Физика металлов и металловедение, 2022, T. 123, № 5, стр. 547-553
Эволюция фазового состава и дюрометрических характеристик в жаропрочном сплаве титана Ti–6.4Al–3.5Zr–2.6Sn–1Nb–0.6Mo–0.2Si при старении
А. Г. Илларионов a, b, *, Д. В. Гадеев a, С. М. Илларионова a, С. Л. Демаков a
a ФГАОУ ВО Уральский федеральный университет имени первого Президента России Б.Н. Ельцина
620002 Екатеринбург, ул. Мира, 19, Россия
b Институт физики металлов им. М.Н. Михеева УрО РАН
620108 Екатеринбург, ул. С. Ковалевской, 18, Россия
* E-mail: a.g.illarionov@urfu.ru
Поступила в редакцию 18.10.2021
После доработки 24.01.2022
Принята к публикации 25.01.2022
- EDN: XIOXVQ
- DOI: 10.31857/S0015323022050047
Аннотация
Методами оптической, растровой, просвечивающей электронной микроскопии, полнопрофильного рентгеноструктурного фазового анализа, дюрометрии изучена эволюция фазового состава и твердости в жаропрочном титановом сплаве ВТ18У (Ti–6.4Al–3.5Zr–2.6Sn–1Nb–0.6Mo–0.2Si) в процессе старения в течение 1 ч в диапазоне температур 550–700°С. Дано объяснение особенностей изменения рассчитанных с использованием полнопрофильного анализа периодов (параметров) кристаллических решеток фаз (β, α', αII, αI и α2), образующихся при высокотемпературной обработке при 915°С и последующем старении сплава ВТ18У. Показано, что максимум твердости при 650°С у состаренного сплава ВТ18У связан с максимальным при этой температуре количеством α2-выделений, фиксируемым полнопрофильным анализом. В опытном сплаве на основе ВТ18У с повышенным содержанием циркония (7 мас. %) и олова (4 мас. %) установлены морфологические особенности выделения αII и α2-фаз и закономерности изменения легирования алюминием, цирконием, оловом фаз (β, αII, αI, α2), формирующихся в ходе старения при 700°С в течение 100 ч.
ВВЕДЕНИЕ
Титановый сплав ВТ18У (средний марочный состав, мас. % – Ti–6.8Al–4Zr–2.5Sn–1Nb–0.7Mo–0.15Si [1]) за счет комплексного многокомпонентного легирования (α-стабилизатором алюминием, нейтральными упрочнителями цирконием и оловом, вблизи предела растворимости в α-фазе тугоплавкими β-изоморфными стабилизаторами молибденом, ниобием, β-эвтектоидо-образующим стабилизатором кремнием) обладает высокими жаропрочными свойствами и используется для изготовления деталей компрессора высокого давления газотурбинных двигателей с рабочими температурами до 550–600°С [2]. В настоящее время ведутся исследования по созданию на базе ВТ18У композитов, упрочненных TiB, TiC, для повышения жаропрочных характеристик до температур работы 700°С [3, 4], по получению качественных сварных соединений [5], в том числе за счет микролегирования [6], по влиянию окисления [7] и текстуры [8] на его структуру и свойства.
Окончательный комплекс свойств сплава ВТ18У обычно формируется при двойном отжиге, включающем высокотемпературный нагрев сплава в двухфазную α + β-область в интервал 900–950°С, охлаждение на воздухе и низкотемпературную обработку в диапазоне 550–650°С [1, 2]. При низкотемпературной обработке в сплаве ВТ18У возможно образование не только частиц вторичной αII-фазы, но и интерметаллидных соединений, включая упорядоченную α2-фазу [9].
В монографии [10] отмечается, что в результате двойного отжига в сплаве IMI685, относящемся, как и ВТ18У к псевдо- α-сплавам, фиксируется минимальная ползучесть, если после высокотемпературной обработки скорость охлаждения в используемой среде составляет 1–10°/с. В работе [11] показано, что близкая к верхнему пределу этого диапазона скорость охлаждения (9–13°/с) реализуется при охлаждении в воду полуфабрикатов толщиной 25 мм из титанового сплава ВТ23 (Ti–4.7Al–2Mo–4.5V–1.1Cr–0.7Fe), имеющего сходное со сплавом ВТ18У суммарное содержание легирующих элементов (в пределах 13–15 мас. %).
