Химическая физика, 2023, T. 42, № 2, стр. 28-36
Физико-химические и массообменные процессы при нагреве образцов из офлюсованных магнетитовых железорудных концентратов в тепловых установках
Б. П. Юрьев 1, *, В. А. Дудко 1
1 Уральский федеральный университет имени первого Президента России Б.Н. Ельцина
Екатеринбург, Россия
* E-mail: yurev-b@mail.ru
Поступила в редакцию 10.03.2022
После доработки 06.05.2022
Принята к публикации 20.05.2022
- EDN: IXXXOZ
- DOI: 10.31857/S0207401X23020164
Аннотация
Установлено, что обжиг образцов (гранул) в слое из офлюсованных магнетитовых железорудных концентратов сопровождается протеканием сложных физико-химических процессов, связанных с окислением магнетита и разложением карбонатов. При их нагреве наряду с теплообменными процессами протекают и массообменные. Эти процессы взаимосвязаны и оказывают влияние друг на друга, а также на степень завершенности процессов окисления и декарбонизации в слое. Рассмотрен механизм окисления образцов, содержащих магнетит. Уточнена модель процесса массообмена для периода разложения карбонатов. Предложено уравнение, описывающее кинетику окисления магнетита в образцах при нагреве для более общего вида краевых условий. Приведено уравнение, позволяющее определять константу скорости процесса окисления в зависимости от характеристик газа-теплоносителя и свойств материала. Разработана методика расчета коэффициента диффузии кислорода в продуктах сгорания различных топлив. Проведены эксперименты по изучению кинетики процессов окисления и декарбонизации в слое гранул на экспериментальной установке, позволяющие моделировать эти процессы в различные периоды их термообработки в тепловых установках и рассчитывать коэффициенты массообмена. Это позволит определять степени завершенности процессов по высоте слоя при заданных значениях температуры и продолжительности обжига.
ВВЕДЕНИЕ
В промышленных технологиях наряду с теплообменными широко распространены и масообменные процессы. Очень часто они идут совместно, и от интенсивности одних зависит скорость протекания других [1–3]. Это в полной мере относится и к процессу термической обработки образцов из офлюсованных магнетитовых концентратов, которые широко используются в металлургии при производстве чугуна или стали в качестве железосоставляющей в шихте. При нагреве в таких образцах возникают как потоки кислорода, принимающие участие в окислении магнетита, так и встречные потоки диоксида углерода, которые образовались в процессе разложения карбонатов [4–12]. Таким образом, основными источниками образования потоков массы вещества при обжиге офлюсованных магнетитовых образцов являются реакции окисления магнетита до гематита и разложения карбонатов [13–19]. При этом неизбежно взаимное наложение этих потоков, несмотря на различия начальных температур их возникновения и продолжительности существования.
В обжигаемом слое из образцов протекают физико-химические процессы в пространстве между гранулами (их форма близка к сферической), в порах материала, а также на поверхности раздела фаз. При этом нужно иметь в виду, что решающее значение при термообработке имеют гетерогенные процессы, связанные с окислением магнетита и разложением карбонатов, причем перенос теплоты и массы будет происходить не только в пределах самих образцов (гранул), но и через поверхность раздела между твердой и газовой фазами.
Основная задача расчета процессов массопередачи связана с определением коэффициентов пропорциональности в уравнениях кинетики или коэффициентов массообмена [20]. Аналитическое определение коэффициентов массообмена при обжиге гранул весьма сложно и требует знания многих дополнительных величин. Более перспективно экспериментальное определение этих коэффициентов.
В настоящей работе не ставилась задача аналитического описания процессов окисления и декарбонизации, происходящих при обжиге гранул. Для этого потребовалось бы совместное решение дифференциальных уравнений тепло- и массообмена в неподвижном плотном слое материала. Однако такое решение чрезвычайно сложно и для него прежде всего необходимо изучить массообменные характеристики. Цель работы состояла в исследовании физико-химических и массообменных процессов при окислительном обжиге офлюсованных гранул и определении коэффициентов массообмена в процессах окисления и декарбонизации.
ИЗУЧЕНИЕ МЕХАНИЗМА И КИНЕТИКИ МАССООБМЕНА ПРИ ОБЖИГЕ ОКОМКОВАННЫХ ЖЕЛЕЗОРУДНЫХ ГРАНУЛ
Что касается механизма окисления магнетитовых гранул, то необходимо отметить следующее. Процесс окисления сферических гранул идет в направлении от периферии к центру концентрическим фронтом [21, 22]. При обжиге гранул в потоке газа внешнее диффузионное сопротивление уменьшается с повышением скорости движения газа и в реальных условиях становится пренебрежимо малым по сравнению с внутренним диффузионным сопротивлением [23, 24]. Химическая кинетика протекания реакции окисления магнетита до гематита практически не влияет на общую продолжительность массообменных процессов, что подтверждается величинами энергии активации, представленными в работе [25].
