Физика металлов и металловедение, 2021, T. 122, № 3, стр. 323-328
Исследование лазерной сварки пористых металлов с применением компактных вставок и нанопорошков
А. Н. Черепанов a, *, В. О. Дроздов a, В. И. Мали b, А. Г. Маликова a, А. М. Оришич a
a Институт теоретической и прикладной механики им. С.А. Христиановича СО РАН
630090 Новосибирск, ул. Институтская, 4/1, Россия
b Институт гидродинамики им. М.А. Лаврентьева СО РАН
630090 Новосибирск, просп. акад. Лаврентьева, 15, Россия
* E-mail: cherepanov.anatolyi@yandex.ru
Поступила в редакцию 16.06.2020
После доработки 02.11.2020
Принята к публикации 03.11.2020
Аннотация
Экспериментально исследовано влияние тепловых режимов и некоторых технологических приемов (применение промежуточных вставок из компактного металла, наномодифицирующих добавок) на качество получаемых лазерной сваркой неразъемных соединений пористых пластин титана или нержавеющей стали. Установлено, что для получения качественного бездефектного шва необходимо использование промежуточной вставки из компактного (не пористого) металла, размещаемой встык между торцами свариваемых пластин. При этом положение фокального пятна следует устанавливать на глубине, равной толщине пластины, т.е. на ее нижней поверхности. Для получения шва с валиком либо заподлицо со свариваемыми пластинами высота вставки должна превышать толщину пластин. Применение наномодифицирующих добавок на основе нитрида титана повышает дисперсность и однородность структуры шва, что положительно сказывается на механических характеристиках сварного соединения.
ВВЕДЕНИЕ
Пористые материалы, в том числе пеноматериалы, называют материалами будущего. Это связано с их уникальными физико-механическими свойствами: тепло- шумо- и ударозащитными характеристиками, а также легкостью и высокой удельной прочностью. Они способны поглощать большое количество энергии при сохранении низкого уровня напряжения. Применение легких пористых материалов весьма эффективно в аэрокосмических исследованиях и производстве оборудования в химической, радиотехнической, кораблестроительной и других отраслях [1–6]. Существенным фактором, который препятствует широкому применению пористых металлов, является проблема получения качественных, надежных неразъемных соединений. Наиболее перспективным способом соединения изделий из пористых металлов с глубоким проплавлением является лазерная сварка. Однако особенности физических процессов, лежащих в основе этого метода, недостаточно изучены, что является причиной сравнительно редкого использования лазерной сварки пористых материалов [2, 3].
Целью настоящей работы являлось изучение влияния режимов лазерной сварки и технологических приемов (наномодифицирование, использование промежуточных вставок) на морфологию, структуру и качество сварного соединения пористых пластин из титана или нержавеющей стали.
МЕТОДИКА ЭКСПЕРИМЕНТА И МАТЕРИАЛЫ
Для проведения экспериментальных работ были использованы пористые пластины из титана марки ВТ 1-0 и нержавеющей стали марки 12Х18Н10Т толщиной 2 мм со средним значением пористости 33, 35% соответственно. Пластины были изготовлены в промышленных условиях методом спекания порошковых материалов. Лазерную сварку (ЛС) в стык опытных образцов размером 50 × 20 × 2 мм осуществляли на автоматизированном лазерном технологическом комплексе “Сибирь-1”, разработанном в ИТПМ СО РАН. Лазерное излучение фокусировалось на образцах с помощью ZnSe-линзы с фокусным расстоянием 254 мм и длиной волны 10.6 мкм. Для защиты сварного шва использовали инертный газ (гелий). Непосредственно перед сваркой кромки образцов зачищали с помощью металлического шабера, а затем обрабатывали-ацетоном.
Прочность сварных соединений измеряли на машине Zwick/Roell Z100 по результатам испытания 6 образцов. Твердость определяли по методу Виккерса на микротвердомере Wilson Hardeness Group Tuken 1102. Макро- и микроструктуру сварных швов исследовали на оптическом микроскопе Olympus LEXT OLS3000. Термообработку проводили в камерной печи Carbolite. Подготовку шлифов осуществляли на автоматических отрезных и полировальных машинах пробоподготовки (Presi).
