Химия твердого топлива, 2019, № 4, стр. 18-25
УГЛЕРОДНЫЙ СОРБЕНТ НА ОСНОВЕ МЕЛОЧИ СПЕЦКОКСА ДЛЯ ИЗВЛЕЧЕНИЯ ЗОЛОТА
С. В. Ефремова 1, *, А. А. Кабланбеков 1, **, К. К. Анарбеков 1, ***, Л. В. Бунчук 1, ****, Ю. И. Сухарников 1, *****, Н. И. Богданович 2, ******, А. Ж. Терликбаева 1, *******, А. А. Жарменов 1, ********
1 РГП “Национальный центр по комплексной переработке минерального сырья Республики Казахстан”
050036 Алматы, Республика Казахстан
2 ФГАОУ ВО “Северный (Арктический) федеральный университет имени М.В. Ломоносова”
163002 Архангельск, Россия
* E-mail: s_yefremova@cmrp.kz
** E-mail: e-mail: kablanbekov_as@mail.ru
*** E-mail: Kuna89kr@mail.ru
**** E-mail: scc04@mail.ru
***** E-mail: scc04@gmail.com
****** E-mail: n.bogdanovich@narfu.ru
******* E-mail: alma_terlikbaeva@mail.ru
******** E-mail: jarmen56@mail.ru
Поступила в редакцию 14.01.2019
После доработки 13.02.2019
Принята к публикации 02.04.2019
Аннотация
Выполнены исследования по получению углеродных сорбентов на основе мелочи спецкокса с помощью комбинирования методов парогазовой (отходящим газом после карбонизации при 600°С шубаркольского угля, углекислым газом, перегретым водяным паром) и химической (гидроксидом натрия) активации. Изучены их текстурные и сорбционные характеристики. Показана необходимость разделения углеродной и минеральной частей мелочи спецкокса методом отмучивания в воде. Установлена высокая адсорбционная активность полученных образцов в отношении ионов золота (степень извлечения 99.4–99.9%). Рекомендованы метод получения сорбента на основе мелочи спецкокса для извлечения золота из цианистых растворов и оптимальные условия его адсорбции.
Производство углеродных сорбентов актуально на протяжении ряда лет. Различные адсорбтивы, например компоненты-загрязнители газовых выбросов, сбросовых сточных вод или полезные компоненты продуктивных растворов, имеют высокую степень сродства с углеродными адсорбентами [1–4], обеспечивая универсальность их использования. Ввиду высокой стоимости последних исследователями ведется поиск доступного сырья и способов его переработки, которые бы в комплексе позволили создать материалы с необходимой сорбционной емкостью при достаточном уровне прочности и приемлемой цене [5]. С этой точки зрения в числе популярных сырьевых ресурсов выступают отходы сжигания твердого топлива, отходы угледобычи, коксовая крошка, активированный кокс, каменные и бурые угли [4, 6–10].
В филиале РГП “Национальный центр по комплексной переработке минерального сырья Республики Казахстан” “Центр металлургии” (Восточно-Казахстанская область) запущена установка термоокислительного обжига углей с получением спецкокса для металлургических процессов. В качестве восстановителя используется спецкокс крупностью 5–25 мм. При этом мелочь спецкокса размером до 5 мм накапливается в отвалах, хотя потенциально может быть рассмотрена в качестве сырьевого источника для производства углеродных сорбентов. В связи с этим в настоящем исследовании поставлена цель – разработать углеродный сорбент на основе мелочи спецкокса и испытать его в сорбционной технологии извлечения золота.
ЭКСПЕРИМЕНТАЛЬНАЯ ЧАСТЬ
В качестве сырьевого ресурса использовали мелочь (2–5 мм) спецкокса, произведенного в Центре металлургии из некоксующегося шубаркольского угля на установке термоокислительного обжига мощностью 15000 т/год. Детальная характеристика спецкокса представлена в [11].
Сорбенты получали путем парогазовой и химической активации мелочи спецкокса, а также комбинированными приемами ее обработки. Парогазовую активацию выполняли при температуре 850–900°С в течение 1–2 ч, применяя в качестве активирующего агента попеременно отходящий газ после карбонизации при 600°С шубаркольского угля, углекислый газ, перегретый водяной пар. Химическую активацию осуществляли обработкой мелочи спецкокса раствором гидроксида натрия с концентрацией 50 и 70 г · дм–3 при соотношении Т : Ж = 1 : 15 в течение 3 ч при кипячении и для сравнения без нагрева.
