Физика металлов и металловедение, 2020, T. 121, № 6, стр. 667-672
Влияние Yb на структуру и свойства электропроводного сплава Al–Y–Sc
Р. Ю. Барков a, *, О. А. Яковцева a, О. И. Мамзурина a, И. С. Логинова a, С. В. Медведева a, А. С. Просвиряков a, А. В. Михайловская a, А. В. Поздняков a
a НИТУ “МИСиС”
119049 Москва, Ленинский пр., 4, Россия
* E-mail: barkov@misis.ru
Поступила в редакцию 04.12.2019
После доработки 14.01.2020
Принята к публикации 20.01.2020
Аннотация
Исследовано влияние добавки иттербия на фазовый состав, упрочнение при отжиге до и после прокатки, электропроводность и механические свойства сплава Al–0.2% Y–0.2Sc. В литой структуре помимо алюминиевого твердого раствора выявлена дисперсная эвтектика, в которой интерметаллидная фаза размером 100–250 нм обогащена иттрием и иттербием. Максимальное упрочнение слитка достигается после отжига при 300°С в течение 3 ч за счет выделения дисперсоидов Al3Мe. Отжиг деформированных листов при 300°С приводит к росту твердости и предела текучести, что связано с инициированием процесса дораспада алюминиевого твердого раствора. Т.е. добавка иттербия стимулирует гетерогенное зарождение дисперсоидов Al3Мe в процессе отжига после прокатки. При этом электропроводность по международному стандарту на отожженную медь с увеличением температуры и времени отжига увеличивается от 54 до 54.9% и 57.7% после отжига при 200°C и 300°C соответственно.
ВВЕДЕНИЕ
Скандий в алюминиевых сплавах является эффективным упрочнителем и антирекристаллизатором за счет способности образовывать пересыщенный твердый раствор при кристаллизации, распад которого при отжиге слитков приводит к формированию наноразмерных когерентных дисперсоидов L12-фазы Al3Sc [1–9]. Выделение частиц фазы Al3Sc происходит гомогенно в матрице алюминиевого твердого раствора [1]. Когерентные частицы эффективны в определенном интервале температур и склонны к потере когерентности при температурах выше 400°С [6]. Добавка циркония приводит к повышению термической устойчивости дисперсоидов с образованием выделений фазы Al3(Sc1 − xZrx) [10]. В последние годы активно проводят исследования влияния добавок иттрия [11–24] и иттербия [25–37] на структуру и свойства алюминия [11–19, 25–32] и сплавов на его основе [20–24, 33–37], которые образуют сложную фазу Al3Me (Me–Sc, Zr, Y, Yb и др.). Легирование иттрием сплавов на основе систем Al–Zr [11–15] и Al–Sc–Zr [16–19] приводит к повышению плотности выделений дисперсоидов фаз типа Al3Ме и температуры начала рекристаллизации [11–19]. Упрочнение деформируемых сплавов на основе систем Al–Mg и Al–Cu, легированных иттрием происходит по тому же принципу [20–24]. Добавка иттербия уже в двойных сплавах приводит к образованию выделений Al3Yb [25, 28], что способствует существенному приросту твердости слитков в процессе отжига. Комплексное легирование приводит к большему эффекту упрочнения за счет образования более сложных выделений фазы Al3М [26, 27, 29–32]. Совместно с хромом и цирконием иттербий способствует повышению коррозионной стойкости высокопрочных алюминиевых сплавов [33–35] и прочности магналиев [37].
Данная работа направлена на исследование влияния малой добавки иттербия на структуру и прочностные характеристики свойства сплава Al–0.2Y–0.2Sc, имеющего повышенную электропроводность.
МЕТОДИКА ЭКСПЕРИМЕНТОВ
Исследуемый сплав состава Al–0.2% Y–0.2% Sc–0.3% Yb (AlYScYb) выплавлен в электрической печи сопротивления с использованием алюминия марки А99 [38], лигатур Al–10% Y, Al–10% Yb и Al–2% Sc.
Термическую обработку проводили в сушильном шкафу “Nabertherm N30/65A” с точностью поддержания температуры 1°С. Прокатку слитков проводили на лабораторном стане ДУО-300 с шириной валков 300 мм.
