Известия РАН. Серия физическая, 2020, T. 84, № 6, стр. 887-891
Анализ продуктов электрохимической эксфолиации графита методами резерфордовского обратного рассеяния и ренгеновской дифрактометрии
Н. Г. Савинский 1, Н. С. Мелесов 1, Е. О. Паршин 1, С. В. Васильев 1, В. И. Бачурин 1, *, А. Б. Чурилов 1
1 Федеральное государственное бюджетное учреждение науки “Физико-технологический институт
имени К.А. Валиева” Российской академии наук, Ярославский филиал
Ярославль, Россия
* E-mail: vibachurin@mail.ru
Поступила в редакцию 09.01.2020
После доработки 07.02.2020
Принята к публикации 26.02.2020
Аннотация
Методами рентгеновской дифрактометрии и резерфордовского обратного рассеяния исследован процесс электрохимической эксофолиации графита. Показано, что данный процесс позволяет получать частицы графита с уменьшенным более чем в два раза размером кристаллитов и, соответственно, числа графеновых слоев в них. Установлено влияние параметров процесса эксфолиации на химический состав получаемых частиц графита.
ВВЕДЕНИЕ
Уникальные электронные, механические, оптические, теплофизические свойства графена делают его кандидатом номер один для следующей генерации электронных, оптоэлектронных приборов и сенсорики [1–3]. Среди многочисленных способов получения графена методы эксфолиации отличаются низкой стоимостью и технологической простотой процесса. Процесс эксфолиации имеет несколько смысловых значений: отшелушивание, расслоение, отслоение. К существующим методам эксфолиации относятся CВЧ-обработка, отрывание скотчем, размол в шаровых мельницах, ультразвуковая обработка углерода в жидкой фазе и другие. Их классифицируют как физические методы, которые дают продукты высокого качества, но с малыми выходами (менее 5%), а также с низким латеральным размером чешуйки графена, менее 1 мкм. Химическая эксфолиация, обычно ассоциируемая с методом Хаммерса для синтеза оксидов графена, – достаточно гибкий технологический метод с хорошим выходом продукта.
Сущность метода – диффузия ионов из раствора в межслойное пространство графитовых слоев под действием электрического поля. И катодный. и анодный потенциалы способны продвигать “гостевые” ионы, которые в дальнейшем осуществляют структурную деформацию в графитовых рабочих электродах [4]. Катионная (графит используется в качестве катода) интеркаляция в основном проходит в среде органики, а анионная интеркаляция проводится преимущественно в водных растворах электролитов и занимает значительно меньшее время по сравнению с катионной. Однако получающийся в обоих случаях продукт по своим свойствам далек от графена, так как содержит значительное количество дефектов в виде кислородных групп [5]. Даже после восстановления кислородные группы не удаляются полностью [6]. Кроме того, он представляет собой частицы графита с несколькими слоями, которые требуют длительной обработки ультразвуковой (УЗ) или СВЧ-обработки для разделения слоев.
Электрохимическая эксфолиация рассматривается сегодня как перспективная стратегия производства графена в промышленных масштабах с высокой эффективностью и низкой ценой. Одним из важнейших вопросов технологии эксфолиации графита является состав и качество продуктов. Среди многочисленных публикаций (см., например, обзор [7]), посвященных этой технологии, существует малое число работ, в которых относительно подробно освещены вопросы влияния параметров эксфолиации графита на размеры и химический состав продуктов процесса [8, 9]. Отчасти это связано с экспериментальными трудностями определения этих характеристик. Цель представленной работы – исследование влияния параметров электрохимической эксфолиации графита на химический состав и размеры продуктов процесса методами спектроскопии резерфордовского обратного рассеяния (РОР) и рентгеновской дифрактометрии.
