Физика металлов и металловедение, 2022, T. 123, № 3, стр. 248-259
Влияние режимов селективного лазерного сплавления на структуру сплава ЮНДК
И. В. Шакиров a, *, А. С. Жуков a, **, С. Н. Перевислов b, А. В. Олисов c
a НИЦ “Курчатовский институт” – ЦНИИ КМ “Прометей”
191015 Санкт-Петербург, ул. Шпалерная, 49, Россия
b Институт химии силикатов им. И.В. Гребенщикова РАН (ИХС РАН)
199034 Санкт-Петербург, наб. Макарова, 2, Россия
c Национальный исследовательский Томский государственный университет
634050 Томск, пр. Ленина, 36, Россия
* E-mail: i.v.shakirov@yandex.ru
** E-mail: jouan@mail.ru
Поступила в редакцию 17.08.2021
После доработки 03.12.2021
Принята к публикации 06.12.2021
- EDN: QJPFAR
- DOI: 10.31857/S001532302203010X
Аннотация
Изучается влияние основных параметров процесса селективного лазерного сплавления (СЛС) на структуру и свойства постоянных магнитов из сплава ЮНДК. Были изготовлены серии образцов, сочетающие различные режимы селективного лазерного сплавления, использован сферический порошок сплава ЮНДК, полученный методом распыления расплава. Установлен подходящий диапазон технологических параметров, который позволяет изготавливать образцы постоянных магнитов с оптимальной структурой. Сделаны выводы по влиянию основных параметров процесса СЛС на морфологию поверхности наплавляемого сплава. Путем оптимизации режимов сканирования был достигнут эффект снижения растрескивания и, соответственно, получения высокого уровня физических и механических свойств образцов из сплава ЮНДК.
ВВЕДЕНИЕ
Магнитотвердые сплавы отличаются комплексом механических свойств, который делает их весьма трудно поддающимися механической обработке. Таким образом, создание постоянных магнитов сложной формы классическими методами – литьем и механообработкой, представляет собой технологическую проблему. Освоение новой технологии получения постоянных магнитов с помощью аддитивных методов (селективного лазерного сплавления (СЛС) и прямого лазерного выращивания (ПЛВ)) является чрезвычайно актуальной задачей [1].
Следует отметить, что одно из главных преимуществ аддитивных технологий (АТ) по сравнению с классическими технологиями заключается в возможности изготовления изделия практически любой геометрической формы, изготовление которых невозможно классическими способами.
Магнитотвердые материалы являются функциональными материалами, которые помимо удовлетворительных механических свойств должны обладать высоким уровнем магнитных гистерезисных свойств (коэрцитивной силой по индукции HСВ, остаточной магнитной индукцией Br, максимальным энергетическим произведением (ВН)max), которые более чувствительны к структуре, чем механические свойства. При изготовлении постоянного магнита методом литья необходимо строго контролировать температурные режимы, влияющие на процессы структурообразования. В противном случае изготовленный материал не будет обладать необходимыми магнитными свойствами. Для аддитивного метода производства также важен процесс структурообразования, который, в свою очередь, зависит от технологических режимов процесса СЛС [2, 3]. Таким образом, технология СЛС предоставляет возможность, изменяя параметры синтеза, оказывать влияние на структуру металла, что представляет большой интерес для изучения.
За последние годы интерес к аддитивному производству магнитных материалов значительно вырос. Существует ряд исследований с применением магнитных материалов различных систем [4, 5]. Большое внимание сосредоточено на попытках производства постоянных магнитов методом СЛС и подготовки материалов из редкоземельных металлов системы Nd–Fe–B [6–11].
В настоящее время магниты Nd–Fe–B показали наивысшее значение коэрцитивной силы (около 10 кЭ) среди аддитивных постоянных магнитов, полученных методом СЛС [12] и с использованием стереолитографии [13], за которыми следуют сплав ЮНДК (2 кЭ [14]) и Mn–Al (1 кЭ [15]). С помощью технологии ПЛВ также были напечатаны образцы систем Fe–Ni и Fe–Co с более низкой коэрцитивной силой (50 Э [16, 17]). На сегодняшний день существует очень мало исследований, посвященных сплавам ЮНДК в аддитивном производстве [4]. Имеются данные об изучении структуры образцов из сплава ЮНДК, полученных по технологии ПЛВ на установке Optomec MR-7 LENS [18, 14 ].
В последнее время наблюдается возрождение интереса к постоянным магнитам без использования редкоземельных металлов (РЗМ) для снижения стоимости и обхода барьеров в цепочке поставок важнейших компонентов, которые зависят от международных источников РЗМ и их оксидов (например, Dy, Sm, Nd) [19]. Однако типичные постоянные магниты на основе сплава ЮНДК обладают относительно низким максимальным энергетическим произведением, которое является мерой энергии, запасаемой магнитным материалом [20], по сравнению с существующими магнитами на основе РЗМ [21]. Исходя из этого, применение аддитивных технологий лазерного синтеза в совокупности с оптимизацией геометрической формы магнитов и возможностью создания улучшенной структуры дают основания полагать, что сплавы ЮНДК повысят свой потенциал в применении.
