Известия РАН. Серия физическая, 2021, T. 85, № 7, стр. 978-983
Применение лазерного облучения аморфных сплавов для получения аморфно-нанокристаллических композитов
И. Е. Пермякова 1, *, А. А. Иванов 2, А. В. Шеляков 2
1 Федеральное государственное унитарное предприятие
“Центральный научно-исследовательский институт черной металлургии имени И.П. Бардина”
Москва, Россия
2 Федеральное государственное автономное образовательное учреждение высшего профессионального образования “Национальный исследовательский ядерный университет “МИФИ”
Москва, Россия
* E-mail: inga_perm@mail.ru
Поступила в редакцию 25.01.2021
После доработки 25.02.2021
Принята к публикации 29.03.2021
Аннотация
С помощью эксимерного KrF лазера, согласно специально разработанным режимам облучения, реализована различная степень кристаллизации поверхности и объема быстрозакаленных лент аморфного сплава на основе кобальта и железа. Изучено влияние геометрии облучения и параметров лазерного воздействия на механическое поведение исследованного аморфного сплава и аморфно-кристаллических композитов в сопоставлении с эволюцией их структуры.
ВВЕДЕНИЕ
Как известно, аморфные сплавы (АС), обладая необычным комплексом свойств (магнитных, механических, коррозионных, электрических) относятся к классу неупорядоченных материалов [1, 2]. При воздействии внешних факторов возможны их переходы к более равновесному состоянию как с сохранением аморфности при структурной релаксации, так и с упорядочением в структуре, т.е. с выделением кристаллических фаз в процессе кристаллизации [3–5]. Использование лазерных технологий имеет огромный потенциал применительно к АС [6–8]. Задавая при лазерном отжиге закон распределения температурных полей в быстрозакаленных лентах, можно получать аморфно-кристаллические композиты. Грамотное использование лазерного излучения становится полезным для локального улучшения магнитных свойств АС, целенаправленного воздействия на механизмы их кристаллизации и порядок фазообразования, а также для повышения прочности [9]. Однако существует необходимость в комплексном исследовании влияния лазерного излучения на АС с целью контролируемой модификации их поверхности и объема, формирования аморфно-нанокристаллических композитов с повышенной термической стабильностью, ненулевой пластичностью, оптимальной твердостью, удовлетворительной коррозионностойкостью и улучшенными магнитно-мягкими характеристиками. Комбинирование аморфного и кристаллического состояний, образование градиентных структур даст новый импульс в создании так называемых “интеллектуальных” материалов, функционирующих с соответствующей реакцией на изменение внешних условий.
МАТЕРИАЛЫ И МЕТОДИКА ЭКСПЕРИМЕНТА
Объектом исследования выбран АС Co28.2Fe38.9Сr15.4Si0.3B17.2, полученный закалкой из расплава в виде ленты, толщиной ~25 мкм и шириной ~1 см. Облучение блестящей (неконтактной к закалочному барабану при получении) стороны ленты АС осуществляли эксимерным ультрафиолетовым KrF лазером серии CL-7100 (OptoSystems) с длиной волны λ = 248 нм и длительностью импульса τ = 20 нс по следующим режимам:
1) путем создания локальных облученных зон на поверхности аморфных лент через диафрагму c круговыми отверстиями (рис. 1). Данные зоны были распределены по трем вариантам, в строго заданном геометрическом порядке (рис. 2). Параметры лазерного излучения для каждой зоны подобраны с учетом проведенного ранее в работе [10] числового моделирования температурных полей в АС: частота следования f = 2 Гц, количество импульсов n = 500, энергия импульса Ei = 150 мДж, плотность энергии W = 0.6 Дж/см2, площадь кругового пятна S = 7 мм2. Совокупность указанных значений позволяет перевести зону облучение в нанокристаллическое состояние на глубину не менее половины толщины ленты.
Рис. 2.
Варианты избирательного облучения поверхности лент АС: плотно покрываемый (а), полосовой (б), шахматный (в). 1 – Аморфная матрица, 2 – зона лазерного воздействия.
