Физика металлов и металловедение, 2023, T. 124, № 2, стр. 226-232
Изменение микроструктуры и фазового состава 3D-напечатанного сплава Ti–6Al–4V при механическом нагружении
А. В. Панин a, b, *, М. С. Казаченок a, Л. А. Казанцева a, c, О. Б. Перевалова a, С. А. Мартынов a
a Институт физики прочности и материаловедения СО РАН
634055 Томск, просп. Академический, 2/4, Россия
b Национальный исследовательский Томский политехнический университет
634050 Томск, просп. Ленина, 30, Россия
c Томский государственный архитектурно-строительный университет
634003 Томск, пл. Соляная, 2, Россия
* E-mail: pav@ispms.ru
Поступила в редакцию 16.06.2022
После доработки 10.11.2022
Принята к публикации 24.11.2022
- EDN: HJOOWU
- DOI: 10.31857/S0015323022600691
Аннотация
Представлены результаты in situ исследований эволюции микроструктуры и фазового состава 3D‑напечатанных образцов Ti–6Al–4V при растяжении в колонне просвечивающего электронного микроскопа. Показано, что микроструктура образцов Ti–6Al–4V, полученных методом электронно-лучевой проволочной аддитивной технологии, состоит из столбчатых первичных β-зерен, внутри которых располагаются рейки α/α'-Ti, разделенные прослойками остаточной β-фазы и собранные в пакеты. Характерной особенностью 3D-напечатанных образцов Ti–6Al–4V является концентрационная неоднородность легирующих элементов вследствие частичного распада мартенситной α'-фазы. При одноосном растяжении имеет место переориентация кристаллической решетки α/α'-Ti вблизи межфазных границ. В переориентированных областях решетки α/α'-Ti, в местах, обогащенных ванадием, могут развиваться индуцированные деформацией α' → α"-превращения.
ВВЕДЕНИЕ
В настоящее время в научно-технической литературе уделяется повышенное внимание исследованию и разработке аддитивных технологий получения деталей из титановых сплавов для сложных узлов аэрокосмической, транспортной и оборонной техники [1]. При этом микроструктура 3D-напечатанных титановых изделий существенно отличается от микроструктуры аналогичных изделий, изготовленных методами литья и штамповки [2]. В частности, микроструктура 3D-напечатанного титанового сплава Ti–6Al–4V может состоять из стабильных α- и β-фаз, а также метастабильных α'- и α"-мартенситных фаз [3–5]. Стабильность микроструктуры и объемная доля вторых фаз определяются распределением легирующих элементов в процессе высокоскоростного охлаждения ванны расплава и многократных циклов нагрева–охлаждения при нанесении последующих слоев. Соответственно перед разработчиками методов 3D-печати стоит актуальная задача детально исследовать неравновесную структуру 3D-напечатанных материалов, а также выяснить закономерности ее эволюции при различных условиях нагружения.
Индуцированные деформацией фазовые превращения наиболее подробно изучены в метастабильных β-титановых сплавах, пластическая деформация которых осуществляется не только путем дислокационного скольжения и двойникования, но и путем развития мартенситных превращений [6]. Показано, что концентрационная неоднородность β-стабилизаторов в α- и β-фазах являются причиной образования мартенситной α"-фазы в титановых сплавах при механическом нагружении. Например, при одноосном растяжении титанового сплава Ti–10V–2Fe–3Al уже при степени деформации ~3%, соответствующей деформирующим напряжениям 220 МПа, имеет место зарождение игольчатой αʹʹ-фазы на границах β‑зерен [7]. In-situ исследования титанового сплава Ti–24Nb–4Zr–7.9Sn, подвергнутого одноосному растяжению в колонне просвечивающего электронного микроскопа, показали, что распространение полос сдвига сопровождается выделением α"-фазы [8]. Особо важно отметить работу [9], согласно которой при циклическом нагружении сплава Ti–5Al–5V–5Mo–1Cr–1Fe при комнатной температуре первоначально имеет место двойникование пластин α-фазы, однако при увеличении количества циклов внутри пластин α фазы выделяются дисперсные частицы α"-фазы.
