4 и 6 ч в печи в атмосфере аргона с последующим охлаждением на воздухе.
Все образцы были разрезаны параллельно направлению прокатки для изучения микроструктуры. Фиксация образцов при приготовлении шлифов осуществлялась с помощью эпоксидной смолы. Для шлифования использовалась карборундовая наждачная бумага с размерами зерна от 80 до 1200 баллов. Окончательная полировка производилась с применением суспензии 3 мкм частиц Al2O3.
Аттестация микроструктуры и идентификация фаз производились методами растровой электронной микроскопии (РЭМ), энергодисперсионной спектрометрии (ЭДС) и рентгеноструктурного анализа (РСА).
3. РЕЗУЛЬТАТЫ И ОБСУЖДЕНИЕ
3.1. Аттестация микроструктуры и идентификация фаз
На рис. 3a и рис. 3б представлена микроструктура образцов, синтезированных посредством горячего пакетного прессования (ГПП) и посредством ГПП с последующей прокаткой (ГППП) соответственно. Светлые и темные области на изображениях отвечают слоям титана и алюминия, соответственно. Как можно видеть из рис. 3a и 3б, получено гладкое соединение слоев титана и алюминия без каких-либо дефектов их сопряжения – трещин и пустот. Как показано на рис. 3в и 3г, для образцов обоих типов на границе раздела титана и алюминия формируется непрерывный слой материала.
Рис. 3.
РЭМ изображения в моде обратно рассеянных электронов (BSE), дающие представление о морфологии структуры образцов, прошедших обработку (a) горячего пакетного прессования (ГПП) (б), и ГПП с последующей пакетной прокаткой (ГППП) (б, г).
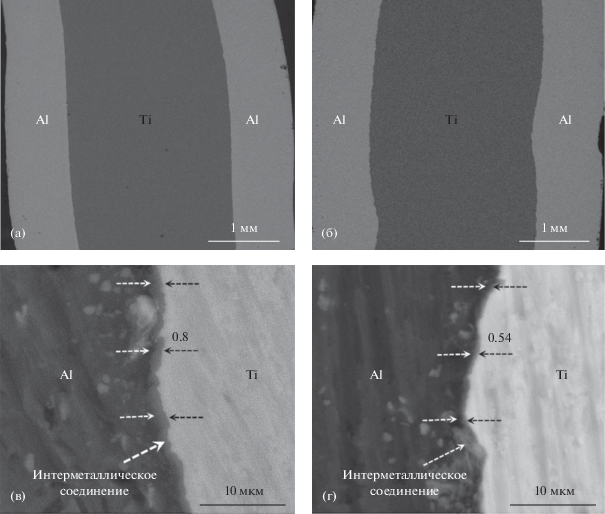
Согласно данным рентгеноструктурного (рис. 4) и ЭДС (рис. 5) анализа, Al3Ti – единственная интерметаллическая фаза, образовавшаяся на границе раздела разнородного материала, что хорошо согласуется с результатами предыдущих исследований [5, 6, 11–13, 15, 16]. На рис. 6 можно видеть, что толщина интерметаллидного слоя в образцах, синтезированных с помощью горячего пакетного прессования и прокатки, больше в сравнении с образцами ГПП, что является результатом деформационного наклепа. Другими словами, в процессе деформационного упрочнения неизбежно продуцируются дефекты кристаллического строения, такие как дислокации, которые обеспечивают дополнительные каналы диффузии, эффективно приводящие к возрастанию толщины разделительных слоев при повышенных температурах отжига [6].
Рис. 4.
Рентгенограмма композита, прошедшего горячее пакетное прессование и прокатку (ГППП) с последующим отжигом при 650°C продолжительностью 6 ч.
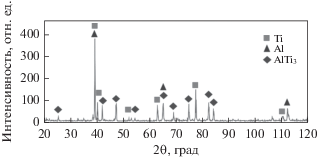
3.2. Характер роста соединения Al3Ti
При увеличении температуры и продолжительности отжига был отмечен и рост толщины слоя Al3Ti. Изображения этого сформировавшегося слоя Al3Ti были получены в результате съемки в обратно рассеянных электронах (BSE) после отжига при температуре 650°C в течение 2, 4 и 6 ч (см. рис. 7) и после отжигов продолжительностью 6 ч при температурах 550, 600°C (см. рис. 8). Средние значения толщины сформировавшегося слоя Al3Ti приведены в табл. 2.
Рис. 7.
РЭМ изображения (BSE), представляющие слой сопряжения разнородных материалов в образце композита, прошедшего отжиг при 650°C в течение 2 (а), 4 (б), 6 ч (в).
