Химия твердого топлива, 2019, № 4, стр. 9-17
ПРЕОБРАЗОВАНИЕ МИНЕРАЛЬНОЙ ЧАСТИ БУРОГО УГЛЯ КАНСКО-АЧИНСКОГО БАССЕЙНА И КАМЕННОГО УГЛЯ ЭКИБАСТУЗСКОГО БАССЕЙНА ПРИ ИХ ИЗМЕЛЬЧЕНИИ В ДЕЗИНТЕГРАТОРЕ
М. Ю. Чернецкий 1, *, Е. Б. Бутаков 1, **, А. В. Кузнецов 1, ***, А. П. Бурдуков 1, ****
1 ФГБУН Институт теплофизики имени С.С. Кутателадзе СО РАН
630090 Новосибирск, Россия
* E-mail: micch@yandex.ru
** E-mail: e_butakov@mail.ru
*** E-mail: temkansu@yandex.ru
**** E-mail: e_butakov@mail.ru
Поступила в редакцию 15.01.2019
После доработки 13.03.2019
Принята к публикации 02.04.2019
Аннотация
Установлены основные закономерности в преобразовании минеральной части для углей разной степени метаморфизма – бурого угля Канско-Ачинского бассейна и каменного угля Экибастузского бассейна при их измельчении на разных по степени энергонапряженности мельницах. Для бурых углей измельчение в дезинтеграторе приводит к более равномерному распределению минеральных веществ по размерным фракциям и обогащению мелкой фракции компонентами внутренней золы и железосодержащими минералами по сравнению с шаробарабанной мельницей. Измельчение в дезинтеграторе экибастузского угля не приводит к значительным изменениям в распределении минеральных компонент как по размерным фракциям, так и по плотности по сравнению с шаробарабанной мельницей.
Предварительная интенсивная механическая обработка топлива – одна из перспективных технологий в теплоэнергетике, позволяющая значительно повысить реакционную способность топлива [1, 2]. В Институте теплофизики СО РАН проводятся исследования по получению механоактивированного угля, измельченного в мельнице дезинтеграторного типа, и сжиганию его на огневых стендах [3]. Предлагаемая технология сжигания углей обеспечивает розжиг и стабилизацию горения пылеугольного факела без применения высокореакционного газомазутного топлива.
Предварительная интенсивная механическая обработка топлива значительно влияет как на структуру угля, так и на условия сжигания в топочной камере [4, 5]. Подобная обработка существенно сказывается на процессах преобразования минеральной части и осаждения золы. Ранее [6] было исследовано влияние предварительной интенсивной механической обработки в дезинтеграторе на преобразование минеральной части кузнецкого каменного угля. Было установлено значительное влияние на перераспределение минеральных компонент при использовании энергонапряженной мельницы – дезинтегратора по сравнению со стандартными мельницами, используемыми в теплоэнергетике, как по размерным фракциям, так и по плотности. В частности, было установлено насыщение мелких фракций соединениями железа, что может приводить к снижению первичных прочных железистых отложений за счет более быстрого выгорания пирита и преобразования железосодержащих соединений.
Но, как известно, влияние измельчения на распределение минеральной части углей может быть различно [7–10], поэтому актуальным остается вопрос о влиянии измельчения в дезинтеграторе на перераспределение минеральных компонент для углей разной степени метаморфизма.
Цель работы – изучение процесса преобразования минеральной части углей разной степени метаморфизма – бурого угля Канско-Ачинского бассейна и каменного угля Экибастузского бассейна, при их измельчении на разных по степени энергонапряженности мельницах.
ЭКСПЕРИМЕНТАЛЬНАЯ ЧАСТЬ
Угли (табл. 1) подвергали измельчению в шаробарабанной мельнице (ШБМ) и мельнице дезинтеграторного типа (подробное описание данных мельниц и их различия в способе измельчения угольного вещества дано в [6]).
Таблица 1.
Технические характеристики исходного угля
Уголь | W а | Ad | V daf | Cdaf | Hdaf | Sdaf | Odaf | $Q_{s}^{{daf}}$, ккал/кг |
---|---|---|---|---|---|---|---|---|
мас. % | % на daf | |||||||
Бурый | 30 | 12 | 46 | 71.4 | 4.00 | 0.3 | 22.9 | 6230 |
Экибастузский | 7 | 48 | 24 | 80 | 5.1 | 0.7 | 13.7 | 7350 |
Для определения состава продуктов термического преобразования минеральных веществ, а также их количества в разных по размерам частицах был использован метод рентгеноспектрального флуоресцентного анализа [11].
Угольную пробу разделяли по плотности центрифугированием (центрифуга J-15; число оборотов 1500, объем тяжелой жидкости 100 мл, масса пробы 30 г, время центрифугирования 20 мин).
