Известия РАН. Энергетика, 2023, № 1, стр. 35-50
Обоснование практических рекомендаций по организации оптимальных режимов предварительной термической обработки и сжигания угля в пылевидном состоянии
Е. А. Бойко 1, *, А. В. Страшников 1, **
1 ФГАОУ ВО “Сибирский федеральный университет”
Красноярск, Россия
* E-mail: EBoiko@sfu-kras.ru
** E-mail: savtr@mail.ru
Поступила в редакцию 22.06.2022
После доработки 24.10.2022
Принята к публикации 31.10.2022
- EDN: LVQGZR
- DOI: 10.31857/S000233102301003X
Аннотация
На основе данных о реакционной способности угля выполнено расчетное обоснование требований к организации процессов его подготовки и сжигания с учетом исходного качества и режимов работы систем подготовки и топочных устройств энергетических паровых котлов. Установлена взаимосвязь между такими режимными параметрами работы устройства для предварительной термической обработки угля как размер пылеугольных частиц, температура и длительность обработки с качеством исходного топлива с целью обеспечения устойчивого воспламенения и полноты выгорания продуктов термохимического превращения угля в условиях топочной камеры котельного агрегата. Результаты цикла аналитических исследований обобщены и доведены до уровня инженерной методики (в виде номограммы), которая позволяет по известным характеристикам исходного топлива (реакционная способность и размер частиц) определять оптимальные значения температуры и времени процесса предварительной термической обработки угля перед сжиганием в топочной камере парового котла. Найденные режимные параметры работы устройства предварительной термообработки угля обеспечивают выполнение поверочных (тепловых) и конструкторских расчетов реальных топливоиспользующих установок, например, систем безмазутной растопки и пылеприготовления. Установлено, что наиболее оптимальный режим предварительной термообработки полифракции бурых канско-ачинских углей с точки зрения эффективности воспламенения и сжигания продуктов термообработки составляет 800–850°С при времени обработки 0.6–1.2 с. Результаты расчетных исследований нашли свое подтверждение при проведении экспериментальных работ на специальном лабораторном стенде, обеспечивающем режим предварительной термической обработки угля в пылевидном состоянии в широком диапазоне температур и дожигания пыле- и газообразных продуктов термообработки в различных условиях.
ВВЕДЕНИЕ
В связи с прогнозируемым увеличением в ближайшие 20 лет абсолютного количества твердого топлива в мировом производстве электрической энергии (28% в 2035 г. [1]) и наблюдающимся дефицитом электрической и тепловой энергии значительное внимание в мире уделяется повышению эффективности и экологической безопасности процессов сжигания твердых топлив на пылеугольных тепловых электрических станциях, вырабатывающих 40.6% электрической и тепловой энергии [2]. В то же время прослеживается общемировая тенденция существенного колебания качества энергетических углей, что приводит к увеличению использования непроектных топлив, т.е. углей с теплотехническими характеристиками, отличающимися от проектных. В связи с этим ухудшаются как технико-экономические, так и экологические показатели работы энергетических котельных агрегатов. По этой причине особую актуальность приобретает создание и применение новых технологий, способствующих эффективному сжиганию твердых топлив независимо от их качества. К основному числу таких технологий относятся системы безмазутной подсветки и растопки котлов, предварительной термической подготовки топлива, эколого- и энергоэффективных горелочных и топочных устройств, разработка которых основана на глубоком понимании протекания физико-химических процессов при термическом превращении углей в пылевидном состоянии. При этом отсутствие надежных методов проектирования подобных устройств является сдерживающим фактором развития технологии подготовки и сжигания угля.
Аналитические и экспериментальные исследования процесса термической обработки различных углей показали, что эффективность их энергетического использования во многом будет определяться параметрами температурно-временного режима его подготовки. С другой стороны, как отмечено в работе [3], температурно-временной режим обработки пылеугольных частиц главным образом определяется качеством исходного угля, размером частиц и температурой процесса. Поэтому для разработки практических рекомендаций по организации температурно-временного режима обработки угля в пылевидном состоянии на реальных энерготехнологических установках необходима оптимизация критериев, характеризующих эффективность энергетического использования продуктов термообработки с одновременной оценкой динамики изменения их качества.
ПОСТАНОВКА ЗАДАЧ ИССЛЕДОВАНИЯ
Согласно [3] параметры оптимизации режима предварительной термообработки угля в пылевидном состоянии должны удовлетворять следующим условиям, обеспечивающим успешное энергетическое использование продуктов термической подготовки:
– максимальное испарение влаги и удаление балластных летучих (CO2);
– обеспечение минимальной концентрации летучих веществ, газифицированных вокруг топливной частицы, обеспечивающей стабильное их воспламенение при попадании в реакционное пространство (например, в топочную камеру котельного агрегата);
– минимизация тепловых потерь с химическим и механическим недожогом при дожигании продуктов термообработки в условиях реакционного пространства.
Математическая форма записи параметров оптимизации имеет следующий вид:
(1)
${{W}^{h}},\;{{C}_{{{\text{C}}{{{\text{O}}}_{{\text{2}}}}}}} \to \min ;{\text{ }}\sum\limits_{i = 1}^n {C_{i}^{{{\text{Vol}}}}} \geqslant C_{{{\text{Vol}}}}^{{\min }};\,\,\,\sum\limits_{i = 1}^n {\tau _{{i,{\text{Vol}}}}^{'}} \leqslant {{\tau }_{{{\text{пр}}}}},$Выбор первого критерия в качестве параметра оптимизации обоснован в работах [4, 5] и обусловлен необходимостью исключения процесса выделения балластирующих компонентов топлива из совокупного топочного процесса, обеспечивая тем самым минимальные энергетические затраты на воспламенение и выгорание пыле- и газообразных продуктов термообработки в топочном объеме парового котла.