В работе [12] установлено, что при охлаждении в воде сплава ВТ18У с температуры вблизи нижнего предела рекомендованного высокотемпературного нагрева 900°С наряду с первичной α-фазой (αΙ) фиксируется метастабильный β-твердый раствор и незначительное количество α2-фазы. При более высоких температурах нагрева (915°С и выше) вплоть до температуры полного полиморфного α + β → β-превращения (Тпп) высокотемпературный β-твердый раствор частично претерпевает мартенситное β → α'-превращение. Но в работе [12] не рассмотрена эволюция полученного при охлаждении в воде структурно-фазового состояния сплава ВТ18У при последующем нагреве в диапазоне температур низкотемпературной обработки, хотя это важно с научной и практической точки зрения. Такое исследование проведено в настоящей работе с использованием методики полнопрофильного рентгеноструктурного фазового анализа, нашедшей применение при изучении процессов распада метастабильных фаз в сплавах титана [13].
МАТЕРИАЛ И МЕТОДИКИ
Материалом для исследования служили полученные деформацией в β-области в промышленных условиях прутки диаметром 21 мм из псевдо-α-сплава ВТ18У и опытного сплава, отличающегося от ВТ18У повышенным содержанием циркония (7 мас. %) и олова (4 мас. %). Сплав ВТ18У, по данным микрорентгеноспектрального анализа (МРСА), имел следующий химический состав (в мас. %) – Ti–6.4Al–3.5Zr–2.6Sn–1Nb–0.6Mo–0.2Si. Сплав ВТ18У прошел двухступенчатую обработку: высокотемпературный нагрев в воздушной атмосфере до 915°С, выдержка 1 ч, охлаждение в воде, последующее старение при 550, 600, 650, 700°С в течение 1 ч, охлаждение на воздухе. Опытный сплав подвергали высокотемпературной обработке при 1150°С с последующим охлаждением на воздухе, затем старению при 700°С в течение 100 ч, охлаждение на воздухе.
Методами исследования служили оптическая микроскопия (ОМ), растровая (РЭМ) и просвечивающая (ПЭМ) электронная микроскопия, рентгеноструктурный фазовый анализ (РСФА), измерение твердости по Роквеллу. Металлографические исследования проводили на оптическом микроскопе Olimpus JX51. Для МРСА использовали микроскоп РЭМ “JSM 6490LV” с приставкой для микроанализа Oxford Inca. МРСА тонких фольг из опытного сплава осуществляли на ПЭМ “JEM-210”, оснащенным энергодисперсионным рентгеновским спектрометром. РСФА проводили на дифрактометре Bruker D8 Advance в CuKβ-излучении. Для полнопрофильного анализа дифрактограмм использовали программу Bruker Topas (версия 4.2). Измерение твердости по Роквеллу осуществляли при нагрузке 1500 H.
РЕЗУЛЬТАТЫ И ИХ ОБСУЖДЕНИЕ
Микроструктура псевдо-α-сплава ВТ18У после охлаждения в воде с температуры 915°С (рис. 1) характеризуется наличием полиэдрических со средним размером около 75 мкм β-превращенных зерен, имеющих α-оторочку. Внутри β-зерен фиксируются по несколько пакетов (от 2-х до 5-ти) первичных αΙ-пластин (рис. 1а). α Ι-пластины в пакетах разделены тонкими прослойками β-фазы, видимыми на рис. 1б как более светлые области.
В соответствии с данными РСФА (рис. 2), в структуре также присутствует α'-мартенсит и α2-фаза. Из этого следует, что β-прослойки частично претерпели превращение в α'-мартенсит, а α2-фаза могла образоваться в αΙ-пластинах, но в микроструктуре сплава α' и α2-фазы не выявляются при исследовании ОМ и РЭМ из-за высокой дисперсности.
Рис. 2.
Дифрактограмма (а) и данные ее полнопрофильного анализа (б) сплава ВТ18У после высокотемпературной обработки при 915°С: 1 – линия {002}α', 2 – линия {002}αI, 3 – линия {110}β, 4 – линия {101}αI, 5 – линия {101}α', 6 – линия {201}α2, 7 – линия {102}α2.