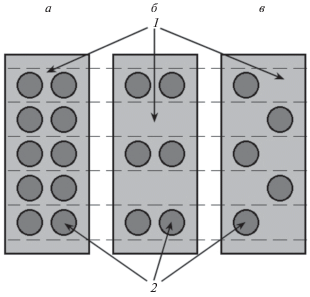
2) Количество импульсов n изменялось от 1 до 1000 (с шагом 100), а другие параметры лазерной установки оставались постоянными (f = 2 Гц, Ei = = 150 мДж, W = 0.6 Дж/см2).
3) Частота f варьировалась 2, 10, 20 и 50 Гц при n = 100, Ei = 150 мДж, W = 0.6 Дж/см2.
Пластичность аморфно-нанокристаллических композитов определяли на изгиб: образец помещали между двумя параллельными пластинами специального устройства при условии, что блестящая сторона лент всегда была в растянутом состоянии. После сближения пластин с постоянной скоростью пластичность ε оценивали по формуле:
где h – толщина ленты АС; d – расстояние между пластинами в момент разрушения образца. Из уравнения (1) следует, что при ε = 1 образец не ломается, сохраняя максимальную пластичность на изгиб, а при ε → 0 материал становится хрупким. Прочностные характеристики композитов определяли из кривых растяжения, полученных с помощью электромеханической универсальной испытательной машины (Instron-5565) со скоростью 0.1 мм/мин. Микротвердость HV образцов измеряли при индентировании пирамидой Виккерса с использованием твердомера ПМТ-3M (Lomo).Аморфную и кристаллические фазы в сплаве идентифицировали с помощью просвечивающей электронной микроскопии (ПЭМ) на микроскопе JEM 2100 (JEOL).
Морфологию поверхности облученных АС и их фрактографию изучали с привлечением растровой электронной микроскопии на установках JSM 35С (JEOL) и Versa 3D (FEI).
РЕЗУЛЬТАТЫ И ИХ ОБСУЖДЕНИЕ
В быстрозакаленных АС отсутствует механизм деформационного упрочнения [11]. Деформация АС при комнатной температуре происходит путем формирования и распространения сильнолокализованных полос сдвига. Так, понижение вязкости материала в полосах сдвига приводит к неконтролируемому их прохождению и разрушению образца при растяжении. В связи с этим, в настоящее время активно разрабатываются подходы повышения пластичности АС: например, путем оптимизации химического состава или создания аморфно-кристаллических композитов. В данной работе нами предприняты попытка сформировать аморфно-нанокристаллический материал на базе АС, применяя широкие возможности лазерного дизайна (селективность воздействия, высокие скорости нагрева или охлаждения, большая интенсивность и монохроматичность пучка, регулировка и оптимизация параметров излучения).
На основании экспериментальных данных по механическим испытаниям (табл. 1) установлено, что аморфно-нанокристаллические композиты, созданные по первому режиму лазерной обработки АС Co28.2Fe38.9Сr15.4Si0.3B17.2, с расположением в “шахматном” порядке аморфных и облученных зон (рис. 2в), демонстрируют наилучшее сопротивление при одноосном растяжении и пластичность на изгиб в сравнении с композитами, полученными по иной геометрии облучения (рис. 2а и 2б). Обсудим причины такого поведения. Разрушение исходных закаленных лент АС происходит вследствие проскальзывания после начала макроскопического течения вдоль плоскостей максимальных сдвиговых напряжений, которые располагаются под углом 45°–55° к направлению приложения нагрузки (рис. 3). Такая преимущественная ориентация полос сдвига и распространяющихся по ним трещин относительно оси образца может нарушаться при растяжении облученных композитов на основе АС. По-видимому, полосы сдвига и возникающие из них трещины, встречая на своей траектории определенное “препятствие” в виде селективных зон облучения с повышенными значениями твердости и модуля Юнга, тормозятся на них или вынужденно меняют направление движения. В связи с этим, могут наблюдаться признаки нестабильного разрушения по причине прерывистого распространения трещины. Следует отметить, что множественные пересечения под разными углами отклонившихся от своего первоначального направления полос сдвига, способствуют упрочнению [12]. Именно для этого в наших композитах наряду с облученными зонами сохранены протяженные участки аморфной фазы. Кроме того, на характер деформации и разрушения композитов из АС могут влиять переходные области, которые формируются между аморфной матрицей и зонами лазерного воздействия. Именно в них активно проходят диффузионные процессы, постепенная смена ближнего порядка на дальний, миграция областей свободного объема, изменение концентраций легирующих элементов (бора и кремния).
