Известия РАН. Энергетика, 2022, № 4, стр. 3-10
Расчет себестоимости производства водорода, получаемого по алюмоводной технологии
Э. П. Волков *
Федеральное государственное бюджетное учреждение науки Объединенный институт
высоких температур Российской академии наук
Москва, Россия
* E-mail: volkov_ep@ihed.ras.ru
Поступила в редакцию 14.02.2022
После доработки 14.04.2022
Принята к публикации 18.04.2022
- EDN: QKGINY
- DOI: 10.31857/S0002331022040082
Аннотация
Настоящий период развития электроэнергетики мира характеризуется стремлением научной общественности и руководства многих промышленно развитых стран осуществлять, в связи с происходящими климатическими изменениями, переход к так называемой низкоуглеродной энергетике. Определенную роль при этом играют решения отдельных крупных энергетических компаний, связанных с созданием нового сектора энергетики – водородной энергетики. Для этого последние 3–4 года широко разворачиваются работы по созданию безуглеродных технологий получения водорода. Среди последних находится и алюмоводная технология его производства. При этом важнейшей характеристикой любой технологии является себестоимость производимой продукции. В настоящей статье приводятся расчеты по определению себестоимости производства водорода, получаемого по алюмоводной технологии.
МОДЕЛЬ РАСЧЕТА
При расчете стоимости водорода учитываются составляющие капитальных и текущих (эксплуатационных) затрат по всей технологической цепочке его производства: восстановление алюминия методом электролиза из окиси алюминия с его последующим диспергированием и производством рабочего порошка, окисление порошка алюминия водой и получение водорода, компримирование водорода до рабочих параметров (20–90 МПа) и при необходимости использование остаточного низкопотенциального тепла для различных целей.
Технологическая схема получения водорода приведена на рис. 1.
Рис. 1.
Схема производства “безуглеродного” водорода на основе реакции гидротермального окисления алюминия.
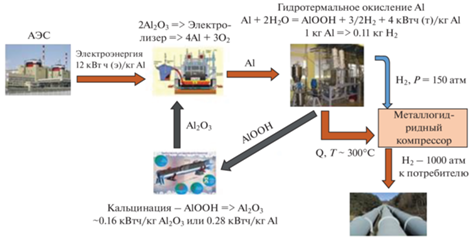
Важно отметить, что конечным продуктом является водород высокой чистоты (99.99%) с давлением в зависимости от требований заказчика – 20–40 или 90 МПа без углеродного следа.
Стоимость водорода рассчитывалась применительно к параметрам работы предлагаемой нами для сооружения пилотной установки производительностью по водороду 72 000 кг/год (хотя данное обстоятельство не принципиально, поскольку все расчеты проводятся на производительность 1 кг/час получаемого водорода в течение годового функционирования производства).
Стоимость водорода рассчитывается по известной методике, основанной на использовании коэффициента возврата капитала CRF, учитывающего среднюю стоимость капитала и номинальную продолжительность жизненного цикла актива в течение годовой эксплуатации оборудования.
Для расчета себестоимости C (USD/кг) используется выражение
где CAPEX – капитальные затраты, USD/кг/год; CRF – коэффициент возврата капитала, безразмерная величина; OPEX – эксплуатационные затраты, USD/кг/год.
Капитальные затраты оцениваются по их удельной годовой величине на оборудование по всей технологической цепочке с учетом коммуникаций и оборудования собственных нужд.
Основным оборудованием комплекса являются:
1. Электролизеры алюминия с коммуникациями;
2. Печь для кальцинации гидроокиси алюминия с коммуникациями;
3. Установка для диспергирования жидкого алюминия и получения исходного продукта (порошка) для реактора-окислителя;
4. Модуль гидроокисления алюминия и производства высокочистого водорода (99.99%);
5. Термосорбционный компрессор для сжатия водорода до его рабочего состояния (20–90 МПа);
6. Кроме того, необходимо учесть капитальные затраты на здания и сооружения технологического комплекса.
Основными эксплуатационными затратами в алюмоводной технологии являются затраты на используемую электроэнергию. Вторым источником затрат (малых по величине) являются затраты на расходуемую обычную (умягченную) воду, добавляемую в цикл для компенсации потерь при оборотном водоснабжении.