Разделение углеродной и минеральной частей спецкокса проводили методом отмучивания, основанном на разной скорости падения углеродных частиц и частиц минеральной части в воде. Для этого мелочь спецкокса взбалтывали в большом количестве воды. Для достижения более полного разделения в воду добавляли керосин в соотношении керосин : вода = 1 : 8. Пульпу перемешивали в течение 10–20 мин. По окончании перемешивания происходило быстрое разделение содержимого на два слоя. Гидрофобный углерод концентрировался сверху в слое керосина, а гидрофильные компоненты золы оседали в воде на дно сосуда.
Удельную площадь поверхности и суммарный объем пор образцов сорбентов устанавливали с помощью метода БЭТ по низкотемпературной адсорбции азота на приборе AccuSorb (Micromeritics, USА). Адсорбционные свойства характеризовали по показателю адсорбционной способности по йоду и адсорбции золота из модельных растворов.
Определение адсорбционной активности по йоду (Ай) выполняли по разности содержания йода в растворе до и после взаимодействия с сорбентом [11].
Модельные растворы с разной концентрацией золота (от 2 до 10 мг · дм–3) готовили из стандартного солянокислого раствора с концентрацией золота 1 г · дм–3 методом разбавления в мерной посуде. Аликвоту стандартного раствора разбавляли водой для получения исходного раствора с концентрацией золота 100 мг · дм–3. Далее точное количество исходного раствора разбавляли щелочным раствором (рН 10.5) цианида натрия с концентрацией 0.3 г · дм–3. В золотосодержащий раствор вводили определенное количество ионов серебра, меди и цинка для получения состава, аналогичного продуктивному раствору. Для поддержания водородного показателя на уровне 10.5 добавляли раствор гидроксида натрия.
Сорбцию золота изучали в статических условиях при соотношении сорбент (г) : раствор (см3) = = 1 : 200; 1 : 100; 1 : 50, исходном значении рН раствора в среднем 10.5 и времени контакта сорбента с раствором от 15 до 60 мин.
Для количественного описания равновесия сорбции ионов золота на поверхности углеродного сорбента, полученного из мелочи спецкокса, применяли модели изотерм Ленгмюра и Фрейндлиха [12, 13].
С целью оптимизации параметров процесса извлечения золота новым углеродным сорбентом использовали метод трехфакторного эксперимента с применением центрального композиционного ротатабельного плана второго порядка [14].
ОБСУЖДЕНИЕ РЕЗУЛЬТАТОВ
Известно, что адсорбционные свойства углеродных адсорбентов во многом определяются особенностями их строения – структурой углерода, размерами его кристаллов, наличием тех или иных химических соединений на поверхности.
Как было показано ранее [11], мелочь спецкокса образована частицами разных размеров с различной структурой. При преимущественном преобладании непористых частиц методом сканирующей электронной микроскопии установлено присутствие частиц, пронизанных порами округлой и овальной формы размером от менее 1 до 30 мкм. Методом просвечивающей электронной микроскопии показано, что основную массу составляют рыхлые частицы с порами от 2 до 5 нм. Однако углерод в них, по данным микродифракционного исследования, подтвержденного результатами рентгенофазового анализа, выполненного по методике [15], характеризуется наличием трехмерно-упорядоченной структуры, хотя в нем также присутствуют уплощенные частицы округлой формы аморфного углеродного вещества. Такое строение мелочи спецкокса обусловливает низкий уровень ее сорбционной активности, о чем свидетельствует показатель адсорбции йода, равный 1.9%. В то же время сформировавшаяся при получении спецкокса система пор – это обнадеживающий фактор развития микропористости различными приемами активации.