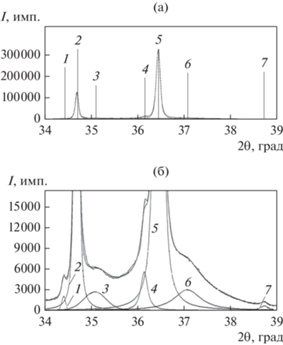
Фиксируемая пакетная структура αΙ-фазы унаследована от исходного полуфабриката, а образование α'-мартенсита связано с частичным растворением первичных α Ι-пластин в β-матрице в ходе выдержки при 915°С, сопровождающимся уменьшением количества β-стабилизаторов (Mo, Nb) в β-твердом растворе. Это снижает стабильность β‑матрицы к мартенситному β → α'-превращению при охлаждении в воде. Твердость сплава после высокотемпературной обработки составила 36 HRC.
Полнопрофильный анализ дифрактограммы (рис. 2б) позволил рассчитать периоды (параметры) решетки фиксируемых в ВТ18У структурных составляющих: aβ = 0.3264 нм, aαI = 0.2932 нм, сαI = 0.4684 нм, с/аαI = 1.598, aα' = 0.2970 нм, сα' = = 0.4744 нм, с/аα' = 1.597, aα2 = 0.5797 нм, сα2 = = 0.4643 нм, (с/а)α2 = 0.801. Сравнительный анализ периодов (параметров) решеток фаз αI и α', имеющих однотипную ГПУ-решетку, показал, что у α'-мартенсита периоды a и c выше, а параметр c/a ниже, чем у αI-фазы. Это связано с тем, что α'-мартенсит, образующийся при охлаждении по бездиффузионному механизму из β-матрицы, имеет состав, близкий к β-твердому раствору, который при нагреве в двухфазную α + β-область содержит, исходя из диаграмм состояния титана с легирующими элементами [14], большее количество β-стабилизаторов (Mo, Nb, Si), нейтральных упрочнителей (Zr, Sn) и меньшее – α-стабилизатора (Al), чем αI-фаза. При этом радиус атомов Sn (162 пм), Zr (160.25 пм), больше, а атомов Mo (136.26 пм), Nb (142.9 пм), Si (115.3 пм), Al (143.17 пм) меньше, чем размер атома титана (146.15 пм) [15, 16]. Учитывая небольшое содержание Mo, Nb, Si в сплаве ВТ18У, это способствует получению более высоких периодов решетки а, с и, согласно данным монографии [17], более низкого параметра c/a у α'-мартенсита.
Дифрактограммы, полученные с состаренного при различных температурах сплава ВТ18У, приведены на рис. 3. Повышение температуры старения от 550 до 700°С способствует изменению интенсивности и положения дифракционных линий от фаз, зафиксированных после высокотемпературной обработки при 915°С, а также появлению вместо линий α'-мартенсита линий вторичной αII-фазы (рис. 3). Это указывает на развитие в сплаве ВТ18У процессов распада неравновесных фаз.
Рис. 3.
Участки дифрактограмм с данными полнопрофильного анализа сплава ВТ18У, состаренного при 550 (а); 600 (б); 650 (в); 700°С (г): 1 – линия {110}β, 2 – линия {101}αI, 3 – линия {101}αII, 4 – линия {201}α2, 5 – линия {102}α2.
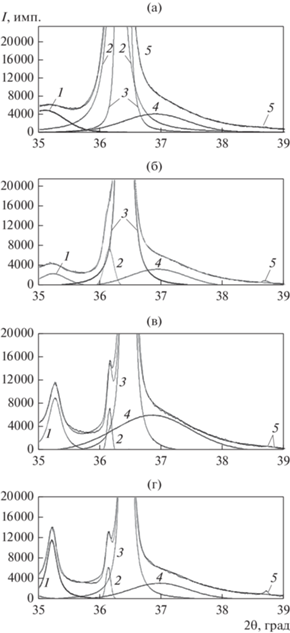
Изменение с температурой старения периода решетки β-фазы и параметра c/a αI, αII, α2-фаз, дано на рис. 4.
Рис. 4.
