Известия РАН. Энергетика, 2022, № 5, стр. 36-48
Оптимизационные исследования парогазовой установки с внутрицикловой газификацией бурых углей на основе различных моделей газогенератора
А. М. Клер 1, И. Г. Донской 1, *, А. Ю. Маринченко 1
1 Федеральное государственное бюджетное учреждение науки Институт систем энергетики
им. Л.А. Мелентьева СО РАН
Иркутск, Россия
* E-mail: donskoy.chem@mail.ru
Поступила в редакцию 27.04.2022
После доработки 14.06.2022
Принята к публикации 16.06.2022
- EDN: IMFNHZ
- DOI: 10.31857/S0002331022050053
Аннотация
В работе приводятся результаты расчетных исследований перспективной энергетической установки с газификацией углей. Обсуждаются варианты включения физико-химических моделей, описывающих реагирование твердого топлива, в общую схему оптимизации установок. С помощью кинетико-термодинамической модели получены характеристики процесса газификации выбранных углей в широком диапазоне условий. Полученные данные используются для оптимизации узла газификации в составе парогазовой установки.
ВВЕДЕНИЕ
ПГУ с внутрицикловой газификацией угля (ВЦГУ) являются перспективными установками, обладающими высокой энергетической, экономической и экологической эффективностью [1]. Их технологические схемы состоят из большого числа разнотипных элементов, объединенных различными материальными и энергетическими потоками. Поэтому выбор параметров ПГУ с ВЦГУ является сложной задачей, качественно решить которую можно лишь с использованием методов математического моделирования и оптимизации. Для решения таких задач в Институте систем энергетики им. Л.А. Мелентьева СО РАН были разработаны методы автоматизации математического моделирования сложных теплоэнергетических установок, оптимизации их схем и параметров, построены математические модели элементов и схем теплоэнергетических установок различных типов, проводились оптимизационные исследования ряда теплоэнергетических установок различного уровня мощности [2].
Одним из наиболее важных элементов ПГУ с ВЦГУ является газогенератор, в котором происходит образование горючего генераторного газа.
При расчете газогенераторного процесса возникает проблема выбора подходящей математической модели, которая с необходимой точностью учитывала бы влияние важных факторов. Обычно в подобных исследованиях используется традиционная термодинамическая модель конечного равновесия [3, 4]. Такой подход имеет ограниченную применимость, поскольку равновесие достигается только при достаточно высоких температурах и больших временах реагирования. Вместе с тем повышение сложности математической модели газогенератора приводит к ее практической неприменимости в условиях вычислительной оптимизации теплоэнергетических установок, когда требуется большое число обращений к этой модели. В такой ситуации требуется соблюдение баланса между детальностью модели (возможностью определить ряд важных характеристик процесса газификации) и ее вычислительной сложностью.
В настоящей работе ставится задача на основе оптимизационных исследований провести сравнение двух математических моделей одноступенчатых газогенераторов с газификацией в спутном потоке нагретой паровоздушной среды и определить их влияние на оптимальные технико-экономические показатели и основные параметры ПГУ с ВЦГУ при использовании различных типов углей.
ИСПОЛЬЗОВАНИЕ МОДЕЛИ ГАЗОГЕНЕРАТОРА В СОСТАВЕ ЭНЕРГЕТИЧЕСКОЙ УСТАНОВКИ
Реактор для термохимической конверсии всегда работает в составе энергетической или энерготехнологической установки, а значит его рабочие режимы должны удовлетворять условиям согласованной работы с другими узлами (топливоподготовкой, системой шлакоудаления и очистки газов, котлами-утилизаторами, двигателями, химическими реакторами). Для этого необходимо учитывать график нагрузки, инерционность процесса, зависимость характеристик процесса от расхода топлива, возможности регулирования температуры в реакционной зоне, требования к параметрам рабочих тел и теплоносителей и т.д. Для оптимизации режимов работы энергоустановки требуется многократное обращение к ее математической модели включая модель реактора, поэтому математическая модель реактора должна давать решение за разумное вычислительное время [5]. Особенно важно это при использовании эффективных градиентных методов оптимизации, в которых производные целевой функции и ограничений определяются конечно-разностным способом [6, 7]. Тогда термогидродинамические модели, включающие детальное описание механических, теплофизических и химических процессов в трехмерной области, оказываются совершенно неподходящими для целей оптимизации. Более широко используются эмпирико-балансные модели и равновесные термодинамические модели [3, 8, 9].
Разные математические модели процессов конверсии угля могут отличаться не просто набором коэффициентов, но и классом задач, которые они позволяют сформулировать. Эмпирико-балансные модели сводятся к решению алгебраических уравнений; равновесные термодинамические модели сводятся к задачам нелинейного программирования; кинетические модели дают системы обыкновенных дифференциальных уравнений; модели процессов переноса это, как правило, уравнения в частных производных; моделирование энергетических установок требует решения задач оптимизации структуры и состояния графа с разнородными вершинами. Аналитическое исследование этих задач применительно к реальным условиям практически невозможно. Поэтому во всех случаях требуются разные численные методы, а стыковка моделей на разных уровнях рассмотрения не всегда может быть произведена полноценно.
