Известия РАН. Серия физическая, 2021, T. 85, № 7, стр. 1044-1052
Фазовый состав, структура и свойства электровзрывного покрытия системы WC–Ag–N после электронно-пучковой обработки и азотирования
Д. А. Романов 1, В. В. Почетуха 1, В. Е. Громов 1, *, Ю. Ф. Иванов 2, К. В. Соснин 1
1 Федеральное государственное бюджетное образовательное учреждение высшего образования
“Сибирский государственный индустриальный университет”
Новокузнецк, Россия
2 Федеральное государственное бюджетное учреждение науки
“Институт сильноточной электроники Сибирского отделения Российской академии наук”
Томск, Россия
* E-mail: gromov@physics.sibsiu.ru
Поступила в редакцию 25.01.2021
После доработки 25.02.2021
Принята к публикации 29.03.2021
Аннотация
Комбинированным методом, сочетающим электровзрывное напыление, электронно-пучковую обработку и азотирование получено покрытие на основе серебра, меди, карбидов и нитридов вольфрама. Методами современного физического материаловедения (сканирующая и просвечивающая электронная микроскопия, рентгенофазовый анализ) изучены структура и фазовый состав покрытий. Определены износостойкость, коэффициент трения, твердость и электроэрозионная стойкость.
ВВЕДЕНИЕ
В настоящее время для различных отраслей промышленности разрабатывается множество сплавов с определенными свойствами, в том числе и для электротехнической отрасли. В частности, для дугостойких контактов переключателей мощных электрических сетей используют сплавы на основе меди, серебра, алюминия, платины, золота молибдена, вольфрама и других химических элементов. Такие сплавы должны обладать определенным комплексом свойств, в том числе высокой электропроводностью, теплопроводностью, дугостойкостью, стойкостью против коррозии и др. Этим требованиям отвечают композиционные материалы на основе матрицы, обладающей высокой электропроводностью и наполнителя с высокой дугостойкостью. В качестве матрицы используют такие металлы как медь, серебро, золото, платина и сплавы на их основе. В качестве наполнителя применяют оксиды цинка, олова, меди, кадмия и других металлов, карбиды и нитриды вольфрама и молибдена [1–3]. Несмотря на приемлемые характеристики этих композиционных материалов их применение неэффективно с экономической точки зрения по сравнению с формированием аналогичных покрытий на поверхности экономичных подложек. Однако, получить такие композиционные покрытия до сих пор не представляется возможным из-за ряда проблем их формирования, в том числе низкой адгезии покрытий, либо невозможности получения покрытия из-за технологических особенностей того или иного метода. Исключение составляет метод электровзрывного напыления, позволяющий формировать композиционные покрытия, в том числе, и с высокой электроэрозионной стойкостью [4, 5]. Улучшить качество поверхности электровзрывных покрытий, гомогенизировать их объем и создать наноструктурное состояние позволяет обработка низкоэнергетическими электронными пучками [6]. Повысить твердость электровзрывных покрытий возможно с применением азотирования. Современная физика конденсированного состояния в качестве одного из своих приоритетных направлений указывает разработку методов повышения эксплуатационных характеристик различных материалов. Учитывая все вышесказанное, упрочнение поверхности контактов переключателей мощных электрических сетей является актуальной задачей как для физики конденсированного состояния, так и разработки новых способов формирования композиционных покрытий с лучшими эксплуатационными характеристиками.
С учетом вышеизложенного целью настоящей работы является исследование структуры и свойств композиционного покрытия состава Ag–WC–N, сформированного на меди комбинированным методом, сочетающим электровзрывное напыление, облучение импульсным электронным пучком и последующее азотирование в плазме газового разряда низкого давления.
