Известия РАН. Серия физическая, 2021, T. 85, № 9, стр. 1224-1228
Накопление дефектов в поликристаллических твердых растворах медь–алюминий и роль энергии дефекта упаковки
Н. А. Конева 1, Л. И. Тришкина 1, Т. В. Черкасова 1, 2, *, Н. А. Попова 1, Н. В. Черкасов 1
1 Федеральное государственное бюджетное образовательное учреждение высшего образования
“Томский государственный архитектурно-строительный университет”
Томск, Россия
2 Федеральное государственное бюджетное образовательное учреждение высшего образования
“Национальный исследовательский Томский политехнический университет”
Томск, Россия
* E-mail: cherkasova_tv@mail.ru
Поступила в редакцию 19.04.2021
После доработки 12.05.2021
Принята к публикации 28.05.2021
Аннотация
С использованием просвечивающей дифракционной электронной микроскопии исследована эволюция дислокационной структуры при активной пластической деформации в сплавах медь–алюминий в интервале концентраций 0–14 ат. % Аl. По микроснимкам определены типы дислокационных субструктур в зависимости от концентрации легирующего элемента. Измерены параметры дефектной структуры и установлена их взаимосвязь с энергией дефекта упаковки.
ВВЕДЕНИЕ
Количество содержания второго компонента (Al) в сплавах Cu–Al дает возможность широко изменять энергию дефекта упаковки (ЭДУ), а также степень ближнего порядка в сплавах, которое дает изменение сопротивлению движения дислокаций по материалу. Величина энергии дефекта упаковки при увеличении содержания Al быстро падает. Пластическая деформация металлов и сплавов позволяет увеличивать накопление различных дефектов структуры, характеризующихся такими параметрами, как средняя скалярная плотность дислокаций 〈ρ〉, плотность статически запасенных дислокаций ρS, плотность геометрически необходимых дислокаций ρG, кривизна-кручение кристаллической решетки χ и плотность микродвойников ρдв, а также деформационных микрополос и оборванных субграниц. Формирование дефектной субструктуры в материале возможно при выполнении таких факторов, как пластическая деформация и ее скорость, температура испытания, средний размер зерен 〈d〉 и ЭДУ γДУ, величина которой может влиять на формирование дислокационной субструктуры. Субструктурное упрочнение приводит к изменению напряжения старта дислокаций и сил трения, (что особенно может быть заметно в самом начале пластического течения) и, следовательно, к изменению сопротивления началу деформации, что является одним из важных механизмов упрочнения металлов и сплавов [1–3].
Проведем анализ влияния ЭДУ на формирование и накопление различных субструктурных дефектов в поликристаллических материалах. Подобных количественных исследований в литературе недостаточно.
Для металлов без примесей, таких как Cu, Al и Ni, при небольших γДУ средняя плотность дислокаций 〈ρ〉 увеличивается [4]. Следует отметить, что при исследовании дефектной структуры рентгеноструктурным методом по плотности дислокаций не соответствуют данным, полученным структурными методами. Это приведено при исследовании чистой меди и сплавов с добавлением цинка Cu–Zn, содержание Zn в сплаве составляло 10 и 30 вес. % [5]. Энергия дефекта упаковки в данных материалах составляла 41, 22 и 7 МДж/м2 соответственно. В сплавах системах Cu–Al проводилось изучение влияния γДУ на измерение плотности дислокаций при ударных нагружениях. Количество второго компонента Al составляло 0.2, 2, 4 и 6 вес. % [6]. Анализ результатов данной работы показал связь ЭДУ с накоплением дислокаций [6]. В настоящее время работ по исследованию влияния γДУ на скорость накопления различных дефектов мало.
В современных условиях создание материалов с заранее заданными прочностными свойствами требует детального исследования тонкой микроструктуры сплавов. Известно, что вариация ЭДУ может приводить к формированию сплавов с различными типами дислокационных субструктур и соответственно к созданию их прочностных характеристик. Сплавы системы Cu–Al являются модельными для осуществления этих задач. С изменением величины ЭДУ от 10 до 60 мДж/м2 наблюдается широкий спектр типов дислокационных субструктур [2, 7–9].
Целью настоящей работы являлось проведение изучение качественных и количественных параметров. Обнаружение связь между параметрами и их изменение с величиной ЭДУ в сплавах системы Cu–Al при разных степенях деформации.
МАТЕРИАЛЫ И МЕТОДИКА ИССЛЕДОВАНИЯ
Изучение дефектной субструктуры проводилось на сплавах системы медь-алюминий. Содержание второго элемента Al изменялось от 0.5 до 14 ат. %. Изучение дефектной структуры проводилось для средних размеров зерен 20 и 240 мкм. К образцам с размером 100 × 12 × 2 мм3 применялся тип деформации растяжения на машине Instron со скоростью 2 · 10–2 с–1. Исследования образцов проводилось при температуре 293 К. Для изучения дислокационной субструктура применялся метод просвечивающей дифракционной электронной микроскопии (ПЭМ). Деформация образцов: εист = 0.02–0.90. Снимки в колонне микроскопа увеличивали до Х30000. По микрофотографиям, которые были получены с помощью электронного микроскопа, проводились измерения следующих параметров дислокационной субструктуры (ДСС): плотность дислокаций и ее составляющие, плотность микродвойников и кривизна-кручение кристаллической решетки. Методы, которые использовались для определения параметров ДСС, описаны в [10].
