Химическая физика, 2019, T. 38, № 3, стр. 74-79
Влияние физических факторов при подготовке реакционной смеси в турбулентных потоках на скорость полимеризации бутадиена в присутствии TiCl4–Al(i-C4H9)3 и молекулярно-массовые характеристики бутадиенового каучука
Н. В. Улитин 1, *, К. А. Терещенко 1, Д. А. Шиян 1, А. С. Зиганшина 1, Г. М. Ганиев 1, В. П. Захаров 2
1 Казанский национальный исследовательский технологический университет
Казань, Россия
2 Башкирский государственный университет
Уфа, Россия
* E-mail: n.v.ulitin@mail.ru
Поступила в редакцию 05.03.2018
После доработки 13.07.2018
Принята к публикации 20.08.2018
Аннотация
На примере полимеризации бутадиена (каталитическая система – TiCl4–Al(i-C4H9)3, растворитель – толуол, температура – 298 K) как модельного объекта процессов полимеризации диенов в присутствии микрогетерогенных полицентровых каталитических систем Циглера–Натта по итогам моделирования установлено, что: 1) увеличение скорости подачи реакционной смеси в трубчатый турбулентный аппарат диффузор-конфузорной конструкции, отношения диаметра диффузора к диаметру конфузора и угла раскрытия диффузора приводит к локальному росту кинетической энергии турбулентности и скорости ее диссипации и, как следствие, к уменьшению наиболее вероятного эквивалентного радиуса частиц каталитической системы, увеличению скорости полимеризации и уменьшению средних молекулярных масс полимера; 2) изменение отношения длины секции к диаметру диффузора при постоянном диаметре диффузора или при постоянной длине секции и изменение количества секций трубчатого турбулентного аппарата от 4 до 8 практически не отражается на скорости полимеризации и молекулярно-массовых характеристиках полимера.
ВВЕДЕНИЕ
Эффективным методом увеличения активности микрогетерогенных каталитических систем Циглера–Натта и, как следствие, скорости полимеризации диенов в присутствии этих каталитических систем является увеличение концентрации центров роста цепей за счет диспергирования частиц каталитической системы в турбулентных потоках при кратковременном (порядка 1 с) пропускании реакционной смеси через трубчатый турбулентный аппарат диффузор-конфузорной конструкции [1]. Так, в работах [2, 3] это было показано на примере полимеризации бутадиена в присутствии каталитической системы TiCl4–Al(i-C4H9)3 (растворитель – толуол). В работе [4] с помощью фундаментальной модели теоретически на количественном уровне формализовали полученные в работах [2, 3] экспериментальные данные по кинетике этого процесса и молекулярно-массовым характеристикам образующегося в нем бутадиенового каучука. Цель настоящей работы – выявить с помощью представленной в работе [4] модели полимеризации бутадиена в присутствии каталитической системы TiCl4–Al(i-C4H9)3 принципы регулирования скорости полимеризации диенов в присутствии микрогетерогенных каталитических систем Циглера–Натта и молекулярно-массовых характеристик образующихся диеновых каучуков при пропускании реакционной смеси через трубчатый турбулентный аппарат диффузор-конфузорной конструкции.
МЕТОДИКА КОМПЬЮТЕРНОГО МОДЕЛИРОВАНИЯ
Течение реакционной смеси в трубчатом турбулентном аппарате диффузор-конфузорной конструкции описывается системой уравнений, включающей в себя следующие уравнения (в данном случае реакционная смесь моделируется как двухфазная несжимаемая жидкость, в которой дисперсной фазой являются частицы каталитической системы, а дисперсионной средой – смесь толуола и бутадиена) [4]: 1) уравнение неразрывности для реакционной смеси; 2) уравнение сохранения импульса для реакционной смеси; 3) уравнение сохранения энергии для реакционной смеси; 4) уравнение для расчета относительной скорости фаз; 5) уравнение для расчета изменения объемной доли частиц каталитической системы TiCl4–Al(i-C4H9)3; 6) уравнения k–ε-модели турбулентности (k и ε – кинетическая энергия турбулентности и скорость ее диссипации); 7) уравнение популяционного баланса, описывающее диспергирование частиц каталитической системы TiCl4–Al(i-C4H9)3 в турбулентных потоках. Система, состоящая из этих уравнений, позволяет рассчитать распределение частиц каталитической системы по эквивалентным радиусам на выходе из трубчатого турбулентного аппарата при заданных на входе в аппарат распределении частиц каталитической системы по эквивалентным радиусам и скорости подачи реакционной смеси [4]. Эту систему уравнений в работе [4] верифицировали за счет совпадения теоретически рассчитанного распределения частиц каталитической системы TiCl4–Al(i-C4H9)3 по эквивалентным радиусам ([TiCl4]0 = 5 ммоль/л, [Al(i-C4H9)3]0 = = 7 ммоль/л – начальные концентрации компонентов каталитической системы) на выходе из шестисекционного трубчатого турбулентного аппарата (диаметр диффузора D = 0.024 м, диаметр конфузора d = 0.015 м, длина диффузор-конфузорной секции L = 0.048 м, угол раскрытия диффузора α = 45°, L/D = 2, D/d = 8/5; см. рис. 1а), через который со скоростью v = 0.9 м/с пропускали толуольные растворы каталитической системы и бутадиена, с соответствующим экспериментальным распределением из работы [5].