Эксплуатационные затраты состоят из шести основных компонентов:
1. Расход и стоимость электроэнергии на электролиз алюминия;
2. Расход и стоимость электроэнергии на кальцинацию гидроокиси алюминия, а также расход и стоимость природного газа и воды на эти цели;
3. Расход электроэнергии на диспергирование алюминия и производство порошка;
4. Эксплуатационные расходы на восполнение потерь алюминия при длительной эксплуатации контура его воспроизводства;
5. Эксплуатационные затраты на установки по окислению алюминия водой, выделения из пароводородной смеси водорода и повышения давления водорода до требуемых величин, в зависимости от целей его использования;
6. Кроме этого, необходимо учесть затраты на оплату эксплуатационного персонала, проведение ремонта, обслуживания оборудования и закупку необходимых для функционирования комплекса расходных материалов.
С учетом перечисленных затрат (капитальных и эксплуатационных) производится расчет стоимости 1 кг водорода в условиях годового функционирования производства.
Конкретные значения капитальных и эксплуатационных расходов взяты из данных реальной и многолетней эксплуатации установок по производству алюминия и алюминиевого порошка на Красноярском и Тайшетском алюминиевых заводах (компания “РУСАЛ”) и опыта работы большой стендовой установки ОИВТ РАН по непосредственно алюмоводной технологии и стендовой установки термосорбционного компримирования водорода.
СТОИМОСТЬ ЭЛЕКТРОЭНЕРГИИ
Стоимость электроэнергии зависит от генерирующего источника, от которого она поступает на энергетический комплекс, вырабатывающий водород.
При поступлении электроэнергии от действующих атомных электростанций (с шин АЭС) стоимость электроэнергии будет около 0.01 USD/кВт ч.
Электроэнергия, вырабатываемая ГЭС в первой и второй ценовых зонах, отпускается по цене от 0.01 до 0.02 USD/кВтч (перерасчет по курсу 64 руб./USD – 2019 г.) [1].
Поставка электроэнергии может осуществляться в рамках долгосрочных соглашений о закупке электроэнергии, производимой энергоустановками на возобновляемых источниках энергии (ВИЭ). В этом случае стоимость электроэнергии оценивается в интервале 0.09–0.22 USD/кВт ч [2].
Цены на оптовых рынках на электроэнергию в РФ (вне зависимости от типа генератора) лежат в интервале 0.03–0.035 USD/кВт ч (данные на октябрь 2019 г.) [3].
В дальнейших расчетах будем принимать, что электроэнергия поставляется производителям водорода по ценам 0.01 USD/кВт ч и 0.03 USD/кВт ч.
В будущем, в случае создания атомно-водородного энергетического комплекса (АВЭК), имеющего технологическую цепь АЭС + водородопроизводящий комплекс и выпускающим товарный водород, стоимость электроэнергии для производства водорода может быть около 0.01USD/кВт ч.
РАСЧЕТ СТОИМОСТИ ВОДОРОДА, ПОЛУЧАЕМОГО МЕТОДОМ ГИДРОТЕРМАЛЬНОГО ОКИСЛЕНИЯ АЛЮМИНИЯ
Расчеты выполняются с учетом данных, приведенных при производстве алюминия с использованием инертных анодов [4].
Использование инертных анодов для электролиза алюминия безусловно не является новой идеей. Впервые она была сформулирована Чарльзом Мартином Холлом в его знаменитом патенте 1886 г. В текущих условиях основным преимуществом инертных анодов является их экологичность. Предполагается, что использование в электролизе алюминия инертных анодов устранит выбросы окиси углерода и перфторуглеродных газов (CF4 и C2F6). Кроме того, будут исключены выбросы фтора и пыли во время замены анодов. В идеале исчезают все затраты, напрямую связанные с производством угольных анодов. Эта экономия может быть значительной, достигая 25–30% [5, 6].
ОК “РУСАЛ” в настоящее время является единственной в мире компанией, которая имеет опыт промышленного производства алюминия с использованием инертных анодов [7]. По информации, полученной от “РУСАЛа”, затраты на производство инертных анодов выше, чем затраты на производство углеродных анодов. Расход электроэнергии на электролиз с использованием инертных анодов также несколько выше, чем в процессе Холла–Эру. С другой стороны, ресурс инертных анодов существенно больше, чем ресурс их угольных аналогов. Утверждается, что в целом суммарные затраты электроэнергии и текущие расходы при эксплуатации анодов в обоих процессах оказываются примерно одинаковыми. Исходя из этого утверждения и в виду отсутствия детальной информации о технико-экономических характеристиках электролиза с инертными анодами, в последующих расчетах мы будем использовать хорошо известные данные для процесса Холла–Эру.