При исследовании условий оптимальности и возможностей управления реакторами для термохимической конверсии твердых топлив часто используются методы, разработанные для процессов химической технологии. В работах [10, 11] обосновывается концепция многомасштабного моделирования химико-технологических и теплотехнических процессов на основе моделей пониженной размерности (Reduced Order Models, ROM). Редукция моделей должна проводиться при соблюдении условия о сохранении “области надежности” (trust region), т.е. области параметров, в пределах которой упрощенная модель сохраняет свои аппроксимирующие свойства. Редукция может проводиться разными путями, как исходя из физического анализа задачи (пренебрежение явлениями/эффектами из соображений симметрии, анализа размерностей и масштабов), так и с помощью подходящих методов регрессии результатов детального моделирования (полиномиальная аппроксимация, факторный анализ, principal component analysis, look up-table approach и т.д.). Если неполная аппроксимация оказывается намного эффективнее в вычислительном плане, возможно применение специальных фильтров или вариаций метода штрафных функций [12]. Таким образом, можно поставить задачу о выборе оптимально упрощенной модели процесса на основе его детальной математической модели при ограничениях на погрешность аппроксимации и мощность вычислительных ресурсов. Критерием оптимизации может быть, например, число обращений к детальной модели или общее время оптимизации для модельных задач.
Разработка упрощенных моделей для этих процессов сводится к использованию регрессионных методов [13–15] или представлению реактора в виде связанного набора реакторов идеального перемешивания/идеального вытеснения [16, 17]. Для упрощения субмоделей термохимических превращений часто применяют равновесные термодинамические модели и их сочетания с моделями гетерогенной химической кинетики [18, 19]. Полученные упрощенные модели нуждаются в тщательной верификации и валидации (путем сравнения с результатами расчетов на детальных моделях и с экспериментальными данными). Верифицированная модель пониженной размерности, позволяющая надежно оценивать характеристики процесса при многократном сокращении вычислительного времени, может быть использована для полноценной оптимизации энергетических установок. Подобные подходы и модели используются при решении задач оптимизации режимов сжигания и газификации твердого топлива в составе ТЭС. В настоящей работе используется табуляция и интерполяция режимов.
ТЕРМОДИНАМИЧЕСКАЯ МОДЕЛЬ ГАЗОГЕНЕРАТОРА
При газификации твердого топлива протекает огромное число химических реакций, однако при высоких температурах и достаточно больших временах пребывания можно считать, что реакционная система достигает состояния химического равновесия. Тогда состав продуктов определяется экстремумом функции состояния. Обычно для практических расчетов достаточно хорошим приближением является идеальность газовой и конденсированных фаз. Тогда задача расчета химического состояния газовой фазы выглядит следующим образом [20]:
Найти ${{{\mathbf{n}}}^{{eq}}} = {\text{ arg min}}G\left( {{\mathbf{n}},T} \right),$
при условиях:
Индикаторами эффективности режимов являются адиабатическая температура процесса, выход твердого остатка и химический КПД газификации, равный отношению теплот сгорания генераторного газа и топлива, из которого он был получен:
Для равновесных расчетов не требуются сведения о геометрии аппарата, размерах частиц и временах их пребывания в реакционной зоне, поскольку равновесное состояние не зависит от пути его достижения. С этим же связаны и недостатки термодинамической модели, в первую очередь – переоценка степени конверсии топлива. Для учета кинетических ограничений на достижимость равновесного состояния мы используем гибридную модель, которая в явном виде учитывает скорости гетерогенных реакций топлива.
ГИБРИДНАЯ МОДЕЛЬ ГАЗОГЕНЕРАТОРА
В настоящей работе используется вычислительный инструмент, оценивающий эффективность режимов работы газогенератора (подробно описанный в работах [25, 26]). За счет ряда упрощений модели такие расчеты можно проводить в широком диапазоне условий за разумное вычислительное время, при этом сохранять важные детали (зависимость степени конверсии топлива от состава атмосферы, времени пребывания и среднего размера частиц). Уравнение теплового баланса частиц топлива в переменном тепловом поле записывается следующим образом:
Здесь z – пространственная координата (длина реакционной зоны), м; U – скорость движения частицы, м/с; mp – масса частицы, кг; Tp – температура частицы, К; cp – теплоемкость частицы, Дж/кг/К; α – коэффициент теплоотдачи, Вт/м2/К; Sp – внешняя поверхность частицы, м2; ε – степень черноты частицы; σ – постоянная Стефана-Больцмана, Вт/м2/К4; Tg – температура газа, К; Tw – температура стенки, К; rj – скорость физико-химического процесса, связанного с частицей, кг/с (сушка, пиролиз, реакции с газами); Qj – тепловой эффект, Дж/кг.
