Известия РАН. Серия физическая, 2022, T. 86, № 11, стр. 1553-1559
Эволюция микроструктуры, прочности, пластичности и электропроводности в ультрамелкозернистом сплаве Cu–0.5Cr при холодной прокатке и старении
Е. А. Саркеева 1, *, И. В. Александров 1
1 Федеральное государственное бюджетное образовательное учреждение высшего образования
“Уфимский государственный авиационный технический университет”
Уфа, Россия
* E-mail: sarkeeva.e@inbox.ru
Поступила в редакцию 30.06.2022
После доработки 15.07.2022
Принята к публикации 22.07.2022
- EDN: XMVAYN
- DOI: 10.31857/S0367676522110230
Аннотация
Представлены результаты исследования эволюции микроструктуры, механических свойств и электропроводности ультрамелкозернистого состояния сплава Cu–0.5(вес. %)Cr в ходе холодной прокатки с различными степенями обжатия и старения. Ультрамелкозернистое состояние было получено методом равноканального углового прессования. Исследования проведены в сравнении с крупнозернистым состоянием сплава.
ВВЕДЕНИЕ
Сплавы системы Cu–Cr являются объектом активных исследований, так как обладают высокими прочностью, электро- и теплопроводностью. Данные материалы используются для производства электрических проводников, используемых в миниатюрных интеллектуальных вычислительных системах в микроэлектронике в качестве профилей для коллекторных пластин электродвигателей, которые требуют высокопрочных проводящих материалов [1, 2].
Необходимое сочетание прочности и электропроводности возможно достичь благодаря оптимальной деформационной-термической обработке [1–3]. Традиционно, для получения листовых заготовок применяется холодная деформация прокаткой. Однако материалы после прокатки, наряду с повышенной прочностью, характеризуются пониженными пластичностью и электропроводностью, что снижает потенциал их применения и заставляет большее внимание уделять достижению баланса между данными свойствами. Особое внимание при формировании оптимального комплекса свойств отводится пост-деформационной термообработке (ТО), т.к., с одной стороны, реализованное в результате старения дисперсионное упрочнение дает большой прирост прочности, а, с другой стороны, оно приводит к восстановлению электропроводности [3, 4, 6–9].
Достижение уникального сочетания технологических и эксплуатационных свойств в сплавах возможно за счет формирования в них ультрамелкозернистой или нанокристаллической (НК) структуры. Эффективным для получения ультрамелкозернистой (УМЗ) структуры является метод интенсивной пластической деформации (ИПД) [5–12], в частности, равноканальное угловое прессование (РКУП). Например, в работах [11, 12] показано, что в сплавах Cu–0.5(вес. %)Cr и Cu–0.69(вес. %)Cr подвергнутых 4 проходам РКУП удалось увеличить предел прочности до 570 и 530 МПа, за счет уменьшения размера структурных составляющих до 510 и 540 нм и выделения дисперсных частиц Cr. Применение РКУП позволяет получать массивные заготовки в виде прутков, однако промышленное производство требует дальнейшего передела прутков в ленты, листы, пластины и др. Таким образом, актуальным является вопрос исследования влияния прокатки на микроструктуру УМЗ медных сплавов.
Целью данной работы является экспериментальное исследование влияния холодной прокатки и последующего старения на микроструктуру и свойства дисперсионно-твердеющего сплава Cu–0.5(вес. %)Cr (Cu–0.5)Cr с УМЗ структурой, полученной методом РКУП.
МЕТОДИКА ЭКСПЕРИМЕНТА
В качестве материала для исследований был выбран промышленный электротехнический сплав Cu–0.5Cr. Образцы в исходном состоянии имели размеры 10 × 10 × 60 мм и форму прямоугольных параллелепипедов. Для формирования пересыщенного твердого раствора образцы выдерживали в течение 0.5 ч при 1000°С и далее закаливали в 5%-ном растворе NaCl. Далее это состояние обозначено как “ИС” (Исходное состояние).
