Физика металлов и металловедение, 2022, T. 123, № 12, стр. 1304-1312
Роль структурной наследственности в управлении функционально-механическими характеристиками стареющего никелида титана
Е. П. Рыклина a, *, К. А. Полякова a, С. Р. Мурыгин a, В. С. Комаров a, Н. Н. Реснина b, В. А. Андреев c
a НИТУ “МИСиС”
119049 Москва, Ленинский просп., 4/1, Россия
b СПбГУ
199034 Санкт-Петербург, Университетская наб., 7–9, Россия
c ИМЕТ РАН
119334 Москва, Ленинский просп., 49, Россия
* E-mail: ryklina@tmo.misis.ru
Поступила в редакцию 09.06.2022
После доработки 05.07.2022
Принята к публикации 23.07.2022
- EDN: KDVOEF
- DOI: 10.31857/S0015323022600605
Аннотация
Проведены сравнительные исследования функционально-механических характеристик сплава Ti−50.8 ат. % Ni в разных исходных структурных состояниях и после старения при 430°С, 10 ч; проанализированы особенности эволюции исследуемых параметров при деформации растяжением в интервале температур −196°С ≤ Т ≤ +100°С. Наиболее высокий уровень прочностных характеристик (до 1500 МПа), а также наибольшая разница между дислокационным и фазовым пределами текучести (до 1200 МПа) реализуется в результате старения сплава с исходной развитой дислокационной структурой и аморфизированным объемом ~30%. Эффективность старения материала с исходно рекристаллизованной структурой зависит от размера зерна: функционально-механические характеристики мелкозернистого сплава практически не изменяются; в исходно крупнозернистом они существенно повышаются. Полученные закономерности могут быть использованы для прогнозирования комплекса функционально-механических свойств, формирующегося в результате старения никелида титана с разной исходной структурой.
ВВЕДЕНИЕ
Научные основы управления функционально-механическими свойствами никелида титана базируются на установленной взаимосвязи между структурой, полученной в результате деформации с применением разных схем напряженно-деформированного состояния и последеформационного отжига (ПДО) [1–3]. Стареющие сплавы на основе никелида титана остаются наиболее востребованными, поскольку именно старение позволяет варьировать их структуру и характеристики формовосстановления в широком диапазоне; эта уникальная особенность делает их незаменимыми при разработке и создании интеллектуальных конструкций медицинского назначения [4–6]. Анализ опубликованных данных [7–10] позволяет заключить, что исходная (перед старением) структура оказывает выраженное влияние на размер, морфологию и характер распределения частиц фазы Ti3Ni4, выделяющихся при старении, что позволяет констатировать существование структурной наследственности.
Сформировавшаяся в результате старения микроструктура (далее “микроструктура старения”) влияет на стадийность и последовательность мартенситных превращений (МП) [7–9, 11, 12]. Оба этих фактора – особенности микроструктуры старения и МП, должны оказывать влияние на функционально-механические характеристики. Сравнение данных, полученных в работах [13–15], подтверждает это предположение. Цитируемые публикации, тем не менее, не позволяют составить исчерпывающего представления о характере корреляции исходной структуры, микроструктуры старения и функционально-механических свойств, поскольку сравнительные испытания проводили при конкретных температурах без учета температурного диапазона МП, в котором сплавы с ЭПФ проявляют свои свойства. Таким образом, возможности старения при варьировании исходной структуры как фактора, влияющего на конечный комплекс свойств никелида титана, остаются неизученными. Отсутствие таких данных свидетельствует о существовании серьезных пробелов, препятствующих созданию полноценной научной базы для управления функционально-механическими характеристиками, определяющими ресурс формовосстановления сплавов с памятью формы. Очевидно, что проведение подобных исследований принципиально важно, поскольку известно, что варьирование исходного фазового состояния, определяемого температурой, является мощным инструментом управления функциональными характеристиками [13–17]. Исследования, выполненные в рамках настоящей работы, восполняют обозначенный пробел и позволяют выявить особенности проявления структурной наследственности при старении никелида титана в реализации функционально-механических характеристик в широком температурном диапазоне.