Цель данной работы – определение возможности изготовления постоянных магнитов из сплава ЮНДК методом СЛС, а также установление значений технологических параметров лазерного синтеза, при которых формируется структура, соответствующая приемлемому уровню магнитных свойств.
МЕТОДИКА
Экспериментальные образцы порошков сплава ЮНДК были созданы на установке распыления расплава HERMIGA 75/3IV. В полученном порошке крупная фракция удалена отсевом через сито с ячейкой 80 мкм. Морфология поверхности частиц порошка представлена на рис. 1а, 1б. Результаты измерений фракционного состава пробы порошка сплава ЮНДК на лазерном анализаторе Malvern Mastersizer 2000 составляют: d0.1 = = 7.06 мкм; d0.5 = 22.43 мкм; d0.9 = 60.26 мкм. Графически результаты лазерной дифрактометрии представлены на рис. 1в.
Рис. 1.
Порошок сплава ЮНДК: (а) общий вид частиц, (б) форма и поверхность отдельных частиц, (в) распределение частиц порошка по размерам.
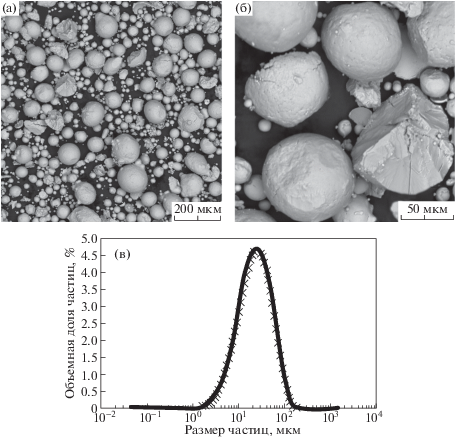
В табл. 1 представлен химический состав полученного порошка сплава ЮНДК.
Таблица 1.
Химический состав порошка
Элемент | Содержание, % (вес.) |
---|---|
Co | 23.9 |
Cr | – |
Ni | 13.4 |
Al | 6.9 |
Fe | 50.4 |
Cu | 3.6 |
C | 0.19 |
S | 0.02 |
O | 0.459 |
N | 0.16 |
Остальное | 0.9 |
С использованием установки “Russian SLM Factory” были изготовлены серии образцов, сочетающие различные режимы селективного лазерного сплавления. Основные характеристики установки: объем построения – диаметр 170 мм, высота 140 мм; мощность лазерного источника 200 Вт; длина волны лазера 1064 нм; диаметр пятна лазера 100 мкм; толщина слоя построения 20–75 мкм; точность позиционирования платформы построения 2–3 мкм; потребление инертного газа 5–15 л/мин.
Первоначально был создан экспериментальный образец с использованием полученных порошков сплава ЮНДК и применением стандартных режимов СЛС для нержавеющих сталей [22, 23] (мощность 195 Вт, скорость 800 мм/с, сканирование блоками шириной 5 мм).
Затем, с целью установить влияние различных режимов процесса СЛС на морфологию поверхности наплавляемого сплава, создавали образцы, которые представляли собой подготовленную стальную подложку (сталь 40), прошедшую дробеструйную обработку, с наплавленным на ее поверхность одинарным порошковым слоем сплава ЮНДК.
Наконец, с учетом детального изучения влияния параметров СЛС была разработана и применена оптимизированная стратегия сканирования лазерным лучом при получении партии экспериментальных образцов (куб со стороной 10 мм) для исследования магнитных свойств.
Исследования фазового состава экспериментальных образцов сплава ЮНДК выполняли на многофункциональном рентгеновском дифрактометре Rigaku Ultima IV. Дифракционный спектр образцов получен в рентгеновском излучении с использованием медного анода в геометрии Брэгга–Брентано c детектором D/teX Ultra, скорость перемещения которого составляла 2°/мин. Коллимацию первичного рентгеновского пучка осуществляли с помощью щелей размером 1/2 × 5 мм. Также использовали щели Соллера расходимостью 5° на первичном и на дифрагированном пучках. Режим работы рентгеновской трубки составлял 40 кВ/ 40 мA.
Морфология полученных дорожек сплава ЮНДК была исследована с использованием сканирующей электронной микроскопии (СЭМ). В работе представлены изображения поверхности образцов, полученные с помощью микроскопа Vega 3 Tescan. Получение ориентационной карты кристаллов посредством дифракции обратнорассеянных электронов (ДОЭ) осуществляли на микроскопе Tescan LYRA 3.
