Известия РАН. Серия физическая, 2021, T. 85, № 11, стр. 1596-1599
Система контроля акустического излучения разрядных процессов на электрической подстанции для целей диагностики технического состояния изоляционного оборудования
Д. А. Иванов 1, *, М. Ф. Садыков 1, Д. А. Ярославский 1, А. В. Голенищев-Кутузов 1, Т. Г. Галиева 1
1 Федеральное государственное бюджетное образовательное учреждение высшего образования
“Казанский государственный энергетический университет”
Казань, Россия
* E-mail: ivanov.da@kgeu.ru
Поступила в редакцию 21.06.2021
После доработки 05.07.2021
Принята к публикации 28.07.2021
Аннотация
Разработан метод контроля над состоянием высоковольтной изоляции открытых электрических подстанций на основе построения акустического слепка излучаемых неисправным оборудованием звуковых и ультразвуковых колебаний. Описывается методология построения системы мониторинга, приборная реализация и способ обработки полученной диагностической информации.
ВВЕДЕНИЕ
Акустические методы широко используются в неразрушающем контроле оборудования и материалов, например, ультразвуковые эхо-импульсные методы, методы акустической эмиссии и др. Выделяемая при частичном разряде (ЧР) энергия вызывает в материале диэлектрика химические и структурные изменения, происходит излучение электромагнитных волн, выделение тепла и акустического давления в виде импульсов. В связи с этим широко распространены методы регистрации частичных разрядов на основе детектирования подобных явлений [1–3]. Комплексные методы, основанные на анализе сразу нескольких физических явлений, обладают большей чувствительностью и эффективностью и так же находят практическое применение [4].
Регистрация акустического сигнала ЧР основана на обнаружении упругих волн механических колебаний, возбуждаемых во время разряда. ЧР происходит как “микровзрыв” (микроискра), который возбуждает механическую волну, распространяющуюся сферически во все стороны (сферический волновой фронт в случае поверхностного ЧР). Разряд действует как точечный источник акустических волн. Поскольку продолжительность разряда мала, акустический спектр излучаемой волны может быть очень широким (до нескольких МГц). Интенсивность излучаемой акустической волны пропорциональна энергии, выделяемой в разряде, а ее амплитуда пропорциональна квадратному корню из энергии разряда. Зависимость между амплитудой акустической волны и величиной разряда (в кулонах) является линейной [5]. Эта волна может быть зарегистрирована датчиком или преобразователем, данные с которого можно собрать и проанализировать. При этом форма сигнала зависит от источника ЧР и самого датчика.
Объектом данного исследования являются разрядные процессы в опорно-стержневой изоляции открытых электрических подстанций. На подстанциях такого типа применяются полимерные и фарфоровые изоляторы. ЧР в них возникают на внутренних и поверхностных дефектах [5].
В однородной среде ультразвуковые волны распространяются прямолинейно. Однако если на их пути возникает поверхность раздела сред, то часть ультразвукового потока отражается, а часть, преломляясь, проникает далее. Чем значительнее различие в акустическом сопротивлении сред, тем большая часть энергии отражается на их границе, а также значительнее угол преломления. Волновое сопротивление определяется выражением
где ρ – плотность среды, ν – скорость УЗ в данной среде. На границе фарфор/полимер – воздух отражение практически полное, поэтому мы далее при рассмотрении ЧР в изоляторах будем говорить о регистрации разрядов в поверхностных дефектах.Развитие цифровой техники, повышение скорости компьютерного сбора данных сделали доступными создание и экспериментальное использование методов микрофонных решеток для локализации и количественной оценки точечных источников акустического сигнала на площадях в несколько десятков квадратных метров [6].
АКУСТИЧЕСКИЙ КОНТРОЛЬ РАЗРЯДНЫХ ПРОЦЕССОВ НА ЭЛЕКТРИЧЕСКОЙ ПОДСТАНЦИИ
Для локализации источника ультразвука от возникающих на изоляции ЧР была создана система мониторинга высоковольтных изоляторов (ВИ) на подстанции открытого типа. Система представляет собой четыре микрофонные решетки, установленные по периметру подстанции (рис. 1).
Рис. 1.
Схема расположения микрофонных решеток на подстанции: 1 – микрофонные решетки, 2 – локализуемый источник ультразвукового излучения.