Сравнение величин константы скорости окисления Fe3O4 до Fe2O3 в атмосфере кислорода при диффузии его через слой твердого оксида Fe2O3 с найденными значениями константы окисления в атмосфере воздуха показывает, что последние на два порядка меньше первых. Влияние состава газа указывает на то, что при обжиге гранул действует механизм диффузии кислорода не в твердой, а в газовой фазе, находящейся в порах гранулы.
Процессам массообмена в пористых телах посвящен ряд работ [23, 24], в которых предложено рассматривать диффузию газового компонента к поверхности реагирования по схеме газ–твердое тело. Такой подход не позволяет учитывать влияния состава газовой фазы, давления в системе, а также индивидуальных свойств материала на протекание массообменных процессов при обжиге гранул в слое.
Доставка кислорода к поверхности реагирования зависит от строения капилляров в пористом теле гранулы и определяется лабиринтным фактором, характеризующим влияние свойств материала на протекание диффузионных процессов [26]. Результаты изменения этого или аналогичного параметра в зависимости от температуры для железорудных гранул получены в работе [23]. Молекулы кислорода, достигнув границы раздела фаз магнетит–гематит, должны вступать в реакцию и переходить из газообразной фазы в твердую, что должно приводить к созданию разрежения в порах и поступлению новых объемов газа. Однако при изучении механизма окисления магнетитовых гранул автором работы [22] влияние данного явления на скорость и ход процесса не обнаружено.
Приведенное в работах [22, 27] уравнение кинетики окисления справедливо для диффузионной области и для случая, когда начальная степень окисления гранулы равна нулю, а концентрация кислорода в газовом потоке постоянна. Это ограничивает его применение для анализа работы промышленных агрегатов, так как при переходе из одной технологической зоны в другую степень окисления гранул отлична от нуля, а концентрация кислорода в газе-теплоносителе существенно изменяется.
Для общего случая краевых условий:
(1)
${{\psi }_{{\tau = 0}}} = {{\psi }_{0}}\,\,{\text{и}}\,\,{{C}_{{{{{\text{O}}}_{{\text{2}}}}}}} = {\text{const}}$(2)
$\frac{1}{3}\psi + \frac{1}{2}{{\left( {1 - \psi } \right)}^{{2{\text{/}}3}}} = \frac{1}{3}{{\psi }_{0}} + \frac{1}{2}{{\left( {1 - {{\psi }_{0}}} \right)}^{{2{\text{/}}3}}} - k\tau ,$При рассмотрении диффузионных процессов в пористых телах в работе [27] и в ряде других авторы предлагают использовать для расчетов эффективный коэффициент диффузии кислорода к фронту реагирования, найденный для системы газ–твердое тело. Такой подход методически прост, но ограничивает использование экспериментальных данных, так как в действительности диффузионный перенос осуществляется через газовый слой, заполняющий поры гранулы [23], и коэффициент диффузии в этом случае зависит от состава газовой фазы. Наиболее логично изменение свойств материала, влияющих на диффузионные процессы, представлять в виде зависимости от температуры, а состав газовой фазы учитывать для каждого конкретного случая.
Зависимость константы скорости окисления k от характеристик газа-теплоносителя и свойств материала приведена в работе [22]. После ряда преобразований она принимает следующий вид:
(3)
$k = {{D}_{{{{{\text{O}}}_{{\text{2}}}}}}}{{P}_{0}}\frac{1}{{{{r}^{2}}}}\frac{M}{{RT}}\frac{9}{{\rho g_{{{\text{FeO}}}}^{H}}}\frac{\varepsilon }{{{{k}_{1}}{{{\left( {1 - \varepsilon } \right)}}^{2}}}}{\text{ln}}\frac{{1 - {{C}_{{\text{p}}}}}}{{1 - {{C}_{{{{{\text{O}}}_{{\text{2}}}}}}}}},$Величина ${\varepsilon \mathord{\left/ {\vphantom {\varepsilon {{{k}_{1}}}}} \right. \kern-0em} {{{k}_{1}}}}{{\left( {1 - \varepsilon } \right)}^{2}} = \varepsilon \left( T \right),$ входящая в формулу (3), характеризует влияние свойств материала на процесс диффузии кислорода к поверхности реагирования. Так как теоретически возможно представить только качественную картину изменения этой составляющей выражения (3), для ее практического применения при использовании выражений (2) и (3) были проанализированы результаты лабораторных исследований, полученные в работе [28].
Обработка экспериментальных данных [28] показала, что функция ε(T) имеет экстремальный характер и приближенно представляется в виде
(4)
$\varepsilon \left( T \right) = a{{\left( {\frac{T}{{1000}}} \right)}^{b}}{\text{exp}}\left( {d\frac{T}{{1000}}} \right),$Свойства железорудных гранул в процессе нагрева претерпевают изменения. Так, например, при температурах до 1000 °C протекают процессы рекристаллизации [29], в связи с этим возможное увеличение реакционной поверхности и пористости приведет к возрастанию величины ε(T). Уменьшение этой величины при температурах выше 1000 °C связано с развитием твердофазного спекания зерен, появлением жидких фаз, перекрывающих поры, а значит, и уменьшением доли широко разветвленных мелких и открытых пор [27, 30].