В α-титановых сплавах развитие индуцированных деформацией α' → α"-превращений наблюдалось только в высоконеравновесных поверхностных слоях образцов технического титана ВТ1-0, подвергнутых предварительному облучению непрерывными электронными пучками и последующему одноосному растяжению [10]. В α + β-титановых сплавах образование α"-фазы происходило при скретч-тестировании образцов Ti–6Al–4V, подвергнутых предварительной электронно-пучковой обработке [11], или в процессе ультразвуковой ударной обработки [12]. Очевидно, что появление α"-фазы в сплаве Ti–6Al–4V возможно лишь в метастабильной микроструктуре, сформированной в результате высокоэнергетических воздействий. К последним несомненно относится 3D-печать. В работе [13] методом in situ рентгеновской дифракции наблюдали образование мартенситной α"-фазы при растяжении образцов Ti–6Al–4V, полученных методом электронно-лучевого сплавления. В работе [14] было высказано предположение, что неравновесная структура образцов Ti–6Al–4V, обусловленная неполным распадом α'-фазы в процессе 3D-печати, является причиной формирования мартенситной фазы α"-Ti при их скретч-тестировании, однако прямого подтверждения индуцированных деформацией фазовых превращений представлено не было. Целью данной работы является in situ исследование методом просвечивающей электронной микроскопии структурных и фазовых превращений, развивающихся в 3D-напечатанных образцах Ti–6Al–4V при одноосном растяжении.
МАТЕРИАЛЫ И МЕТОДИКА ИССЛЕДОВАНИЯ
3D-напечатанные заготовки в форме параллелепипеда с размерами 25 мм × 25 мм × 70 мм были получены путем электронно-лучевого плавления проволоки Ti–6Al–4V диаметром 1.6 мм на установке для проволочного электронно-лучевого аддитивного производства (ИФПМ СО РАН, Томск, Россия). Химический состав проволоки, определенный методом микроэнергодисперсионного анализа, являлся следующим (вес. %): Ti – 89.6%, Al – 5.3%, V – 4.2%, примеси – 0.9%. Плавление проволоки проводили в вакууме 1.3 × 10–3 Па электронной пушкой с плазменным катодом при ускоряющем напряжении 30 кВ. Ток пучка был равен 20 мА. Расстояние между электронной пушкой и плитой построения составляло 630 мм. Подача проволоки осуществлялась со скоростью 2 м/мин под углом 35° к поверхности подложки. Стратегия 3D-печати заготовок заключалась в перемещении опорной плиты относительно электронного луча по меандровой траектории с зеркально наплавленными слоями со скоростью 2.25 мм/с. Расстояние между соседними треками в пределах одного слоя составляло ~3 мм. После наплавки каждого слоя опорная плита опускалась на 3 мм.
Микроструктуру 3D-напечатанных образцов Ti–6Al–4V изучали с помощью оптического микроскопа Zeiss Axiovert 40 МАТ, сканирующего электронного микроскопа (СЭМ) Apreo S, а также методом дифракции обратно рассеянных электронов (EBSD) с использованием приставки Oxford Instruments Nordlys. In situ исследования эволюции микроструктуры и фазового состава образцов Ti–6Al–4V в процессе одноосного растяжения при комнатной температуре проводили с помощью просвечивающего электронного микроскопа (ПЭМ) JEM-2100, оборудованного натяжным держателем с одинарным наклоном (Gatan, model 654), а также системой для микроэнергодисперсионного анализа (OXFORD INCA Energy). Скорость перемещения подвижного захвата составляла 0.12 мм/мин. Подготовку образцов Ti–6Al–4V для ПЭМ-исследований осуществляли в несколько этапов. Из центральной части 3D‑напечатанных заготовок были вырезаны образцы в форме прямоугольных пластин с размерами 11.5 мм × 2.5 мм × 0.5 мм. На установке 200 Fischione утоняли центральную область (вышлифовывали сферическое углубление) до толщины ~100 мкм. Дальнейшее утонение центральной части до появления отверстия производили с использованием системы прецизионной ионной полировки (MODEL 1051 TEM Mill) пучком ионов аргона в вакууме при напряжении 6–8 кВ и угле скольжения 5°–7°.