МАТЕРИАЛ И МЕТОДИКИ ИССЛЕДОВАНИЯ
Исследования проводили на проволочных образцах сплава Ti–50.8 ат. % Ni (с содержанием примесей, ат. %: О − 0.1; C − 0.037; H − 0,0072; N − 0.009 ат. %), полученного в ОOО “ПЦ МАТЭК-СПФ” в соответствии с технологическим процессом, описанным в [18]. Образцы диаметром 0.6 мм, полученные в результате многопроходного холодного волочения с накопленной истинной (логарифмической) деформацией е = 0.6, были разделены на 3 группы: одна часть образцов оставлена в исходном деформированном состоянии, вторую и третью часть подвергали ПДО при 600 и 800°С, 1 ч для получения рекристаллизованной структуры с размером зерна 3 и 9 мкм соответственно (табл. 1). В правом столбце табл. 1 приведены ссылки на источники, содержащие детальное описание исходных структурных состояний исследуемого сплава.
Таблица 1.
Режимы обработки образцов, полученных холодным волочением с накопленной деформацией е = 0.6 и соответствующие им структурные состояния
Все три группы образцов подвергали последующему старению при 430°С в течение 10 ч; интервал температур 420−440°С был определен в работах [12, 20] как оптимальный с точки зрения максимальной интенсивности старения.
Структурные исследования проводили с использованием просвечивающего электронного микроскопа (ПЭМ) JEM-2100 при ускоряющем напряжении 200 кВ. Калориметрические кривые записывали при скоростях нагрева и охлаждения 10°С/мин с использованием калориметра марки “Mettler Toledo 822е”; температуры начала и окончания прямых и обратных мартенситных превращений определяли методом касательных по стандарту ASTM F2004-17. Испытания на растяжение проводили с использованием образцов длиной 100 мм на универсальной разрывной машине “INSTRON 5966” до разрушения со скоростью деформации 20 мм/мин в диапазоне температур −196 ≤ Т ≤ 100°С. Непосредственно перед испытанием образцы погружали в кипяток и сразу переносили в испытательную камеру с заданной температурой. По диаграммам растяжения определяли функционально-механические характеристики в исходном состоянии и после старения.
РЕЗУЛЬТАТЫ И ОБСУЖДЕНИЕ
В условиях старения (430°C, 10 ч) холодно-деформированного сплава формируется структура, представляющая собой смесь рекристаллизованных зерен и субзерен полигонизованной субструктуры B2-аустенита размером ~40 нм (рис. 1а). На картине микродифракции определяется наложение дуговых рефлексов от наносубзерен и распределенных по кольцу точечных рефлексов от нанозерен; регистрируются рефлексы фаз (110)В2 и (211)В2, (221)R, (121)В19′. Выделения фазы Ti3Ni4 на светлопольных и темнопольных изображениях визуально не определяются, при этом соответствующие рефлексы (133) на электронограммах присутствуют.
Рис.1.
Микроструктура (ПЭМ) после старения в разных исходных состояниях: а) е = 0.6; б) 600°С; в) 800°С; НЗ – нанозерна; НС – наносубзерна.
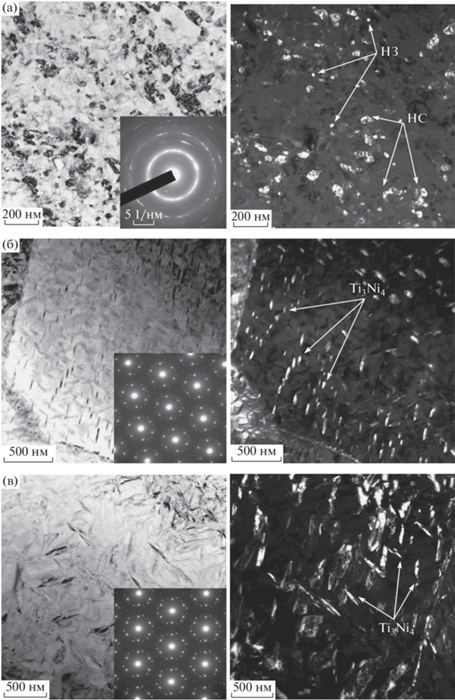
Размер частиц фазы Ti3Ni4 и характер их распределения в структуре с исходным рекристаллизованным зерном зависит от его размера. В обоих случаях характер распределения частиц в объеме зерна гетерогенный: в мелкозернистой структуре он выражен слабо (рис. 1б), а в материале с более крупным зерном усиливается (рис. 1в).
