Известия РАН. Серия физическая, 2020, T. 84, № 7, стр. 1057-1064
Получение ультрадисперсных монокристаллов карбида кремния плазмодинамическим методом при разных способах инициирования дугового разряда
Д. С. Никитин 1, *, А. А. Сивков 1, 2, И. А. Рахматуллин 1
1 Федеральное государственное автономное образовательное учреждение высшего образования
“Национальный исследовательский томский политехнический университет”
Томск, Россия
2 Цзилиньский университет
Чанчунь, Китайская народная республика
* E-mail: nikitindmsr@yandex.ru
Поступила в редакцию 18.02.2020
После доработки 16.03.2020
Принята к публикации 27.03.2020
Аннотация
Исследован плазмодинамический синтез в системе Si–C. Монокристаллические частицы кубического карбида кремния средним размером до ~70 нм сформированы в сверхзвуковой струе углеродо-кремниевой электроразрядной плазмы, генерированной коаксиальным магнитоплазменным ускорителем с графитовыми электродами. Показано влияние способа инициирования дугового разряда в ускорительном канале на фазовый и гранулометрический состав продукта синтеза. Процесс предионизации прекурсоров, происходящий при использовании графитизации канала формирования плазменной структуры, позволяет осуществлять их более эффективную возгонку и получение частиц β-SiC без примесей материала прекурсоров (~99%).
ВВЕДЕНИЕ
Керамика из карбида кремния SiC уже несколько последних десятилетий активно используется в различных отраслях промышленности: химической промышленности, двигателестроении, машиностроении, металлургии, ядерной энергетике и других областях. Такое широкое применение карбида кремния обусловлено совокупностью уникальных физических характеристик, таких как высокая твердость (~30 ГПа), высокая термостойкость (на воздухе до температур ~1700°С, низкий коэффициент теплового расширения – 4.0 · 10–6 К–1), стойкость к химически агрессивным средам и к радиационному излучению (до 1016 нейтронов ∙ см–2). Наличие таких свойств обеспечивает работу изделий на основе SiC в жестких средах. Кроме того, карбид кремния является материалом с выдающимися полупроводниковыми свойствами (ширина запрещенной зоны ~3 эВ, высокая пробивная напряженность 4.0 МВ ∙ см–1), что позволяет использовать его для изготовления устройств силовой электроники, в том числе для эксплуатации в экстремальных условиях.
Особую важность имеет проблема синтеза ультрадисперсного карбида кремния, поскольку материалы в диспергированном состоянии могут демонстрировать уникальные сочетания свойств [1]. Известно, что наноразмерные частицы SiC используются для создания наноструктурированной керамики, в качестве армирующего материала для повышения износостойкости, твердости, прочности, вязкости разрушения и уменьшения трения [2–6], для создания наноразмерных электронных устройств, микро- (MEMS) и наноэлектромеханических (NEMS) систем, наносенсоров [7].
Использование ультрадисперсного карбида кремния позволяет дополнительно улучшить свойства изделий на его основе. Отсюда следует актуальность проблемы синтеза ультрадисперсного карбида кремния и получения на его основе наноструктурированной керамики. В настоящее время широко известный метод Ачесона является основным способом производства карбида кремния, поскольку он позволяет получать SiC в больших количествах, однако не может быть применен для синтеза наноструктур SiC вследствие больших размеров зерен порошка и неудовлетворительной структуры продукта. Наиболее распространенными альтернативными способами получения наноразмерного карбида кремния являются высокоэнергетические процессы, включая карботермический [8] и микроволновой [9] синтез, лазерный пиролиз [10], самораспространяющийся высокотемпературный синтез [11], различного рода плазменные технологии [12] и золь–гель метод [13]. Необходимые условия для синтеза SiC (прежде всего, температура более 2545 ± 40°C) также могут быть достигнуты методами, основанными на использовании низкотемпературной плазмы [14]. Среди этих методов можно выделить плазмодинамический синтез, который основан на применении гиперскоростной струи кремний-углеродной электроразрядной плазмы, генерируемой посредством импульсного сильноточного коаксиального магнитоплазменного ускорителя (КМПУ). Такой метод характеризуется быстродействием (длительность процесса менее 1 мс), высокой скоростью кристаллизации и монокристаллической структурой частиц продукта [15, 16]. В настоящей работе рассмотрены возможные варианты реализации инициирования дугового разряда в ускорительном канале ускорителя, их влияние на процесс возгонки прекурсоров, эффективность плазмодинамического синтеза, фазовый и гранулометрический состав продукта.