Известно, что одним из распространенных способов парогазовой активации углей и коксов с целью получения сорбента является окисление в присутствии диоксида углерода при высоких температурах [5]. Для сокращения затратной составляющей данного процесса была изучена возможность использования отходящего газа после карбонизации угля в качестве активирующего агента. Полученные результаты (табл. 1, образец СК–ПГС) свидетельствуют о незначительном развитии поверхности и системы микропор мелочи спецкокса под действием парогазовой смеси в составе отходящего газа: активность по йоду (Ай), выбранная как показатель микропористости и удельной поверхности, возросла немногим чуть более чем в 4 раза, достигнув 8.9%. Невысокое значение активности по йоду данного образца может быть обусловлено рядом факторов. В первую очередь, закупориванием пор в результате адсорбционно-конденсационных процессов компонентов отходящего газа. Углеводородные соединения, в частности смолистые вещества, в газообразном состоянии проникая вглубь имеющихся и вновь образовавшихся пор активируемого материала, после его охлаждения конденсируются, забивая поровое пространство. В целях устранения данного негативного явления активированный образец СК–ПГС обрабатывали раствором гидроксида натрия, как описано в [16], где показана целесообразность такой обработки на примере углеродных сорбентов из растительного сырья, активированных парогазовой смесью после карбонизации прекурсора. Однако в данном случае химическая обработка щелочью не дала положительного эффекта (табл. 1, образец СК–ПГСЩ).
Таблица 1.
Результаты активации углеродсодержащих материалов на основе мелочи спецкокса с использованием углекислого газа, в том числе в составе отходящего газа после карбонизации шубаркольского угля
Образец | Активирующий агент | Т, °С | t, ч | Маркировка после активации | Выход, % | Ай, % |
---|---|---|---|---|---|---|
Мелочь спецкокса | ПГС | 850–900 | 2 | СК–ПГС | 87 | 8.9 |
СК–ПГС | NaOH, 30 г · дм–3 | 90 | 2 | СК–ПГСЩ | 100 | 7 |
УСК | ПГС | 850–900 | 1 | УСК–ПГС | 83 | 10.2 |
УСК | СО2 | 850–900 | 0.5 | УСК–СО2–1 | 75 | 16.5 |
УСК | СО2 | 850–900 | 1 | УСК–СО2–2 | 73 | 17.8 |
Отрицательное влияние на формирование пористой структуры сорбента оказывает и высокая зольность исходного сырья. В связи с этим было выполнено разделение углеродной и минеральной частей спецкокса методом отмучивания. Так как частицы минеральной части гораздо тяжелее частиц углерода, они в состоянии покоя пульпы быстро оседали на дно. Углеродный материал (УСК) оставался на поверхности воды. Его выход составил 60%, адсорбционная активность по йоду – 2.5%.
Данные по активации углеродного материала парогазовой смесью (табл. 1, образец УСК–ПГС) говорят о слабой эффективности изучаемого приема, что, вероятно, связано с недостаточным содержанием CO2 в отходящем газе. С учетом этого была выполнена активация диоксидом углерода, который для достижения стехиометрического соотношения с углеродом, взятым для активации, подавали в течение 0.5 ч со скоростью 1 дм3 · мин–1. Полученный образец УСК–СО2–1 имел показатель активности по йоду, равный 16.5%. Увеличение продолжительности активации в 2 раза (образец УСК–СО2–2) не позволило получить ожидаемого результата: значение Ай возросло всего на 1.3%, достигнув 17.8%.
Очевидно, трудность активации углеродного материала из мелочи спецкокса вызвана его строением, характеризующимся присутствием нескольких рентгеновских фаз, в том числе высокоупорядоченной графитоподобной компоненты [11].
В технологии производства углеродных сорбентов особое место отводится термохимическим способам активации с применением гидроксидов щелочных металлов, поскольку этот метод позволяет получать сорбенты с высокими показателями адсорбционных свойств, варьировать в широких пределах параметры их пористой структуры и даже повышать селективность к ионам сорбируемых металлов [2, 9, 17, 18]. В связи с этим выделенный из мелочи спецкокса углеродный материал (образец УСК) при разных режимных параметрах (табл. 2) обрабатывали раствором гидроксида натрия для удаления углеводородных соединений с образованием дополнительной пористости, а затем подвергали парогазовой активации. Ввиду гидрофобности поверхности углерода введение керосина в воду при отмучивании мелочи спецкокса обеспечило повышение выхода углеродного материала (85% против 60% при отмучивании в воде) при существенном сокращении потерь. Причем с увеличением времени обработки мелочи спецкокса смесью керосин : вода от 10 до 20 мин выход углеродного материала возрос с 85% (УСК–К10) до 92% (УСК–К20). Активацию полученных разными способами углеродных материалов проводили перегретым водяным паром в два этапа. Представленные в табл. 2 данные указывают на эффективность чередования процессов нагрев–охлаждение, оказывающих влияние на формирование и развитие пористой структуры и удельной поверхности, о чем свидетельствует рост сорбционной емкости готовых сорбентов в отношении йода свыше 50%. Удельная площадь поверхности данных образцов составила 600–610 м2 · г–1, суммарный объем пор – 0.40–0.42 см3 · г–1.