РЕЗУЛЬТАТЫ ЭКСПЕРИМЕНТА И ИХ ОБСУЖДЕНИЕ
Вследствие высокой скорости охлаждения ванны расплава микроструктура образцов Ti‒6Al–4V, полученных методом электронно-лучевой проволочной аддитивной технологии, состоит из столбчатых первичных β-зерен, внутри которых наблюдаются рейки α либо α' фазы (α/α'-Ti), собранные в пакеты (рис. 1). Средние поперечные размеры первичных β-зерен и реек α/α'-Ti составляют 1 мм и 300 нм соответственно. Рейки α/α'-Ti разделены тонкими прослойками остаточной β-фазы толщиной 20 нм (рис. 2). Локальное содержание легирующих элементов в рейках α/α'-Ti и прослойках β-фазы, определенное методом энергодисперсионной рентгеновской спектроскопии, представлено в табл. 1.
Рис. 1.
Оптическое (а) и СЭМ-изображения (б), а также EBSD карта (в) микроструктуры недеформированного образца Ti–6Al–4V. На EBSD карте приведен стереографический треугольник с цветовой дифференциацией кристаллографических направлений.
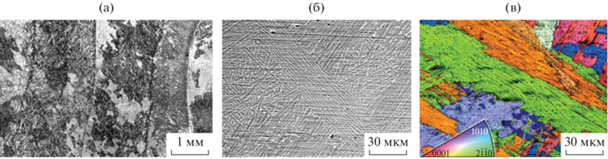
Рис. 2.
Светлопольное (a) и темнопольные (б, в) ПЭМ-изображения, а также микроэлектронограмма (г) микроструктуры недеформированного образца Ti–6Al–4V. Темнопольные изображения получены в рефлексах $~\bar {1}0\bar {1}$ оси зоны $\left[ {\bar {2}\bar {3}2} \right]~$α-Ti (б) и $\bar {2}2\bar {2}$ оси зоны $\left[ {341} \right]~$β-Ti (в).
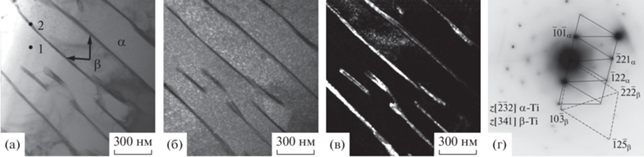
При растяжении образцов Ti–6Al–4V в колонне электронного микроскопа имеет место переориентация локальных областей вблизи границ реек α/α'-Ti (рис. 3а, 4а). Сравнение рис. 3б, 3в показывает, что приграничные области α/α'-Ti, не находящиеся в отражающем положении на рис. 3б, выявляются на темнопольном ПЭМ-изображении в рефлексе $1\bar {1}\bar {2}$α-Ti (рис. 3в). Образование приграничных областей, характеризующихся малоугловой разориентацией, подтверждается тем фактом, что темнопольные ПЭМ-изображения на рис. 3б, в получены в рефлексах, принадлежащих одной оси зоны $\left[ {13\bar {1}} \right]~$α-Ti (рис. 3е).
Рис. 3.
Светлопольное (a) и темнопольные (б–д) ПЭМ-изображения, а также микроэлектронограмма (е) микроструктуры растянутого образца Ti–6Al–4V. Темнопольные изображения получены в рефлексе $~\bar {1}0\bar {1}$ оси зоны $\left[ {13\bar {1}} \right]~$α-Ti (б), в рефлексе $1\bar {1}\bar {2}$ оси зоны $\left[ {13\bar {1}} \right]~$α-Ti (в) и в близкорасположенных рефлексах $\bar {1}13$ оси зоны $\left[ {\overline {7.} 11.\bar {6}} \right]$ α"-Ti, $0\bar {1}\bar {3}$ оси зоны $\left[ {13\bar {1}} \right]~$α-Ti и $\bar {1}12$ оси зоны [531] β-Ti (г, д). д – Увеличенное изображение фрагмента, выделенного на рис. 3г. Смещение подвижного захвата составляет 0.55 мм.