Выполнение второго критерия оптимизации $\sum\nolimits_{i = 1}^n {C_{i}^{{{\text{Vol}}}}} \geqslant C_{{{\text{Vol}}}}^{{\min }}$ гарантирует устойчивость воспламенения газообразных продуктов термической обработки угля и, как следствие, устойчивость воспламенения и выгорания пылеугольного факела независимо от качества исходного топлива и режима работы топочной камеры котельного агрегата.
Суть третьего критерия заключается в сокращении длительности выделения летучих веществ, лимитирующих процесс выгорания твердого органического топлива (в частности, углей с высоким выходом летучих веществ) в топочной камере, за счет предварительной термической обработки угольных частиц. Как показано в работе [3] применительно к бурым углям Канско-Ачинского месторождения, к числу таких летучих веществ относятся оксид углерода и смолистые вещества в парообразном состоянии. Необходимое время пребывания пылеугольных частиц τпр в топочной камере котлоагрегата с учетом скорости витания пылеугольных частиц оценивается по выражению (2).
(2)
${{\tau }_{{{\text{пр}}}}} = {{\tau }_{{\text{г}}}}\frac{{{{\omega }_{{\text{г}}}}}}{{{{\omega }_{{\text{г}}}} - {{\omega }_{{{\text{вит}}}}}}},$(3)
${{\tau }_{{\text{г}}}} = \frac{{273Q_{i}^{r}}}{{{{q}_{V}}{{V}_{{\text{г}}}}{{T}_{{{\text{ср}}}}}}},$На рис. 1 представлен расчетный график изменения времени пребывания пылеугольных частиц (τпр, с) с различной теплотой сгорания ($Q_{i}^{r}$, кДж/кг) при двух температурах сжигания (Тср, К), характерных для топочных камер с твердым и жидким шлакоудалением от теплонапряжения топочного объема (qV, кВт/м3).
Рис. 1.
Зависимость времени пребывания пылеугольных частиц в топочной камере котельного агрегата от теплонапряжения топочного объема: Δ – $Q_{i}^{r}$ = 10 000 кДж/кг; ⚪ – $Q_{i}^{r}$ = 15 000 кДж/кг; ◻ – $Q_{i}^{r}$ = 20 000 кДж/кг; - - - – Тср = 1473 К; — – Тср = 1773 К.
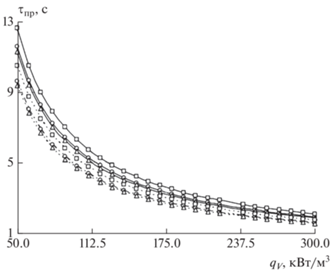
Рядом экспериментально-расчетных исследований, опубликованных в работах [7–9] на примере канско-ачинских углей, показано, что из трех вышеперечисленных параметров оптимизации наиболее приоритетным и объективным является второй критерий, характеризующий устойчивое воспламенение и выгорание пылеугольного факела, в связи с тем, что обеспечение этого критерия гарантирует выполнение первого и третьего условий оптимизации процесса предварительной термоподготовки угля в пылевидном состоянии. Однако ни в одной из вышеперечисленных работ не приводится строгого математического описания для выполнения количественной оценки данного параметра применительно к процессу предварительной термической обработки пылеугольных частиц.
Результаты многочисленных исследований процесса воспламенения твердого органического топлива, проводившиеся как в условиях лабораторного эксперимента, так и в условиях промышленных энергетических установок, отчетливо показывают, что летучие вещества играют весьма значительную роль как при воспламенении, так и на начальной стадии горения топлива [3, 7, 10, 11].
В работе [3] отмечается, что условия воспламенения летучих веществ (температура, концентрация) не характеризуют способность к возгоранию самой углеродной основы, но в ряде случаев именно начиная с температуры воспламенения летучих веществ наблюдается устойчивое горение нелетучего коксового остатка. Предположение о том, что на воспламенение угольных частиц существенное влияние оказывает прогрев частиц за счет горения летучих, подтверждено специальными опытами [11]. Установлено, что воспламенение летучих веществ во время их выделения невозможно до тех пор, пока температура пылевоздушной смеси и концентрация летучих веществ в ней не достигнут соответствующих значений.
Оптимизация мощности и параметров устройства предварительной термической обработки угольной пыли определяется условиями воспламенения пылегазовоздушного потока (смеси). Поскольку процесс термической обработки реализуется, как правило, в камерах циклонного типа, можно с достаточной вероятностью предположить, что образующийся многокомпонентный пылегазовый поток характеризуется повышенным уровнем турбулентности, обусловленным конструкцией устройства. Повышенный уровень турбулентности способствует интенсификации процессов турбулентного обмена импульсом, теплотой и массой в поперечном направлении, что дает возможность рассматривать устройство термической обработки твердого топлива в пылевидном состоянии в первом приближении как “реактор Лонгвелла”, в котором создается интенсивная мелкомасштабная турбулентность, обеспечивающая почти мгновенное смешение продуктов сгорания с нагреваемой аэросмесью [12]. Иными словами, в первом приближении многокомпонентный поток в устройстве термической подготовки твердого топлива предполагается рассматривать одномерным с равномерной структурой полей концентраций, температур и скорости в поперечных сечениях устройства. Это допущение позволяет исключить анализ влияния реальной аэродинамической обстановки процесса на параметры потока и достаточной степенью упрощения оценить конечные эффекты.