После отжига при 300°С в течение 3 ч слиток прокатывали при температуре 300°С от толщины 20 до 10 мм и при комнатной температуре до толщины 1 мм.
Металлографические исследования и идентификацию фаз проводили при помощи светового микроскопа (СМ) Axiovert 200 MMAT “CarlZeiss”, растрового электронного микроскопа (РЭМ) TESCAN VEGA 3LMH с использованием энерго-дисперсионного детектора X-Max 80 и просвечивающего электронного микроскопа JEOL 2000-EX с рабочим напряжением 120 кВ. Образцы были подготовлены в стандартном электролите A2 на установке электролитического утонения Struers Tenupol-5. Подготовку шлифов для микроструктурных исследований производили на установке Struers Labopol-5 с использованием шлифовальной бумаги различной дисперсности и суспензии на основе коллоидного оксида кремния.
Твердость измеряли стандартным методом Виккерса на автоматизированном универсальном твердомере 930N фирмы Wolpert согласно ГОСТ 2999-75, ошибка в определении не превышала 3 HV. Механические характеристики при растяжении определяли на универсальной испытательной машине Zwick/Roell Z250 серии Allround в комплексе с автоматическим датчиком продольной деформации согласно ГОСТ 1497-84. Среднее квадратичное отклонение от среднего значения было в пределах 1–2% (5 МПа) от измеряемой величины. Электропроводность сплавов анализировали методом “двойного моста” с использованием миллиомметра INSTEK GOM-802 на образцах с поперечным сечением 1 × 5 мм2 и длиной 70 мм.
РЕЗУЛЬТАТЫ ЭКСПЕРИМЕНТОВ И ОБСУЖДЕНИЕ
Микроструктура сплава AlYScYb в литом состоянии представлена на рис. 1. В структуре помимо алюминиевого твердого раствора выявлена дисперсная эвтектика, в которой интерметаллидная фаза обогащена иттрием и иттербием (см. карты распределения легирующих элементов на рис. 1). Скандий однородно распределен в алюминиевом твердом растворе, а концентрация иттрия и иттербия в растворе составляет по 0.1–0.2% согласно результатам микрорентгеноспектрального анализа. Размер эвтектической фазы кристаллизационного происхождения находится в интервале 100–250 нм. Похожая структура была получена в сплаве Al–0.2% Y–0.2Sc (AlYSc) [18].
Рис. 1.
Микроструктура сплава в литом состоянии и распределение легирующих элементов между фазами (СЭМ).
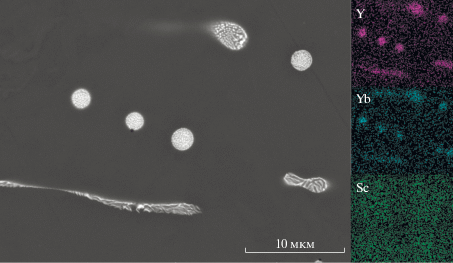
Образцы сплава отжигали при температурах 300, 370 и 440°С в течение разного времени для определения режима, обеспечивающего максимальное упрочнение. Кривые зависимости твердости от времени отжига проходят через максимум в исследуемом температурном интервале. С увеличением температуры отжига сокращается время достижения максимума твердости с 3–4 ч до 0.5 ч. Максимальный прирост твердости в 38 HV достигается после отжига при 300°С, а при более высоких температурах максимум существенно ниже (рис. 2). При этом разупрочнение при увеличении времени выдержки усиливается с ростом температуры.
Упрочнение в процессе отжига слитков происходит за счет выделения дисперсоидов Al3Ме. На рис. 3 представлена микроструктура сплава после отжига при 300°С в течение 3 ч и микроэлектронограмма в оси зоны (112). Выделения фазы Al3Ме имеют L12-структуру. Можно отметить достаточно однородное распределение дисперсоидов, зарождающихся преимущественно гомогенно в матрице.
Рис. 3.
Микроструктура сплава после отжига при 300°С в течение 3 часов (а – светлопольное изображение, б – темнопольное изображение) и микроэлектронограмма в оси зоны (112) (в).
