Физика металлов и металловедение, 2020, T. 121, № 1, стр. 25-31
Влияние добавок скандия на температурную зависимость теплоемкости и термодинамических функций алюминиево-магниевых сплавов
И. Н. Ганиев a, *, М. Т. Норова b, Б. Б. Эшов b, Н. Ф. Иброхимов c, С. Ж. Иброхимов c
a Институт химии им. В.И. Никитина Академии наук Республики Таджикистан
734063 , Душанбе, ул. Айни, 299/2, Таджикистан
b Государственное научное учреждение “Центр исследования инновационных технологий при Академии наук Республики Таджикистан”
734063 , Душанбе, ул. Айни, 299/3, Таджикистан
c Таджикский технический университет им. М.С. Осими
734042 , Душанбе, ул. акад. Раджабовых, 10, Таджикистан
* E-mail: ganiev48@mail.ru
Поступила в редакцию 06.05.2019
После доработки 25.06.2019
Принята к публикации 10.07.2019
Аннотация
Для измерения удельной теплоемкости использован метод “охлаждения”, основанный на законе охлаждения Ньютона–Рихмана. Показано, что в алюминиево-магниевых сплавах с ростом концентрации магния и температуры удельная теплоемкость сплавов растет, а от содержания скандия – незначительно уменьшается. Удельные энтальпия и энтропия сплавов с повышением температуры растут, а значение удельной энергии Гиббса – уменьшается. Добавки скандия практически не влияют на изменение термодинамических функций сплавов.
ВВЕДЕНИЕ
Алюминиево-магниевые сплавы широко используются в промышленности. К сплавам системы Al–Mg относится большая группа широко используемых в промышленности сплавов типа АМг1, АМг2, АМг3, АМг4 и АМг6. С ростом содержания магния в сплавах типа “магналий” твердость и усталостная прочность повышается, а пластичность понижается. Эти сплавы отличаются высокой пластичностью, хорошей свариваемостью и высокой коррозионной стойкостью.
Для улучшения свойств сплавы типа “магналий” подвергаются легированию различными компонентами. Также следует отметить, что разработка состава новых сплавов на основе алюминия с заданными характеристиками возможна при наличии информации о термодинамических свойствах каждого отдельного компонента, составляющих систему в целом. Перспективным является модифицирование алюминиевых сплавов металлами, которые мало растворяются или практически не растворимы в твердом алюминии, но образуют с алюминием различные химические соединения, в частности редкоземельные металлы [1–7].
Изучение теплоемкости является одним из основных методов исследования структурных и фазовых превращений в сплавах. Из температурной зависимости теплоемкости можно определить другие физические характеристики твердого тела: температуру и тип фазового превращения, температуру Дебая, энергию образования вакансий, коэффициент электронной теплоемкости и др.
ТЕОРИЯ И ОПИСАНИЕ МЕТОДА
Для измерения удельной теплоемкости сплавов в широкой области температур использовался закон охлаждения Ньютона–Рихмана. Всякое тело, имеющее температуру выше окружающей среды, будет охлаждаться, причем скорость охлаждения зависит от величины теплоемкости тела. Если взять два одинаковой формы металлических образца и охлаждать их от одной температуры, то по кривым охлаждения можно найти теплоемкость одного образца, зная теплоемкость другого (эталона).
Количество тепла, теряемого объемом dV металла за время dτ, равно
где $С_{Р}^{0}$ – удельная теплоемкость металла, $\rho $ – плотность металла, Т – температура образца (принимается одинаковой во всех точках образца, так как линейные размеры тела малы, а теплопроводность металла велика).Величину $\delta Q$ можно подсчитать по закону:
где dS – площадь поверхности, T0 – температура окружающей среды, α – коэффициент теплоотдачи.Приравнивая выражения (1) и (2), получим
Полагая, что $С_{Р}^{0},$ ρ и $\frac{{dT}}{{d\tau }}$ не зависят от координат точек в объеме, а α, Т и Т0 не зависят от координат точек на поверхности образца, можно записать
или
где V – объем всего образца, а ρV = m – масса, S – площадь поверхности всего образца.Соотношение (5) для двух образцов одинакового размера при допущении, что S1 = S2, T1 = T2, α1 = α2, можно представить так:
(6)
$C_{{{{P}_{2}}}}^{0} = С_{{{{P}_{1}}}}^{0}\frac{{{{m}_{1}}}}{{{{m}_{2}}}}\frac{{{{{\left( {\frac{{dT}}{{d\tau }}} \right)}}_{1}}}}{{{{{\left( {\frac{{dT}}{{d\tau }}} \right)}}_{2}}}} = С_{{{{P}_{1}}}}^{0}\frac{{{{m}_{1}}}}{{{{m}_{2}}}}\frac{{{{{\left( {\frac{{\Delta T}}{{\Delta \tau }}} \right)}}_{1}}}}{{{{{\left( {\frac{{\Delta T}}{{\Delta \tau }}} \right)}}_{2}}}},$Следовательно, зная массы образцов m1 и m2, скорости охлаждения эталона и изучаемого образца и удельную теплоемкость эталона $C_{{{{P}_{1}}}}^{0}$, можно вычислить удельную теплоемкость $С_{{{{P}_{2}}}}^{0}$ исследуемого образца из первой части уравнения (6).
