Физика металлов и металловедение, 2023, T. 124, № 3, стр. 303-309
Моделирование роста аустенитного зерна в низколегированных сталях при аустенитизации
И. И. Горбачев a, *, Е. И. Корзунова a, В. В. Попов a, Д. М. Хабибулин b, Н. В. Урцев b
a Институт физики металлов имени М.Н. Михеева УрО РАН
620990 Екатеринбург, ул. С. Ковалевской, 18, Россия
b Исследовательско-технологический центр “Аусферр”,
455000 Магнитогорск, ул. Ломоносова, д. 11/1, Россия
* E-mail: gorbachev@imp.uran.ru
Поступила в редакцию 17.11.2022
После доработки 26.12.2022
Принята к публикации 25.01.2023
- EDN: CNDVHL
- DOI: 10.31857/S0015323022601738
Аннотация
Разработана модель, описывающая рост зерна при аустенитизации с учетом сдерживания движущихся границ зерен карбонитридными выделениями. Для описания поведения последних модель опирается на подход для прогнозирования эволюции карбонитридных частиц, предложенный нами ранее. Осуществлена программная реализация разработанной модели и выполнены численные расчеты. Проведено сравнение результатов расчетов с имеющимися в литературе экспериментальными данными и показано их хорошее согласие.
ВВЕДЕНИЕ
Размер зерна является важным фактором, определяющим механические свойства сталей [1–5]. Его необходимо тщательно контролировать при проведении операций горячей деформации (например, горячей прокатки) и термической обработки. Размер аустенитного зерна, образовавшегося в процессе выдержки под прокатку, влияет на протекание фазовых и структурных превращений при последующей горячей деформации. Размер аустенитного зерна, сформировавшегося в результате термической или термомеханической обработки, обеспечивает начальное условие для последующего фазового превращения при охлаждении и, таким образом, влияет на конечную микроструктуру и результирующие механические свойства. Например, увеличение размера аустенитного зерна сдвигает диаграмму превращения при непрерывном охлаждении в сторону увеличения времени реакции, тем самым повышая возможность образования бейнита и мартенсита [6–8].
Легирование сталей сильными карбонитридообразующими элементами, такими как ниобий, титан, ванадий или алюминий, приводит к формированию в стали дисперсных выделений, сдерживающих рост аустенитных зерен при горячей прокатке, сварке или термической обработке [9–12].
В последние годы был сделан ряд попыток разработать модель, описывающую рост зерна при аустенитизации в сталях, содержащих дисперсные выделения [11, 13, 14]. Однако в этих работах используются очень упрощенные модели для описания эволюции выделений при аустенитизации, что является существенным недостатком, так как часто именно кинетика эволюции выделений вторых фаз является основным фактором, определяющим скорость роста зерна.
В настоящей работе представлена модель для прогнозирования роста зерна при аустенитизации, которая включает в качестве составной части описание эволюции карбонитридных частиц, основанное на подходе, предложенном нами ранее [15]. Разработанная модель ориентирована на малоуглеродистые низколегированные стали с карбонитридным упрочнением.
ПОСТРОЕНИЕ МОДЕЛИ
Разработанная модель состоит из двух частей: одна описывает рост зерен при аустенитизации, а вторая – эволюцию карбонитридных выделений в процессе аустенитизации.
Модель роста зерен во многом аналогична моделям, использовавшимся в работах [13, 14].
Движущая сила роста зерен определяется выражением [16, 17]:
где $\bar {D}$ – средний диаметр зерна, γ – энергия границы зерна, принимаемая равной 0.5 Дж м–2 [18], α – безразмерная геометрическая постоянная. Для трехмерного роста зерен, исследованного в настоящей работе, α = 4 [19].Частицы второй фазы, присутствующие в матрице, тормозят рост аустенитного зерна. Эти выделения закрепляют границы аустенитных зерен, замедляя или даже полностью тормозя их движение при термической обработке. Закрепляющая сила определяется объемной долей частиц (f) и их размером (средним радиусом частиц R). Сила, действующая на границу зерна со стороны частиц второй фазы, выражается как [20]
где β – безразмерная константа. Согласно [21], β = 12.Аналогично тому, как это было сделано в нашей работе [22], для оценки тормозящей силы выделений вместо отношения f/R в уравнении (2) используем выражение
где fi и Ri – объемная доля и размер частиц i-го размерного интервала.С учетом этого выражение (2) для тормозящей силы приобретает вид:
(4)
${{P}_{z}} = {{\beta \gamma }}\left[ {\sum\limits_i {\left( {\frac{{{{f}_{i}}}}{{{{R}_{i}}}}} \right)} } \right].$Скорость движения границы зерна может быть выражена следующим образом:
где M – подвижность границы зерна.Температурная зависимость подвижности выражается аррениусовским соотношением:
где ${{R}_{{\text{g}}}}$ – газовая постоянная.Согласно [11] предэкспоненциальный множитель, M0 равен 120 м4/(Дж с), а энергия активации, Q, принимается равной 350 кДж/моль.