ИС характеризуется крупнозернистой микроструктурой со средним размером зерна 260 ± 11 мкм и большим количеством двойников отжига. В микроструктуре видны включения размером 4.3 ± ± 0.1 мкм на основе хрома [13].
Далее часть образцов в ИС была подвергнута холодной прокатке (ХП). Вторая часть образцов подвергалась РКУП.
ХП проводили при комнатной температуре со степенями обжатия 40, 60, 80 и 90%. За один проход при прокатке уменьшение толщины составило примерно 5%. Между проходами заготовки охлаждали на воздухе, чтобы минимизировать влияние деформационного нагрева на микроструктуру.
РКУП осуществляли в оснастке с внутренним углом пересечения каналов ψ = 90° по маршруту Bc (поворот заготовки на угол 90° по часовой стрелке вдоль продольной оси заготовки после каждого прохода) при комнатной температуре со скоростью 0.2 мм/с. Было сделано 4 прохода. После РКУП была проведена ХП при комнатной температуре со степенями обжатия 40, 60, 80 и 90%. Направление прокатки было параллельно направлению экструзии.
Старение проводили на воздухе в печи Nobertherm 45 при 425°С в течение 40 мин. Исследования микроструктуры и свойств проводили в плоскости прокатки. Для исследования микроструктуры использовали оптический микроскоп (ОМ) OLIMPUS GX51, растровый электронный микроскоп JEOL JSM-6490LV и просвечивающий электронный микроскоп (ПЭМ) JEOL 2100. Расчет размера зерен/субзерен в микроструктуре после деформации проводили по темнопольному изображению. Измерения проводили вдоль короткой оси, т.е. измеряли толщину зерен/субзерен.
Испытания на растяжение проводили при скорости деформации 10–3 с–1 на приборе Instron 8801 при комнатной температуре. Образцы вырезали из центральной части РКУП заготовок и листов после прокатки параллельно направлению деформации. Измерение электропроводности проводили методом вихревых токов в соответствии с ГОСТ 27333-87 на приборе ВЭ-27НЦ/4-5. Измерения проводили при комнатной температуре. Погрешность измерения составила ±2%.
ЭКСПЕРИМЕНТАЛЬНЫЕ РЕЗУЛЬТАТЫ И ИХ ОБСУЖДЕНИЕ
В ходе ХП со степенями обжатия от 40 до 90% микроструктура ИС вытягивается в направлении прокатки. При больших степенях деформации микроструктура становится ламелярной. Наблюдается значительное уменьшение расстояния между границами, измеренного в перпендикулярном направлении к плоскости прокатки, с 200 ± 10 до 350 ± 10 нм. На рис. 1а представлена типичная микроструктура после прокатки со степенью обжатия 90% (состояние 90ХП). Видно, что границы уширены и изогнуты [14].
Последующее старение прокатанного ИС (состояние 90ХП + ТО) приводит к распаду пересыщенного твердого раствора и выделению дисперсных частиц со средним размером 13 ± 1 нм (рис. 1б). При этом среднее расстояние между границами практически не меняется и составляет 360 ± 15 нм.
РКУП (рис. 2а) приводит к значительному измельчению структурных элементов и преобразованию микроструктуры ИС в УМЗ структуру за счет перестройки дислокаций. В ходе РКУП дислокации непрерывно генерируются и за счет постепенной объеденения в клубки/ячейки и границы субзерен, в итоге формируют новые границы зерен [15]. В результате 4 проходов РКУП (состояние РКУП4) формируется вытянутая микроструктура со средним размером зерен/субзерен 255 ± 20 нм. Анализ фотографий микроструктуры после РКУП выявил наличие частиц вторичных фаз. Таким образом, во время ИПД активизировались процессы диффузии, приводящие к разложению перенасыщенного твердого раствора и образованию частиц размером около 6 нм.
Микроструктура состояний РПКУП4 + 40ХП и РПКУП4 + 90ХП, полученных в результате холодной прокатки состояния РКУП4 со степенями обжатия 40 и 90% соответственно, представлена на рис. 2.