Измерение теплоемкости проводилось на установке, схема которой представлена на рис. 1. Электропечь 3 смонтирована на скамье, по которой она может перемещаться вправо и влево. Образец 4 (тоже может перемещаться) представляет собой цилиндр высотой 30 мм и диаметром 16 мм с высверленным каналом с одного торца, в который вставлена термопара. Концы термопары подведены к измерителю Digital Multimeter UT71B 7, который осуществлял прямую фиксацию результатов измерений на компьютере 8 в виде таблицы. Используя табличные данные, были построены кривые охлаждения образцов из исследуемых сплавов.
ЭКСПЕРИМЕНТАЛЬНЫЕ РЕЗУЛЬТАТЫ И ИХ ОБСУЖДЕНИЕ
Синтез алюминиево-магниевых сплавов проводился в шахтной лабораторной печи типа СШОЛ под слоем флюса. Для синтеза сплавов были использованы алюминий марки А7 (ГОСТ 11069-2001), магний марки Мг95 (ГОСТ 804-93) и лигатура на основе алюминия, содержащая 2.0 мас. % скандия. Содержание магния в сплаве АМг2 составило 2 мас. %, в сплаве АМг3 – 3 мас. %, а сплаве АМг4 – 4 мас. %. Магний вводили в расплав алюминия в завернутом в алюминиевую фольгу виде. Содержание скандия в сплавах составляло 0.01; 0.05; 0.1 и 0.5 мас. %.
Состав сплавов контролировали методом атомно-эмиссионного спектрального анализа на дифракционном спектрографе ДФС-452 с многоканальной оптической регистрирующей системой МОРС-9. При этом в качестве источника возбуждения была использована электрическая дуга. На рис. 2 приведены аналитические линии для магния и скандия, которые показывают наличие магния, скандия и примесей в сплаве.
Рис. 2.
Интенсивность спектральных линий для магния и цинка (а) и скандия (б) в сплаве АМг4: ▲ – Mg, △ – Mg–, ◼ ‒ Zn, ⚫ – Sc.
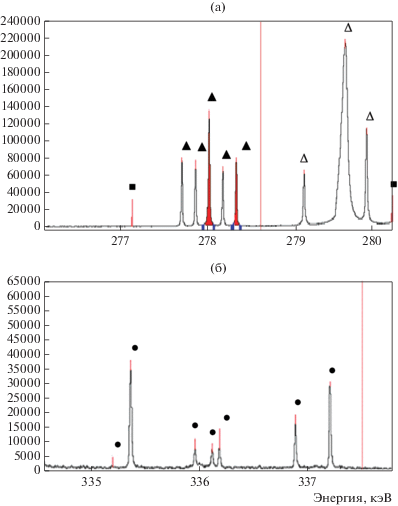
Микроструктурное исследование сплавов. Для проведения микроанализа на образцах исследуемых сплавов путем шлифования, полирования и травления были приготовлены микрошлифы. Образцы вырезали ручной ножовкой, не допуская при этом сильного нагрева образцов. Размер микрошлифов составлял 1.5–2.0 см2. Образцы подвергали травлению в подогретом до 60−70°С 20%-ном водном растворе NaOH. После травления микрошлиф промывали в проточной воде и тщательно высушивали. Структуру сплавов изучали с помощью металлографического микроскопа NEOPHOT-31 при увеличении 200 крат.