Зависимость периода кристаллической решетки β-фазы aβ (а), параметров с/а αI-фазы (пунктирная ли- ния), αII-фазы (штрихпунктирная линия) и 2*(с/а) α2- фазы (сплошная линия) (б) от температуры старения сплава ВТ18У.
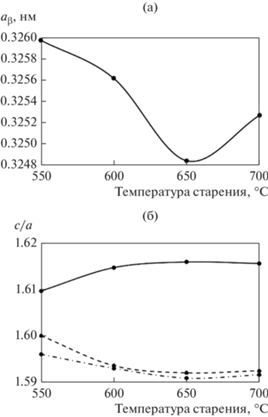
Параметр c/a служит индикатором уровня легирования указанных фаз [17]. Следует отметить, что у α2-фазы с упорядоченной ГПУ решеткой период а вдвое больше, чем период а у α-фазы с неупорядоченной ГПУ решеткой. Поэтому для удобства сравнительного анализа изменения параметра c/a фиксируемых αI, αII, α2-фаз на рис. 4б для α2-фазы приведены значения параметра 2*(c/a). Из рис. 4б видно, что с увеличением температуры старения происходит “зеркальное” изменение параметров c/a αI-фазы и 2*(c/a) α2-фазы: при снижении параметра c/a αI-фазы увеличивается параметр 2*(c/a) α2-фазы и наоборот.
Учитывая это и более высокий, чем у α'-мартенсита, параметр c/a αI-фазы, можно заключить, что в ходе старения из αI-фазы происходит выделение α2-фазы. Максимальное ее количество образуется при 650°С, исходя из среднего относительного изменения интенсивности линий α2 фазы на дифрактограммах (рис. 5), рассчитанного по данным полнопрофильного анализа (рис. 3). Как известно [2], α2-фаза представляет собой интерметаллид на основе алюминида титана Ti3Al, ее выделение в ходе старения приводит к обеднению αI-фазы по алюминию, а, в соответствии с данными из [16], это способствует снижению параметра c/a αI- фазы. И наоборот, повышение содержания алюминия в α2-фазе при старении способствует росту этого параметра.
Рис. 5.
Изменение с температурой старения по данным полнопрофильного анализа дифрактограмм среднего значения суммы относительной интенсивности линий {201}α2 и {102}α2, нормированных к интенсивности этих линий при температуре старения 550°С.
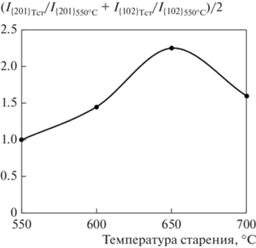
Уменьшение интенсивности линий α2-фазы при повышении температуры старения с 650 до 700°С (рис. 5), по нашему мнению, связано с близостью температуры 700°С к температурной границе существования этой фазы, которая, согласно данным работы [9], в сплаве ВТ18У лежит в районе 750°С. В целом можно отметить, что приведенный параметр 2*(c/a) α2-фазы выше, чем параметр c/a αI-фазы, очевидно, из-за более высокого содержания в α2-фазе алюминия, который способствует росту c/a [17].
Период решетки β-фазы меняется через минимум при 650°С. В работе [9] было показано, что минимальный инкубационный период распада β‑фазы с образованием α-фазы в жаропрочных титановых сплавах типа ВТ18У соответствует именно 650°С. αII-фаза выделяется в ходе старения из метастабильных β-фазы и α'-мартенсита с формированием смеси из αII и вновь образованной β-фазы. Образование αII-фазы, согласно [17], сопровождается обогащением β-твердого раствора β-стабилизаторами, в нашем случае молибденом, ниобием, кремнием, которые в β-фазе имеют атомный радиус сопоставимый (ниобий) и меньший (молибден, кремний) чем расчетный атомный радиус β-титана (142.11пм [18]). Это приводит, в целом, к снижению при старении по сравнению с высокотемпературной обработкой (аβ = 0.3264 нм) периода решетки β-фазы (рис. 4а).
Увеличение периода решетки β-фазы при повышении температуры старения с 650 до 700°С связано с ростом объемной доли присутствующего β-твердого раствора в сплаве, и, соответственно, снижения относительного содержания β-стабилизаторов в нем. Рост объемной доли β-фазы в структуре в данном случае вытекает из повышения интенсивности линий β-фазы на дифрактограммах, в частности, расчет по данным полнопрофильного анализа (рис. 3в, 3г) показал, что интенсивность линии {110}β увеличивается в 1.25 раза.
