Химическая физика, 2020, T. 39, № 9, стр. 94-99
Синтез литых композиционных материалов на основе карбидов вольфрама с никелевой связкой методом СВС-металлургии
С. Л. Силяков 1, *, В. И. Юхвид 1, Н. Ю. Хоменко 1, Т. И. Игнатьева 1, Н. В. Сачкова 1
1 Институт структурной макрокинетики и проблем материаловедения им. А.Г. Мержанова
Российской академии наук
Черноголовка, Россия
* E-mail: ssl@ism.ac.ru
Поступила в редакцию 05.06.2019
После доработки 05.06.2019
Принята к публикации 20.06.2019
Аннотация
Экспериментально показана возможность синтеза литых композиционных материалов W–C–Ni методами СВС-металлургии из высокоэкзотермических смесей на основе оксидов WO3 и NiO и комплексного восстановителя, состоящего из Al, Ca и графита, при повышенном давлении газа (азота). Показано, что при вариации соотношения WO3 и NiO, содержаний углерода, алюминия и кальция в широких интервалах их значений исходные смеси сохраняют способность к горению, а температура горения превышает температуру плавления композиционного и шлакового (оксидного) продуктов горения. Под действием гравитации происходит сепарация расплавов композиционного материала и шлака, а при последующем охлаждении – формирование их структуры. В работе изучены закономерности горения смесей, гравитационной сепарации продуктов горения, формирования их состава и структуры.
ВВЕДЕНИЕ
Композиционные материалы (КМ) на основе карбидов вольфрама используют для получения покрытий, наносимых на детали машин и механизмов, с целью их защиты их от интенсивного износа. Наиболее часто применяется релит в сочетании с кобальтовой связкой [1–4]. Высокая стоимость кобальта вынуждает заменять его близкими по свойствам металлами, в частности никелем. Сравнительные испытания двух сплавов, WC–Co и WC–Ni, показывают преимущество первого из них по прочности, твердости и износостойкости по сравнению со сплавом с никелевой связкой [5, 6]. Однако в ряде случаев при изготовлении деталей механизмов или нанесении покрытий при помощи пламенного или высокоскоростного газоплазменного напыления сплавы на основе WC–Ni не имеют конкуренции. В этом случае детали механизмов способны противостоять воздействию коррозии в условиях интенсивного износа [7–12].
Основным методом получения карбида вольфрама (WC), релита (WC–W2C) и их сплавов с никелем является порошковая металлургия [5]. Перспективу промышленного освоения имеют и другие методы [12–15]. В настоящей статье приведены результаты исследований по синтезу литых КМ (WC–Ni) методами СВС-металлургии.
МЕТОДИКА ЭКСПЕРИМЕНТА
В качестве компонентов исходных высокоэкзотермических смесей термитного типа использовали порошки оксидов вольфрама(VI) и никеля(II) марки “Ч”, порошок алюминия марки АСД-1, кальций гранулированный марки CAS 7440-70-2 (активность – 99.1%) и графит марки ГМЗ с размером зерна 90/63 мкм. Перед смешением компоненты исходной смеси высушивали. Синтез осуществляли в бомбе постоянного давления. Во всех экспериментах сжигание экзотермической смеси осуществляли в графитовых стаканах внутренним диаметром 20 мм и высотой 60 мм. Порошки экзотермических смесей весом 30 г засыпали в стаканы при плотности засыпки 1.98–2.00 г/см3. Воспламенение осуществлялось вольфрамовой электроспиралью. Горение смесей осуществляли в атмосфере технического азота при начальном давлении газа 5.0 МПа. После горения и охлаждения продукт горения имел вид литого двухслойного слитка с верхним шлаковым слоем и нижним слоем из КМ на основе W–C.
В экспериментах проводили видеосъемку, определяли скорость (u) и пределы горения, относительную потерю массы (η1) и относительный выход композиционного материала в слиток (η2), которые рассчитывали по следующим формулам:
где Hi – высота слоя экзотермической смеси, ti – время горения слоя смеси, m1 – вес исходной смеси, m2 – вес продуктов горения, m3 – вес композиционного материала.