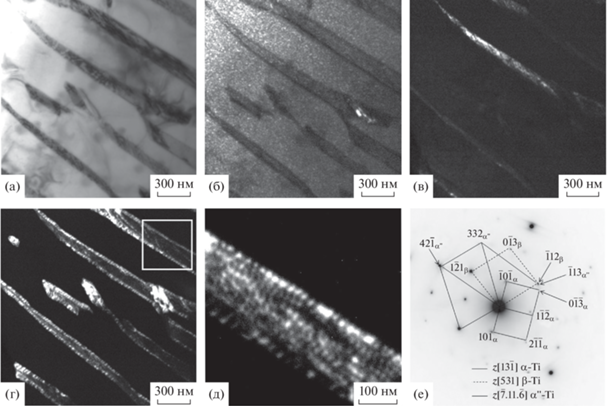
Анализ рис. 3г, 3д показал, что переориентированные области вблизи границ реек α/α'-Ti имеют полосчатый контраст, характерный для стенки краевых дислокаций. Очевидно, что дислокационные стенки возникают в α-фазе как результат релаксации упругих напряжений, появляющихся на границе между α- и β-фазами при одноосном растяжении. Аналогичное формирование дислокационных стенок вблизи границы α/β наблюдалось в образцах сплава Ti–6Al–4V, как результат релаксации внутренних напряжений, возникающих в процессе закалки в воду от 800°С [15].
Угол разориентации θ малоугловых границ, образованных стенкой краевых дислокаций, связан с расстоянием D между дислокациями следующим выражением [16]:
Согласно рис. 3д, среднее расстояние между дислокациями составляет 22 нм. Таким образом, угол разориентации не превышает 1.4°.
Необходимо отметить, что поскольку темнопольные ПЭМ-изображения на рис. 3г, 3д получены в близкорасположенных рефлексах α, α"- и β-фаз, то расположение прослойки остаточной β фазы можно выявить только при сопоставлении с изображениями реек α/α'-Ti в образцах до деформации (ср. рис. 2в и 3г). Также невозможно однозначно утверждать, присутствовала ли мартенситная α"-фаза в прослойках остаточной β‑фазы недеформированного образца, либо возникла в процессе β → α"-превращения при пластической деформации.
При дальнейшем нагружении ширина переориентированных областей в рейках α/α'-Ti увеличивается, а границы данных областей все больше искривляются (рис. 4). Очевидно, что с увеличением степени деформации образцов Ti–6Al–4V возрастает степень переориентации приграничных областей, в результате чего на микроэлектронограмме появляются рефлексы α-Ti, принадлежащие другой оси зоны (рис. 4е). Важно отметить, что переориентированные области наблюдаются только в рефлексе $0\bar {1}0$ α-Ti (рис. 4г). При этом, как видно из сравнения рис. 2в и рис. 4д, ширина прослойки остаточной β-фазы при растяжении образцов Ti–6Al–4V не изменяется.
Рис. 4.
Светлопольное (a) и темнопольные (б–д) ПЭМ-изображения, а также микроэлектронограмма (е) микроструктуры растянутого образца Ti–6Al–4V. Темнопольные изображения получены в близкорасположенных рефлексах $0\bar {1}5$ оси зоны $\left[ {\bar {1}51} \right]~$α-Ti и $3\bar {1}2$ оси зоны $\left[ {20\bar {3}} \right]~$α-Ti (б), в рефлексе $1\bar {1}6$ оси зоны $\left[ {\bar {1}51} \right]~$α-Ti (в), в рефлексе $0\bar {1}0$ оси зоны $\left[ {20\bar {3}} \right]~$α-Ti (г), а также в близкорасположенных рефлексах 202 оси зоны $\left[ {\bar {1}51} \right]$ α-Ti и $2\bar {2}0$ оси зоны [110] β-Ti (д). Смещение подвижного захвата составляет 0.91 мм.
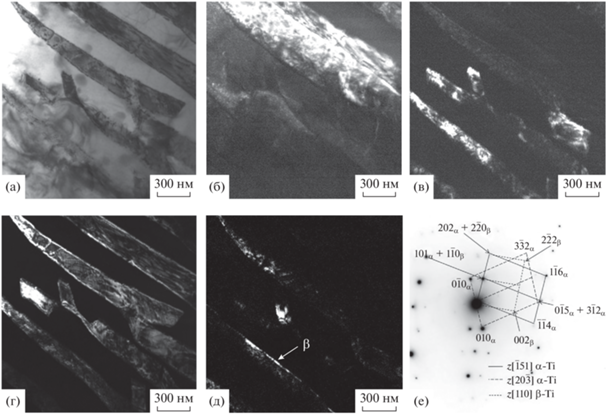
Особенностью микроструктуры исследованных образцов Ti–6Al–4V является концентрационная неоднородность ванадия вследствие частичного распада мартенситной α' фазы в процессе 3D печати. Последнее обусловливает наличие в рейках α/α'-Ti локальных областей, в которых содержание ванадия оказывается существенно больше величины его предельной растворимости в α-фазе (2.7 вес. %). На рис. 5 представлены ПЭМ-изображения рейки α/α'-Ti, в которой уже в процессе 3D-печати (вследствие высоких остаточных напряжений [17]) возникли локальные области α'-фазы, характеризующиеся малоугловой разориентацией. В некоторых из этих разориентированных областей содержание ванадия оказывается достаточно высоким (табл. 1). Сравнительный анализ рис. 5 и 6 свидетельствует о том, что при последующем одноосном растяжении в переориентированных областях решетки α/α'-Ti, в местах, обогащенных ванадием, может образовываться нанокристаллическая орторомбическая α"-фаза.
