Известия РАН. Серия физическая, 2021, T. 85, № 6, стр. 836-841
Ультразвуковая визуализация динамики разрушения армированных композитов
Ю. С. Петронюк 1, 2, *, С. А. Титов 2, В. М. Левин 1, Т. Б. Рыжова 3
1 Федеральное государственное бюджетное учреждение науки
Институт биохимической физики имени Н.М. Эмануэля Российской академии наук
Москва, Россия
2 Федеральное государственное бюджетное учреждение науки
Научно-технологический центр уникального приборостроения Российской академии наук
Москва, Россия
3 Федеральное государственное унитарное предприятие
“Центральный аэрогидродинамический институт имени профессора Н.Е. Жуковского”
Жуковский, Россия
* E-mail: jps7@mail.ru
Поступила в редакцию 09.12.2020
После доработки 25.01.2021
Принята к публикации 26.02.2021
Аннотация
Представлены результаты исследования структуры образцов, выполненного с помощью импульсного акустического микроскопа, совмещенного со специально разработанной миниатюрной испытательной машиной. Рассматриваются особенности проведения таких экспериментов. Показана возможность измерения деформации образца при его механических испытаниях неразрушающими методами акустической микроскопии.
ВВЕДЕНИЕ
Ультразвук широко используется для визуализации, неразрушающего контроля, оценки структуры и дефектов в объеме армированных композитов [1–7]. Возможности ультразвуковой техники определяются типом зондирующего излучения и диапазоном используемых частот. Ультракороткие импульсы фокусированного ультразвука, длительностью 1.5–2 колебания в диапазоне частот 50–200 МГц обеспечивают акустическую визуализацию элементов внутренней микроструктуры армированных композитов на глубине до 4–5 мм, в зависимости от частоты зондирующего излучения, свойств отдельных компонентов композита и качества их упаковки. На акустических изображениях отчетливо выявляются протяженные области потери сплошности, даже если расстояние между берегами отслоения оказывается минимальным, как в случае закрытой трещины [8, 9]. К числу отображаемых несплошностей принадлежат зоны отслоения полимерного связующего от волокон, трещины в объеме связующего между волокнами, трещины между слоями (межслоевые отслоения).
В данной работе импульсная акустическая микроскопия используется для наблюдения процессов необратимого деформирования и разрушения композитного материала, которые включают в себя совокупность структурных изменений в объеме связующего, внутри армирующих слоев и на границах между ними [10]. Эта проблема привлекает внимание исследователей с момента появления композитов; их изучение остается актуальным и сегодня, благодаря необходимости вскрыть механизмы необратимого деформирования на уровне микроструктурных изменений [11].
Первоначально, изучение микроструктуры и ее нарушений осуществлялось разрушающими методами – образец разрезался на серию плоских сечений, микроструктура на поверхности наблюдалась и оценивалась стандартной техникой оптической или электронной микроскопии. В последние десятилетия бурно развивается техника неразрушающей визуализации объемной микроструктуры [12]; в рамках такого подхода перспективным оказывается метод импульсной акустической микроскопии – он обладает достаточно высоким разрешением (10–100 мкм) и сохраняет преимущества ультразвуковых методов – простой, безопасный, довольно быстрый, не требующий специальных условий и тщательной подготовки образцов [13].
В работе рассматривается подход, при котором импульсный акустический микроскоп объединен с испытательной машиной в единый комплекс, что открывает возможность прямого наблюдения в реальном масштабе времени структурных изменений в объеме образцов, зарождения и накопления дефектов, процессов релаксации.
МЕТОДЫ И ОБРАЗЦЫ
В основе метода импульсной акустической микроскопии лежит зондирование образца фокусированным ультразвуковым пучком в иммерсионной капле [14, 15]. Зондирующее излучение представляет собой импульс длительностью 1–2 периода на рабочей частоте от 50 МГц и выше. Объемная визуализация обеспечивается разделением по времени эхоимпульсов, отраженных от границ раздела на разной глубине в объеме объекта.
Для изучения процессов разрушения композитного материала использовался импульсный микроскоп с рабочей частотой акустического объектива 100 МГц. Сканирование образцов осуществлялось за счет прецизионного перемещения акустической линзы с шагом до 15 мкм, при этом обеспечивалось пространственное разрешение акустических изображений порядка 30 мкм на всю глубину образца. Ультразвуковая визуализация выполнялась непосредственно в процессе растягивающего воздействия на образец. Для этого импульсный акустический микроскоп сопрягался с горизонтальной испытательной минимашиной с максимальной нагрузкой 5500 Н, конструкция которой обеспечивает доступ акустической линзы к области растяжения (рис. 1). Растяжение производилось со скоростью 10 мм/мин; параллельно с ультразвуковой визуализацией снималась кривая нагружения образца.