Скорость движения границы зерна также может быть выражена как
Объединив выражения (4)–(7), получим дифференциальное уравнение, описывающее рост зерен:
(8)
$\frac{{dD}}{{dt}} = {{M}_{0}}{\text{exp}}\left( { - \frac{Q}{{{{R}_{{\text{g}}}}T}}} \right)\gamma \left\{ {\alpha \frac{1}{D} - \beta \left[ {\sum\limits_i {\left( {\frac{{{{f}_{i}}}}{{{{R}_{i}}}}} \right)} } \right]} \right\}.$При описании эволюции выделений предполагалось, что выделения имеют сферическую форму и постоянный состав, на межфазных границах устанавливается локальное термодинамическое равновесие, и массоперенос контролируется объемной диффузией в матрице. При этом учитывалась возможность образования и одновременной эволюции нескольких избыточных фаз.
Метод расчета основан на использовании приближения среднего поля. В этом случае скорость роста (или растворения) частиц каждого размерного класса и состава рассчитывается с учётом диффузионного взаимодействия между частицей и ее средним окружением. Для этого вокруг каждой частицы строятся виртуальные полевые ячейки, внутри которых на основе решения системы диффузионных уравнений и определяются концентрационные профили легирующих элементов (диффузионные поля). При этом предполагается, что концентрации компонентов на границах всех полевых ячеек одинаковы:
(9)
$^{\gamma }X_{i}^{{fl}}\left( {r = \,{{\,}^{L}}R_{l}^{f}} \right) = \,{{\,}^{\gamma }}X_{i}^{L}.$Обмен веществом между частицами происходит через стенки полевых ячеек.
Предполагалось, что размеры полевых ячеек связаны с размером частиц следующим образом:
где ${{F}_{f}}$ – объемная доля карбонитридной фазы f.При нахождении распределений концентраций элементов в полевых ячейках использовалось приближение квазистационарного поля. В этом случае система уравнений диффузии, описывающих потоки вещества в ячейке, связанной с частицей фазы f l-го размерного интервала, для (N + 1)-компонентной системы имеет вид
(11)
$\sum\limits_{j = 1}^N {{{{\tilde {D}}}_{{ij}}}\frac{{{{\partial }^{\gamma }}X_{j}^{{fl}}}}{{\partial r}}} = \frac{{K_{i}^{{fl}}}}{{{{r}^{2}}}},$Концентрации компонентов на межфазных границах должны удовлетворять условиям локального равновесия и баланса масс. Для случая карбидных или нитридных выделений постоянного состава MXn условия равновесия между частицей l-го размерного интервала и матрицей с поправкой на кривизну межфазной границы имеют вид:
(12)
${{\bar {G}}_{{\text{M}}}} + n{{\bar {G}}_{{\text{X}}}} - \frac{{2\sigma {{V}_{{{\text{M}}{{X}_{n}}}}}}}{{R_{l}^{{{\text{M}}{{X}_{n}}}}}} = {{G}_{{{\text{M}}{{X}_{n}}}}},$Для описания термодинамических свойств аустенита использовалась модель Хиллерта–Стаффонссона, обобщенная Сандманом и Агреном в работах [23, 24].