Рис. 1.
Эскиз трубчатого турбулентного аппарата диффузор-конфузорной конструкции (а) и схема экспериментальной установки для проведения полимеризации бутадиена (б): D – диаметр диффузора, d – диаметр конфузора, L – длина диффузор-конфузорной секции, α – угол раскрытия диффузора; 1 и 2 – емкости для реагентов, 3 – трубчатый турбулентный аппарат диффузор-конфузорной конструкции, 4 – лабораторный реактор-полимеризатор смешения (колба объемом 500 см3), 5 – трехходовой кран, 6 – мешалка.
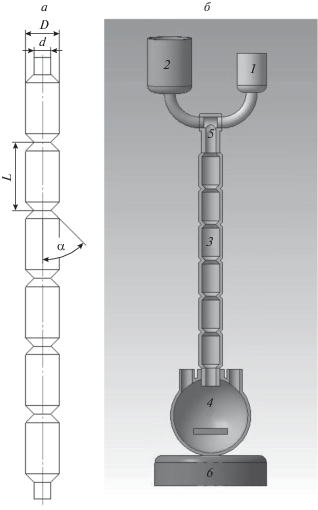
Зная эквивалентные радиусы частиц каталитической системы на выходе из трубчатого турбулентного аппарата, можно перейти к кинетическим активностям центров роста цепей j-го типа, расположенных на поверхности частиц каталитической системы монодисперсного состава:
(1)
$\begin{gathered} {{s}_{1}} = a{{\left[ {{{{({r \mathord{\left/ {\vphantom {r {3.39}}} \right. \kern-0em} {3.39}})}}^{{ - 7.42}}} + {{{(0.0785 - 0.00181r)}}^{{ - 1}}}} \right]}^{{ - 1}}}, \\ {{s}_{2}} = a(0.595 - 0.00886r) - {{s}_{1}}, \\ {{s}_{3}} = a(0.375 + 0.00448r), \\ {{s}_{4}} = a(0.03 + 0.00438r), \\ \end{gathered} $Коэффициенты из выражений (1) определили в результате решения обратной кинетической задачи, исходя из двух условий. С одной стороны, зависимости (1) должны описывать экспериментальные относительные кинетические активности центров роста цепей различных типов из работы [7] (см. рис. 2). С другой стороны, коэффициенты зависимостей (1) должны быть подобраны так, чтобы вычисленные по формуле (2) активности Sj позволили адекватно описать экспериментальные кинетические кривые полимеризации (зависимости конверсии бутадиена от времени полимеризации) и молекулярно-массовые характеристики бутадиенового каучука [2, 3].
Рис. 2.
Зависимость относительных кинетических активностей центров роста цепей различных типов от эквивалентного радиуса частиц каталитической системы TiCl4–Al(i-C4H9)3 монодисперсного состава; линии – расчет по формулам (1), номера линий соответствуют номерам типов центров роста цепей; точки – эксперимент: ◼ – 1-й тип, ⚫ – 2-й тип, ▲ – 3-й тип, ▼ – 4-й тип центров роста цепей [7].