РЕЗУЛЬТАТЫ ИССЛЕДОВАНИЯ
Как было отмечено ранее, величина второго элемента Al в сплавах Сu–Al оказывает существенное влияние на величину энергии дефекта упаковки и формирование типов ДСС. В сплавах Cu + 0.5; 3; 5 aт. % Al, где γДУ составляет ∼4 ·104 Дж/м2, при умеренных степенях деформации (εист = 0.05–0.10) наблюдается следующая последовательность эволюции ДСС: хаотическое распределение дислокаций, клубковая, ячеистая субструктура и фрагментированная. Увеличение содержания второго элемента Al до 14 ат. %, при тех же степенях деформации, может приводить к формированию следующей цепочки ДСС: хаотическое распределение дислокаций, дислокационные скопления, длинные прямолинейные дислокации, которые располагаются в основном вдоль плотноупакованных направлений, дислокационные сгущения, которые состоят из нескольких дислокаций и сетчатой, дислокации которых пересекаются в двух направлениях. Рост степени деформации сопровождается появлением разориентированных субструктур. При повышенных степенях деформации (εист = 0.20–0.90) и с ростом второго компонента алюминия до 14 ат. % образуются ДСС с разориентировками более 0.5°: ячеистая ДСС, микрополосовая ДСС, ячеисто-сетчатая ДСС и микродвойниковая. При деформациях εист = 0.10 формируется одна система микродвойников, а при εист = 0.30–90 наблюдается образование нескольких систем микродвойников.
Рост плотности дефектов, таких как плотность дислокаций, микрополос и микродвойников влечет за собой образование разориентировок, которые характеризуются появлением на микроснимках экстинкционных деформационных контуров, возникающих в исследованных сплавах при повышенных степенях деформации (рис. 1). Появление контуров свидетельствует о возникновении кривизны-кручения кристаллической решетки в материале [11, 12].
Рис. 1.
Микроснимки экстинкционных деформационных контуров (К) в исследованных сплавах при повышенных степенях деформации (εист = 0.30–0.90).
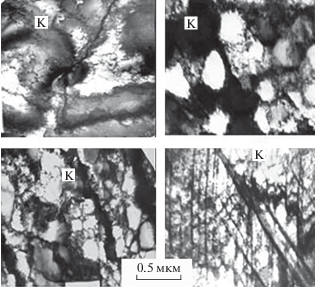
По микрофотографиям были измерены величины 〈ρ〉, ρS и ρG в зависимости от величины γДУ [13, 14]. Полученные экспериментальные данные для размеров зерен 20 и 240 мкм, деформированных до εист = 0.30 показаны на рис. 2. Видно, что величина плотности дислокаций и ее компонент убывают ростом ЭДУ. Плотность статистически запасенных дислокаций выше в сплавах с низкой ЭДУ. Анализ данного рисунка позволяет указать влияния размера зерен на величину ρS и ρG при малых значениях ЭДУ, а именно: величина ρS и ρG выше в сплавах с размером зерна 20 мкм. При больших значениях ЭДУ и рассмотренных размерах зерен значения ρS и ρG отличаются незначительно.
Рис. 2.
Взаимосвязь средней скалярной плотности дислокаций 〈ρ〉, плотности статистически запасенных ρS и геометрически необходимых ρG дислокаций от энергии дефекта упаковки γДУ при разных размерах зерен 〈d〉 = 20 (а), 240 мкм (б). Степень деформации εист = 0.30.
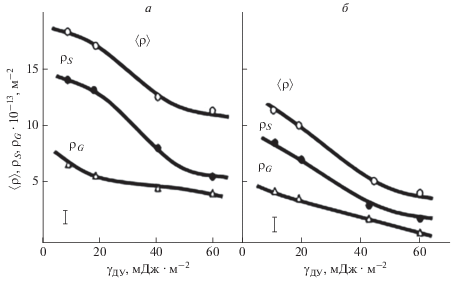
Взаимосвязь плотности микродвойников с изменением ЭДУ для исследованных размеров зерен показана на рис. 3. Анализируя зависимости на рис. 3 можно отметить следующее: при увеличении энергии дефекта упаковки плотность микродвойников линейно уменьшается при всех исследованных степенях деформации. Плотность микродвойников уменьшается в сплавах с меньшим размером зерна при всех исследованных степенях деформации.
Рис. 3.