МАТЕРИАЛ И МЕТОДИКА ИССЛЕДОВАНИЯ
Объектом исследования являлись покрытия состава Ag–WC–N, сформированные на меди марки М00 комбинированным методом, сочетающим электровзрывное напыление, облучение импульсным электронным пучком и последующее азотирование в плазме газового разряда низкого давления. Электровзрывное формирование покрытия проводили на установке ЭВУ 60/10М. Процесс осуществляли при следующих параметрах: время воздействия плазмы на поверхность образца ~100 мкс, поглощаемая плотность мощности на оси струи ~5.5 ГВт/м2, давление в ударно-сжатом слое вблизи облучаемой поверхности ~12.5 МПа, остаточное давление газа в рабочей камере ~100 Па; температура плазмы на срезе сопла ~104 К [7, 8]. В качестве материала для напыления использовали серебряную фольгу массой 350 мг, на поверхность которой помещали порошок WC массой 200 мг. Облучение импульсным электронным пучком (20 и 40 Дж/см2, 200 мкс, 3 имп.) и азотирование (923 К, 3 ч) выполняли на установке “КОМПЛЕКС” [9]. Исследование дефектной субструктуры и элементного состава осуществляли методами сканирующей (прибор Carl Zeiss EVO50 515 с приставкой для энергодисперсионного рентгеноспектрального анализа EDS X-Act) и просвечивающей дифракционной (прибор JEM 2100F) электронной микроскопии. Исследование фазового состава и структурных параметров образцов проводилось на дифрактометре XRD-6000 на CuKα-излучении. Анализ фазового состава осуществлен с использованием баз данных PDF 4+, а также программы полнопрофильного анализа POWDER CELL 2.4. Твердость покрытия измеряли с помощью ультрамикротестера Shimadzu DUH-211 (Pn = 30 мН). Трибологические свойства покрытия изучали на трибометре Pin on Disc and Oscillating TRIBOtester (“TRIBOtechnic”, Франция). Тест на износостойкость проводился в геометрии “шарик-диск” при следующих параметрах: шарик из стали ШХ15 диаметром 6 мм, нагрузка – 3 Н, дистанция – 300 м, радиус трека износа – 2 мм, скорость перемещения шарика – 25 мм/с. Износостойкость образцов с покрытием определяли, используя метод потери массы образца в результате испытания. Взвешивание образцов до и после испытаний осуществляли на аналитических весах марки CAUW 220D. Испытания на электроэрозионную стойкость покрытий в условиях дуговой эрозии проводили на контактах электромагнитных пускателей марки CJ20. В соответствии с требованиями режима испытаний AC-3 [10] на коммутационную износостойкость при работе в трехфазной цепи использовали переменный ток и индуктивную нагрузку. Значения низкого напряжения составляли 400/230 В, частота 50 Гц для токов до 320 А и cos φ = 0.35 и числе коммутационных циклов 7000. Электропроводность измерялась на том же стенде, где проводили испытания на электроэрозионную стойкость.
РЕЗУЛЬТАТЫ И ИХ ОБСУЖДЕНИЕ
В результате испытаний на износостойкость установлено, что износостойкость медного образца с нанесенным покрытием превышает износостойкость меди без покрытия в 1.5 раза. Коэффициент трения образцов с покрытием составляет μ = 0.6, что на 14% выше коэффициента трения исходных образцов меди.
Твердость покрытия, измеренная на поперечном шлифе вдоль дорожки, проходящей параллельно поверхности покрытия на расстоянии 20 мкм от поверхности, изменяется в весьма широком интервале от 540 до 15500 МПа при среднем значении 3920 МПа. Твердость образца меди без покрытия составляет 1270 МПа. Следовательно, твердость сформированного покрытия превышает твердость исходной меди более чем в 3 раза.
Электроэрозионная стойкость покрытий отвечает требованиям стандартов [10]. Число циклов включения/отключения до полного разрушения покрытий составило 7000. Это на 17% больше по сравнению с покрытиями системы CuO–Ag, полученными электровзрывным методом в работе [11]. Электрическое сопротивление покрытий системы ZnO–Ag при этом также как и для покрытия, полученного комбинированным методом, не превышает 15 мкОм. Электропроводность сформированных покрытий близка к электропроводности серебра [12] и составляет 62.0 МСм/м.
Методом сканирующей электронной микроскопии поперечных шлифов показано, что толщина покрытия изменяется в пределах 50–85 мкм (рис. 1а). Покрытие структурно неоднородно, содержит включения различной формы и размеров (рис. 1б).
Рис. 1.
Результат исследования покрытий состава Ag–WC– методом сканирующей электронной микроскопии. Поперечный шлиф. а – Общий вид покрытия и подложки; б – увеличенное изображение структурных элементов покрытия; в – совмещенное изображение структуры с содержанием элементов вдоль линии А–А; г – изменение концентрации элементов I вдоль линии А–А в зависимости от толщины h покрытия; д – наложение изображений, полученных в характеристическом рентгеновском излучении атомов меди, серебра и вольфрама на общий вид покрытия и подложки; е – наложение изображений, полученных в характеристическом рентгеновском излучении атомов меди, серебра и вольфрама на увеличенное изображение структурных элементов покрытия.