Таблица 2.
Результаты активации углеродных материалов из мелочи спецкокса с использованием перегретого водяного пара
Условия обработки образца УСК | 1-й этап активации водяным паром | 2-й этап активации водяным паром | ||||||
---|---|---|---|---|---|---|---|---|
t, мин | расход воды, кг/1 кг сорбента | выход, % | Ай, % | t, мин | расход воды, кг/1 кг сорбента | выход, % | Ай, % | |
с (NaОH) = 70 г · дм–3, без нагрева, 3 ч, | 50 | 10.5 | 60 | 34.3 | ||||
Т : Ж = 1 : 15* | 50** | 16.9** | 50** | 52.1** | ||||
с (NaОH) = 50 г · дм–3, при кипячении, 3 ч, | 50 | 18 | 26 | 33 | ||||
Т : Ж = 1 : 15* | ||||||||
Керосин : вода = 1 : 8, | 60 | 10 | 66.7 | 29.2 | 60 | 24.4 | 47.4 | 50.8 |
Т : Ж= 1 : 90, при перемешивании, 20 мин*** |
Поскольку наработанные при разных условиях углеродные сорбенты после двухстадийной активации перегретым водяным паром имели практически одинаковые текстурные характеристики и показатели адсорбционной способности по йоду, для тестирования в процессе извлечения золота из модельного раствора были выбраны образцы типа УСК–Н2О, отличающиеся простотой получения, для сравнения после одного (УСК–Н2О–1, Ай = 27%) и двух (УСК–Н2О–2, Ай = 52%) этапов активации перегретым водяным паром. Результаты показали (табл. 3), что оба сорбента, несмотря на разную сорбционную активность по йоду, в одинаковых условиях проявляют достаточно высокую активность по отношению к ионам золота, обеспечивая 80–90%-ное его извлечение (в обоих случаях процесс протекает с понижением рН до ∼9). Можно предположить, что для рассматриваемого процесса важна не столько удельная поверхность сорбента, сколько химия его поверхности, определяемая наличием активных центров и их количеством, о значимой роли которых сообщалось в [3].
Таблица 3.
Сорбция металлов сорбентами типа УСК–Н2О из модельного раствора
Aй, % | pHисх | Время сорбции, мин | Степень извлечения*, % | Доля благородных металлов на адсорбенте, % | |||
---|---|---|---|---|---|---|---|
Au | Ag | Cu | Zn | ||||
27 | 10.5 | 30 | 85.4 | 91 | 6.7 | 43 | 38.5 |
27 | 60 | 91 | 79 | 0 | 81.1 | 28.9 | |
52 | 30 | 87.6 | 95.5 | 8.6 | 46.6 | 36.2 | |
52 | 60 | 78.3 | 84.5 | 0 | 52.3 | 36 |
Как показали кинетические исследования (рис. 1), полное насыщение сорбента при извлечении золота из сложного модельного раствора с концентрацией Au ∼ 10 мг · дм–3 наступает уже в первые 15 мин независимо от соотношения сорбент (г) : раствор (см3). Величина адсорбции закономерно, причем достаточно равномерно, растет с увеличением количества адсорбтива в растворе, о чем свидетельствуют изотермы адсорбции (рис. 2), полученные в экспериментах на растворах с разной (от ∼2 до ∼10 мг · дм–3) концентрацией ионов золота при практически одинаковом содержании сопутствующих металлов. Степень извлечения ионов золота в зависимости от их концентрации в растворе находится на уровне 99.4–99.9%.
