Физика металлов и металловедение, 2019, T. 120, № 5, стр. 477-483
Изучение влияния добавок ванадия на микроструктуру и механические свойства свежелитого и аустенитизированного высокопрочного чугуна
Х. Бахшинежад a, А. Хонарбахшрауф a, *, Х. Абдолла-Пур a
a Факультет материалов и металлургии, Семнанский университет
Семнан, Иран
* E-mail: ahonarbakhsh@semnan.ac
Поступила в редакцию 12.07.2017
После доработки 08.09.2018
Принята к публикации 10.12.2018
Аннотация
Присутствие ванадия как легирующего элемента по-разному сказывается на свойствах литейных чугунов. Изучено влияние различного объема добавок ванадия, включая 0, 0.87 и 1.45 вес. %, на микроструктуру, на формирование различных фаз и на механические свойства свежелитого и аустенитизированного высокопрочного (АВП) чугуна. После отливки, приготовления и определения химического состава образцов были проведены их термообработка (ТО) по аустенитизации при 900°C в течение 45 мин и TO, состоящая в закалке с изотермической выдержкой в бейнитной области в течение 60 мин при 350°C. Тесты на растяжение и ударную вязкость, а также рентгеноструктурный анализ (РСА) и металлографические (ОМ) исследования были проведены с целью изучить механические свойства и структуру АВП чугуна. Микроструктура образцов включала карбиды в аусферритной матрице. Результаты показали, что с ростом содержания ванадия, прочность на растяжение и работа ударного разрушения высокопрочного чугуна (с шаровидным графитом) уменьшаются, тогда как ТО может улучшить эти показатели.
ВВЕДЕНИЕ
Аустенитизированный высокопрочный чугун (АВПЧ) был создан как перспективный конструкционный материал с уникальным сочетанием таких свойств, как хорошая деформируемость, прочность [1–4], износостойкость [5–7], усталостная прочность [8–10] и вязкость разрушения [11–14].
Привлекательные и выдающиеся свойства АВПЧ относят на счет его уникальной микроструктуры. Когда термообработка (TO), состоящая в закалке с изотермической выдержкой в бейнитной области (ЗВБО), проводится на высокопрочном чугуне (ВПЧ), возникает микроструктура, состоящая из феррита (α) и высокоуглеродистого аустенита (γВУ) с шаровидным графитом в матрице, совершенно отличная от микроструктуры, формирующейся в сталях после ЗВБО и состоящей из феррита и карбида (бейнита). По этой причине продукт ЗВБО реакции в ВПЧ чаще называют аусферритом, чем бейнитом [2, 15].
Превращение в ВПЧ при ЗБВО проходит в два этапа (по двухступенчатой реакции). На первом этапе первичный аустенит (γ) распадается на игольчатый феррит и высокоуглеродистый аустенит [2, 3, 16]:
Если литье осуществляется при ЗБВО температуре в течение продолжительного времени, будет происходить вторая реакция. На этом этапе высокоуглеродистый аустенит может распадаться на феррит и карбид:
Наилучшие свойства АВПЧ достигаются после завершения первого этапа (1-ой реакции) и перед стартом 2-ой реакции (второго этапа). Этот промежуток времени между моментом окончания 1-ой реакции и началом второго этапа превращения получил название “технологического окна”. Для того чтобы увеличить протяженность “технологического окна”, осуществляют добавку таких химических элементов, как никель, молибден и медь. Эти элементы предотвращают дальнейший распад аустенита в перлит и феррит при охлаждении [15–19].
Указанные легирующие добавки в чугуне имеют огромное влияние на микроструктуру и свойства АВПЧ. Контролируя химический состав и параметры ТО, можно получить различный размер, форму и пространственное распределение гранул шарового графита, а также обеспечить контроль за микроструктурой матрицы. Такие легирующие элементы, как кремний, медь, никель, молибден, хром, ванадий и титан находят в этом случае обычное применение [20].