Рис. 1.
Схема экспериментального стенда: 1 – преобразователь; 2 – иммерсионная среда; 3 – образец; 4 – захваты; 5 – электронный блок; 6 – механический сканер; 7 – двигатель; 8 – датчик силы; 9 – энкодер; 10 – компьютер (а); и его общий вид (б).
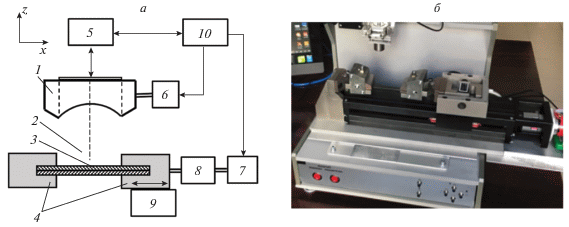
Образцы углепластиков формировались в виде 4-слойных пластин из слоев волокон (препрега) T800SC-24 K/ER450 с 35% содержанием эпоксидного связующего и чередующейся ориентацией (90/45)S волокон. Толщина слоев в образцах составляла 0.13 мм. Были сформированы пластинки размером 100 × 15 мм. Образцы-пластинки растягивались поэтапно с шагом 200 Н до потери пластиной целостности, в нашем случае до нагрузки 2000 Н. В конце каждого этапа нагружения выполнялась визуализация внутренней структуры образца при постоянной величине нагрузки. В процессе визуализации формируется 3D объемное изображение образца с площадью сечения 15 × 15 мм2. Использование электронных ворот по глубине позволяет рассматривать структуру отдельных слоев композита в виде двумерных акустических изображений (С-сканов). Латеральное разрешение определяется, как обычно, длиной волны излучения и угловой апертурой зондирующего пучка. В нашем случае ультразвуковой пучок с рабочей частотой 100 МГц и 22° обеспечивает разрешение порядка 30–60 мкм в углепластиках.
ЭКСПЕРИМЕНТАЛЬНЫЕ РЕЗУЛЬТАТЫ
На рис. 2. показана динамика микроструктурных изменений в объеме углепластика при возрастании растягивающих усилий – 800, 1200, 1600 и 2000 Н. Структура композита содержит многочисленные границы раздела между армирующими элементами и связующим. При минимальной нагрузке или в ее отсутствие на акустических изображениях слоев наблюдается параллельная укладка углеродных волокон в слоях препрега (рис. 2а).
Рис. 2.
Акустические изображения повреждений структуры углепластика (90/45)2S в процессе растяжения с усилием от 800 до 2000 Н: (1) отслоения волокон с 90° ориентацией; (2) отслоения и разрушение волокон в слоях 45°.

Структурные повреждения, внесенные действием растягивающих нагрузок, являются, в первую очередь, нарушениями сплошности. Обширная трещина, параллельная плоскости сканирования, на акустических изображениях наблюдается в виде яркой области на соответствующей глубине; при этом на изображениях нижерасположенных слоев наблюдается тень. Тень может также формироваться наклонными или вертикальными трещинами, отражение от которых не попадает в апертуру акустического объектива. Кроме того, низкий уровень принимаемого сигнала может быть обусловлен наличием на пути зондирующего пучка скопления повреждений малого размера – менее разрешающей способности системы визуализации; звук рассеивается на таких дефектах структуры, что препятствует его распространению в нижележащий слой. На рис. 2 показана микроструктура образцов при нагрузках 1200 Н. На изображениях наблюдаются тени – вертикальные линии, количество которых увеличивается с ростом нагрузки (рис. 2б–2г). При таких нагрузках возникают повреждения связанные с отслоением связующего от углеродных нитей в слоях с ориентацией волокон, перпендикулярной направлению нагрузки [16]. При больших нагрузках 1600 и 2000 Н наблюдаются также межслоевые отслоения – яркие треугольные области вверху у кромки образца (рис. 2в, 2г).
Основным достоинством предложенного в работе подхода in situ ультразвуковой визуализации нагруженных образцов является возможность наблюдать зарождение и развитие повреждений, рост их числа с увеличением нагрузки. Однако часть повреждений предвестников разрушения материала формируют лишь тени и могут остаться необнаруженными на фоне картины исходной естественной структуры композита. Далее авторами предлагается алгоритм цифровой обработки изображений, который позволяет повысить выявляемость таких дефектов и определять деформацию образца.