На рис. 3 в качестве примера представлена микроструктура сплава АМг4 со скандием. В результате проведенных исследований установлено, что структура изученных сплавов однотипная и состоит из твердого раствора алюминия. Также наблюдаются частицы интерметаллических фаз (Mg2Al3), образовавшихся в процессе кристаллизации сплава. Количество и размер частиц второй
фазы в конечном итоге влияют на различные свойства исходного сплава. Видно, что добавки скандия в сплав АМг4 измельчают структуру, и она становится однородной и мелкозернистой.
Исследование удельной теплоемкости сплавов. Исследования температурной зависимости теплоемкости и изменений термодинамических функций сплавов АМг2, АМг3 и АМг4 со скандием проводили по методикам, описанным в работах [8–15].
Теплоемкость сплавов АМг2, АМг3 и АМг4 со скандием измеряли в режиме “охлаждения”. Для измерения температуры использовали многоканальный цифровой термометр, который позволял прямо фиксировать результаты измерений на компьютере в виде таблиц. Точность измерения температуры составляла 2°С. Временной интервал фиксации температуры составлял 10 с. Относительная погрешность измерения температуры в интервале от 40 до 800°С составляла ±1.5%. Погрешность измерения теплоемкости по предлагаемой методике не превышает 1.5% (табл. 1 и 2).
Таблица 1.
Экспериментальные значения скорости охлаждения (dT/dτ, К/c) образцов из меди марки М00
Т, К | № измерения | ||
---|---|---|---|
1 | 2 | 3 | |
300 | 0.0 | 0.0 | 0.0 |
400 | 0.2 | 0.1 | 0.1 |
500 | 0.4 | 0.2 | 0.2 |
600 | 0.5 | 0.3 | 0.3 |
700 | 0.7 | 0.6 | 0.4 |
800 | 0.8 | 0.8 | 0.4 |
Таблица 2.
Удельная теплоемкость (кДж/кг К) меди марки М00
Т, К | Теплоемкость Cu марки М00 по данным [16] | Теплоемкость Cu марки М00, определенная экспериментально по отношению к алюминию марки А7 | ||
---|---|---|---|---|
№ измерения | ||||
1 | 2 | 3 | ||
300 | 0.3850 | 0.3759 | 0.3699 | 0.3678 |
400 | 0.3977 | 0.3883 | 0.3820 | 0.3800 |
500 | 0.4080 | 0.3984 | 0.3919 | 0.3899 |
600 | 0.4169 | 0.4070 | 0.4004 | 0.3984 |
700 | 0.4251 | 0.4151 | 0.4083 | 0.4064 |
800 | 0.4336 | 0.4234 | 0.4164 | 0.4146 |
Обработку результатов измерений производили с помощью программы MS Excel. Графики строили с помощью программы Sigma Plot. Величина коэффициента корреляции составляла Rкорр > 0.9544, подтверждая правильность выбора аппроксимирующей функции.
Предварительно для определения погрешности метода проводилось измерение теплоемкости меди марки М00 по отношению к алюминию марки А7. Результаты для трех параллельных измерений представлены в табл. 1 и 2. Как видно, установленные значения погрешности измерений теплоемкости меди марки М00 не превышают 1.5%. Далее, в работе в качестве эталона нами была взята медь марки М00. В этом плане именно медь является более надежным металлом, так как она характеризуется более высокой температурой плавления и достоверными значениями величины теплоемкости, определенными многими авторами разными методами [15, 16].
Сравнение экспериментально полученных значений удельной теплоемкости меди по отношению с данными, приведенными в справочнике [16], показывает почти 99%-ную их сходимость.
Экспериментально полученные кривые охлаждения образцов из сплавов АМг2, АМг3 и АМг4 с добавками скандия представлены на рис. 4. Полученные зависимости температуры образцов из сплавов (рис. 4) описываются уравнением вида
где a b, p, k – постоянные для данного образца, τ – время охлаждения.Рис. 4.
Зависимости температуры образцов (Т) от времени охлаждения (τ) для сплавов АМг2 (а), АМг3 (б) и АМг4 (в) со скандием.