ЭКСПЕРИМЕНТ
В данной работе эксфолиацию проводили в двухэлектродной ячейке. В качестве анода использовалась графитовая фольга (иногда свернутая в трубку), а в качестве катодов – металлические фольги платины или нержавеющей стали. Коммерческая графитовая фольга “Графлекс” (производства РФ) 0.5 мм толщиной, имеющая содержание углерода 99.5% использовалась после сушки при 100°С в течение 5 часов. Для приготовления рабочих растворов электролитов использовали деионизованную воду, в которой растворяли сульфат аммония (NH4)2SO4 квалификации “о. с. ч.” в необходимой концентрации перемешиванием до полного растворения на магнитной мешалке. После приготовления раствора электролита графитовый анод и платиновый катод помещались в раствор электролита. Процесс проводился в потенциостатическом режиме при 10 В. В процессе эксфолиации выделяются пузыри газа на обоих электродах, в раствор переходят частицы графита. По окончании процесса суспензию графита фильтровали через 2 мкм ПТФЭ-фильтр, обильно промывали водой для удаления остатков электролита, и затем один раз изопропанолом. Сушили в сушильном шкафе 24 ч при 60°С. В табл. 1 приведены условия процесса эксфолиации образцов и исходной графитовой фольги.
Таблица 1.
Условия проведения процесса электрохимической эксфолиации графитовой фольги
№ | Образец | Условия проведения эксфолиации | Концентрация (NH4)2SO4 |
Напряжение, В |
---|---|---|---|---|
1 | О1 | Катод Pt, анод графитовая фольга | 3.0 M | 10 |
2 | О2 | Катод Pt, анод графитовая фольга | 0.1 M | 10 |
3 | О3 | Катод Pt, анод графитовая фольга. Аскорбиновая кислота (0.01 M) | 3.0 M Ascorbic Acid 0.01 M |
10 |
4 | О4 | Исходная графитовая фольга | – | – |
Метод электронной микроскопии с использованием сканирующего электронного микроскопа “SUPRA” применяли для исследования процесса эксфолиации графита и морфологии его продуктов.
Фазовый анализ продуктов эксфолиации методом рентгеновской дифракции проводили на рентгеновском дифрактометре ARLX’Tra при следующих режимах и параметрах: излучение CuKα с длиной волны $\lambda = 0.15418$ нм; ускоряющее напряжение 35 кВ; ток накала рентгеновской трубки 40 мА.
Элементный состав образцов определяли методом резерфордовского обратного рассеяния (РОР). В качестве образцов использовались три таблетки из спрессованного продукта эксфолиации и пластина графита как эталон. Измерения проводились на установке K2MV (HVEE). Использовали ионы He+ с энергией 1.0 MэВ при нормальном падении пучка. Регистрация рассеянных ионов осуществлялась под углом θ = 150° с помощью полупроводникового детектора с поверхностным барьером, имеющего разрешение 13 кэВ. Телесный угол детектора равен 3.415 мср. Доза облучения во всех экспериментах составляла 54 мкКл при величине ионного тока на образце 40 нА.
РЕЗУЛЬТАТЫ И ИХ ОБСУЖДЕНИЕ
В процессе электрохимической эксфолиации графитовый электрод после подачи напряжения в течение нескольких секунд сильно деформируется, расширяется, как с краев, так и в плоскости. Через 1–2 минуты с поверхности фольги начинают отслаиваться чешуйки графена. Видимое газообразование на электродах способствует деформации структуры еще больше. Структура набухает, вспучивается, трескается, становится похожей на елочную бумажную гирлянду. Толщина фольги увеличивается более чем в 10 раз. На рис. 1 представлена характерная поверхность эксфолиированного графита. Это складчатая поверхность хаотично расположенных графитовых чешуек, причем края имеют тенденцию к скручиванию. Измерение толщины слоя графитовой пачки возможно только на торце края, что практически сделать достаточно трудно. На рис. 2 представлена фотография края графитовой эксфолиированной чешуйки, толщина которой изменяется от 8 до 16 нм. Чтобы получить статистически достоверный результат потребуется значительный массив данных, получить который чрезвычайно трудоемко. Поэтому нами для оценки толщины пластин некоторого числа атомарных слоев был использован метод, основанный на анализе рентгеновской дифракции порошка эксфолиированного графита.