Во многих статьях показано, что добавка ванадия сказывается на микроструктуре матрицы чугуна. Поскольку ванадий является стабилизатором карбида, его добавка сказывается и на улучшении затвердевания метастабильной подсистемы аустенит–цементит, и как следствие, она обнаруживает тенденцию способствовать формированию эвтектического карбида [21–25].
Было установлено, что добавка ванадия вплоть до 0.5 вес. % слегка снижает количество глобулярного графита. Подобно многим другим элементам, ванадий ограничивает формирование аустенита в железе за счет сужения области существования аустенита на равновесной диаграмме состояний системы Fe–C. Это означает, что ванадий отчасти способствует увеличению образования феррита, и, следовательно, температура превращения возрастает. Когда ванадий добавляют в чугун, в микроскопе можно наблюдать маленькие светлого контраста включения. Также улучшаются предел текучести и прочности на растяжение, а вместе с ними и износостойкость материала [23–25].
Итак, в этой работе мы исследовали влияние добавки 0.87 или 1.45 вес. % ванадия вместе с ЗВБО термообработкой на механические свойства, микроструктуру и колебания фазового состава ВП чугуна.
МЕТОДИКА ЭКСПЕРИМЕНТА
Формы для литья были изготовлены в песке с привлечением натриевого жидкого стекла в качестве связующего компонента и углекислого (CO2) газа, для получения Y-образных отливок размером 55 × 150 × 180 мм (согласно рекомендациям ASTM стандарта A897/A897M-16). Для противодействия эффекту давления, возникающему из-за увеличения удельного объема графита при затвердевании, все изложницы были изготовлены за 24 ч до начала процедуры литья, с целью достижения требуемой прочности конструкции. Расплавы высокопрочного чугуна были приготовлены из слитков доменного чугуна и ферросплавов с использованием индукционной 3-кГц плавильной печи с объемом загрузки 25 кг и номинальной мощностью 60 кВт. Ванадий добавляли в расплав в форме феррованадия при 1550°C перед разливкой. После удаления шлака каждая порция расплава была разлита в льячку, предварительно нагретую до 1570°C. Затем плунжерным методом была проведена сфероидизирующая обработка расплава отливки, с использованием достаточного количества Fe–Si–5% Mg. Для того чтобы вызвать кристаллизацию расплава, в нее окончательно добавляли Fe–75% Si-сплав.
Все объемы плавок были разлиты в изложницы при температурах 1350–1370°C. Их итоговый химический состав определяли электроискровым оптикоэмиссионным спектроскопическим методом (см. табл. 1).
Таблица 1.
Химический состав свежелитых высокопрочных чугунов (вес. %)
Материал | C | Si | Mn | S | P | Mg | V | Fe |
---|---|---|---|---|---|---|---|---|
ВПЧ | 3.67 | 2.41 | 0.03 | 0.018 | 0.023 | 0.03 | – | Ост. |
ВПЧ с 0.87% V | 3.65 | 2.43 | 0.06 | 0.015 | 0.021 | 0.03 | 0.87 | Ост. |
ВПЧ с 1.45% V | 3.65 | 2.44 | 0.07 | 0.016 | 0.023 | 0.03 | 1.45 | Ост. |
Образцы были приготовлены с прицелом на проведение тестов на растяжение и разрывных испытаний по методу Шарпи из нижней части Y‑блоков (в соответствии с рекомендациями ASTM, по стандартам A897 и ASTM E23 соответственно).
ТО по аустенитизации была проведена при 900°C в течение 45 мин в муфельной печи, а затем в течение 60 мин в соляной ванне температурой 350°C была осуществлена ЗВБО термообработка. Микроструктура образцов была исследована методом оптической микроскопии после их полировки и травления 2%-ным раствором Ниталя (раствор азотной кислоты в спирте) при комнатной температуре.