Состав газовой фазы оказывает влияние на окислительные процессы, происходящие при обжиге магнетитовых гранул. В реальных условиях диффузия кислорода протекает в смеси газов, представляющих собой продукты сгорания жидкого или газообразного топлива, заполняющие поры материала.
Коэффициент диффузии компонента k в смеси с i-тыми инертными составляющими равен [20]
(5)
${{D}_{k}} = \left( {1 - {{y}_{k}}} \right){{\left[ {\sum\limits_1^i {\left( {\frac{{{{y}_{i}}}}{{{{D}_{{ik}}}}}} \right)} } \right]}^{{ - 1}}},$Были проведены расчеты по определению коэффициента диффузии кислорода в продуктах сгорания природного газа пяти месторождений; смеси доменного газа с природным (в соотношениях 1 : 1 и 7 : 3) и малосернистого мазута при изменении коэффициента расхода воздуха (α) от 1.5 до 3.0, а также температуры рассматриваемых материалов от 165 до 1400 °С. Расчеты показали, что для всех видов природного газа коэффициент ${{D}_{{{{{\text{O}}}_{{\text{2}}}}}}}$ при одной и той же температуре практически одинаков. Характерной особенностью природного газа является большая величина отношения объема воздуха, идущего на горение, к объему газа. Это обеспечивает преимущественное содержание в продуктах горения азота, чем и объясняется примерное постоянство величины ${{D}_{{{{{\text{O}}}_{{\text{2}}}}}}}$ для газа разных месторождений.
По этой же причине значения коэффициента диффузии в воздухе и продуктах сгорания природного газа весьма близки. Так, при 1100 °С и α = = 1.5 в атмосфере азота ${{D}_{{{{{\text{O}}}_{{\text{2}}}}}}} = 3.334 \cdot {{10}^{{ - 4}}},$ а в атмосфере продуктов сгорания природного газа – 3.354 · 10–4 м2/с, т.е. они различаются менее чем на 1%.
Для случая обжига офлюсованных гранул в температурных интервалах, соответствующих процессу разложения карбонатов, определение коэффициента диффузии усложняется. Диффузионные процессы можно представить двумя моделями [23]. Если реакция разложения карбонатов (обычно кальция и магния) протекает достаточно медленно и давление в порах гранул не превышает давления газа-теплоносителя, то процесс подчиняется второму закону Фика, а величина ${{D}_{{{{{\text{O}}}_{{\text{2}}}}}}}$ будет меняться за счет изменения мольных долей всех компонентов газа в порах гранул. Если же процесс разложения протекает быстро, в порах создается избыточное давление и диффузия затормаживается.
Для выявления типа модели массообмена в период разложения карбонатов проводили эксперименты по изучению кинетики процесса окисления и декарбонизации при скоростях нагрева, которые имеют место в промышленных агрегатах. Гранулы, содержащие 9% известняка, нагревали в потоке воздуха и непрерывно фиксировали изменение их массы. Уменьшение массы образца при полном разложении карбонатов должно было составлять 3.96%, что и наблюдалось при скорости нагрева vt = 1100 °C/мин, когда декарбонизация значительно опережает окисление. При vt = = 30 °C/мин заметное разложение карбонатов начинается выше температуры 700 °C и завершается примерно при 930 °C. Изменение массы образца в этом случае составляет всего 3%. Следовательно, в период разложения карбонатов кальция окислительные процессы продолжаются.
Расчеты, выполненные с использованием опытных данных, показали, что на 2.4 · 10–3 молей кислорода, поглощенного в результате окисления магнетита, выделяется 1.7 · 10–3 молей диоксида углерода [21]. Хорошая соизмеримость потоков свидетельствует о том, что в указанных условиях обжига CO2 будет выделяться из пор гранулы диффузионным путем, а повышения давления, тормозящего перенос кислорода, не происходит. Если выбранная модель процесса справедлива, то разложение карбонатов начнется после того, как материал нагреется до температуры, при которой равновесное парциальное давление ${{P}_{{{\text{C}}{{{\text{O}}}_{{\text{2}}}}}}}$ станет равным парциальному давлению CO2 в потоке. Это явление должно сопровождаться температурной остановкой [31].
Однако в условиях обжига гранул диоксид углерода, выделяющийся в газовую фазу, заполняющую поры, повышает его парциальное давление и этим приводит к тому, что в дальнейшем процесс разложения может идти лишь с повышением температуры. При достижении температуры, при которой давление ${{P}_{{{\text{C}}{{{\text{O}}}_{{\text{2}}}}}}} = f\left( {{{t}_{{\text{м}}}}} \right)$ (tм – температура материала °С) становится равным давлению в газовом потоке (Pобщ), условия для дальнейшего повышения температуры отсутствуют. Но то обстоятельство, что нагревается малое количество карбонатов в смеси с концентратом, должно привести лишь к замедлению процесса нагрева. После завершения диссоциации карбонатов скорость нагрева должна возрасти.
Такая картина изменения температуры гранул действительно наблюдалась при скорости нагрева vt = 100 °C/мин. При достижении температур 860–880 °C обнаруживается заметное уменьшение скорости нагрева, а при температуре ∼910 °C она вновь возрастает.