Таблица 1.
Механические характеристики (прочность, пластичность) композитов, полученных при лазерном дизайне поверхности лент АС Co28.2Fe38.9Сr15.4Si0.3B17.2
Вариант облучения АС | σ, ГПа | ε, отн. ед. |
---|---|---|
Необлученный (исходный) | 2.94 | 1 |
Плотно покрываемый | 1.13 | 0.01 |
Полосовой | 2.06 | 0.09 |
Шахматный | 2.35 | 0.28 |
Рис. 3.
Схема сдвигового разрушения АС при растяжении и соответствующая данному механическому испытанию ориентация полос сдвига в необлученном сплаве Co28.2Fe38.9Сr15.4Si0.3B17.2.
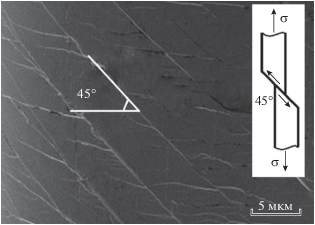
Вариант композитного материала, представленный на рис. 2а, разрушается макроскопически хрупко ниже предела упругости из-за слишком большой по площади и объему кристаллической составляющей в АС, которая вызывает блокировку пластического сдвига всего композита. Трещины в данном случае прямые и перпендикулярны оси растяжения.
Таким образом, сочетание в композите чередующихся в шахматном порядке аморфных (~83%) и нанокристаллических (~17%) областей, полученных в ходе лазерного отжига АС Co28.2Fe38.9Сr15.4Si0.3B17.2, обеспечивает как достаточно высокую прочность, так и ненулевую пластичность исследуемого материала.
Изучая морфологию картин разрушения при растяжении вдоль всей ширины ленточных композитов, представленных на рис. 2б и 2в, можно заметить, что необработанные лазером зоны характеризуются рваными и крупнозубчатыми краями излома с большим количеством полос сдвига на поверхности (рис. 4а). В свою очередь области, подверженные облучению, если и ломаются, то более ровно и прямолинейно, высота зубцов, сформированных вследствие отколов, мала (рис. 4б). Кроме того, проведен анализ микрофрактограмм, полученных с поверхностей разрушения аморфно-кристаллических композитов. На изломе аморфной зоны композита присутствуют как гладкие участки скола, так и “венный” узор (рис. 5а). Структура излома по мере продвижения к области лазерного отжига может существенно видоизменяться. Так, например, на рис. 5б продемонстрирован достаточно равномерный ямочный узор, образованный сеткой утонченных вен, а на рис. 5в – чешуйчатый излом. Вязкость материала сохраняется, но в меньших микромасштабах. Очевидно, что кристаллографический дальний порядок начинает постепенно устанавливаться, подобно тому, как это происходит и при печном нагреве АС [13, 14].
Рис. 4.
Морфология картин разрушения аморфно-нанокристаллического композита на основе АС Co28.2Fe38.9Сr15.4Si0.3B17.2: фрагмент необлученной поверхности (а), облученный участок (б).
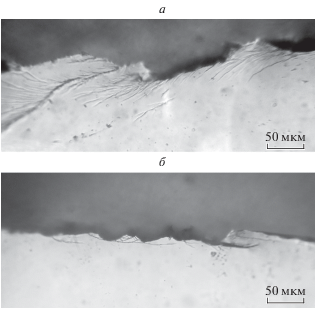
Рис. 5.
