Физика металлов и металловедение, 2020, T. 121, № 1, стр. 72-78
Особенности структуры и свойства поверхности метастабильной аустенитной стали, подвергнутой жидкостной цементации при пониженной температуре
Р. А. Саврай a, *, П. А. Скорынина a, А. В. Макаров a, b, c, А. Л. Осинцева a
a Институт машиноведения УрО РАН
620049 Екатеринбург, ул. Комсомольская, 34, Россия
b Институт физики металлов УрО РАН
620108 Екатеринбург, ул. С. Ковалевской, 18, Россия
c Уральский федеральный университет
620002 Екатеринбург, ул. Мира, 19, Россия
* E-mail: ras@imach.uran.ru
Поступила в редакцию 12.07.2019
После доработки 23.07.2019
Принята к публикации 19.08.2019
Аннотация
Исследовано влияние жидкостной цементации при температуре 780°С на структуру, химический и фазовый состав, микротвердость и шероховатость поверхности коррозионностойкой аустенитной хромоникелевой стали. Установлено, что глубина цементованного слоя составила около 2 мм. При этом в поверхностном слое глубиной до 0.15 мм структура стали состоит из пересыщенного углеродом аустенита γC, α'-мартенсита и дисперсных карбидов хрома Cr23C6, расположенных по границам аустенитных зерен. В теле зерна карбиды не наблюдаются. На глубине от 0.15 до 2 мм в структуре присутствуют аустенит γC и карбиды хрома Cr23C6, причем количество и размер карбидов уменьшаются по мере удаления от поверхности стали. После цементации на поверхности исследованной стали наблюдается рост микротвердости в 4 раза (от 200 до 800 HV0.025) и параметра шероховатости Ra до 1.35 мкм.
ВВЕДЕНИЕ
Эксплуатационные свойства изделий машиностроения во многом определяет состояние их поверхностного слоя, поскольку именно поверхность подвергается воздействию коррозионных сред, износу и контактным нагрузкам. Поэтому для обеспечения необходимой работоспособности поверхность должна обладать целым комплексом свойств, который определяется условиями работы изделия. Аустенитные нержавеющие стали типа 18Cr–10Ni, которые получили широкое распространение в промышленности, обладают высокой коррозионной стойкостью, однако характеризуются низкими прочностными [1] и трибологическими свойствами [2], а также недостаточно высокой контактной выносливостью в условиях циклического ударного нагружения [3]. Упрочнение и повышение износостойкости аустенитных нержавеющих сталей может быть достигнуто как деформационными обработками [4–8], так и за счет обогащения поверхностного слоя атомами внедрения: углеродом (цементация) и азотом (азотирование) [9–12], или сочетанием этих способов (комбинированной обработкой) [13]. Применительно к аустенитным хромоникелевым сталям цементация является наиболее предпочтительным процессом химико-термической обработки, поскольку позволяет формировать более глубокие упрочненные слои, которые, в отличие от азотированных слоев, остаются слабомагнитными [14].
Как правило, цементацию проводят в твердых, жидких и газовых карбюризаторах при температуре от 850°С и выше. Такая обработка позволяет получить упрочненный слой значительной глубины (1 мм и более) и может быть эффективно реализована в условиях современного промышленного производства. Однако цементация по стандартным режимам обычно характеризуется выделением большого количества карбидов, что приводит к снижению коррозионных свойств аустенитной нержавеющей стали. Поэтому в последние годы активно исследуется низкотемпературная (ниже 500°С) цементация, позволяющая сохранить коррозионные свойства стали путем снижения вероятности карбидообразования в поверхностном слое [15–17]. Однако существенным недостатком такого вида цементации является небольшая (около 0.1 мм) глубина упрочненного слоя. Поэтому значительный интерес представляет изучение возможности достижения большей глубины упрочненного слоя при снижении температуры цементации до 700–800°С, направленном на сохранение коррозионной стойкости аустенитной хромоникелевой стали. Поскольку цементация является диффузионным процессом, снижение ее температуры может существенно замедлить процесс насыщения поверхности углеродом. В этом случае цементацию целесообразно проводить в жидком карбюризаторе, где скорость насыщения углеродом и равномерность обработки поверхности выше, чем при использовании других карбюризаторов.
Целью настоящей работы явилось исследование структуры, химического и фазового состава, микротвердости и шероховатости поверхности аустенитной стали AISI 321, подвергнутой жидкостной цементации при температуре 780°С.