Продукты синтеза исследовали методами классического химического и рентгенофазового анализов. Микроструктура литых материалов исследовалась с использованием автоэмиссионного сканирующего электронного микроскопа сверхвысокого разрешения Zeiss Ultra plus (Германия). Расчет адиабатических температур горения выполнен с использованием программы Thermo [16].
ЭКСПЕРИМЕНТАЛЬНАЯ ЧАСТЬ
Исходный состав и оптимальные соотношения между компонентами экзотермической смеси термитного типа WO3 : Al : Ca : C в соотношении 0.705 : 0.090 : 0.164 : 0.041 были получены в ходе исследовательской работы [17]. В первой серии экспериментов в исходный состав WO3/Al/Ca/C вводили смесь NiO : Al состава 0.806 : 0.194, продукты сгорания которой являются источником никеля.
Термодинамический расчет исследуемого состава [(WO3/Al/Ca/C) + α(NiO/Al)] показал, что при всех значениях весовых соотношений α температуры горения составов превышают температуру плавления конечных продуктов синтеза (рис. 1). Согласно термодинамическому расчету продуктами горения являются два расплава: W–C–Ni с примесью Al и Al2O3–CaO.
Рис. 1.
Влияние соотношения весовых долей (α) на равновесную адиабатическую температуру горения (Тг), соотношение фаз (a), состав целевого (б) и шлакового (в) продуктов горения. Исходный состав WO3/Al/Ca/C + α(NiO/Al) при соотношениях реагентов в смесях WO3 : Al : Ca : C и NiO : Al, равных 0.705 : 0.090 : 0.164 : 0.041 и 0.806 : 0.194 соответственно; Р0 = 5 МПа; аg – суммарное количество газообразных продуктов реакции, акм – суммарное количество элементов КМ (W, Ni, C, Al), ашлак – суммарное количество оксидных продуктов реакции (Al2O3, CaO).
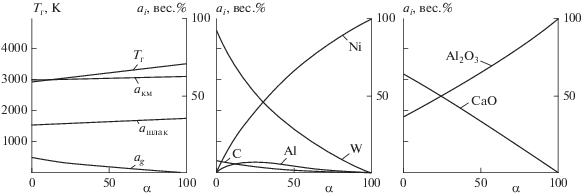
Экспериментальные исследования процесса горения экзотермической смеси [(WO3/Al/Ca/C) + + α(NiO/Al)] показали, что горение осуществляется при любом соотношении α, а продукты горения имеют литой вид. При увеличении доли NiO/Al в исходной смеси значения скорости горения u и относительный выход η2 КМ в слиток возрастают на начальном участке, а далее изменяются незначительно (рис. 2). При этом относительная потеря массы η1 при горении монотонно снижается.
Рис. 2.
Влияние соотношения весовых долей (α) на параметры u, η1 и η2. Исходная смесь, соотношения реагентов и начальное давление те же, что и для рис. 1.
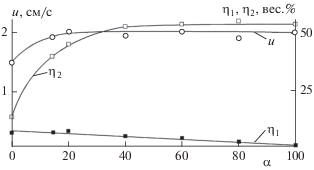
Исследование зависимости химического состава литых металлокерамических продуктов в диапазоне 5 ≤ α ≤ 25 вес.% от соотношения NiO/Al в смеси WO3/Al/Ca/NiO/C выявили линейное увеличение содержания никеля в синтезированном КМ с увеличением α (рис. 3). Увеличение доли NiO/Al приводит к росту содержания никеля в литом КМ от 5 до 24 вес.%. Вместе с тем в литом КМ отмечается линейное увеличение содержания примесного алюминия и уменьшение содержания углерода. Для второй серии экспериментов в качестве базовой выбрана смесь [85% (WO3/Al/Ca/C) + 15% (NiO/Al)]. Согласно химическому и рентгеновскому анализу литой КМ, полученный из этой смеси, содержит 2.2 вес.% углерода и включает в себя четыре основные фазы: W2C, W, Ni2W4C, Ni3W9C4 (рис. 4).
Рис. 3.
Влияние соотношения весовых долей (α) на химический состав литого КМ. Исходная смесь, соотношения реагентов и начальное давление те же, что и для рис. 1.