ЭКСПЕРИМЕНТАЛЬНАЯ ЧАСТЬ
Плазмодинамический синтез ультрадисперсного карбида кремния реализован с помощью экспериментальной установки на базе емкостного накопителя энергии с максимальными зарядным напряжением Uзар = 5 кВ и емкостью конденсаторных батарей C = 28.8 мФ, который служил источником импульсного электропитания для КМПУ с графитовыми электродами. Общая конструкция КМПУ представлена на рис. 1. В канал формирования плазменной структуры, образуемый изолятором центрального электрода и графитовой вставкой, закладываются исходные прекурсоры – смесь порошкообразных кремния Si и углерода C в соотношении, близком к стехиометрическому. При замыкании ключа по разрушаемой перемычке из токопроводящего материала, нанесенного по поверхности изолятора в канале формирования плазменной структуры, и по смеси прекурсоров начинает протекать ток разряда, происходит возгонка прекурсоров в плазменное состояние с образованием сильноточного дугового разряда, который ускоряется в коаксиальной системе вдоль графитового ускорительного канала за счет собственного магнитного поля электрода-ствола и дополнительного магнитного поля индуктора. При выходе плазменной структуры из ускорительного канала в свободном пространстве камеры-реактора, наполненной аргоном при нормальных условиях, формируется сверхзвуковая плазменная струя, в условиях которой происходит синтез SiC, его высокоскоростное распыление в инертной атмосфере с формированием монокристаллических частиц.
Из цикла предшествующих работ по проблеме плазмодинамического синтеза в углеродных системах следует, что осциллограммы тока и напряжения имеют время предыонизации [17] – время от подачи напряжения до возникновения плазменной струи и начала ее ускорения, включающее, прежде всего, время разогрева исходной смеси. По-видимому, время предыонизации оказывает значительное влияние на фазовый состав конечного продукта, поскольку именно в этот момент происходит или более плавный, или скачкообразный переход исходных реагентов в плазменное состояние, т.е. эффективность процесса синтеза зависит от того, насколько исходные прекурсоры “подготовлены” на этапе предыонизации. Это определяется условиями инициирования дугового разряда, в особенности способом его инициирования и начальным сопротивлением перемычки.
С целью определения наиболее эффективного способа инициирования дугового разряда в ускорительном канале КМПУ в настоящей работе рассмотрены два варианта разрушения токопроводящей перемычки между графитовым центральным электродом и поверхностью ускорительного канала, представленные на рис. 2: 1) в виде углеродных волокон (а), натягиваемых из дна канала формирования плазменной структуры до внешней конусообразной поверхности изолятора – места соприкосновения с электродом-стволом; и 2) путем графитизации поверхности изолятора (б) – нанесением тонкого слоя графитового аэрозоля на внутреннюю поверхность канала формирования плазменной структуры, а также на поверхность заложенной смеси прекурсоров Si–C.
Рис. 2.
Изображение узла центрального электрода при использовании: а − углеволокон; б − графитизации; 1 – центральный электрод, 2 – изолятор центрального электрода, 3 – графитовая вставка, 4 – канал формирования плазменной структуры, 5 – графитовый ускорительный канал.
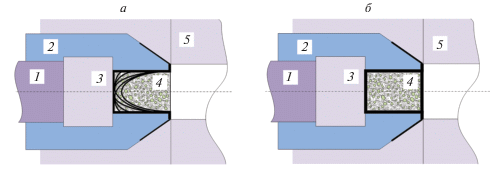
Эксперименты с использованием разных способов инициирования плазменной струи проведены при одинаковых энергетических параметрах и эксплуатационных условиях: емкость конденсаторных батарей C = 6 мФ, зарядное напряжение Uзар = 3 кВ. При проведении экспериментов предполагалось, что способ инициирования дугового разряда будет влиять на фазовый состав продукта синтеза в результате изменения времени и характера перехода смеси прекурсоров в плазменное состояние. Важнейшим показателем, позволяющим проследить эту зависимость, является, очевидно, форма осциллограмм рабочего тока плазменной перемычки и напряжения на электродах. На рис. 3 изображены осциллограммы рабочего напряжения u(t) и тока i(t) (а и б), кривые мощности p(t) и тока i(t) (в и г) во всех экспериментах; на основании осциллограмм рассчитаны экспериментальные параметры, приведенные в табл. 1, в том числе время задержки импульса Δt, максимальные значения тока Im, напряжения Um и мощности Pm разряда и подведенной энергии W.