Экспериментальные образцы, полученные с применением оптимизированной стратегии сканирования, подвергали термомагнитной обработке (ТМО), выполненной по стандартным режимам. Закалка с температуры 1290 ± 10°С, скорость охлаждения 14.5°C/мин, затем 20 мин остывания на электромагните до температуры 400 ± 10°C. Режим отпуска: 610 ± 10°C – выдержка 3 ч, 590 ± 10°C – выдержка 8 ч, 570 ± 10°C – выдержка 15 ч, 550 ± 10°C – выдержка 20 ч, далее следовало остывание с печью до комнатной температуры.
Магнитные измерения для экспериментальных образцов магнитных материалов на основе сплава ЮНДК, полученных методом СЛС, проводили на гистерезисграфе MH-50. Образцы намагничивали в замкнутом потоке магнитного поля напряженностью до 2500 кА/м.
РЕЗУЛЬТАТЫ ЭКСПЕРИМЕНТА И ОБСУЖДЕНИЕ
Применение стандартных режимов СЛС для нержавеющих сталей при создании образцов из сплава ЮНДК привело к образованию развитой системы трещин с характерной анизотропией относительно оси Z. На рис. 2 представлено изображение структуры полученного образца из сплава ЮНДК в двух плоскостях (а – перпендикулярно оси Z, горизонтальная плоскость, б – вертикальная плоскость, г – ориентационная карта кристаллитов, вертикальная плоскость). Ориентационная карта отображает характерную для образцов СЛС кристаллическую структуру: различимы очертания кристаллизовавшихся ванн расплава, морфология зерен имеет выраженную анизотропию. Трещины преимущественно располагаются по границе кристаллитов. Для сравнения представлена структура сплава ЮНДК, полученного по литейной технологии (рис. 2в), данный образец обладает довольно высокой пористостью и включениями различного состава на границах зерен, что, по-видимому, связано с вытеснением тугоплавких дисперсных частиц фронтом кристаллизации.
Рис. 2.
Участки шлифа, образец СЛС горизонтальная (а) и вертикальная (б) плоскость; (в) литой сплав; (г) ориентационная ДОЭ-карта (образец СЛС, вертикальная плоскость).
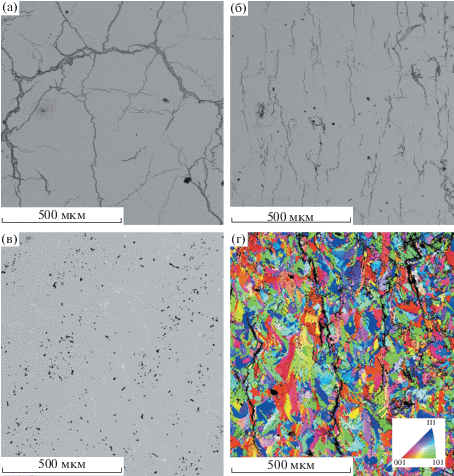
Применение стандартных режимов СЛС, которые хорошо себя показали при производстве образцов из аустенитных нержавеющих сталей, не позволяют получить образец из сплава ЮНДК с монолитной структурой без трещин.
На рис. 3 представлена рентгенограмма экспериментального образца, полученного методом СЛС из порошков сплава ЮНДК с применением стандартных режимов СЛС для нержавеющих сталей. Показано сравнение двух дифракционных спектров, полученных в продольном и поперечном направлении. Приведена штрих-диаграмма относительной интенсивности дифракционных максимумов. Различие в интенсивности пиков указывает на анизотропию. Для удобства восприятия каждая дифрактограмма сдвинута относительно предыдущей на 6000 имп., верхняя кривая находится в исходном положении. Обнаружены две фазы: одна с объемноцентрированной кубической решеткой, являющейся α-Fe (Im3m), другая – с примитивной кубической решеткой (Pm3m), образованной интерметаллидом NiAl. Это объясняется тем, что в процессе распада α‑твердого раствора на основе соединения NiAl, характеризующегося примитивной кубической решеткой (Pm3m), образуются две фазы, из которых первая представляет собой неупорядоченный твердый раствор на основе α-Fe с Im3m-решеткой, а вторая обогащена Ni и Al и упорядочена по типу CsCl (Pm3m). При термообработке без магнитного поля частицы α-Fe ориентируются длинными осями вдоль кристаллографических направлений типа 〈100〉. При термомагнитной обработке сплавов частицы α-Fe ориентируются вдоль направления [100], составляющего наименьший угол с направлением магнитного поля. В результате возникает индуцированная одноосная магнитная анизотропия.
Рис. 3.
Дифракционные спектры образца, полученного методом СЛС из сплава ЮНДК в продольном и поперечном сечении.
