Известия РАН. Серия физическая, 2021, T. 85, № 7, стр. 984-989
Влияние лазерной обработки на прочностные характеристики γ-фазы в сплавах системы железо–хром–никель
Е. Н. Блинова 1, *, М. А. Либман 1, В. Н. Петровский 2, Е. В. Пименов 1, П. П. Умнов 3, В. П. Филиппова 1, Т. Р. Чуева 3, Н. А. Шурыгина 1
1 Федеральное государственное унитарное предприятие
“Центральный научно-исследовательский институт черной металлургии имени И.П. Бардина”,
Научный центр металловедения и физики металлов
Москва, Россия
2 Федеральное государственное автономное образовательное учреждение высшего профессионального образования “Национальный исследовательский ядерный университет “Московский инженерно-физический институт”
Москва, Россия
3 Федеральное государственное бюджетное учреждение науки
“Институт металлургии и материаловедения имени А.А. Байкова Российской академии наук”
Москва, Россия
* E-mail: blinova_en@rambler.ru
Поступила в редакцию 30.12.2020
После доработки 25.02.2021
Принята к публикации 29.03.2021
Аннотация
Исследовано влияние интенсивного нагрева лазерным излучением на прочностные характеристики γ-фазы в славах системы железо-хром-никель. Показано, что применение лазерного излучения для нагрева исходной α-фазы до температуры окончания α → γ превращения приводит к образованию γ-фазы с существенно более высокими значениями микротвердости и предела текучести, чем у равновесной γ-фазы. Обсуждается возможный механизм этого явления.
ВВЕДЕНИЕ
Одной из важнейших проблем, стоящих перед современным материаловедением, является проблема создания металлических материалов, сочетающих высокие значения прочностных и пластических характеристик. Решение этой задачи может быть достигнуто путем реализации в металлических сплавах фазовых превращений, приводящих к образованию метастабильных фаз с механическими характеристиками, существенно отличающимися от этих характеристик, полученных в равновесном состоянии.
Одним из способов получения таких метастабильных фаз является применение термической обработки с использованием лазерного излучения, которое характеризуется двумя факторами – локальностью воздействия и скоростью нагрева. Обработка с использованием лазерного излучения применяется для создания градиентных материалов – материалов, которые представляют собой определенное сочетание макроскопических областей с существенно различающимися по физическим и механическим свойствам.
В работах [1–6] была продемонстрирована возможность создания магнитных градиентных материалов на основе сплавов железа, представляющих собой распределение по заданному закону макроскопических парамагнитных областей γ-фазы в ферромагнитной α-матрице. Для создания таких материалов использовалось сочетание холодной пластической деформации и последующего нагрева лазерным излучением. Локальность последнего позволяло получать парамагнитные области необходимой формы и размера.
Между тем, второй важнейший фактор лазерного нагрева – его скорость, практически не был изучен. А именно этот фактор открывает путь к созданию метастабильных фаз с необычными физическими и механическими свойствами.
В связи с этим, целью настоящей работы было исследование влияния нагрева интенсивным лазерным излучением на механические свойства, в частности, прочностные характеристики сплавов на основе железа.
ФИЗИЧЕСКИЕ СВОЙСТВА И ФАЗОВЫЙ СОСТАВ ИССЛЕДОВАННЫХ СПЛАВОВ
В настоящей работе исследовалось влияние нагрева интенсивным лазерным излучением на прочностные характеристики γ-фазы в аустенитно-мартенситных сплавах системы железо-хром-никель. Выбор этой системы обусловлен тем обстоятельством, что, варьируя содержание и соотношение в сплаве хрома и никеля, можно существенным образом изменять температуру начала γ → α превращения, а также тем, что различие между температурами начала γ → α и α → γ составляет сотни градусов, что позволяет в полной мере использовать возможности интенсивного нагрева лазерным излучением. Кроме того, в сплавах выбранной для исследований системы α и γ фаза существенно различаются по магнитным свойствам – α-фаза обладает ферромагнитными характеристиками, а γ-фаза – парамагнитными. Это делает данные сплавы очень удобным объектом для анализа влияния лазерного воздействия на фазовый состав.