Пользуясь зависимостью давления диссоциации тонкодисперсного карбоната кальция от абсолютной температуры [31]:
(6)
${\text{lg}}{{P}_{{{\text{C}}{{{\text{O}}}_{{\text{2}}}}}}} = {{8600} \mathord{\left/ {\vphantom {{8600} T}} \right. \kern-0em} T} + 7.5,$Таблица 1.
Значения температур начала процесса диссоциации и при достижении условия ${{P}_{{{\mathbf{C}}{{{\mathbf{O}}}_{{\mathbf{2}}}}}}} = {{P}_{{{\mathbf{общ}}}}}$
Номер эксперимента | Барометрическое давление Pобщ, Торр | Содержание CO2 в газе-теплоносителе, % | Температура начала процесса разложения CaCO3, °C | Температура, при которой ${{P}_{{{\text{C}}{{{\text{O}}}_{{\text{2}}}}}}} = {{P}_{{{\text{общ}}}}},$ °C | |
---|---|---|---|---|---|
расчет | опыт | ||||
1 | 758 | 8.8 | 742 | 887 | 860–880 |
2 | 733 | – | – | 880 | 860–880 |
3 | 750 | 10.8 | 760 | 885 | 860–880 |
Формулу (6) можно использовать для определения равновесного парциального давления диоксида углерода ${{P}_{{{\text{C}}{{{\text{O}}}_{{\text{2}}}}}}}$ в порах гранулы в период разложения карбонатов, когда мольная доля CO2 равна
(7)
$y_{{{\text{C}}{{{\text{O}}}_{{\text{2}}}}}}^{'} = {{{{P}_{{{\text{C}}{{{\text{O}}}_{{\text{2}}}}}}}} \mathord{\left/ {\vphantom {{{{P}_{{{\text{C}}{{{\text{O}}}_{{\text{2}}}}}}}} {{{P}_{{{\text{общ}}}}}}}} \right. \kern-0em} {{{P}_{{{\text{общ}}}}}}},$(8)
$y_{j}^{'} = {{{{y}_{j}}\left( {1 - y_{{{\text{C}}{{{\text{O}}}_{{\text{2}}}}}}^{'}} \right)} \mathord{\left/ {\vphantom {{{{y}_{j}}\left( {1 - y_{{{\text{C}}{{{\text{O}}}_{{\text{2}}}}}}^{'}} \right)} {\left( {1 - {{y}_{{{\text{C}}{{{\text{O}}}_{{\text{2}}}}}}}} \right)}}} \right. \kern-0em} {\left( {1 - {{y}_{{{\text{C}}{{{\text{O}}}_{{\text{2}}}}}}}} \right)}},$Выделяющийся в газовую фазу диоксид углерода должен снижать процентное содержание кислорода в потоке теплоносителя. Однако расчеты показывают, что на 1 м3 газа-теплоносителя выделяется примерно 0.015 м3 CO2, что соответствует снижению концентрации кислорода на 1.5%. При рассмотрении процессов окисления магнетита таким изменением концентрации кислорода можно пренебречь.
Коэффициент диффузии кислорода определяли по формуле (5), но с учетом действительного содержания газовых компонентов в порах (см. формулы (7) и (8)). Расчеты по изменению величины ${{D}_{{{{{\text{O}}}_{{\text{2}}}}}}}$ проводили применительно к нагреву офлюсованных гранул в атмосфере продуктов сгорания природного газа, мазута и обогащенного доменного газа (70% доменного газа плюс 30% природного газа) при двух значениях общего давления в системе: 730 и 760 Торр. Из данных, представленных на рис. 1 видно, что с повышением температуры до 800 °C скорость роста коэффициента диффузии ${{D}_{{{{{\text{O}}}_{{\text{2}}}}}}}$ снижается, а выше 800–810 °C значения его уменьшаются за счет насыщения пор гранулы диоксидом углерода [23].
Рис. 1.
Изменение коэффициента диффузии кислорода при обжиге офлюсованных гранул продуктами сгорания природного газа (1), мазута (2) и обогащенного доменного газа (3) в температурных интервалах разложения СаСО3 при двух значениях общего давления: 730 (пунктирные линии) и 760 Торр (сплошные линии).
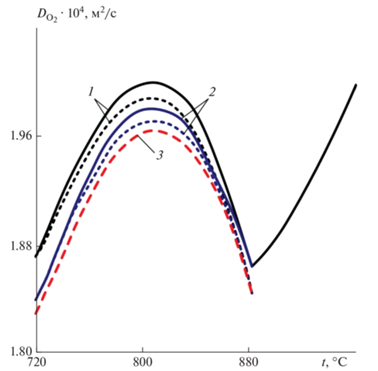
Начиная с момента времени, когда ${{P}_{{{\text{C}}{{{\text{O}}}_{{\text{2}}}}}}} = {{P}_{{{\text{общ}}}}},$ и до завершения процесса разложения углекислых соединений, можно считать, что диффузия кислорода осуществляется в атмосфере диоксида углерода, а величину ${{D}_{{{{{\text{O}}}_{{\text{2}}}}}}}$ следует определять для двойной газовой системы ${\text{C}}{{{\text{O}}}_{2}} \rightleftarrows {{{\text{O}}}_{2}}.$ В условиях разложения карбонатов коэффициент диффузии кислорода снижается до 40% (по сравнению с его значением, относящимся к продуктам сгорания жидкого или газообразного топлив). Это явление особенно важно для случая, когда в качестве флюсующей добавки применяется доломит. При этом температурный интервал разложения карбонатных соединений существенно растягивается, так как начало разложения смещается в область более низкой температуры.