Рис. 5.
Светлопольное (a) и темнопольные (б, в) ПЭМ-изображения, а также микроэлектронограмма (г) микроструктуры недеформированного образца Ti–6Al–4V. Темнопольные изображения получены в рефлексе 100 (б) и рефлексе $1\bar {1}1$ оси зоны $\left[ {011} \right]~$α-Ti (в).
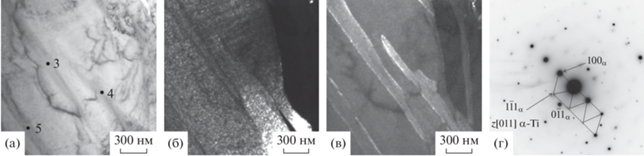
Рис. 6.
Светлопольное (a) и темнопольные (б, в) ПЭМ-изображения, а также микроэлектронограмма (г) микроструктуры растянутого образца Ti–6Al–4V. Темнопольные изображения получены в рефлексе $022$ оси зоны $\left[ {100} \right]~$α"-Ti (б) и рефлексе $1\bar {1}1$ оси зоны $\left[ {011} \right]~$α-Ti (в). Смещение подвижного захвата составляет 0.91 мм.
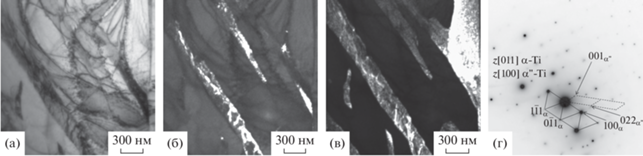
Как правило, мартенситная α"-фаза образуется при закалке высоколегированных титановых сплавов. Ее появление обусловлено высокой концентрацией β-стабилизирующих элементов (Mo, V, Nb и др.), которые изменяют электронную конфигурацию атомов титана и приводят к сильному искажению ОЦК-решетки, в результате которого кубическая структура метастабильного β‑твердого раствора трансформируется в орторомбическую [6, 18]. Тем не менее в образцах двухфазного α + β-титанового сплава Ti–6Al–4V, полученных методом аддитивных технологий, α" фаза наблюдается достаточно часто [3–5, 19–22]. Согласно [23], α' → α"-фазовое превращение в системе Ti–V является энергетически выгодным при концентрации ванадия в диапазоне от 5.3 до 12.6 вес. %. Локальные области со столь высоким содержанием ванадия могут образовываться в образцах 3D-напечатанных сплавов Ti–6Al–4V в результате частичного распада мартенситной α'-фазы.
Известно, что полный распад мартенситной α' фазы в титановом сплаве Ti–6Al–4V происходит при выдержке при температуре 700°С в течение 30 мин [24]. При селективном лазерном спекании тонкого слоя титанового порошка скорость охлаждения ванны расплава оказывается чрезвычайно высокой (105–108 K/c) [5]. Соответственно в таких образцах частичный распад α' фазы с образованием α"-фазы наблюдается только после их термической обработки [4, 5, 19]. В свою очередь, при электронно-лучевом плавлении титановой проволоки размер ванны расплава оказывается существенно больше, а скорость ее охлаждения существенно ниже (103 K/c [21]). Можно ожидать, что в исследованных образцах Ti–6Al–4V, испытавших многократные циклы нагрева– охлаждения в процессе послойного роста, уже произошел частичный распад α'-фазы, обусловливающий появление локальных областей с высоким содержанием легирующих элементов.