Сварку образцов проводили при различных значениях мощности излучения (W) (0.7–1.2) кВт и скоростях сварки (v) (0.8–1.5) м/мин. Для компенсации металла в сварном шве вследствие пористости и инфильтрации расплава в прилегающие области пористых пластин применяли вставки из соответствующего компактного металла. Для этого нарезались полоски длиной 20 мм, равной ширине свариваемых пластин, высотой немного больше их толщины (2.0–2.9) мм и шириной (0.6–0.8) мм. Титановые – для сварки титановых пластин, стальные – для сварки стали (рис. 1).
При сварке пористых металлов для предотвращения проваливания шва на верхней поверхности (лицевой стороне) необходимо в сварочную ванну водить присадочный материал. Это может быть осуществлено за счет подачи присадочной проволоки, а также путем применения накладки или промежуточной вставки. Применение наплавочной проволоки при лазерной сварке тонколистовых материалов вследствие малых размеров сварочной ванны весьма затруднительно. Применение накладки закрывает стык пластин. Это затрудняет совмещение лазерного луча с границей стыка. Кроме того, требуется зачистка поверхности после сварки для удаления остатков накладки. Поэтому предпочтение было отдано использованию промежуточной вставки. Экспериментально было показано, что в этом случае при правильно выбранных ее параметрах и режимах сварки возможно получение качественного неразъемного соединения пористых металлов.
Были подготовлены вставки различной высоты h = hp + Δh, где hp – толщина свариваемых пластин, Δh – “прибыль” (превышение высоты вставок над поверхностью пластин). Для удобства работы вставку приклеивали к торцам свариваемых встык пластин клеем БФ-6, после чего проводили сушку в течении 10–20 мин.
Для модифицирования сварного шва использовали порошковую композицию, содержащую наночастицы TiN, плакированные титаном [7]. Наномодификатор в виде клеевой суспензии наносился на верхнюю поверхность вставки в области свариваемых торцов в количестве 0.1–0.3% по массе проплавляемого металла.
РЕЗУЛЬТАТЫ ИССЛЕДОВАНИЯ
На рис. 2 представлены фотографии сварных соединений без применения нанопорошка, полученных с использованием промежуточной вставки высотой h = 2 мм (равной толщине пластин, Δh = 0). Соединение на рис. 2а получено при проплавлении лишь с лицевой стороны (верхней поверхности). Мощность лазерного излучения составляла 0.9 кВт, скорость сварки – 1.2 м/мин. Лазерный луч был направлен на середину вставки под прямым углом к ее поверхности, фокусное пятно располагалось на нижней поверхности вставки (заглубление пятна Δf = 2 мм).
Рис. 2.
Морфология сварных швов пористого титана с использованием компактной вставки при режимах сварки: v = = 1.2 м/мин, W = 0.9 кВт, Δf = 2 мм, (а) при Δh = 0 и одноразовом проплавлении с лицевой стороны; (б) при Δh = 0 и двойном проплавлении – с лицевой (верхней) и нижней поверхностей; (в) при Δh/hp = 0.45 и двойном проплавлении – с лицевой (верхней) и нижней поверхностей; (г) при Δh/hp = 0.35 и двойном проплавлении – с лицевой (верхней) и нижней поверхностей.

Видно, что соединение в этом случае (рис. 2а) имеет сквозное, практически бездефектное проплавление, однако с заметной (0.4 мм) впадиной в верхней области шва, образовавшейся вследствие не скомпенсированного оттока жидкости в пористую среду. В связи с непроплавлением нижней кромки вставки было выполнено ее обработка с нижней поверхности. В этом случае (рис. 2б) сварной шов характеризуется впадинами в области соединения, как с верхней, так и нижней поверхностей пластин. При этом ширина проплавленных периферийных областей более чем в 2 раза превышает ширину самой вставки в связи с плавлением пластин и инфильтрацией расплава.