Скорость сушки rdr рассчитывается по-разному в зависимости от температурных условий:
Скорость пиролиза rpyr зависит от температуры по аррениусовскому закону:
Гетерогенные реакции протекают согласно уравнениями диффузионной кинетики:
Здесь Cg – концентрация газообразного окислителя (O2, CO2, H2O); kg – предэкспоненциальный множитель гетерогенной реакции, м/с; Eg – энергия активации, Дж/моль; NuD – диффузионное число Нуссельта; Dg – коэффициент диффузии газообразного окислителя, м2/с; dp – средний размер частицы, м. Тепловые эффекты Qj оцениваются из термохимических данных [21]. Коэффициенты диффузии Dg рассчитываются из данных [27]: для O2 и Н2О – как бинарные коэффициенты диффузии в смеси с СО2 или N2. Скорость движения частиц считается равной скорости движения газа, которая определяется из уравнения неразрывности. Состав газа в каждом сечении считается равновесным при фиксированной степени превращения топлива (т.е. для газовой фазы решается равновесная задача, как в предыдущем разделе). Для поиска стационарного решения используется итерационная схема: скорость конверсии топлива рассчитывается с помощью системы обыкновенных дифференциальных уравнений для изменения массы частиц при заданном распределении температур; с помощью термодинамической модели вычисляется тепловыделение и состав газовой фазы в каждом расчетном элементе; затем решается стационарная задача переноса теплоты с учетом источников теплоты. Итерации завершаются, когда распределение температур перестает ощутимо изменяться.
Расчеты проводятся для цилиндрической реакционной зоны диаметром 3 м и длиной 9 м, рабочее давление около 15 атм. Расход топлива составляет около 50 кг/с, средний размер частиц 0.1 мм. Газифицирующим агентом является смесь воздуха и водяного пара (температура 655 К). Варьируемыми параметрами являются удельный расход воздуха (1–6 кг/кг топлива), удельный расход пара (0–0.1 кг/кг топлива), а также расход топлива (от 80 до 120% от номинальной нагрузки). Характеристиками процесса газификации являются температура и состав выходящего газа, доля механического недожога и химический КПД. Расчетные данные преобразовывались в таблицы, которые затем использовались при оптимизации парогазовой установки. Прямые расчеты показали, что интерполяция достаточно хорошо (в пределах 1.5%) определять характеристики процесса газификации в промежуточных режимах.
ТЕПЛОВАЯ СХЕМА И МАТЕМАТИЧЕСКАЯ МОДЕЛЬ ПАРОГАЗОВОЙ УСТАНОВКИ С ВНУТРИЦИКЛОВОЙ ГАЗИФИКАЦИЕЙ УГЛЯ
Рассматриваемая установка (рис. 1) состоит из трех блоков: газификации, газотурбинного и паротурбинного. Основными элементами блока газификации являются: подсистема подготовки топлива, собственно газогенератор, состоящий из реакционной камеры, в которой происходит процесс газификации угля и конвективной шахты, в которой продукты газификации охлаждаются, отдавая свое тепло воде или пару. Газотурбинный блок включает: воздушный компрессор, камеру сгорания и газовую турбину, находящуюся на одном валу с компрессором. Паротурбинный блок включает в качестве основных элементов: котел-утилизатор, в который поступают выхлопные газы газовой турбины (в котле-утилизаторе располагаются пароперегревательные, испарительные и экономайзерные поверхности нагрева), паровую турбину и конденсатор.
Рис. 1.
Расчeтная схема ПГУ с газификацией угля: 1 – газогенератор, 2 – дожимной компрессор, 3 – топка газогенератора, 4–8 – котел-утилизатор на продуктах газификации, 9 – камера сгорания газовой турбины, 10 – воздушный компрессор, 11 – газовая турбина, 12–19 – котел-утилизатор на продуктах сгорания, 20–22 – отсеки паровой турбины, 23 – конденсатор, 24 – циркуляционный насос системы технического водоснабжения, 25 – конденсатный насос, 26–28 – золо- и сероочистка.
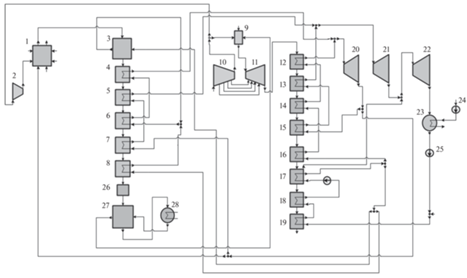
Для построения математических моделей ПГУ с ВЦГУ был использован программно-вычислительный комплекс “Система машинного построения программ СМПП-ПК”, позволяющий на основе заданных математических моделей элементов и технологических связей между ними строить модель установки в целом [7]. В данной работе были использованы ранее созданные в ИСЭМ СО РАН математические модели: камер сгорания газовых турбин, основанные на энергетических и материальных балансах; газоводяных и газопаровых радиационных и конвективных теплообменников, в основе которых лежат нормативные методы теплового, аэродинамического и гидравлического расчетов котельных агрегатов, а также элементы их прочностного расчета; паровых, газовых турбин и компрессоров, основанные на их расчетах по отсекам, и др.