Согласно нашим предыдущим исследованиям, мартенситная α"-фаза наиболее часто образуется в образцах Ti–6Al–4V, полученных методом электронно-лучевой проволочной аддитивной технологии при водяном охлаждении плиты построения [21]. Важно отметить, что при этом величина микроискажений в кристаллической решетке α/α'-Ti более чем в 2 раза превышает микроискажения в образцах, полученных без принудительного охлаждения. Можно полагать, что именно в областях высокой локальной кривизны ГПУ-решетка теряет устойчивость, трансформируясь в орторомбическую α"-фазу [22].
На светлопольном ПЭМ-изображении деформированных образцов Ti–6Al–4V присутствует большое количество экстинкционных контуров (рис. 6а). Последнее свидетельствует о том, что в процессе одноосного растяжения имеет место сильное искажение кристаллической решетки реек α/α'-Ti, возникающее в результате совместной деформации соседних реек. Очевидно, что пластическая деформация является дополнительной движущей силой, приводящей к α' → α"-фазовому превращению в локальных областях реек α/α'-Ti с высоким содержанием ванадия.
ЗАКЛЮЧЕНИЕ
Характерной особенностью микроструктуры образцов титанового сплава Ti–6Al–4V, полученных методом электронно-лучевой проволочной аддитивной технологии, является образование столбчатых первичных β-зерен, внутри которых наблюдаются рейки α/α'-Ti, собранные в пакеты и разделенные прослойками остаточной β-фазы, а также концентрационная неоднородность легирующих элементов. В процессе одноосного растяжения происходит переориентация кристаллической решетки в рейках α/α'-Ti вблизи межфазных границ за счет образования стенки краевых дислокаций. В переориентированных областях решетки α/α'-Ti в местах, обогащенных ванадием, могут развиваться индуцированные деформацией α' → α"-превращения.
Работа выполнена при финансовой поддержке Российского научного фонда (грант № 21-19-00795). Исследования выполнены с использованием оборудования ЦКП “Нанотех” ИФПМ СО РАН и ЦКП НОИЦ НМНТ ТПУ.
Список литературы
Sames W.J., List F.A., Pannala S., Dehoff R.R., Babu S.S. The metallurgy and processing science of metal additive manufacturing // Int. Mater. Rev. 2016. V. 61. P. 315–360.
Herzog D., Seyda V., Wycisk E., Emmelmann C. Additive manufacturing of metals // Acta Mater. 2016. V. 117. P. 371–392.
Murr L.E., Quinones S.A., Gaytan S.M., Lopez M.I., Rodela A., Martinez E.Y., Hernandez D.H., Martinez E., Medina F., Wicker R.B. Microstructure and mechanical behavior of Ti–6Al–4V produced by rapid-layer manufacturing, for biomedical applications // J. Mech. Behav. Biomed. Mater. 2009. V. 2. P. 20–32.
Казанцева Н.В., Крахмалев П.В., Ядройцева И.А., Ядройцев И.А. Лазерная аддитивная 3D-печать титановых сплавов: современное состояние, проблемы, тенденции // ФММ. 2021. Т. 122. № 1. С. 8–30.
Jaber H., Kónya J., Kulcsár K., Kovács T. Effects of Annealing and Solution Treatments on the Microstructure and Mechanical Properties of Ti6Al4V Manufactured by Selective Laser Melting // Materials. 2022. V. 15. P. 1978.
Niessen F., Pereloma E. A Review of In Situ Observations of Deformation-Induced β ↔ α" Martensite Transformations in Metastable β Ti Alloys // Adv. Eng. Mater. 2022. V. 24. P. 2200281.
Duerig T.W., Albrecht J., Richter D., Fischer P. Formation and reversion of stress induced martensite in Ti–IOV–2Fe–3AI // Acta Metall. 1982. V. 30. P. 2161–2172.
Yao T., Du K., Hao Y., Li S., Yang R., Ye H. In-situ observation of deformation-induced αʹʹ phase transformation in a β-titanium alloy // Mater. Lett. 2016. V. 182. P. 281–284.
Chen W., Yang Sh., Lin Y.C., Shi S., Chen C., Zhang X., Zhoul K. Cyclic deformation responses in α-phase of a lamellar near β-Ti alloy // Mater. Sci. Eng. A. 2020. V. 796. P. 139994.