Размер частиц минимален в приграничных зонах и увеличивается к центру зерна, расстояние между частицами растет, а линейная частота их распределения и объемная доля уменьшаются. Трехкратное увеличение размера зерна (с 3 до 9 мкм) коррелирует с ростом диаметра частиц в 2 раза в приграничных зонах и в 3 раза в центре зерна. При переходе от приграничной зоны к центру зерна, а также при увеличении размера зерна форма частиц изменяется с эллиптической на линзовидную уплощенную. Наиболее вытянутые частицы, диаметр которых в 8 раз превосходит их толщину, обнаружены в центре зерна размером 9 мкм [9]. В крупных частицах фазы Ti3Ni4 после старения наблюдается фрагментация за счет образования субграниц (рис. 1в), что косвенно свидетельствует о потере когерентности частиц фазы Ti3Ni4 с В2-матрицей [21].
Формирующаяся при старении микроструктура оказывает выраженное влияние на кинетику и стадийность МП. Результаты калориметрических исследований позволяют выявить следующие закономерности. Непосредственно после холодной деформации прямые и обратные МП отсутствуют, что характерно для сильно наклепанного материала (ρ ≅ 1012–13 cм−2) с частично аморфизированной структурой [1]. После отжига при 430°С, 10 ч определяется одно прямое превращение В2 → R при 40°С и соответствующее обратное R → В2 при 44°С (рис. 2). Начало прямого МП R → B19' определяется при температуре −48°С, при этом само превращение протекает в широком интервале температур. Пик обратного МП B19' → R регистрируется при температуре 20°С.
После рекристаллизационного отжига при 600°С прямые МП В2 → R и R → B19' перекрываются, их пики очень близки (9 и 1°С соответственно). Обратные МП протекают по схеме B19' → R(2) → В2. Последующее старение приводит к обособлению калориметрических пиков прямых МП и почти двукратному уширению общего интервала прямых МП (с 24 до 46°С).
Увеличение размера рекристаллизованного зерна до 9 мкм (ПДО 800°С, 1 ч) приводит к появлению одностадийного МП В2 → B19' (без промежуточной R фазы); с пиком при −37°С; обратное МП B19' → B2 определяется при −13°С. После старения наблюдается трехступенчатое МП B2 → R, R → B19'(1), B19' → В2(2); пики регистрируются при 43, 6 и −9°С соответственно. При обратном МП определяются практически два сливающихся пика B19'(2) → B2 и B19'(1) → B2-превращений при температурах 45 и 50°С соответственно (рис. 2).
Полученные закономерности могут быть объяснены с привлечением опубликованных данных [9]. Известно, что зарождение частиц фазы Ti3Ni4 энергетически более выгодно в зонах с дисторсией кристаллической решетки В2-аустенита [16]: чем выше дефектность исходной структуры, тем больше центров зарождения частиц. Наибольшей дефектностью из трех типов исходной структуры обладает холоднодеформированная (рис. 1а), плотность дефектов в которой оценивается как ρ ≅ ≅ 1012−13cм−2 при относительно равномерном их распределении [1]. В такой структуре частицы фазы Ti3Ni4 растут в одинаковых условиях конкурирующего роста, их размер остается в пределах 3−5 нм [10].
В исходной мелкозернистой структуре плотность дефектов решетки в целом выше (ρ ≅ 108 cм−2), чем в более крупнозернистой (ρ ≅ 106−7 cм−2) [1]. Концентрация дефектов в приграничной зоне зерна выше, чем в центре [22]; эта разница не так значительна в мелком зерне по сравнению с крупным. Аналогичный характер изменения концентрации никеля по сечению зерна обнаружен в работе [9] при использовании энергодисперсионного анализа: в более крупном зерне сегрегация Ni в приграничной зоне достигает 54 ат. %. Это объясняет наблюдаемые различия: в мелком зерне центров зарождения частиц больше, чем в крупном, а при одинаковой концентрации никеля по сечению зерна частицы фазы Ti3Ni4 зарождаются и растут в условиях конкурирующего роста [23, 24]. В крупнозернистой структуре с более низкой общей плотностью дефектов центров зарождения частиц меньше, а в условиях повышенной концентрации никеля в приграничных зонах частицы в процессе их роста при таком же времени старения достигают значительно бóльших размеров. Эти же факторы объясняют различие в размере и характере распределения частиц в приграничной зоне и центре более крупного зерна.