Для изучения морфологии матрицы были использованы РСА-методы, позволившие оценить объемную долю аустенита, а также размеры ячейки феррита. Рентгеновская съемка проведена в CuKα-излучении при 35 кВ и силе тока 30 мA, в диапазоне углов дифракции 2θ от 35° до 85°, скорость сканирования 1°/мм. Полученные дифракционные профили были изучены для установления положения пиков интенсивности рассеяния и фазовой структуры с помощью компьютерной программы X’Pert High Score. Для феррита были рассмотрены рефлексы от плоскостей (110), (200) и (211) ОЦК решетки, а для аустенита – рефлексы от плоскостей (111), (200) и (220) ГЦК-решетки.
Для определения объемной доли аустенита Vγ в матрице высокопрочного чугуна, прошедшего ЗВБО термообработку, было использовано следующее уравнение:
где Iα –пик интенсивности (110) от феррита (α), Iγ – пик интенсивности (111) от аустенита (γ), R – константа, характерная для проведенных измерений, величиной 0.85.Для определения размера ферритного зерна (d) было использовано уравнение Шерера:
где λ – длина волны падающего рентгеновского излучения, β – ширина (211) пика от феррита на половине высоты в радианах, θ – угол Брэгговского отражения [26–28].РЕЗУЛЬТАТЫ И ОБСУЖДЕНИЕ
В работе были исследованы образцы различного состава – с ванадием и без него, а также прошедшие или не прошедшие ЗВБО термообработку. На рис. 1 представлены изображения микроструктуры свежелитых образцов после травления. Как видно на рис. 1a, микроструктура свежелитого образца ВП чугуна без ванадия содержит гранулы шарового графита в ферритной и перлитной матрице. На рис. 1б, в представлены изображения микроструктуры свежелитых образцов с ванадием. Фазовая структура была проанализирована РСА методами.
Рис. 1.
Микроструктура образцов перед ЗВБО термообработкой: a – ВПЧ, б – ВПЧ с 0.87 вес. % V, в – ВПЧ с 1.45 вес. % V.
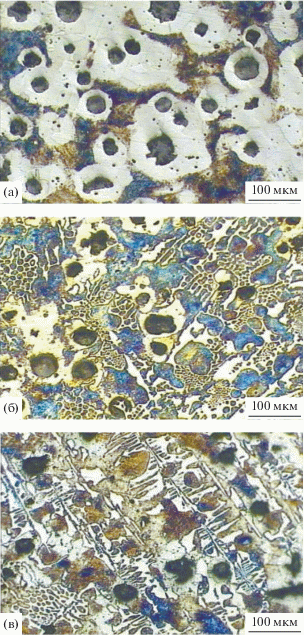
Рентгеновские дифрактограммы свежелитых образцов представлены на рис. 2. Рентгеновская дифрактограмма свежелитого образца ВПЧ без ванадия (рис. 2a) показывает, что ферритная фаза (α) фиксируется при 2θ углах 44°, 65° и 82°, что соответствует (110), (200) и (211) плоскостям, наряду с присутствием карбидной фазы Fe5C2. На рис. 2б, в показано, что с добавкой ванадия появляется карбид V4C3, вдобавок к ферритной (α) и карбидной (Fe3C)-фазам.
Рис. 2.
Дифрактограммы образцов перед их ЗВБО т/обработкой: a – ВПЧ, б – ВПЧ с 0.87 вес. % V, в – ВПЧ с 1.45 вес. % V.