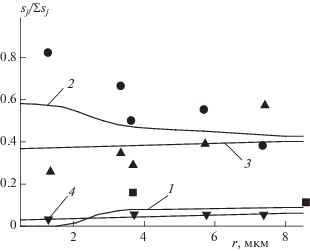
После трубчатого турбулентного аппарата реакционная смесь попадает в реактор-полимеризатор смешения (см. рис. 1б). Макрокинетику полимеризации бутадиена в реакторе-полимеризаторе смешения описывает система, состоящая из следующих уравнений (в данном случае реакционная смесь моделируется как однофазная несжимаемая жидкость, поскольку возникает необходимость рассмотрения реакций между компонентами реакционной массы) [4]: 1) уравнение неразрывности для реакционной смеси; 2) уравнения неразрывности по компонентам реакционной смеси; 3) уравнение сохранения импульса для реакционной смеси; 4) уравнение сохранения энергии для реакционной смеси; 5) уравнения k–ε-модели турбулентности. При этом скорость изменения массовой доли компонентов реакционной смеси задается, исходя из модели кинетики рассматриваемого процесса [4]. Компонентами реакционной смеси считали бутадиен, Al(i-C4H9)3, активные полимерные цепи (цепи, содержащие на концах центры роста цепей различных типов), неактивные полимерные цепи, толуол как растворитель. Модель макрокинетики полимеризации бутадиена в работе [4] верифицировали за счет совпадения теоретически рассчитанных кинетических кривых полимеризации и среднечисленной (Mn) и среднемассовой (Mw) молекулярных масс бутадиенового каучука с соответствующими экспериментальными данными, полученными в работах [2, 3] в результате проведения полимеризации бутадиена (начальная концентрация бутадиена [M]0 = 1.5 моль/л) при 298 K в лабораторном реакторе-полимеризаторе смешения – круглодонной колбе объемом 500 см3 с двухлопастной мешалкой. При этом в расчете не учитывали турбулентно-вихревое течение, возникающее при попадании реакционной смеси в реактор-полимеризатор смешения, поскольку время ввода реакционной смеси в реактор-полимеризатор (2–3 с) значительно меньше времени полимеризации (1.5–2 ч).
В настоящей работе методика компьютерного моделирования заключалась в следующем. В качестве программно-вычислительного средства использовали модульную платформу ANSYS Workbench 17.1 [8]. Сначала в модуле Geometry этой платформы строили заданную расчетную область – осевое сечение трубчатого турбулентного аппарата диффузор-конфузорной конструкции, т.е. моделирование осуществляли в двумерной осесимметричной постановке задачи. После чего в модуле Mesh разбивали построенную расчетную область на ячейки, формируя расчетную сетку. Расчет диспергирования частиц каталитической системы TiCl4–Al(i-C4H9)3 проводили в модуле Fluent с использованием системы уравнений, описывающих течение реакционной смеси через трубчатый турбулентный аппарат, которую Fluent решал в каждой ячейке расчетной сетки с использованием встроенных алгоритмов. При этом варьировали: 1) скорость подачи реакционной смеси в трубчатый турбулентный аппарат, v – от 0.3 до 1.5 м/с; 2) отношение диаметра диффузора к диаметру конфузора, D/d – от 8/7 до 8/3; 3) угол раскрытия диффузора α – от 15° до 90°; 4) отношение длины секции к диаметру диффузора трубчатого турбулентного аппарата, L/D – от 4/3 до 8/3 при постоянном диаметре диффузора D = = 0.024 м и от 12/8 до 12/4 при постоянной длине секции L = 0.048 м; 5) число секций n – от 4 до 8. При варьировании каждого параметра все остальные геометрические характеристики аппарата и скорость течения реакционной смеси не меняли и закладывали в соответствии параметрами, используемыми в работах [2, 3] для получения экспериментальных данных (диаметр диффузора D = = 0.024 м, диаметр конфузора d = 0.015 м, длина диффузор-конфузорной секции L = 0.048 м, угол раскрытия диффузора α = 45°, L/D = 2, D/d = 8/5, скорость течения реакционной смеси v = 0.9 м/с).
В качестве выходных данных расчета получали распределения частиц каталитической системы по эквивалентному радиусу. Затем по формулам (1) и (2) пересчитывали эти распределения в кинетические активности центров роста цепей различных типов. Зная последние, пересчитывали их в начальные концентрации центров роста цепей ${{\left. {{{\mu }_{{j0}}}} \right|}_{{t = 0}}}$ по формуле ${{\left. {{{\mu }_{{j0}}}} \right|}_{{t = 0}}} = {{{{S}_{j}}} \mathord{\left/ {\vphantom {{{{S}_{j}}} {{{k}_{{pj}}}}}} \right. \kern-0em} {{{k}_{{pj}}}}},$ где ${{k}_{{pj}}}$ – константы скоростей реакций роста цепей на центрах роста j-го типа. Эти данные далее использовали в качестве начальных условий при моделировании макрокинетики полимеризации бутадиена в реакторе-полимеризаторе смешения. Рассматривали полимеризацию бутадиена, протекающую в лабораторном реакторе-полимеризаторе смешения объемом 500 см3, который в работах [2, 3] являлся частью лабораторной установки. При моделировании макрокинетики полимеризации в модуле Geometry платформы ANSYS Workbench 17.1 строили расчетную область реактора-полимеризатора – его горизонтальное сечение на уровне перемешивающего устройства (поскольку в этом сечении векторы скорости течения реакционной массы расположены в горизонтальной плоскости [9]). После чего в модуле Mesh расчетную область реактора-полимеризатора разбили на ячейки, сформировав расчетную сетку и задав скорость ее вращения в 400 об./мин (скорость вращения мешалки). В качестве выходных данных расчета по модели макрокинетики полимеризации получали конверсию бутадиена, среднечисленную и среднемассовую молекулярные массы бутадиенового каучука, усредненные по всем ячейкам расчетной сетки.
