Известия РАН. Серия физическая, 2020, T. 84, № 3, стр. 439-442
Исследование свойств порошков на медной и никелевой основе для получения градиентных материалов методом селективного лазерного плавления
А. А. Вознесенская 1, *, Д. А. Кочуев 1, А. С. Разносчиков 1, А. В. Киреев 1, К. С. Хорьков 1
1 Федеральное государственное бюджетное образовательное учреждение высшего образования
“Владимирский государственный университет имени Александра Григорьевича и Николая Григорьевича Столетовых”
Владимир, Россия
* E-mail: 2obk@bk.ru
Поступила в редакцию 20.09.2019
После доработки 15.11.2019
Принята к публикации 27.11.2019
Аннотация
Рассмотрен подход для получения градиентных материалов из порошков хром-никелевой стали и чистой меди методом селективного лазерного плавления. Исследован фазовый и гранулометрический состав порошковых материалов. Установлена зависимость температуры порошкового материала от интенсивности лазерного излучения. Выявлены оптимальные характеристики процесса лазерного плавления и получены образцы многослойного покрытия методом селективного лазерного плавления.
ВВЕДЕНИЕ
При селективном лазерном плавлении свойства наплавляемого слоя, такие как однородность, плотность, адгезия к поверхности предыдущих слоев, зависят от целого ряда параметров: плотность мощности в лазерном пятне, скорость сканирования, фракционный и химический состав, а также поглощательная способность наплавляемого материала [1]. Исследование поглощения порошковых материалов представляет особый интерес для развития селективного лазерного плавления, поскольку оно позволяет определить параметры обработки, пригодные для детали с минимальным содержанием дефектов. Данная информация позволяет быстро подобрать режим построения модели, учесть особенности материала при выборе стратегии построения и расположения поддерживающих структур, и как следствие, получить более равномерный и воспроизводимый процесс лазерного плавления в процессе синтеза детали [2]. Исследование коэффициента поглощения лазерного излучения частицами порошковых материалов позволит расширить круг легирующих добавок в металлы [3] при селективном лазерном плавлении, использование которых ограничено различной температурой плавления порошкового материала [4]. При создании градиентных материалов актуально использование меди и хром-никелевой стали. Это обусловлено хорошей смачиваемостью всех компонентов входящих в состав порошковых материалов. Таким образом, высокая адгезионная стойкость наносимых слоев будет обеспечиваться объемной диффузией компонентов системы. Данный эффект применим при производстве узлов, испытывающих значительные механические, термические и коррозионные нагрузки в процессе эксплуатации. Внешняя поверхность детали может формироваться из хромистой стали, что обеспечит указанные характеристики, а внутренние поверхности можно выполнить из меди для обеспечения эффективного теплоотвода от внешней поверхности к внутренним теплоотводящим каналам. Применение технологии селективного лазерного плавления для производства таких узлов позволит обеспечить оптимальный режим работы изделия. В структуре детали, полученной таким образом, будут отсутствовать незаложенные конструкцией зазоры и полости, в которых присутствует тепловое сопротивление, приводящее к неравномерному прогреву и расширению участка.
Как правило, в виде порошка материал имеет более высокую поглощательную способность чем, например, в виде проката [5]. По сравнению с плотными материалами, высокая поглощательная способность вызвана наличием промежутков (пор) между гранулами в структуре порошкового слоя, развитой поверхностью частиц и более низкой теплопроводностью, что препятствует процессу плавления [6]. Поглощательная способность A определяется как отношение энергии, поглощенной поверхностью материала, к энергии, падающей на поверхность материала. Обычно в экспериментах измеряют коэффициент отражения R. Поглощательная способность рассчитывается исходя из соотношения A + R = 1. Поскольку порошковые материалы являются пористой структурой, то часть падающего излучения поглощается внешней поверхностью частиц, а другая часть излучения проникает в поры [7]. Поглощение порами приближается к поглощению черного тела. Также структура поверхности порошкового слоя изменяется в процессе лазерного плавления и это провоцирует изменение поглощательной способности [8]. При облучении порошка, благодаря частичному поглощению излучения, происходит рост температуры области воздействия. В данной работе рассмотрены измерения только той части поглощаемой мощности, которая преобразуется в тепло. Предполагается, что коэффициент поглощения неизменен в пределах температурных флуктуаций во время измерения и не зависит как от поглощенной доли падающего на поверхность образца пучка, так и от плотности мощности падающего излучения.