Условия баланса масс на межфазной границе для выделений фазы f l-го размерного интервала имеют вид:
(13)
$\left[ {{{^{f}{{X}_{i}}\bar {V}_{\gamma }^{a}} \mathord{\left/ {\vphantom {{^{f}{{X}_{i}}\bar {V}_{\gamma }^{a}} {\bar {V}_{f}^{a}}}} \right. \kern-0em} {\bar {V}_{f}^{a}}} - \,{{\,}^{{\gamma b}}}X_{i}^{{lf}}} \right]\frac{{dR_{l}^{f}}}{{dt}} - \frac{{^{f}K_{i}^{l}}}{{{{{\left( {R_{l}^{f}} \right)}}^{2}}}} = 0,$В рассматриваемом случае система уравнений, которым должны удовлетворять распределения концентраций компонентов в полевых ячейках и скорости движения межфазных границ, должна быть дополнена условием сохранения массы. Условие сохранения массы учитывает, что, если средние концентрации элементов в матрице являются функциями времени, то и объемная доля избыточной фазы также является функцией времени. Условие сохранения массы имеет вид (для каждого элемента системы i):
(14)
$\sum\limits_f {\alpha {{{_{f}^{{}}}}^{f}}{{X}_{i}}} + {{\left( {1 - \sum\limits_f {{{\alpha }_{f}}} } \right)}^{\gamma }}{{\bar {X}}_{i}} - \,{{\,}^{0}}{{X}_{i}} = 0,$Для нахождения распределений концентраций элементов в ячейках используется метод конечных разностей. При этом непрерывные распределения концентраций компонентов заменяются сеточными функциями, определенными в дискретных узлах пространственной сетки.
Предполагалось, что зарождение частиц карбонитридных фаз происходит на дислокациях. В этом случае для описания скорости зарождения выделений использовался подход, развитый в работах [25, 26].
Порядок расчета эволюции выделений был следующим:
1. Расчет размеров полевых ячеек, связанных с частицами всех избыточных фаз и разных размерных интервалов;
2. Построение пространственных сеток в полевых ячейках для всех фаз и всех размерных интервалов;
3. Расчет концентраций элементов на границах ячеек, соответствующих условиям локального термодинамического равновесия, баланса масс и сохранения массы;
4. Расчет распределений концентраций компонентов в ячейках и скоростей движения межфазных границ для частиц всех избыточных фаз всех размерных интервалов;
5. Расчет распределений частиц по размерам и объемных долей для всех избыточных фаз на новом временном шаге без учета образования новых зародышевых центров;
6. Расчет скоростей зарождения выделений для всех избыточных фаз;
7. Расчет распределений частиц по размерам и объемных долей для всех избыточных фаз на новом временном шаге с учетом процессов зарождения.
Более подробно методика расчета эволюции выделений описана в работе [15]. Необходимые для расчетов термодинамические параметры и коэффициенты диффузии приведены в работах [27–29].
При моделировании эволюции выделений и роста аустенитного зерна исходными данными являлись распределения выделений по размерам, их объемная доля и исходный средний размер аустенитных зерен.
Для расчетов использовалась пошаговая процедура. На каждом временном шаге выполнялись следующие операции:
1. Рассчитывалось состояние ансамбля выделений (их объемные доли и распределение по размерам) на данном временном шаге;
2. Рассчитывалась движущая сила роста зерен и тормозящая сила со стороны выделений;
3. Вычислялась скорость роста зерен и, соответственно, их средний размер на следующем временном шаге.
Найденные значения среднего размера зерен, объемных долей и распределения по размерам выделений служили исходными данными для расчетов на новом временном шаге.
ТЕСТИРОВАНИЕ РАЗРАБОТАННОЙ МОДЕЛИ РОСТА ЗЕРНА ПРИ АУСТЕНИТИЗАЦИИ
Для проверки возможностей прогнозирования изменения размера аустенитного зерна при высокотемпературной деформации с помощью предложенного алгоритма было выполнено сравнение результатов расчетов с данными экспериментальных исследований, выполненных в работах [13, 14]. В обоих статьях исследовали малоуглеродистые стали, легированные Nb и Ti.
В работе [13] исследовали рост аустенитного зерна при отжиге стали Х80, химический состав которой приведен в табл. 1. Исследования были проведены для температурного диапазона 950–1250°С.
Таблица 1.
Химический состав стали Х80, исследованной в работе [13] (мас. %)
C | Mn | Nb | Ti | N | Mo | Fe |
---|---|---|---|---|---|---|
0.06 | 1.65 | 0.034 | 0.012 | 0.005 | 0.24 | Осн. |
Полученные по данным в работе [13] экспериментальные зависимости среднего размера аустенитного зерна от времени отжига представлены на рис. 1.
В исходном состоянии в исследуемой стали присутствовали две карбонитридные фазы: фаза близкая по составу к нитриду титана и фаза близкая по составу к карбиду ниобия. В работе [13] выполнена оценка исходного состояния ансамблей TiN и NbC. Но мы несколько уточнили оценку исходного размера частиц TiN, выполненную Мааликяном и др. [13], учтя, что при нагреве в аустенитную область часть нитридов титана может раствориться, и их размеры изменятся.
