Физика металлов и металловедение, 2022, T. 123, № 12, стр. 1355-1361
Сверхпрочность наноструктурных металлических материалов: физическая природа и механизмы упрочнения
Р. З. Валиев a, b, *, Э. И. Усманов a, b, Л. Р. Резяпова a
a Институт физики перспективных материалов ФГБОУ ВО УГАТУ
450000 Уфа, ул. К. Маркса, 12, Россия
b ФГБОУ ВО Башкирский государственный университет
450076 Уфа, ул. Заки Валиди, 32, Россия
* E-mail: ruslan.valiev@ugatu.su
Поступила в редакцию 02.09.2022
После доработки 10.10.2022
Принята к публикации 20.10.2022
- EDN: BBKUCI
- DOI: 10.31857/S0015323022601180
Аннотация
Ультрамелкозернистые (УМЗ) металлические материалы, полученные интенсивной пластической деформацией (ИПД), типично проявляют очень высокие прочностные свойства, значения которых значительно выше, чем предсказывает известное соотношение Холла–Петча. Наши исследования показывают, что причиной этого является то, что ИПД не только формирует УМЗ-структуру, но и приводит к образованию других наноструктурных особенностей – дислокационных субструктур, нанодвойников, наноразмерных выделений вторых фаз, которые вносят дополнительный вклад в упрочнение. При этом проведенный анализ механизмов упрочнения свидетельствует, что важный вклад в упрочнение вносят также структура и состояние границ зерен – их неравновесность, наличие зернограничных сегрегаций. На этой основе обсуждаются подходы достижения в металлических материалах очень высокой прочности, используя ИПД.
ВВЕДЕНИЕ
Как известно, прочностные свойства чистых металлов и сплавов определяются несколькими факторами, но средний размер зерна, как правило, играет основную роль [1, 2]. В частности, зависимость прочности различных поликристаллических материалов от среднего размера зерен d обычно описывается известным уравнением Холла–Петча, согласно которому предел текучести σy имеет вид:
(1)
${{{{\sigma }}}_{{\text{y}}}} = {{{{\sigma }}}_{0}} + {{k}_{{{\text{HP}}}}}{{d}^{{ - {1 \mathord{\left/ {\vphantom {1 2}} \right. \kern-0em} 2}}}},$В этой связи прочность чистых металлов и сплавов может быть существенно повышена за счет формирования в их объеме ультрамелкозернистой (УМЗ) структуры со средним размером зерен менее 1 мкм и преимущественно большеугловыми границами, что возможно реализовать методами интенсивной пластической деформации (ИПД) [3–5]. Для этой цели в настоящее время наиболее популярными являются такие методы ИПД как равноканальное угловое прессование (РКУП), интенсивная пластическая деформация кручением (ИПДК) и ряд других. Деформационная обработка материалов с помощью методов ИПД стала ключевым шагом, положившим начало комплексным исследованиям механических свойств объемных наноматериалов, и сейчас является основой для многочисленных исследований различных наноструктурных металлических материалов (см. недавние обзоры и книги по этой тематике) [5–10]. Выполненные работы включают в себя изучение механизмов упрочнения, пластичности и способов ее повышения, усталости, ударной вязкости и других служебных свойств.
За последние два десятилетия в целом ряде работ (см., напр., [3–10]) было довольно подробно изучено влияние уменьшения размера зерен до нанометрового диапазона на прочность материалов. Во многих исследованиях, как правило, наблюдали повышение прочности с уменьшением размера зерна в соответствии с уравнением (1), однако для наноразмерных зерен (менее 50–100 нм) это соотношение часто нарушается, так что кривая Холла–Петча отклоняется от линейной зависимости, и ее наклон kHP становится отрицательным (рис. 1, кривая 1) (см, напр., [5]). Эта проблема подвергалась широкому анализу во многих экспериментальных и теоретических исследованиях. Кроме этого, в нескольких недавних работах было показано, что УМЗ-материалы могут обладать значительно более высокой прочностью, чем прогнозируется по соотношению Холла–Петча для диапазона ультрамелких зерен (см. рис. 1, кривая 2) [11, 12]. Причина такой сверхпрочности может быть связана с влиянием различных наноструктурных особенностей, наблюдаемых в металлах и сплавах, подвергнутых ИПД и находящихся как в объеме зерен (дислокационные субструктуры, наноразмерные частицы вторичных фаз, нанодвойники), так и по их границам (нанокластеры и сегрегации) [10].