Рост параметра c/a αII-фазы при повышении температуры старения с 650 до 700°С связан с увеличением содержания в ней α-стабилизатора алюминия, нейтральных упрочнителей олова и циркония и снижением содержания β-стабилизаторов. Последнее происходит за счет их более активного перераспределения с формируемым при распаде β-твердым раствором в результате увеличения диффузионной подвижности легирующих элементов с ростом температуры старения.
Необходимо отметить, что параметр c/a αII-фазы при всех температурах старения ниже параметра c/a αI-фазы (рис. 4б). Это свидетельствует о различии химического состава формирующихся в ходе старения αI и αII-фаз. Как будет показано ниже на примере длительно состаренного опытного сплава (табл. 1), αII-фаза по сравнению с αI фазой обеднена по α-стабилизатору алюминию и нейтральному упрочнителю цирконию, обогащена по нейтральному упрочнителю олову. По данным [16] это создает условия получения более низкого параметра c/a у αII-фазы по сравнению с αI.
Таблица 1.
Содержание Al, Zr, Sn в структурных составляющих состаренного опытного сплава
Структурная составляющая | Содержание элемента, мас. % | ||
---|---|---|---|
Al | Zr | Sn | |
β | 4.1 | 7.1 | 4.3 |
αII | 6.0 | 6.4 | 4.8 |
αI | 6.6 | 6.6 | 3.3 |
α2 | 9.1 | 7.9 | 6.3 |
Изменение твердости сплава ВТ18У в состаренном состоянии показано на рис. 6. Полученная зависимость хорошо коррелирует с количеством упрочняющей упорядоченной α2-фазы в сплаве после старения, которое качественно можно оценить по отношению интенсивности ее линий на дифрактограммах (рис. 5). Максимум количества α2-фазы в ходе старения при температуре 650°С способствует получению и максимума твердости.
Дополнительный вклад в упрочнение возможен за счет выделения вторичной αII-фазы, но он гораздо менее существенный по двум причинам. Во-первых, из-за малой объемной доли в структуре метастабильных фаз – β, α' (суммарно менее 10% – [12]), из которых она выделяется, по сравнению с первичной αI-фазой (около 90%), из которой образуется α2-фаза. Во-вторых, из-за различия морфологии образующихся при старении αII и α2-фаз, как показано ниже на опытном сплаве (рис. 7).
Рис. 7.
Структура состаренного при 700°С в течение 100 ч опытного сплава: а – светлое поле, б – темное поле в рефлексе [220]β, в – темное поле в рефлексе [101]α2.
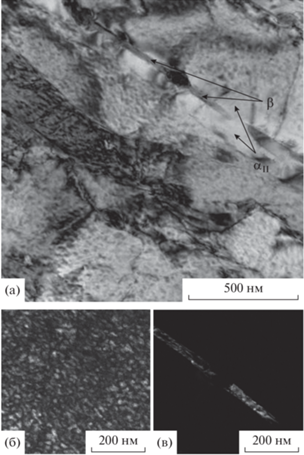
Экспериментальное подтверждение различия в морфологии и химическом составе фаз, образующихся при старении в сплавах типа ВТ18У, проведено на опытном сплаве с повышенным содержанием циркония (до 7 мас. %) и олова (до 4 мас. %), состаренном при 700°С в течение 100 ч. Использование опытного сплава вместо ВТ18У и увеличение времени старения с 1 до 100 часов обусловлено необходимостью получить достоверные данные о перераспределении легирующих элементов в различных структурных составляющих в ходе старения. Во-первых, опытный сплав более легирован нейтральными упрочнителями (Zr, Sn) по сравнению с промышленным сплавом ВТ18У, что, исходя из данных литературы [2], способствует образованию большего количества α2-фазы при старении без существенного роста Тпп. Во-вторых, значительное увеличение времени выдержки при максимальной из использованных в работе температуре старения 700°С обеспечивает получение выделений необходимого размера, достаточного для достоверного определения в них химического состава при ПЭМ исследовании.