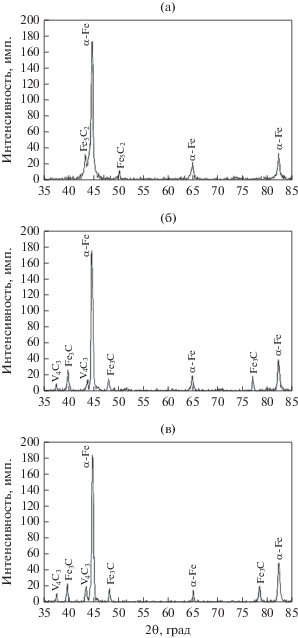
Во время затвердевания расплава ванадий способствует формированию эвтектического карбида железа, что объясняется снижением стабильной эвтектической температуры наряду с увеличением соответствующей метастабильной температуры. Также ванадий в некоторой степени способствует формированию перлита во время эвтектоидного превращения. Наблюдается и тот факт, что добавка ванадия приводит к формированию в микроструктуре дополнительной фазы [23–25]. В твердом состоянии растворимость легирующего элемента уменьшается с падением температуры. Таким образом, когда аустенит насыщается ванадием, дальнейшее его охлаждение приводит к выпадению карбида ванадия. Растворение легирующих элементов в жидких и твердых фазах железа приводит к изменениям в равновесной диаграмме состояний системы Fe–C.
В общем случае элементы, добавка которых приводит к увеличению разницы между эвтектическими стабильной и метастабильной температурами, способствуют формированию графита, тогда как элементы, добавка которых приводит к сокращению указанной разницы, увеличивают формирование карбида. Ванадий принадлежит к числу тех легирующих элементов, которые снижают “зазор” между эвтектическими стабильной и метастабильной температурами и тем самым способствует карбидообразованию [29–31].
Микроструктура образцов после их ЗВБО термообработки представлена на рис. 3. Видно, что в объеме матрицы, наряду с игольчатым ферритом также наблюдается аустенит (аусферрит) с дисперсными гранулами шарового графита. С ростом величины добавки ванадия, оказалось, что количество игольчатого феррита в матрице снижается. Присутствие ванадия привело к формированию грубых эвтектических карбидов пластинчатой, блочной и ячеистой морфологии. Это отмечается и в работах других авторов [32, 33].
Можно утверждать, что присутствие в микроструктуре обогащенных ванадием грубых частиц есть результат эвтектической реакции во время затвердевания в межячеистых областях, которые обогащены по ванадию и углероду.
По дифрактограммам можно судить и о кристаллической структуре образцов после их ЗВБО термообработки. Результаты РСА представлены на рис. 4. Рентгеновская дифрактограмма образцов после их ЗВБО термообработки, представленная на рис. 4a, показывает, что ферритная и аустенитная фазы с ГЦК кристаллической решеткой фиксируются при 2θ углах в 43°, 50° и 74°, с отвечающими им плоскостями
Рис. 4.
Дифрактограммы образцов после их ЗВБО термообработки. a – АВПЧ, б – АВПЧ с 0.87 вес. % V, в – АВПЧ с 1.45 вес. % V.
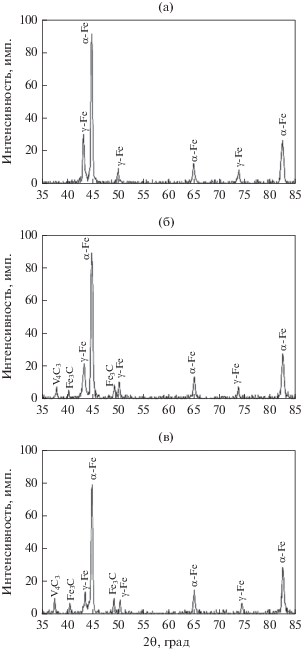
(111), (200) и (220), соответственно. На рис. 4б, в присутствие в наших образцах карбида ванадия V4C3 (на 37° съемки, а также присутствие карбида железа Fe3C на 40° и 49°) подтверждается этими рентгенограммами.