Наблюдаемый характер МП в различной исходной структуре в целом отвечает известным закономерностям. Уменьшение концентрации дефектов структуры при повышении температуры рекристаллизационного отжига способствует “вырождению” В2 → R-превращения, переходу к одностадийному мартенситному превращению, сужению интервалов превращений вследствие повышения структурной однородности аустенита и их смещению в область более высоких температур [1, 9, 16].
После старения при 430°С исходного холоднодеформированного материала плотность дефектов остается достаточно высокой (ρ ≅ 1010 cм−2) [1], что создает серьезные препятствия для движения межфазных границ при протекании прямого МП и подавляет образование мартенсита. В мелкозернистой структуре в соответствии с законом распределения Гаусса присутствует большое количество мелких зерен (менее 2 мкм), в которых образование мартенсита также подавлено за счет выделения дисперсных частиц фазы Ti3Ni4 при высокой плотности их распределения [24]. В соответствии с данными, полученными с использованием съемки “in situ” в работе [23], в приграничных зонах зерна с мелкими частицами при их высокой плотности распределения образование мартенсита также подавлено. Такая структурная неоднородность объясняет расширение интервала прямых МП.
В структуре с размером исходного зерна 9 мкм, в соответствии с данными [23], полученными в результате исследований “in situ”, МП в зерне с гетерогенным распределением частиц фазы Ti3Ni4 протекают не одновременно, а последовательно в разных зонах зерна, отличающихся размером, морфологией и плотностью распределения частиц. В такой структуре присутствуют все типы МП, присущих стареющим сплавам Ti−Ni [9, 23]. При охлаждении и нагреве МП в приграничной зоне зерна развиваются через промежуточную R-фазу. Прямое В2 → В19'-превращение протекает в центральной зоне зерна при самой низкой температуре [23]; оно является следствием нарушения когерентной связи при укрупнении частиц до ~350 нм и обеднения В2-аустенита никелем (трактовка этого МП обоснована Зельдовичем с соавторами [25]).
На основании результатов калориметрических исследований были выбраны температуры деформации для проведения испытаний на растяжение, соответствующие разным фазовым состояниям; температура Мs (температура начала прямого МП, она же температура легкой деформации [16]) была выбрана для всех структурных состояний.
На рис. 3 приведены сравнительные диаграммы температурной зависимости исследуемых характеристик до и после старения: предела проч-ности (σuts), дислокационного предела текучести (σу), фазового предела текучести (σtr); критического напряжения переориентации мартенсита охлаждения (σcr). Обозначены точки Мs и $M_{{\text{s}}}^{\sigma }$ (температура образования мартенсита напряжений [16, 26]). Во всех случаях анализировали изменение значений Δσ = σу − σtr, поскольку эта характеристика определяет ресурс обратимой деформации материала [14, 16, 26] и позволяет оценить эффективность старения никелида титана в разных исходных структурных состояниях.
Рис. 3.
Диаграммы температурной зависимости функционально-механических характеристик и пример их определения (а) в исходном состоянии (а−в) и после старения (г–е): σuts − предел прочности; σу − дислокационный предел текучести; σtr − фазовый предел текучести; Δσ = σу − σtr (на диаграммах показаны значения Δσ при температурах Мs и Мs + 60°С; σcr − критическое напряжение переориентации мартенсита охлаждения.
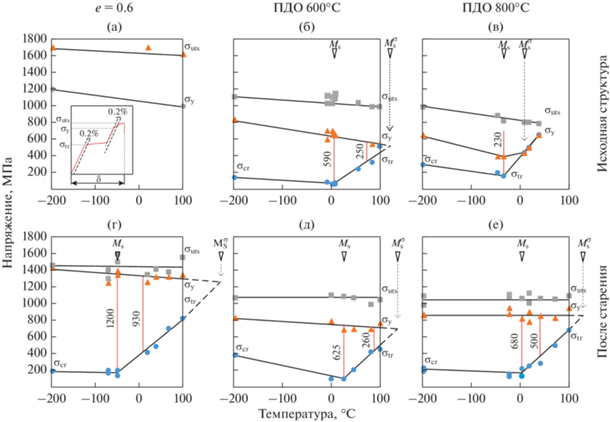
Максимальные значения прочностных характеристик реализуются непосредственно после холодного волочения: σuts в диапазоне 1600–1700 МПа и σу в диапазоне 1100–1200 МПа, снижаясь с повышением температуры испытания (рис. 3а). Фазовый предел текучести не определяется из-за подавления всех МП (см. рис. 2а).