РАСЧЕТНОЕ ОБОСНОВАНИЕ ОПТИМАЛЬНЫХ РЕЖИМОВ ПРЕДВАРИТЕЛЬНОЙ ТЕРМООБРАБОТКИ УГЛЯ
Для количественной оценки условий воспламенения с учетом принятых допущений необходимо и достаточно определить величину минимальной концентрации летучих веществ ($\sum\nolimits_{i = 1}^n {C_{i}^{{{\text{Vol}}}}} $), газифицированных вокруг частицы, при которой возможно пламенное горение летучих веществ, после ее попадания в топочную камеру котельного агрегата.
При этом необходимо учитывать, что существуют так называемые концентрационные границы зажигания – верхняя и нижняя границы концентраций компонентов горючей смеси, когда избыток горючего и окислителя препятствует возникновению пламени. Для практических задач большее значение имеет нижняя концентрационная граница, так как верхняя не может быть достигнута для пылеугольных частиц на значительном расстоянии от ее поверхности [13].
Исходя из вышесказанного, для определения режимов предварительной термической обработки угля необходимо определить аналитическую форму записи следующего условия: $\sum\nolimits_{i = 1}^n {C_{i}^{{{\text{Vol}}}}} \geqslant C_{{{\text{Vol}}}}^{{\min }}$ или $\sum\nolimits_{i = 1}^n {C_{i}^{{{\text{Vol}}}}} - C_{{{\text{Vol}}}}^{{\min }} \geqslant 0$, где $C_{{{\text{Vol}}}}^{{{\text{min}}}}$ – нижняя концентрационная граница, характеризующая возможность стабильного пламенного горения летучих продуктов термической деструкции топлива.
Математическая задача определения концентрации летучих веществ на нижней концентрационной границе может быть представлена следующей системой уравнений:
(4)
${{D}_{{{\text{Vol}}}}}\left( {\frac{{{{d}^{2}}{{C}_{{{\text{Vol}}}}}}}{{d{{r}^{2}}}} + \frac{2}{r}\frac{{d{{C}_{{{\text{Vol}}}}}}}{{dr}}} \right) - W\frac{{d{{C}_{{{\text{Vol}}}}}}}{{dr}} = 0,$(6)
${{\left. { - {{D}_{{{\text{Vol}}}}}\frac{{d{{C}_{{{\text{Vol}}}}}}}{{dr}}} \right|}_{{r = {{r}_{0}}}}} = {{L}_{{{\text{Vol}}}}},$Скорость молярного переноса W определяется на основе рассуждений, изложенных в [3]. Выделим две контрольные поверхности S1 и S2. Поверхность S1 совпадает с геометрической поверхностью частицы, S2 представляет собой произвольную сферическую поверхность радиуса r, удаленную на расстояние r–r0 от первой (см. рис. 2).
Если обозначить скорости движения летучих веществ через эти поверхности соответственно W0 и W(r), то количество летучих веществ, прошедших за время dτ через эти поверхности, можно записать в виде:
Поскольку все количество летучих веществ проходит через первую и вторую поверхность, то справедливо равенство $4\pi r_{0}^{2}{{W}_{0}}d\tau \; = \;4\pi {{r}^{2}}W\left( r \right)d\tau $.
Откуда
Согласно [3] отношение $\frac{{r_{0}^{2}{{W}_{0}}}}{{{{r}^{2}}}}$ для удобства вычислений можно представить в виде следующего равенства:
(11)
$\frac{{r_{0}^{2}{{W}_{0}}}}{{{{r}^{2}}}} = \frac{{\alpha {{D}_{{{\text{Vol}}}}}}}{{{{r}^{2}}}}.$Тогда уравнение (4) с учетом (11) можно представить в виде
(12)
$\frac{{{{d}^{2}}{{C}_{{{\text{Vol}}}}}}}{{d{{r}^{2}}}} + \left( {\frac{2}{r} - \frac{\alpha }{{{{r}^{2}}}}} \right)\frac{{d{{C}_{{{\text{Vol}}}}}}}{{dr}} = 0.$Решением этого уравнения является функция [14]:
(13)
${{C}_{{{\text{Vol}}}}} = \frac{{{{A}_{1}}}}{\alpha }\exp \left( { - \frac{\alpha }{r}} \right) + {{A}_{2}}$(14)
${{A}_{1}} = - \frac{{{{L}_{{{\text{Vol}}}}}}}{{{{D}_{{{\text{Vol}}}}}}}r_{0}^{2}\exp \left( {\frac{{{{r}_{0}}{{W}_{0}}}}{{{{D}_{{{\text{Vol}}}}}}}} \right),$(15)
${{A}_{2}} = \frac{{{{L}_{{{\text{Vol}}}}}}}{{{{W}_{0}}}}\exp \left( {\frac{{{{r}_{0}}{{W}_{0}}}}{{{{D}_{{{\text{Vol}}}}}}}} \right).$Таким образом, окончательное решение уравнения (4), удовлетворяющее условиям (5) и (6), имеет вид:
(16)
${{C}_{{{\text{Vol}}}}} = \frac{{{{L}_{{{\text{Vol}}}}}}}{{{{W}_{0}}}}\exp \left( {\frac{{{{r}_{0}}{{W}_{0}}}}{{{{D}_{{{\text{Vol}}}}}}}} \right)\left[ {1 - \exp \left( { - \frac{{r_{0}^{2}{{W}_{0}}}}{{{{D}_{{{\text{Vol}}}}}r}}} \right)} \right].$Для определения потока летучих LVol необходимо знать, во-первых, время выделения и, во-вторых, количество выделяющихся летучих веществ.