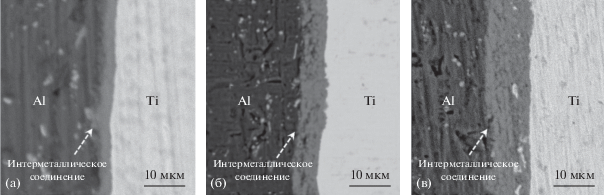
Рис. 8.
РЭМ изображения (BSE), представляющие слой сопряжения разнородных материалов в образце композита, прошедшего отжиг в течение 6 часов при температуре 550 (а), 600°C (б).
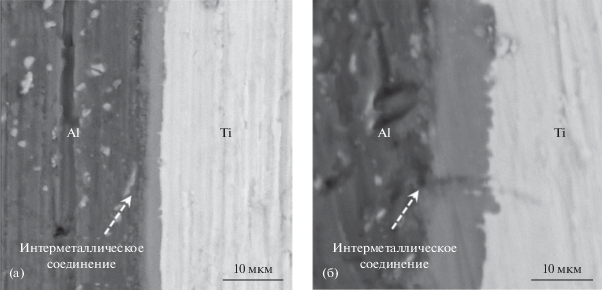
Таблица 2.
Средняя толщина Al3Ti слоев (Δx, мкм) после отжигов, различной продолжительности (t) и температуры (T). Экспериментальные данные
Т, °С | Время, ч | ||
---|---|---|---|
2 | 4 | 6 | |
550 | 0.70 | 1.00 | 2.77 |
600 | 2.40 | 3.70 | 8.50 |
650 | 3.50 | 7.50 | 8.80 |
Зависимость толщины этого слоя от величины температуры и продолжительности диффузионного процесса может быть описана уравнением [17]:
где x – толщина формирующегося слоя, k – постоянный коэффициент в законе роста, t – продолжительность диффузионного процесса и n – показатель степени в законе роста (n = 0.5 – в случае параболической кинетики роста, а при линейной n = 1) [17]. Использование значений из табл. 2 в уравнении (2) позволило установить зависимость толщины от продолжительности отжига. Вид этой зависимости представлен на рис. 9. Результаты ее линейного регрессивного анализа дали значения показателя степени в законе роста 1.17, 1.10 и 0.86 при температурах отжига 550, 600 и 650°C соответственно. Таким образом, значения показателя степени в законе роста оказались порядка единицы, что можно расценивать как свидетельство в пользу линейной кинетики роста формирующегося Al3Ti слоя.Рис. 9.
Зависимости ln x от ln t , построенные методом линейной регрессии с привлечением уравнения (2).
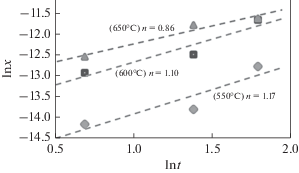
Энергия активации диффузионного роста подчиняется, как правило, температурной зависимости, характерной для закона Аррениуса [18]:
(3)
$k = A{\text{exp}}({{ - {{E}_{a}}} \mathord{\left/ {\vphantom {{ - {{E}_{a}}} {RT}}} \right. \kern-0em} {RT}});\quad$(4)
${\text{ln}}k = {\text{ln}}A--{{{{E}_{{\text{a}}}}} \mathord{\left/ {\vphantom {{{{E}_{{\text{a}}}}} {RT}}} \right. \kern-0em} {RT}},$Рис. 10.
Зависимость ln k от 1/T (обратной температуры), для описания роста толщины Al3Ti слоя, построенная методом линейной регрессии с привлечением уравнения (4).
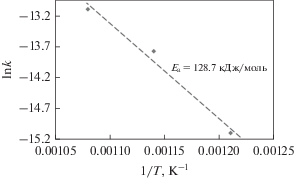
3.3. Формирование соединения Al3Ti
Как можно видеть на диаграмме состояния Ti/Al (рис. 11) [21], Al и Ti образуют между собой несколько соединений, включая Ti3Al, TiAl2, TiAl, Ti2Al5 и Al3Ti. В табл. 3 приведены выражения для свободной энергии образования соединений алюминида титана как функции температуры, которые позаимствованы из [22]. На рис. 12 представлены значения свободной энергии образования алюминидов титана, рассчитанные в температурной области от 300 до 900°C. Как видно на рис. 12, наименьшие значения свободной энергии образования отвечают соединениям TiAl2 и Ti2Al5. В свое время Раман и Шуберт пришли к заключению, что формирование TiAl2 и Ti2Al5 начинается с формирования TiAl3 [23]. Таким образом, считается, что среди алюминидов у Al3Ti самая низкая свободная энергия образования. Согласно модифицированной модели формирования алюминидов, базирующейся на оригинальном расчете значения эффективной энтальпии образования алюминида, предложенной авторами [24], для интерметаллида Al3Ti в сравнении с другими алюминидами характерно отрицательное значение эффективной энтальпии образования, максимальное по абсолютной величине. Так что Al3Ti – это первая фаза, которая зарождается и растет на границах Ti/Al (см. табл. 4). Указанный факт находится в согласии с результатами ЭДС анализа (см. рис. 5).