Получим выражение для коэффициента массообмена. Для этого найдем приращение массы материала ΔGм за интервал времени, в течение которого степень окисления изменится на величину Δψ:
(9)
$\Delta {{G}_{{\text{м}}}} = \frac{1}{9}\rho g_{{{\text{FeO}}}}^{H}\left( {1 - \varepsilon } \right)\left( {1 - f} \right)\Delta \psi \Delta V.$В то же время величина ΔGм пропорциональна разности концентраций кислорода на поверхности реагирования (граница раздела фаз Fe3O4 и Fe2O3) и внешней поверхности гранулы, а также продолжительности протекания процесса:
(10)
$\Delta {{G}_{{\text{м}}}} = {{K}_{V}}\left( {C - {{C}_{{\text{p}}}}} \right)\Delta V\Delta \tau .$Приравнивая выражения (9) и (10), после ряда преобразований с учетом уравнения (4) получим
(11)
$\begin{gathered} {{K}_{V}} = 3{{D}_{{{{{\text{O}}}_{{\text{2}}}}}}}\frac{{1 - f}}{{{{r}^{2}}}}P\left( h \right)\frac{M}{{RT}}\alpha {{\left( {\frac{T}{{1000}}} \right)}^{b}}{\text{exp}}\left( {d\frac{T}{{1000}}} \right) \times \\ \times \,\,\left( {\frac{1}{{1 - {{{\left( {1 - \psi } \right)}}^{{\frac{1}{3}}}}}} - 1} \right)\frac{{1 - \varepsilon }}{{C - {{C}_{{\text{p}}}}}}{\text{ln}}\frac{{1 - {{C}_{{\text{p}}}}}}{{1 - C}}. \\ \end{gathered} $В уравнениях (9)–(11): 1/9 – коэффициент, учитывающий массу кислорода, расходуемую на окисление единицы массы FeO до Fe2O3; f – порозность слоя, доли ед.; ΔV – элемент объема слоя, м3/м2; KV – объемный коэффициент массообмена, кг/м3 · с; C – парциальное давление кислорода в пограничном слое, доли ед.; Δτ – время протекания процесса, с; P(h) – изменение общего давления газа по высоте слоя, Па.
Практическое применение уравнения (11) затруднено из-за необходимости знания большого количества дополнительных величин. Аналитическое определение коэффициентов массообмена при обжиге гранул (как отмечалось выше) также весьма сложно. Совместное решение уравнений тепло- и массообмена было бы полезным при использовании теоретических зависимостей коэффициентов массообмена от температуры, которые не найдены и вряд ли будут найдены в ближайшее время. Поэтому ниже приводятся результаты экспериментального определения этих коэффициентов.
Эксперименты проводили на установке, состоящей из обжиговой чаши диаметром 200 мм, газового горна, баллонов с пропан-бутановой смесью, регулирующей и контрольно-измерительной аппаратуры. Сырые гранулы диаметром 14–15 мм готовили на чашевом грануляторе из тщательно перемешанной смеси, %: соколовско-сарбайский концентрат – 91; известняк – 8; бентонит – 1. Влажность гранул перед опытами составляла 7–8%. Установка позволяла фиксировать в каждом опыте время отдельных периодов термообработки (отличающихся температурой подаваемого газа): I – сушка (tг = 410 °C), II – подогрев (tг = 1000 °C), III – обжиг (tг = 1275 °C) и IV – охлаждение.
В табл. 2 приведены исследованные режимы термообработки гранул, а также данные по изменению их химического и минералогического составов в процессе обжига. Отношение CaO : SiO2 в гранулах поддерживали в интервале 1.1–1.2. Слой нагревался продуктами сгорания смеси пропана и бутана, имевшей теплоту сгорания 86 150 кДж/м3. Скорость фильтрации v в экспериментах меняли от 0.6 до 1.0 м/с. В ходе опыта с помощью платинородий-платиновых термопар измеряли температуру на границе раздела “постель”–слой, а также на расстояниях h, равных 50, 100, 150 мм от “постели” по высоте слоя. С помощью двух отсасывающих термопар фиксировали температуру газов на входе в слой и выходе из него.
Таблица 2.