МАТЕРИАЛ И МЕТОДИКА ЭКСПЕРИМЕНТА
Исследовали коррозионностойкую аустенитную сталь AISI 321 промышленной плавки состава (мас. %): 0.05 С; 16.80 Cr; 8.44 Ni; 0.33 Ti; 1.15 Mn; 0.67 Si; 0.26 Mo; 0.13 Co; 0.03 Nb; 0.31 Cu; 0.036 P; 0.005 S; остальное Fe. В состоянии поставки сталь представляла собой прокатанный лист толщиной 10 мм. Образцы для цементации изготавливали в виде пластин размерами 52 × 40 мм. Термическую обработку (закалку) подготовленных образцов из стали AISI 321 проводили по следующему режиму: нагрев до температуры 1100°С, выдержка при этой температуре в течение 40 мин, охлаждение в воду. Поверхность образцов подвергали механическому шлифованию и электролитическому полированию. Жидкостную цементацию образцов закаленной стали AISI 321 проводили с использованием лабораторной печи в тигле диаметром 100 мм и высотой 300 мм в расплаве солей с добавлением карбида кремния состава (в мас. %) 80% Na2CO3 + 10% NaCl + 10% SiC при температуре 780°С в течение 15 ч. После окончания цементации образцы охлаждали в воде.
Микроструктуру стали в закаленном состоянии изучали методом оптической микроскопии с применением микроскопа Neophot-21. Структуру и фазовый состав стали, а также поверхности образцов после цементации изучали с применением сканирующего электронного микроскопа Tescan VEGA II XMU с системой рентгеновского энергодисперсионного микроанализа INCA ENERGY 450. Рентгеноструктурный анализ выполняли на дифрактометре Shimadzu XRD-7000 в CrКα-излучении. Определяли фазовый состав, интегральную ширину B линий аустенита (111)γ и (200)γ, и плотность дислокаций ρ. Количество α-фазы рассчитывали по формуле: Vα = 100/{1 + 1.45 × × (I(111)γ/I(110)α)}, где Vα – объемная доля α-фазы, об. %; I(111)γ и I(110)α – интегральные интенсивности линий γ и α фаз [18]. Плотность дислокаций ρ рассчитывали по формуле: ρ = k × B2, где B – интегральная ширина линии (111)γ, рад.; k – постоянный коэффициент k = 2 × 1016 см–2 [19].
Микротвердость по методу восстановленного отпечатка определяли на приборе Shimadzu HMV-G21DT при нагрузке 0.245 Н, скорости нагружения 40 мкм/с и выдержке под нагрузкой 15 с. Изменение микротвердости по глубине цементованного слоя исследовали на поперечном шлифе. Параметры шероховатости поверхности образцов определяли с помощью оптического профилометра Wyko NT-1100.
ЭКСПЕРИМЕНТАЛЬНЫЕ РЕЗУЛЬТАТЫ И ИХ ОБСУЖДЕНИЕ
На рис. 1 представлена микроструктура стали AISI 321 после термической обработки. Она состоит из аустенитных зерен (γ-фазы) и отдельных включений карбида титана TiC. Согласно данным рентгеноструктурного анализа (рис. 2а), α-фаза отсутствует в структуре закаленной стали. Микротвердость стали AISI 321 в закаленном состоянии составляет 200 HV0.025.
Рис. 2.
Рентгеновские дифрактограммы поверхности стали AISI 321 в закаленном состоянии (а) и после цементации (б).
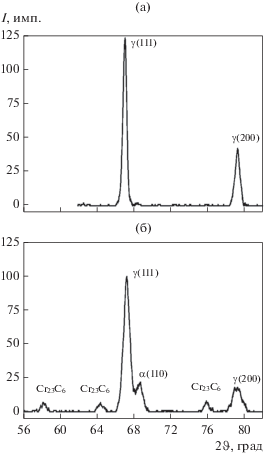
После жидкостной цементации при температуре 780°С структура поверхностного слоя стали AISI 321 на глубине до 0.15 мм состоит из обогащенного углеродом аустенита γС, мартенсита и карбидов хрома Cr23C6 (рис. 3), что подтверждается данными рентгеноструктурного анализа (рис. 2б). При этом количество α-фазы достигает 14 об. % (табл. 1). На глубине более 0.15 мм α-фаза отсутствует, структура состоит из γС-фазы и карбидов Cr23C6. (см. рис. 3а). Отметим, что карбидные частицы достаточно малы (размер большинства из них не превышает 1 мкм), сосредоточены по границам аустенитных зерен, и отсутствуют внутри зерен (см. рис. 3б). Это обусловлено более высокой диффузионной подвижностью атомов на границах зерен и свидетельствует о том, что при температуре цементации 780°С диффузионная подвижность атомов в теле зерна уже недостаточна для выделения карбидной фазы. Цементация также приводит к росту ширины В ренгеновских линий аустенита (111)γ от 30.0 (в закаленном состоянии) до 48.4 мин, (200)γ – от 33.0 до 40.2 мин (см. табл. 1). Это вызвано микроискажениями кристаллической решетки, которые могут быть вызваны повышенным содержанием в ней углерода и ростом плотности дефектов кристаллического строения. В частности, плотность дислокаций ρ в поверхностном слое в результате цементации возрастает от 1.93 × 1012 до 3.97 × 1012 см–2 (см. табл. 1).