Рисунок 2 (в, г) иллюстрирует морфологию сварных швов при двойном проплавлении промежуточных вставок (сверху и снизу) при v = 1.2 м/мин, W = 0.9 кВт, ∆f = 2 мм и различных значениях их высоты: а – h = 2.9 мм, б – h = 2.7 мм, т.е. превышение высоты вставок ∆h над поверхностью пластин составляло ∆h/hp = 0.45 и ∆h/hp = 0.35 соответственно. Не трудно видеть, что в этом случае над сварным швом формируется валик, высота которого находится в прямой зависимости от ∆h. При этом поверхность корня соединений практически находится в одной плоскости с нижней поверхностью соединяемых пластин. Не симметрия валика на рис. 2в, очевидно, связана с отклонением лазерного луча от средней линии вставки. Наличие валика над швом является упрочняющим фактором, но он может быть не желателен по техническим или иным соображениям.
На рис. 3 представлены результаты экспериментального определения значений величины ∆h, при которой высота валика незначительна или близка к нулю. Было установлено, что при мощности излучения W = 0.9 кВт, скорости сварки v = 0.8 м/мин и заглублении лазерного луча Δf = 2 мм эта величина составляет 0.4–0.5 мм т.е. ∆h/hp ~ 0.20–0.25.
Рис. 3.
Морфология сварных швов пористого титана с использованием компактной вставки при режимах сварки: v = = 0.8 м/мин, W = 0.9 кВт, Δf = 2 мм и двойном проплавлении – с верхней и нижней поверхностей; (а) при Δh/hp = 0.30, (б) при Δh/hp = 0.25.
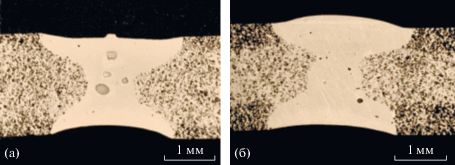
Указанные параметры относятся к сварке рассматриваемых здесь титановых пластин, имеющих среднюю пористость ~33%. При увеличении (уменьшении) пористости, очевидно, потребуется увеличение (уменьшение) “прибыли” ∆h.
Аналогичные исследования проведены для процесса сварки пористых пластин из нержавеющей стали 12ХН10Т с пористостью ~35% и размером 2 × 20 × 50 мм с применением промежуточных вставок из компактной стали того же состава. На рис. 4 представлены фотографии, характеризующие морфологию шва при различных значениях ∆h.
Рис. 4.
Морфология сварных швов пористой стали с использованием компактной вставки при режимах сварки: v = = 1.5 м/мин, W = 1.2 кВт, Δf = 2 мм; а – при Δh/hp = 0.43 и одноразовом проплавлении с лицевой стороны; б – при Δh/hp = 0.35 и одноразовом проплавлении с лицевой стороны; в – при Δh/hp = 0.33 и двойном проплавлении – с лицевой (верхней) и нижней поверхностей; г – при Δh/hp = 0.28 и двойном проплавлении – с лицевой (верхней) и нижней поверхностей.

Как и в случае сварки титановых пластин, большое значение для формирования качественного соединения имеют геометрические параметры вставок, выбирая значения которых можно получать швы с валиком (рис. 4а, 4б), либо заподлицо с основным металлом (рис. 4в, 4г). Установлено, что для формирования шва заподлицо со свариваемыми пластинами толщиной 2 мм и пористостью ~35% высота прибыльной части вставки должна быть равна 0.6 мм (∆h/hp ~ 0.3).
Исследовали влияние на свойства сварного шва нанопорошковых модифицирующих добавок, ранее показавших положительное влияние на структуру и механические характеристики отливок [8], сварных соединений и покрытий при лазерной обработке компактных сплавов [9–11].
Как видно из рис. 5 при сварке титановых образцов структура шва имеет пластинчатое строение типа корзиночного плетения, представленное α‑фазой. Пластины ее разориентированы относительно друг друга. Такая структура характерна для титановых сплавов, в которых произошло полиморфное превращение из β- в α-титан (при охлаждении). Границы макрозерен являются границами первичных β-зерен, а их внутризеренная структура образовалась при последующем охлаждении. На шлифах рис. 5а, 5в видна неравномерная граница между пористым металлом и переплавленным металлом шва. Применение наномодифицирующей добавки привело к повышению дисперсности структуры и уменьшению размера пластин (рис. 5г).