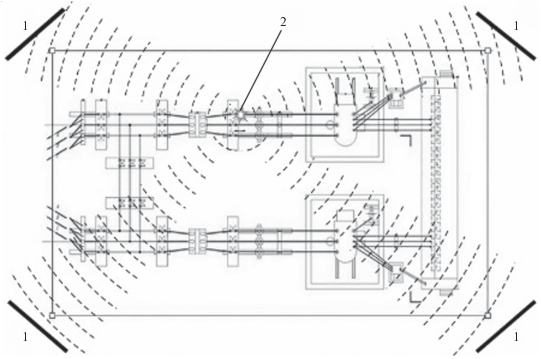
В предлагаемой системе мониторинга микрофонная решетка состоит из четырех пьезоэлектрических приемников с резонансной частотой 41 кГц. Схема одного канала приведена на рис. 2. В схеме предусилителя был использован операционный усилитель LM324A, коэффициент усиления сигнала схемы усиления составляет 2000. Такое решение необходимо для аналогового сбора данных для дальнейшей обработки. Акустическая волна от ЧР возбуждает пъезоэлектрический кристалл приемника, создавая небольшое переменное напряжение, которое усиливается предусилителем, а затем фильтруется. На рис. 3 приведены усиленные сигналы на каждом приемнике для одного и того же ЧР.
После предусиления сигналы собираются на аналого-цифровом преобразователе USB-6251 и обрабатываются на персональном компьютере. Полученное в результате программной обработки изображение места возникновения ультразвука накладывается на кадр с видеокамеры с указанием интенсивности. Вся конструкция микрофонной решетки заключена в металлический корпус для минимизации наведенного электромагнитного шума от высоковольтного оборудования.
Для локализации акустического источника с помощью микрофонной решетки исследуется кросс-корреляция сигналов датчиков [7, 8]. Пространственное расположение приемников с обозначениями их порядковых номеров указаны на рис. 4. Источник сигнала – rS. Кросс-корреляция выполняется для сигналов пар приемников r1–r4 и r2–r3.
Функция кросс-корреляции для пары приемников r1–r4
(2)
${{R}_{{{{r}_{1}},{{r}_{4}}~}}}\left( T \right) = \sum\limits_{n = - \infty }^\infty {{{r}_{1}}\left( n \right){{r}_{4}}\left( {n + T} \right)} .$Последовательность получаемого сигнала каждого приемника делится на равные отрезки из N точек. Отрезки с нулевым уровнем сигнала отбрасываются, что позволяет значительно повысить отношение “сигнал/шум”. Получаемое значение функции ${{R}_{{{{r}_{1}},{{r}_{4}}~}}}\left( T \right)$ определяет уровень корреляции между выходами двух датчиков r1 и r4. Более высокий уровень корреляции означает, что аргумент T относительно близок к реальной разнице во времени прихода сигнала. Для пары датчиков r1–r4 разница во времени прибытия T определяется отношением
где θ – угол между нормалью, соединяющей приемники r1 и r4 и направлением звуковой волны.Для пары приемников r2–r3 кросс-корреляция сигналов исследуется аналогичным способом. Разница во времени прибытия для каждой пары приемников микрофонной решетки по результатам кросс-корреляции сигналов позволяет восстанавливать координаты источника акустического излучения – локализовать место дефекта на обследуемых высоковольтных изоляторах. Интенсивность регистрируемых сигналов позволяет судить о величине ЧР и выявлять дефектные ВИ. Дальнейшее обследование выявленного ВИ проводится ранее разработанным способом [9–11] при помощи бесконтактного диагностического комплекса [12, 13].
Разработан и создан стенд [13], позволяющий в лабораторных условиях изучать электрофизические процессы в различных диэлектрических материалах и изделиях под воздействием сильных переменных электрических полей, включающий электромагнитный, акустический и тепловизионный датчики. Одновременное использование нескольких датчиков позволяет повысить точность локализации ЧР в изоляторе. На стенде были изучены особенности дефектов на стержне и в контакте “стержень–оконцеватель”. В результате была построена схема электрофизических процессов, сопровождающих излучение ЧР, и установлены причины их возникновения. Стенд используется для настройки и градуировки микрофонных решеток на получение объективной информации о регистрируемых с их помощью дефектах [14]. Это необходимо для определения степени работоспособности изоляторов с помощью системы мониторинга.