Структура состаренного при 700°С в течение 100 ч опытного сплава (рис. 7) состоит из крупных пластин αI-фазы, имеющих относительно невысокую плотность дислокаций (рис. 7а), разделенных тонкими β-прослойками (рис. 7б), к которым прилегают области типа “пластин” αII‑фаз (рис. 7а), образующиеся при старении, очевидно, за счет движения межфазной β/αI-границы.
Темпопольный анализ показал, что в αI-пластинах при старении происходит равномерное выделение дисперсных частиц α2-фазы (рис. 7в). αII-пластины свободны от α2 -выделений. Т.е., в состаренном состоянии опытный сплав состоит из упрочненных α2-фазой αI-пластин и относительно мягких прослоек из смеси β + αII-фаз.
Различия в морфологии выделяющихся при старении α2, αII-фаз в опытном сплаве согласуются с приведенными выше данными об определяющей роли α2-фазы, а не αII в упрочнении при старении промышленного сплава ВТ18У.
Данные локального МРСА, полученные при ПЭМ исследовании, по содержанию основных легирующих элементов (Al, Zr, Sn) в структурных составляющих, фиксируемых в опытном сплаве после старения, приведены в табл. 1.
Представленные в таблице результаты хорошо согласуются с данными литературы, использованными в первой части работы при анализе влияния химического состава образующихся в ходе старения фаз на изменение параметров их кристаллических решеток в промышленном сплаве ВТ18У. Необходимо еще обратить внимание на более высокое содержание циркония и олова в упорядоченной α2-фазе по сравнению с β-твердым раствором, что, в целом, не характерно для неупорядоченных αII и αI-фаз (табл. 1). Последнее, очевидно, связано с повышением стабильности α2-фазы при введении в нее Zr, Sn [2].
ЗАКЛЮЧЕНИЕ
Исходя из выполненных исследований, получены следующие результаты:
РСФА, проводимый в CuKβ-излучении в сочетании с полнопрофильным анализом линий, позволяет после старения сплава ВТ18У надежно разделить накладывающиеся линии αI, αII, α2-фаз.
Дано объяснение особенностей изменения рассчитанных периодов (параметров) кристаллических решеток фаз (β, α', αII и α2), образующихся при высокотемпературной обработке и последующем старении в промышленном сплаве ВТ18У.
Показано, что максимум твердости при 650°С состаренного промышленного сплава ВТ18У связан с наибольшим фиксируемым количеством α2-выделений при этой температуре старения.
На опытном сплаве на основе ВТ18У с повышенным содержанием циркония (7 мас. %) и олова (4 мас. %) установлены морфологические особенности выделения α2- и αII-фаз и характер перераспределения легирующих элементов (алюминия, циркония, олова) в фазовых структурных составляющих (β, αII, αI, α2), формирующихся в ходе старения при 700°С в течение 100 ч.
Работа выполнена в рамках Госзадания Минобрнауки РФ УрФУ № 0836-2020-0020.
Список литературы
Moiseev V. Titanium alloys russian aircraft and aerospace applications. CRC Press Taylor & Francis Group, 2006. 214 p.
Ильин А.А., Колачев Б.А., Полькин И.С. Титановые сплавы. Состав, структура, свойства. Справочник. М.: ВИЛС–МАТИ, 2009. 520 с.
Гайсин Р.А., Имаев В.М., Имаев Р.М. Микроструктура и механические свойства композита псевдо α‑титановый сплав/TiB, полученного in situ с помощью литья и подвергнутого деформационной и термической обработке // ФММ. 2018. Т. 119. № 9. С. 961−970.
Imayev V.M., Gaisin R.A., Imayev R.M. Microstructure and mechanical properties of near α titanium alloy based composites prepared in situ by casting and subjected to multiple hot forging // J. Alloys Compd. 2018. V. 762. P. 555−564.
Панин В.Е., Панин С.В., Почивалов Ю.И., Смирнова А.С., Еремин А.В. Структурно-масштабные уровни пластической деформации и разрушения сварных соединений высокопрочных титановых сплавов // Физическая мезомеханика. 2018. Т. 21. № 4. С. 33−44. [Panin V.E., Panin S.V., Pochivalov Y.I., Smirnova A.S., Eremin A.V. Structural scale levels of plastic deformation and fracture of high-strength titanium alloy welds // Phys. Mesomech. 2018. V. 21. № 5. P. 464−474].