В связи с этим актуальной задачей, рассматриваемой в настоящей статье, является анализ природы сверхпрочности УМЗ-материалов с учетом действия различных механизмов упрочнения, включающих в себя как известные, обусловленные присутствием наночастиц и других указанных наноструктурных особенностей, так и новые, связанные с влиянием зернограничных структур в УМЗ-материалах.
ЭКСПЕРИМЕНТАЛЬНЫЕ НАБЛЮДЕНИЯ
В последнее десятилетие был выполнен целый ряд исследований прочностных свойств различных наноструктурных металлов и сплавов, включая Al сплавы [13, 14], стали [15, 16], а также титановые материалы [17]. Во всех случаях при измельчении микроструктуры методами ИПД наблюдали значительное повышение прочности материалов, при этом значения предела текучести существенно превышали значения, рассчитанные из соотношения Холла–Петча. Данное положение иллюстрирует рис. 2 [13], где видно, что значения пределов текучести для УМЗ Al-сплавов 1570 и 7475 с размером зерен около 100 нм значительно выше, чем предсказывает соотношение Холла–Петча для близких Al сплавов с аналогичным размером зерен.
Рис. 2.
Зависимость предела текучести от среднего размера зерен для Al сплавов 1100 и Al–3% Mg и значения предела текучести для УМЗ сплавов 1570 и 7475 [13].
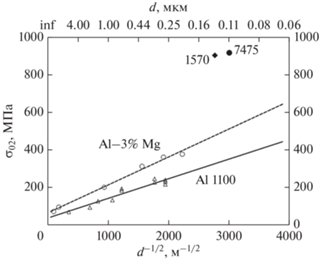
Рассмотрим более внимательно результаты экспериментов по получению высокопрочного состояния в технически чистом титане Grade 4, обработанном методами РКУП и ИПДК. Данный материал (состав, вес. % Fe – 0.5, O – 0.4, C – 0.08, N – 0.05, H2 – 0.015, Ti – основа) является весьма важным материалом для медицинских применений при изготовлении имплантатов. В то же время повышение его прочности важно для создания имплантатов улучшенной конструкции с повышенной остеоинтеграцией [18]. Детальное описание обработки технически чистого титана методами РКУП и ИПДК для формирования УМЗ-структуры опубликовано в предыдущих исследованиях [17–19]. Микроструктуру образцов после ИПД-обработки исследовали методами просвечивающей электронной микроскопии (ПЭМ), рентгеновской дифракции и сканирующей электронной микроскопии с использованием дифракции обратного рассеяния электронов (ДОЭ). Испытания на растяжение проводили на испытательной машине “Instron 5982” при комнатной температуре после ИПДК на малых образцах размерами 1 × 0.25 × 3 мм со скоростью деформации 3 × 10–4 с–1 [10, 13] и на стандартных цилиндрических образцах диаметром 3 мм и длиной 15 мм, полученных после РКУП обработки.
Исследования показывают, что обработка методами РКУП или ИПДК может обеспечить формирование различных типов границ зерен (ГЗ). После малого числа проходов при РКУП или первых оборотах при ИПДК в структуре появляется большое количество малоугловых границ. С увеличением числа проходов доля малоугловых границ уменьшается [5]. В частности, в технически чистом титане, подвергнутом ИПДК с пятью оборотами, доля большеугловых границ с углом разориентации более 15° составляет около 80% вместо 20–30% после одного оборота. При этом в титане, подвергнутом ИПДК, средний размер зерна составляет около 120 нм. Такая УМЗ-структура устойчива при нагреве до 300°С.