Фрактограммы композита: а – необлученная (аморфная) область; б, в – области вблизи зоны лазерного воздействия.
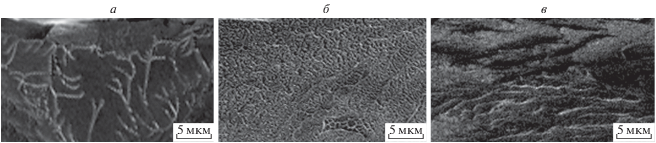
После лазерного воздействия на исследуемые быстрозакаленные ленты АС по второму и третьему режиму перед нами стояла задача выяснить как меняется микротвердость облученных зон в зависимости от одного выбранного параметра облучения (количества импульсов n или их частоты f) при сохранении постоянными других параметров (рис. 6). На рис. 6а показано, что поведение HV носит нелинейный характер при увеличении n (рис. 6а). На начальной стадии лазерной обработки значения микротвердости постепенно плавно возрастают. Вероятно, в структуре происходят атомные перестройки без диффузии на дальние расстояния. Вплоть до 300 импульсов сохраняется аморфное состояния сплава, что подтверждено контрастом типа “соль–перец”, не меняющимся при переходе от светлопольного изображения к темнопольному при исследованиях ПЭМ. Далее, при n ≥ 400, с выделением в аморфной матрице первых нанкристаллов α-Fe и α-Co со средним размером от 5 до 30 нм (рис. 7а) и увеличении их объемной доли при лазерном отжиге следует заметный рост микротвердости. Максимум HV соответствует n = 500. После обработки свыше 600 импульсов отмечается резкое снижение HV, связанное выделением боридов, полной кристаллизацией сплава и ростом зерен (рис. 7б и 7в).
Рис. 6.
Зависимость микротвердости АС Co28.2Fe38.9Сr15.4Si0.3B17.2 от параметров облучения: числа импульсов (а) при втором режиме лазерной обработки и частоты следования импульсов (б) при третьем режиме. Пунктиром показано значение HV исходных лент АС и необлученных зон, соответственно.
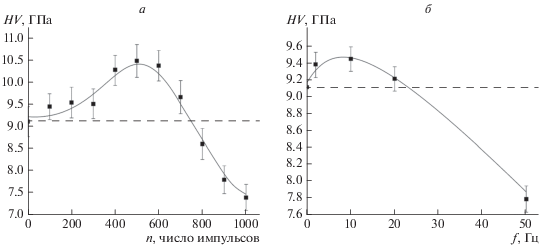
Рис. 7.
Эволюция структуры сплава Co28.2Fe38.9Сr15.4Si0.3B17.2 при лазерной обработке по второму режиму (ПЭМ-изображения): n = 300 (а), n = 600 (б), n = 800 (в).
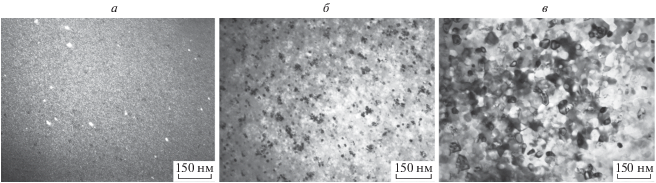
Обратимся к результатам, полученным после третьего режима лазерной обработки лент АС. Изучено влияния частоты следования импульсов на твердость АС Co28.2Fe38.9Сr15.4Si0.3B17.2. На рис. 6б представлен ход данной зависимости. Видно, что импульсное облучение в частотном диапазоне от 2 до 10 Гц способно повысить твердость материала. При f = 50 Гц HV снижается на 14.4% относительно первоначального значения, т.е. до обработки. Таким образом, увеличение f > 20 Гц приводит к стремительному разупрочнению, вызванному агрессивным влиянием тепловых процессов на АС при данном режиме лазерного отжига. На краях зон лазерного воздействия встречаются области со следами оплавления и дендритной кристаллизации (рис. 8).