Илларионов А.Г., Попов А.А., Илларионова С.М., Гадеев Д.В., Елкина О.А. Влияние микродобавок хрома, гафния и иттрия на структуру и свойства жаропрочного титанового сплава ВТ18У // Diagnostics, Resource and Mechanics of Materials and Structures. 2017. № 3. С.15−22.
Калиенко М.С., Ледер М.О., Волков А.В., Желнина А.В., Панфилов П.Е. Исследование деформационного поведения титанового сплава ВТ18у в окисленном состоянии // Деформация и разрушение материалов. 2019. № 9. С. 36−41. [Kalienko M.S., Leder M.O., Volkov A.V., Zhelnina A.V., Panfilov P.E. Deformation behavior of a VT18U titanium alloy in the oxidized state // Russian Metallurgy (Metally) 2020. №4. P. 325−329.]
Исаенкова М.Г., Крымская О.А., Бабич Я.А., Медведев П.Н. Влияние кристаллографической текстуры α-фазы на анизотропию свойств листов из псевдо-α- и (α + β)-сплавов титана // Деформация и разрушение материалов. 2020. № 7. С. 20−25. [Isaenkova M.G., Krymskaya O.A., Babich Y.A., Medvedev P.N. Effect of the crystallographic texture in the α phase on the anisotropy of the properties of pseudo-α and (α + β) titanium alloy sheets // Russian Metallurgy (Metally) 2021. № 4. P. 430−436.]
Попов А.А., Попова М.А. Изотермические диаграммы выделения силицидных и алюминидных фаз в жаропрочных титановых сплавах // МиТОМ. 2016. № 11. С. 23−28. [Popov A.A., Popova M.A. Isothermal diagrams of precipitation of silicide and aluminide phases in refractory titanium alloys // Metal Science and Heat Treatment, 2017. V. 58. № 11–12. P. 662−666.]
Polmear I.J. Light alloys from traditional alloys to nanocrystals. Elsevier, 2006. 436 p.
Федулов В.Н. Прогнозирование эффективности термического упрочнения титановых сплавов // Литье и металлургия. 2006. № 1. С. 130−135.
Гадеев Д.В., Илларионов А.Г., Демаков С.Л. Формирование структуры, фазового состава и свойств в жаропрочном титановом сплаве при закалке // МиТОМ. 2015. № 8. С. 17−22. [Gadeev D.V., Illarionov A.G., Demakov S.L. Formation of structure, phase composition and properties in refractory titanium alloy under quenching // Metal Sci. Heat Treatment. 2015. V. 57. № 7–8. P. 463−468.]
Желнина А.В., Калиенко М.С., Илларионов А.Г., Щетников Н.В. Трансформация структуры, параметров фаз при старении сплава титана Ti–10V–2Fe–3Al и их связь упрочнением // ФММ. 2020. Т. 121. № 12. С. 1324−1330.
Phase diagrams of binary titanium alloys (Monograph series on alloy phase diagrams) / By ed. Joanne L. Murray. ASM International, 1987. 345 p.
Miracle D.B., Senkov O.N. A critical review of high entropy alloys and related concepts // Acta Mat. 2017. V. 122. P. 448−511.
Illarionov A.G., Vodolazskiy F.V., Barannikova N.A., Kosmatskiy Ya.I., Khudorozhkova Yu.V. Influence of phase composition on thermal expansion of Ti–0.4Al, Ti–2.2Al–2.5Zr and Ti–3Al–2.5V alloys // J. Alloys Compd. 2020. V. 857. P. 158049.
Цвиккер У. Титан и его сплавы. М.: Мир.1979. 512 с.
Khrunyk Y.Y., Ehnert S., Grib S.V., Illarionov A.G., Stepanov S.I., Popov A.A., Ryzhkov M.A., Belikov S.V., Xu Z., Rupp F., Nüssler A.K. Synthesis and characterization of a novel biocompatible alloy, Ti–Nb–Zr–Ta–Sn // Int. J. Mol. Sci. 2021. V. 22. P. 10611. https://doi.org/10.3390/ijms221910611
Дополнительные материалы отсутствуют.
Инструменты
Физика металлов и металловедение