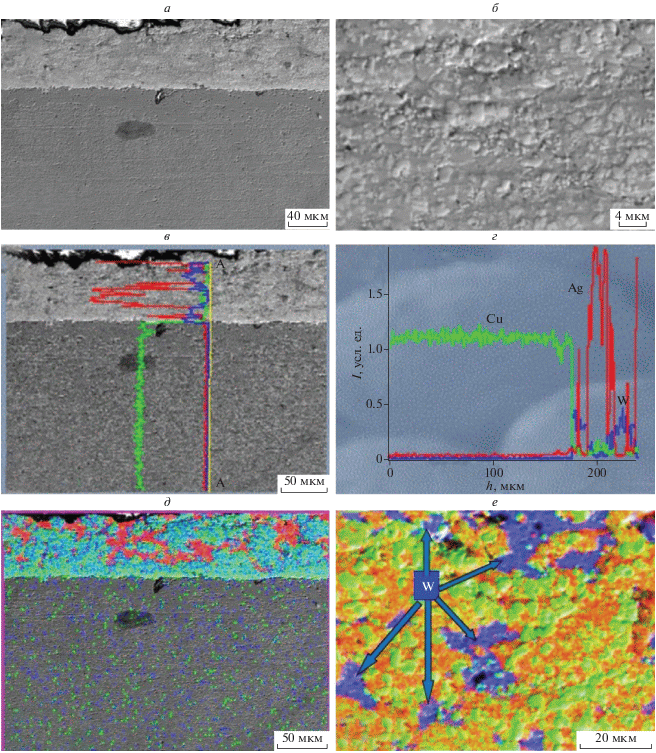
Ранее было показано [13], что в основе формирования структуры электровзрывных покрытий различных систем лежит механизм, основанный на возникновении динамических ротаций частиц напыляемого материала [14–18]. В работе [19] после электровзрывного напыления (ЭВН) покрытий системы CuO–Ag наблюдались ротации с размерами от 1 до 4 мкм, обогащенные серебром. Ротации имели хорошо различимую оболочку толщиной от 0.1 до 0.2 мкм, отделяющую их от окружающего материала покрытия. При исследовании покрытий, полученных в настоящей работе, логично предположить, что и в этом случае природой структурообразования может являться формирование вихревых иерархически организованных структур. Удельный вес серебра составляет 10.5 г/см3, а вольфрама – 19.3 г/см3. Это соотношение отвечает условиям формирования ротационной вихревой структуры, согласно которым, удельный вес компонентов отличается почти в два раза [19]. Однако, последующая после ЭВН обработка электронным пучком и азотирование привели к расплавлению покрытия и гомогенизации его структуры (рис. 1). Скорее всего это явилось причиной “исчезновения” динамических ротаций, характерных для структуры электровзрывных покрытий.
Элементный состав покрытия изучали методами микрорентгеноспектрального анализа. Установлено, что основным элементом покрытия является серебро, в значительно меньшем количестве присутствуют вольфрам и медь (рис. 1в, 1г). Указанные элементы распределены в покрытии неоднородно (рис. 1д, 1е). Обнаруживаются островки, обогащенные атомами вольфрама (рис. 1е). Размеры таких островков изменяются в пределах от единиц до десятков микрометров.
Исследования, выполненные методами рентгенофазового анализа, выявили присутствие в покрытии твердых растворов на основе меди и серебра, карбидов вольфрама состава WC и W2C и нитрида вольфрама WN. Основными являются фазы на основе меди, серебра и карбида вольфрама. Нитриды вольфрама присутствуют в небольшом (до 2 об. %) количестве.
Дефектную субструктуру, элементный и фазовый состав покрытия изучали методами просвечивающей электронной дифракционной микроскопии. Элементный состав фольги изучали методами микрорентгеноспектрального анализа. Формирующие покрытие элементы распределены неоднородно, образуя области разнообразной формы и размеров (рис. 2). Основными элементами данного участка фольги являются медь, вольфрам и серебро (табл. 1).
Рис. 2.
Светлопольное изображение участка покрытия (а) и изображение данного участка фольги, полученное в характеристическом рентгеновском излучении атомов углерода (б), азота (в), меди (г), серебра (д) и вольфрама (е).

Таблица 1.