Для проведения исследований были выбраны сплавы, химический состав которых приведен в табл. 1. Сплавы были выплавлены в вакуумной индукционной печи объемом 5 кг из чистых шихтовых материалов и разлиты в атмосфере аргона на слитки, которые были прокованы при температуре 1150°С с дальнейшей осадкой вдоль и поперек волокон, на сутунку с габаритами 20 × 100 × 300 мм. Горячую прокатку сутунок проводили с предварительным подогревом при температуре 1150°С на размер 2.6–2.7 мм. Горячедеформированные листы отжигались при температуре 1150°С и охлаждались с печью. После зачистки горячедеформированные листы толщиной 2.5 мм были подвергнуты холодной деформации с различными степенями обжатия. Важно отметить, что в процессе холодной деформации промежуточные отжиги не проводились.
Таблица 1.
Химические составы исследованных сплавов
№ сплава | Содержание элементов, % (остальное – железо) | ||||||
---|---|---|---|---|---|---|---|
углерод | кремний | марганец | фосфор | сера | хром | никель | |
1 | <0.02 | 0.30 | 0.33 | 0.004 | 0.006 | 18.31 | 9.65 |
2 | <0.02 | 0.29 | 0.34 | 0.004 | 0.006 | 17.36 | 8.50 |
3 | <0.02 | 0.33 | 0.36 | 0.004 | 0.006 | 15.82 | 6.85 |
Для исследований были отобраны образцы сплавов различных составов после горячей и холодной деформации с различной степенью обжатия. В табл. 2 приведены результаты измерений магнитных свойств, температур прямого γ → α и обратного α → γ превращений и фазового состава сплавов после горячей и холодной деформации.
Таблица 2.
Магнитные свойства, температуры γ → α и α → γ превращений, фазовый состав исследованных сплавов
№ сплава | Состояние сплава | ε , % | 4πIs, Тл | Фазовый состав | n, % | Т0, °С | ΔТ, °С |
---|---|---|---|---|---|---|---|
1 | ГД | – | 0 | γ | 0 | –120 | |
ГД + ХД | 17.3 | 0.09 | α + γ | 10 | – | 500–700 | |
32.7 | 0.18 | α + γ | 20 | – | |||
48.0 | 0.60 | α + γ | 50 | – | |||
57.7 | 0.86 | α + γ | 80 | – | |||
73.1 | 0.92 | α | 90 | – | |||
2 | ГД | – | 0 | γ | 0 | –30 | |
ГД + ХД | 17.3 | 0.63 | α + γ | 50 | – | 500–700 | |
32.7 | 0.87 | α + γ | 70 | – | |||
46.1 | 1.08 | α + γ | 80 | – | |||
61.5 | 1.15 | α | 95 | – | |||
75.0 | 1.17 | α | 95 | – | |||
3 | ГД | – | 1.24 | α | ~100 | 100 | |
ГД + ХД | 17.3 | 1.24 | α | ~100 | – | – | |
23.0 | 1.23 | α | ~100 | – | |||
34.6 | 1.23 | α | ~100 | – | |||
50.0 | 1.23 | α | ~100 | – | |||
65.4 | 1.24 | α | ~100 | – |
Для определения фазового состава и доли ферромагнитной α-фазы в исследованных сплавах после различных видов деформации использовалось сочетание методов рентгеноструктурного анализа и измерения намагниченности насыщения. Измерение интервала температур α → γ превращения проводилось методом калориметрии путем нагрева со скоростью 180°С/мин в интервале температур от комнатной до 1000°С. Температуры γ → α превращения рассчитывались на основании данных по химическому составу по известным формулам [7].