ЗАКЛЮЧЕНИЕ
В ходе исследования получены три вида композитных материалов (плотно покрытые, полосовые, “шахматные”) представляющих собой аморфную матрицу, армированную кристаллическими областями, которые были сформированы в строго заданных технологических позициях по поверхности и в объеме быстрозакаленных лент АС за счет селективного воздействия эксимерного ультрафиолетового лазера. Установлено, что чередование в композите в шахматном порядке кристаллических и аморфных зон в соотношении приблизительно 1 : 5 по объемной доле, является оптимальным для сочетания высоких значений прочности и удовлетворительной пластичности. Показано, что зависимость микротвердости АС Co28.2Fe38.9Сr15.4Si0.3B17.2 от числа импульсов лазерного воздействия является немонотонной функцией. Данное поведение обусловлено последовательной сменой структурной релаксации в АС (с изменением локального композиционного и топологического упорядочения) на процесс кристаллизации (с зарождением и выделением кристаллических фаз, ростом зерен) при лазерной обработке. Показано, что режим облучения с частотой следования импульсов 2 Гц ≤ f ≤ 20 Гц (при n = 100, Ei = 150 мДж, W = 0.6 Дж/см2) улучшает и эффективно поддерживает высокие значения микротвердости АС Co28.2Fe38.9Сr15.4Si0.3B17.2 при сохранении аморфности в структуре.
Работа выполнена при финансовой поддержке РФФИ (проект № 20-08-00341а). Авторы выражают благодарность доценту Т.Н. Плужниковой (Тамбовский государственный университет им. Г.Р. Державина) за помощь и консультирование в испытаниях на растяжение.
Список литературы
Greer A.L. In: Physical metallurgy. V. 1. Netherlands, Amsterdam: Elsevier, 2014. P. 305.
Glezer A.M., Permyakova I.E. Melt-Quenched Nanocrystals. Boca Raton: CRC Press, 2013. 369 p.
Egami T., Iwashita T., Dmowski W. // Metals. 2013. V. 3. No. 1. P. 77.
Aronin A., Abrosimova G. // Metals. 2020. V. 10. No. 3. Art. No. 358.
Glezer A.M., Potekaev A.I., Cheretaeva A.O. Thermal and time stability of amorphous alloys. Boca Raton: CRC Press, 2017. 180 p.
Borodako K.A., Shelyakov A.V., Sitnikov N.N. et al. // J. Phys. Conf. Ser. 2020. V. 1461. № 1. Art. No. 012018.
Jiao Y., Brousseau E., Shen X. et al. // J. Mater. Process. Technol. 2020. V. 283. Art. No. 116714.
Шлыкова А.А., Федоров В.А., Гасанов М.Ф. и др. // Вектор науки ТГУ. 2018. Т. 43. № 1. С. 90.
Пермякова И.Е. // Изв. РАН. Сер. физ. 2018. Т. 82. № 9. С. 1197; Permyakova I.E. // Bull. Russ. Acad. Sci. Phys. 2018. V. 82. No. 9. P. 1086.
Пермякова И.E. // Изв. РАН. Сер. физ. 2020. Т. 84. № 7. С. 1014; Permyakova I.E. // Bull. Russ. Acad. Sci. Phys. 2020. V. 84. No. 7. P. 839.
Глезер А.М., Пермякова И.Е., Громов В.В. и др. Механическое поведение аморфных сплавов. Новокузнецк: Изд-во СибГИУ, 2006. 416 с.
Пермякова И.Е., Глезер А.М., Григорович К.В. // Изв. РАН. Сер. физ. 2014. Т. 78. № 10. С. 1246; Permyakova I.E., Glezer A.M., Grigorovich K.V. // Bull. Russ. Acad. Sci. Phys. 2014. V. 78. No. 10. P. 996.
Wetzig K., Pompe W., Fiedler H. et al. // Cryst. Res. Technol. 1983. V. 18. No. 9. P. 1181.
Алехин В.П., Хоник В.А. Структура и физические закономерности деформации аморфных сплавов. М.: Металлургия, 1992. 248 с.
Дополнительные материалы отсутствуют.
Инструменты
Известия РАН. Серия физическая