РЕЗУЛЬТАТЫ И ИХ ОБСУЖДЕНИЕ
Момент времени Δt является началом работы КМПУ. В этот момент по замкнутому контуру, включающему конденсаторные батареи емкостного накопителя энергии, центральный электрод и электрод-ствол, начинает протекать увеличивающийся во времени ток i(t). В табл. 1 видно, что основные энергетические параметры не отличаются существенно (в случае использования графитизации присутствует даже некоторое снижение энергетических параметров), что позволяет сравнивать результаты проведенных серий экспериментов. При наличии некоторых незначительных отличий осциллограмм тока и напряжения в рабочем режиме, тем не менее важные отличия наблюдаются в осциллограммах в докоммутационном периоде.
В случае (1) при использовании углеволокон начальное сопротивление которых R0 составляет около 1.0 Ом, ток разряда начинает протекать с момента t = 0 при приложения напряжения, как видно на рис. 3 (кривые 1). Это приводит к электрическому взрыву проводников – углеродных волокон. Под действием возникшего импульса мощности, показанного на рис. 3в, 3г, происходит выброс из канала формирования плазменной структуры порошкообразной массы прекурсоров Si + С, что уменьшает вероятность их полной возгонки в плазменное состояние и высокоэффективное протекание в дальнейшем плазмохимического синтеза β-SiC. Вероятная феноменологическая модель электрического взрыва углеволокон представлена на рис. 4а. Длительность электровзрывного импульса мощности амплитудой до 80 МВт составляет около 10 мкс. Ток достигает уровня в несколько кА и снижается практически до нуля. После этого происходит повторный пробой ионизованного промежутка и формирование дуговой стадии разряда с повышенным уровнем мощности на начальном этапе ускорения плазменной структуры.
Рис. 4.
Феноменологические модели возгонки прекурсоров в случае инициирования плазменного потока посредством углеродных волокон (а) и графитизации (б). Этапы возгонки при использовании углеродных волокон: 1 – исходное состояние (толстые линии – углеродные волокна), 2 – электрический взрыв волокон, 3 – образование дугового разряда и движение образовавшейся плазменной струи (тонкие черные линии сзади – границы плазменного потока, толстые черные линии – головная ударная волна). Этапы возгонки при использовании графитизации: 1 – начальное состояние (толстые линии – слой графитового аэрозоля), 2 – процесс предыонизации (толстые и тонкие линии внутри канала формирования плазменной структуры – каналы повышенной проводимости), 3 – образование “горячих точек” (Θmax) и тепловой пробой.
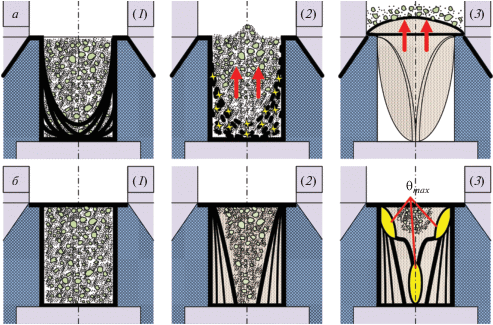
В случае (2) при использовании графитизации поверхности изолятора при R0 около 10 кОм электровзрыв не происходит, и значительно увеличивается длительность интервала времени до соответствующего момента Δt2, как это видно на рис. 3 (кривые 2). Протекающие в течение этого периода времени до Δt2 процессы хорошо описываются теорией теплового пробоя, обусловленного тепловыми процессами, протекающими в материале при воздействии на него электрического поля. Этот вид пробоя происходит при повышенной проводимости твердых диэлектриков и больших диэлектрических потерях в результате протекания тока внутри диэлектрика [18]. Состав межэлектродного пространства электрически неоднороден, поскольку углеродный слой перемычки и материал прекурсоров обладают проводимостью. При подаче напряжения возникает множество дискретных каналов повышенной проводимости, обеспечивающих джоулев разогрев перемычки и массы прекурсоров. Это приводит к еще большему нарастанию тока в цепи, так как сопротивление межэлектродного участка резко (экспоненциально) уменьшается. Происходит нарушение теплового равновесия, процесс становится лавинообразным: проводимость и температура взаимно “раскачивают” друг друга. В итоге происходит дальнейшее нарастание тепла вплоть до момента, когда количество теплоты, которое выделяется в объеме заложенных прекурсоров за счет диэлектрических потерь, превышает количество теплоты, которое система способна рассеивать в текущих условиях [19]. Это – момент теплового разрушения материала, иными словами, возникает тепловой пробой [20] с последующим формированием плазменной структуры дугового разряда.