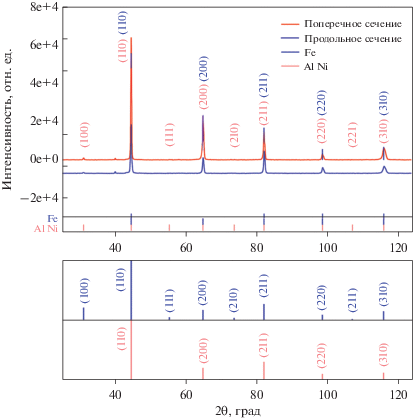
Ввиду проявления трещинообразования в процессе СЛС, необходимо детально изучить влияние режимов СЛС на формирование структуры образца из сплава ЮНДК. Для этого процесс сплавления был реализован на уровне единичных дорожек и областей сканирования с частичным перекрытием приблизительно 25 мкм.
На рис. 4 представлены изображения, полученные с помощью СЭМ, иллюстрирующие морфологию единичных дорожек, которые создавались при толщине порошкового слоя 20 мкм, мощности лазерного излучения 160, 170, 180 и 190 Вт, скорости сканирования: 500, 600, 700 и 800 мм/с.
Рис. 4.
Изображение морфологии поверхности наплавляемого сплава при различных значениях скорости сканирования и мощности лазерного излучения.
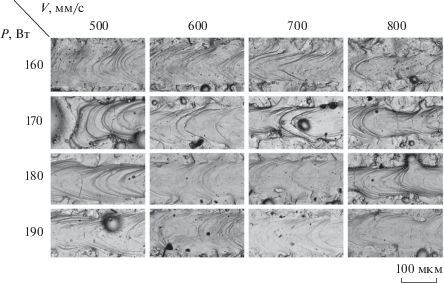
C увеличением скорости от 500 до 800 мм/с, при постоянной мощности, увеличиваются расстояния между наплывами на поверхности наплавленного сплава, увеличивается доля исходных нерасплавленных частиц порошка. Средняя ширина изолированной дорожки составляет порядка 130 мкм, это несколько превосходит диаметр пятна лазерного луча, который условно равен 100 мкм.
Понижение скорости сканирования приводит к появлению трещин в наплавленном металле. Увеличение мощности приводит к лучшему проплавлению порошкового слоя и металла основы. Так, при мощности 160 и 170 Вт происходит неполное проплавление порошкового слоя, расплавляются не все порошковые частицы на пути лазерного луча, при значениях мощности 180, 190 Вт происходит полное проплавление порошка, и вследствие более глубокой ванны расплава меняется морфология поверхности образца. Таким образом, наплавка формируется наилучшим образом при мощности излучения 190 Вт и скорости 800 мм/с.
Далее, с целью установить влияние толщины порошкового слоя на морфологию дорожек, были получены три отдельные дорожки с установленными ранее оптимальными значениями мощности – 190 Вт и скорости сканирования – 800 мм/с при различной толщине порошкового слоя: 20, 40 и 60 мкм (см. рис. 5).
Рис. 5.
Морфология дорожек с различной толщиной порошкового слоя: (а) 20, (б) 40, (в) 60 мкм. Скорость сканирования – 800 мм/с, мощность – 190 Вт.
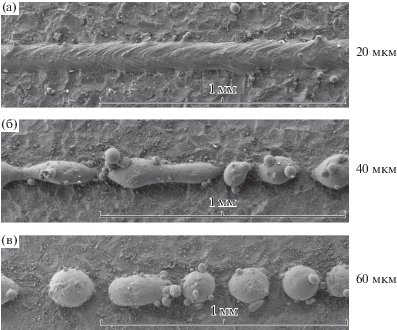
Полное проплавление единичных изолированных друг от друга дорожек происходит только при толщине слоя 20 мкм. С толщиной слоя 40 мкм и выше не происходит проплавления металла подложки, отсутствует формирование ванны расплава необходимой геометрии, капли расплавленного исследуемого сплава застывают на поверхности подложки. Однако при создании областей сканирования с частичным перекрытием дорожек в 25 мкм, при всех значениях мощности 160–190 Вт происходит полное проплавление с толщиной порошкового слоя до 40 мкм (рис. 6).
Рис. 6.
Морфология поверхности участков сплошного сканирования при толщине слоя 40 мкм, мощности 190 Вт и скорости: (а) 500, (б) 600, (в) 700, (г) 800 мм/с.