Влияние режима термообработки гранул из офлюсованных железорудных концентратов на изменение их химического и минералогического составов
v, м/с | ∆τ, периодов обработки, мин | h, мм | Содержание, % | ||||||||||||||
---|---|---|---|---|---|---|---|---|---|---|---|---|---|---|---|---|---|
I | II | III | IV | Fe3O4 | Fe2O3 | CaCO3 | CaO | CaSO4 | Ca2Fe2O5 | Fe2SiO4 | CaFeSiO4 | Ca3SiO5 | CaFe2O4 | Ca2SiO4 | Пр.* | ||
1.0 | 5 | – | 5 | 3.0 | 150 | 34.6 | 49.2 | 0.5 | 0.3 | 1.1 | 2.0 | 0.7 | 1.7 | 0.7 | 2.1 | 0.6 | 6.5 |
9.0 | 100 | 29.7 | 55.3 | 1.8 | 0.4 | 1.1 | 0.1 | 0.7 | 0.9 | 0.7 | 1.3 | 0.9 | 7.1 | ||||
17 | 50 | 31.2 | 54.3 | 4.3 | 0.3 | 1.2 | нет | 0.3 | 0.3 | 0.2 | 0.5 | 0.1 | 7.3 | ||||
5 | – | 10 | 4.0 | 150 | 30.2 | 53.0 | 0.4 | 0.4 | 1.2 | 1.5 | 0.7 | 1.1 | 0.6 | 2.2 | 1.1 | 7.6 | |
7.0 | 100 | 25.2 | 57.9 | 0.4 | 0.3 | 1.2 | 2.4 | 0.6 | 1.7 | 0.6 | 2.5 | 0.6 | 6.6 | ||||
11.0 | 50 | 30.2 | 55.0 | 1.9 | 0.2 | 1.3 | 0.8 | 0.3 | 0.6 | 0.7 | 1.9 | 0.6 | 6.5 | ||||
5 | – | 20 | 2.0 | 150 | 18.8 | 66.0 | 0.3 | 0.3 | 1.0 | 1.4 | 0.3 | 0.5 | 0.7 | 2.7 | 0.5 | 7.5 | |
8.0 | 100 | 29.4 | 54.7 | 0.2 | 0.1 | 0.5 | 2.5 | 0.3 | 0.6 | 0.3 | 4.0 | 0.3 | 7.1 | ||||
12.0 | 50 | 27.8 | 56.4 | 0.2 | 0.1 | 0.2 | 2.3 | 0.3 | 0.6 | 0.2 | 4. | 0.3 | 7.4 | ||||
0.7 | 5 | – | 7 | 1.0 | 150 | 17.8 | 64.0 | 1.1 | 0.6 | 0.7 | 3.5 | 0.6 | 0.6 | 0.7 | 3.7 | 1.3 | 5.4 |
13.0 | 100 | 24.2 | 54.6 | 0.2 | 0.3 | 0.8 | 4.7 | 0.3 | 0.7 | 0.8 | 5.0 | 2.1 | 6.3 | ||||
19.0 | 50 | 18.7 | 61.4 | 0.2 | 0.4 | 1.0 | 3.6 | 0.3 | 0.6 | 0.8 | 4.0 | 2.5 | 6.5 | ||||
5 | – | 17 | 1.5 | 150 | 7.7 | 72.4 | 0.9 | 0.5 | 0.7 | 4.0 | 0.2 | 0.3 | 0.9 | 4.5 | 1.3 | 6.6 | |
5.0 | 100 | 17.9 | 61.5 | 0.1 | 0.2 | 0.1 | 4.2 | 0.1 | 0.3 | 0.6 | 6.4 | 0.8 | 7.8 | ||||
9.0 | 50 | 14.2 | 65.9 | 0.2 | 0.2 | 0.2 | 3.6 | 0.1 | 0.3 | 0.7 | 6.1 | 1.9 | 6.6 | ||||
5 | 3 | 10 | 1.0 | 150 | 16.7 | 62.4 | 0.8 | 0.4 | 0.7 | 4.2 | 0.2 | 0.2 | 0.8 | 6.0 | 1.2 | 6.4 | |
5.0 | 100 | 20.8 | 58.2 | 0.1 | 0.2 | 0.1 | 5.1 | 0.2 | 0.2 | 0.7 | 6.0 | 1.8 | 6.6 | ||||
7.0 | 50 | 22.1 | 57.9 | 0.2 | 0.2 | 0.1 | 4.3 | 0.2 | 0.3 | 0.7 | 5.6 | 2.1 | 6.3 | ||||
5 | 3 | 20 | 0.5 | 150 | 6.6 | 72.5 | 0.8 | 0.5 | 0.6 | 4.1 | 0.1 | 0.3 | 0.7 | 6.0 | 1.0 | 6.8 | |
4.0 | 100 | 9.7 | 71.4 | 0.2 | 0.2 | 0.1 | 3.9 | 0.1 | 0.2 | 0.7 | 4.7 | 1.7 | 7.1 | ||||
6.0 | 50 | 13.7 | 67.5 | 0.1 | 0.2 | 0 | 3.5 | 0.1 | 0.2 | 0.8 | 5.2 | 1.8 | 6.9 |
Особенность опытов состояла в том, что после частичной термической обработки гранул в период обжига их охлаждали в токе аргона со скоростью 80–90 °C/мин. Таким образом, в заданный момент времени мгновенно прекращали развитие окислительных процессов и резко замедляли процесс разложения карбонатов. Охлажденные гранулы подвергали химическому и минералогическому анализам. Для расчета коэффициентов массообмена использовали уравнение (10), в котором $\Delta V = \omega \Delta h,$ где ω – площадь сечения аппарата, м2, Δh – высота элемента слоя, м.