На рис. 3 представлены дифрактограммы эталонного и эксфолиированного образцов графита. Данные идентификации дифрактограмм характеризуют продукты эксфолиации графита как многослойные структуры, которые содержат в основном гексагональную структуру ABAB (2H), как и исходная графитовая фольга. Кроме того, процесс обработки графита приводит к увеличению пиков, соответствующих орторомбической ABCABC (3R) структуре.
Основной дифракционный пик первого порядка, соответствующий грани (002), наблюдается при θ = 26.54° и 26.34° для фольги и частиц графита, что соответствует межплоскостному расстоянию в направлении (с), перпендикулярном плоскости (002), dс = 0.336 и 0.339 нм.
Размер блоков когерентного рассеяния (кристаллитов) оценивался по формуле Шеррера [10] в приближении лоренцевской формы линии на дифрактограмме:
При расчетах учитывались и экспериментальная полуширина дифракционного пика от графита, и полуширина эталона, в качестве которого использовался корунд α-Al2O3NIST-1976a.
Далее по формуле ${{N}_{c}} = {{{{L}_{c}}} \mathord{\left/ {\vphantom {{{{L}_{c}}} {{{d}_{c}}}}} \right. \kern-0em} {{{d}_{c}}}}$ можно определить количество слоев ${{N}_{c}}$ в кристаллите вдоль направления “c”.
Обработка полученных результатов показала, что размер кристаллитов ${{L}_{c}}$ в исходной фольге составляет $33 \pm 5$ нм, а в частицах графита после эксфолиации $12 \pm 3$ нм. То есть электрохимическая эксфолиация углеродной фольги приводит к более чем двукратному уменьшению размеров кристаллитов. В последнем случае кристаллиты содержат 30–50 слоев графена. Основываясь на классификации, предложенной редакцией журнала “CARBON” [11], при величине числа слоев графита более 10, согласно номенклатуре, материалы могут быть отнесены не к графенам, а к графитовым наноплатам и наночешуйкам.
Химический состав продукта эксфолиации получен методом РОР. На рис. 4 приводятся спектры РОР для всех четырeх образцов. Вертикальными маркерами с подписями химических элементов на графике обозначено положение поверхностных сигналов от соответствующих элементов.
Рис. 4.
Спектры резерфордовского обратного рассеяния образцов, полученных при различных условиях электрохимической эксфолиации графита, и исходной графитовой фольги: 1 – образец О1; 2 – О2; 3 – О3; 4 – О4.
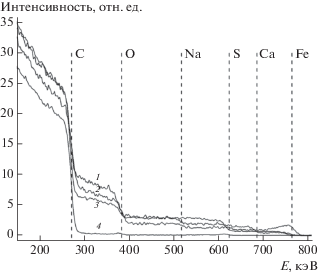
Результаты количественного анализа состава образцов методом РОР сведены в табл. 2.
Таблица 2.