Результаты расчетов, проведенных с помощью гибридной модели, хранятся в виде массивов данных, которые используются в модели установки следующим образом. При расчете узла газификации вызывается подпрограмма, которая, используя значения входящих параметров (расхода и температуры дутьевого воздуха), производит интерполяцию по рассчитанным точкам и выдает информацию о выходящих потоках химических компонентов газа, степени использования топлива и температуре продуктов газификации.
С помощью СМПП была разработана математическая модель парогазовой установки с внутрицикловой газификацией угля. Модель включает 784 исходных, 19 итерационно-уточняемых и 981 вычисляемых параметров.
Для оптимизационных исследований использовался разработанный в ИСЭМ СО РАН эффективный метод ступенчатой оптимизации, основанный на том, что точное решение системы уравнений, описывающих ПГУ, достигается в оптимальной точке [26]. При этом все итерационные процессы вынесены с уровня математических моделей на уровень оптимизации. Такой подход позволяет проводить оптимизацию с большой скоростью и точностью, определяя диапазон оптимальных значений параметров установки и ее технико-экономических показателей.
Всего для ПГУ с газификацией угля оптимизировался 57 параметр. При этом учитывалось 137 ограничений-неравенств, формирующих область, в которой работа элементов установки физически и технически допустима.
Капиталовложения в ПГУ с ВЦГУ определялись по методике, представленной в [29]. Все затраты на установку разбиваются на несколько составляющих: зависящие от электрической мощности, зависящие от количества тепла, отводимого от конденсаторов паровых турбин, зависящие от стоимости основного теплоэнергетического оборудования, затраты на строительную часть и зависящие от объема потребляемого топлива. Стоимость газогенератора принималась пропорционально расходу топлива, стоимость турбомашин и насосов – их мощности, а стоимость теплообменников – пропорционально их массе или площади теплопередающей поверхности.
В расчетах приняты следующие исходные стоимостные характеристики элементов оборудования: постоянная составляющая капиталовложений – 8000 тыс. долл., удельная стоимость блока газификации – 4000 тыс. долл./(кг у.т./с), удельная стоимость металла труб теплообменников из перлитной стали – 100 долл./м2, из углеродистой стали – 80 долл./м2, из аустенитной стали – 120 долл./м2, удельная стоимость воздушных компрессоров – 54 долл./кВт, газовой турбины – 72 долл./кВт, паровой турбины – 60 долл./кВт. Число часов использования установленной мощности ПГУ принималось равным 7000.
Температура газов на входе в газовую турбину для всех вариантов принималась одинаковой и равной 1427°С. Расчеты проводились для углей Березовского, Мугунского и Уртуйского месторождений [30]. В расчете использовались две математические модели газогенератора – модель конечного термодинамического равновесия и модель из работ [25, 26]. Соответственно, в зависимости от используемой модели газогенератора решались три вида задач:
Вариант 1. Используется модель конечного термодинамического равновесия с фиксированной долей недожога угля.
Вариант 2. Используется модель конечного термодинамического равновесия с расчетом величины недожога угля с помощью зависимостей, полученных по модели из работ [25, 26].
Вариант 3. Используется модель с учетом неравновесного состава газа на выходе (модель из работ [25, 26]).
Для каждого варианта были проведены оптимизационные расчеты по критерию максимума КПД и минимума цены электроэнергии при заданной внутренней норме возврата капиталовложений (в расчетах принималась равной 0.15) [28, 29]. Причем, задача минимизации цены электроэнергии решалась при двух значениях цены топлива – 100 и 400 долл./т у.т. Максимальная полезная мощность установки во всех расчетах принималась равной 400 МВт.
РЕЗУЛЬТАТЫ ОПТИМИЗАЦИИ УСТАНОВКИ
Результаты представлены в табл. 2. Основные технико-экономические параметры показаны на рис. 2–4. Как видно из представленных результатов, данные, полученные как при использовании разных моделей газогенератора, так и при использовании разных углей, значительно отличаются.
Рис. 3.
Результаты расчетов на минимум цены электроэнергии при цене топлива 100 долл./т у.т.: (а) цена электроэнергии, (б) удельные капиталовложения, в) КПД.
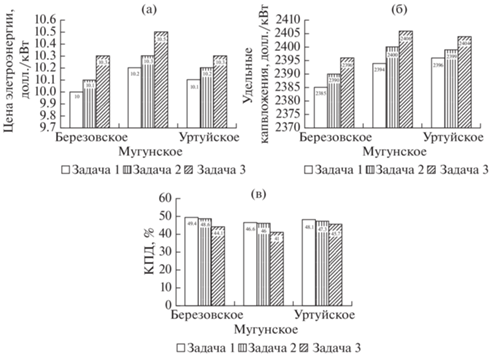
Рис. 4.
Результаты расчетов на минимум цены электроэнергии при цене топлива 400 долл./т у.т.: (а) цена электроэнергии, (б) удельные капиталовложения, (в) КПД.