Коэффициенты массообмена, характеризующие процессы окисления и декарбонизации, рассчитывали отдельно для каждого процесса. Из полученных результатов расчетов (табл. 3) следует, что с увеличением продолжительности обработки гранул в зоне обжига с 10 до 20 мин коэффициент массообмена, связанный с процессом окисления материала на одном и том же горизонте слоя (150 мм), уменьшается. Это объясняется повышением степени окисленности и появлением диффузионных затруднений.
Таблица 3.
Влияние условий термообработки гранул из офлюсованных железорудных концентратов на степень развития (β) в них процессов окисления (А) и декарбонизации (Б), а также на коэффициент массообмена, характеризующий эти процессы
v, м/с | ∆τ, периода обработки, мин | h, мм | β, % | ${{K}_{V}},$ кг/м3 · с | ||||
---|---|---|---|---|---|---|---|---|
I | II | III | А | Б | А | Б | ||
1.0 | 5 | – | 5 | 150 | 57 | 95 | $\frac{{0.60}}{{900{\text{*}}}}$ | $\frac{{0.21}}{{900}}$ |
100 | 63 | 81 | $\frac{{0.68}}{{800}}$ | $\frac{{0.68}}{{800}}$ | ||||
50 | 61 | 55 | $\frac{{0.67}}{{800}}$ | – | ||||
5 | – | 20 | 150 | 76 | 97 | $\frac{{0.21}}{{1000}}$ | $\frac{{0.02}}{{1000}}$ | |
100 | 63 | 98 | $\frac{{0.17}}{{900}}$ | $\frac{{0.06}}{{900}}$ | ||||
50 | 65 | 98 | $\frac{{0.18}}{{700}}$ | – | ||||
5 | – | 7 | 150 | 78 | 88 | $\frac{{0.58}}{{800}}$ | $\frac{{1.30}}{{800}}$ | |
100 | 70 | 98 | $\frac{{0.49}}{{700}}$ | – | ||||
50 | 76 | 98 | $\frac{{0.55}}{{600}}$ | – | ||||
0.7 | 5 | – | 17 | 150 | 90 | 91 | $\frac{{0.27}}{{970}}$ | $\frac{{0.03}}{{970}}$ |
100 | 78 | 99 | $\frac{{0.23}}{{850}}$ | $\frac{{0.12}}{{850}}$ | ||||
50 | 82 | 98 | $\frac{{0.24}}{{670}}$ | – | ||||
5 | 3 | 10 | 150 | 79 | 92 | $\frac{{0.30}}{{1000}}$ | $\frac{{0.03}}{{1000}}$ | |
100 | 74 | 99 | $\frac{{0.27}}{{850}}$ | $\frac{{0.15}}{{850}}$ | ||||
50 | 72 | 98 | $\frac{{0.27}}{{550}}$ | – | ||||
0.7 | 5 | 3 | 20 | 150 | 92 | 92 | $\frac{{0.20}}{{1100}}$ | $\frac{{0.01}}{{1100}}$ |
100 | 88 | 98 | $\frac{{0.20}}{{900}}$ | $\frac{{0.07}}{{900}}$ | ||||
50 | 83 | 99 | $\frac{{0.19}}{{800}}$ | $\frac{{0.39}}{{800}}$ |
При одинаковой выдержке материала в зоне обжига величина KV уменьшается в направлении к нижним горизонтам слоя, что обусловлено снижением температуры материала. Коэффициент массообмена, связанный с процессом декарбонизации, увеличивается по мере снижения температуры (табл. 3) из-за уменьшения давления диссоциации карбоната и значения разности (C – Cp) в выражении (10). Химическим анализом установлено, что при выдержке гранул в зоне обжига более 10 мин степень их окисления менялась незначительно, а содержание FeO достигало расчетной величины, равной 5% (16% Fe3O4). К концу периода обжига степень окисления гранул по магнетиту в среднем составляла 80%. Увеличение длительности выдержки гранул в зоне обжига свыше 10 мин не приводит к заметному изменению и степени декарбонизации гранул в слое. Завершенность этого процесса к концу периода обжига составляет практически 100%.
Найденные по экспериментальным данным усредненные значения коэффициентов массообмена характеризуют скорость протекания процессов окисления и декарбонизации в слое гранул в период обжига. Сопоставление их абсолютных значений не дает представления о количественной характеристике процессов. Однако применение найденных значений KV дает возможность определять степень завершенности процессов на любом горизонте и в среднем по слою при заданных значениях температуры и продолжительности обжига. Другими словами, коэффициент KV можно использовать при расчетах массообменных процессов в качестве константы и рассчитывать химический состав материалов, входящих в зону обжига, по результатам анализа конечного продукта или находить конечный состав материала по результатам анализа исходной пробы.