После ЗВБО термообработки интенсивность карбидных пиков ослабевает. Для проведения сравнения пиков интенсивности рассеяния от феррита и аустенита возьмем пик (110) для феррита и пик (111) для аустенита. Интенсивности обоих пиков снижаются при возрастании содержания ванадия. В образцах свежелитого высокопрочного чугуна максимум интенсивности пика рассеяния от феррита наблюдается на образце, содержащем 1.45 вес. % ванадия. На ЗВБО образцах ВП чугуна максимум интенсивности пиков рассеяния от феррита и аустенита наблюдается на образцах, нелегированных ванадием. С ростом содержания ванадия, интенсивности пиков рассеяния от феррита и аустенита уменьшаются по высоте. Из сравнения ВПЧ и АВПЧ образцов следует, что максимальная интенсивность пика рассеяния от феррита наблюдается на образце, содержащем 1.45 вес. % ванадия.
О том, как сказывается добавка ванадия на величину объемной доли аустенита, можно судить по данным табл. 2. Результаты показывают, что объемная доля аустенита уменьшается с ростом содержания ванадия. Добавка ванадия приводит к формированию карбидов ванадия, которые вполне могут сохраняться нерастворенными в процессе ЗВБО термообработки.
Таблица 2.
Эффект ванадия на объемную долю аустенита, размер зерна феррита, прочность на растяжение и энергию ударного разрушения
Тип чугуна | Объемная доля аустенита, % | Размер зерна феррита, нм | Прочность на растяжение, Н/мм2, ±10% | Энергия ударного разрушения, Дж, ±5% |
---|---|---|---|---|
ВПЧ | – | 72.9 | 532 | 10 |
АВПЧ | 28 | 77.1 | 968 | 12 |
ВПЧ с 0.87% V | – | 58.3 | 404 | 4 |
АВПЧ с 0.87% V | 22 | 62.5 | 639 | 5 |
ВПЧ с 1.45% V | – | 45.5 | 374 | 2.4 |
АВПЧ с 1.45% V | 17 | 53.5 | 621 | 3 |
Результаты измерения размера зерна феррита на различных образцах также приведены в табл. 2. Отмечено, что частицы карбида ванадия выступают в качестве центров зарождения феррита. Tем самым увеличение числа таких центров зарождения во время аустенит–ферритного превращения приводит к снижению размера зерна феррита [30, 34]. Основываясь на теориях роста зерен, в материалах с частицами вторичных фаз [35] на росте зерен должны сказываться эффекты пиннинга межзеренных границ на таких частицах. Поэтому размер ферритного зерна уменьшается по мере увеличения объемной доли этих частиц. С другой стороны, наша термообработка привела к росту ферритного зерна, что можно объяснить сокращением при ней числа центров зарождения феррита, а также уменьшением объемной доли выделений карбида.
О том, как сказывается добавка ванадия на прочности на растяжение наших образцов, можно судить по данным табл. 2. В свежелитых образцах рост содержания ванадия сопровождается монотонной убылью прочности на растяжение. После ЗВБО термообработки ВПЧ образцов прочность на растяжение достигает своего максимального значения 968 Н/мм2, и затем, с ростом добавки ванадия, она снижается по мере уменьшения количества игольчатого феррита. Таким образом, проводя ЗВБО термообработку, мы снижаем эффективное влияние ванадия на рост температуры вязко-хрупкого перехода, улучшаем структуру и увеличиваем прочность на растяжение.
Результаты измерений энергии ударного разрушения (ЭУР) образцов ВПЧ с разным содержанием ванадия также представлены в табл. 2. С ростом добавки ванадия, ЭУР образцов снижается за счет возрастания хрупкости. Для АВПЧ образцов значения ЭУР слегка выше в сравнении с ВПЧ образцами, что может быть связано с более высокой способностью аусферритной матрицы к деформированию.