Интересным примером является исследование высокопрочного УМЗ Ti, полученного с помощью комбинированной ИПД обработки в форме длинномерных прутков, предназначенных для последующего изготовления медицинских имплантатов. Эта оригинальная технология изготовления прутков диаметром до 8 мм и длиной до 3 м из УМЗ Ti включает РКУП с последующей термомеханической обработкой (ТМО) [20].
Такая комбинированная ИПД-обработка приводит к формированию в прутках УМЗ-структуры, состоящей из равноосных зерен размером менее 150 нм (рис. 3), хотя присутствуют и вытянутые в продольном направлении зерна с субструктурой внутри. Измерения разориентации границ зерен методом ДОЭ-анализа показали, что доля большеугловых границ в данном состоянии составляет менее 40%. В то же время, варьируя режимы деформации и проводя ТМО при 300–350°С, было обнаружено значительное уменьшение субструктурных элементов и увеличение доли большеугловых границ до 80% при сохранении среднего размера зерна.
Рис. 3.
Микроструктура технически чистого титана Grade 4: (a) в исходном горячекатаном состоянии; (б, в) после РКУП + ТМО; а, б – оптическая, в – просвечивающая электронная микроскопия [20].
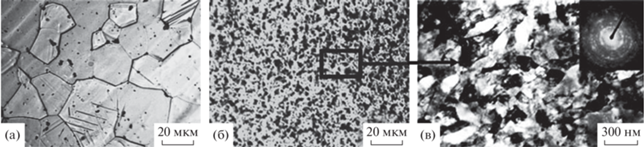
В последние годы технология получения прутков из нанотитана была усовершенствована, и в настоящее время оригинальная установка РКУП-Конформ используется при получении опытно-промышленных партий прутков нанотитана для изготовления медицинских имплантатов для стоматологии и челюстно-лицевой хирургии [18].
Недавно обработка титана Grade 4, включающая ИПДК на 10 оборотов и отжиги по разным режимам (табл. 1), была подробно исследована в работе [19]. В табл. 1 приведены структурные параметры титана после этих обработок.
Таблица 1.
Структурные параметры технически чистого титана Grade 4 после различных обработок
Состояние | Средний размер зерен, d, мкм | Общая плотность дислокаций, ρ, м–2 | Средний размер частиц Fe2Ti, r, нм | Объемная доля частиц Fe2Ti, f, % |
---|---|---|---|---|
Горячекатаный | 10 ± 2 | ≈2.4 × 1014 | 103 | 2–3 |
ИПДК | 0.12 ± 0.03 | ≈2.1 × 1015 | – | <1 |
ИПДК + 700°С | 5 ± 1 | ≈2.2 × 1014 | 35 ± 7 | 4–5 |
ИПДК + 700°С + ИПДК | 0.09 ± 0.03 | ≈1.6 × 1015 | – | <1 |
ИПДК + 700°С + ИПДК + 350°С | 0.12 ± 0.04 | ≈2.3 × 1014 | 18 ± 10 | 7–8 |
Также в табл. 2 приведены данные о механических свойствах титана после этих обработок. Из полученных данных следует, что формирование УМЗ-структуры в технически чистом титане методом ИПДК приводит к увеличению микротвердости до 353 ± 7 HV (табл. 2). Последующий отжиг при 700°C в течение 30 мин приводит к разупрочнению материала за счет развития процессов рекристаллизации и сопровождается снижением твердости до значений 266 ± 5 HV (ИПДК + 700). После последующей обработки двойной вклад в прочность от образовавшейся ω-фазы и полученной УМЗ-структуры обеспечивает еще большее повышение микротвердости до 423 ± 8 HV (ИПДК + 700 + ИПДК), а последующий отжиг при 350 °C в течение 30 мин для снятия напряжения в материале сохраняет достигнутые показатели микротвердости на весьма высоком уровне 433 ± 3 HV (ИПДК + 700 + ИПДК + 350). На рис. 4 представлены инженерные кривые зависимости напряжений течения от степени деформации при растяжении исследованных образцов. В исходном состоянии характер кривой типичен для материалов, полученных горячей прокаткой. После достижения предела текучести наблюдается постепенный рост напряжений до максимальных значений с последующим снижением, вызванным локализацией деформации. ИПД кручением существенно меняет характер кривой. Наблюдается уменьшение равномерной деформации, значительный рост параметров прочности и снижение пластичности. Высокотемпературный отжиг деформированного состояния приводит к развитию рекристаллизации и нивелированию эффекта упрочнения от формирования УМЗ-структуры и искажений кристаллической решетки. Повторное ИПДК приводит к резкому росту прочности материала, но значительной потере пластичности. Однако последующий отжиг при температуре 350°C для снятия напряжений обеспечивает увеличение пластичности с сохранением высокой прочности.