Из рис. 1 видно, что после выдержки при температуре 1250°С в течение 50–100 с быстрый рост размера зерна прекращается. Это свидетельствует о том, что зерна к этому моменту достигают размера, который контролируется присутствующими выделениями. Размер зерен к этому моменту достигает значения ~50 мкм.
Рис. 1.
Изменение размера аустенитного зерна в процессе отжига: по данным [13] – штриховые линии; расчетные зависимости на основе алгоритма, предложенного в настоящей работе, – сплошные линии; символы – результаты металлографических измерений.
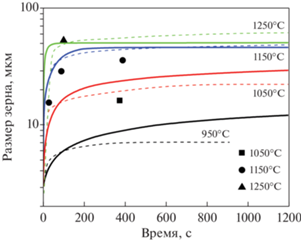
Расчет показывает, что частицы карбида ниобия при температуре 1250°С растворяются в течение нескольких секунд. Следовательно, сдерживать рост зерна при этой температуре могут только нитриды титана, основная часть которых останется нерастворенной.
Согласно [21] в этом случае размер зерна связан с радиусом и объемной долей выделений следующими соотношением:
Наш алгоритм оперирует не со средним значением, а с ансамблем частиц с некоторым распределением по размерам. Поэтому выражение (15) приобретает вид
(16)
$D = \frac{1}{3}{{\left[ {\sum\limits_i {\left( {\frac{{{{f}_{i}}}}{{{{R}_{i}}}}} \right)} } \right]}^{{ - 1}}}.$На основании термодинамических расчетов можно оценить, что равновесная объемная доля TiN при 1250°С составляет 0.000201. С учетом этого, используя выражение (16) и предполагая, что размеры частиц распределены согласно нормальному распределению шириной ~5 нм (аналогично приведённому в [13] распределению частиц TiN), можно оценить, что средний размер TiN при этой температуре равен ~28.5 нм.
Рис. 2.
Изменение размера аустенитного зерна в процессе отжига: по данным [14] – пунктирные линии и символы; расчетные зависимости на основе алгоритма, предложенного в настоящей работе, – сплошные линии.
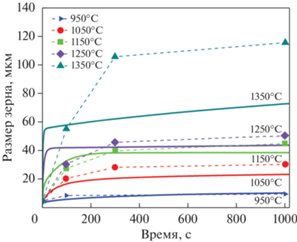
В работе [13] была определена объемная доля TiN в исходном состоянии – 0.00022. При нагреве до 1250°С часть нитридов растворяется, и средний размер частиц этой фазы немного уменьшается. Расчет показывает, что выдержки при 1250°С в течение 50–100 с достаточно, чтобы объемная доля TiN практически достигла равновесного значения. Для того, чтобы средний радиус выделений к этому времени достиг значения 28.5 нм, исходный средний радиус должен составлять 29.5 нм.
Таким образом, при расчетах предполагалось, что в исходном состоянии нитриды титана имеют средний размер 29.5 нм, и их размеры распределены по нормальному закону шириной 5 нм, а их объемная доля равна 0.00022.
Остальные необходимые для расчетов параметры были непосредственно взяты из работы [13]. Исходный средний размер зерен аустенита был равен 3.5 мкм. В исходном состоянии присутствовали частицы карбида ниобия двух фракций: мелкие, имевшие средний размер 3.5 нм, объемная доля которых составляла 1.0 × 10–4 и крупные со средним размером 24 нм и объемной долей 2.8 × 10–4. Ширина распределения мелких частиц NbС задавалась 2 нм, крупных – 8 нм.
Сравнение приведённых на рис. 1 экспериментальных и расчетных зависимостей размера аустенитного зерна от времени отжига показывает, что они хорошо согласуются.
Рост зерна при аустенитизации также исследовали в работе [14]. Исследования проводили на стали Х70, химический состав которой представлен в табл. 2. Исследования были проведены для температурного диапазона 950–1350°С.
Таблица 2.
Химический состав стали Х70, исследованной в работе [14] (мас. %)
C | Mn | V | Nb | Ti | N | Mo | Si | Fe |
---|---|---|---|---|---|---|---|---|
0.0878 | 1.61 | 0.0013 | 0.0363 | 0.018 | 0.0038 | 0.009 | 0.3035 | Осн. |
Как и в ранее рассмотренной стали в данной стали в исходном состоянии присутствовали две карбонитридные фазы: фаза близкая по составу к нитриду титана, и фаза, близкая по составу к карбиду ниобия.