Карбидная фаза зарождается и растет на оксидных бимолекулярных пленках. Эти бимолекулярные пленки (БМП) представляют собой окисленные “обломки” поверхности расплава, которые наслаиваются, наезжая друг на друга во время помешивания или разливания расплава, и каждая, испытывая всестороннюю компрессию, оказывается в объеме расплава во взвешенном состоянии (как в суспензии) [36]. Эти БМП могут действовать в роли трещин внутри карбидов, вырастающих с включением БМП в себя и оказывающихся в хрупком состоянии. Эти БМП в ВПЧ могут приводить к сокращению объема пор и к возникновению поверхностей хрупкого (откольного) разрушения, являющихся большими, гладкими и в основном состоящих из фасеток хрупкого разрушения и, следовательно, приводящих к снижению механических свойств. Аустенитизация может оказывать позитивный эффект, так что она может приводить к упрочнению на оксид-оксидных интерфейсах в центральной части БМП, и как результат, БМП уже не могут всегда выступать в роли зародышей трещин.
ВЫВОДЫ
1. Рост содержания ванадия приводит к уменьшению размера ферритного зерна, объемной доли аустенита, прочности на растяжение и энергии ударного разрушения. С ростом содержания ванадия, количество карбидов возрастает, что и сказывается на отмеченных выше свойствах.
2. Аустенитизация образцов при 900°C в течение 45 мин и последующая закалка с изотермической выдержкой в бейнитной области при 350°C в течение 60 мин (ЗВБО обработка) приводят в итоге к увеличению размера ферритного зерна, прочности на растяжение и энергии ударного разрушения в сравнении с образцами, не подвергавшимися указанной комплексной термообработке.
Список литературы
Harding R.A., Gilbert G.N.J. Why the properties of ductile irons should interest engineers // Br. Foundrym. 1986. V. 79. P. 489–496.
Dodd J. High strength, high ductility ductile irons. // Mod. Cast. 1978. V. 68(5). P. 60–66.
Gundlach R.B., Janowak J.F. Development of a ductile iron for commercial austempering // AFS Trans. 1983. V. 94. P. 377–388.
Johansson M. Austenitic bainitic ductile iron // AFS Trans. 1977. V. 85. P. 117–122.
Schmidt I., Schuchert A. Unlubricated wear of austempered ductile cast iron // Z. Metall. 1987. V. 78. P. 871–875.
Sahin Y., Erdogan M., Kilicli V. Wear behavior of austempered ductile irons with dual matrix structures // Mater. Sci. Eng. A. 2007. V. 444. P. 31–38.
Bartosiewicz L., Krause A.R., Alberts F.A., Iqbal Singh, Putatunda S.K. Influence of microstructure on high cycle fatigue behavior of austempered ductile cast iron // Mater. Charact. 1993. V. 30(4). P. 221–234.
Shanmugam P., Rao P.P., Udupa K.R., Venkataraman N. Effect of microstructure on the fatigue strength of an austempered ductile Iron // J. Mater. Sci. 1994. V. 29(18). P. 4933–4940.
Bartosiewicz L., Krause A.R., Sengupta A., Putatunda S.K. Relationship between fatigue threshold and fatigue strength in austempered ductile cast iron // Int. Symp. Test. Fail. Anal. 1990. V. 16. P. 323–336.
Bartosiewicz L., Duraiswamy S., Sengupta A., Putatunda S.K. Near threshold fatigue crack growth behavior of austempered ductile cast iron // Morris Fine Symp. 1991. 135–138.
Rao P.P., Putatunda S.K. Influence of microstructure on fracture toughness of austempered ductile cast iron // Met. Mater. Trans. A. 1997. V. 28. P. 1457–1470.
Janowak J.F., Norton P.A. A guide to mechanical properties possible by austempering, 1.5% Ni, 0.3% Mo iron // AFS Trans. 1985. V. 88. P. 123–135.
Putatunda S.K., Singh I. Fracture toughness of unalloyed austempered ductile cast iron // J. Test. Eval. 1995. V. 23. P. 325–332.
Doong J.L., Chen C. Fracture toughness of bainitic-nodular cast iron // Fatigue Fract. Eng. Mater. Struct. 1989. V. 12. P. 155–165.
Putatunda S.K., Kesani S., Tackett R., Lawes G. Development of austenite free ADI (austempered ductile cast iron) // Mater. Sci. Eng. A 2006. V. 435–436. P. 112–122.