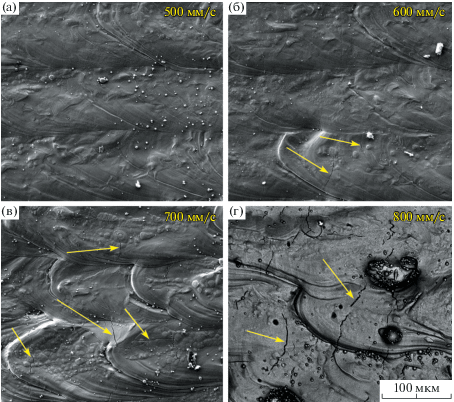
На поверхности металла при скорости сканирования 500 мм/с (рис. 6а) трещины практически отсутствуют. В отличие от отдельных дорожек, на участках сплошного сканирования с увеличением скорости сканирования усиливаются процессы трещинообразования, которые не проявляли себя при сплавлении отдельных дорожек. При сплошном сканировании участка порошка (один слой) картина распределения температурных полей приобретает более сложный характер, в сравнении с одной изолированной дорожкой. Таким образом, на основании приведенных экспериментальных данных уставлено различие в выборе оптимальных параметров СЛС (мощности излучения, скорости сканирования, толщины порошкового слоя) для единичной дорожки, области сканирования в один порошковый слой с частичным перекрытием и объемным образцом.
Неравномерное распределение температур в процессе СЛС, резкий градиент температур в ванне расплава и зоне термического влияния приводят к трещинообразованию. Наплавляемый металл и нагретый участок образца расширяются и вызывают в остальной части образца напряжения, которые приводят к образованию характерных трещин и их направленному росту в процессе создания образца слой за слоем. Сплав ЮНДК обладает значительной литейной усадкой, что дополнительно увеличивает внутренние напряжения, приводящие к растрескиванию. Таким образом, типичные подходы для подбора режимов селективного лазерного сплавления сплава ЮНДК не дают должного эффекта. Необходимо изучение влияния возникающих тепловых полей в процессе СЛС на микроструктуру сплава ЮНДК с помощью численного моделирования [24]. Для этого были проведены исследования по моделированию тепловых полей и установление зависимости между режимами СЛС и структурой создаваемого образца. Подробное изучение влияния тепловых полей последовательного и кольцевого сканирования на микроструктуру сплава ЮНДК изложено в работе [24]. Помимо мощности излучения, скорости сканирования и толщины порошкового слоя, на тепловое поле большое влияние оказывает стратегия сканирования в зависимости от сечения детали при сплавлении каждого слоя порошка в процессе печати детали. Таким образом, меняя стратегию сканирования, можно уменьшить остаточные напряжения в образце, приводящие к трещинообразованию.
Далее были получены образцы с применением оптимизированной стратегии сканирования, которая заключается в последовательном сканировании лазерным лучом начиная из центра по концентрическим квадратам (схематически изображено на рис. 7а, где представлен внешний вид образцов). В табл. 2 представлен список полученных образцов с указанием режимов СЛС и магнитных свойств. При изготовлении данной серии образцов мощность лазерного излучения варьировали от 110 до 190 Вт, скорость сканирования лазерным лучом от 500 до 800 мм/с, толщина порошкового слоя составляла 40 мкм. Полученные образцы подвергали ТМО. Дифракционные спектры образцов данной серии идентичны представленному выше спектру (см. рис. 3). Репрезентативная микроструктура образца представлена на рис. 7б, соответствует образцу № 5. Применение оптимизированной стратегии сканирования позволило значительно снизить количество дефектов в виде пор и трещин.
Рис. 7.
Образцы из сплава ЮНДК: а – внешний вид; б – изображение вертикального шлифа; в – изображение горизонтального шлифа после травления; г – ориентационная ДОЭ-карта, вертикальная плоскость.
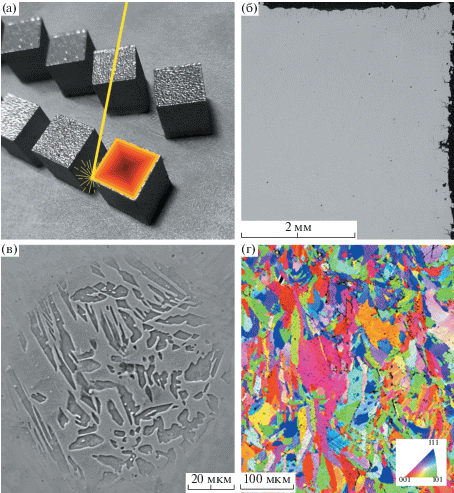
Таблица 2.
Образцы СЛС. Результаты магнитных измерений
№ | Мощность, Вт | Скорость, мм/с | Угол наклона 〈100〉, ° | Br, Тл | НСВ, кА/м | (ВН)max, кДж/м3 |
---|---|---|---|---|---|---|
1 | 190 | 500 | 20.8 | 0.657 | 24.3 | 21.2 |
2 | 190 | 550 | 16.7 | 0.788 | 32.9 | 26.7 |
3 | 190 | 600 | 11.9 | 0.816 | 35.3 | 29.4 |
4 | 190 | 650 | 12.3 | 0.989 | 36.2 | 33.2 |
5 | 190 | 700 | 9.3 | 1.095 | 38.7 | 36.0 |
6 | 190 | 800 | 14.8 | 1.011 | 38.1 | 35.1 |
7 | 170 | 800 | 10.2 | 0.993 | 37.4 | 34.9 |
8 | 150 | 800 | 22.5 | 0.817 | 27.2 | 23.9 |
9 | 130 | 800 | 32.5 | 0.708 | 25.3 | 22.4 |
10 | 110 | 800 | 30.4 | 0.612 | 17.0 | 15.5 |
Образцы полученной партии имеют схожую микроструктуру, выявляемую травлением (рис. 7в), которая представляет собой периодически расположенные вытянутые кристаллиты сильномагнитной фазы α1 (обогащенной железом и кобальтом), расположенных в слабомагнитной матрице α2 (обогащенной никелем и алюминием).