ЦИФРОВАЯ ОБРАБОТКА ИЗОБРАЖЕНИЙ
На рис. 3 представлены фрагменты акустических изображений для одного из образцов углепластика. Изображения получены при нагрузках 1200 и 1400 Н в слое толщиной 100 мкм на глубине 300 мкм и позволяют видеть структуру обоих слоев волокон с ориентацией 45° и 90° к направлению нагрузки. При построении и обработке акустических изображений использовались ультразвуковые пространственно-временные сигналы s0(x, y, t) и s1(x, y, t), записанные для испытуемого образца при указанных выше нагрузках. Ультразвуковые данные при текущей механической нагрузке, обрабатывались в нескольких этапов.
На первом этапе осуществлялась компенсация кривизны поверхности образца и ее непараллельности по отношению к плоскости сканирования. Для этого измерялись задержки τ0(x, y) и τ1(x, y) эхо-сигналов, отраженных от внешней границы образца, и путем интерполяции по временной переменной формировались сигналы s0(x, y, t – τ0(x, y)) и s1(x, y, t – τ1(x, y)).
На следующем этапе обработки производилась компенсация общего смещения образца, неизбежно возникающего в экспериментальной установке из-за деформаций элементов конструкции экспериментальной установки с течением времени при изменении механической нагрузки. Величина такого смещения определялась методом корреляции изображений. На изображениях, измеренных для разных нагрузок, выделялись квадратные области, и для них находился нормированный коэффициент корреляции [17]. Положение максимума рассчитанного коэффициента корреляции показывает величины относительного смещения изображений в направлениях х и y. Размер выделенных областей с одной стороны был достаточно большим для получения состоятельной оценки коэффициента корреляции, с другой – он был малым по сравнению с размером всего изображения. Как показывают проведенные исследования, величина такого общего смещения образцов может быть весьма значительной, достигая нескольких десятых долей миллиметра [18].
После компенсации общего смещения определялось распределение смещений локальных участков образца – дальнейшей деформацией образца при возрастании нагрузки. Для этого на опорном и текущем изображениях выделялись пары областей небольшого размера, которые были равномерно расположены в узлах квадратной сетки. Для каждой пары выбранных окон рассчитывался коэффициент корреляции, и определялось поле смещений в продольном и поперечном направлениях.
Предложенный метод обработки ультразвуковых данных был опробован при испытаниях образцов четырехслойного углепластика (45/90)S при возрастающей от 0 до 1400 Н нагрузке. Эксперименты [18] показывают, что величины продольных и поперечных деформаций растут приблизительно линейно и достигают значений +1.2 и –0.3%, соответственно. Полученные значения максимальных деформаций находятся в соответствии со значениями других авторов [16].
Вместе с тем компенсация поля относительной деформации образца, приобретаемой при изменении нагрузки, позволяет привести получаемые изображения к единому пространственному масштабу и корректно вычесть стационарную часть изображений. В качестве примера на рис. 3 приведены изображения I1(x, y), I2(x, y), полученные при нагрузках 1200 и 1400 Н, соответственно. Изображения были получены при установке электронных ворот по времени задержки так, чтобы визуализировать границу первого и второго слоев. На изображениях наблюдается сильный структурный шум, характерный для ультразвуковых изображений углепластиков на данной частоте. Изображения выглядят практически идентичными и образование дефектов, вызванных увеличением нагрузки, зафиксировать на фоне шума представляется затруднительным.
Для выявления дефектов, образующихся при нарастании нагрузки, получаем разностное изображение DI(x, y) (рис. 4а):
Видно, что исходная структура на изображении DI(x, y) существенно менее выражена по сравнению с исходными изображениями I1(x, y) и I2(x, y); однако отчетливо выделяются два протяженных дефекта A и B, ориентированных перпендикулярно приложенной нагрузке вдоль нитей в верхнем слое 90°. Эффективность подавления структурного шума демонстрирует сравнение графиков зависимостей I2(y) и DI(y), отнесенных к координате x = 8 мм (рис. 4в). В результирующей зависимости DI(y) уверенно обнаруживаются пики A и B, образованные соответствующими повреждениями структуры. В исходной же зависимости I2 (пунктир) отклики от дефектов скрыты структурным шумом, и их обнаружение представляется затруднительным. Следует отметить, что дальнейшее испытание образца и оптическое наблюдение его состояния после разрушения подтверждает тот факт, что в указанных местах присутствует протяженные трещины, выходящие на поверхность.