где m – количество выделившихся к данному моменту времени летучих веществ, кг; τ – время термического разложения, с; ƒ – поверхность угольной частицы, м2.При определении поверхности частицы, в качестве упрощения, принимается сферическая форма пылеугольной частицы. Для определения скорости движения потока летучих с поверхности угольной частицы предположим, что имеет место поток летучих веществ интенсивностью LVol, и выделим на пути этого потока некоторую поверхность ƒ. Считаем, что плотность вещества потока летучих равна γVol (кг/м3). Тогда за время τ через выделенную поверхность пройдет следующее количество вещества [3], м3:
Это же самое количество вещества (м3) можно представить как:
Приравнивая (18) и (19), получим соотношение
Плотность летучих веществ γVol можно определить, зная их состав (см. табл. 1 на примере газообразных продуктов термического разложения бородинского угля). В табл. 2 приведены значения плотности летучих веществ, выделяющихся при термическом разложении бородинского угля. Проведение настоящих исследований на бородинском угле Канско-Ачинского месторождения обусловлено значительным потенциалом месторождения с точки зрения балансовых запасов и масштабов его энергетического использования в настоящее время и на длительную перспективу.
Таблица 1.
Состав газа пиролиза бородинского угля
Температура процесса, °С | Состав газа пиролиза, объемн, % | ||||
---|---|---|---|---|---|
CO2 | смола | CO | H2 | CH4 | |
400 | 74.5 | – | 15.2 | 2.4 | 7.6 |
600 | 38.7 | 4.8 | 20.4 | 7.4 | 29 |
800 | 19.8 | 4.5 | 25.2 | 30.7 | 19.8 |
1000 | 16.4 | 1.1 | 22.9 | 45.1 | 14.9 |
1200 | 10.7 | 0.4 | 26.4 | 55.6 | 6.0 |
Таблица 2.
Плотность летучих веществ (газообразных продуктов) термической деструкции бородинского угля
Температура процесса, °С | 400 | 600 | 800 | 1000 | 1200 |
---|---|---|---|---|---|
Плотность летучих веществ γVol, кг/м3 | 0.698 | 0.407 | 0.239 | 0.166 | 0.12 |
Коэффициент диффузии летучих веществ DVol может быть рассчитан по формуле [13]:
(21)
${{D}_{{{\text{Vol}}}}} = \frac{{1 - {{\mu }_{A}}}}{{\frac{{{{\mu }_{B}}}}{{{{D}_{{AB}}}}} + \frac{{{{\mu }_{C}}}}{{{{D}_{{AC}}}}} + \ldots + \frac{{{{\mu }_{D}}}}{{{{D}_{{AD}}}}}}},$Коэффициенты диффузии для бинарной системы ${{D}_{{1,2}}}$ рассчитываются по формуле [13]:
(22)
${{D}_{{1,2}}} = \frac{{0.002628}}{{P\sigma _{{1,2}}^{2}\Omega _{{1,2}}^{{{{{(1,1)}}_{*}}}}}}\sqrt {\frac{{{{T}^{3}}\left( {{{M}_{1}} + {{M}_{2}}} \right)}}{{2{{M}_{1}}{{M}_{2}}}}} ,$Результаты расчета коэффициентов диффузии летучих веществ, газообразных продуктов термической деструкции бородинского угля в зависимости от состава выделяющихся летучих веществ приведены в табл. 3.
Таблица 3.
Коэффициенты диффузии летучих веществ термической деструкции бородинского угля, см2/с
$T$, °С | ${{D}_{{{{{\text{H}}}_{{\text{2}}}}}}}$ | DCO | ${{D}_{{{\text{C}}{{{\text{H}}}_{{\text{4}}}}}}}$ | Dсмолы | ${{D}_{{{\text{C}}{{{\text{O}}}_{{\text{2}}}}}}}$ | Dсмеси |
---|---|---|---|---|---|---|
400 | 2.745 | 0.668 | 0.922 | 0.505 | 0.762 | 0.807 |
600 | 4.181 | 1.001 | 1.457 | 0.911 | 1.250 | 1.455 |
800 | 5.995 | 2.284 | 2.544 | 1.654 | 2.129 | 3.142 |
1000 | 8.108 | 3.886 | 4.150 | 2.529 | 3.393 | 5.721 |
1200 | 10.578 | 6.249 | 5.454 | 3.684 | 4.647 | 8.425 |
Если при решении уравнения (16) воспользоваться неравенством (7), которое означает, что для того чтобы произошло воспламенение, концентрация летучих веществ должна быть больше значения ее на нижней концентрационной границе, значение W0 выразить через размер пылеугольной частицы и время процесса ее температурной обработки, используя уравнения 18–20, получим зависимость, связывающую между собой основные режимные параметры работы устройства для предварительной термической обработки пылеугольных частиц и минимальную концентрацию летучих веществ, выделившихся при термическом разложении топлива в пылеподогревателе, обеспечивающую устойчивое воспламенение и выгорание пылеугольного факела.