В работе [14] выполнена оценка исходного состояния ансамблей TiN и NbC. Но, аналогично тому, как это было сделано для расчетов при сравнении с [13], мы уточнили оценку исходного размера частиц TiN, выполненную в [14].
Объемная доля нитридов титана в исходном состоянии была задана соответствующей максимальному связыванию Ti и N – 2.5 × 10–4. Средний радиус выделений этой фазы был оценен также, как для ранее рассмотренной стали. Он составил 26.5 нм. Предполагалось, что размеры частиц TiN распределены по нормальному закону с шириной распределения 5 нм.
В исходном состоянии присутствовали карбиды ниобия двух фракций: крупные и дисперсные. В работе [14] были определены объемные доли, средние размеры и распределения частиц по размерам для карбидов ниобия обеих фракций.
Объемная доля крупных частиц NbC составляла 2.6 × 10–4, средний радиус частиц – 31 нм, ширина распределения – 5 нм. Объемная доля мелких выделений NbC составляла 1.6 × 10–4, средний радиус частиц – 3.5 нм, ширина распределения – 2 нм.
На рис. 2 приведены построенные по данным, приведенным в [14], экспериментальные зависимости изменения среднего размера аустенитных зерен в рассматриваемой стали в процессе отжига при температурах 950–1350°С, а также расчетные зависимости, построенные на основе предложенного в настоящей работе алгоритма.
Видно, что при всех температурах, кроме температуры 1350°C, наблюдается хорошее согласие расчетов и эксперимента. Аномальное расхождение для температуры 1350°С довольно трудно объяснить. Возможно, это объясняется образованием в некоторых объемах образца δ-феррита, диффузия в котором протекает значительно быстрее, чем в аустените. Этого можно ожидать вследствие δ-стабилизирующего влияния Nb при наличии некоторой неоднородности по составу.
Таким образом, в обеих сталях в большинстве случаев наблюдается хорошее согласие расчетов с экспериментом. Небольшие различия результатов расчетов и эксперимента можно объяснить небольшой погрешностью определения объемных долей и размеров частиц в исходном состоянии в работах [13, 14].
ЗАКЛЮЧЕНИЕ
Представлена модель, описывающая рост аустенитного зерна в низколегированных сталях, содержащих дисперсные выделения, которые могут тормозить этот рост. Разработанная модель состоит из двух частей: роста зерна и эволюции выделений.
Модель позволяет учитывать: конечную объемную долю выделений вторых фаз, возможность зарождения новых частиц вторых фаз, диффузионное взаимодействие элементов в твердом растворе, наличие в аустенитной матрице выделений разного состава и сдерживание роста аустенитного зерна карбонитридными выделениями.
Осуществлена программная реализация разработанного алгоритма и проведено сравнение результатов расчетов с экспериментальными данными, имеющимися в литературе. Проведенное сравнение показало хорошее согласие результатов расчетов с экспериментом.
Список литературы
Пимккеринг Ф.Б. Физическое металловедение и разработка сталей. М.: Металлургия, 1982. 184 с.
Матросов А.Ю., Литвиненко Д.А., Голованенко С.А. Сталь для магистральных газопроводов. М.: Металлургия, 1989. 288 с.
Muszka K., Majta J., Bienais L. Effect of grain refinement on mechanical properties of microalloyed steels // Metal. Foundry Eng. 2006. V. 32. № 2. P. 87–97.
Пышминецев И.Ю., Смирнов М.А. Структура и свойства сталей для магистральных газопроводов. Екатеринбург: УМЦ УПИ, 2019. 249 с.
Хлусова Е.И., Сыч О.В., Орлов В.В. Хладостойкие стали. структура, свойства, технологии // ФММ. 2021. Т. 122. № 6. С. 621–657.
Barford J., Owen W. The effect of austenite grain size and temperature on the rate of bainite transformation // J. Iron Steel Inst. 1961. V. 197. № 2. P. 359–360.
Hanamura T., Torizuka S., Tamura S., Enokida S., Takechi H. Effect of austenite grain size on transformation behavior, microstructure and mechanical properties of 0.1C–5Mn martensitic steel // ISIJ Int. 2013. V. 53. № 12. P. 2218–2225.
Уткинa И.Ю., Ефименко Л.А., Бобринская В.Ю., Капустин О.Е. Оценка роли ванадия и молибдена в изменении кинетики распада аустенита и механических свойств смоделированной зоны перегрева малоуглеродистых ниобийсодержащих сталей // ФММ. 2021. Т. 122. № 7. С. 769–775.