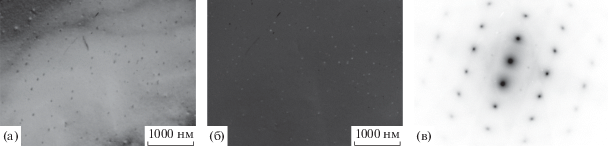
На рис. 4 представлены зависимости твердости от времени отжига холоднокатаных листов сплава при температурах 100–550°С в течение 1 ч и при температурах 150, 200 и 300°С в течение разного времени в сравнении со сплавом AlYSc [18]. Зеренная структура сплава AlYScYb сохраняется нерекристаллизованной вплоть до 450°С (вставка на рис. 4а). При температуре 550°С полностью проходит рекристаллизация и твердость резко снижается (рис. 4а). Аналогичная зеренная структура отмечена в сплаве AlYSc [18]. Добавка иттербия не оказало существенного влияния на температуру начала рекристаллизации, она осталась в интервале 450–550°С. Однако отмечено существенное влияние добавки иттербия на кинетику изменения твердости в процессе отжига прокатанных листов. На температурной зависимости твердости при 300–350°С отмечено появление локального максимума (рис. 4а). Повышение твердости выявлено также на временной зависимости при 300°С (рис. 4б). Через 0.5 ч отжига при 300°С твердость возрастает от 67 до 76 HV и практически не изменяется при увеличении времени отжига до 7 ч. Накопление дефектов при прокатке повышает вероятность гетерогенного зарождения, и упрочнение можно связать с дораспадом алюминиевого твердого раствора и повышением плотности распределения дисперсоидов Al3Me. Отжиг при низких температурах (150 и 200°С) не приводит к изменению твердости листов (рис. 4б). Вероятно, температуры 150–200°С низки для инициирования дораспада твердого раствора.
Рис. 4.
Зависимость твердости от времени отжига 1 мм листов при температурах 100–550°С в течение 1 часа (а) и при температурах 150, 200 и 300°С в течение разного времени (б) в сравнение со сплавом AlYSc [18].
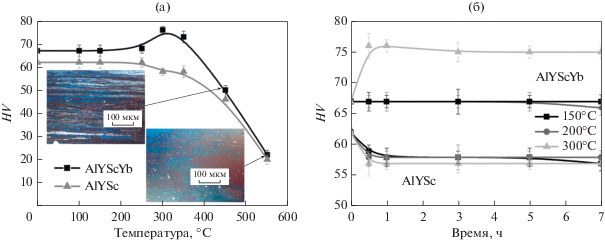
Важно отметить, что эффекта упрочнения не выявили в сплаве без иттербия (рис. 4б), в случае которого наблюдали разупрочнение, вызванное полигонизацией [18, 19]. Таким образом, можно предположить, что добавка иттербия стимулирует гетерогенное зарождение дисперсоидов Al3Ме.
Результаты определения характеристик прочности и пластичности при одноосном растяжении листов в деформированном и отожженном состояниях хорошо коррелируют с твердостью. В табл. 1 представлены механические характеристики при одноосном растяжении исследуемого сплава в сравнении со сплавом без Yb. В деформированном состоянии предел текучести составляет 212 МПа, в процессе отжига при 200°C не изменяется, и увеличивается до 231 МПа после 1 ч отжига при 300°C. При этом стоит отметить, что предел текучести сплава с добавкой Yb на 30–50 МПа выше, чем в сплаве без него (табл. 1).
Таблица 1.