ЗАКЛЮЧЕНИЕ
Среди сложных высоковольтных электроэнергетических устройств, требующих диагностирования в процессе эксплуатации, высоковольтные изоляторы занимают особое место. Многочисленные ВИ на линиях электропередач или электрических подстанций подвержены комплексному воздействию сильных электрических полей, градиентов световых и тепловых полей, электродинамических и механических воздействий. Все это создает условия для возникновения дефектов, что неизбежно приводит к разнообразным отказам и даже авариям в сложных электроэнергетических системах.
Разработана система мониторинга высоковольтной изоляции открытых электрических подстанций. Система основана на построении акустического слепка излучаемых неисправным оборудованием звуковых и ультразвуковых колебаний. Выполненные лабораторные испытания разработанной системы мониторинга показали возможность ее использования на практике для мониторинга состояния ВИ, находящихся в режиме эксплуатации. Бесконтактный диагностический комплекс позволяет выполнять многопараметрический анализ выявленных дефектов.
Исследования выполнены при финансовой поддержке Министерства науки и высшего образования Российской Федерации в рамках государственного задания на выполнение НИР по теме “Распределенные автоматизированные системы мониторинга и диагностики технического состояния воздушных линий электропередачи и подстанций на основе технологии широкополосной передачи данных через линии электропередач и промышленного интернета вещей” (номер темы 075-00063-20-02).
Список литературы
Boggs S. // IEEE Electr. Insul. Mag. 1990. V. 6. P. 33.
Phung B.T., Blackburn T.R., Liu Z. // J. Electr. Electron. Eng. 2001. V. 21. P. 41.
Polyakov D.A., Tereschenko N.A., Nikitin K.I. et al. // J. Phys. Conf. Ser. 2021. V. 1791. No. 1. Art. No. 012058.
Голенищев-Кутузов А.В., Голенищев-Кутузов В.А., Иванов Д.А. и др. // Дефектоскопия. 2019. № 8. С. 34; Golenishchev-Kutuzov A.V., Golenishchev-Kutuzov V.A., Ivanov D.A. et al. // Rus. J. Nondestruct. Test. 2019. V. 55. No. 8. P. 596.
Lundgaard L.E. // IEEE Electr. Insul. Mag. 1992. V. 8. P. 34.
Rohwetter P., Habel W., Heidmann G. et al. // IEEE Trans. Diel. Electr. Insul. 2015. V. 22. No. 1. P. 52.
Silverman H.F., Yu Y., Sachar J.M. et al. // IEEE Trans. Sp. Audio Proc. 2005. V. 13. No. 4. P. 593.
Pihera J. et al. // 2020 IEEE 3rd Int. Conf. Diel. (ICD). 2020. P. 830.
Голенищев-Кутузов В.А., Голенищев-Кутузов А.В., Иванов Д.А. и др. Способ бесконтактной дистанционной диагностики состояния высоковольтных изоляторов. Пат. РФ № 2679759, кл. G01R 31/12. 2018.
Голенищев-Кутузов А.В., Иванов Д.А., Калимуллин Р.И. и др. // Изв. РАН. Сер. физ. 2020. Т. 84. № 12. С. 1502; Golenishchev-Kutuzov A.V., Ivanov D.A., Kalimullin R.I., Semennikov A.V. // Bull. Russ. Acad. Sci. Phys. 2020. V. 84. No. 12. P. 1502.
Ilkhechi H.D., Samimi M.H. // IEEE Trans. Diel. Electr. Insul. 2021. V. 28. No. 1. P. 42.
Ivanov D., Sadykov M., Golenishchev-Kutuzov A. et al. // E3S Web Conf. 2020. V. 220. Art. No. 01071.
Галиева Т.Г., Иванов Д.А. // Динам. нелин. дискр. эл.-техн. и электрон. систем: мат. XIV Всерос. нау-ч.-техн. конф. Чебоксары: изд-во Чуваш. ун-та, 2021. С. 488.
Andreev N.K. // E3S Web Conf. 2019. V. 124. Art. No. 05043.
Дополнительные материалы отсутствуют.
Инструменты
Известия РАН. Серия физическая