Таблица 2.
Механические свойства титана Grade 4 в различных структурных состояниях
Состояние | Микротвердость, HV | σ0.2, МПа | σUTS, МПа | ε, % |
---|---|---|---|---|
Горячекатаный | 237 ± 2 | 500 | 680 | 23.9 ± 1.4 |
ИПДК | 353 ± 7 | 1020 | 1170 | 8.9 ± 1.2 |
ИПДК + 700°С | 266 ± 5 | 600 | 720 | 31 ± 2 |
ИПДК + 700°С + ИПДК | 423 ± 8 | 1200 | 1340 | 0.9 ± 0.4 |
ИПДК + 700°С + ИПДК + 350°С | 433 ± 3 | 1340 | 1510 | 10 ± 2 |
АНАЛИЗ МЕХАНИЗМОВ УПРОЧНЕНИЯ
С целью установить основные механизмы упрочнения после комбинированной деформационно-термической обработки технически чистого титана Grade 4, а также для понимания природы его сверхпрочного состояния, рассмотрим вклады различных микроструктурных параметров в общую прочность материала. В согласии с [1, 6, 9, 21], для данной цели применим подход, который учитывает аддитивный вклад таких механизмов упрочнения, как зернограничный (σgb), дислокационный (σd), твердорастворный (σss) и дисперсионный (σor) в напряжение течения:
(2)
${{{{\sigma }}}_{{\text{y}}}} = {{{{\sigma }}}_{0}} + {{{{\sigma }}}_{{{\text{gb}}}}} + {{{{\sigma }}}_{{\text{d}}}} + {{{{\sigma }}}_{{{\text{ss}}}}} + {{{{\sigma }}}_{{{\text{or}}}}},$Зернограничное упрочнение (эффект Холла–Петча)
Зернограничное упрочение может быть рассчитано с помощью уравнения Холла–Петча (1) [1, 2, 21, 22]. В работах [6, 22] показано, что значение коэффициента Холла–Петча kHP для технически чистого титана может заметно снижаться при измельчении его структуры до УМЗ-состояния. Следуя данным из источника [22], использовали два значения kHP: 0.45 МПа м1/2 для крупнозернистого Ti и 0.12 МПа м1/2 для УМЗ-Ti.
Данные о средних размерах зерен титана Grade 4 в различных состояниях представлены в табл. 1. Рассчитанные данные σgb приведены в табл. 3. Для титана Grade 4 в исходном состоянии вклад зернограничного упрочнения составил около 140 МПа. Последующая обработка методом ИПДК с 10 оборотами приводит к значительному росту данного показателя до значений примерно 350 МПа за счет сильного измельчения зеренной структуры. Последующий отжиг при 700°С в течение 30 мин приводит к рекристаллизации структуры и соответственно к росту зерен, в следствии этого, зернограничное упрочнение снизилось до значения 200 МПа. Комбинированная обработка по режиму ИПДК + отжиг 700°С + + ИПДК позволила получить структуру с еще меньшим размером зерен, и как следствие, привела к увеличению величины зернограничного упрочнения до 400 МПа. Применение отжига при 350°С в течение 30 мин после комбинированной деформационно-термической обработки привело к небольшому укрупнению зеренной структуры и соответственно к изменению значения зернограничного упрочнения до примерно 340 МПа.