При развитии рекристаллизации и росте размера зерна (ПДО 600−800°С) происходит снижение общего уровня прочностных характеристик (σuts и σу). Общий уровень значений σtr и σcr при этом меньше в мелкозернистом материале (70−500 МПа, см. рис. 3б) по сравнению с крупнозернистым (180−650 МПа, см. рис. 3в). При увеличении размера зерна происходит сближение дислокационного и фазового пределов текучести за счет снижения общего уровня значений σy и повышения значений σcr и σtr (см. рис. 3б, 3в). При этом максимальное значение Δσ при температуре Мs снижается с 590 МПа до 230 МПа. В крупнозернистом материале при температурах испытания выше 10°С значения σу и σtr отдельно не определяются (см. рис. 3в).
После старения во всех случаях происходит сближение прочностных характеристик по сравнению с исходным состоянием (см. рис.3). Следует заметить, что после старения значения предела прочности становятся нечувствительными к температуре испытания во всех структурных состояниях. Максимальный уровень значений σuts и σу реализуется в диапазоне 1350−1450 МПа в результате старения сплава с исходной структурой деформационного наклепа (см. рис. 3г). Несмотря на подавление прямого МП (см. рис. 2), фазовый предел текучести уверенно определяется при всех температурах деформации; общий уровень значений σcr−σtr изменяется в пределах 180−800 МПа. Этот режим обработки обеспечивает наибольшую разницу Δσ = 1200 МПа при температурах испытания ниже Мs.
Старение сплава с мелкозернистой структурой приводит к некоторому сближению прочностных характеристик за счет повышения общего уровня дислокационного предела текучести до 560−820 МПа (см. рис. 3д); при этом значения предела прочности не изменяются по сравнению со значением в исходном несостаренном состоянии (см. рис. 3б). Общий уровень значений фазового предела текучести практически не изменяется после старения по сравнению с исходным состоянием; величина Δσ увеличивается незначительно (с 590 до 625 МПа) при температуре Мs.
В результате старения исходно крупнозернистого материала происходит значительный рост прочностных характеристик и их заметное сближение (см. рис. 3в, 3е). При этом уровень их значений во всем температурном диапазоне остается постоянным. Общий уровень значений фазового предела текучести практически не изменяется после старения по сравнению с исходным несостаренным состоянием (см. рис. 3е). Величина Δσ после старения увеличивается в 3 раза по сравнению с исходным состоянием (с 230 до 680 МПа). Температура образования мартенсита напряжений $M_{{\text{s}}}^{\sigma }$ в результате старения сдвигается в область более высоких температур, причем этот эффект более выражен в крупнозернистом материале по сравнению с мелкозернистым.
Особенности эволюции пластичности в исходном состоянии и после старения позволяют проследить диаграммы, приведенные на рис. 4. Минимальные значения относительного удлинения при разрушении (δ ≤ 8%) определяются в исходной деформированной структуре и повышаются до 14–16% в результате старения.
Рис. 4.
Температурная зависимость относительного удлинения в исходном состоянии (синие кривые) и после старения (красные кривые).
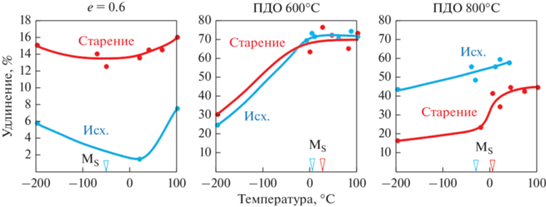
Старение исходной мелкозернистой структуры не приводит к заметным изменениям пластичности. В исходной крупнозернистой структуре пластичность выше (45 ≤ δ ≤ 55%), чем в состаренном состоянии (18 ≤ δ ≤ 42%, см. рис. 4). Максимальные значения пластичности наблюдаются вблизи точки Мs, что хорошо согласуется с данными [16, 27].