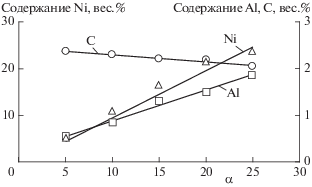
Для повышения содержания связанного углерода в КМ в базовую смесь вводили в избытке углерод (∆[С]). Введение ∆[С] в исходную смесь значительно повлияло на характеристики процесса (рис. 5). С увеличением ∆[С] в исходной смеси значения параметров u и η1 снижаются. При ∆[С] > 2.0 продукт горения имеет вид спеченного “кермета” При ∆[С] = 9.0 достигается концентрационный предел горения, и экзотермическая смесь воспламеняется, а затем затухает. Из рис. 6 следует, что с ростом ∆[С] повышается содержание углерода в литом КМ, и при ∆[С] = = 2.2 вес.% его значение достигает 4.2 вес.%. При этом содержание примесных алюминия и кальция в литом КМ также повысилось. Литой материал, полученный из этой смеси, сформирован из четырех фаз: WC, W2C, Ni3W10C3,4. и Ni3Al (рис. 7).
Рис. 5.
Влияние избыточного содержания углерода Δ[С] в исходной смеси на параметры u, η1 и η2. Исходная смесь WO3 : Al : Ca : C : NiO состава 0.599 : 0.106 : 0.139 : 0.035 : 0.121; Δ[С] = 0 ≡ α = 15 вес.% (рис. 2–4).
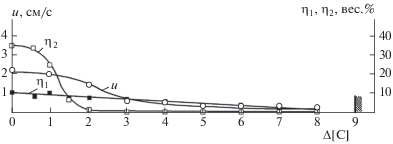
Третья серия экспериментов направлена на снижение содержания примесного Al в литом КМ за счет уменьшения содержания алюминия в составе исходной смеси WO3/Al/Ca/C/NiO (табл. 1). Для третьей серии экспериментов был выбран состав с ∆[С] = 1.8. При увеличении дефицита алюминия в смеси от –2.5 до –7.5 вес.% содержание Al в литом КМ снижается от 1.28 до 0.46 вес.%, а содержание углерода достигает максимума – 3.95 вес.% (табл. 1). Микроструктура и карта распределения элементов, состав структурных составляющих в литом КМ и его рентгенограмма представлены соответственно на рис. 8, 9 и 10. Из анализа карты, представленной на рис. 8, следует, что вольфрам локализован в ограненных зернах и зернах кружевной формы. Там же локализован углерод. По данным микроанализа и рентгенофазового анализа (рис. 9 и 10) они представляют собой фазы WC (крупные зерна), W2C (мелкие зерна) и Ni3W10C3.4 (кружевные зерна). Границы между зернами содержат раствор W и Al в Ni (рис. 8, 10).
Таблица 1.
Влияние недостатка алюминия в исходной смеси WO3 : Al : Ca : C : NiO состава 0.579 : 0.106 : 0.135 : 0.067 : 0.113 на химический состав литых КМ и параметры синтеза; P0 = 5 МПа
Δ[Al] | Доля Al в исходной смеси, вес.% | Относительная потеря массы (η1), % | Относительный выход КМ в слиток (η2), % | Содержание Al в слитке, вес.% | Содержание С в слитке, вес.% | Содержание Ni в слитке вес.% | Содержание W в слитке, вес.% |
---|---|---|---|---|---|---|---|
–2.5 | 10.04 | 11.37 | 46.90 | 1.28 | 3.21 | 15.80 | остальное |
–5.0 | 9.81 | 12.46 | 46.76 | 0.58 | 3.48 | 18.60 | – |
–7.5 | 9.57 | 9.52 | 47.32 | 0.53 | 3.95 | 17.50 | – |
–10.0 | 9.34 | 7.36 | 47.45 | 0.47 | 3.42 | 16.20 | – |
–15.0 | 8.87 | 6.05 | 45.32 | 0.46 | 3.24 | 16.00 | – |
Рис. 8.
Карта распределения элементов в литом КМ. Исходная смесь WO3/Al/Ca/C/NiO при Δ[Al] = –7.5 вес.% (см. табл. 1).