Таблица 3.
Расчетные вклады в предел текучести УМЗ титана Grade 4 различных механизмов упрочнения и экспериментальные данные о величинах предела текучести σy для всех исследованных состояний
Состояние | σy, МПа |
σy расч, МПа |
σ0, МПа |
σgb, МПа |
σd, МПа |
σss, МПа |
σor, МПа |
σSL, МПа |
---|---|---|---|---|---|---|---|---|
Горячекатаный | 500 | 480 | 80 | 140 | 150 | 110 | 0 | 0 |
ИПДК | 1020 | 980 | 350 | 440 | 0 | 0 | ||
ИПДК + 700°С | 600 | 600 | 200 | 140 | 70 | 0 | ||
ИПДК + 700°С + ИПДК | 1200 | 1170 | 400 | 380 | 0 | 200 | ||
ИПДК + 700°С + ИПДК + 350°С | 1340 | 830 | 340 | 150 | 150 | 0 |
Дислокационное упрочнение
Вклад дислокаций в упрочнение материала обычно описывают с помощью уравнения Тейлора [1, 2, 21]:
где для Ti [22] α1 = 0.2 – константа дислокационного упрочнения, b = 0.347 нм – вектор Бюргерса, G = 45.6 ГПа – модуль сдвига и М = 3 – фактор Тейлора, ρ – общая плотность дислокаций.Данные о плотности дислокаций титана Grade 4 в различных состояниях представлены в табл. 1. Результаты расчетов σd приведены в табл. 3. Для образцов в исходном состоянии рассчитанный вклад в прочность составляет 150 МПа. После обработки методом ИПДК наблюдается увеличение плотности дислокаций, рассчитанное по этим данным дислокационное упрочнение равно 440 МПа. Последующий отжиг при 700°С приводит к рекристаллизации структуры и соответственно к аннигиляции дефектов кристаллической решетки, рассчитанный вклад дислокационного упрочнения снижается до 140 МПа. После комбинированной деформационно-термической обработки по режиму: ИПДК + отжиг 700°С + ИПДК наблюдается достаточно высокая плотность дислокаций. В этом случае дислокационное упрочнение составляет 380 МПа. Последующий отжиг при 350°С приводит к интенсивной аннигиляции дефектов кристаллической решетки, в результате чего наблюдается значительное снижение плотности дислокаций. В данном состоянии упрочнение от дислокаций составляет 150 МПа.
Твердорастворное упрочнение
Твердорастворное упрочнение пропорционально квадратному корню из концентрации примесей O, N и C в Ti, и определяется с помощью следующего уравнения [22, 23]:
где c – кислородный эквивалент в атомных процентах, определяемый как O + 20N + $\frac{3}{4}$C.Долю O, N и C в составе титана Grade 4 в исходном состоянии определяли с помощью оптико-эмиссионного спектрометра. Рассчитанное по полученному кислородному эквиваленту σss представлено в табл. 3. В исходном состоянии твердорастворное упрочнение титана Grade 4 составило 110 МПа. Судя по работе [23], изменение концентрации примесных элементов в технически чистом титане после деформационно-термических обработок незначительно влияет на его упрочнение. В связи с этим твердорастворное упрочнение титана Grade 4 после деформационно-термических обработок можно принять приблизительно равным значению σss для данного материала в исходном состоянии.