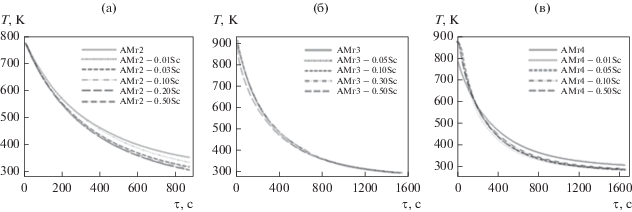
Дифференцируя уравнение (7) по τ, получаем уравнение для определения скорости охлаждения сплавов
Были рассчитаны значения коэффициентов a, b, p, k, ab, pk в уравнении (8).
На рис. 5 представлены кривые скорости охлаждения сплавов с коэффициентом регрессии не менее 0.998.
Рис. 5.
Температурная зависимость скорости охлаждения образцов из сплавов АМг2 (а), АМг3 (б) и АМг4 (в) со скандием.
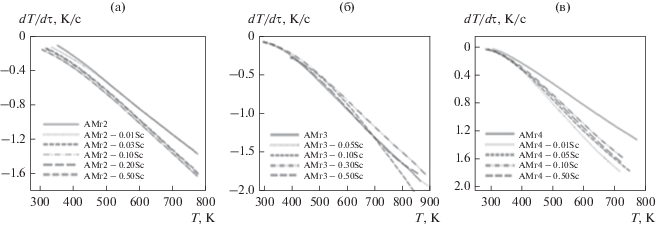
Далее по рассчитанным значениям величин скорости охлаждения образцов из сплавов по уравнению (6) была вычислена их удельная теплоемкость. Получены полиномы, описывающие температурную зависимость удельной теплоемкости сплавов АМг2, АМг3 и АМг4 со скандием в виде общего уравнения:
Результаты расчета теплоемкости по формулам (6) и (9) через100 К представлены на рис. 6.
Рис. 6.
Температурная зависимость удельной теплоемкости меди (1) и сплавов АМг2 (2), АМг3 (3) и АМг4 (4) с 0.5 мас. % скандия.
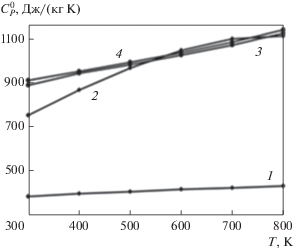
Для расчета температурной зависимости изменений удельных энтальпии, энтропии и энергии Гиббса по (10)–(12) были использованы интегралы от удельной теплоемкости, определенной по уравнению (9):
(11)
$\begin{gathered} \left[ {{{S}^{0}}(T) - {{S}^{0}}({{T}_{0}})} \right] = a\ln \frac{T}{{{{T}_{0}}}} + b\left( {T - {{T}_{0}}} \right) + \\ + \,\,\frac{c}{2}\left( {T_{{}}^{2} - T_{0}^{2}} \right) + \frac{d}{3}\left( {T_{{}}^{3} - T_{0}^{3}} \right); \\ \end{gathered} $(12)
$\begin{gathered} \text{[}{{G}^{0}}(T) - {{G}^{0}}({{T}_{0}}){\text{ }}] = [{{H}^{0}}(T) - {{H}^{0}}({{T}_{0}}){\text{ }}] - \\ - \,\,T[{{S}^{0}}(T) - {{S}^{0}}({{T}_{0}}){\text{ }}], \\ \end{gathered} $Результаты расчета температурной зависимости изменений энтальпии, энтропии и энергии Гиббса для сплавов АМг2 и АМг4 по уравнениям (10)–(12) через 100 К представлены на рис. 7.
ВЫВОДЫ
1. В режиме “охлаждения” установлена удельная теплоемкость сплавов АМг2, АМг3 и АМг4 со скандием. Получены математические модели, описывающие температурную зависимость теплоемкости и изменений термодинамических функций (энтальпия, энтропия, энергия Гиббса) сплавов в интервале температур 300–800 К.
2. Показано, что с ростом температуры удельные теплоемкость, энтальпия, энтропия сплавов увеличиваются, а значение удельной энергии Гиббса уменьшается.
3. Установлено, что добавки скандия в изученном концентрационном интервале (0.01–0.5 мас. %) практически не влияют на значения удельной теплоемкости и изменений термодинамических функций исходных сплавов АМг2, АМг3 и АМг4.
Список литературы
Белецкий В.М., Кривов Г.А. Алюминиевые сплавы (Состав, свойства, технология, применение) / Под ред. Фридляндера И.Н. Справочник. К.: КОМИТЕХ., 2005. 365 с.