ОБСУЖДЕНИЕ РЕЗУЛЬТАТОВ
Бурый и экибастузский угли имеют существенно различную зольность, отличаются по минеральному составу и разной связанностью минералов с угольным веществом. Минеральная часть экибастузского угля в основном представлена глинистыми минералами. Кальцит и доломит содержится в небольших количествах в виде примесей. Внешняя порода канско-ачинских углей представлена тонкодисперсным кварцем, разнообразными глинистыми минералами. Кальций в углях находится преимущественно в составе органической части в виде гуматов кальция и равномерно распределен по массе угля. Значительные отличия в составе и связанности с органической массой для данных углей определяют и разное влияние измельчения на перераспределение минеральной части угля по размерным фракциям.
На рис. 1–5 представлены результаты РФА для двух типов помола бурого угля. Видно, что при измельчении данного угля на ШБМ наблюдается значительная неравномерность распределения минеральных веществ по размерным фракциям (рис. 1). Обогащение минеральными веществами мелких фракций сопровождается ростом в ней кремния, который в меньшей степени связан с угольным веществом (рис. 2). Также в мелких фракциях повышается содержание алюминия (рис. 3). Соответственно, снижается доля кальцийсодержащих минералов в составе органической части (рис. 4). Это объясняется, в первую очередь, преобладанием во внешней породе углей легко разламываемых минералов, содержащих силикатные и алюмосиликатные формы, в том числе кварц и разнообразные глинистые минералы. Данные компоненты в процессе размола измельчаются значительно быстрее и обогащают мелкие фракции пыли.
Рис. 1.
Распределение доли минеральных веществ во фракциях угольной пыли бурого угля после измельчения в дезинтеграторе (1) и ШБМ (2).
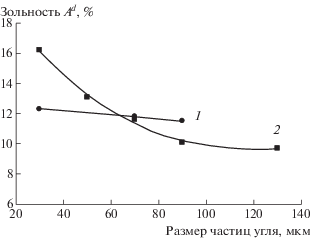
Рис. 2.
Распределение компонента SiO2 во фракциях угольной пыли бурого угля после измельчения в дезинтеграторе (1) и ШБМ (2).
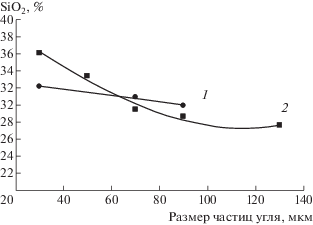
Рис. 3.
Распределение компонента Al2O3 во фракциях угольной пыли бурого угля после измельчения в дезинтеграторе (1) и ШБМ (2).
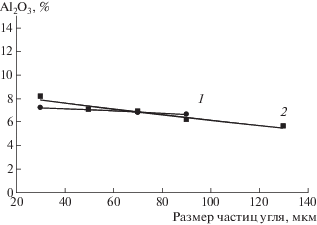
Рис. 4.
Распределение компонента CaO во фракциях угольной пыли бурого угля после измельчения в дезинтеграторе (1) и ШБМ (2).
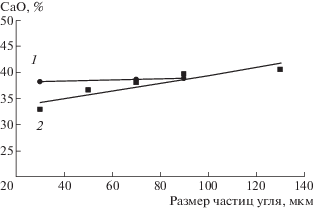
Рис. 5.
Распределение компонента Fe2O3 во фракциях угольной пыли бурого угля после измельчения в дезинтеграторе (1) и ШБМ (2).
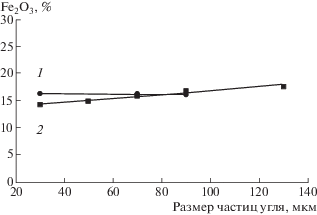
Измельчение в дезинтеграторе приводит к более равномерному распределению неорганической составляющей угля по фракциям (рис. 1). Это связано с тем, что дезинтегратор обладает более интенсивным воздействием на угольное вещество и более эффективным раскрытием органоминеральных сростков, благодаря чему мелкая фракция обогащается такими элементами, как кальцийсодержащие минералы (рис. 4), в большей степени связанных с органической частью угля. Мелкая фракция насыщается железосодержащими минералами (рис. 5), имеющими большую сопротивляемость размолу. При этом за счет обогащения мелкой фракции данными минералами снижается доля кремния и алюминия (рис. 2, 3).
В экибастузском угле минеральная часть, представленная глинистыми тонкодисперсными минералами, плохо отделяется от угольного вещества при измельчении. Это определяет тот факт, что при размоле в ШБМ минеральными веществами обогащается более крупная фракция (рис. 6), хотя для большинства углей, в том числе бурого, наблюдается противоположный результат. Результаты также подтверждаются работами [12, 13], в которых отмечается слабовыраженная зависимость неравномерности распределения состава минеральной части по фракциям для экибастузского угля при размоле в ШБМ.
Рис. 6.
Распределение доли минеральных веществ во фракциях угольной пыли экибастузского угля после измельчения в дезинтеграторе (1) и ШБМ (2).