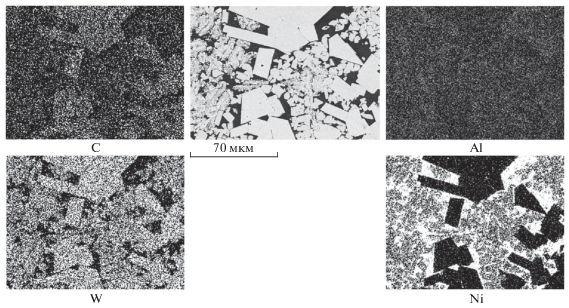
Рис. 9.
Дифрактограмма литого КМ. Исходная смесь WO3/Al/Ca/C/NiO при Δ[Al] = –7.5 вес.% (см. табл. 1).
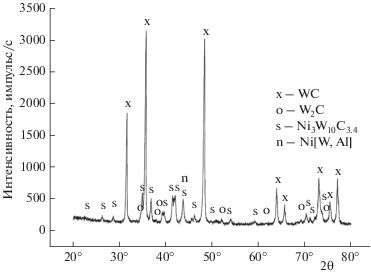
ОБСУЖДЕНИЕ РЕЗУЛЬТАТОВ
Экспериментально и методами термодинамики показано, что смесь сохраняет способность к горению при любых соотношениях между составами WO3/Al/Ca/C и NiO/Al, а температура их горения превышает температуру плавления продуктов горения, композиционного материала и шлака. Под действием гравитации происходит сепарация расплавов композиционного материала и шлака, а при последующем охлаждении – формирование их структуры. По данным химического и рентгенофазового анализов и электронной микроскопии, а также по результатам термодинамического расчета слой композиционного материала сформирован из целевых элементов W, C и Ni, а также включает примеси Al и O. Шлаковый слой после кристаллизации представляет собой твердый оксидный раствор Al2O3 и CaO. По данным термодинамических исследований газовые продукты горения содержат до 4% CO, до 3% Al2O от веса смеси, а также пары металлов (Al, Ca, Ni).
Из сопоставления содержания W, Ni C и Al в исходной смеси и в продуктах горения следует, что в процессе химического превращения и постпроцессах W и Ni почти целиком переходят в слиток композиционного материала, а углерод значительно расходуется на восстановление WO3 и NiO, что приводит к дефициту С и появлению Al в композиционном материале, а также появлению CO в газовой фазе.
Экспериментально показано, что дефицит углерода и содержание примесного алюминия в литом КМ удается существенно уменьшить при создании избытка углерода и дефицита Al в исходной смеси (рис. 6, табл. 1). Еще одним приемом повышения содержания углерода в КМ является использование углерода в виде графита с размером частиц ~100 мкм [18].
Схема химического превращения для исследуемой смеси WO3/Al/Ca/C/NiO может быть представлена в виде
(1)
${\text{W}}{{{\text{O}}}_{3}} + {\text{Ca}} + {\text{Al}} + {\text{C}} \to {\text{W}} + {\text{A}}{{{\text{l}}}_{{\text{2}}}}{{{\text{O}}}_{3}} + {\text{CaO}} + {\text{CO}},$(2)
${\text{NiO}} + {\text{Al}} + {\text{Ca}} + {\text{C}} \to {\text{Ni}} + {\text{A}}{{{\text{l}}}_{{\text{2}}}}{{{\text{O}}}_{{\text{3}}}} + {\text{CaO}} + {\text{CO}},$(3)
${\text{W}} + {\text{С}} + {\text{Ni}} + {\text{Al}} \to {\text{W}}{\kern 1pt} --{\kern 1pt} {\text{C}}{\kern 1pt} --{\kern 1pt} {\text{Ni}}{\kern 1pt} --{\kern 1pt} {\text{Al}}.$На первой стадии синтеза в волне горения параллельно протекают процессы металлотермического восстановления оксидов вольфрама и никеля алюминием, кальцием и углеродом (реакции (1), (2)). На второй стадии в реакционном объеме реализуется СВС-реакция взаимодействия между восстановленным вольфрамом, никелем, углеродом и примесным алюминием (реакция (3)).