Полученные результаты представляются вполне логичными и закономерными. Дислокационный предел текучести определяется в основном размером зерна (субзерна), подчиняется закону Холла–Петча и коррелирует с изменением предела прочности в интервале температур от −196°С до 100°С. Характер температурной зависимости исследуемых параметров на всех стадиях разупрочнения в целом укладывается в известные сведения о механизмах структурных процессов при деформации никелида титана [16, 26]. Значения фазового предела текучести определяется положением температуры деформации относительно температуры начала прямого МП и подчиняется уравнению Клапейрона−Клаузиуса. Для напряжения критической переориентации мартенсита (σcr) характерна слабая температурная зависимость в отличие от фазового предела текучести. Максимальные значения параметра Δσ определяются в области температур испытаний ниже точки Мs при переориентации мартенсита охлаждения. Развитие рекристаллизации сопровождается снижением прочностных характеристик и сближением значений дислокационного и фазового пределов текучести, преимущественно за счет снижения σу.
Снижение прочностных характеристик в зависимости от температуры деформации при растяжении объясняется изменением фазового состояния: ниже температуры Мs стабильной фазой является В19'-мартенсит, а выше точки Мs − В2-аустенит, R‑фаза или их смесь, которые обладают меньшей прочностью [16, 26]. После старения значения предела прочности не зависят от температуры испытания, что характерно для всех структурных состояний.
Выявленные закономерности позволяют заключить, что эффективность влияния старения на функционально-механические характеристики никелида титана определяется особенностями исходной структуры, в частности, плотностью и характером распределения дефектов кристаллической решетки, и размером зерна. Смещение температуры легкой деформации (минимальное значение σtr) на диаграммах в точности совпадает со смещением положения точки Мs на калориметрических кривых и также позволяет судить об эффективности старения.
В холоднодеформированном материале при температуре 430°С процессы старения и разупрочнения протекают одновременно; эти факторы являются конкурирующими. Наблюдаемое снижение прочностных характеристик в результате старения (рис. 3г) позволяет предположить, что предел прочности оказывается в большей степени чувствителен к разупрочнению, в результате которого напряжение, необходимое для зарождения микротрещины, смещается в область более высоких значений. При этом упрочнение в результате старения вносит больший вклад в повышение дислокационного предела текучести.
Полученные результаты хорошо согласуются с данными авторов [27, 28], полученными в результате испытаний по схеме растяжения при комнатной температуре никелида титана, подвергнутого холодной деформации и последующему старению в интервале температур 400−500°С.
Наблюдаемые различия влияния старения сплава с разным размером рекристаллизованного зерна могут быть объяснены с использованием следующих известных данных. Ресурс повышения прочностных характеристик рекристаллизованного никелида титана за счет дисперсионного твердения при старении ограничивается уровнем значений 1200 МПа для предела прочности и 600−800 МПа для дислокационного предела текучести [14, 27, 28]. Поскольку мелкозернистый никелид титана имеет достаточно высокие прочностные характеристики в исходном несостаренном состоянии (σuts = 1100–1200 МПа и σу = 600–800 МПа), в результате старения мы наблюдаем небольшое повышение этих характеристик на 100−200 МПа. Следует подчеркнуть, что в результате старения исходно боле крупнозернистого никелида титана реализуется эквивалентный уровень прочностных характеристик. Другими словами, размер рекристаллизованного зерна оказывает выраженное влияние на комплекс функционально-механических характеристик никелида титана в широком интервале температур. В результате старения это различие практически стирается.
Неизменный уровень предела прочности после старения во всем интервале температур испытаний свидетельствует об упрочнении В2-аустениты и R-мартенсита; при этом старение не приводит к дополнительному упрочнению мартенсита охлаждения. Слабо выраженное влияние старения на уровень значений фазового предела текучести и критического напряжения переориентации мартенсита согласуется с данными [16].
Сравнительный анализ данных, полученных авторами [14, 15, 27, 28], позволяет заключить, что для реализации максимального уровня прочностных характеристик никелида титана продолжительность старения может быть ограничено одним часом; при этом для достижения максимальной реализации эффектов памяти формы в сплаве с исходно крупнозернистой структурой время старения целесообразно увеличивать до 10 ч.