В результате холодной прокатки со степенью обжатия 40% состояния РКУП4 микроструктура вытягивается в направлении прокатки. Средний размер зерен/субзерен достигает 406 ± 16 нм (рис. 3). Выявленные изменения в микроструктуре являются следствием использованной схемы деформации. Ранее вытянутые в направление деформации зерна/субзерна, характерные для состояния РКУП4, становятся уплощёнными за счет уменьшения их толщины [16]. Последующее увеличение степени обжатия до 90% приводит к постепенному уменьшению среднего поперечного размера зерен/субзерен до 229 ± 15 нм. При больших степенях обжатия, наряду с вытянутыми сильнодеформированными зернами, наблюдаются мелкие равноосные зерна, свободные от дислокаций, с ровными тонкими границами (рис. 2г). Подобные зерна наблюдали в работе [16] после прокатки образцов чистой меди, подвергнутых 4, а особенно 10 проходам РКУП. В микроструктуре также наблюдаются частицы вторичных фаз диаметром в диапазоне 3–6 нм.
Таким образом, в результате холодной прокатки УМЗ состояния удалось сформировать микроструктуру с меньшим размером зерен/субзерен по сравнению прокатанным исходным состоянием. Границы зерен/субзерен становятся более тонкими и резкими, что связано с увеличением их разориентировки.
В результате старения не происходит существенного изменения размера зерен/субзерен (рис. 3) в микроструктуре состояний РКУП4, РКУП4 + ХП со степенью обжатия 40, 60 и 80%. После прокатки со степенью обжатия 90% размер зерна/субзерна увеличивается с 229 ± 15 до 305 ± ± 20 нм.
Старение не приводит к видимому изменению в расположении и плотности дислокаций как в РКУП4 + ТО, так и в РКУП4 + 90ХП + ТО состояниях (рис. 4а и 4б). Сохраняются зерна/субзерна с размытыми и неровными границами. Неоднородность в распределении дислокаций внутри некоторых из них свидетельствует о сохранении напряженного состояния. Старение сопровождается формированием частиц сферической и эллипсоидальной форм (рис. 4в). Частицы расположены неравномерно как по объему, так и по границам зерен. Размер частиц увеличивается и составляет около 10 ± 1 нм. Таким образом, при старении предварительная деформационная обработка (РКУП + ХП) приводит к выделению частиц с меньшим размером, чем после старения ИС + ХП состояния (13 ± 1 нм).
Пластическая деформация способствует изменению механических характеристик сплава. ИС + ХП приводит к увеличению предела прочности с 160 МПа до 440 МПа (табл. 1, рис. 5а), относительное удлинение уменьшается с 42 до 16% (табл. 1, рис. 5б). РКУП приводит к росту предела прочности σв с 160 ± 10 до 425 ± 10 МПа, что связано с дислокационным и зернограничным упрочнениями. При этом относительное удлинение уменьшается с 42 ± 2 до 17 ± 2%. Последующая ХП со степенью обжатия 40% способствует разупрочнению, что связано с увеличением среднего размер зерен/субзерен (рис. 3) в соответствии с соотношением Холла-Петча [17, 18]. При дальнейшем увеличении степени обжатия до 90% предел прочности возрастает до 510 ± 18 МПа. Смена схемы деформации с РКУП на ХП приводит к снижению относительного удлинения с 17 ± 2 до 12 ± 1%. Дальнейшее увеличение степени деформации приводит к ее восстановлению до 17 ± 1%.
Таблица 1.
Механические и электрические свойства
Состояние | σв, МПа | ε, % | IACS, % |
---|---|---|---|
ИС | 160 ± 10 | 42 ± 2 | 37 |
ИС + 90ХП | 440 ± 10 | 16 ± 1 | 35 |
ИС + 90ХП + ТО | 465 ± 10 | 18 ± 2 | 67 |
РКУП4 | 425 ± 7 | 17 ± 2 | 39 |
РКУП4 + 90ХП | 510 ± 18 | 17 ± 1 | 35 |
РКУП4 + 90ХП + ТО | 460 ± 10 | 25 ± 1 | 70 |
Рис. 5.