Рис. 3.
Структура поверхностного слоя стали AISI 321 (электронная сканирующая микроскопия) после цементации: а – общий вид; б – участок, обозначенный рамкой на рис. 3а. Цифрами 1, 2 и 3 обозначены участки, на которых проводился энергодисперсионный микроанализ.

Таблица 1.
Объемная доля α-фазы Vα, интегральная ширина В рентгеновских линии (111)γ и (200)γ и плотность дислокаций ρ в поверхностном слое стали AISI 321
Режим обработки | Vα, об. % | В(111)γ, мин | В(200)γ, мин | ρ, 1012, см–2 |
---|---|---|---|---|
Закалка | 0 | 30.0 | 33.0 | 1.93 |
Цементация | 14 | 48.4 | 40.2 | 3.97 |
Согласно данным микрорентгеноспектрального анализа в теле зерна на глубине до 0.15 мм, количество углерода и остальных легирующих элементов в кристаллах игольчатой формы (рис. 4а) и за их пределами (рис. 4б) одинаково. Это подтверждает результаты металлографического анализа, согласно которым в теле зерна карбидная фаза отсутствует, и следовательно наблюдаемые кристаллы являются именно кристаллами мартенсита. Проведенный химический анализ расположенных по границам зерен частиц (см. рис. 3б) указывает на повышенное содержание в них углерода и хрома (рис. 4в), что, с учетом данных рентгеноструктурного анализа (см. рис. 2б), позволяет идентифицировать данные частицы как карбиды хрома Cr23C6.
Формирование мартенсита в цементованной стали AISI 321 может быть обусловлено несколькими факторами. В науглероженных нержавеющих сталях, таких как Х18Н9Т, возможно образование α-мартенсита в результате выделения карбидной фазы, сопровождающегося обеднением окружающей аустенитной матрицы по хрому и ростом температуры начала мартенситного превращения Мн [20]. Однако, как следует из рис. 3, в теле зерна карбиды хрома не наблюдаются. Поэтому наиболее вероятной причиной образования мартенсита является деформация аустенитной матрицы. Известно, что при цементации в материале возникают значительные термические напряжения, релаксация которых в аустенитных сталях может происходить путем деформации в процессе охлаждения после цементации. Например, полосы скольжения и образование мартенсита деформации наблюдали в поверхностном слое стали AISI 304L после низкотемпературной цементации [21]. По некоторым оценкам, уровень напряжений в поверхностном слое цементованной стали может достигать 2000 МПа [22]. О прошедшей деформации также свидетельствует повышенная плотность дислокаций в поверхностном слое стали AISI 321, которая после цементации возрастает в два раза по сравнению с плотностью дислокаций в закаленном состоянии (см. табл. 1). Следовательно, можно утверждать, что мартенсит, образующийся в стали AISI 321 после цементации, имеет деформационное происхождение. Кроме того, для аустенита, пересыщенного азотом или углеродом (expanded austenite), характерно смещение линий аустенита (111)γ и (200)γ в сторону меньших углов [23, 24] по сравнению с положением рентгеновских линий в стали в закаленном состоянии. Из рис. 2 следует, что в стали AISI 321, подвергнутой цементации, такого смещения линий не наблюдается. Возможной причиной этого является перераспределение атомов углерода в результате деформационного старения путем миграции находящихся в твердом растворе атомов внедрения (углерода) к дислокациям и образования атмосфер Коттрелла. Микрорентгеноспектральный анализ показал, что общее содержание углерода на поверхности цементованной стали, измеренное в теле зерна, возрастает до 1.74 мас. %, тогда как по данным рентгеноструктурного анализа содержание углерода в аустените составляет 0.66 мас. %. Отметим, что максимальное наблюдаемое содержание углерода в аустенитной стали близкого химического состава составило 4.74 мас. % и было получено после низкотемпературной газовой цементации тонких фольг при температуре 380°С [25].