Таблица 3.
Температурная зависимость свободной энергии образования разнообразных интерметаллических Ti–Al соединений [22]
Соединения | Свободная энергия образования, Дж/моль |
---|---|
Ti3Al | –29 633.6 + 6.70801T |
TiAl | –37 445.1 + 16.79376T |
TiAl3 | –40 349.6 + 10.36525T |
TiAl2 | –43 858.4 + 11.02077T |
Ti2Al | –40 495.4 + 9.52964T |
Рис. 12.
Свободная энергия образования различных интерметаллидных соединений алюминида титана как функция температуры [28].
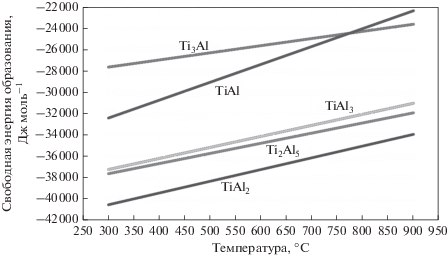
Таблица 4.
Рассчитанные значения ΔHo (стандартная энтальпия образования) и ΔHm (эффективная энтальпия образования) разнообразных интерметаллических соединений в бинарной системе Ti–Al [28]
Интерметаллические соединения | Лимитирующий элемент | ΔH°, кДж | ΔHm , кДж |
---|---|---|---|
TiAl2 | Титан | –43.8584 | –2.6580 |
Ti2Al5 | Титан | –40.4954 | –2.8358 |
TiAl3 | Титан | –40.3496 | –3.2279 |
TiAl | Титан | –37.4451 | –1.4978 |
Ti3Al | Титан | –29.6336 | –0.7902 |
3.4. Взаимная диффузия в бинарной системе Ti/Al
Изучая области диаграммы состояний Ti/Al, обогащенные Ti и Al (см. рис. 11 и рис. 13 ) [21, 25], можно убедиться, что при 550–650°C твердый раствор Al в Ti существует в широкой области составов, и максимальная растворимость Al в Ti составляет около 11.7 ат. %. В то же время, твердый раствор Ti в Al имеет узкую область существования, а растворимость Ti в Al составляет приблизительно 0.12 ат. % [21, 25]. Как видно из рис. 14a, следует ожидать, что при зарождении фазы Al3Ti насыщение твердого раствора Ti в Al протекает быстрее, чем насыщение твердого раствора Al в Ti. При росте слоя Al3Ti, процесс взаимной диффузии атомов Ti и Al следует представлять себе так, как показано на рис. 14б. Также, согласно рис. 15, рентгеновский анализ с привлечением метода картирования зоны реакции по разнородным компонентам свидетельствует в пользу взаимной диффузии атомов алюминия и титана. Из рис. 15 ясно, что титан и алюминий являются взаимно-диффундирующими элементами, но очевидна разница в количествах атомов, продиффундировавших в зоне реакции. За отмеченную разницу в диффузии ответственны значения коэффициентов диффузии. В общем случае, коэффициенты диффузии всех атомов обнаруживают тенденцию следовать закону Аррениуса. Так что мы имеем [21]:
где D – коэффициент самодиффузии, Do – предельное значение коэффициента диффузии (при T → ∞), Q – энергия активации диффузии, kB – постоянная Больцмана, T – абсолютная температура. В температурной области, исследованной в данном эксперименте, было справедливо соотношение $D_{{\text{o}}}^{{{\text{Al}}}} > D_{{\text{o}}}^{{{\text{Ti}}}}.$ Так что величина коэффициента диффузии зависела в основном от энергии активации диффузии, различной в различных интерметаллических соединениях. Результаты исследования на диффузионных парах Ti/Al в [26, 21 ] показывают, что значения энергии активации диффузии атомов алюминия и титана в объеме алюминидов титана зависят от величины композиционного отношения алюминия к титану в этом алюминиде. Например, с ростом величины указанного отношения алюминия к титану в алюминиде, как это происходит в последовательности Ti3Al → TiAl → → TiAl3, диффузия алюминия облегчается в сравнении с диффузией титана, и требуемая, таким образом, энергия активации диффузии алюминия в TiAl3 оказывается ниже, чем в случае Ti3Al. Авторы [26] также отметили, что диффузия атомов алюминия в Al3Ti более интенсивная в сравнении с диффузией атомов титана. Тем самым, диффузия титана лимитируется ростом формирующегося (в результате реакции) слоя, и, в итоге, рост Al3Ti продолжается на стороне титановой составляющей композита. Более