РАСЧЕТ КАПИТАЛЬНЫХ ЗАТРАТ НА ПРОИЗВОДСТВО ВОДОРОДА
Они состоят из суммы затрат на оборудование и коммуникации технологической цепочки:
1) Капитальные затраты на электролизеры с коммуникациями.
Известны удельные капитальные затраты в целом по различным алюминиевым заводам.
Удельные затраты для Тайшетского алюминиевого завода, как наиболее современного, построенного в РФ компанией “РУСАЛ” в 2019 г., составляют 2 USD/кг Al/год [8, 9]. Период эксплуатации алюминиевого завода оценивается величиной не менее 40 лет. В этих капитальных затратах присутствует и составляющая по зданиям. С учетом того, что в алюмоводной технологии окись алюминия циркулирует по замкнутому контуру, многие помещения и сооружения, связанные с приемом бокситов, их разгрузкой, транспортировкой внутри алюминиевого завода будут отсутствовать. Поэтому снижение удельных капитальных затрат из-за отсутствия этих зданий и сооружений можно отнести на капитальные затраты по зданиям установок окисления алюминия и компримирования водорода.
В этом случае удельные капитальные затраты на здания и сооружения отделений окисления алюминия и компримирования водорода входят в общие капвложения контура электролиза алюминия.
Тогда:
1) CAPEX · CRF установок по электролизу алюминия будет равным 0.05 USD/кг Al/год (с учетом затрат на здания и сооружения установок по окислению алюминия и компримирования водорода).
2) Капитальные затраты на установку по кальцинации гидроокиси с коммуникациями [10].
Удельные капитальные затраты на печь CAPEX = 0.006 USD/кг Al/год.
Срок эксплуатации 30 лет.
CAPEX · CRF = 0.0002.
3) Капитальные затраты на установку диспергирования алюминия с коммуникациями.
Удельные капитальные расходы на установку диспергирования равны 0.06 USD/кг Al/год [11].
Срок эксплуатации 20 лет.
CAPEX · CRF = 0.003.
4) На установку гидроокисления алюминия.
Удельные капитальные затраты равны 2.4 USD/кг H2 (данные ОИВТ РАН).
Срок службы 40 лет.
CAPEX · CRF = 0.06.
5) На термосорбционный компрессор водорода удельные капитальные затраты равны 2.0 USD/кг H2 (данные ОИВТ РАН).
Срок службы 30 лет.
CAPEX · CRF = 0.07.
6) Капитальные затраты на здания и сооружения установок по окислению алюминия и компримированию водорода учтены в CAPEX электролизного отделения.
Всего удельные капитальные затраты на блок установок, связанных с воспроизводством алюминия, равны
${{K}_{{Al}}} = {\text{ }}0.05 + 0.0002 + 0.003 = 0.0532\,\,{\text{USD/кг}}\,\,{\text{Al/год,}}$
или в пересчете на 1 кг водорода: 0.48 USD/кг H2/год, где
– первое слагаемое – удельные годовые амортизационные отчисления на 1 кг Al на электролизное отделение;
– второе слагаемое – удельные годовые амортизационные отчисления на 1 кг Al на установку кальцинации;
– третье слагаемое – удельные годовые амортизационные отчисления на 1 кг Al на установку диспергирования алюминия.
Капитальные расходы по установкам всего комплекса производства водорода равны:
где
– первое слагаемое – удельные капитальные затраты на блок установок, связанных с воспроизводством алюминия в перерасчете на 1 кг H2;
– второе слагаемое – удельные капитальные затраты на установку гидроокисления алюминия;
– третье слагаемое – удельные капитальные затраты на установку компримирования водорода.
РАСЧЕТ ЭКСПЛУАТАЦИОННЫХ ЗАТРАТ НА ПРОИЗВОДСТВО ВОДОРОДА
Учитывались следующие эксплуатационные затраты:
1. Расход и стоимость электроэнергии на электролиз алюминия.
Расход электроэнергии на электролиз алюминия колеблется в пределах 12–14 кВтч/кг Al (нами расход принимался равным 14 кВт ч/кг Al) или 126 кВт ч/кг H2 [5, 6, 9].