Процесс СЛС характеризуется направленным теплоотводом (в отрицательном направлении оси Z), обусловленным влиянием платформы и нижних слоев металла в процессе построения. Таким образом, процесс СЛС создает условия направленной кристаллизации, ориентационная ДОЭ-карта, иллюстрирующая характерную морфологию зерен, вытянутых вдоль оси Z, представлена на (рис. 7г).
Морфология зерен, по сравнению со структурой образца, полученного ранее без оптимизации стратегии сканирования (рис. 2г), отличается другим видом границ, что говорит об эффекте применения оптимизированной стратегии сканирования. Очертания кристаллизовавшихся ванн расплава не выявляются, зерна размером 50–100 мкм свободно вырастали через несколько печатных слоев, структура имеет более равновесный характер.
На рис. 8 представлена полюсная фигура (образец № 5), полученная таким образом, что направление Z полюсной фигуры совпадает с направлением оси Z образца.
Структурочувствительные свойства зависят от угла наклона кристаллографического направления 〈100〉 по отношению к геометрической оси образца. На основании полученного массива данных подсчитан усредненный угол наклона кристаллографического направления 〈100〉 по отношению к оси Z образцов № 1–9 (см. табл. 2). Наилучший уровень магнитных структурочувствительных свойств (остаточной индукции и максимального энергетического произведения) достигается при условии, что вытянутые зерна имеют кристаллографическое направление 〈100〉, близкое к геометрической оси Z образца, вдоль которого происходит намагничивание. Полученная зависимость (BH)max от угла наклона кристаллографического направления 〈100〉 от оси Z образца показана на рис. 9а. Характер зависимости показывает связь между уровнем магнитных свойств и характеристиками структуры. Большая погрешность связана с подготовкой металлографического шлифа и методом подсчета усредненного угла наклона кристаллографического направления 〈100〉 по отношению к оси Z образца.
Рис. 9.
Зависимость максимального энергетического произведения (BH)max от (а) угла наклона кристаллографического направления 〈100〉 относительно оси Z, (б) мощности излучения при скорости сканирования 800 мм/с, (в) скорости сканирования при мощности 190 Вт.
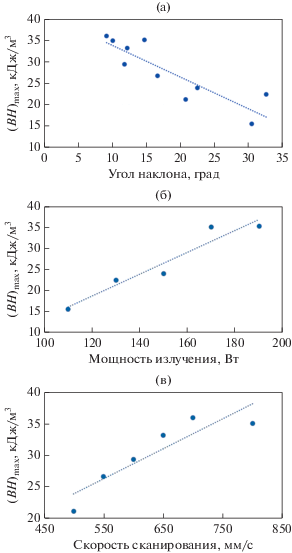
Представлены зависимости максимального энергетического произведения от мощности излучения (рис. 9б) и скорости сканирования (рис. 9в). При создании объемных образцов увеличение мощности излучения и скорости сканирования приводит к увеличению магнитных характеристик Br, HCB и (BH)max. Образец № 5 (табл. 2) характеризуется наилучшим уровнем магнитных свойств: Вr = 1.095 Тл, HСВ = 38.7 кА/м (486 Э); (ВH)max = 36.0 кДж/м3.
Характерная петля гистерезиса для данного образца показана на рис. 10.
Из представленных зависимостей можно видеть, что увеличение мощности излучения от 110 до 190 Вт (дальнейшее увеличение мощности ограничено техническими возможностями установки), при постоянной скорости сканирования 800 мм/с, как и увеличение скорости сканирования при постоянной мощности излучения 190 Вт способствует формированию направленной анизотропной структуры с минимальным углом отклонения кристаллографического направления 〈100〉 от оси Z образца, что позволяет получить хороший уровень магнитных свойств после ТМО. Данные зависимости были достигнуты путем оптимизации стратегии сканирования на основании численных методов.
ВЫВОДЫ
Проблема трещинообразования при создании магнитных материалов из сплава ЮНДК методом СЛС была исследована на примере образцов различной геометрии (единичной дорожки, области сканирования в один порошковый слой с частичным перекрытием и объемным образцом). Экспериментально показано, что поиск оптимальных параметров для получения образцов магнитных материалов из сплава ЮНДК заключается не только в выборе мощности излучения, скорости сканирования лазерным лучом, толщины порошкового слоя. Определяющее значение имеет выбор оптимальной стратегии сканирования с учетом распределения температурных полей.