Результаты элементного анализа образцов эксфолиированного графита методом резерфордовского обратного рассеяния (РОР)
№ | Содержание, ат. % | |||||
---|---|---|---|---|---|---|
C | O | Na | S | Ca | Fe | |
О1 | 80.7 | 16.7 | 1.9 | 0.08 | 0.36 | 0.06 |
О2 | 84.7 | 13.4 | 1.1 | 0.27 | 0.04 | 0.48 |
О3 | 92.7 | 6.1 | 0 | 1.1 | 0 | 0.15 |
О4 | 99.1 | 0.7 | 0 | 0.12 | 0 | 0.01 |
Анализ проведенных измерений позволяет сделать следующие выводы. Для исходной графитовой фольги содержание углерода к кислороду составляет 142, тогда как после проведения эксфолиации по условиям 1 (образец О1) – 4.83. Это характеризует процесс эксфолиации как окислительный. Получившийся графит декорирован кислородными группами, благодаря положительному потенциалу, используемому для кислых электролитов, например, серной кислоты. Так же окислительные процессы сопровождают эксфолиацию в растворах сульфониевых солей, используемых как электролиты. Во время электрохимической диссоциации воды генерируется весьма сильный окисляющий агент гидроксил-радикал OH* (Стандартный водородный электрод –2.8 В) [12]. Поэтому очень желательно удалить этот радикал и значительно улучшить качество конечного продукта [13, 14]. Второй образец имеет соотношение С/O равное 6.32. При уменьшении концентрации исходного электролита c 3 до 0.1 M процесс окисления замедляется, но при этом значительно уменьшается производительность процесса эксфолиации. В третьем случае в ходе эксфолиации использовался классический восстановитель – аскорбиновая кислота. Соотношение С/O 15.2 в этом случае выше, но, тем не менее, процесс окисления значителен и в этом случае. В дальнейшем необходимо исследовать процесс эксфолиации графитовой фольги путем подбора концентрации электролита и восстановителей с целью уменьшения негативного процесса окисления графита.
ЗАКЛЮЧЕНИЕ
Исследование методом рентгеновской дифрактометрии образцов графитовой фольги и продуктов электрохимической эксфолиации установило наличие двух кристаллографических фаз: гексагональной 2H и орторомбической 3R. Методами рентгеновской дифрактометрии и электронной микроскопии показано, что эксфолиированные образцы графита имеют практически в два раза меньшие размеры кристаллитов, которые содержат 30–50 графеновых слоев и их можно классифицировать как нанографиты.
Исследование методом РОР установило значительное окисление образцов графита в процессе электрохимической эксфолиации, связанное с генерацией сильного окислителя – гидроксильного радикала. Использование аскорбиновой кислоты. как антиоксиданта-восстановителя позволяет уменьшить окисление эксфолиированного продукта.
Работа выполнена в рамках государственного задания Ярославского филиала Физико-технологического института имени К.А. Валиева РАН Минобрнауки РФ по теме № 0066-2019-0003 на оборудовании Центра коллективного пользования “Диагностика микро- и наноструктур”.
Список литературы
Novoselov K.S., Geim A.K., Morozov S.V. et al. // Science. 2004. V. 306. P. 666.
Соловьев М.Е., Раухваргер А.Б., Савинский Н.Г. и др. // Журн. общ. химии. 2017. Т. 87. № 4 С. 677; Solov’ev M.E., Raukhvarber A.B., Savinskii N.G. et al. // Rus. J. Gen. Chem. 2017. V. 87. № 4. P. 805.
Hondred J.A., Medintz I.L., Claussen J.C. // Nanoscale Horizons. 2019. V. 4. P. 735.
Yang S., Brüller S., Wu Zhong-Shuai et al. // J. Amer. Chem. Soc. 2015. V. 137. Art. № 13927.
Ambrosi A., Pumera M. // Chem. Eur. J. 2016. № 22. P. 153.
Huang X., Li S., Qi Z. et al. // Nanotech. 2015. V. 26. Art. № 105602.
Yang S., Lohe M.R., Müllen K. et al. // Adv. Mater. 2016. V. 28(29). Art. № 6213.
Huang. X., Li S. // Nanotech. 2015. V. 26. P. 105602.
Hofmann M., Wan Yu // Nanotech. 2015. V. 26. P. 335607.
Seehra M.S., Geddam U.K. // Carbon. 2015. V. 95. P. 818.
Bianco A., Cheng H.-W. // Carbon. 2013. V. 65. P.11.
Repine J.E., Eaton J.W., Anders M.W. et al. // J. Clin. Invest. 1979. V. 64. P. 1642.
Rao K.S., Senthilnathan J., Yung-Fang Liu et al. // Nature Sci. Rep. 2014. P. 6.
Yang S., Brüller S. // J. Amer. Chem. Soc. 2015. V. 13. P. 13927.
Дополнительные материалы отсутствуют.
Инструменты
Известия РАН. Серия физическая