того, в соединениях типа A3B (Al3Ti), кристаллизующихся в составляющей материала с кристаллической структурой, производной от L12, вокруг атома основного элемента A (Al) в его ближайшем соседстве находятся восемь атомов A (Al) и четыре атома B (Ti); при этом, каждый атом B (Ti) окружен двенадцатью атомами A (Al). Таким образом, соответствующий атом A (Al) способен диффундировать посредством обмена мест в узлах решетки с близлежащей вакансией без локального разупорядочения, тогда как перескоки атомов B (Ti) в близлежащий узел решетки предполагают участие связей, не отвечающих упорядоченному состоянию [27]. Поэтому алюминий расценивается как доминирующий диффундирующий элемент, что находится в согласии с результатами наблюдений, представленными в [26].Рис. 13.
Фрагмент диаграммы состояний бинарной системы Ti–Al, представляющий область, обогащенную алюминием [25].
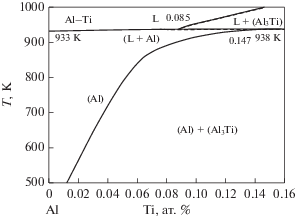
4. ВЫВОДЫ
В данном исследовании, рост слоя интерметаллического соединения Al3Ti в диффузионно сопряженных областях многослойного Ti/Al композита был изучен в температурной области от 550 до 650°C. Сделаны следующие основные выводы:
(1) Получены гладкие границы сопряжения титановых и алюминиевых слоев материала, причем без присутствия видимых трещин или пустот.
(2) Единственным интерметаллидом, наблюдавшимся в композите Ti/Al на границах сопряжения разнородного материала, оказался Al3Ti. Толщина слоя Al3Ti возрастала с увеличением температуры и продолжительности технологического отжига.
(3) При различных температурах отжига и его продолжительности были рассчитаны показатели степени в кинетическом законе роста толщины слоя Al3Ti и значение энергии активации его роста. Для температур 550, 600 и 650°C, значения показателя степени в кинетическом законе роста n составили 1.17, 1.10 и 0.86 соответственно. Значения степенного показателя в кинетическом законе роста, полученные при различных температурах отжига, оказались порядка единицы, что свидетельствует о линейности закона роста формирующегося слоя Al3Ti. Для линейной кинетики роста слоя Al3Ti в качестве значения энергии активации соответствующего события была предложена величина 128.7 кДж моль–1, что отвечает энергии активации диффузии алюминия в объеме слоя Al3Ti.
(4) Как Al, так и Ti представляли собой элементы, атомы которых диффундировали при исследованных температурах отжига. Однако доминирующей диффундирующей компонентой являлся алюминий, а рост Al3Ti слоя происходил главным образом по границам сопряжения Ti/Al3Ti.
Авторы хотели бы поблагодарить членов Совета по научным исследованиям Технического университета Саханда за обеспечение исследовательских возможностей при проведении осуществленных нами исследований.
Список литературы
Wu X. Review of alloy and process development of TiAl alloys // Intermetallics. 2006. V. 14. P. 1114–1122.
Stoloff N.S., Sikka V.K. Physical metallurgy and processing of intermetallic compounds. Springer Science & Business Media, 2012. 684 p.
Djanarthany S., Viala J.-C., Bouix J. An overview of monolithic titanium aluminides based on Ti3Al and TiAl // Materials Chemistry and Physics. 2001. V. 72. P. 301–319.
Sauthoff G. Intermetallics. Weinheim; N.Y.; Basel; Cambridge; Tokyo: VCH, 1995. 165 p.
Bataev I., Bataev A., Mali V., Pavliukova D. Structural and mechanical properties of metallic–intermetallic laminate composites produced by explosive welding and annealing // Materials & Design. 2012. V. 35. P. 225–234.
Xu L., Cui Y.Y., Hao Y.L., Yang R. Growth of intermetallic layer in multi-laminated Ti/Al diffusion couples // Mater. Sci. Eng.: A. 2006. V. 435–436. P. 638–647.