Попов В.В. Моделирование превращений карбонитридов при термической обработке сталей. Екатеринбург: УрО РАН, 2003. 378 с.
San Martin D., Caballero F.G., Capdevila C., De Andres C.G. Austenite grain coarsening under the influence of niobium carbonitrides // Mater. Trans. 2004. V. 45. № 9. P. 2797–2804.
Banerjee K., Militzer M., Perez M., Wang X. Nonisothermal austenite grain growth kinetics in a microalloyed X80 linepipe steel // Metal. Mater. Trans. A. 2010. V. 41A. № 12. P. 3161–3172.
Roy S., Chakrabarti D., Dey G.K. Austenite grain structures in Ti- and Nb-containing high-strength low-alloy steel during slab reheating // Mater. Sci. Forum. 2014. V. 783–786. P. 669–673.
Maalekian M., Radis R., Militzer M., Moreau A., Poole W.J. In situ measurement and modelling of austenite grain growth in a Ti/Nb microalloyed steel // Acta Mater. 2012. V. 60. P. 1015–1026.
Khalaj G., Yoozbashizadeh H., Khodabandeh A., Tamizifar M. Austenite grain growth modelling in weld heat affected zone of Nb/Ti microalloyed linepipe Steel // Mater. Sci. Techn. 2014. V. 30. № 2. P. 424–433.
Popov V.V., Gorbachev I.I., Pasynkov A.Yu. Simulation of precipitates evolution in multiphase multicomponent systems with consideration of nucleation // Philosoph. Mag. 2016. V. 96. № 35. P. 3632–3653.
Patterson B.R., Liu Y. Relationship between grain boundary curvature and grain size // Metall. Trans. 1992. 23A. P. 2481–2482.
Hellman P, Hillert M. On the effect of second-phase particles on grain growth // Scand. J. Metall. 1975. V. 4. P. 211–219.
Humphreys F.J., Hatherly M. Recrystallization and related annealing phenomena. 2nd ed. Oxford, Elsevier, 2004. 574 p.
Hillert M. On the theory of normal and abnormal grain growth // Acta Met. 1965. V. 13. P. 227–238.
C.S. Smith. Introduction to grains, phases, and interfaces – an interpretation of microstructure // Trans. AIME. 1948. V. 175. P. 15–51.
Rios P.R. Overview № 62: A theory for grain boundary pinning by particles // Acta Metallurgica. 1987. V. 35. № 12. P. 2805–2814.
Горбачёв И.И., Пасынков А.Ю., Попов В.В. Прогнозирование размера аустенитного зерна микролегированных сталей на основе моделирования эволюции карбонитридных выделений // ФММ. 2015. Т. 116. № 11. С. 1184–1191.
Hillert M., Staffonsson L.-I. The regular solution model for stoichiometric phases and ionic melts // Acta Chemica Scand. 1970. V. 24. № 10. P. 3618–3626.
Sandman B., Agren J. A regular solution model for phase with several components and sublattices, suitable for computer applications // J. Phys. Chem. Solids. 1981. V. 42. № 4. P. 297–301.
Liu W.J., Jonas J. Characterisation of critical nucleus/matrix interface: Application to Cu–Co alloys and microalloyed austenite // Mater. Sci. Technol. 1988. V. 5. P. 8–12.
Liu W.J., Jonas J. Nucleation kinetics of Ti carbonitride in microalloyed austenite // Metall. Trans. A. 1989. V. 20. P. 689–697.
Горбачев И.И., Попов В.В., Пасынков А.Ю. Термодинамическое моделирование карбонитридообразования в сталях с Nb и Ti // ФММ. 2012. Т. 113. № 7. С. 727–735.
Горбачев И.И., Попов В.В., Пасынков А.Ю. Моделирование эволюции выделений двух карбонитридных фаз в сталях с Nb и Ti при изотермическом отжиге // ФММ. 2013. Т. 114. № 9. С. 807–817.
Горбачев И.И., Попов В.В., Пасынков А.Ю. Расчеты влияния легирующих добавок (Al, Cr, Mn, Ni, Si) на растворимость карбонитридов в малоуглеродистых низколегированных сталях // ФММ. 2016. Т. 117. № 12. С. 1277–1287.
Дополнительные материалы отсутствуют.
Инструменты
Физика металлов и металловедение