Анализируя результаты, приведенные в табл. 2, можно сделать следующие выводы. Сплавы 1 и 2 в горячедеформированном состоянии содержат γ-фазу, применение последующей холодной деформации инициирует γ → α превращение тем интенсивней, чем выше степень обжатия. Так, в сплаве 1 после обжатия в 73% по данным рентгеноструктурного анализа образуется 90% α-фазы, намагниченность насыщения составляет 0.92 Тл. Сплав 2 после обжатия в 75% также содержит 95% α-фазы и имеет намагниченность насыщения 1.17 Тл. Различие в интенсивности образования α-фазы в сплавах 1 и 2 связано с положением температуры начала γ → α превращения, в сплаве 2 она, очевидно, несколько выше. Сплав 3 испытывает γ → α превращение при температурах выше комнатной. Соответственно, в состоянии после горячей деформации он содержит только α-фазу, величина намагниченности насыщения составляет 1.24 Тл и практически не изменяется при применении холодной деформации с различными степенями обжатия.
Данные, приведенные в табл. 2, свидетельствуют о том, что реализация α → γ превращения с помощью интенсивного нагрева лазерным излучением возможна в сплавах 1 и 2 всех выбранных составов. В сплаве 3, у которого образование α-фазы начинается выше комнатной температуры, не представляется возможным зафиксировать образующуюся при лазерном нагреве γ-фазу при комнатной и более низких температурах. Вообще говоря, чем ниже температура γ → α превращения, тем образующаяся при нагреве лазерным излучением γ-фаза, будет стабильной в более широкой области температур.
Термическая обработка с использованием лазерного излучения, необходимая для образования γ-фазы, проводилась путем сверхбыстрого нагрева выше температуры окончания α → γ превращения, которая в случае выбранных нами сплавов 1 и 2 превышает 700°С (табл. 2). Термической обработке подвергались холоднодеформированные образцы сплавов 1 и 2 после максимального обжатия (табл. 2). Толщина таких образцов составляла ~0.65 мм.
ТЕХНОЛОГИЯ НАГРЕВА С ПОМОЩЬЮ ЛАЗЕРНОГО ИЗЛУЧЕНИЯ
Для проведения нагрева лазерным излучением использовался роботизированный комплекс BlackBird, оснащенный роботом фирмы АВВ, волоконным иттербиевым непрерывным лазером модели ЛС – 2 с максимальной средней мощностью 2 кВт с длиной волны 1.07 мкм (производство IPG Photonics) и сканирующей оптической системой Line-scan LK690F (производство IPG Photonics).
Процесс лазерной термообработки заключался в сканировании поверхности образца размерами 30 × 60 мм, размещенного в специальной оправе, расфокусированными лазерными дорожками шириной 1.5–2 мм. При проведении экспериментов по лазерной термообработке варьировались три основных параметра: количество лазерных дорожек, скорость движения лазерного пучка и расстояния между фокусом лазера и поверхностью образца. Для того, чтобы нагревание образца посредством облучения лазером было эффективным, но не приводило к разрушению поверхности образца, в схеме эксперимента использовалось расфокусированное излучение – плоскость фокусировки была поднята выше поверхности образца. Мощность лазерного излучения в ходе эксперимента не варьировалась и составляла 2 кВт. Высокое значение мощности позволяло прогреть с наибольшей скоростью достаточно широкую зону образца до температуры, необходимой для осуществления фазового перехода в обрабатываемой области.
В целях предотвращения термических деформаций во время обработки, образец жестко фиксировался в оправе из сплава ДТ-16, толщиной 5 мм. После обработки образец остывал в оправе до комнатной температуры.
На рис. 1 схематично показан процесс лазерной термической обработки образцов выбранных сплавов. В табл. 3 приведены параметры лазерного воздействия при термической обработке железо-хром-никелевых сплавов в толщине ~0.65 мм. Измерение температуры на поверхности образца производилось дистанционно с помощью тепловизора FLIR 650 SC. Обработанные участки обладали излучательной способностью отличной от чистой поверхности металла, поэтому дополнительно была проведена калибровка коэффициента излучательной способности. Особенностью лазерного излучения является его нестационарный характер. Поэтому как основной параметр измерения была выбрана максимальная температура, достигаемая образцом в точке измерения. Области измерения температуры образца сплава 1 в толщине 0.65 мм, подвергнутого интенсивному лазерному нагреву по режиму 1 (табл. 3) при средней температуре ~900°С, показаны на рис. 2 линиями.