Формула (10) пригодна для расчета не только усредненных значений коэффициентов массообмена, но и локальных. Для этого необходимо иметь данные об истинном времени протекания процессов окисления и декарбонизации, для чего требуется проведение специальных исследований.
ЗАКЛЮЧЕНИЕ
В работе проведено изучение процессов окисления и разложения карбонатов при обжиге офлюсованных магнетитовых гранул. Предложено кинетическое уравнение для описания процесса окисления гранул. Уточнена модель массообмена для периода разложения карбонатов в гранулах и разработана методика расчета коэффициента диффузии кислорода. Определены коэффициенты массообмена, характеризующие скорость протекания процессов окисления и декарбонизации в слое гранул в период обжига и позволяющие определять степень завершенности этих процессов в различные периоды термообработки.
Список литературы
Королев В.Н. // Тепломассообмен. Екатеринбург: УГТУ–УПИ, 2006.
Брюханов О.Н., Шевченко С.Н. // Тепломассообмен. М.: Инфра – М, 2012.
Дульнев Г.Н. // Теория тепло- и массообмена. СПб.: НИУ ИТМО, 2012.
Yang X.Y., Gong Z.Q., Liu F.L. // J. Cent. South Univ. Technol. 2004. V. 11. № 2. P. 152.
Gao Q.J., Shen Y.S., Liu C.S. // J. Iron Steel Res. Intern. 2016. V. 23. № 10. P. 1007.
Zhang H.Q., Fu J.T. // Intern. J. Miner. Metall. Mater. 2017. V. 24. № 6. P. 603.
Zhang H.Q., Fu J.T., Guo Z.Q. // J. Wuhan Univ. Technol. Mater. Sci. Ed. 2018. V. 33. № 6. P. 1516.
Liang R.Q., Yang S., He J.C. // J. Iron Steel Res. Intern. 2013. V. 20. № 9. P. 16.
Петров Л.В., Соляников В.М. // Хим. физика. 2021. Т. 40. № 11. С. 9.
Шайтура Н.С., Ларичев М.Н. // Хим. физика. 2020. Т. 39. № 9. С. 18.
Рязанов А.А., Рахимов Р.З., Винниченко В.И. и др. // Строит. материалы. 2020. № 3. С. 54.
Фрумина Н.С., Кручкова Е.С., Муштакова С.П. // Аналитическая химия кальция. Сер. Аналитическая химия элементов. М.: Наука, 1974.
Колобердин В.И., Боброва Н.С. // Химия и хим. технология. 2005. Т. 48. Вып. 1. С. 81.
Голубев В.О., Белоглазов И.Н. // Записки Горного института. 2006. Т. 169. С. 104.
Манташян А.А. // Хим. физика. 2021. Т. 40. № 4. С. 18.
Кольцов Н.И. // Хим. физика. 2021, Т. 40. № 11. С. 3.
Eriksson A., Andersson C., Semberg P. // ISIJ Intern. 2021. V. 61. № 5. P. 1439.
Kumar T.K.S., Viswanathan N.N., Bjorkman B. // Metall. Mater. Trans. B. 2019. V. 50. № 1. P. 162.
Sardari A., Alamdari E.K., Toncaboni S.Z. et al. // Intern. J. Miner. Metall. Mater. 2017. V. 24. № 5. P. 486.
Кафаров В.В. Основы массопередачи. М.: Высш. шк., 1962.
Абзалов В.М., Горбачев В.А., Евстюгин С.Н. и др. Физико-химические и теплотехнические основы производства железорудных окатышей. / Под ред. акад. Леонтьева Л.И. Екатеринбург: МИЦ, 2015.
Эдстрем И.О. // Пробл. современной металлургии. 1958. № 1. С. 3.
Юрьев Б.П., Брук Л.Б., Спирин Н.А. и др. Основы теории процессов при обжиге железорудных окатышей. Нижний Тагил: НТИ (филиал) УрФУ, 2018.
Берман Ю.А., Марков А.Д. // Изв. вузов. Черн. металлургия. 1971. № 1. С. 31.
Ball D.F., Buler F.G., Ratter H. // Iron and Steel. 1966. V. 39. № 4. P. 150.
Фон Богданди Л., Энгель Г.Ю. Восстановление железных руд. Пер. с нем. М.: Металлургия, 1971.
Братчиков С.Г., Берман Ю.А., Белоцерковский Я.Л. и др. Теплотехника окускования железорудного сырья. М.: Металлургия, 1970.
Копырин И.А., Перминов Н.И., Борц Ю.М. // Изв. вузов. Черн. металлургия. 1970. № 6. С. 28.
Похвиснев А.Н., Савельев Б.А. // Сталь. 1958. № 2. С. 105.
Юсфин Ю.С., Базилевич Т.Н., Савицкая Л.Ю. // Изв. вузов. Черн. металлургия. 1968. № 9. С. 31.
Есин О.А., Гельд П.В. // Физическая химия пирометаллургических процессов. Т. 1. М.: Металлургиздат, 1950.
Дополнительные материалы отсутствуют.
Инструменты
Химическая физика