Полученные закономерности могут быть использованы для прогнозирования комплекса функционально-механических свойств, формирующегося в результате старения никелида титана с разной исходной структурой.
ВЫВОДЫ
1. Исходная структура никелида титана решающим образом определяет микроструктру, формирующуюся в процессе старения: размер, форму и характер распределения частиц фазы Ti3Ni4. Это влияние обусловлено различием в плотности дефектов кристаллической решетки в исходной структуре и характере их распределения, размером рекристаллизованного зерна, а также градиентом концентрации никеля в объеме рекристал-лизованного зерна.
2. Исходная структура В2-аустенита и микроструктура старения выраженно влияют на последовательность и стадийность мартенситных превращений.
3. Эффективность старения с точки зрения воздействия на функционально-механические характеристики определяется особенностями исходной структуры:
− наиболее высокий уровень прочностных характеристик, а также наибольшая разница между дислокационным и фазовым пределами текучести до 1200 МПа реализуется в результате старения при 430°С (10 ч) сплава с исходной развитой дислокационный структурой и частичной аморфизацией;
− функционально-механические характеристики сплава с мелкозернистой структурой изменяются незначительно;
− в материале с исходно крупнозернистой структурой комплекс функционально-механических характеристик существенно повышается.
4. Старение позволяет обеспечить эквивалентный уровень функционально-механических характеристик никелида титана в широком температурном интервале вне зависимости от размера исходного зерна.
Работа выполнена при поддержке Минобрнауки России в рамках государственного задания (код проекта 0718-2020-0030).
Список литературы
Prokoshkin S., Brailovski V., Inaekyan K., Korotitskiy A., Kreitsberg A. Thermomechanical Treatment of TiNi Intermetallicc-Based Shape Memory Alloys // Mat. Sci. Found. 2015. V. 81–82. P. 260–341.
Zhapova D., Grishkov V., Lotkov A., Timkin V., Gusarenko A., Rodionov I. Behavior of inelastic and plastic strains in coarse-grained Ti–49.3Ni–50.7 (at %) alloy deformed in B2 states // Metals. 2021. V. 11. № 5. P. 741.
Kreitcberg A., Brailovski V., Prokoshkin S., Gunderov D., Khomutov M., Inaekyan K. Effect of the grain/subgrain size on the strain-rate sensitivity and deformability of Ti–50 at % Ni alloy // Mat. Sci. Eng. A. 2015. V. 622. P. 21–29.
Auricchio F., Boatti E., Conti M., Marconi S. SMA biomedical applications. Shape Memory Alloy Engineering: For Aerospace, Structural, and Biomedical Applications. Butterworth-Heinemann. 2021. P. 627–658.
Mohd Jani J., Leary M., Subic A., Gibson M.A. A review of shape memory alloy research, applications and opportunities // Mater. Des. 2014. V. 56. P. 1078–1113.
Khmelevskaya I.Yu., Ryklina E.P., Prokoshkin S.D., Markossian G.A., Tarutta E.P., Iomdina E.N. A shape memory device for the treatment of high myopia // Mat. Sci. Eng. A. 2008. V. 481–482. P. 651–653.
Khalil-Allafi J., Eggeler G., Dlouhy A., Schmahl W., Somsen C. On the influence of heterogeneous precipitation on martensitic transformations in a Ni-rich NiTi shape memory alloy // Mater. Sci. Eng: A. 2004. V. 378. № 1–2. P. 148–151.
Khalil-Allafi J., Dlouhy A., Eggeler G. Ni4Ti3-precipitation during aging of NiTi shape memory alloys and its influence on martensitic phase transformations // Acta Mater. 2002. V. 50. № 17. P. 4255–4274.
Ryklina E.P., Polyakova K.A., Tabachkova N.Y., Resnina N.N., Prokoshkin S.D. Effect of B2 austenite grain size and aging time on microstructure and transformation behavior of thermomechanically treated titanium nickelide // JALCOM. 2018. V. 764. P. 626–638.
Poletika T.M., Girsova S.L., Lotkov A.I. Ti3Ni4 precipitation features in heat-treated grain/subgrain nanostructure in Ni-rich TiNi alloy // Intermet. 2020. V. 127. Cтaтья № 106966.
Wang X., Kustov S., Li K., Schryvers D., Verlinden B., Humbeeck V. Effect of nanoprecipitates on the transformation behavior and functional properties of a Ti–50.8 at % Ni alloy with micron-sized grains // Acta Mater. 2015. V. 82. P. 224–233.