Рис. 1.
Схема эксперимента по лазерной термической обработке: 1 – лазер, 2 – тепловизор, 3 – обработанная область образца, 4 – расфокусированное излучение.
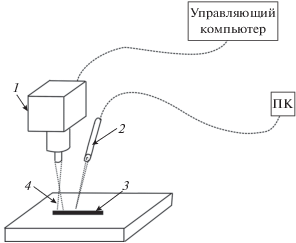
Таблица 3.
Параметры лазерного воздействия при термической обработке холоднодеформированных железо-хром-никелевых сплавов
№ режима | Количество лазерных дорожек | Скорость обработки, м/мин | Мощность, кВт | Расстояние между фокусом лазера и поверхностью образца, мм |
---|---|---|---|---|
1 | 10 линий на 10 мм | 30 | 2 | 300 |
2 | 32.5 | |||
3 | 35 | |||
4 | 35 | 250 | ||
5 | 275 | |||
6 | 10 линий на 14 мм | 26 | 250 |
Рис. 2.
Образец сплава 1, обработанный лазерным излучением при температуре ~950°С; прямые линии – области измерения температуры.
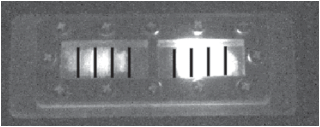
Так как лазерное излучение приводит к достаточно неоднородному температурному полю по поверхности образца (рис. 2), указанную температуру следует рассматривать как некоторое среднее значение. Важно отметить, что, реализация α → γ превращения произошла лишь в тех местах поверхности образца, где температура была выше 700°С (табл. 2).
ОБСУЖДЕНИЕ РЕЗУЛЬТАТОВ
Рассмотрим влияние нагрева лазерным излучением на макроскопическую структуру выбранного для экспериментов сплава. В центре термически обработанного образца сплава отчетливо видно пятно, которое образовалось при нагреве лазерным излучением. Так как α и γ-фаза существенно отличаются по магнитным характеристикам, качественное определение фазового состава областей, подвергнутых лазерному нагреву и свободных от него, может быть проведено при помощи сильного постоянного магнита. В нашем случае для этого использовался магнит, изготовленный из сплава КС-37. Проведенные измерения показали, что в области пятна практически отсутствует взаимодействие магнита и образца сплава. Это свидетельствует о том, что сплав в местах лазерной обработки является парамагнитным, то есть содержит преимущественно γ-фазу. Области, не затронутые лазерным нагревом, наоборот, очень сильно взаимодействуют с постоянным магнитом, то есть имеют структуру ферромагнитной α-фазы. Полученные результаты, несмотря на их качественный характер, свидетельствуют о том, что в процессе термической обработки реализовалось фазовое α → γ превращение с образованием устойчивой до комнатной температуры γ-фазы.
Для исследования прочностных характеристик γ-фазы, образовавшейся в результате термообработки с использованием лазерного излучения, нами применялся метод измерения микротвердости по Виккерсу. Хотя микротвердость определяется в поверхностном слое образца, ее величина в сплавах, выбранных для исследований, однозначно связана с пределом текучести σ0.2 простым эмпирическим соотношением σ0.2 ≈ 0.33 HV (HV – твердость по Виккерсу) [7].
На рис. 3 приведены результаты измерения микротвердости в поперечном направлении образца сплава 1, подвергнутого лазерной термической обработке. Зависимость микротвердости для образца сплава 1, подвергнутого лазерному излучению, имеет немонотонный вид, характеризующийся довольно широкой площадкой протяженностью ~8 мм в центре пятна (рис. 2 и 3). В пределах этой площадки образец является парамагнитным, то есть содержит в основном, γ-фазу. Области вне пятна на рис. 2 имеют ферромагнитные свойства, что свидетельствует о наличии в этих областях α-фазы. Таким образом, в результате локального лазерного воздействия в образце сформировалась двухфазная макроструктура, состоящая из γ и α-фаз, а также переходной α + γ области, ширина которой достигает ~5–6 мм.