(23)
${{\gamma }_{{{\text{Vol}}}}}\exp \left( {\frac{{r_{0}^{2}{{V}^{{daf}}}{{\gamma }_{r}}}}{{3{{\gamma }_{{{\text{Vol}}}}}\tau {{D}_{{{\text{Vol}}}}}}}} \right)\left( {1 - \exp \left( { - \frac{{r_{0}^{2}{{V}^{{daf}}}{{\gamma }_{r}}}}{{3{{\gamma }_{{{\text{Vol}}}}}\tau {{D}_{{{\text{Vol}}}}}}}} \right)} \right) - C_{{{\text{Vol}}}}^{{\min }} = 0,$Значения $C_{{{\text{Vol}}}}^{{{\text{min}}}}$ рассчитываются по формуле Ле-Шателье [13]
(24)
$\frac{{100}}{{C_{{{\text{Vol}}}}^{{{\text{min}}}}}} = \frac{{{{n}_{1}}}}{{{{N}_{1}}}} + \frac{{{{n}_{2}}}}{{{{N}_{2}}}} + \ldots + \frac{{{{n}_{i}}}}{{{{N}_{i}}}},$Величины n1, n2, … ni заимствованы для бородинского угля при температурах 400, 600, 800, 1000 и 1200°С из [9], а значения N1, N2, … Ni – из [13]. Результаты расчетов нижней концентрационной границы воспламенения газообразных продуктов термического разложения бородинского угля по формуле Ле-Шателье приведены в табл. 4.
Таблица 4.
Зависимость нижней концентрационной границы воспламенения летучих веществ бородинского угля от температуры процесса
Температура процесса, °С | 400 | 600 | 800 | 1000 | 1200 |
---|---|---|---|---|---|
Концентрация, $C_{{{\text{Vol}}}}^{{{\text{min}}}}$, кг/м3 | 0.03019 | 0.01558 | 0.00938 | 0.00582 | 0.00464 |
Уравнение (23) позволяет связать между собой такие режимные параметры работы устройства предварительной термической обработки угля как размер пылеугольных частиц (r0), температура (Ттп) и время (τтп) обработки с качеством исходного топлива, исходя из условия обеспечения устойчивого воспламенения и выгорания продуктов термохимического превращения угля в условиях топочной камеры котельного агрегата (см. условие 1). В данном случае решением трансцендентного уравнения (23) является время термообработки (τтп, с) при условии изменения размеров пылеугольных частиц (r0) от 50 до 1000 мкм. Температура термической обработки варьировалась от 400 до 1200°С. Уравнение (23) решалось комбинированным численным методом (сочетание методов бисекции и секущих) с точностью 10–6 [15].
Результаты цикла аналитических исследований обобщены и доведены до уровня инженерной методики (в виде номограмм – см. рис. 3 и 4). Полученные номограммы позволяют по известным характеристикам исходного топлива (реакционная способность и размер частиц) определять оптимальные значения температуры и времени процесса предварительной термической обработки бородинского угля перед сжиганием в топочной камере парового котла. В свою очередь, найденные режимные параметры работы устройства термообработки угля позволяют выполнить поверочный (тепловой) и конструкторский расчеты пылеподогревателя.
Рис. 3.
Зависимость времени термической обработки (τтп, с) бородинского угля по условию устойчивости воспламенения пылеугольного факела от температуры обработки (Ттп, °С) и размера частиц (r0, мкм): 1 – 50; 2 – 100; 3 – полифракция; 4 – 200; 5 – 300; 6 – 400; 7 – 500.
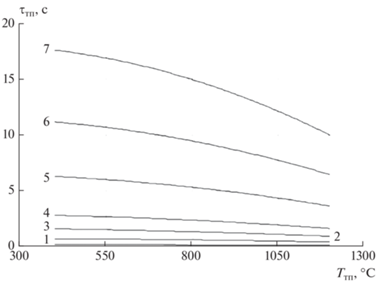
Рис. 4.
Зависимость времени термической обработки (τтп, с) бородинского угля по условию устойчивости воспламенения пылеугольного факела от размера частиц (r0, мкм) и температуры обработки (Ттп, °С): 1 – 400; 2 – 600; 3 – 800; 4 – 1000; 5 – 1200.
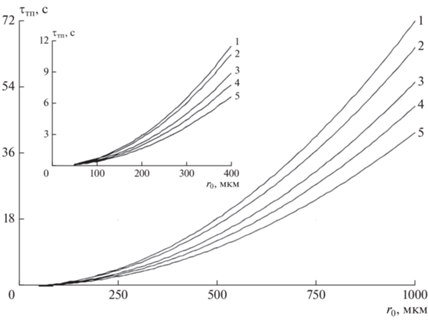
Необходимо отметить, что сопоставлением полученных результатов, представленных на рис. 3 и 4, хорошо подтверждается ранее высказанное предположение [16], сформулированное в виде третьего условия оптимизации (формула 1). Для всех расчетных режимов на примере предварительной термической обработки и сжигания бородинского угля показано строгое соблюдение условия $\sum\nolimits_{i = 1}^n {\tau _{{i,{\text{Vol}}}}^{'}} \leqslant {{\tau }_{{{\text{пр}}}}}$ при температуре процесса в устройстве предварительной термоподготовки Ттп > 600°C.