Kolobova A.Y., Ryklina E.P., Prokoshkin S.D., Inaekyan K.E., Brailovskii V. Study of the Evolution of the Structure and Kinetics of Martensitic Transformations in a Titanium Nickelide upon Isothermal Annealing after Hot Helical Rolling // Phys. Met. Metall. 2018. V. 119. № 2. P. 134–145.
Ostropiko E., Yu Konstantinov A. Functional behaviour of TiNi shape memory alloy after high strain rate deformation // Mat. Sci. Techn. 2021. V. 37. № 8. P. 794–804.
Polyakova, K.A., Ryklina, E.P., Prokoshkin, S.D. Effect of Grain Size and Ageing-Induced Microstructure on Functional Characteristics of a Ti–50.7 at % Ni Alloy // Shape Mem. Super. 2020. V. 6. № 1. P. 139–147.
Polyakova K., Ryklina E., Prokoshkin S. Thermomechanical response of Titanium Nickelide on austenite grain/subgrain size // Mat. Tod.: Proc. 2017. V. 4. № 3. P. 4836–4840.
Otsuka K., Ren X. Physical metallurgy of Ti–Ni-based shape memory alloys // Progr. Mat. Sci. 2005. V. 50. № 5. P. 511–678.
Ryklina E., Prokoshkin S., Vachiyan K. Nanostructured titanium nickelide: Realization of abnormally high recovery strain // IOP Conf. Ser.: Mater. Sci. Eng. 2014, V. 63. № 1. P. 012110.
Prokoshkin S., Khmelevskaya I., Andreev V., Karelin R., Komarov V., Kazakbiev A. Manufacturing of long-length rods of ultrafine-grained Ti–Ni shape memory alloys // Mat. Sci. For. 2018. V. 918 MSF. P. 71–76.
Ryklina E.P., Ashimbaev D.A., Murygin S.R. Thermokinetics of shape recovery of nanostructured titanium nickelide // Lett. Mat. 2022. V.12. № 2. P. 89–93.
Ryklina E.P., Prokoshkin S.D., Chernavina A.A., Perevoshchikova N.N. Investigation on the influence of thermomechanical conditions of induction and structure on the shape memory effects in Ti−Ni alloy // Inorg. Mat. 2010. V. 1. № 3. P. 188–194.
Зельдович В.И., Собянина Г.А., Пушин В.Г., Хачин В.Н. Фазовые превращения в сплавах никелида титана. II. Процесс старения при непрерывном охлаждении // ФММ. 1994. Т. 77. № 1. С. 114–120.
Горелик С.С., Добаткин С.В., Капуткина Л.М. Рекристаллизация металлов и сплавов. М.: МИСиС, 2005. 432 с.
Karbakhsh Ravari B., Farjami S., Nishida M. Effects of Ni concentration and aging conditions on multistage martensitic transformation in aged Ni-rich Ti–Ni alloys // Acta Mater. 2014. V. 69. P. 17–29.
Wang X., Li C., Verlinden B., Humbeeck J.V. Effect of grain size on aging microstructure as reflected in the transformation behavior of a low-temperature aged Ti–50.8 at % Ni alloy // Scr. Mater. 2013. V. 69. № 7. P. 545–548.
Зельдович В.И., Хомская И.В., Фролова Н.Ю., Сбитнева Г.А. О зарождении R-мартенсита в никелиде титана // ФММ. 2001. Т. 92. № 5. С. 71–76.
Prokoshkin S.D. Chapter 4 Shape memory effects / in: Brailovski V., Prokoshkin S., Terriault P., Trochu F.: Shape Memory Alloys: Fundamentals, Modeling, Applications. ÉTS Publ, Montreal 2003. 851 p.
Сплавы никелида титана с памятью формы. Часть I. Структура и фазовые превращения. / Под научной редакцией В.Г. Пушина. Екатеринбург: Изд. РАН, 2006. 440 с.
Pushin V.G. Alloys with a thermomechanical memory: structure, properties, and application // Phys. Met. Metal. 2000. V. 90. № 1. P. 68–95.
Дополнительные материалы отсутствуют.
Инструменты
Физика металлов и металловедение