Кайгородова Л.И., РаспосиенкоД.Ю., Пушин В.Г., Пилюгин В.П., Смирнов С.В. Влияние отжига на структуру и свойства стареющего сплава Al–Li–Cu–Mg–Zr–Sc–Zn подвергнутого магапластической деформации // ФММ. 2019. Т. 120. № 2. С. 169–175.
Назаров Ш., Росси С., Бисон П., Пеззато Л., Каллиари И., Ганиев И // Влияние добавок редкоземельных металлов на свойства сплавов Al–Li // ФММ. 2019. Т. 120. № 4. С. 339–345.
Красноярский В.В., Сайдалиев Н.Р. Коррозионно-электрохимические свойства сплавов алюминия с железом в нейтральных растворах // Защита от коррозии и окружающей среды. 1991. Вып. 3. С. 14–19.
Фролов В.Ф., Беляев С.В., Губанов И.Ю., Безруких А.И., Костин И В. Влияние технологических факторов на образование дефектов структуры в крупнотоннажных слитках из алюминиевых сплавов серии 1ХХХ // Вестник МГТУ им. Г.И. Носова. 2016. Т. 14. № 2. С. 25–31.
Чукин М.В., Салганик В.М., Полецков П.П. Кузнецова А.С., Бережная Г.А., Гущина М.С. Основные виды и области применения нано-структурированного высокопрочного листового проката // Вестник МГТУ им. Г.И. Носова. 2014. № 4. С. 41–44.
Chen X.G. Growth mechanisms of intermetallic phases in DC cast AA1XXX alloys // Essential Readings in Light Metals. V. 3. Cast Shop for Aluminum Production. 2013. P. 460–465.
Grange D.A. Microstructure control in ingots of aluminum alloys with an emphasis on grain refinement // Essential Readings in Light Metals. V. 3. Cast Shop for Aluminum Production. 2013. P. 354–365.
Geoffrey K. Sigworth Fundamentals of Solidification in Aluminum Castings // International Journal of Metal casting. 2014. V. 8. № 1. P. 7–20.
Иброхимов Н.Ф., Ганиев И.Н., Низомов З., Ганиева Н.И., Иброхимов С.Ж. Влияние церия на теплофизические свойства сплава АМг4 // ФММ. 2016. Т. 117. № 1. С. 53–57.
Азимов Х.Х., Ганиев И.Н., Амонов И.Т., Иброхимов Н.Ф. Влияние лития на теплоемкость и изменений термодинамических функций алюминиевого сплава AЖ2.18 // Вестник МГТУ им. Г.И. Носова. 2018. Т. 16. № 1. С. 37–44.
Ганиев И.Н., Сафаров А.Г., Одинаев Ф.Р., Якубов У.Ш., Кабутов К. Температурная зависимость теплоемкости и изменений термодинамических функции сплава АЖ 4.5 с оловом // Изв. вузов. Цветная металлургия. 2019. № 1. С. 50–58.
Отаджонов С.Э., Ганиев И.Н., Махмудов М., Сангов М.М. Температурная зависимость теплоемкости и изменений термодинамических функция сплава АК1М2 с кальцием // Изв. Юго-Западного государственного ун-та. Серия техника и технология. 2018. № 3(28). С. 105–115.
Якубов У.Ш., Ганиев И.Н., Махмадизода М.М., Сафаров А.Г., Ганиева Н.И. Влияние стронция на температурную зависимость удельной теплоемкости и изменений термодинамических функций сплава АЖ5К10 // Вестник Санкт-Петербургского государственного университета технологии и дизайна. Серия естественных наук. 2018. № 3. С. 61–67.
Джайлоев Дж.Х., Ганиев И.Н., Хакимов А.Х., Иброхимов Н.Ф., Азимов Х.Х. Влияние бария на температурную зависимость удельной теплоемкости и изменений термодинамических функций сплава АЖ2.18 // Вестник ТНУ. Серия естественных наук. 2018. № 4. С. 240–248.
Зиновьев В.Е. Теплофизические свойства металлов при высоких температурах. Справ. изд. М.: Металлургия, 1989. 384 с.
Термодинамические свойства индивидуальных веществ. Справочник / Под ред. Глушкова В.П. М.: Наука, 1982. 559 с.
Дополнительные материалы отсутствуют.
Инструменты
Физика металлов и металловедение