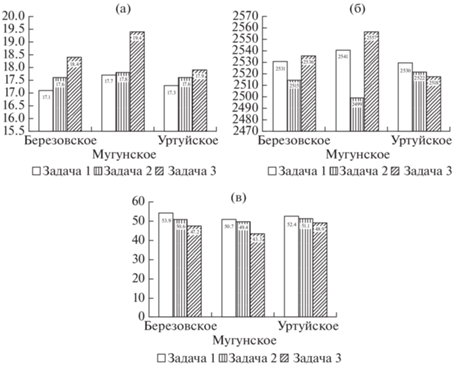
Оптимизационные расчеты по определению максимума КПД показали (рис. 2), что самые высокие значения КПД получаются в варианте 1 (равновесная модель газогенератора с фиксированной долей недожога угля). В варианте 2 (табл. 1), в котором доля недожога угля определялась по модели с учетом неравновесного состава газа как функция удельного расхода воздуха на газификацию и температуры воздуха на входе, КПД установки на 1.6–2% ниже, чем в варианте 1. На 12–18% возрастает удельный расход воздуха, на 20% возрастает температура газа на выходе. Меняется состав продуктов газификации. Возрастает расход СО2 на 28–30%, N2 на 18%, H2O на 9% и уменьшается расход СО на 15–20%. Полностью уходит метан из состава газа. На 20% уменьшается низшая теплота сгорания продуктов газификации. При этом расход уноса возрастает незначительно. Это связано с тем, что используемые в варианте 2 зависимости более точно отражают связь между температурой продуктов газификации и потерями исходного топлива, связанными с недожогом. С точки зрения решения задачи максимизации КПД это приводит к повышению температуры продуктов газификации и понижению их калорийности, но позволяет избежать значительных потерь топлива с уносом. Таким образом, использование этих зависимостей позволяет уточнить полученные технико-экономические показатели установки даже при использовании модели конечного термодинамического равновесия.
Таблица 1.
Характеристики рассматриваемых углей
Месторождение | Состав рабочей массы топлива, % | Низшая теплота сгорания, МДж/кг | ||||||
---|---|---|---|---|---|---|---|---|
$W_{t}^{r}$ | Ar | Sr | Cr | Hr | Nr | Or | ||
Березовское | 33 | 4.7 | 0.2 | 44.2 | 3.1 | 0.4 | 14.4 | 15.66 |
Мугунское | 22 | 15.6 | 0.9 | 46 | 3.6 | 0.9 | 11 | 17.29 |
Уртуйское | 29.5 | 8.8 | 0.3 | 46.9 | 3 | 0.5 | 11 | 16.83 |
Таблица 2.
Результаты расчетов (цена топлива – 100 долл./т у.т.)
Уголь Березовского месторождения | Уголь Мугунского месторождения | Уголь Уртуйского месторождения | ||||||||||||||||
---|---|---|---|---|---|---|---|---|---|---|---|---|---|---|---|---|---|---|
max КПД | min Cel | max КПД | min Cel | max КПД | min Cel | |||||||||||||
1 | 2 | 3 | 1 | 2 | 3 | 1 | 2 | 3 | 1 | 2 | 3 | 1 | 2 | 3 | 1 | 2 | 3 | |
Расход топлива в ГГ, кг/с | 44.7 | 46.1 | 49 | 51.7 | 52.6 | 57.9 | 43.3 | 44.5 | 48.8 | 49.7 | 50.3 | 56.4 | 42.8 | 44.4 | 46.2 | 49.4 | 50.2 | 52 |
Температура газа на выходе ГГ, °С | 950 | 1180 | 958 | 950 | 1123 | 1013 | 950 | 1179 | 1059 | 950 | 1113 | 1066 | 950 | 1195 | 999 | 950 | 1129 | 1020 |
Удельный расход воздуха на газификацию угля, кг/кг | 2.1 | 2.4 | 2.4 | 2.2 | 2.4 | 2.5 | 2.2 | 2.6 | 2.7 | 2.4 | 2.7 | 2.7 | 2.2 | 2.7 | 2.7 | 2.4 | 2.7 | 2.7 |
Расход СО2 на выходе, кг/с | 26.9 | 37.4 | 28.5 | 32.7 | 42 | 34.2 | 20.9 | 31.1 | 24 | 25.8 | 34.3 | 27.8 | 23.8 | 35.3 | 25.2 | 29.2 | 38.9 | 28.6 |
Расход СН4 на выходе, кг/с | 0.23 | 0 | 0.02 | 0.05 | 0 | 0 | 0.3 | 0 | 0 | 0.05 | 0 | 0 | 0.26 | 0 | 0 | 0.05 | 0 | 0 |
Расход N2 на выходе, кг/с | 69.7 | 84.3 | 88.9 | 84.9 | 97.1 | 110.9 | 73.1 | 89.1 | 99.4 | 88.7 | 101.4 | 115.3 | 72.7 | 89.3 | 93.5 | 88.3 | 101.5 | 107.3 |