Ранее в работе [17] было найдено оптимальное соотношение между металлами-восстановителями в шихте, которое обеспечивает синтез стекловидного эвтектического раствора Al2O3–СаO с температурой плавления 1300–1500 °С [19]. Для практической цели исследования понижение температуры кристаллизации этого раствора оксидов за счет оптимального эвтектического соотношения между оксидами Al и Ca и вместе с тем снижение вязкости шлаковой оксидной фазы позволяют максимально увеличить полноту выхода карбидовольфрамовой металлокерамики в слиток.
ЗАКЛЮЧЕНИЕ
Проведенные исследования показали, что варьирование соотношения компонентов экзотермической смеси термитного типа позволяет получать КМ различного состава. Реализуемые в ходе синтеза высокие температуры горения без использования каких-либо дополнительных источников питания обеспечивают синтез КМ в литом виде. Синтезированные литые сплавы могут найти свое потенциальное применение в качестве наплавочных материалов при всех видах наплавки как в порошкообразном, так и в стержневом или ином виде.
Список литературы
Жудра А.П. // Автомат. сварка. 2014. № 6–7. С. 66.
Сом А.И. // Там же. 2004. № 10. С. 49.
Жудра А.П., Ворончук А.П. // Там же. 2012. № 1. С. 39.
Воробьева Г.А., Складнова Е.Е., Ерофеев В.К., Устинова А.А. Конструкционные стали и сплавы. СПб.: Политехника, 2013.
Панов В.С., Чувилин А.М. Технология и свойства спеченных твердых сплавов и изделий из них: Уч. пос. для вузов. М.: МИСИС, 2001.
Курлов А.С., Гусев А.И. Физика и химия карбидов вольфрама. М.: Физматлит, 2013.
Liyanagea T., Fisher G., Gerlich A.P. // J. Wear. 2012. V. 274–275. P. 345; https://doi.org/10.1016/j.wear.2011.10.001
Zhou T., Lee K.Y., Gao L.-X., Zhang Da-Quan. // J. Corrosion Engin. Sci. and Technol. 2014. V. 49. Issue 3. P. 204.
Shan-PingLu, Oh-YangKwon // Surf. Coat. Technol. 2002. V. 153. Issue 1. P. 40; https://doi.org/10.1016/s0257-8972(01)01555-9
BillelCheniti, DjamelMiroud, PavolHvizdoš, JánBalko, RichardSedlák, TamásCsanádi, BrahimBelkessa, MartinFides. // Mater. Chem. Phys. 2018. V. 208. P. 237; https://doi.org/10.1016/j.matchemphys.2018.01.052
Fernandes C.M., Senos A.M.R., Vieira M.T., Antunes J.M. // Intern. J. Refract. Met. Hard Mater. 2008. V. 26. P. 491.
Taheri-Nassaj E., Mirhosseini S.H. // J. Mater. Processing Technol. 2003. V. 142. Issue 2. P. 422.
Лаптев А.В., Толочин А.И., Очкас Л.Ф. // Порошковая металлургия. 2003. № 11/12. С. 84.
Tolochin A.I., Laptev A.V., Okun I.Yu., Kovalchenko M.S. // Powder Metall. Metal Ceram. 2011. 50. № 5–6. P. 83.
Sakaki M., Karimzadeh Behnami A., Bafghi M.Sh. // Intern. J. Refract. Met. Hard Mater. 2014. V 44. P. 142.
Shiryaev A. // Intern. J. Self-Propag. High-Temp. Synth. 1995. V. 4. № 4. P. 351.
Силяков С.Л., Юхвид В.И. // Хим. физика. 2019. Т. 38. № 1. С. 49; https://doi.org/10.1134/S0207401X19010126
Silyakov S.L. and Yukhvid V.I. // Intern. J. Self-Propag. High-Temp. Synth. 2011. V. 20. № 3. P. 211.
Диаграммы состояния систем тугоплавких оксидов. Справочник / Под ред. Талахова Ф.Я. Вып. 5. Двойные системы. Л.: Наука, 1985. Ч. 1. С. 125.
Дополнительные материалы отсутствуют.
Инструменты
Химическая физика