Механические свойства при одноосном растяжении в сравнение со сплавом AlYSc
Состояние | AlYSc [18] | AlYScYb | ||||
---|---|---|---|---|---|---|
σ0.2, МПа | σВ, МПа | δ, % | σ0.2, МПа | σВ, МПа | δ, % | |
Деформированное | 186 ± 2 | 201 ± 1 | 11.8 ± 0.2 | 212 ± 1 | 225 ± 1 | 8.6 ± 0.6 |
Отжиг 200°C, 1 ч | 178 ± 1 | 198 ± 1 | 10.7 ± 0.8 | 213 ± 1 | 230 ± 1 | 8.7 ± 1.2 |
Отжиг 200°C, 5 ч | 174 ± 1 | 194 ± 1 | 12.2 ± 0.4 | 212 ± 2 | 228 ± 2 | 11.5 ± 0.8 |
Отжиг 200°C, 7 ч | 178 ± 1 | 200 ± 1 | 15.1 ± 0.8 | 211 ± 2 | 228 ± 2 | 10.8 ± 0.7 |
Отжиг 300°C, 1 ч | 179 ± 2 | 200 ± 2 | 16.5 ± 0.5 | 231 ± 1 | 244 ± 1 | 7.6 ± 0.8 |
Отжиг 300°C, 5 ч | 177 ± 2 | 199 ± 3 | 15.2 ± 0.4 | 226 ± 2 | 240 ± 3 | 10.8 ± 0.4 |
Отжиг 300° C, 7 ч | 183 ± 3 | 202 ± 2 | 15.8 ± 0.3 | 226 ± 2 | 241 ± 2 | 11.9 ± 0.2 |
Значения электропроводности по международному стандарту на отожженную медь (МСнОМ) в деформированном и отожженном состояниях сплавов AlYScYb и AlYSc, электротехнического алюминиевого сплава 1350 и чистого Al представлены в табл. 2. Электропроводность сплава AlYScYb с увеличением температуры и времени отжига увеличивается от 54 до 54.9% (отжиг 200°C) и 57.7% МСнОМ (отжиг 300°C), что вызвано уменьшением числа дефектов.
Таблица 2.
Электропроводность по МСнОМ в сравнение со сплавом AlYSc, с чистым Al и электротехническим алюминиевым сплавом 1350
Увеличение плотности дисперсоидов, приводящее к росту твердости и предела текучести, также оказывает существенное влияние на повышение электропроводности, связанное с обеднением алюминиевой матрицы. Отметим, что при некритичном снижении электропроводности, в сравнении с электротехническим алюминиевым сплавом 1350, исследуемый сплав имеет значительно больший предел текучести – 226–231МПа против 110 МПа для сплава 1350.
ВЫВОДЫ
Исследовано влияние добавки 0.3% Yb на фазовый состав, упрочнение при отжиге до и после прокатки сплава Al–0.2% Y–0.2Sc с повышенной прочностью и электропроводностью. Структура слитка представлена алюминиевым твердым раствором и дисперсной эвтектикой с размером интерметаллидной фазы 100–250 нм, обогащенной иттрием и иттербием. Повышение твердости образцов сплава в 38 HV достигается после отжига при 300°С в течение 3 ч за счет выделения когерентных дисперсоидов фазы Al3Мe с L12-структурой. Установлено, что отжиг листов при 300°С приводит к росту твердости и предела текучести, что может быть следствием увеличения плотности дисперсоидов за счет дополнительного распада алюминиевого твердого раствора, инициированного предварительной холодной деформацией.
Увеличение плотности дисперсоидов, приводящее к росту твердости и предела текучести, также оказывает существенное влияние на повышение электропроводности, связанное с обеднением алюминиевой матрицы. При этом электропроводность с увеличением температуры и времени отжига увеличивается от 54 до 54.9% и 57.7% МСнОМ после отжига при 200 и 300°C соответственно, а наибольший предел текучести составляет 231 МПа при относительном удлинении 7%.
Работа выполнена при поддержке Министерства образования и науки РФ в рамках государственного задания № 11.7172.2017/8.9 на 2017–2020 гг.
Список литературы
Hyland R.W. Homogeneous nucleation kinetics of Al3Sc in a dilute Al–Sc alloy // Metal. Trans. A. 1992. V. 23. P. 1947.
Davydov V.G, Rostova T.D., Zakharov V.V., Filatov Y.A., Yelagin V.I. Scientific principles of making an alloying addition of scandium to aluminium alloys // Mater. Sci. Eng. A. 2000 V. 280. P. 30–36.
Rostova T.D., Davydov V.G., Yelagin V.I., Zakharov V.V. Effect of scandium on recrystallization of aluminum and its alloys // Mater. Sci. F. 2000. V. 331–337. P. 793–798.
Zakharov V.V. Effect of scandium on the structure and properties of aluminum alloys // Met. Sci. Heat Treat. 2003. V. 45. № 7–8. P. 246–253.
Jones M.J., Humphreys F.J. Interaction of recrystallization and precipitation: the effect of Al3Sc on the recrystallization behavior of deformed aluminium // Acta Mater. 2003. V. 51. P. 2149–2159.