Рис. 5.
Микрофотографии сварного соединения титана: (а, в) переходная зон; (б), (г) центральная зона шва. (а, б) Соединение без наномодификатора; (в, г) с наномодифицирующей добавкой (TiN + Ti).

Из микрофотографий шлифов (рис. 4а, 4б, 6а, 6б) видно, что структура не модифицированного сварного соединения стали имеет грубое столбчатое строение от периферии вплоть до центра шва. Наномодифицрующие добавки уменьшают размер столбчатых дендритов и формируют в центральной зоне шва структуру из равноосных зерен (рис. 4в, 4г, 6в, 6г), что положительно сказывается на механических свойствах сварочного шва.
Рис. 6.
Микрофотографии сварного соединения стали: (а, в) переходная зон; (б), (г) центральная зона шва. (а, б) Соединение без наномодификатора; (в, г) с наномодифицирующей добавкой (TiN + Ti).

Следует заметить, что внутренняя структура и морфология сварных соединений влияют на прочность неразъемного соединения, которая должна быть не ниже прочности основного материала. В связи с этим проводились исследования прочности полученных опытных образцов на разрыв и изгиб. В табл. 1 приведены результаты испытаний модифицированных неразъемных соединений пористых титановых или стальных образцов на разрыв.
Таблица 1.
Временная прочность на разрыв соединений пористых образцов титана и стали
Номер образца титана | Временная прочность на разрыв σB, МПа | Номер образца стали | Временная прочность на разрыв σB, МПа |
---|---|---|---|
1 | 59.64 | 1 | 87.54 |
2 | 60.98 | 2 | 98.68 |
3 | 71.22 | 3 | 74.00 |
4 | 71.03 | 4 | 76.03 |
5 | 77.79 | 5 | 78.06 |
6 | 62.29 | 6 | 80.75 |
Среднее значение | 65.17 | Среднее значение | 82.51 |
Приведенные в таблице данные характеризуют временную прочность сварных соединений. Во всех образцах (как титана, так и стали) разрушение произошло по основному металлу. Это указывает на более высокие значения временного сопротивления разрыву области сварного шва. Рисунок 7 иллюстрирует изменение твердости металла в поперечном направлении в области сварного соединения для не модифицированных и модифицированных образцов из титана (а) или стали (б).
Рис. 7.
Распределение микротвердости поперек области соединения пористых пластин: а – титана, б – стали; 1 – основной металл, 2 – зона инфильтрации, 3 – сварочный шов. Черная линия – без модификатора, серая – с наномодифицирующей добавкой (TiN + Ti).
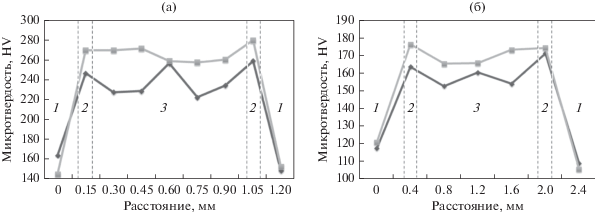
Видно, что микротвердость сварных швов модифицированных образцов несколько выше, чем не модифицированных, и характеризуется более однородным по ширине шва распределением. Учитывая прямую связь прочности с твердостью, это означает, что модифицированные швы имеют более высокие значения прочности по сравнению с не модифицированными.
На рис. 8 представлены результаты испытаний прочности на изгиб сварных соединений титана или стали. Образцы предварительно были подвергнуты термообработке в вакуумной печи при температуре 700°С с целью снятия остаточных сварочных напряжений и стабилизации структуры.
Рис. 8.
Диаграммы прочности на изгиб сварных соединений: а – титана, б – стали. 1 – без модификатора; 2 – с наномодифицирующей добавкой (TiN + Ti); 3 – основной металл.