В зависимости от стоимости потребляемой электроэнергии ее стоимость на электролиз 1 кг алюминия оценивалась по двум вариантам:
a) потребляемая электроэнергия берется с шин генераторов атомной электростанции и ее стоимость равна 0.01 USD/кВт ч, в этом случае рассматривается атомно-водородный энергетический комплекс (АВЭК) – АЭС + технологические установки по производству и компримированию водорода. Конечным продуктом данного комплекса является водород;
b) электроэнергия поступает с оптового рынка, и в этом случае стоимость электроэнергии равна 0.03 USD/кВт ч.
В зависимости от вышеназванных вариантов стоимости электроэнергии, ее стоимость на электролиз 1 кг алюминия будет равна соответственно 0.14 USD/кг Al и 0.42 USD/кг Al.
2. Расход и стоимость электроэнергии на кальцинацию гидроокиси алюминия, а также расход и стоимость природного газа и воды для этой цели брались по данным эксплуатации установок на Красноярском алюминиевом заводе и рассчитывались также при двух вариантах стоимости электроэнергии (0.01 и 0.03 USD/кВт ч):
а) стоимость электроэнергии на кальцинацию гидроокиси алюминия на 1 кг алюминия, при удельной стоимости электроэнергии – 0.01 USD/кВтч равна 0.00033 USD и при 0.03 USD/кВт ч равна 0.001USD;
б) стоимость природного газа, расходуемого на кальцинацию 1 кг гидроксида алюминия равна 0.006 USD/кг Al;
в) стоимость воды 0.003 USD/кг Al.
Общая стоимость эксплуатационных затрат на кальцинацию гидроокиси алюминия равна – 0.01 USD/кг Al.
3. Расход электроэнергии на диспергирование алюминия и производство порошка.
По данным Красноярского алюминиевого завода расход электроэнергии на диспергирование алюминия равен 0.4 кВт ч/кг Al [11] и при стоимости электроэнергии 0.01 USD/кВт ч эксплуатационные затраты составят – 0.004 USD/кВт ч, а при стоимости 0.03 USD/кВт ч стоимость расходуемой на диспергирование 1 кг алюминия электроэнергии будет равна 0.012 USD/кВт ч.
4. Эксплуатационные расходы на восполнение потерь алюминия при длительной эксплуатации контура его воспроизводства.
Для поддержания материального баланса работы технологической установки в течение длительного периода времени придется компенсировать незначительные потери алюминия в замкнутом контуре установки. Такие потери нами оцениваются в 1% в год. Стоимость компенсации данных потерь оценивается величиной потерь – 0.004 USD/кг Al.
В целом эксплуатационные затраты в контуре воспроизводства алюминия при цене электроэнергии 0.01 USD/кВт ч равны:
5. Эксплуатационные затраты на установки по окислению алюминия водой, выделения из пароводородной смеси водорода и повышения давления водорода до требуемых величин в зависимости от целей его использования.
Эти процессы происходят в двух модулях:
непосредственно в алюмоводном реакторе с конденсатором пароводородной смеси и термосорбционном компрессоре водорода (ТСКВ).
Собственно расход электроэнергии на функционирование этих модулей составляет, по данным опытных (стендовых) установок ОИВТ РАН, соответственно: 0.365 кВт ч/кг H2 и 0.12 кВт ч/кг H2.
Стоимость эксплуатационных расходов на два модуля при цене электроэнергии 0.01 USD/кВт ч составит 0.005 USD/кг H2, при цене 0.03 USD/кВт ч – 0.015 USD/кг H2.
6. Ежегодные затраты на оплату эксплуатационного персонала, расходы на аноды и покупку расходных материалов (криолит, фторид алюминия и т.д.).
По данным компании “РУСАЛ” с учетом только воспроизводства в цикле алюминия, т.е. отсутствием по сравнению с заводом цепочки завоза, разгрузки и доставки по заводу глинозема, данные расходы приняты равными 0.16 USD/кг Al [4, 9].