Moore D.J., Rouns T.N., Rundamn K.B. The effect of heat treatment, mechanical deformation, and alloying element additions on the rate of bainite formation in austempered ductile irons // J. Heat Treat. 1985. V. 4(1). P. 7–24.
Janowak J.F., Gundlach R.B., Eldis G.T., Rohrting K. Technical advances in cast iron metallurgy // AFS Int. J. Cast Met. 1982. V. 6. P. 28–42.
Eric O., Sidjanin L., Miskovic Z., Zec S., Jovanovic M.T. Microstructure and toughness of Cu–Ni–Mo austempered ductile iron // Mater. Lett. 2004. V. 58. P. 2707–2711.
Yang J., Putatunda S.K. Improvement in strength and toughness of austempered ductile cast iron by a novel two-step austempering process // Mater. Des. 2004. V. 25. P. 219–230.
Kiani-Rashid A.R. The bainite transformation and the carbide precipitation of 4.88% aluminium austempered ductile iron investigated using electron microscopy // J. Alloy. Compd. 2009. V. 477. P. 490–198.
Ohide T., Ikawan K. Effect of vanadium on the as-cast and isothermally transformed structures of spheroidal graphite cast iron // J. Jpn. Foundrym. Soc. 1985. V. 57. P. 522–527.
Maselenkov S.B., Teikh V.A., Silman G.I., Thomas V.K. Distribution of V, Mo, Cu, and W in cast iron // J. Rus. Cast. Prod. 1969. P. 375–377.
Filippov A.S., Blank E.M., Ivelier V.S. Influence of vanadium additions on the structure and properties of irons // J. Rus. Cast. Prod. 1969. P. 289–291.
Barton R. The influence of alloying elements in cast iron // J. Br. Cast Iron Res. Assoc. 1960. V. 8. P. 567–585.
Dawson J.V. Vanadium in cast iron // Uk Inter. Exch. Pap. 1982. P. 1–16.
Myszkaa D., Gietka T. Comparing the possibilities of austenite content determination in austempered ductile iron // Arch. Found. Eng. 2011. V. 11. P. 135–140.
Gietka T., Dymski S. The attempt at evaluation of the ADI microstructure with the use of the image analysis // Arch. Found. Eng. 2010. V. 10. P. 57–62.
Cullity B.D. Elements of X-ray diffraction, 2nd edn., 1974.
Rezvani M., Harding R.A., Campbell J. The effect of vanadium in as-cast ductile iron // Int. J. Cast Met. Res. 1997. V. 10. P. 1–15.
Todd J.A., Li P. Microstructure mechanical properties relationships in isothermally transformed vanadium steels // Met. Trans. A. 1986. V. 17. P. 1991–1202.
Ubhi H.S., Baker T.N. The influence of manganese and silicon on the precipitation of vanadium carbide in steel // Mater. Sci. Eng. 1988. P. 189–199.
Laino S., Sikora J.A., Dommarco R.C. Development of wear resistant carbidic austempered ductile iron (CADI) // Wear. 2008. V. 265. P. 1–7.
Sun X., Wang Y., Li D.Y., Wang G. Modification of carbidic austempered ductile iron with nano ceria for improved mechanical properties and abrasive wear resistance // Wear. 2013. V. 301. P. 116–121.
Crooks M.J., Garrate-Reed A.J., Van der Sande J.B., Owen W.S. The isothermal austenite ferrite transformation in some deformed vanadium steels // Met.Trans. A. 1982. V. 13. P. 1347–1353.
Fan D., Chen L., Ping S.P. Numerical simulaton of Zener pinning with growing second-phase particles // J. Am. Ceram. Soc. 1998. V. 81. P. 526–532.
Campbell J. Castings. 2nd edn., Butterworth, 2003.
Дополнительные материалы отсутствуют.
Инструменты
Физика металлов и металловедение