Причем длительность термообработки пылеугольных частиц разных размеров, обеспечивающая устойчивость воспламенения пыле- и газообразных продуктов сокращается при изменении размера с 500 мкм до 50 мкм при температуре термообработки 400°С почти в 18 раз, а при температуре обработки 1200°С до 7.5.
Для частиц монофракционного состава, например, частиц размером 100 мкм, изменение температуры процесса предварительной термообработки с 400 до 1200°С приводит к сокращению времени термообработки по условию обеспечения устойчивости воспламенения пыле- и газообразных продуктов термообработки на 47%, для частиц с размером 500 мкм – 55%, 1000 мкм – 62%.
ЭКСПЕРИМЕНТАЛЬНАЯ УСТАНОВКА И РЕЗУЛЬТАТЫ НАТУРНЫХ ИССЛЕДОВАНИЙ
В подтверждение обоснованности теоретических выводов и отработки режимов выполнен цикл экспериментальных исследований процесса предварительной термической обработки бородинского угля в пылевидном состоянии с последующим сжиганием газообразных и твердых продуктов термообработки.
Экспериментальная установка для исследования процессов термоокислительной декструкции пылевидного твердого топлива с последующим дожиганием продуктов термообработки в условиях предварительного высокоскоростного нагрева с горизонтальной реакционной камерой (трубчатой печью) представлена на рис. 5.
Рис. 5.
Принципиальная схема и вид лабораторной установки по предварительной термической обработке угля в пылевидном состоянии: 1 – камера дожигания продуктов термообработки; 2 – муфельный электронагреватель; 3 – бункер угольной пыли; 4 – дутьевой вентилятор; 5 – горизонтальная цилиндрическая реакционная камера (участок термообработки); 6 – автотрансформатор; 7 – транзистор; 8 – переменный резистор; 9 – резистор; 10 – контроллер температуры; 11 – термопара.
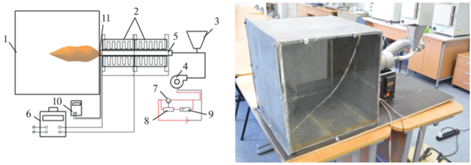
Основной частью экспериментальной установки является горизонтальная цилиндрическая реакционная камера (10) длиной 450 мм и диаметром 35 мм с электрическим компенсационным обогревом и камерой дожигания (1), что позволяет проводить исследования в стационарном режиме при соблюдении различных условий как по температуре предварительной термической обработки пылевоздушного потока (200–1200°С), времени пребывания частиц угля в реакционном пространстве (0.1–0.8 с), так и размера пылеугольных частиц (63–1000 мкм).
Угольная пыль из бункера пыли поступает в реакционное пространство через тангенциальную горелку из аэромеханического питателя пыли. Транспорт пыли к горелке осуществляется в зависимости от целей эксперимента либо инертным газом (аргон), либо воздухом. Расход воздуха определяется по ротаметру марки РМ 0.04Ж.
Для исследования процессов предварительной термообработки угольных частиц и горения пылегазообразных продуктов термообработки в качестве первичного и вторичного воздуха используются воздух, нагнетаемый дутьевым вентилятором (4), оснащенный частотным преобразователем для регулирования производительности вентилятора. Расход воздуха в зону термообработки варьировался в диапазоне (1–8) × 10–4 м3/с, что обеспечивает необходимое по условиям эксперимента время пребывания угольных частиц в зоне предварительной термообработки от 0.1 до 0.8 с.
Температурный режим работы реакционной камеры и соответственно процесса термообработки определяется величиной подаваемого напряжения, регулирование значения которого осуществляется однофазным регулятором напряжения (РНО). Регистрация температурного режима работы трубчатой печи осуществляется с помощью платино-платиновой термопары (ПП68), соединенных с регистрирующим прибором-самописцем марки КСП-4.
Дожигание пылегазообразных продуктов термообработки пылеугольных частиц осуществляется в реакционной камере (1), имитирующей топочное пространство. Такая организация процесса предварительной термической обработки и дожигания пылегазообразных продуктов термоподготовки позволяет выполнять сбор и количественную оценку недогоревших коксовых частиц с анализом величины механического недожога топлива от температурного уровня его предварительного нагрева.
Такая конструкция экспериментальной установки позволяет осуществлять газовый анализ газообразных продуктов, выделяющихся при предварительном нагреве топлива. Отбор газов и угольных частиц осуществляется трубками Прандтля в устье горелочного устройства, за счет разрежения, создаваемого перистальтическим насосом для отбора газообразных продуктов термоокислительной деструкции на анализ, осуществляется тягонапоромером марки ТНЖ-Н с классом точности 1.5 и поддерживается порядка 0.1–0.2 мм рт. ст. Анализ состава газообразных продуктов термообработки угольных частиц осуществлялся на хроматографическом газоанализаторе марки 3700 (ЛХМ-80).
Экспериментальная установка обладает минимальной инерционностью, так выход на стационарный режим ее работы составляет не более 5 мин, скорость изменения температурного режима работы установки – 100°С/мин.
Демонстрация наглядных результатов проведения экспериментальных исследований по предварительной термической обработке угля в пылевидном состоянии и дожиганию пыле- и газообразных продуктов представлена на рис. 6.