Дисперсионное упрочнение
Дисперсионное упрочнение, обусловленное влиянием дисперсных частиц, обычно оценивают с помощью уравнения Орована, которое имеет следующий вид [21, 23]:
где r – радиус частиц и λ – среднее расстояние между центрами частиц, которое определяется следующим уравнением [21, 23]: где f – объемная доля частиц.Размеры наночастиц интерметаллидов и их объемная доля представлены в табл. 1. Наиболее крупные частицы наблюдаются в состоянии после ИПДК + отжиг 700°С. Расчеты по уравнению Орована демонстрируют, что данные частицы вносят дополнительный вклад в упрочнение титана после ИПДК + отжиг 700°С примерно равный 70 МПа. Наибольшая объемная доля наноразмерных частиц наблюдается в состоянии после ИПДК + отжиг 700°С + ИПДК + отжиг 350°С. Проведенные расчеты по уравнению Орована демонстрируют дополнительный вклад в упрочнение титана Grade 4 в данном состоянии в размере 150 МПа. В горячекатаном состоянии и после ИПДК дисперсионное упрочнение не учитывается в связи с малой долей выделившихся частиц и трудностью их выявления на снимках ПЭМ. В случае состояния после ИПДК + отжиг 700°С + ИПДК дополнительный вклад в упрочнение вносит метастабильная ω-фаза (σSL), которая, как показали исследования, формируется в результате данной ИПДК.
Рассчитанное упрочнение Grade 4 после ИПДК + отжиг 700°С + ИПДК, обусловленное дополнительным вкладом ω-фазы, составило 200 МПа.
В табл. 3 представлено сравнение рассчитанного упрочнения титана Grade 4 в различных состояниях с экспериментальными результатами механических испытаний. Как видно из представленных данных – вклад в прочность УМЗ-титана вносят разные механизмы упрочнения. Однако в состоянии с наибольшей прочностью (σy = = 1340 МПа) суммарный вклад от рассмотренных механизмов упрочнения заметно меньше этой величины. Это несоответствие указывает на то, что при деформации УМЗ-титана в данном состоянии действует еще и иной механизм упрочнения. Аналогичные выводы ранее были сделаны в работах сотрудников нашей лаборатории с коллегами и для других УМЗ-металлических материалов – Al сплавов [13, 14] и ряда сталей [15, 16]. Такой механизм упрочнения может быть связан с состоянием границ зерен в УМЗ-материалах, их неравновесной структурой, содержащей зернограничные дислокации, а также зернограничные сегрегации легирующих элементов [10, 23].
Недавние модельные расчеты, проведенные в [24], показывают, что образование сегрегаций примесей или легирующих элементов на границах зерен может значительно тормозить зарождение дислокаций на границах зерен, внося вклад в дополнительное упрочнение УМЗ-материалов. В то же время данные компьютерного моделирования [25, 26] и экспериментальных исследований [13, 14, 16] дают убедительные свидетельства образования зернограничных сегрегаций при формировании УМЗ-структур в металлических материалах с использованием методов ИПД, но их природа и морфология тесно связаны с режимами обработки.
ЗАКЛЮЧЕНИЕ
Итак, результаты недавних исследований показывают, что прочность УМЗ-материалов, полученных методами ИПД, традиционно значительно выше, чем может быть предсказана из соотношения Холла–Петча. Физическая природа данного явления связана с тем, что прочностные свойства УМЗ-материалов обусловлены не только наличием ультрамелких зерен, но и другими наноструктурными особенностями – образованием субзеренной дислокационной структуры, нанодвойниками, наноразмерными выделениями вторых фаз, а также структурой границ зерен – их неравновесностью и присутствием зернограничных сегрегаций примесей или легирующих элементов. Последний фактор является новым, но весьма важным, поскольку может вносить значительный вклад в прочность УМЗ-материалов. Более того, сегрегации на границах зерен могут влиять и на пластичность таких металлов и сплавов. В частности, недавно показано, что наличие зернограничных сегрегаций Zn в Al сплавах с ультрамелким зерном обеспечивает даже проявление сверхпластичности при пониженных температурах [25]. Можно ожидать, что в предстоящие годы исследование механизмов упрочнения и управление ими, используя методы ИПД, станет актуальным направлением в разработках металлических материалов, обладающих не только очень высокой прочностью, но и пластичностью и другими повышенными механическими свойствами.