РЕЗУЛЬТАТЫ И ИХ ОБСУЖДЕНИЕ
На основе результатов вычислительных экспериментов установлено, что наибольшее влияние на кинетику процессов получения бутадиенового каучука в присутствии каталитической системы TiCl4–Al(i-C4H9)3 при пропускании реакционной смеси через трубчатый турбулентный аппарат диффузор-конфузорной конструкции оказывает скорость подачи в него реакционной смеси. Увеличение скорости подачи реакционной смеси в трубчатый турбулентный аппарат при прочих равных условиях приводит к существенному росту значений кинетической энергии турбулентности k от 0.02 до 0.3 Дж/кг и скорости ее диссипации ε от 0 до 30 м2/c3 (k в связи с вязким трением преобразуется в тепловую энергию и тратится на диспергирование частиц каталитической системы; значение ε в числовом выражении характеризует скорость расхода кинетической энергии k на преодоление сил вязкого трения, препятствующих движению турбулентных вихрей; при увеличении k скорость турбулентных пульсаций и напряжения, возникающие в связи с вязким трением, будут увеличиваться – это обеспечивает уменьшение размеров частиц каталитической системы), уменьшению наиболее вероятного эквивалентного радиуса частиц каталитической системы TiCl4–Al(i-C4H9)3 от 3.5 до 0.7 мкм (рис. 3), а значит, к увеличению ее удельной поверхности (от 0.3 до 1.3 м2/г) и активности (от 0.02 до 0.08 мин–1) (рис. 4) и, как следствие, к увеличению скорости полимеризации бутадиена от 0.03 до 0.12 моль/л · мин (рис. 5) и уменьшению среднемассовой (от 6.5 · 105 до 3 · 105, рис. 6) и среднечисленной (от 6.5 · 104 до 4 · 104) молекулярных масс бутадиенового каучука. Также заметно (но уже в меньшей мере) аналогичную тенденцию наблюдали при увеличении отношения диаметра диффузора к диаметру конфузора и увеличении угла раскрытия диффузора. Изменение отношения длины секции к диаметру диффузора трубчатого турбулентного аппарата при постоянном диаметре диффузора или при постоянной длине секции и изменение количества секций практически не сказываются на дисперсном составе каталитической системы (наиболее вероятный эквивалентный радиус частиц каталитической системы TiCl4–Al(i-C4H9)3 составляет в среднем 1.5 мкм), скорости полимеризации бутадиена (в среднем 0.06 моль/л · мин) и молекулярно-массовых характеристиках бутадиенового каучука (среднечисленная молекулярная масса – в среднем 5 · 104, среднемассовая молекулярная масса – в среднем 4.25 · 105).
Рис. 3.
Распределения частиц каталитической системы TiCl4–Al(i-C4H9)3 по эквивалентному радиусу на выходе из трубчатого турбулентного аппарата диффузор-конфузорной конструкции, dqr/dr (диаметр диффузора D = 0.024 м, диаметр конфузора d = 0.015 м, длина секции L = 0.048 м, угол раскрытия диффузора α = 45°, L/D = 2, D/d = 8/5, число секций n = 6, скорость подачи реакционной смеси v = 0.3 (1), 0.6 (2), 0.9 (3), 1.2 (4), 1.5 (5) м/с); 0 – процесс без турбулизации.
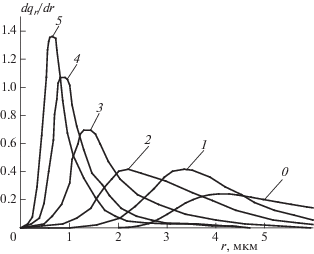
Рис. 4.