Iwamura S., Miura Y. Loss in coherency and coarsening behavior of Al3Sc precipitates // Acta Mater. 2004. V. 52. P. 591–600.
Costa S., Puga H., Barbosa J., Pinto A.M.P. The effect of Sc additions on the microstructure and age hardening behaviour of as cast Al–Sc alloys // Mater. Des. 2012. V. 42. P. 347–352.
Zakharov V.V., Rostova T.D. Hardening of aluminum alloys due to scandium alloying // Met. Sci. Heat Treat. 2014. V. 55. № 11–12. P. 660–664.
Zakharov V.V., Fisenko I.A., Alloying Aluminum Alloys with Scandium // Met. Sci. Heat Treat. 2017. V. 59. № 5–6. P. 278–284.
Fuller C.B., Seidman D.N. Temporal evolution of the nanostructure of Al3(Sc,Zr) alloys: Part II-coarsening of Al3(Sc1 − xZrx) precipitates // Acta Mater. 2005. V. 53. № 20. P. 5415–5428.
Zhang Y., Gao H., Kuai Y., Han Y., Wang J., Sun B., Gu S., You W. Effects of Y additions on the precipitation and recrystallization of Al–Zr alloys // Mater. Charact. 2013. V. 86. P. 1–8.
Zhang Y., Gu J., Tian Y., Gao H., Wang J., Sun B. Microstructural evolution and mechanical property of Al‒Zr and Al–Zr–Y alloys // Mater. Sci. Eng. A. 2014. V. 616. P. 132–140.
Gao H., Feng W., Wang Y. Structural and compositional evolution of Al3(Zr,Y) precipitates in Al–Zr–Y alloy // Mater. Charact. 2016. V. 121. P. 195–198.
Gao H., Feng W., Gu J., Wang J., Sun B. Aging and recrystallization behavior of precipitation strengthened Al–0.25Zr–0.03Y alloy // J. Alloys. Compd. 2017. V. 696. P. 1039–1045.
Pozdniakov A.V., Barkov R.Yu., Prosviryakov A.S., Churyumov A.Yu., Golovin I.S., Zolotorevskiy V.S. Effect of Zr on the microstructure, recrystallization behavior, mechanical properties and electrical conductivity of the novel Al–Er–Y alloy // J. Alloys and Compd. 2018. V. 765. P. 1–6.
Pozdnyakov A.V., Osipenkova A.A., Popov D.A., Makhov S.V., Napalkov V.I. Effect of low additions of Y, Sm, Gd, Hf and Er on the structure and hardness of alloy Al – 0.2% Zr – 0.1% Sc // Met. Sci. Heat Treat. 2017. V. 58. P. 537–542.
Pozdniakov A.V., Aytmagambetov A.A., Makhov S.V., Napalkov V.I. Effect of impurities of Fe and Si on the structure and strengthening upon annealing of the Al–0.2% Zr–0.1% Sc alloys with and without Y additive // Phys. Met. Metall. 2017. V. 118. P. 479–484.
Pozdniakov A.V., Barkov R.Yu. Microstructure and mechanical properties of novel Al–Y–Sc alloys with high thermal stability and electrical conductivity // J. Mater. Sci. Technol. 2020. V. 36. P. 1–6.
Pozdnyakov A.V., Barkov R.Yu. Effect of impurities on the phase composition and properties of a new alloy of the Al–Y–Er–Zr–Sc system // Metallurgist. 2019. V. 63. № 1–2. P. 79–86.
Cao F., Zhu X., Wang S., Shi Lu, Xu G., Wen J. Quasi-superplasticity of a banded-grained Al–Mg–Y alloy processed by continuous casting-extrusion // Mater. Sci. Eng. A. 2017. V. 690. P. 433–445.
Barkov R.Y., Pozdniakov A.V., Tkachuk E., Zolotorevskiy V.S. Effect of Y on microstructure and mechanical properties of Al–Mg–Mn–Zr–Sc alloy with low Sc content // Mater. Lett. 2018. V. 217. P.135–138.
Pozdniakov A.V., Barkov R.Y. Microstructure and materials characterisation of the novel Al–Cu–Y alloy // Mater. Sci. Technol. 2018. V. 34. № 12. P. 1489–1496.