Рис. 6.
Структура факела при сжигании продуктов предварительной термической обработки полифракции бородинского угля: (а) – температура предварительной обработки Ттп = 600°С; (б) – Ттп = 800°С. Длительность термообработки составила τтп = 0.5 с.
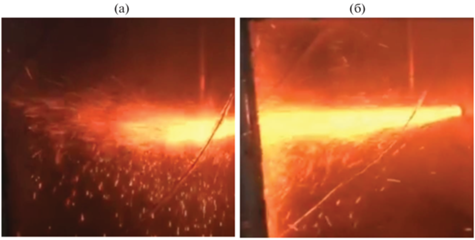
Кривые динамики выделения индивидуальных компонентов суммарного газа при термоокислительной деструкции бородинского угля полифракционного состава (R90 = 60%) с длительностью термообработки τтп = 0.5 с приведены на рис. 7. Характеристики исходного бурого бородинского угля приведены в работе [6].
Рис. 7.
Конечный выход индивидуальных газовых компонентов при термоокислительной деструкции бородинского угля (размер 63–150 мкм; время предварительной термообработки τтп = 0.5 с) в условиях высокоскоростного нагрева: ◇ – CO2; ◻ – CO; Δ – CH4; × – H2.
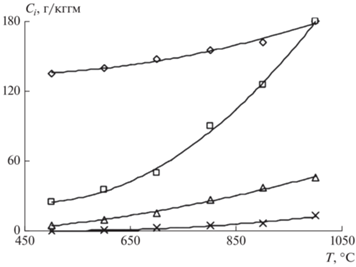
Полученные экспериментальные данные по динамике термоокислительной деструкции полифракции бородинского угля в условиях высокоскоростного нагрева отражают сложный характер зависимостей выхода индивидуальных компонентов суммарного газа как от времени, так и от температуры протекания процесса. При этом характер соответствующих закономерностей различен для каждого из компонентов. Например, динамика массового выхода CO2 с повышением температуры заметно ниже, чем выделения CO, CH4 и H2. При этом конечный выход CO, CO2, CH4 и H2, как иллюстрирует рис. 8, возрастают с повышением температуры процесса термообработки. Количественная оценка скоростей реакций позволила выделить параллельно-последовательные группы, константы скорости которых отличаются в 2–5 раз. Более быстрые из них обусловлены разрывом слабых периферийных кислородосодержащих связей, а группа медленных реакций включает в себя процессы более глубокой деструкции ядра макромолекулы угля. Интересно отметить, что в суммарном газе низкотемпературных опытов преобладают продукты группы более быстрых реакций – CO и CO2. С повышением температуры неуклонно возрастает доля продуктов медленных реакций – H2 и CH4. Роль последовательных стадий увеличивается с повышением температуры процесса, параллельных – с увеличением скорости нагрева.
Рис. 8.
Интенсивность выгорания нелетучих остатков частиц (размер 63–100 мкм) бородинского угля при различной температуре предварительной обработки, °С: ⚪ – 400; ◻ – 600; Δ – 800; ◇ – 1000.
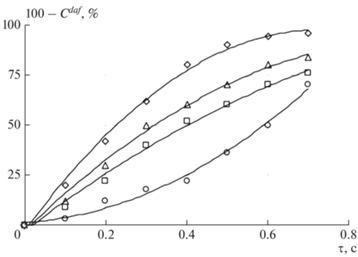
Повышение температуры процесса предварительной термообработки топлива в диапазоне температур от 400 до 1000°С приводит к росту выхода таких индивидуальных газообразных компонентов как CO2 на 27%, CO – 83%, CH4 – 89% и H2 – 93%.
Типичные результаты интенсивности выгорания нелетучих остатков термообработки бородинского угля на примере частиц размером от 63 до 100 мкм представлены на рис. 8.
Исследование кривых выгорания нелетучих остатков показало, что при скоростях нагрева менее 103 град/с выгорание коксовых частиц завершается в период их прогрева. При больших скоростях нагрева время выгорания нелетучих остатков складывается из неизотермической и изотермической составляющих.
Анализ экспериментальных данных по исследованию кинетики различных этапов термохимического превращения пылевидного топлива позволяет констатировать, что реакционный механизм и профиль кривых остаются неизменными при экстремальных скоростях нагрева (в пределах 10–2–106 град/с).
Экспериментально установлено, что с повышением температуры предварительной термообработки пылеугольных частиц (размер 63–100 мкм) с 400 до 1000°С интенсивность выгорания нелетучих остатков повышается на 42%. При температуре предварительной термообработки пылеугольных частиц 1000°С нелетучие остатки выгорают с полнотой 99% за 0.7 с. Снижение температуры предварительной термообработки до 400°С при прочих равных условиях приводит к уменьшению полноты выгорания до 73%.
ЗАКЛЮЧЕНИЕ
1. Установлена взаимосвязь между такими режимными параметрами работы устройства для предварительной термической обработки угля как размер пылеугольных частиц (r0), температура (Ттп) и длительность (τтп) обработки с качеством исходного топлива с целью обеспечения устойчивого воспламенения и полноты выгорания продуктов термохимического превращения угля в условиях топочной камеры котельного агрегата. Длительность термообработки пылеугольных частиц разных размеров, обеспечивающая устойчивость воспламенения пыле- и газообразных продуктов сокращается при изменении размера с 500 мкм до 50 мкм при температуре термообработки 400°С почти в 18 раз, а при температуре обработки 1200°С до 7.5. Для частиц монофракционного состава, например, частиц с размером 100 мкм, изменение температуры процесса предварительной термообработки с 400 до 1200°С приводит к сокращению времени термообработки по условию обеспечения устойчивости воспламенения пыле- и газообразных продуктов термообработки на 47%, для частиц с размером 500 мкм – 55%, 1000 мкм – 62%.