Chen S., Li L., Chen Y., Huang J. Joining mechanism of Ti/Al dissimilar alloys during laser welding- brazing process // J. of Alloys and Comp. 2011. V. 509. P. 891–898.
Shirzadi A.A. Diffusion Bonding Aluminum Alloys and Composites: New Approaches and Modelling. King’s College Cambridge, 1997. 158 p.
Diffusion bonding of materials / Ed. Kazakov N.F. Elsevier, 2013. 304 p.
Rusnaldy R. Diffusion bonding: an advanced of material process // Rotasi. 2001. V. 3. P. 23–27.
Liu J., Su Y., Xu Y., Luo L., Guo J., Fu H. First Phase Selection in Solid Ti/Al Diffusion Couple // Rare Metal Mater. and Eng. 2011. V. 40. P. 753–756.
Liu J.-P., Luo L.-S., Su Y.-Q., Xu Y.-J., Li X.-Z., Chen R.-R., Guo J.-J., Fu H.-Z. Numerical simulation of intermediate phase growth in Ti/Al alternate foils // Transactions of Nonferrous Metals Society of China. 2011. V. 21. P. 598–603.
Sun Y.-B., Zhao Y.-Q., Zhang D., Liu C.-Y., Diao H.-Y., Ma C.-L. Multilayered Ti–Al intermetallic sheets fabricated by cold rolling and annealing of titanium and aluminum foils // Transactions of Nonferrous Metals Society of China. 2011. V. 21. P. 1722–1727.
Oh J., Lee W., Pyo S.G., Park W., Lee S., Kim N.J. Microstructural analysis of multilayered titanium aluminide sheets fabricated by hot rolling and heat treatment// Metallurgical and Materials Transactions A. 2002. V. 33. P. 3649–3659.
Foadian F., Soltanieh M., Adeli M., Etminanbakhsh M. A Study on the Formation of Intermetallics During the Heat Treatment of Explosively Welded Al-Ti Multilayers // Metallurgical and Materials Transactions A. 2014. V. 45. P. 1823–1832.
Mirjalili M., Soltanieh M., Matsuura K., Ohno M. On the kinetics of TiAl3 intermetallic layer formation in the titanium and aluminum diffusion couple // Intermetallics. 2013. V. 32. P. 297–302.
Wagner C. The evaluation of data obtained with diffusion couples of binary single-phase and multiphase systems // Acta Metallurgica. 1969. V. 17. P. 99–107.
Mehrer H. Diffusion in solids: fundamentals, methods, materials, diffusion-controlled processes. Berlin, Heidelberg, N.Y. Springer Science & Business Media, 2007. 651 p.
Kidson G., Miller G. A Study of the Interdiffusion of Aluminum and Zirconium // J. of Nuclear Materials. 1964. V. 12. P. 61–69.
Van Loo F., Rieck G. Diffusion in the titanium-aluminum system–II. Interdiffusion in the composition range between 25 and 100 at. % Ti // Acta Metallurgica. 1973. V. 21. P. 73–84.
Mishin Y., Herzig C. Diffusion in the Ti–Al system // Acta Materialia. 2000. V. 48. P. 589–623.
Kattner U., Lin J.-C., Chang Y. Thermodynamic assessment and calculation of the Ti–Al system // Metallurgical Transactions A. 1992. V. 23. P. 2081–2090.
Raman A., Schubert K. On the constitution of some alloy series related to TiAl3. II. Investigations in some T4–Al–Si and T4…6-in systems // Z. Metallkd. 1965. V. 56. P. 44–52.
Laik A., Bhanumurthy K., Kale G. Intermetallics in the Zr–Al diffusion zone // Intermetallics. 2004. V. 12. P. 69–74.
Kerr H.W., Cisse J., Bolling G. On equilibrium and non-equilibrium peritectic transformations // Acta Metallurgica. 1974. V. 22. P. 677–686.
Van Loo F., Rieck G. Diffusion in the titanium-aluminium system–I. Interdiffusion between solid Al and Ti or Ti–Al alloys // Acta Metallurgica. 1973. V. 21. P. 61–71.
Nakajima H., Sprengel W., Nonaka K. Diffusion in intermetallic compounds // Intermetallics. 1996. V. 4. P. S17–S28.
Assari A.H., Eghbali B. Interfacial layers evolution during annealing in Ti–Al multi-laminated composite processed using hot press and roll bonding // Metals and Materials International. 2016. V. 22. P. 915–923.
Дополнительные материалы отсутствуют.
Инструменты
Физика металлов и металловедение