Расход СО на выходе, кг/с | 27.9 | 22.4 | 29.2 | 31.7 | 26.3 | 34.7 | 30.5 | 26.1 | 32.6 | 34.4 | 30.4 | 37.6 | 30.1 | 24.3 | 33 | 34 | 28.4 | 373 |
Расход H2S на выходе, кг/с | 0.09 | 0.1 | 0.1 | 0.1 | 0.1 | 0.12 | 0.4 | 0.4 | 0.44 | 0.45 | 0.46 | 0.5 | 0.13 | 0.14 | 0.15 | 0.15 | 0.16 | 0.17 |
Расход Н2О на выходе, кг/с | 8.6 | 9.48 | 15.6 | 10.7 | 11.3 | 19.8 | 5.7 | 6.3 | 13.2 | 7.2 | 7.6 | 15.3 | 6.7 | 7.6 | 13 | 8.3 | 9 | 15.2 |
Расход Н2 на выходе, кг/с | 2.3 | 2.4 | 1.87 | 2.7 | 2.7 | 2.1 | 2.1 | 2.3 | 1.6 | 2.5 | 2.5 | 1.9 | 2.2 | 2.3 | 1.8 | 2.5 | 2.5 | 2 |
Расход уноса на выходе, кг/с | 2.7 | 2.8 | 4 | 3.1 | 3.2 | 4.5 | 8.7 | 11.4 | 10.2 | 10 | 12.3 | 11.7 | 4.9 | 5.1 | 4.7 | 5.6 | 5.7 | 5.2 |
Низшая теплота сгорания газа, МДж/м3 | 4.5 | 3.6 | 3.5 | 4.2 | 3.6 | 3.3 | 4.7 | 3.8 | 3.5 | 4.4 | 3.8 | 3.5 | 4.6 | 3.6 | 3.7 | 4.3 | 3.6 | 3.6 |
Давление газа перед ГТ, МПа | 1.9 | 1.9 | 1.3 | 1 | 1 | 1.2 | 1.9 | 1.9 | 1.3 | 1 | 1 | 1.1 | 1.9 | 1.9 | 1.3 | 1 | 1 | 1.2 |
Температура газа на выходе ГТ, °С | 700 | 672 | 749 | 838 | 804 | 782 | 697 | 669 | 746 | 835 | 802 | 783 | 699 | 672 | 746 | 836 | 803 | 778 |
Давление острого пара, кг/см2 | 15.2 | 14.4 | 14.4 | 15.2 | 14.4 | 14.4 | 15.2 | 14.4 | 14.4 | 15.2 | 14.4 | 14.4 | 15.2 | 14.4 | 14.4 | 15.2 | 14.4 | 14.4 |
Температура острого пара, °С | 500.2 | 500 | 445.1 | 483.4 | 498.8 | 435.2 | 500.1 | 414.5 | 471.5 | 483.7 | 410.8 | 439.3 | 500.1 | 497.5 | 475.2 | 483.1 | 496.9 | 467 |
Расход острого пара, кг/с | 112.6 | 115.5 | 112.7 | 140 | 129.6 | 134.4 | 112.4 | 121.2 | 120.7 | 140.5 | 138.7 | 136 | 112.4 | 116.4 | 119.1 | 140.2 | 130.7 | 130.3 |
Давление пара промперегрева, МПа | 2.8 | 2.7 | 3.2 | 3 | 2.6 | 3.2 | 2.8 | 4.5 | 3 | 3 | 3.6 | 2.2 | 2.8 | 2.7 | 2.9 | 2.9 | 2.6 | 2.8 |
Температура пара промперегрева, °С | 532.3 | 536 | 536.1 | 525.5 | 531.1 | 536.1 | 532.4 | 543.1 | 536.4 | 526.5 | 536.2 | 510.7 | 532.5 | 535.8 | 536.8 | 525.6 | 530.5 | 533.9 |
Давление пара контура низкого давления, МПа | 0.6 | 0.6 | 0.6 | 0.6 | 0.6 | 0.6 | 0.6 | 0.6 | 0.6 | 0.6 | 0.6 | 0.6 | 0.6 | 0.6 | 0.6 | 0.6 | 0.6 | 0.6 |
Расход пара контура низкого давления, кг/с | 111.7 | 114.5 | 110.5 | 139.2 | 128.6 | 133.3 | 111.6 | 120.4 | 119.7 | 139.6 | 137.8 | 136.4 | 111.5 | 115.5 | 117 | 139.5 | 129.8 | 128.1 |
Полезная мощность ГТУ, МВт | 227 | 222 | 210 | 200 | 211 | 213 | 227 | 227 | 210 | 199 | 212 | 212 | 227 | 221 | 220 | 199 | 210 | 216 |
Полезная мощность ПТУ, МВт | 176 | 181 | 169 | 203 | 192 | 190 | 176 | 176 | 193 | 204 | 192 | 192 | 176 | 182 | 183 | 205 | 194 | 188 |
В варианте 3, в котором используется модель газогенератора с учетом неравновесного состава газа на выходе (модель из работ [25, 26]), температура воздуха на 5–10% больше, чем в варианте 1. Удельный расход воздуха сопоставим со значениями варианта 2. Изменился состав продуктов газификации. Так, расход СО2 вырос на 6–12%, N2 на 20%, СО на 10% относительно решений, полученных для варианта 1. Значительно вырос расход воды на выходе – на 45–55%, и уменьшился расход Н2 (на 10–15%), возрос расход уноса на 5–5%.