Количественные результаты микрорентгеноспектрального анализа участка фольги, изображение которого приведено на рис. 5а
Элемент | E, кэВ | Масс. % | Количество | Погрешность, % | Ат. % |
---|---|---|---|---|---|
C (K) | 0.277 | 1.38 | 1791 | 3.13 | 2.66 |
Cu (K) | 8.040 | 53.24 | 703 980 | 0.01 | 71.68 |
Ag (L) | 2.984 | 13.89 | 99 865 | 0.07 | 11.01 |
W (M) | 1.774 | 31.49 | 255 149 | 0.03 | 14.65 |
Всего | – | 100 | – | – | 100 |
Результаты, представленные на рис. 3, свидетельствуют о том, что структура покрытия существенным образом различается по мере удаления от поверхности обработки. Верхний слой покрытия имеет нанокристаллическую структуру (рис. 3а). Размер кристаллитов изменяется в пределах 10–15 нм. Средняя часть покрытия содержит области со слоистой структурой (рис. 3б) и области с зеренной структурой (рис. 3в). По границам и в объеме зерен располагаются частицы, размеры которых изменяются в пределах 3–5 нм. В области контакта покрытия и подложки формируется структура столбчатого типа, имеющая нанокристаллическое строение (рис. 3г).
Рис. 3.
Электронно-микроскопическое изображение структуры покрытия состава Ag–WC–N, сформированного на медной подложке комбинированным методом. а – верхний слой с нанокристаллической структурой; б – средняя часть со слоистой структурой; в – области с зеренной структурой в средней части; г – структура столбчатого типа с нанокристаллическим строением, формирующаяся в области контакта покрытия и подложки.
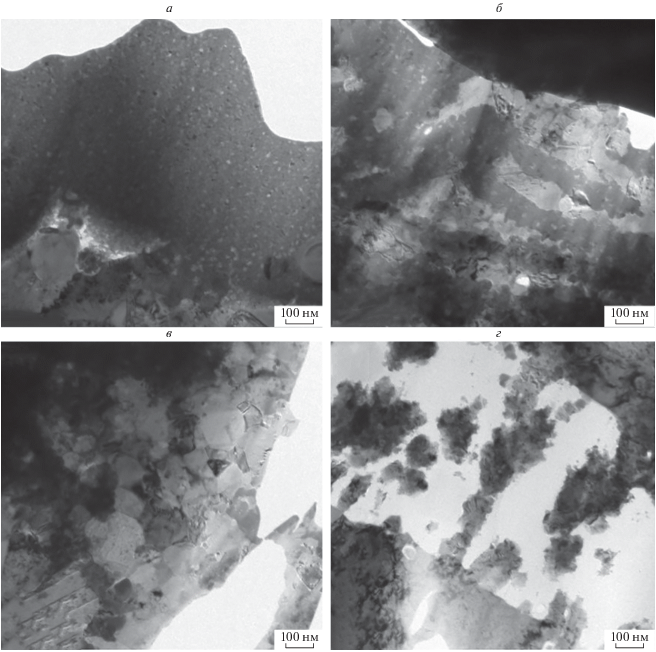
Результаты фазового анализа участка покрытия, электронно-микроскопическое изображение которого представлено на рис. 3а, приведены на рис. 4. Индицирование микроэлектронограммы (рис. 4в), полученной с участка покрытия, выделенного селекторной диафрагмой (рис. 4б), свидетельствует о том, что данная область покрытия сформирована кристаллитами нитрида серебра состава AgN3.
Рис. 4.
Электронно-микроскопическое изображение структуры верхнего слоя с нанокристаллической структурой покрытия состава Ag–WC–N, сформированного на медной подложке комбинированным методом. а – Светлопольное изображение; б – светлопольные изображение с которого получена микроэлектронограмма, в – микроэлектронограмма, полученная с области фольги, приведенной на б; г – темнопольное изображение, полученное в рефлексе [402]AgN3. На в указан рефлекс, в котором получено темнопольное изображение.