Рис. 1.
Кинетические кривые адсорбции ионов золота сорбентом типа УСК–Н2О (состав модельного раствора, мг · дм–3: Au 9.93; Ag 0.18; Cu 29.93; Zn 9.5): 1 – сорбент (г) : раствор (см3) = 1 : 200; 2 – сорбент (г) : : раствор (см3) = 1 : 100; 3 – сорбент (г) : раствор (см3) = 1 : 50.
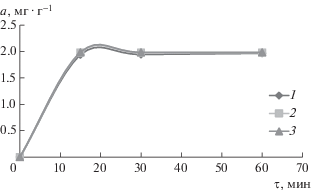
Рис. 2.
Изотермы адсорбции ионов золота сорбентом типа УСК–Н2О (состав модельных растворов, мг · дм–3: Au 1.85, Ag 0.16, Cu 29.58, Zn 9.88; Au 3.76, Ag 0.09, Cu 29.58, Zn 9.50; Au 5.66, Ag 0.13, Cu 28.68, Zn 9.25; Au 7.74, Ag 0.14, Cu 28.68, Zn 9.25; Au 9.93, Ag 0.18, Cu 29.93, Zn 9.5): 1 – сорбент (г) : раствор (см3) = 1 : 200; 2 – сорбент (г) : раствор (см3) = = 1 : 100; 3 – сорбент (г) : раствор (см3) = 1 : 50.
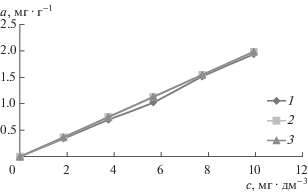
По изотермам Ленгмюра и Фрейндлиха, построенным на основании результатов сорбционного извлечения ионов золота, рассчитаны константы соответствующих уравнений Ленгмюра (am = 3.08, KL = 2.32) и Фрейндлиха (KF = 1.68 и n = 4.70). Принимая во внимание значения данных показателей, в соответствии с [19] можно говорить, что адсорбция ионов золота углеродным сорбентом из мелочи спецкокса из сложного модельного раствора протекает благоприятно. Модель Ленгмюра показывает хорошее соответствие расчетной величины экспериментальным данным адсорбции в области малых концентраций золота (от 2 до 6 мг · дм–3), поэтому может быть использована в дальнейшем для прогнозирования величины адсорбции из растворов с заданной концентрацией.
С помощью метода трехфакторного эксперимента с применением центрального композиционного ротатабельного плана второго порядка [14] построена математическая модель адсорбции ионов золота углеродным сорбентом из мелочи спецкокса, имеющая следующий вид:
На основе построенных поверхностей отклика степени извлечения ионов золота при различных параметрах сорбции (рис. 3) рекомендованы следующие оптимальные условия: масса сорбента – 5 г, время взаимодействия – 20 мин, концентрация раствора – от 2 до 10 мг · дм–3.
ВЫВОДЫ
1. Разработан способ получения углеродного сорбента, включающий разделение мелочи спецкокса на углеродную и минеральную части методом отмучивания в воде с последующей активацией перегретым водяным паром.
2. На основе мелочи спецкокса синтезирован углеродный сорбент, обеспечивающий высокую скорость адсорбции и практически полное извлечение ионов золота (99.4–99.9%) в широком диапазоне концентраций из сложных модельных растворов.
3. Моделями изотерм Ленгмюра и Фрейндлиха подтверждено, что адсорбция ионов золота углеродным сорбентом на основе мелочи спецкокса протекает благоприятно. Модель Ленгмюра целесообразно использовать при изучении процесса сорбции полученным сорбентом.
4. По результатам математического моделирования методом трехфакторного эксперимента с применением центрального композиционного ротатабельного плана второго порядка, рекомендованы оптимальные условия сорбционного извлечения золота углеродным сорбентом на основе мелочи спецкокса из водных растворов.