На рис. 5 представлены результаты измерения микротвердости в поверхностном слое стали AISI 321. Из рис. 5 следует, что микротвердость стали после цементации возрастает от 200 до 800 HV0.025, что сопоставимо с твердостью рассматриваемой стали после интенсивной поверхностной пластической деформации с более высоким содержанием α'-мартенсита в поверхностном слое [6, 13].
Рис. 5.
Микротвердость HV0.025 в поверхностном слое стали AISI 321 после цементации на различной глубине h от поверхности. Штриховой линией обозначена микротвердость стали в закаленном состоянии.
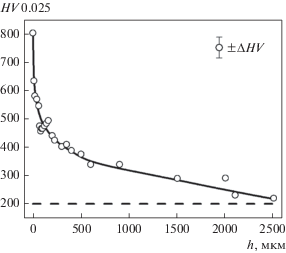
Поскольку содержание α'-мартенсита в стали после цементации составляет около 14 об. % (см. табл. 1), то можно утверждать, что высокая концентрация углерода в поверхностном слое стали вносит в упрочнение существенный вклад. При этом общая глубина упрочненного слоя аустенитной стали AISI 321, подвергнутой жидкостной цементации при температуре 780°С, составила 2 мм. Рисунок 6 показывает, что на указанной глубине сохраняются даже карбиды хрома Cr23C6, однако по мере удаления от поверхности образца количество карбидов, расположенных по границам зерен, уменьшается. Например, низкотемпературная цементация стали AISI 321SS при температуре 500°С обеспечила формирование упрочненного слоя гораздо меньшей глубины, которая составила 0.018 мм [26]. Схематическое изображение структуры поверхностного слоя стали AISI 321 после жидкостной цементации при 780°С показано на рис. 7.
Рис. 6.
Структура стали AISI 321 (электронная сканирующая микроскопия) после цементации на глубине 2 мм.
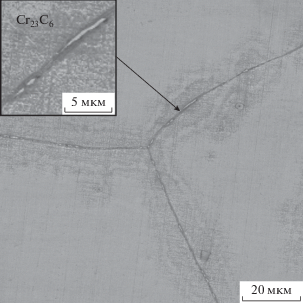
Исследования, выполненные при помощи оптической профилометрии, показали, что поверхность стали AISI 321 в закаленном состоянии (полированная поверхность) характеризуется значением параметра шероховатости Ra = 0.03 мкм (рис. 8а). После цементации стали параметр Ra возрастает до 1.35 мкм (рис. 8б). Это обусловлено формированием деформационного рельефа (указан стрелками 1 на рис. 8в) при релаксации термических напряжений, а также наличием некоторого количества окислов на поверхности (указаны стрелкой 2 на рис. 8в).
Рис. 8.
Вид поверхности стали AISI 321 (а, б – оптическая профилометрия, в – электронная сканирующая микроскопия) в закаленном состоянии (а) и после цементации (б, в). Стрелками 1 указаны полосы скольжения, стрелкой 2 указаны окислы.
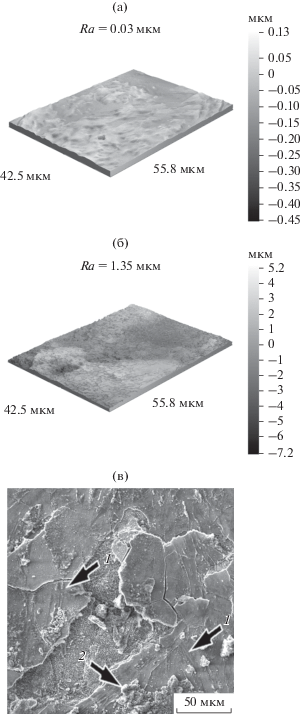
Таким образом, снижение температуры жидкостной цементации до 780°C хотя и приводит к образованию карбидов, однако они мелкодисперсные и сосредоточены по границам зерен. Количество α'-мартенсита также невелико, при этом мартенсит, образующийся в стали AISI 321 после цементации, имеет деформационное происхождение.