Применение оптимизированной стратегии сканирования лазерным лучом в процессе СЛС позволило создать образец постоянного магнита с приемлемым уровнем магнитных свойств и отсутствием трещин в объеме образца.
Для полученных методом СЛС экспериментальных образцов из сплава ЮНДК максимальное значение магнитных характеристик: Вr = = 1.095 Тл, HСВ = 38.7 кА/м (486 Э); (ВH)max = = 36.0 кДж/м3 было достигнуто для используемой установки СЛС при значениях мощности 190 Вт, скорости сканирования 700 мм/с, толщине слоя 40 мкм и применении оптимизированной стратегии сканирования лазерным лучом.
Возможность корректировать стратегию сканирования лазерным лучом на основании численного моделирования в зависимости от геометрической формы создаваемого образца с целью управления температурными полями, создает предпосылки к улучшению магнитных свойств образцов из сплава ЮНДК и возможности создания магнитов сложной геометрической формы. Присущая методу СЛС направленная кристаллизация в направлении роста образца может быть выгодна использована с целью улучшения кристаллической структуры путем формирования направленной кристаллографической ориентации “легкого” намагничивания 〈100〉 в необходимом направлении в зависимости от геометрии образца и проведением ТМО с приложением магнитного поля в соответствующем направлении.
Экспериментальные исследования выполнены на оборудовании Центра коллективного пользования научным оборудованием “Состав, структура и свойства конструкционных и функциональных материалов” НИЦ “Курчатовский институт” – ЦНИИ КМ “Прометей” при финансовой поддержке государства в лице Министерства образования и науки Российской Федерации в рамках соглашения № 13.CKP.21.0014. Уникальный идентификатор: RF-2296.61321X0014.
Список литературы
Jaćimović J., Binda F., Herrmann L.G., Greuter F., Genta J., Calvo M., Tomše T., Simon R.A. Net shape 3D printed NdFeB permanent magnet // Adv. Eng. Mater. 2017. V. 19. P. 1700098. https://doi.org/10.1002/adem.201700098
Zhukov A.S., Barakhtin B.K., Bobyr V.V., Kuznetsov P.A., Shakirov I.V. The experience of magnets manufacturing from metal powder using a laser // J. Phys. Conference Series. 2021. V. 1791(1). P. 012122.
Bittner F., Thielsch J., Drosse W.G. Laser powder bed fusion of Nd–Fe–B permanent magnets // Progress in Additive Manufacturing. 2020. V. 5. P. 3–9. https://doi.org/10.1007/s40964-020-00117-7
Chaudhary V., Mantri S.A., Ramanujan R.V., Banerjee R., Additive manufacturing of magnetic materials // Progress in Mater. Sci. 2020. V. 114. P. 100688. ISSN 0079-6425, https://doi.org/10.1016/j.pmatsci.2020.100688
Périgo E.A., Jacimovic J., García Ferré F., Scherf L.M., Additive manufacturing of magnetic materials // Additive Manufacturing. 2019. V. 30. P. 100870. https://doi.org/10.1016/j.addma.2019.100870
Baldissera A.B., Pavez P., Wendhausen P.A.P., Ahrens C.H., Mascheroni J.M. Additive manufacturing of bonded Nd–Fe–B–effect of process parameters on magnetic properties // IEEE Trans Magn. 2017. V. 53. P. 1–4. https://doi.org/10.1109/TMAG.2017.2715722
Li L., Tirado A., Nlebedim I.C., Rios O., Post B., Kunc V., Lowden R.R., Lara-Curzio E., Fredette R., Ormerod J., Lograsso T.A., Paranthaman M.P. Big area additive manufacturing of high performance bonded NdFeB magnets // Sci. Reports. 2016. V. 6. Article number 36212.