Феноменологическая картина развития теплового пробоя приведена на рис. 4б, на котором линиями показаны поле градиента температуры и каналы повышенной проводимости. Наличие градиента температур по толщине смеси в канале формирования плазменной структуры ведет к искажению электрического поля. В итоге каналы повышенной проводимости сливаются, появляются так называемые “горячие точки” [21]. Канал теплового пробоя развивается именно от таких горячих точек к электродам. Свою роль в тепловом пробое может играть и пористость порошкообразного материала, а также возможное наличие в нем молекул кислорода. В порах возникают наибольшие релаксационные потери и плотность тока, и выделяется большее количество теплоты, что может приводить к возникновению ионизационного пробоя как разновидности теплового пробоя [22, 23].
Время развития теплового пробоя оценивается по формуле:
При напряженности электрического поля в канале формирования плазменной структуры E = = 3 ∙ 105 В ∙ м–1 и теоретических параметрах кремния (удельная проводимость γ = 833.3 Ом–1 ∙ м–1, температурный коэффициент α = 1.7 ∙ 10–3 К–1, удельная теплоемкость c = 714 Дж ∙ кг–1 ∙ К–1, плотность ρ = 2328 кг ∙ м–3) расчетное время возникновения пробоя составляет tпр = 54.6 ∙ 10–6 с, что сопоставимо со временем Δt2 = 68 мкс, определенным по осциллограммам реального процесса. Это свидетельствует о тепловом характере пробоя при инициировании дугового разряда с помощью графитизации поверхности изолятора в условиях заполнения канала формирования плазменной структуры смесью прекурсоров Si + C. При этом происходит нагрев и перевод в плазменное, химически активное состояние всей массы порошкообразных прекурсоров за время развития теплового пробоя или время предыонизации. Возникновение в данной системе электрического пробоя исключено, поскольку он возникает в материале тогда, когда полностью исключены не только тепловые процессы в нем, но и устранены такие побочные причины, как поверхностные разряды, ионизация воздушных включений в самом диэлектрике [24].
Полученные в процессе экспериментов с разным способом инициирования порошкообразные продукты исследованы методом рентгеноструктурного анализа. На рис. 5 приведены в сравнении рентгеновские дифрактограммы. Совокупность когерентных рефлексов показывает, что продукт включает в себя несколько кристаллических фаз, преимущественно образуется структура карбида кремния кубической сингонии β-SiC. Пять основных высокоинтенсивных пиков дифрактограммы при углах 2θ ≈ 36°, 41°, 60°, 71° могут быть проиндексированы индексами Миллера как 111, 200, 220 и 311 рефлексы β-SiC (JCPDS № 00-029-1129, пространственная группа F-43m 216). Также имеются пики слабой интенсивности при углах 2θ ≈ 29°, 26°, 44°, 47°, которые могут быть отнесены к соответствующим кристаллическим плоскостям кубического кремния Si (JCPDS № 00-027-1402, пространственная группа F43/d-32/m 227) и углерода C в виде графита (JCPDS 00-041-1487, пространственная группа P6-3mc186). Эти пики слабой интенсивности относятся к фазам непрореагировавших прекурсоров кремния и углерода, атомы которых не вступили в реакцию соединения между собой с образованием карбида кремния.
Рис. 5.
Рентгеновские дифрактограммы продуктов, синтезированных при использовании углеволокон и графитизации.
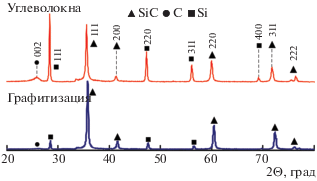
На основании дифрактограмм синтезированных продуктов производился количественный рентгеноструктурный анализ методом Ритвельда, основные результаты которого сведены в табл. 2, где указаны расчетные значения содержания и средние размеры областей когерентного рассеяния (ОКР) карбида кремния кубической сингонии, кремния и углерода, а также указан соответствующий фактор добротности расчета s = Rwp/Rexp, приемлемые значения которого свидетельствуют о корректности расчета. Вне зависимости от способа инициирования дугового разряда, наибольшее содержание в продукте синтеза имеет β-фаза карбида кремния, что показывает адекватность выбора экспериментальных параметров и доказывает исходное предположение о возможности синтеза карбида кремния в гиперскоростной струе, генерируемой магнитоплазменным ускорителем.
Таблица 2.