ЗАКЛЮЧЕНИЕ
Исследовано влияние жидкостной цементации при температуре 780°С на структуру, химический и фазовый состав, микротвердость и шероховатость поверхности коррозионностойкой аустенитной стали AISI 321. Установлено, что глубина цементованного слоя составила около 2 мм. При этом в поверхностном слое глубиной до 0.15 мм структура стали состоит из пересыщенного углеродом аустенита γс, α'-мартенсита и дисперсных карбидов хрома Cr23C6, расположенных по границам аустенитных зерен. В теле зерна карбиды не обнаружены. На глубине от 0.15 до 2 мм в структуре присутствуют аустенит γс и карбиды хрома Cr23C6, причем количество и размер карбидов уменьшается по мере удаления от поверхности стали.
Показано, что мартенсит, образующийся в стали AISI 321 после цементации, имеет деформационное происхождение. Об этом свидетельствует повышенная плотность дислокаций в поверхностном слое стали, которая после цементации возрастает в два раза по сравнению с плотностью дислокаций перед цементацией. Микротвердость поверхности стали AISI 321 после цементации возрастает в 4 раза (от 200 до 800 HV0.025). При этом существенный вклад в упрочнение вносит высокая концентрация углерода в поверхностном слое стали, которая составила около 1.74 мас. %. Рост параметра шероховатости на поверхности цементованной стали до Ra = 1.35 мкм обусловлен формированием деформационного рельефа, а также возникновением на поверхности некоторого количества окислов.
Работа выполнена в рамках государственных заданий ИМАШ УрО РАН по теме № АААА-А18-118020790148-1 и ИФМ УрО РАН по теме № АААА-А18-118020190116-6 в части исследованных материалов и способов их обработки, и в рамках Комплексной программы УрО РАН (проект № 18-10-1-40) в части методики исследования твердости и химического состава модифицированных поверхностных слоев. Электронная сканирующая и оптическая микроскопия, оптическая профилометрия и микродюрометрия выполнены в ЦКП “Пластометрия” ИМАШ УрО РАН.
Список литературы
McGuire M.F. Stainless steels for design engineers. ASM International, 2008. 296 p.
Qin W., Kang J., Li J., Yue W., Liu Y., She D., Mao Q., Li Y. Tribological behavior of the 316L stainless steel with heterogeneous lamella structure // Materials. 2018. V. 11. № 10. Art. 1839.
Savrai R.A., Makarov A.V., Osintseva A.L., Malygina I.Yu. Estimating the contact endurance of the AISI 321 stainless steel under contact gigacycle fatigue tests // J. Mater. Eng. Perform. 2018. V. 27. № 2. P. 601–611.
Кузнецов В.П., Макаров А.В., Осинцева А.Л., Юровских А.С., Саврай Р.А., Роговая С.А., Киряков А.Е. Упрочнение и повышение качества поверхности деталей из аустенитной нержавеющей стали алмазным выглаживанием на токарно-фрезерном центре // Упрочняющие технологии и покрытия. 2011. № 11. С. 16–26.
Макаров А.В., Скорынина П.А., Осинцева А.Л., Юровских А.С., Саврай Р.А. Повышение трибологических свойств аустенитной стали 12Х18Н10Т наноструктурирующей фрикционной обработкой // Обработка металлов (технология, оборудование, инструменты). 2015. № 4(69). С. 80–92.
Savrai R.A., Makarov A.V., Malygina I.Yu., Rogovaya S.A., Osintseva A.L. Improving the strength of the AISI 321 austenitic stainless steel by frictional treatment [Digital resource] // Diagnostics, Resource and Mechanics of materials and structures. 2017. № 5. P. 43–62. http:// dream-journal.org/issues/2017-5/2017-5_149.html.
Наркевич Н.А., Шулепов И.А., Миронов И.П. Структура, механические и триботехнические свойства аустенитной азотистой стали после фрикционной обработки // ФММ. 2017. Т. 118. № 4. С. 421–428.
Макаров А.В., Скорынина П.А., Юровских А.С., Осинцева А.Л. Влияние технологических условий наноструктурирующей фрикционной обработки на структурно-фазовое состояние и упрочнение метастабильной аустенитной стали // ФММ. 2017. Т. 118. № 12. С. 1300–1311.
Cao Y., Ernst F., Michal G.M. Colossal carbon supersaturation in austenitic stainless steels carburized at low temperature // Acta Mater. 2003. V. 51. P. 4171–4181.