Рис. 3.
Распределение микротвердости образца из сплава 1 подвергнутого интенсивному нагреву лазерным излучением.
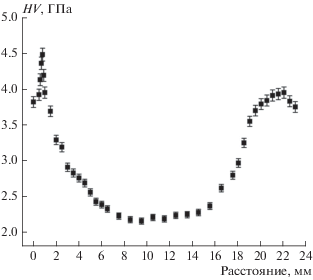
Весьма интересно сравнить распределение микротвердости, измеренной поперек образца и распределение температур, возникающих в образце при нагреве лазерным излучением (рис. 4). Сопоставляя кривые, приведенные на рис. 3 и 4, видим, что площадка, характеризующая наличие γ-фазы в образце, совпадает с областью температур, находящихся выше температуры α → γ превращения (табл. 2). Это еще один аргумент в пользу того, что лазерный нагрев действительно привел к образованию γ-фазы.
Для областей образца, содержащих γ-фазу, величина микротвердости составляет ~2.3–2.4 ГПа, что в переводе в величину предела текучести дает величину ~0.8 ГПа. Таким образом, можно констатировать важный факт, который, по нашему мнению, является основным результатом настоящей работы: высокоскоростной нагрев лазерным излучением исходной α-фазы при температурах выше температуры α → γ превращения приводит к образованию метастабильной γ-фазы с прочностными характеристиками, по меньшей мере, в два раза превосходящей эти характеристики в стабильном состоянии [7].
Природа этого явления не достаточно изучена. Однако, можно высказать предположение, что такой рост прочностных характеристик γ-фазы в сплавах системы железо–хром–никель обусловлен эффектом сверхбыстрого нагрева, при котором образующаяся γ-фаза “запоминает” дефектную структуру, характерную для исходной сильнодеформированной α-фазы.
ЗАКЛЮЧЕНИЕ
Исследованы магнитные свойства, фазовый состав, измерены температуры α → γ и γ → α превращений в сплавах системы железо-хром-никель различных составов. Определены составы сплавов, наиболее чувствительные к воздействию нагрева с использованием лазерного излучения. Установлено, что влияние интенсивного нагрева лазерным излучением на α → γ превращение приводит к образованию метастабильной γ-фазы с прочностными характеристиками существенно превышающими эти характеристики в стабильном состоянии. Сформулированы предположения о механизме влияния нагрева лазерным излучением на природу повышения прочностных характеристик γ-фазы.
Авторы выражают благодарность Д.В. Панову за участие в проведении экспериментов по лазерной термической обработке. Работа выполенена при финансовой поддержке РФФИ (проект № 20-08-00591а).
Список литературы
Галкин М.П., Либман М.А., Эстрин Э.И. // Материаловедение. 2014. № 3. С. 25.
Андреев А.О., Галкин М.П., Либман М.А. и др. // МиТОМ. 2014. № 1. С. 50.
Блинова Е.Н., Глезер А.М., Либман М.А., Эстрин Э.И. // Изв. вузов. Физ. 2014. Т. 57. № 4. С. 8.
Andreev A.O., Bykovskiy D.P., Osintsev A.V. et al. // J. Phys. Conf. Ser. 2017. V. 941. Art. No. 012027.
Андреев А.О., Блинова Е.Н., Либман М.А., Макушев С.Ю. // Материаловедение. 2016. № 10. С. 37.
Andreev A.O., Brovin M.A., Petrovskii V.N., Protasov E.A. // Russ. J. Appl. Phys. 2016. V. 61. No. 4. P. 591.
Гудремон Э. Специальные стали. Т. 1. М.: Металлургиздат, 1959. 952 с.
Дополнительные материалы отсутствуют.
Инструменты
Известия РАН. Серия физическая