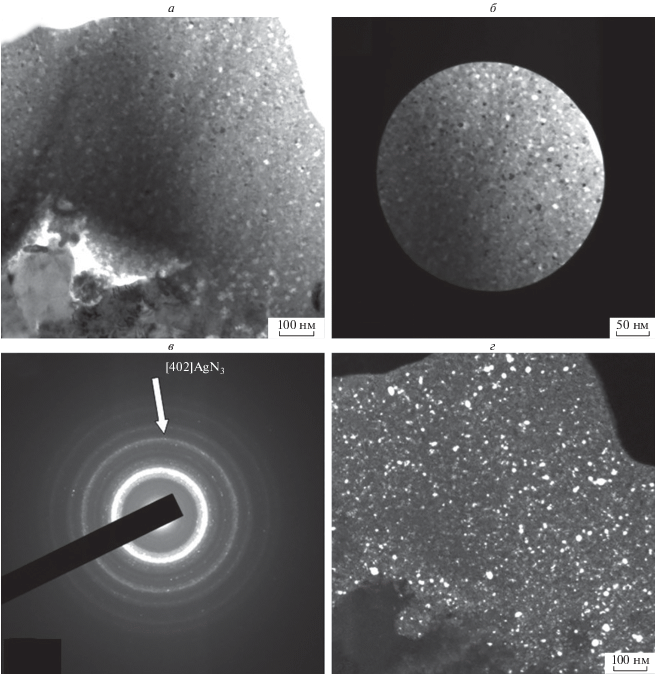
Результаты фазового анализа участка покрытия, электронно-микроскопическое изображение которого представлено на рис. 3в, приведены на рис. 5. Индицирование микроэлектронограммы (рис. 5в), полученной с участка покрытия, выделенного селекторной диафрагмой (рис. 5б), свидетельствует о том, что данная область покрытия сформирована зернами твердого раствора на основе меди. В объеме и на границах зерен располагаются наноразмерные (3–5 нм) частицы нитрида серебра состава AgN3 и карбида вольфрам состава W2C (рис. 5д).
Рис. 5.
Электронно-микроскопическое изображение областей с зеренной структурой в средней части покрытия состава Ag–WC–N, сформированного на медной подложке комбинированным методом. а – Светлопольное изображение; б – светлопольные изображение с которого получена микроэлектронограмма; в – микроэлектронограмма, полученная с области фольги, приведенной на б; г – темнопольное изображение, полученное в рефлексе [111]Cu (рефлекс 1 указан стрелкой на в); д – темнопольное изображение, полученное в рефлексе [002]Cu + [310]AgN3 + [102]W2C (рефлекс 2 указан стрелкой на в).
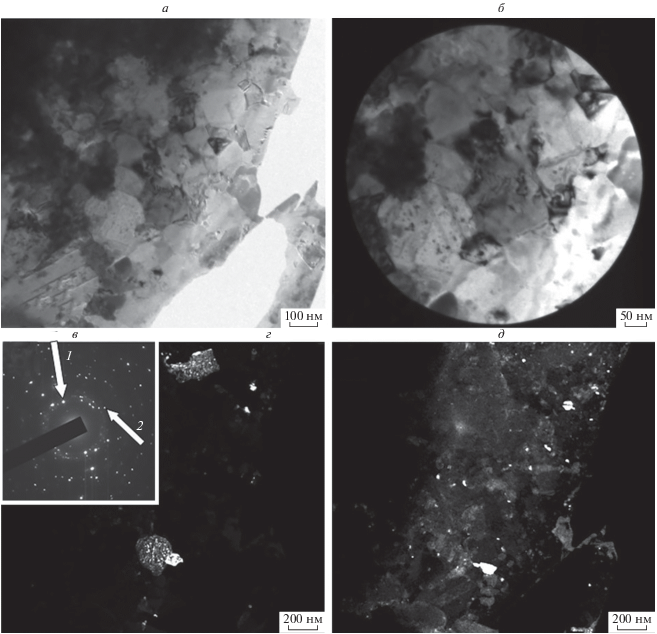
ЗАКЛЮЧЕНИЕ
Комбинированным методом, сочетающим электровзрывное напыление покрытия, облучение импульсным электронным пучком и последующее азотирование в плазме газового разряда низкого давления, на меди сформированы покрытия состава Ag–WC–N толщиной до 85 мкм. Показано, что износостойкость покрытия превышает износостойкость меди в 1.5 раза. Коэффициент трения образцов с покрытием на 14% выше коэффициента трения исходных образцов меди. Установлено, что средняя твердость покрытия составляет 3920 МПа (твердость подложки – 1270 МПа), т.е. твердость сформированного покрытия превышает твердость исходной меди более чем в 3 раза. Методами микрорентгеноспектрального анализа установлено, что основным элементом покрытия является серебро, в значительно меньшем количестве присутствуют вольфрам и медь. Методами рентгенофазового анализа в покрытии выявлены твердые растворы на основе меди и серебра, а также карбиды вольфрама состава WC и W2C, и нитрид вольфрама WN. Основными являются фазы на основе меди, серебра и карбида вольфрама. Методами микрорентгеноспектрального анализа обнаружено, что элементы, формирующие покрытие, распределены неоднородно, образуя области разнообразной формы и размеров. Установлено, что структура покрытия существенным образом зависит от расстояния до поверхности обработки. Верхний слой покрытия имеет нанокристаллическую структуру, сформированную нитридами серебра. Размер кристаллитов изменяется в пределах 10–15 нм. Средняя часть покрытия содержит области двух типов: со слоистой структурой (слои обогащены атомами серебра и вольфрама) и области с зеренной структурой. Зерна сформированы твердым раствором на основе меди. В объеме и на границах зерен располагаются наноразмерные (3–5 нм) частицы нитрида серебра состава AgN3 и карбида вольфрама состава W2C. В области контакта покрытия и подложки формируется структура столбчатого типа, имеющая нанокристаллическое строение.