2. Результаты цикла аналитических исследований обобщены и доведены до уровня инженерной методики (в виде номограммы), которая позволяет по известным характеристикам исходного топлива (реакционная способность и размер частиц) определять оптимальные значения температуры и времени процесса предварительной термической обработки угля перед сжиганием в топочной камере парового котла. Найденные режимные параметры работы устройства предварительной термообработки угля обеспечивают выполнение поверочных (тепловых) и конструкторских расчетов реальных топливоиспользующих установок, например, систем безмазутной растопки и пылеприготовления.
3. Установлено, что оптимальный режим предварительной термообработки углей в пылевидном состоянии (полифракция), с точки зрения эффективности воспламенения и выгорания продуктов термообработки, составляет Ттп = 800–850°С при времени обработки τтп = 0.6–1.2 с. Результаты расчетных исследований нашли свое подтверждение при проведении экспериментальных работ на специальном лабораторном стенде, обеспечивающим режим предварительной термической обработки угля в пылевидном состоянии в широком диапазоне температур и дожигания пыле- и газообразных продуктов термообработки в различных условиях.
4. Экспериментально установлено, что повышение температуры процесса предварительной термообработки бурого бородинского угля в диапазоне температур от 400 до 1000°С приводит к росту выхода таких индивидуальных газообразных компонентов как CO2 на 27%, CO – 83%, CH4 – 89% и H2 – 93%. С повышением температуры предварительной термообработки пылеугольных частиц (размер 63–100 мкм) с 400 до 1000°С интенсивность выгорания нелетучих остатков повышается на 42%. При температуре предварительной термообработки пылеугольных частиц 1000°С нелетучие остатки выгорают с полнотой 99% за 0.7 с. Снижение температуры предварительной термообработки до 400°С при прочих равных условиях приводит к уменьшению полноты выгорания до 73%.
Список литературы
BP Energy Outlook 2035. February 2015. BP p.l.c., 2015. 98 P. http://www.bp.com/content/dam/bp/pdf/energy-economics/energy-outlook-2015/bp-energy-outlook-2035-booklet.pdf
Key World Energy Statistics 2012: International Energy Agency. OECD/IEA, 2012. 80 p. www.iea.org
Бойко Е.А. Реакционная способность энергетических углей // Красноярск: ИПЦ СФУ. 2011. С. 606.
Заворин А.С., Некряч Е.Н. Об условиях преобразования минеральной части пылевидного бурого угля при горении // Изв. вузов. Энергетика. 1988. № 9. С. 91–94.
Brown R.C. Thermochemical Processing of Biomass // Conversion into Fuels. Chemicals and Power. San Francisco. CA, USA: John Wiley & Sons, 2011. P. 348.
Тепловой расчет котельных агрегатов (нормативный метод). Изд. 3-е, перераб. и дополнен. СПб.: НПО ЦКТИ, 1998. С. 257.
Мещеряков В.Г., Верзаков В.Н., Маршак Ю.Л. и др. Структура факела в тангенциальной топочной камере котла БКЗ-500-140 при сжигании березовского и ирша-бородинского углей // Теплоэнергетика. 1989. № 8. С. 13–18.
Маршак Ю.Л., Митор В.В. Проектирование топок с жидким шлакоудалением (руководящие указания и дополнения к нормативному методу теплового расчета котельных агрегатов) // М.: ВТИ, 1983. С. 102.
Бойко Е.А., Страшников А.В. Кинетика термохимического превращения твердого органического топлива при высокоскоростном нагреве // Известия РАН. Энергетика. 2021. № 4. С. 103–126.
Сотников И.А., Окерблом Ю.И., Итман Д.Л. и др. Основные проектные и конструктивные решения по паровому котлу П-67 на канско-ачинских углях для энергоблоков мощностью 800 МВт // Теплоэнергетика. 1978. № 8. С. 15–21.
Бабий В.И., Куваев Ю.Ф. Горение угольной пыли и расчет пылеугольного факела // М.: Энергоатомиздат, 1986. С. 209.
MoGraw, Michael. Coal-water slurries are ready for utility boilers // FRI News. 1989. № 29. P. 1–5.
Померанцев В.В., Арефьев К.М., Ахмедов Д.Б. и др. Основы практической теории горения // Л.: Энергоатомиздат, 1986. С. 312.
Бойко Е.А., Страшников А.В. Теоретическое обобщение и развитие математического аппарата неизотермической кинетики // Известия РАН. Энергетика. 2021. № 2. С. 97–118.
Амосов А.А., Дубинский Ю.А., Копченова Н.В. Вычислительные методы для инженеров // М.: Высшая школа, 1994. С. 554.
Кузнецов П.Н., Федорчак М.А., Тарасова Л.С., Колесникова С.М., Каменский Е.С. Реакционная способность бурых углей в условиях термоокислительной деструкции // Химия твердого топлива. 2012. № 1. С. 1–12.
Дополнительные материалы отсутствуют.
Инструменты
Известия РАН. Энергетика