Панин А.В., Казаченок М.С., Перевалова О.Б., Синякова Е.А., Круковский К.В., Мартынов С.А. Многоуровневые механизмы деформационного поведения технического титана и сплава Ti–6Al–4V, подвергнутых обработке высокочастотными электронными пучками // Физ. мезомех. 2018. Т. 21. № 4. С. 45–56.
Sinyakova E.A., Panin A.V., Perevalova O.B., Shugurov A.R., Kalashnikov M.P., Teresov A.D. The effect of phase transformations on the elastic recovery of pulsed electron beam irradiated Ti–6Al–4V titanium alloy during scratching // J. Alloys Compd. 2019. V. 795. P. 275–283.
Panin A., Dmitriev A., Nikonov A., Perevalova O., Kazantseva Bakulin L., A., Kulkova S. Transformations of the microstructure and phase compositions of titanium alloys during ultrasonic impact treatment. Part II: Ti–6Al–4V Titanium Alloy // Metals. 2022. V. 12. P. 732.
Sofinowski K., Šmíd M., Kuběna I., Vivès S., Casati N., Godet S., Van Swygenhoven H. In situ characterization of a high work hardening Ti–6Al–4V prepared by electron beam melting // J. Mater. Sci. 2019. V. 179. P. 224–236.
Shugurov A., Panin A., Kazachenok M., Kazantseva L., Martynov S., Bakulin A., Kulkova S. Deformation behavior of wrought and EBAM Ti–6Al–4V under scratch testing // Metals. 2021. V. 11. P. 1882.
Cabibbo M., Zherebtsov S., Mironov S., Salishchev G. Loss of coherency and interphase α/β angular deviation from the Burgers orientation relationship in a Ti–6Al–4V alloy compressed at 800°C // J. Mater. Sci. 2003. V. 48. P. 1100–1110.
Грабский М.В. Структура границ зерен в металлах. Москва, Металлургия, 1972. 160 с.
Панин А.В., Казаченок М.С., Казанцева Л.А., Мартынов С.А., Панина А.А., Лобова Т.А. Микроструктура и фазовый состав титановых сплавов ВТ1-0, ВТ6 и ВТ14, полученных методом электронно-лучевой проволочной аддитивной технологии // Поверхность. Рентгеновские, синхротронные и нейтронные исследования. 2022. Т. 11. С. 63–72.
Motyka M. Martensite Formation and Decomposition during Traditional and AM Processing of Two-Phase Titanium Alloys – An Overview // Metals. 2021. V. 11. P. 481.
Wu S.Q., Lu Y.J., Gan Y.L., Huang T.T., Zhao C.Q., Lin J.J., Guo S., Lin J.X. Microstructural evolution and microhardness of a selective-laser-melted Ti–6Al–4V alloy after post heat treatments // J. Alloys Compd. 2016. V. 672. P. 643–652.
Pushilina N., Panin A., Syrtanov M., Kashkarov E., Kudiiarov V., Perevalova O., Laptev R., Lider A., Koptyug A. Hydrogen-induced phase transformation and microstructure evolution for Ti–6Al–4V parts produced by electron beam melting // Metals. 2018. V. 8. P. 301.
Panin A., Martynov S., Kazachenok M., Kazantseva L., Bakulin A., Kulkova S., Perevalova O., Sklyarova E. Effects of Water Cooling on the Microstructure of Electron Beam Additive-Manufactured Ti–6Al–4V // Metals. 2021. V. 11. P. 1742.
Панин В.Е., Панин А.В., Перевалова О.Б., Шулепов И.А., Власов И.В. Влияние кривизны кристаллической решетки на иерархию масштабов деформационных дефектов и характер пластического течения металлических материалов // Физ. мезомех. 2020. Т. 23. № 4. P. 5–12.
Добромыслов А.В., Талуц Н.И. Структура циркония и его сплавов // УрО РАН, Екатеринбург. 1997. 228 с.
Zeng L., Bieler T.R. Effects of working, heat treatment, and aging on microstructural evolution and crystallographic texture of α, α', α" and β phases in Ti–6Al–4V wire // Mater. Sci. Eng. A. 2005. V. 392. P. 403–414.
Дополнительные материалы отсутствуют.
Инструменты
Физика металлов и металловедение