Работа выполнена при финансовой поддержке гранта РНФ (проект № 22-19-00445) и Министерства науки и высшего образования Российской федерации в рамках проекта по соглашению № 075-15-2021-709, уникальный идентификатор проекта RF-2296.61321X0037 (методические рекомендации).
Список литературы
Штремель М.А. Прочность сплавов. Часть II. Деформация: Учебник для вузов. М.: МИСиС, 1997. 527 с.
Гольдштейн М.И., Литвинов В.С., Бронфин Б.М. Металлофизика высокопрочных сплавов. М.: Металлургия, 1986. 312 с.
Valiev R.Z., Islamgaliev R.K., Alexandrov I.V. Bulk nanostructured materials from severe plastic deformation // Prog. Mater Sci. 2000. V. 45. P. 103–189.
Валиев Р.З., Александров И.В. Объемные наноструктурные металлические материалы. М.: ИКЦ “Академкнига”, 2007. 398 с.
Valiev R.Z., Zhilyaev A.P., Langdon T.G. Bulk nanostructured materials: Fundamentals and applications. NJ: TMS-Wiley: Hoboken, 2014. 456 p. (Валиев Р.З., Жиляев А.П., Лэнгдон Т.Дж. Объемные наноструктурные материалы: фундаментальные основы и применения. СПб.: Эко-Вектор, 2017. 479 с.)
Козлов Э.В., Глезер А.М., Конева Н.А., Попова Н.А., Курзина И.А. Основы пластической деформации наноструктурных материалов. М.: ФИЗМАТЛИТ, 2016. 304 с.
Horita Z., Edalati K. Severe plastic deformation for nanostructure controls // Mater. Trans. 2020. V. 61. P. 2241–2247.
Edalati K., Bachmaier A., Beloshenko V.A., Beygelzimer Y., Blank V.D., Botta W.J., Bryła K., Čížek J., Divinski S., Enikeev N.A., Estrin Y., Faraji G., Figueiredo R.B., Fuji M., Furuta T., Grosdidier T., Gubicza J., Hohenwarter A., Horita Z., Huot J., Ikoma Y., Janeček M., Kawasaki M., Král P., Kuramoto S., Langdon T.G., Leiva D.R., Levitas V.I., Mazilkin A., Mito M., Miyamoto H., Nishizaki T., Pippan R., Popov V.V., Popova E.N., Purcek G., Renk O., Révész Á., Sauvage X., Sklenicka V., Skrotzki W., Straumal B.B., Suwas S., Toth L.S., Tsuji N., Valiev R.Z., Wilde G., Zehetbauer M.J., Zhu X. Nanomaterials by severe plastic deformation: review of historical developments and recent advances // Mater. Res. Lett. 2022. V. 10. P. 163–256.
Ovid’ko I.A., Valiev R.Z., Zhu Y.T. Review on superior strength and enhanced ductility of metallic nanomaterials // Prog. Mater Sci. 2018. V. 94. P. 462–540.
Valiev R.Z., Straumal B., Langdon T.G. Using Severe Plastic Deformation to Produce Nanostructured Materials with Superior Properties // Annu. Rev. Mater. Res. 2022. V. 52. P. 357–382.
Valiev R.Z., Enikeev N.A., Langdon T.G. Towards superstrength of nanostructured metals and alloys, produced by SPD // Kovove Mater. 2011. V. 49. P. 1–9.
Firstov S.A., Rogul T.G., Shut O.A. Transition from microstructures to nanostructures and ultimate hardening // Funct. Mater. 2009. V. 16. P. 364–373.