Зависимость активности каталитической системы TiCl4–Al(i-C4H9)3 от ее удельной поверхности Sуд при пропускании реакционной смеси через трубчатый турбулентный аппарат диффузор-конфузорной конструкции. Характеристики аппарата и обозначения см. в подписи к рис. 3.
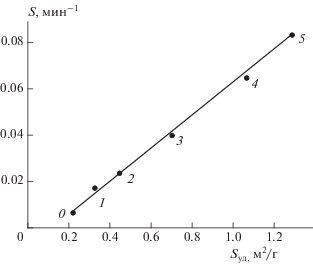
Рис. 5.
Зависимости конверсии бутадиена U от времени полимеризации на каталитической системе TiCl4–Al(i-C4H9)3 при пропускании реакционной смеси через трубчатый турбулентный аппарат диффузор-конфузорной конструкции. Характеристики аппарата и обозначения см. в подписи к рис. 3.
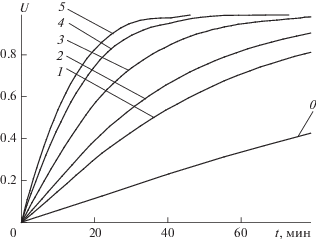
Рис. 6.
Зависимости среднемассовой молекулярной массы бутадиенового каучука Mw от времени полимеризации на каталитической системе TiCl4–Al(i-C4H9)3 при пропускании реакционной смеси через трубчатый турбулентный аппарат диффузор-конфузорной конструкции. Характеристики аппарата и обозначения см. в подписи к рис. 3.
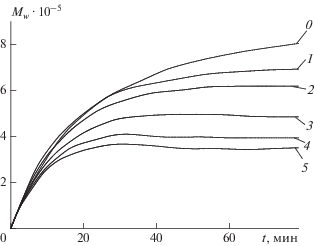
ЗАКЛЮЧЕНИЕ
Таким образом, увеличение скорости подачи реакционной смеси в трубчатый турбулентный аппарат, отношения диаметра диффузора к диаметру конфузора, угла раскрытия диффузора, т.е. параметров, влияющих в первую очередь на увеличение кинетической энергии турбулентности и скорости ее диссипации, в большей степени способствует диспергированию частиц микрогетерогенной полицентровой каталитической системы Циглера–Натта, увеличению скорости полимеризации и уменьшению средних молекулярных масс полидиена, чем увеличение параметров, влияющих в первую очередь на время пребывания частиц в трубчатом турбулентном аппарате (это отношение длины секции к диаметру диффузора при постоянном диаметре диффузора или при постоянной длине секции, количество секций). Поскольку при проведении вычислительных экспериментов варьировали не габариты трубчатого турбулентного аппарата, а соотношение его размеров, все полученные закономерности могут быть применены при конструировании таких аппаратов для промышленной реализации полимеризации, стадия подготовки реакционной смеси которой проводится в турбулентных потоках.
Работа выполнена в рамках государственного задания на 2017–2019 гг. (инициативный научный проект № 10.5548.2017/8.9).
Список литературы
Deberdeev R.Ya., Berlin Al.Al., Dyakonov G.S., Zakharov V.P., Monakov Yu.B. Fast chemical reactions in turbulent flows: theory and practice. Shawbury, Shrewsbury, Shropshire, SY4 4NR, UK: Smithers Rapra Technology Ltd., 2013.
Мингалеев В.З., Захаров В.П., Ионова И.А. и др. // Высокомолекуляр. соединения. А. 2008. Т. 50. № 12. С. 2174.
Мингалеев В.З., Захаров В.П., Монаков Ю.Б. // ЖПХ. 2007. Т. 80. № 7. С. 1160.
Терещенко К.А., Зиганшина А.С., Захаров В.П., Улитин Н.В. // Хим. физика. 2017. Т. 36. № 5. С. 87.
Мингалеев В.З., Захаров В.П., Монаков Ю.Б. // Изв. вузов. Химия и хим. технология. 2008. Т. 51. № 9. С. 63.
Мингалеев В.З. // Кинетика и катализ. 2016. Т. 57. № 1. С. 54.
Мингалеев В.З., Захаров В.П., Тимофеев П.В. и др. // Вестн. Башк. ун-та. 2009. Т. 14. № 3. С. 743.
ANSYS Fluent Theory Guide. Southpointe: ANSYS, Inc., 2011.
Klinov A.V., Mukhametzyanova A.G., Minibaeva L.R. // Chem. and Petroleum Engin. 2012. V. 47. № 11–12. P. 815.
Дополнительные материалы отсутствуют.
Инструменты
Химическая физика