Следует отметить влияние типа используемого угля. Так, в вариантах 1 и 2 самые большие значения КПД получаются для угля Березовского месторождения. Для угля Уртуйского месторождения, у которого более низкая влажность, но более высокая зольность, в этих вариантах КПД ниже на 1.5–2%. Самые низкие значения КПД получились для угля Мугунского месторождения, у которого при относительно низкой влажности самый высокий показатель зольности (в 2 раза выше, чем у Уртуйского, и в 3 раза, чем у Березовского). Решение оптимизационной задачи для варианта 3 показало немного другой результат. Так, самое высокое значение КПД получилось для угля Уртуйского месторождения, а самое низкое – для Мугунского. Возможно это связано с тем, что неравновесная модель более точно описывает процессы частичного окисления горючих компонентов и потери топлива с недожогом. Поэтому более низкая влажность и более высокая калорийность угля Уртуйского месторождения позволяет получить более высокие значения КПД, чем Березовского, даже при более высокой зольности.
Переход от решения задачи максимизации КПД к минимизации цены электроэнергии приводит к снижению капиталовложений и КПД (рис. 3). В то же время для разных вариантов наблюдаются такие же тенденции изменения состава продуктов и параметров газификации, как и при максимизации КПД. Что касается установки в целом, то следует отметить существенное уменьшение давления на входе в газовую турбину (почти в 2 раза) и повышение температуры на выходе из нее (на 100–150°С). Следствием этого является перераспределение выработки электроэнергии между газовой и паротурбинной частями установки. При решении задачи на максимум КПД превышение в выработке электроэнергии на ГТУ составляет 15–30% по сравнению с ПТУ, а при минимизации цены электроэнергии оно не превышает 10%, а для некоторых задач и углей выработка на ПТУ больше чем на ГТУ. Это может быть связано с тем, что для минимизации капиталовложений в установку более выгодным является уменьшить капиталовложения в более дорогую газовую турбину и больше загрузить относительно дешевую паровую.
Увеличение стоимости топлива до 400 долл./т у.т. приводит (рис. 4) к увеличению КПД на 2.5–3.5% для всех рассматриваемых оптимальных решений. Также перераспределение долей ГТУ и ПГУ в выработке станций становится ближе к оптимальному решению полученному при максимизации КПД и для всех решений выше на 10–14% на ГТУ.
Использование более точной модели газогенератора оказывает существенное влияние как на оптимальные параметры установки, так и на ее технико-экономические показатели. Это свидетельствует о целесообразности применения разработанной модели газогенератора для оптимизационных исследований ПГУ с внутрицикловой газификацией угля.
Работа выполнена в рамках проекта государственного задания (№ FWEU-2021-0001) программы фундаментальных исследований РФ на 2021–2030 гг.
Список литературы
Филиппов С.П., Кейко А.В. Газификация угля: на перепутье. Технологические факторы // Теплоэнергетика. 2021. № 3. С. 45. https://doi.org/10.1134/S0040363621030048
Клер А.М. (ред.) Эффективные методы схемно-параметрической оптимизации сложных теплоэнергетических установок: разработка и применение. Новосибирск: Академические изд-во “Гео”, 2018. 145 с.
Olivieri A., Ravelli S. Cogasification of Coal and Biomass in an Integrated Gasification Combined Cycle Power Plant: Effects on Thermodynamic Performance and Gas Composition // Journal of Energy Engineering. 2020. V. 146. № 6. P. 04020071. https://doi.org/10.1061/(ASCE)EY.1943-7897.0000716
Wang Y., Wang J., Luo X., Guo S., Lv J., Gao Q. Dynamic modelling and simulation of IGCC process with Texaco gasifier using different coal // System Science & Control Engineering. 2015. V. 3. № 1. P. 198. https://doi.org/10.1080/21642583.2015.1010046
Van den Berg J. Model reduction for dynamic real-time optimization of chemical processes. Proefschrift. Netherlands: Technische Universiteit Delft, 2005. 167 p.
Kler A.M., Zharkov P.V., Epishkin N.O. Parametric optimization of supercritical power plants using gradient methods // Energy. 2019. V. 189. P. 116230. https://doi.org/10.1016/j.energy.2019.116230
Клер А.М., Деканова Н.П., Щеголева Т.П. и др. Методы оптимизации сложных энергетических установок. Новосибирск: Наука, 1993. 116 с.