ИССЛЕДОВАНИЕ ПОРОШКОВЫХ МАТЕРИАЛОВ
Форма гранул и фракционный состав порошковых материалов были исследованы методом растровой электронной микроскопии. Гранулы хром-никелевой стали представляют собой частицы с развитым рельефом поверхности, который характеризуется высокой газонасыщенностью. Медный порошок имеет более сферичную форму гранул. Изображения частиц полученные на микроскопе представлены на рис. 1. Фазовый состав полученных порошков исследовали методом рентгеновской дифрактометрии на приборе D8 ADVANCE. Порошок состоит на 50.06% из железа, на 48.91% из сплава хрома и никеля, и содержит 1.03% кобальта. Второй порошок на 100% состоит из меди, других фаз обнаружено не было. Результат измерения представляет собой дифрактограмму – зависимость количества отсчетов от угла рассеяния, которая изображена на рис. 1.
Рис. 1.
Результаты исследования фазового (слева) и фракционного (справа) состава порошков: 1 – порошок хром-никелевой стали, 2 – медный порошок.
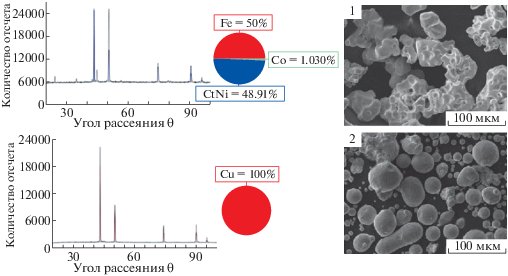
Для измерения поглощательной способности порошковых материалов в качестве источника излучения использовали волоконный лазер с длиной волны излучения 1060 нм. Расфокусированный пучок лазерного излучения был направлен на поверхность порошкового материала, диаметр лазерного пучка на поверхности порошкового материала составлял порядка 8 мм. Измерение температуры проводили двумя методами: 1 – с помощью фотопирометра, 2 – с использованием термопар К-типа. Значения температуры выводили на персональный компьютер через аналогово-цифровой преобразователь. На рис. 2 представлена схема эксперимента по исследованию температурных характеристик, где цифрами обозначены: 1 – источник лазерного излучения, 2 – фокусирующая система, 3 – лазерное излучение, 4 – порошковый материал, 5 – термопары К-типа, 6 – аналого-цифровой преобразователь, 7 – персональный компьютер, 8 – пирометр. На данном экспериментальном стенде были измерены температура порошковых материалов и мощность лазерного излучения. В протокол измерений внесены температура образца T(t) и мощность лазерного излучения P(t), а также интенсивность лазерного излучения I(t). Построен график, на котором отображены изменения температуры поверхности порошкового материала в зависимости от интенсивности лазерного излучения. График изменения значений представлен на рис. 3.
Рис. 3.
График изменения температуры поверхности порошкового материала в зависимости от интенсивности: 1 – порошок хром-никелевой стали, 2 – медный порошок.
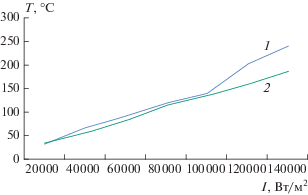
Температура прогрева поверхности порошка хром-никелевой стали изменялась от 33 до 240°С (рис. 3, линия 1), а в случае с медным порошком – от 35 до 187°С (рис. 3, линия 2). Исследуемые порошковые материалы схожи по динамике нагрева, но в конечном итоге нагрев хром-никелевого порошка происходит интенсивней. Таким образом, можно сделать вывод, что из данных порошков можно получить градиентный материал, т.к. скорее всего слои будут хорошо наплавляться друг на друга. Также можно предположить, что медный слой поможет слою хором-никелевого порошка выравнивать температурный вклад в дальнейшем процессе плавления, что важно учитывать при селективном лазерном плавлении.