Valiev R.Z., Enikeev N.A., Murashkin M.Yu., Kazykhanov V.U., Sauvage X. On the origin of extremely high strength of ultrafine–grained Al alloys produced by severe plastic deformation // Scripta Mater. 2010. V. 63. P. 949–952.
Liddicoat P.V., Liao X.Z., Zhao Y., Zhu Y., Murashkin M.Y., Lavernia E.J., Valiev R.Z., Ringer S.P. Nanostructural hierarchy increases the strength of aluminium alloys // Nat. commun. 2010. V. 1. P. 63.
Karavaeva M.V., Kiseleva S.K., Ganeev A.V., Protasova E.O., Ganiev M.M., Simonova L.A., Valiev R.Z. Superior strength of carbon steel with an ultrafine-grained microstructure and its enhanced thermal stability // J. Mater. Sci. 2015. V. 50. P. 6730–6738.
Kim J.G., Enikeev N.A., Seol J.B., Abramova M.M., Karavaeva M.V., Valiev R.Z., Park C.G., Kim H.S. Superior strength and multiple strengthening mechanisms in nanocrystalline TWIP steel // Sci. Rep. 2018. V. 8. P. 11 200.
Semenova I., Salimgareeva G., Da Costa G., Lefebvre W., Valiev R. Enhanced strength and ductility of ultrafine-grained Ti processed by severe plastic deformation // Adv. Eng. Mater. 2010. V. 12. P. 803–807.
Valiev R.Z., Sabirov I., Zemtsova E.G., Parfenov E.V., Dluhoš L., Lowe T.C. Nanostructured commercially pure titanium for development of miniaturized biomedical implants / Titanium in Medical and Dental Applications. Woodhead Publishing. 2018. P. 393–417.
Rezyapova L.R., Valiev R.R., Sitdikov V.D., Valiev R.Z., Study of second phase precipitates in nanostructured commercially pure titanium // Lett. Mater. 2021. V. 11. P. 345–350.
Valiev R., Semenova I.P., Jakushina E., Latysh V.V., Rack H.J., Lowe T.C., Petruželka J., Dluhoš L., Hrušák D., Sochová J. Nanostructured SPD processed titanium for medical implants // Mater. Sci. Forum. – Trans Tech Publications Ltd. 2008. V. 584. P. 49–54.
Balasubramanian N., Langdon T.G. The strength–grain size relationship in ultrafine-grained metals // Metall. Mater. Trans. A. 2016. V. 47. P. 5827–5838.
Luo P., Hu Q., Wu X. Quantitatively analyzing strength contribution vs grain boundary scale relation in pure titanium subjected to severe plastic deformation // Metall. Mater. Trans. A. 2016. V. 47. P. 1922–1928.
Valiev R.Z. Superior strength in ultrafine-grained materials produced by SPD processing // Mater. Trans. 2014. V. 55. P. 13–18.
Bobylev S.V., Enikeev N.A., Sheinerman A.G., Valiev R.Z. Strength enhancement induced by grain boundary solute segregations in ultrafine-grained alloys // Int. J. Plast. 2019. V. 123. P. 133–144.
Chinh N.Q., Murashkin M.Y., Bobruk E.V., Lábár J.L., Gubicza J., Kovács Z., Maier-Kiener V., Valiev R.Z. Ultralow-temperature superplasticity and its novel mechanism in ultrafine-grained Al alloys // Mater. Res. Lett. 2021. V. 9. P. 475–482.
Петрик М.В., Кузнецов А.Р., Еникеев Н.А. Горностырев Ю.Н., Валиев Р.З. Особенности взаимодействия легирующих элементов с границами зерен и образование сегрегаций в сплавах Al–Mg и Al–Zn // ФММ. 2018. Т. 119. № 7. С. 647–652.
Дополнительные материалы отсутствуют.
Инструменты
Физика металлов и металловедение