Wang H., Chen Z., Zhang B., Zeng L., Li Z., Zhang X., Fang N. Thermal-calculation method for entrained-flow coal gasifiers // Energy. 2019. V. 166. P. 373. https://doi.org/10.1016/j.energy.2018.10.004
Lu Y., Li Z., Zhang M., Huang C., Chen Z. The application of thermal-calculation methods in the design and syngas prediction of entrained-flow coal gasifiers // Energy Conversion and Management. 2021. V. 245. P. 114627. https://doi.org/10.1016/j.enconman.2021.114627
Biegler L.T., Lang Y., Lin W. Multi-scale optimization for process systems engineering // Computers & Chemical Engineering. 2014. V. 60. P. 17. https://doi.org/10.1016/j.compchemeng.2013.07.009
Biegler L.T. New nonlinear programming paradigms for the future of process optimization // AIChEJ. 2017. V. 63. № 3. P. 1178. https://doi.org/10.1002/aic.15674
Eason J.P., Biegler L.T. Reduced model trust region methods for embedding complex simulations in optimization problems // Computer Aided Chemical Engineering. 2015. V. 37. P. 773. https://doi.org/10.1016/B978-0-444-63578-5.50124-9
Dowling A.W., Eason J.P., Ma J., Miller D.C., Biegler L.T. Coal Oxycombustion Power Plant Optimization Using First Principles and Surrogate Boiler Models // Energy Procedia. 2014. V. 63. P. 352. https://doi.org/10.1016/j.egypro.2014.11.038
Lang Y., Zitney S.E., Biegler L.T. Optimization of IGCC processes with reduced order CFD models // Computers and Chemical Engineering. 2011. V. 35. P. 1705. https://doi.org/10.1016/j.compchemeng.2011.01.018
Донской И.Г., Маринченко А.Ю., Клер А.М., Рыжков А.Ф. Оптимизация режимов работы парогазовой мини-ТЭС с атмосферным газогенератором // Теплофизика и аэромеханика. 2015. Т. 22. № 5. С. 663.
Li C., Dai Z., Sun Z., Wang F. Modeling of an Opposed Multiburner Gasifier with a Reduced-Order Model // Industrial and Engineering Chemistry Research. 2013. V. 52. P. 5825. https://doi.org/10.1021/ie3030505
Monaghan R.F.D., Ghoniem A.F. A dynamic reduced order model for simulating entrained flow gasifiers. Part I: Model development and description // Fuel. 2012. V. 91. P. 61. https://doi.org/10.1016/j.fuel.2011.07.015
Мессерле А.В., Мессерле В.Е., Устименко А.Б. Плазменная термохимическая подготовка к сжиганию пылеугольного топлива // Теплофизика высоких температур. 2017. Т. 55. № 3. С. 366. https://doi.org/10.7868/S0040364417030140
Ishi H., Hayashi T., Tada H., Yokohama K., Takashima R., Hayashi J. Critical assessment of oxy-fuel integrated coal gasification combined cycles // Applied Energy. 2019. V. 233–234. P. 156. https://doi.org/10.1016/j.apenergy.2018.10.021
Каганович Б.М., Филиппов С.П., Кейко А.В., Шаманский В.А. Термодинамические модели экстремальных промежуточных состояний и их приложения в энергетике // Теплоэнергетика. 2011. № 2. С. 51.
Глушко В.П. (ред.) Термодинамические и теплофизические свойства продуктов сгорания. Т. 1. М.: ВИНИТИ АН СССР, 1971. 263 с.
Каганович Б.М., Кейко А.В., Шаманский В.А., Ширкалин И.А., Зароднюк М.С. Технология термодинамического моделирования. Редукция моделей движения к моделям покоя. Новосибирск: Наука, 2010. 236 с.
Rossi C.C.R.S., Berezuk M.E., Cardozo-Filho L., Guirardello R. Simultaneous calculation of chemical and phase equilibria using convexity analysis // Computers & Chemical Engineering. 2011. V. 35. P. 1226. https://doi.org/10.1016/j.compchemeng.2010.07.019
Асланян Г.С., Гиневская И.Ю., Шпильрайн Э.Э. Влияние параметров парокислородного дутья на газификацию углерода // Химия твердого топлива. 1984. № 1. С. 90.
Donskoy I.G., Shamansky V.A., Kozlov A.N., Svishchev D.A. Coal gasification process simulations using combined kinetic-thermodynamic models in one-dimensional approximation // Combustion Theory and Modelling. 2017. V. 21. № 3. P. 529. https://doi.org/10.1080/13647830.2016.1259505
Donskoy I.G. Numerical study of operating parameters of a single-stage air-steam blown gasification process of pulverized coal // Energy Systems Research. 2019. V. 2. № 3. P. 55. https://doi.org/10.25729/esr.2019.03.0007
Гиршфельдер Дж., Кертисс Ч., Берд Р. Молекулярная теория газов и жидкостей. М.: Издательство иностранной литературы, 1961. 931 с.
Клер А.М., Жарков П.В., Епишкин Н.О. Эффективный подход к оптимизации параметров сложных теплоэнергетических установок // Теплофизика и аэромеханика. 2016. Т. 23. № 2. С. 299.
Клер А.М., Деканова Н.П., Тюрина Э.А. и др. Теплосиловые системы: оптимизационные исследования. Новосибирск: Наука, 2005. 236 с.
Вдовенко В.С., Мартынова М.И., Новицкий Н.В., Юшина Г.Д. Энергетическое топливо СССР (ископаемые угля, горючие сланцы, торф, мазут и горючий природный газ). М.: Энергоатомиздат, 1991. 184 с.
Дополнительные материалы отсутствуют.
Инструменты
Известия РАН. Энергетика