Свойства сплава: зависимость предела прочности от степени деформации (а), зависимость относительного удлинения от степени деформации (б), зависимость электропроводности сплава от степени деформации (в, г).
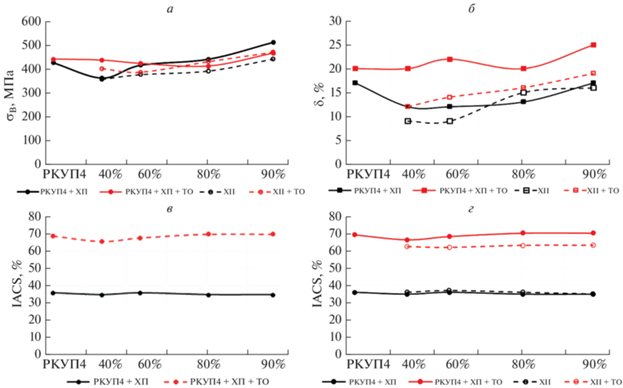
Низколегированный сплав Cu–0.5(Cr относится к классу дисперсионно–упрочняемых сплавов, для которых старение является важнейшим этапом достижения оптимального комплекса прочности и электропроводности. В дополнение к дислокационному и зернограничному упрочнениям происходит упрочнение дисперсными частицами вторичных фаз, которые выделяются при распаде твердого раствора. Частицы, выделяясь в местах скопления дислокаций, границах зерен и субзерен препятствуют движению дислокаций, миграции границ зерен/субзерен. Однако, если частицы укрупняются, вклад дисперсионного упрочнения ослабляется, что наблюдается после старения состояния РКУП4 + ХП. При этом происходит некоторый возврат микроструктуры, что обеспечивает уменьшение предела прочности до 460 ± 10 МПа и улучшение пластичности до 25 ± 1%, что на 8% выше, чем в случае прокатанного крупнозернистого ИС.
В ИС электропроводность составила 37% IACS. Величина электропроводности существенно зависит от уровня дефектности микроструктуры. ИПД и последующая ХП сопровождаются увеличением плотности дислокаций и протяженности границ зерен, на которых происходит рассеяние электронов проводимости. Однако, как видно из рис. 5в, величина электропроводности не сильно зависит от степени деформации. Следовательно, основной вклад в электропроводность вносят атомы легирующего элемента, находящиеся в твердом растворе, что согласуется с результатами, полученными в [19, 20]. В процессе старения происходит распад твердого раствора, в результате которого происходит выделение частиц вторичных фаз и их укрупнение (рис. 4г, табл. 1), а также процессы, приводящие к восстановлению микроструктуры, в результате чего электропроводность всех деформированных состояний восстанавливается до 68–70% IACS. При этом электропроводность прокатанного УМЗ состояния, равная 70% IACS, несколько выше, чем у прокатанного исходного крупнозернистого состояния, равная 67% IACS. Следовательно, предварительная ИПД способствует более полному распаду пересыщенного твердого раствора.
ЗАКЛЮЧЕНИЕ
Холодная прокатка УМЗ состояния приводит к формированию вытянутой сильнодеформированной микроструктуры. При этом увеличение степени обжатия приводит к увеличению размера структурных составляющих при 40% обжатии. При больших степенях обжатия размер размера зерен/cубзерен монотонно уменьшается. Немонотонный характер изменения размера структурных составляющих связан со сменой схемы деформации. Последующее старение приводит к аналогичным изменениям в характер микроструктуры. При этом размер структурных составляющих меняется незначительно. Обнаруженные тенденции слабо отличаются от тенденций, характерных для прокатки и старения ИС.