Вариантом отображения обработанных данных является формирование в виде акустического изображения разности принятых сигналов s0 и s1 в соответствии с выражением:
(2)
$D{{I}_{0}}\left( {x,y} \right) = \max \left\{ {\left| {\left[ {{{s}_{0}}\left( {x,y,t} \right) - {{s}_{1}}\left( {x,y,t} \right)} \right]} \right|} \right\}.$Результат такой обработки показан на рис. 4б. Как видно, на этом изображении также присутствуют отчетливые отклики повреждений. Нужно отметить, что в настоящий момент затруднительно сказать, какой из вариантов разностной обработки является более предпочтительным. Предварительные оценки показывают, что расчет по формуле (1) дает более устойчивые результаты при расположении дефектов в верхних слоях, а расчет по формуле (2) – наоборот, для глубоко расположенных. Для объяснения наблюдаемой особенности необходимы дальнейшие исследования.
ЗАКЛЮЧЕНИЕ
Ультразвуковая визуализация высокого разрешения является эффективным методом для изучения изменений в структуре композита под действием внешней механической нагрузки. Метод позволяет выявлять производственные дефекты и повреждения, полученные в процессе внешнего воздействия. Контраст акустических изображений определяется соотношением импедансов компонентов композита, связан с размерами и геометрической формой структурных элементов. Для повышения выявляемости структурных изменений и исследования их взаимного влияния разработан уникальный стенд для ультразвуковой визуализации in situ. Разработана методика оценки акустических изображений, позволяющая путем корреляционной обработки количественно характеризовать смещение структурных элементов композитной среды при разных нагрузках. Показано, что обработка изображений позволяет определять деформацию образца, неточности в измерениях которой неизбежно возникают непосредственно в процессе нагружения из-за смещения элементов конструкции.
Экспериментальная часть работ выполнена при финансовой поддержке РФФИ (проект № 18-29-17039), а теоретические рассмотрение при финансовой поддержке Министерства науки и высшего образования РФ.
Список литературы
Guillaud N., Froustey C., Dau F. et al. // Compos. Struct. 2015. V. 121. P. 172.
Andreades C., Mahmoodi P., Ciampa F. // Compos. Struct. 2018. V. 206. P. 456.
Петронюк Ю.С., Мороков Е.С., Левин В.М. и др. // Изв. РАН. Сер. физ. 2018. Т. 82. № 5. С. 560; Petronyuk Y.S., Morokov E.S., Levin V.M. et al. // Bull. Russ. Acad. Sci. Phys. 2018. V. 82. No. 5. P. 491.
Wang X., Yao L., Huang Z. // Compos. Struct. 2019. V. 222. Art. No. 110913.
Mardanshahia A., Shokrieha M.M., Kazemirad S. // Compos. Struct. 2020. V. 235. Art. No. 111790.
Petronyuk Y.S., Levin V.M., Ryzhova T.B. et al. // J. Phys. Conf. Ser. 2020. V. 1636. Art. No. 012005.
Morokov E., Levin V., Chernov A. et al. // Compos. Struct. 2021. V. 256. Art. No. 113102.
Левин В.М., Мороков Е.С., Петронюк Ю.С. // Изв. РАН. Сер. физ. 2017. Т. 81. № 8. С. 1053; Levin V.M., Morokov E.S., Petronyuk Y.S. // Bull. Russ. Acad. Sci. Phys. 2017. V. 81. No. 8. P. 950.
Ahmed S.R., Saka M. // NDT E Int. 2000. V. 33. P. 261.
Браутман Л., Крок Р. Композиционные материалы. Т. 5. Разрушение и усталость. М.: Мир, 1978. 488 с.
Wright P., Moffat A.J., Renault A. et al. // JCST. 2010. V. 70. No. 10. P. 1444.
Levin V., Petronyuk Y., Morokov E. et al. // Polym. Eng. Sci. 2019. P. 2508.
Закутайлов К.В., Левин В.М., Петронюк Ю.С. // Завод. лаб. 2009. № 8. С. 28.
Tittmann B., Miyasaka C., Guers M. et al. Non-destructive evaluation (NDE) of aerospace composites: acoustic microscopy. Cambridge: Woodhead Publishing Ltd., 2013. P. 423.
Maslov K., Kim R.Y., Kinra V.K. et al. // Compos. Sci. Technol. 2000. V. 60. P. 2185.
Naderi M., Iyyer N. // Compos. Struct. 2020. V. 234. Art. No. 111659.
Gonzalez R.C., Woods R.E. Digital image processing. New Jersey: Prentice Hall, 2002. 793 p.
Titov S.A., Levin V.M., Petronyuk Y.S. et al. // J. Phys. Conf. Ser. 2020. V. 1636. Art. No. 012025.
Дополнительные материалы отсутствуют.
Инструменты
Известия РАН. Серия физическая