Amer S.M., Barkov R.Yu., Yakovtseva O.A., Pozdniakov A.V. Comparative analysis of structure and properties of quasibinary alloys Al–6.5 Cu–2.3 Y and Al–6 Cu–4.05 Er // Phys. Met. Metall. 2020. (in press).
Pozdniakov A.V., Barkov R.Yu., Amer S.M., Levchenko V.S., Kotov A.D., Mikhaylovskaya A.V. Microstructure, mechanical properties and superplasticity of the Al–Cu–Y–Zr alloy // Mater. Sci. Eng. A. 2019. V. 758. P. 28–35.
Tang C., Zhou D. Precipitation hardening behavior of dilute binary Al–Yb alloy // Trans. Nonferrous Met. Soc. China. 2014. V. 24. P. 2326−2330.
Wen S.P., Gao K.Y, Huang H., Wang W., Nie Z.R. Role of Yb and Si on the precipitation hardening and recrystallization of dilute Al–Zr alloys // J. Alloys and Compd. 2014. V. 599. P. 65–70.
Peng G., Chen K., Fang H., Chen S. A study of nanoscale Al3(Zr,Yb) dispersoids structure and thermal stability in Al–Zr–Yb alloy // Mater. Sci Eng. A. 2012. V. 535. P. 311– 315.
Zhang Y., Gao K., Wen S., Huang H., Wang W., Zhu Z., Nie Z., Zhou D. Determination of Er and Yb solvuses and trialuminide nucleation in Al–Er and Al–Yb alloys // J. Alloys and Compd. 2014. V. 590 P. 526–534.
Nhon Q.Vo, Davaadorj B., Amirreza S., Evander R., Dunand D.C. Effect of Yb microadditions on creep resistance of a dilute Al–Er–Sc–Zr alloy // Materialia. 2018. V. 4. P. 65–69.
Van Dalen M.E., Gyger T., Dunand D.C., Seidman D.N. Effects of Yb and Zr microalloying additions on the microstructure and mechanical properties of dilute Al–Sc alloys // Acta Mater. 2011. V. 59. P. 7615–7626.
Fang H.C., Shang P.J., Huang L.P., Chen K.H., Liu G., Xiong X. Precipitates and precipitation behavior in Al–Zr–Yb–Cr alloys // Mater. Let. 2012. V. 75. P. 192–195.
Zhang Y., Zhou W., Gao H., Han Y., Wang K., Wang J., Sun B., Gu S., You W. Precipitation evolution of Al–Zr–Yb alloys during isochronal aging // Scr. Mater. 2013. V. 69. P. 477–480.
Peng G., Chen K., Fang H., Chen S. EIS Study on Pitting Corrosion of 7150 Aluminum Alloy in Sodium Chloride and Hydrochloric Acid Solution // Mat. Des. 2012. V.36. P. 279–283.
Fang H.C., Chen K.H., Chen X., Chao H., Peng G.S. Effect of Cr, Yb and Zr additions on localized corrosion of Al–Zn–Mg–Cu alloy // Corr. Sci. 2009. V. 51. P. 2872–2877.
Chen K.H., Fang H.C., Zhang Z., Chena X., Liu G. Effect of Yb, Cr. and Zr additions on recrystallization and corrosion resistance of Al–Zn–Mg–Cu alloys // Mat. Sci. Eng. 2008. V. 497. P. 426–431.
Song M., Wu Z., He Y. Effects of Yb on the mechanical properties and microstructures of an Al–Mg alloy // Mat. Sci. Eng. 2008. V. 497. P. 519–523.
Pozdnyakov A.V., Barkov R.Yu., Levchenko V.S. Influence of Yb on the Phase Composition and Mechanical Properties of Low-Scandium Al–Mg–Mn–Zr–Sc and Al–Mg–Cr–Zr–Sc Alloys // Phys. Met. Metall. 2020. V. 121. № 1. P. 84–88.
ASM Handbook. Properties and Selection: Nonferrous Alloys and Special-Purpose Materials. V. 2. The Materials Information Company, 2010.
Дополнительные материалы отсутствуют.
Инструменты
Физика металлов и металловедение