Прочность УМЗ состояния после прокатки и старения слабо отличается от прочности соответствующих состояний, полученных прокаткой и старением ИС. В то же время, пластичность УМЗ состояния, подвергнутого плоской прокатке и старению, выше.
Старение приводит к более высокой электропроводности прокатанного УМЗ состояния, чем у прокатанного ИС крупнозернистого состояния, что связано с более полным распадом пересыщенного твердого раствора.
Обнаруженные закономерности говорят о положительном влиянии предварительного измельчения микроструктуры на уровни пластичности и электропроводности сплава Cu–0.5Cr при прокатке и старении.
Исследование выполнено при финансовой поддержке Министерства науки и высшего образования РФ (проект № 0838-2020-0006 “Фундаментальные исследование новых принципов создания перспективных электромеханических преобразователей энергии с характеристиками выше мирового уровня, с повышенной эффективностью и минимальными удельными показателями, с использованием новых высокоэффективных электротехнических материалов”).
Список литературы
Осинцев О.Е., Федоров В.Н. Медь и медные сплавы, отечественные и зарубежные марки. М.: Машиностроение, 2004. 215 с.
Vinogradov A., Ishida N., Kitagawa K., Kopylov V. // Acta Mater. 2005. V. 53. P. 2181.
Purcek G., Yanar H., Saray O. et al. // Wear. 2014. V. 311. P. 149.
Sarkeeva E.A., Alexandrov I.V. // IOP Conf. Ser. Mater. Sci. Engin. 2020. V. 1008. Art. No. 012057.
Валиев Р.З., Александров И.В. Объемные наноструктурные металлические материалы, Получение, структура и свойства. М.: Академкнига, 2007. 271 с.
Islamgaliev R.K, Nesterov K.M., Bourgon J. et al. // J. Appl. Phys. 2014. V. 115. Art. No. 194301.
Vinogradov A., Suzuki Y., Ishida T. et al. // Mater. Trans. 2004. V. 45. No. 7. P. 2187.
Vinogradov A., Patlan V., Suzuki Y.et al. // Acta Mater. 2002. V. 50. No. 7. P. 1639.
Kun Xia Wei, Wei Wei, Fei Wang et al. // Mater. Sci. Engin. A. 2011. V. 528. No. 3. P. 1478.
Vinogradov A., Ishida T., Kitagawa K., Kopylov V.I. // Acta Mater. 2005. V. 53. No. 8. P. 2181.
Xu C.Z., Wang Q.J., Zheng M.S. et al. // Mater. Sci. Engin. A. 2007. V. 59. P. 303.
Wang Q.J., Xu C.Z., Zheng M.S. et al. // Mater. Sci. Engin. A. 2008. V. 496. P. 434.
Sarkeeva E.A., Alexandrov I.V. // IOP Conf. Ser. Mater. Sci. Engin. 2020. V. 672. Art. No. 012056.
Liua Q., Huang X., Lloyd D.J., Hansen N. // Acta Mater. 2019. V. 50(15). P. 3789.
Hughes D.A., Hansen N. // Acta Mater. 1997. V. 45. P. 3871.
Guowei Wang, Dan Song, Zhikai Zhou et al. // J. Mater. Res. Tech. 2021. V. 15. P. 2419.
Stepanov N.D., Kuznetsov A.V., Salishchev G.A. et al. // Mater. Sci. Engin. A. 2012. V. 554. P. 105.
Petch N.J. // J. Iron. Steel. Inst. 1953. V. 174. P. 25.
Козлов Э.В., Конева Н.А., Попова Н.А. // Изв. РАН. Сер. физ. 2009. Т. 73. № 9. С. 1295; Kozlov E.V., Ko-neva N.A., Popova N.A. // Bull. Russ. Acad. Sci. Phys. 2009. V. 73. No. 9. P. 1227.
Chembarisova R.G. // Tech. Phys. 2020. V. 65. P. 593.
Дополнительные материалы отсутствуют.
Инструменты
Известия РАН. Серия физическая