Результаты рентгеноструктурного анализа продуктов синтеза
№ | Способ инициации | Содержание фаз ω; ОКР | s = Rwp/Rexp | |||
---|---|---|---|---|---|---|
SiC | Si | C | ||||
1 | Углеволокна | ω, % | 50.5 | 31.7 | 17.8 | Rwp = 26.6 Rexp = 17.5 s = 1.52 |
ОКР, нм | 105 | 98 | 15 | |||
2 | Графитизация | ω, % | 91.7 | 5.4 | 2.9 | Rwp = 28.7 Rexp = 15.1 s = 1.90 |
ОКР, нм | 63 | 20 | 22 |
Согласно данным анализа продуктов (табл. 2), в случае графитизации имеет место значительное повышение содержания фазы β-SiC при минимальном содержании непрореагировавших прекурсоров. Это связано с изменением характера периода предыонизации: процесс, близкий к электровзрыву в случае использования углеволокон, способствует резкому выбросу порошкообразной массы в ускорительный канал и, соответствено, менее эффективному вовлечению прекурсоров в химическую реакцию; в случае использования графитизации удается уже на стадии предыонизации провести активацию исходного сырья и более плавно ввести его в зону химической реакции. Различие в степени ввода прекурсоров в химическую реакцию подтверждается многократным уменьшением расчетной величины ОКР кремния в случае использования графитизации. Это означает, что при применении углеволокон исходные прекурсоры, в частности кремний, частично были выброшены в ускорительный канал из канала формирования плазменной структуры в результате импульса мощности, поэтому в конечном продукте присутствуют крупные частицы непрореагировавшего кремния.
Результаты рентгеноструктурного анализа подтверждаются анализом представленных на рис. 6 СЭМ- и ПЭМ-снимков порошков, синтезированных при разных способах инициирования. Как СЭМ-, так и ПЭМ-снимки демонстрируют типичные кристаллические частицы SiC, которые в основном имеют размеры не более 500 нм и различимые формы многогранников. Разница между синтезированными продуктами заключается в том, что продукт, полученный с использованием углеволокон, содержит крупные (>1 мкм) объекты неправильной формы (1). Такие объекты (1) идентифицируются по соответствующей дифракции на выделенной области и темнопольным снимкам (рис. 6в) как кубический кремний. По-видимому, они представляют собой деформированные частицы исходного неионизованного кремниевого прекурсора, который был выброшен из канала формирования плазменной структуры под действием генерируемого импульса мощности. Наряду с крупными частицами кремния в продукте содержатся типичные частицы β-SiC (2).
Рис. 6.
Типичные СЭМ (а, г) ПЭМ (б, в, д, е) изображения продуктов, синтезированных при инициировании разряда путем углеродных волокон (а–в) и графитизацией (г–е).
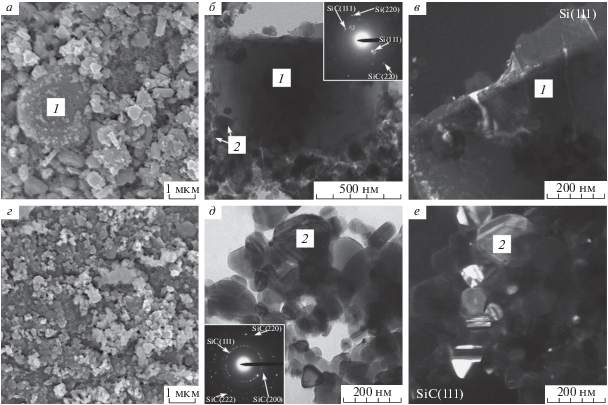
Судя по ПЭМ-снимкам на рис. 6д, 6е, продукт, синтезированный с использованием графитизации, в основном включает в себя частицы в форме усеченных пирамид с треугольным основанием (2), линейный размер которых составляет до 250 нм, толщина – до 80 нм. Однородный характер микроструктуры образца подтверждается дифракцией на выделенной области, которая имеет более выраженный характер и включает в себя только систему дебаевских колец кубического карбида кремния, но практически не содержит рефлексов, соответствующих иным побочным фазам. Большинство частиц (2) идентифицированы по темнопольным микроснимкам как кубический карбид кремния β-SiC. Крупные частицы исходного кремния в продукте отсутствуют. Кроме того, в случае использования графитизации частицы продукта имеют форму, соответствующую для своей сингонии, что подчеркивается отчетливыми экстинкционными контурами, и это, по-видимому, также связано с подготовкой прекурсоров на этапе предыонизации.