Список литературы
Yahyaa M.A., Al-Qodahb Z., Ngaha C.W.Z. // Ren. Sustain. Energy Rev. 2015. V. 46. P. 218. https://doi.org/10.1016/j.rser.2015.02.051
Chen Y., Zhu Y., Wang Z., Li Y., Wang L., Gao X., Ma Y., Guo Y. // Adv. Coll. Interface Sci. 2011. V. 163. P. 39. https://doi.org/10.1016/j.cis.2011.01.006
Рандин О.И., Афонина Т.Ю., Дударев В.И., Москаева Н.Ю., Сырых Ю.С. // Изв. вузов. Цветная металлургия. 2008. № 4. С. 22.
Афонина Т.Ю., Дударев В.И., Ознобихин Л.М., Сырых Ю.С. // Журн. физ. химии. 2007. Т. 81. № 3. С. 432.
Șahin Ö., Saka C. // Biores. Technol. 2013. V. 136. P. 163. https://doi.org/10.1016/j.biortech.2013.02.074
Ahmadpour A., Do D.D. // Carbon. 1996. V. 34. № 4. P. 471. https://doi.org/10.1016/0008-6223(95)00204-9
Zhang C., Chen Z., Li J., Guo Y., Cheng F. // Desalinat. Water Treatm. 2017. № 88. P. 75. https://doi.org/10.5004/dwt.2017.20790
Zhang C., Li J., Chen Z., Cheng F. // J. Chem. Technol. Biotechnol. 2018. № 93. P. 112. https://doi.org/10.1002/jctb.5328
Тамаркина Ю.В., Кучеренко В.А., Шендрик Т.Г. // ХТТ. 2015. № 2. С. 34. . [Solid Fuel Chemistry, 2015, vol. 49, no. 2, p. 91. DOI: 10.3103/S036152191502010X]https://doi.org/10.7868/S0023117715020103
Ефремова С.В. // РХЖ. 2011. Т. 55. № 1. С. 26. [Russian Journal of General Chemistry, 2012, vol. 82, i. 5, p. 963. DOI: 10.1134/S1070363212050295]
Yefremova S., Kablanbekov A., Anarbekov K., Bunchuk L., Terlikbayeva A., Zharmenov A. // Proceedings of the 18th Symposium on Environmental Issues and Waste Management in Energy and Mineral Production. SWEMP 2018 – Selected works. Springer Nature Switzerland AG, 2019. P. 217. https://doi.org/10.1007/978-3-319-99903-6_19.10.1007/978-3-319-99903-6_19
Хохлачева Н.М., Ильина Е.Б., Ряховская Е.В. Поверхностные явления. Адсорбция на поверхности твердых тел: Метод. указания к лаб. работе по курсу “Физическая химия”. М.: МАТИ, 2000. 21 с.
Самонин В.В., Подвязников М.Л., Никонова В.Ю., Спиридонова Е.А., Шевкина А.Ю. Сорбирующие материалы, изделия, устройства и процессы управляемой адсорбции. СПб.: Наука, 2009. 271 с.
Богданович Н.И., Кузнецова Л.Н., Третьяков С.И., Жабин В.И. Планирование эксперимента в примерах и расчетах. Архангельск: САФУ, 2010. 126 с.
Ефремова С.В., Королев Ю.М., Сухарников Ю.И. // ДАН. 2008. Т. 419. № 1. С. 77 [Doklady Chemistry, 2008, vol. 419, p. 1, p. 78. DOI: 10.1134/S0012500808030099]
Ефремова С.В., Кабланбеков А.А., Сухарников Ю.И., Хайн Ю., Жарменов А.А. Пористые углеродные материалы: синтез, характеристика, применение. Алматы, 2017. 160 с.
Белецкая М.Г. Синтез углеродных адсорбентов методом термохимической активации гидролизного лигнина с использованием гидроксида натрия: Автореф. дисс. … канд. тех. наук. Архангельск: САФУ, 2014. 20 с.
Ефремова С.В., Королев Ю.М., Сухарников Ю.И., Кабланбеков А.А., Анарбеков К.К. // ХТТ. 2016. № 3. С. 14. [Solid Fuel Chemistry, 2016, vol. 50, no. 3, p. 152. DOI: 10.3103/S0361521916030058]https://doi.org/10.7868/S0023117716030051
Olalekan A.P., Dada A.O., Okewale A.O. // Res. J. Chem. Environmental Sci. 2013. V. 1. № 1. 5. P. 22.
Дополнительные материалы отсутствуют.
Инструменты
Химия твердого топлива