Kolb T., Huber F., Akbulut B., Donocik C., Urban N., Maurer D., Franke J. Laser beam melting of NdFeB for the production of reare-earth magnets // Proceedings of the EDCP conference 2016. https://doi.org/10.1109/EDPC.2016.7851311
Huber C., Sepehri-Amin H., Goertler M., Groenefeld M., Teliban Iu., Hono K., Suess D. Coercivity enhancement of selective laser sintered NdFeB magnets by grain boundary infiltration // Acta Mater. 2019. V. 172. P. 66–71. https://doi.org/10.1016/j.actamat.2019.04.037
Goll D., Vogelgsang D., Pflanz U., Hohs D., Grubesa T., Schurr J., Bernthaler T., Kolb D., Riegel H., Schneider G. Refining the microstructure of Fe–Nd–B by selective laser melting // Phys. Status Solidi RRL. 2019. V. 13. P. 1800536. https://doi.org/10.1002/pssr.201800536
Urban N., Meyer A., Kreitlein S., Leicht F., Franke J. Efficient near net-shape production of high energy rare earth magnets by laser beam melting // Appl. Mechan. Mater. 2017. V. 871. P 137–144. https://doi.org/10.4028/www.scientific.net/AMM.871.137
Volegov A.S., Andreev S.V., Selezneva N.V., Ryzhikhin I.A., Kudrevatykh N.V., Mädler L., Okulov I.V. Additive manufacturing of heavy rare earth free high-coercivity permanent magnets // Acta Mater. 2020. V. 188. P. 733–739. https://doi.org/10.1016/j.actamat.2020.02.058
Huber C., Mitteramskogler G., Goertler M., Teliban Iu., Groenefeld M., Suess D. Additive Manufactured Polymer-Bonded Isotropic NdFeB Magnets by Stereolithography and Their Comparison to Fused Filament Fabricated and Selective Laser Sintered Magnets // Materials. 2020. V. 13(8). P. 1916. https://www.mdpi.com/1996-1944/13/8/1916.
White E., Rinko E., Prost T., Horn T., Ledford C., Rock C. and Anderson I., Processing of Alnico Magnets by Additive Manufacturing // Appl. Sci. 2019. V. 9(22). P. 4843. https://doi.org/10.3390/app9224843
Radulov I.A., Popov V.V., Koptyug A., Maccari F., Kovalevsky A., Essel S., Gassmann J., Skokov K.P., Bamberger M., Production of net-shape Mn-Al permanent magnets by electron beam melting // Additive Manufacturing. 2019. V. 30. P. 100787. https://doi.org/10.1016/j.addma.2019.100787
Nartu M.S.K.K.Y., Dasari S., Sharma A., Chaudhary V., Varahabhatla S.M., Mantri S.A., Ivanov E., Ramanujan R.V., Dahotre N.B., Banerjee R. Reducing coercivity by chemical ordering in additively manufactured soft magnetic Fe–Co (Hiperco) alloys // J. Alloys Compounds. 2021. V. 861. P. 157998. https://doi.org/10.1016/j.jallcom.2020.157998
Chaudhary V., Yadav N.M.S.K.K., Mantri S.A., Dasari S., Jagetia A., Ramanujan R.V., Banerjee R. Additive manufacturing of functionally graded Co–Fe and Ni–Fe magnetic materials // J. Alloys Compounds. 2020. V. 823. P. 153817. https://doi.org/10.1016/j.jallcom.2020.153817
White E.M.H., Kassen A.G., Simsek E., Tang W., Ott R.T., Anderson I.E. Net Shape Processing of Alnico Magnets by Additive Manufacturing // IEEE Trans. Magn. 2017. V. 53. № 11. P. 2101606.
Skomski R., Manchanda P., Kumar P., Balamurugan B., Kashyap A. and Sellmyer D.J. Predicting the Future of Permanent-Magnet Materials // IEEE Trans. Magn. 2013. V. 49. № 7. P. 3215–3220. https://doi.org/10.1109/TMAG.2013.2248139
Rottmann P.F., Polonsky A.T., Francis T., Emigh M.G., Krispin M., Rieger G., Echlin McL.P., Levi C.G., Pollock T.M. TriBeam tomography and microstructure evolution in additively manufactured Alnico magnets // Mater. Today. 2021. V. 49. P. 23–34. https://doi.org/10.1016/j.mattod.2021.05.003
Zhou Lin, Miller M.K., Ping Lu, Liqin Ke, Skomski R., Dillon H., Xing Q., Palasyuk A., McCartney M.R., Smith D.J., Constantinides S., McCallum R.W., Anderson I.E., Antropov V., Kramer M.J. Architecture and magnetism of alnico // Acta Mater. 2014. V. 74. P. 224–233. ISSN 1359-6454. https://doi.org/10.1016/j.actamat.2014.04.044
Kuznetsov P.A., Shakirov I.V., Zukov A.S., Bobyr’ V.V., Starytsin M.V. Effect of particle size distribution on the structure and mechanical properties in the process of laser powder bed fusion // J. Phys: Conference Series. 2021. V. 1758(1). P. 012021.
Bobyr V., Zhukov A., Shakirov I., Kuznetsov P. Selection of the selective laser melting modes – As the method of achieving an item’s complex shape with the specified physical and mechanical properties // Mater. Today: Proceedings. 2019. V. 19. P. 2129–2133.
Kuznetsov P., Shakirov I., Mozhayko A., Zhukov A., Bobyr V. Comparison of sequential and circular scanning thermal fields and their influence on microstructure of Alnico alloy produced by laser powder bed fusion // J. Physics: Conference Series. 2021. V. 1967. P. 012064.
Дополнительные материалы отсутствуют.
Инструменты
Физика металлов и металловедение