Тогда эксплуатационные затраты на воспроизводство алюминия с учетом затрат на ремонт, персонал и покупку расходных материалов при цене электроэнергии 0.01 USD/кВт ч будут равны:
– первое слагаемое – затраты электроэнергии на электролиз алюминия;
– второе слагаемое – затраты на кальцинацию окиси алюминия;
– третье слагаемое – затраты на диспергирование жидкого алюминия;
– четвертое слагаемое – затраты на возмещение потерь алюминия в цикле (1% от общих затрат);
– пятое слагаемое – затраты на аноды, персонал и закупку расходуемых материалов.
При цене электроэнергии 0.03 USD/кВт ч эти затраты соответственно равны:
Учитывая, что из 1 кг алюминия получается 0.11 кг H2, в пересчете на водород эксплуатационные затраты по циклу воспроизводства алюминия, при стоимости электроэнергии 0.01 USD/кВт ч, равны: 0.318 × 9 = 2.86 USD/кг H2.
При стоимости электроэнергии 0.03 USD/кВт ч эксплуатационные затраты равны 0.606 × 9 = 5.45 USD/кг H2.
ПОЛНЫЕ ЭКСПЛУАТАЦИОННЫЕ ЗАТРАТЫ НА ВЕСЬ ТЕХНОЛОГИЧЕСКИЙ ЦИКЛ ПРОИЗВОДСТВА ВОДОРОДА
В этом случае они равны эксплуатационным затратам по установкам воспроизводства алюминия, пересчитанным на производство водорода и затратам на установки производства водорода и его компримирования, т.е.
и
при цене электроэнергии 0.03 USD/кВт чСТОИМОСТЬ ПРОИЗВОДСТВА ТОВАРНОГО ВОДОРОДА
В итоге стоимость производства товарного водорода (чистотой 99.99% и давлением до 90 МПа) будет равна при себестоимости электроэнергии 0.01 USD/кВт ч
Таким образом, значение стоимости водорода, получаемого по алюмоводной технологии с учетом его компримирования, равны 3.45 USD/кг H2 при стоимости электроэнергии 0.01 USD/кВт ч и 6.05 USD/кг H2 при стоимости электроэнергии 0.03 USD/кВт ч.
Список литературы
Русгидро. Годовой отчет за 2019 год. URL: http://ar2019.rusgydro.ru/sections/indwx.html
Dashboard for energy prices in the EU and main trading partners. URL: http://ec.europa.eu/ e-nergy/data-analysis/energy prices-and-costs/energy-prices-eu-member-states-and-main-trading-pertners.eu (дата обращения 24.05.2021).
Приказ Федеральной антимонопольной службы от 11 декабря 2019 г. № 1625/19 “Об утверждении цен (тарифов) на электрическую энергию (мощность), поставляемую в ценовых зонах оптового рынка субъектами оптового рынка. http://publication.pravo.gov.ru/Document/ vien/0001201912260062
Padamata S.K., Yasinskiy A.S., Polyakov P.V. Progress of Inert Anodes in Aluminium Industry: Review. Journal of Siberian Federal University Chemistry 1(2018) p. 18–30.
Kvande H., Drablos P.A. The Aluminium Smetling Process and Innovativ Alternative Technologies. JOEM 56 (2014) p. 523–532.
Thonstad J., Feellner P., Haarberg G.M. et al. Aluminium Electrolysis – Fundamentals of the Hall-Heroult Process. 3rd ed.- Dusseldorf, Germany: Aluminium – Verlag. MarKeting and Kommunikation GmbH. 2001. – 359 p.
РУСАЛ начал испытания электролизера с инертными анодами нового поколения. Аргументы и факты: Красноярск. 10.06.2020. URL: https://krsk.aif.ru/money/rusal_nacal_ is-pytaniya_electrolizera_s_inertnymi_anodami_novogo_pokoleniya (дата обращения 24.05.2021).
Обухова Е. За секунду до алюминия // Интернет-издание “Эксперт”. URL: https://expert.ru/ expert/2021/13/za-sekundu-do-alyuminiya/
UC Rusal Financial Results Presentation. 1H2020.13.08.2020 URL: https://rusal.ru/en/investors/ financial-stat/presentations.
Шишкин С.Ф. Циклонная печь кальцинации // Новые огнеупоры. 2015. № 4. С. 12–15.
Волочко А., Овчинников В., Садоха М. Технологии и оборудование переработки алюминиевых отходов // Наука и инновации. 2012. № 9 (115). С. 28–37.
Дополнительные материалы отсутствуют.
Инструменты
Известия РАН. Энергетика