Silva I.C., Rebello J.M.A., Bruno A.C., Jacques P.J., Nysten B., Dille J. Structural and magnetic characterization of a carburized cast austenitic steel // Scripta Mater. 2008. V. 59. P. 1010–1013.
Fernandes F.A.P., Gallego L.C.C.J. Microstructure of nitrided and nitrocarburized layers produced on a superaustenitic stainless steel // J. Mater. Res. Technol. 2008. V. 2. № 2. P. 158–164.
Ceschini L., Chiavari C., Marconi A., Martini C. Influence of the countermaterial on the dry sliding friction and wear behaviour of low temperature carburized AISI316L steel // Tribol. Int. 2013. V. 67. P. 36–43.
Макаров А.В., Гаврилов Н.В., Самойлова Г.В., Мамаев А.С., Осинцева А.Л., Саврай Р.А. Влияние непрерывного и газоциклического плазменного азотирования на качество наноструктурированной поверхности аустенитной нержавеющей стали // Обработка металлов (технология, оборудование, инструменты). 2017. № 2(75). С. 55–66.
Tsujikawa M., Egawa M., Sone T., Ueda N., Higashi K. Modification of S phase on austenitic stainless steel using fine particle shot peening steel // Surf. Coat. Technol. 2013. V. 228. P. S318–S322.
Ma F., Pan L., Zhang L. J., Zhu Y. F., Li P., Yang, M. Structure and wear resistance of 0Cr17Ni14Mo2 austenitic stainless steel after low temperature gas carburising // Mater. Res. Innovations. 2014. V. 18. P. 1023–1027.
Cheng L.H., Hwang K.S. Surface hardening of powder injection molded 316l stainless steels through low-temperature carburization // Metall. Mater. Trans. A. 2013. V. 44A. № 2. P. 827–834.
Скорынина П.А., Макаров А.В., Меньшаков А.И., Осинцева А.Л. Влияние низкотемпературной цементации в плазме электронного пучка на упрочнение и шероховатость поверхности метастабильной аустенитной стали // Обработка металлов (технология, оборудование, инструменты). 2019. Т. 21. № 2. С. 97–109.
Коршунов Л.Г., Сагарадзе В.В., Черненко Н.Л., Шабашов В.А. Структурные превращения карбидной фазы в стали Гадфильда, инициированные фрикционным воздействием // ФММ. 2015. Т. 116. № 8. С. 867–873.
Саврай Р.А., Макаров А.В., Пышминцев И.Ю., Уймин М.А. Использование магнитного метода при оценке деформационной стабильности остаточного аустенита в листовых высокопрочных экономнолегированных сталях для автомобилестроения // Дефектоскопия. 2006. № 3. С. 72–78.
Сагарадзе В.В., Уваров А.И. Упрочнение и свойства аустенитных сталей. Екатеринбург: РИО УрО РАН, 2013. 720 с.
Maistro G., Nyborg L., Vezzu S., Cao Y. Microstructural characterization and layer stability of low-temperature carburized AISI 304L and AISI 904L austenitic stainless steel // La Metallurgia Italiana. 2015. № 11–12. P. 21–30.
Collins S.R., Williams P.C., Marx S.V., Heuer A., Ernst F., Kahn H. Low-temperature carburization of austenitic stainless steel. In book ASM Handbook, Vol. 4D, Heat Treating of Irons and Steels / Dossett J., Totten G.E., Eds. ASM International, 2014. 730 p. P. 451–460.
Tong X., Zhang T., Ye W. Effect of carburizing atmosphere proportion on low temperature plasma carburizing of austenitic stainless steel // Adv. Mater. Mech. Ind. Eng. 2014. V. 598. P. 90–93.
Duarte M.C.S., Godoya C., Wilson J.C.A.B. Analysis of sliding wear tests of plasma processed AISI 316L steel // Surf. Coat. Technol. 2014. V. 260. P. 316–325.
Christiansen T.L., Ståhl K., Brink B.K., Somers M.A.J. On the carbon solubility in expanded austenite and formation of Hägg carbide in AISI 316 stainless steel // Steel Research International. 2016. V. 87. № 11. P. 1395–1405.
Sun Y. Kinetics of low temperature plasma carburizing of austenitic stainless steels // J. Mater. Process. Technol. 2005. V. 168. P. 189–194.
Дополнительные материалы отсутствуют.
Инструменты
Физика металлов и металловедение