Изменение плотности микродвойников ρдв с энергией дефекта упаковки γДУ при степенях деформации εист: 0.10 (1), 0.20 (2), 0.30 (3), 0.40 (4), 0.50 (5). Размер зерен 〈d〉 = 20 (а), 240 мкм (б).
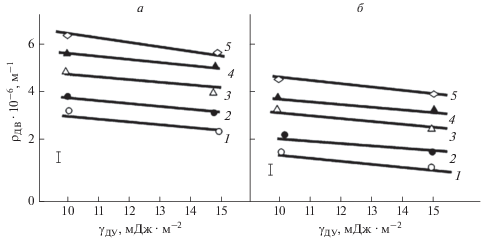
Как было отмечено выше, что формирование в материале экстинкционных деформационных контуров показывают наличие кривизны-кручения кристаллической решетки χ. На рис. 4 приведен пример изменения величины χ от величины энергии дефекта упаковки. С низкой ЭДУ величина кривизны-кручения кристаллической решетки χ растет с деформацией для двух исследованных размеров зерен. Анализ зависимостей показывает, что максимальное значение χ наблюдается в сплавах с низкой ЭДУ. В сплавах с размером зерна 20 мкм и высокими и низкими значениями ЭДУ величина χ отличается до 2 раз.
ЗАКЛЮЧЕНИЕ
Изучена эволюция дислокационной субструктуры в сплавах Cu–Al с изменением величины энергии дефекта упаковки. Установлено влияние энергии дефекта упаковки на параметры дефектной субструктуры. Снижение энергии дефекта упаковки в сплавах приводит к формированию новых типов ДСС, а также к увеличению средней скалярной плотности дислокаций и ее составляющих ρS и ρG. Плотность микродвойников уменьшается с ростом энергии дефекта упаковки. При повышенных степенях деформации в материале возникают экстинкционные деформационные контуры, которые доказывают существование разориентировок в материале и указывают на наличие кривизны-кручения кристаллической решетки. Величина χ уменьшается с ростом γДУ.
Работа выполнена в рамках государственного задания Министерства науки и высшего образования Российской Федерации (тема № FEMN-2020-0004).
Список литературы
Конева Н.А., Козлов Э.В. В кн.: Структурные уровни пластической деформации и разрушения. Новосибирск: Наука, 1990. С. 123.
Конева Н.А., Козлов Э.В. // Изв. вузов. Физ. 1996. Т. 33. № 2. С. 89.
Sevillano J.G. // Mater. Sci. Technol. 1994. V. 6. P. 21.
Dini G., Ueji R., Najafizadeh A., Minir S.M. // Mater. Sci. Engin. A. 2010. V. 527. P. 2759.
Zhao Y.H., Liao X.Z., Horita Z. et al. // Mater. Sci. Engin. A. 2008. V. 493. P. 123.
Steffens Th., Schwink Ch., Korner A., Karnthaler H.P. // Phil. Mag. A. 1987. V. 56. No. 2. P. 161.
Crampin S., Vedensky D.D., Monnier R. // Phil. Mag. A. 1993. V. 67. No. 6. P. 1447.
Дударев Е.Ф. Корниенко А.Л., Бакач Г.П. // Изв. вузов. Физ. 1991. № 3. С. 35.
Коновалова Е.В. Влияние фундаментальных характеристик поликристаллов однофазных ГЦК сплавов на параметры зернограничного ансамбля. Дис. … канд. физ.-мат. наук. Томск: Томский гос. ун-т, 2001. 314 с.
Конева Н.А. Черкасова Т.В., Тришкина Л.И. и др. Дислокационная структура и дислокационные субструктуры. Электронно-микроскопические методы измерения их параметров. Новокузнецк: Изд. центр СибГИУ, 2019. 136 с.
Конева Н.А., Тришкина Л.И., Черкасова Т.В. // Изв. РАН. Сер. физ. 2019. Т. 83. № 6. С. 830; Koneva N.A., Trishkina L.I., Cherkasova T.V. // Bull. Russ. Acad. Sci. Phys. 2019. V. 83. No. 6. Р. 756.
Конева Н.А., Тришкина Л.И., Черкасова Т.В., Козлов Е.В. // Изв. РАН. Сер. физ. 2017. Т. 81. № 3. С. 419; Koneva N.A., Trishkina L.I., Cherkasova T.V., Kozlov E.V. // Bull. Russ. Acad. Sci. Phys. 2017. V. 81. No. 3. P. 391.
Koneva N.A., Trishkina L.I., Cherkasova T.V. // Lett. Mater. 2017. V. 7. No. 3. P. 282.
Козлов Е.В., Тришкина Л.И., Черкасова Т.В., Конева Н.А. // Изв. РАН. Сер. физ. 2011. Т. 75. № 5. С. 830; Kozlov E.V., Trishkina L.I., Cherkasova T.V., Koneva N.A. // Bull. Russ. Acad. Sci. Phys. 2011. V. 75. No. 5. P. 670.
Дополнительные материалы отсутствуют.
Инструменты
Известия РАН. Серия физическая