ЗАКЛЮЧЕНИЕ
Ультрадисперсный карбид кремния получен в сверхзвуковой струе углерод-кремниевой электроразрядной плазмы, генерируемой коаксиальным магнитоплазменным ускорителем с графитовыми электродами. Рассмотрено влияние способа инициирования дугового разряда на процесс возгонки прекурсоров и эффективность плазмодинамического синтеза SiC. Изменение способа инициирования плазменной струи влияет, прежде всего, на время бестоковой паузы. В случае использования углеволокон наблюдается процесс, близкий к электровзрыву проводников с последующим частичным выбросом исходной порошкообразной массы из канала формирования плазменной структуры в ускорительный канал, что приводит к неполной ионизации прекурсоров и пониженному содержанию фазы β-SiC в составе продукта при присутствии крупных частиц кремния. Применение графитизации приводит к увеличению времени Δt и предыонизациипрекурсоров на этапе формирования дугового разряда, более полному протеканию плазмохимической реакции и возрастанию содержания β-SiC. Кроме того, следует отметить высокую технологичность способа инициирования с графитизацией поверхности изолятора, обеспечивающего простоту подготовки ускорителя и надежность его работы.
Работа выполнена в рамках Программы повышения конкурентоспособности ТПУ.
Список литературы
Андриевский Р.А., Рагуля А.В. Наноструктурные материалы: Учеб. пособ для студ. вузов. М.: ИЦ “Академия”, 2005. 192 с.
Parvizi S., Ahmadi Z., Zamharir M.J. et al. // Int. J. Refract. Met. Hard Mater. 2018. V. 75. P. 10.
Ahmadkhaniha D., Eriksson F., Leisner P. et al. // J. Alloys Compounds. 2018. V. 769. P. 1080.
Atrian A., Nourbakhsh S.H. // Mater. Res. Expr. 2018. V. 5. № 8. Art. № 085014.
Akbarpour M.R., Alipour S. // Ceram. Int. 2017. V. 43. № 16. P. 13364.
Moazami-Goudarzi M., Akhlaghi F. // Tribol. Int. 2016. V. 102. P. 28.
Mehmood Z., Haneef I., Udrea F. // Mater. Des. 2018. V. 157. P. 412.
Omidi Z., Ghasemi A., Bakhshi S.R. // Ceram. Int. 2015. V. 41. № 4. P. 5779.
Zhang X. Song B., Zhang Y. et al. // Ceram. Int. 2018. V. 44. № 17. P. 21309.
Liu J., Qiao Y., Zhang P. et al. // Surf. Coat. Technol. 2017. V. 321. P. 491.
Xu R.-R., Su Q. // Mod. Inorg. Synth. Chem. 2017. P. 9.
Lee C.-H. Rai P., Moon S.-Y. et al. // Ceram. Int. 2016. V. 42. № 15. P. 16469.
Mollicone J.,Ansart F., Lenormand P. et al. // J. Eur. Ceram. Soc. 2014. V. 34. № 15. P. 3479.
Rai P., Park J.-S., Park G.-G. et al. // Adv. Powder Technol. 2014. V. 25. № 2. P. 640.
Pak A., Sivkov A., Shanenkov I. et al. // Int. J. Refract. Met. Hard Mater. 2015. V. 48. P. 51.
Sivkov A.A., Nikitin D.S., Pak A.Y. et al. // Tech. Phys. Lett. 2013. V. 39. № 1. P. 107.
Фортов В.Е. Энциклопедия низкотемпературной плазмы. Вводной том II. Книга II. М.: Наука, 2000. 648 с.
Wadhwa C.L. High voltage engineering. New Delhi: New Age Int., 2007. 312 p.
Küchler A. High voltage engineering fundamentals. Technol. Appl. Berlin: Springer, 2018. 650 p.
Франц В. Пробой диэлектриков. М.: Изд-во иностр. лит., 1961. 208 c.
Arora R., Mosch W. High voltage and electronic insulators engineering. New Jersey: John Wiley&Son Inc. 2011. 394 p.
Колесов С.Н., Колесов И.С. Материаловедение и технологические конструкционные материалы. М.: Высшая школа, 2004. 519 с.
Привалов Е.Е. Электротехническое материаловедение: уч. пособ. М.: Директ-Медиа, 2015. 234 с.
Бабиков М.А. Комаров Н.С., Сергеев А.С. Техника высоких напряжений. М.: Госэнергоиздат, 1963. 670 с.
Дополнительные материалы отсутствуют.
Инструменты
Известия РАН. Серия физическая