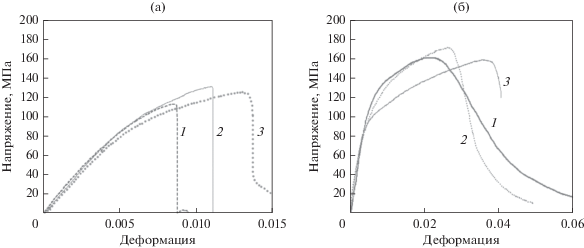
Как видно из графиков, сварные соединения допускают значительный изгиб по линии сварки. При этом прочность на изгиб сварных соединений как титана, так и стали с использованием модификатора несколько выше ~4–7%, чем без модифицирующей добавки.
ВЫВОДЫ
Для получения качественного бездефектного сварного шва необходимо использование промежуточной вставки из компактного металла с прибыльной частью ∆h/hp ~ 0.25–0.30 при исследованном диапазоне пористости. При этом положение фокального пятна следует устанавливать на глубине, равной толщине пластин, а лазерный луч направлять на середину вставки. Применение модифицирующих добавок повышает дисперсность и однородность структуры, что положительно сказывается на механических характеристиках металла. Твердость металла в зоне сварного соединения модифицированных образцов характеризуется более однородным по ширине шва распределением. Испытания прочности на разрыв показали разрушение сварных образцов только по основному металлу. Наномодифицирование повышает прочность сварных соединений титана (стали) на изгиб.
Работа выполнена при финансовой поддержке гранта РФФИ № 08-18-00571а, частично, программ фундаментальных научных исследований государственных академий наук на 2013–2020 годы: проекта АААА-А17-117030610122-6 и проекта АААА-А17-117030610136-3.
Список литературы
Еськов Б.Б., Лагунов Д.В., Лагунов В.С. Пористые материалы. Воронеж: Наука, 1995. 362 с.
Крушенко Г.Г. Технологии и механизм формирования пенометаллов и их применение в летательных аппаратах // Вестник СибГАУ. 2014. № 1(53). С. 154–161.
Shapovalov V. Prospective Applications of Gas-Eutectic Porous Materials (Gasars) in USA// Materials Science Forum. 2007. V. 539–543. P. 1183–1187.
Bunker R.S. Gas turbine cooling. Moving from macro to micro cooling // Proceedings of the ASME Turbo Expo. 2013. P. 3. https://doi.org/10.1115/GT2013-94277
Hammel E., Ighodaro O.L.-R., Okoli O.I. Processing and properties of advanced porous ceramics: an application based review // Ceram. Int. 2014. V. 40. № 10. P. 15351–15370.
Fabrication of Lotus-type Porous Metals and Physical Properties, H. Nakajima, T. Ikeda and S.K. Hyun: Cellular Metals: Manufacture, Properties and Applications, Ed. J. Banhart, N. Fleck and A. Mortensen, Verlag MIT Publ. (2003), 191–202.
Drozdov V.O., Chesnokov A.E., Cherepanov A.N. and Smirnov A.V. Study of the formation process of nanostructured composite powders in a plasma jet // Thermophysics and Aeromechanics. 2019. V. 26. № 5. P. 789–794.
Cherepanov A.N., Ovcharenko V.T. Effect of nanostructured composite powders on the structure and strength properties of the high-temperature inconel 718 alloy// Physics of Metals and Metallography. 2015. V. 116. P. 1279–1284.
Пугачева Н.Б., Сенаева Е.И., Волкова Е.Г., Макаров А.В., Горулева Л.С. Микроструктура выполненного лазерной сваркой соединения хромоникелевой стали и титанового сплава с медной вставкой// Физика металлов и металловедение. 2019. Т. 120. № 8. С. 845–852. https://doi.org/10.1134/S0015323019080126
Черепанов А.Н., Оришич А.М., Овчаренко В.Е., Маликов А.Г., Дроздов В.О., Пшеничников А.П. Влияние наномодифицирующих добавок на свойства многослойного композиционного покрытия, получаемого при лазерной наплавке // ФММ. 2019. Т. 120. № 1. С. 107–112. https://doi.org/10.1134/S0015323019010029
Оришич А.М., Черепанов А.Н., Шапеев В.П., Пугачева Н.Б. Наномодифицирование сварных соединений при лазерной сварке металлов и сплавов. Новосибирск: Изд-во СО РАН, 2014. 252 с.
Дополнительные материалы отсутствуют.
Инструменты
Физика металлов и металловедение