Исследование выполнено при финансовой поддержке Совета по грантам Президента Российской Федерации для государственной поддержки молодых российских ученых – докторов и кандидатов наук МД-486.2020.8 и МК-5585.2021.4 и РФФИ (проект № 20-08-00044). Электронно-микроскопический микродифракционный фазовый анализ покрытия осуществлен при финансовой поддержке РНФ (проект № 19-19-00183).
Список литературы
Li H., Wang X., Guo X. et al. // Mater. Des. 2017. V. 114. P. 139.
Ray N., Kempf B., Mützel T. et al. // Mater. Des. 2015. V. 85. P. 412.
Ray N., Kempf B., Wiehl G. et al. // Mater. Des. 2017. V. 121. P. 262.
Romanov D., Moskovskii S., Konovalov S. et al. // J. Mater. Res. Technol. 2019. V. 8. P. 5515.
Романов Д.А., Будовских Е.А., Громов В.Е., Иванов Ю.Ф. Электровзрывное напыление износо- и электроэрозионностойких покрытий. Новокузнецк: ООО “Полиграфист”, 2014. 203 с.
Громов В.Е., Загуляев Д.В., Иванов Ю.Ф. и др. Структура и упрочнение силумина, модифицированного электронно-ионной плазмой. Новокузнецк: Изд. СибГИУ, 2020. 285 с.
Романов Д.А., Молотков С.Г., Степиков М.А., Громов В.Е. // ФПСМ. 2017. Т. 14. № 1. С. 100.
Багаутдинов А.Я., Будовских Е.А., Иванов Ю.Ф., Громов В.Е. Физические основы электровзрывного легирования металлов и сплавов. Новокузнецк: Изд. СибГИУ, 2007. 301 с.
Коваль Н.Н., Иванов Ю.Ф. // Изв. вузов. Физ. 2019. № 7. С. 59; Koval N.N., Ivanov Yu.F. // Russ. Phys. J. 2019. V. 62. No. 7. P. 1161.
ГОСТ 2933-83. Испытание на механическую и коммутационную износостойкость. Аппараты электрические низковольтные методы испытаний.
Romanov D.A., Moskovskii S.V., Sosnin K.V. et al. // Mater. Res. Exp. 2019. V. 6. Art. No. 055042.
Rautio T., Hamada A., Kumpula J. et al. // Surf. Coat. Technol. 2020. V. 403. Art. No. 126426.
Панин В.Е., Громов В.Е., Романов Д.А. и др. // ДАН. 2017. Т. 472. № 6. С. 650; Panin V.E., Gromov V.E., Romanov D.A. et al. // Dokl. Phys. 2017. V. 62. No. 2. P. 67.
Мещеряков Ю.И., Атрошенко С.А. // Изв. вузов. Физ. 1992. № 4. С. 105.
Мещеряков Ю.И., Диваков А.К., Жигачева Н.И., Мышляев М.М. // ПМТФ. 2007. Т. 48. № 6. С. 135.
Панин В.Е., Егорушкин В.Е. // Физ. мезомех. 2013. Т. 16. № 3. С. 7.
Панин В.Е., Панин А.В., Елсукова Т.Ф., Попкова Ю.Ф. // Физ. мезомех. 2014. Т. 17. № 6. С. 7.
Панин В.Е., Егорушкин В.Е., Панин А.В., Чернявский А.Г. // Физ. мезомех. 2016. Т. 19. № 1. С. 31.
Романов Д.А., Московский С.В., Глезер А.М. и др. // Изв. РАН. Сер. физ. 2019. Т. 83. № 10. С. 1389; Romanov D.A., Moskovskii S.V., Glezer A.M. et al. // Bull. Russ. Acad. Sci. Phys. 2019. V. 83. No. 10. P. 1270.
Дополнительные материалы отсутствуют.
Инструменты
Известия РАН. Серия физическая