ПОЛУЧЕНИЕ ГРАДИЕНТНЫХ МАТЕРИАЛОВ
Для того, чтобы улучшить свойства материала, необходимо правильно подобрать режим обработки порошкового материала лазерным излучением. Многослойное покрытие получают путем поочередного нансения и оплавления порошкового состава, добиваясь формирования нескольких слоев из различных материалов. Лазерную наплавку проводили на стальной подложке с использованием волоконной лазерной системы непрерывного действия, генерирующей на длине волны 1060 нм. Длина волны иттербиевых волоконных лазеров на порядок меньше, чем у СО2-лазеров, что обеспечивает лучшее поглощение падающего излучения для большинства металлов и сплавов и, следовательно, повышает эффективность проводимой обработки. Для фокусировки использовали оптическую систему с объективом плоского поля, (фокусне расстояние 200 мм), оснащенную гальваносканатором. Диаметр пучка в области обработки составлял от 100 до 300 мкм. Для обрабатываемых материалов подбирали режим обработки, исключающий растрескивание образовавшегося материала. При небольших скоростях сканирования происходит увеличение вклада энергии в область облучения, в том числе возможен значительный объемный прогрев обрабатываемого образца. На область воздействия приходится меньшее значение энергии излучения при увеличении скорости сканирования. За счет быстрого прохождения луча происходит локальная обработка порошкового материала. При увеличении скорости сканирования от 100 до 130 мм/с порошковый материал скатывается в капли. При 140 мм/с и выше – капли расплава отрываются от подложки и разлетаются. Данное явление проявляется при недостаточной мощности воздействия лазерного излучения. Следовательно, при повышении скорости сканирования и неизменной мощности наблюдается недостаточный прогрев оплавляемого порошкового материала. Область воздействия лазерного излучения прогревается до температуры оплавления гранулы, но ее недостаточно для образования гомогенной ванны расплава. Это обстоятельство ограничивает использование многих металлов и сплавов для наплавления. При использовании многокомпонентных порошковых систем значительное влияние на качество образуемого покрытия оказывает большая разница температур плавления. Эти факторы препятствуют образованию равномерного валика. Не редким явлением в дорожке расплава является эффект Марангони, проявляющийся в виде конвективных потоков, вызванных градиентом поверхностного натяжения [9, 10]. Эффект проявляется в виде образования отдельных капель расплава, которые заполняются близлежащими частицами порошка. При этом образуются полости вокруг обработанной области воздействия, что в конечном счете приводит к появлению пористости и нарушению гомогенности структуры материала.
Значения параметров, способствующие формированию равномерного валика наплавленного материала на поверхности образца, были следующие: для порошка хром-никелевой стали мощность P = = 130 Вт, скорость сканирования υ = 60 мм/c, для меди P = 100 Вт, υ = 60 мм/с. При указанных параметрах образуются слои, обладающие хорошей адгезионной стойкостью.
Полученный градиентный материал может способствовать повышению эксплуатационных характеристик обрабатываемого изделия непосредственно при получении детали методом селективного лазерного плавления. Благодаря данному методу наплавки открывается возможность модификации множества характеристик поверхностного слоя обрабатываемой детали, таких как: повышение устойчивости к износу и окислению, коррозийная стойкость; повышение твердости изделия; изменение собственной частоты колебания изделия, красностойкость, теплопроводность и так далее.
ЗАКЛЮЧЕНИЕ
В данной работе определены характеристики порошковых материалов, необходимые для дальнейшей послойной наплавки из двух разных порошков на стальной подложке. Были подобраны оптимальные режимы наплавки для данных порошков и получены образцы градиентного материала из последовательно наплавленных порошковых материалов (хром-никелевая сталь и медь), которые в дальнейшем будут исследованы методами металлографии. Также был установлен ряд особенностей данной технологии наплавки, в том числе необходимость постоянного изменения режима обработки. Это вызвано постоянно изменяющейся теплопроводностью образуемого материала, состоящего из чередующихся слоев, имеющих различную величину теплопроводности и степень поглощения.
Список литературы
Alexandrov S., Usov S., Voznesenskaya A. et al. // J. Phys. Conf. Ser. 2019. V. 1164. Art. № 012001.
Смуров И.Ю., Мовчан И.А., Ядройцев И.А. и др. // Вестн. МГТУ Станкин. 2011. Т. 2. № 4. С. 144.
Lario D., Kallenrode M.B., Decker R.B. et al. // Astrophys. J. 2006. V. 653. P. 1531.
Кострицкий В.В., Лисовский А.Л. // Вестн. Полоцк. гос. ун-та. Сер. B. Промышл. прикл. науки. 2013. № 3. С. 97.
Yadroitsev I., Gusarov A., Yadroitsava I. et al. // J. Mater. Proc. Techno. 2010. V. 210. № 12. P. 1624.
Tolochko N.K., Khlopkov Y.V., Mozzharov S.E. et al. // Rapid Prototyping J. 2000. V. 6. № 3. P. 155.
Chernikov A.S., Voznesenskaya A.A., Davydov N.N. et al. // J. Phys. Conf. Ser. 2018. V. 1109. Art. № 012062.
Voznesenskaya A., Kochuev D., Zhdanov A., et al. // J. Phys. Conf. Ser. 2018. V. 1109. Art. № 012056.
Сухов Д.И., Мазалов П.Б., Неруш С.В. и др. // Труды ВИАМ. 2017. № 8(56). С. 34.
Wang D., Wu S., Fu F. et al. // Mater. Design. 2017. V. 117. P. 121.
Дополнительные материалы отсутствуют.
Инструменты
Известия РАН. Серия физическая