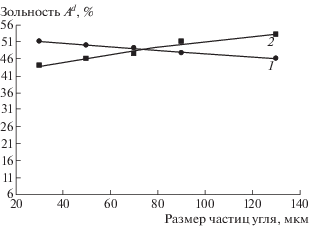
Разделение угольной пыли экибастузского угля на фракции по размерам и проведение для полученных фракций РФА показало, что для угля, измельченного в дезинтеграторе, по сравнению в ШБМ наблюдается:
незначительное обогащение мелкой фракции кварцем (рис. 7) и глинистыми минералами, для которых характерно содержание алюминия (рис. 8);
Рис. 7.
Распределение компонента SiO2 во фракциях угольной пыли экибастузского угля после измельчения в дезинтеграторе (1) и ШБМ (2).
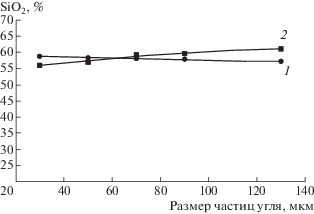
Рис. 8.
Распределение компонента Al2O3 во фракциях угольной пыли экибастузского угля после измельчения в дезинтеграторе (1) и ШБМ (2).
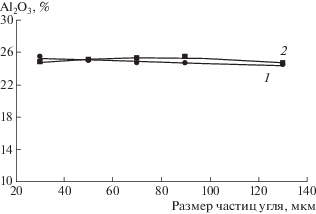
отсутствие значительного влияния на перераспределение кальцийсодержащих минералов (рис. 9) и даже снижение их доли в мелкой фракции, что отличается от ранее исследованных углей;
Рис. 9.
Распределение компонента CaO во фракциях угольной пыли экибастузского угля после измельчения в дезинтеграторе (1) и ШБМ (2).
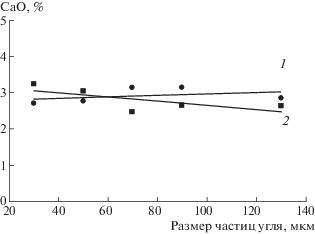
незначительное снижение железосодержащих минералов в мелкой фракции и их увеличение в крупной (рис. 10) после измельчения в дезинтеграторе.
Рис. 10.
Распределение компонента Fe2O3 во фракциях угольной пыли экибастузского угля после измельчения в дезинтеграторе (1) и ШБМ (2).
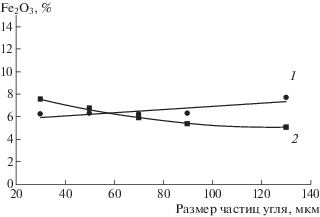
Согласно представлениям [14] о распределении угольного вещества по плотности ρ, во фракции плотностью ≤1600 кг/м3 преимущественно переходят минеральные компоненты, тесно связанные с органической частью, во фракции плотностью 1600–2280 кг/м3 переходят угольно-минеральные сростки, а обособленные минеральные примеси – во фракции плотностью >2280 кг/м3. Для понимания происходящих преобразований в минеральной части угля, после разделения проб по плотности, был выполнен рентгеноспектральный флуоресцентный анализ (РФА) по распределению индивидуальных компонент.
В табл. 2 представлены результаты исследований по разделению угольных проб по плотности для бурого угля. Полученные результаты представлены в виде содержания основных компонентов минеральной части в данной фракции.
Таблица 2.
Распределение минеральных компонентов (%) по фракциям бурого угля
Способ измельчения | Плотность, м3/кг | SiO2 | Al2O3 | Fe2O3 | MgO | CaO | Зольность, % |
---|---|---|---|---|---|---|---|
ШБМ | ≤1400 | 18.0 | 7.6 | 11.0 | 5.9 | 38.6 | 4.2 |
≤1600 | 25.9 | 8.0 | 14.4 | 4.5 | 32.9 | 7.0 | |
≤1800 | 24.9 | 8.3 | 13.9 | 4.7 | 34.3 | 6.8 | |
≤2280 | 47.5 | 4.7 | 40.2 | 0.6 | 2.9 | 60.0 | |
≤2860 | 49.6 | 3.9 | 42.3 | 0.5 | 2.0 | 73.2 | |
Дезинтегратор | ≤1400 | 21.3 | 8.1 | 10.3 | 4.6 | 24.1 | 3.3 |
≤1600 | 31.5 | 7.1 | 12.3 | 4.0 | 37.2 | 6.0 | |
≤1800 | 25.6 | 8.6 | 17.3 | 1.8 | 27.1 | 6.4 | |
≤2280 | 40.2 | 3.2 | 32.4 | 1.5 | 12.5 | 64.2 | |
≤2860 | 45.1 | 3.1 | 36.1 | 1.4 | 11.1 | 76.2 |
Проведенный анализ результатов лабораторных исследований позволил установить, что следствием измельчения в дезинтеграторе бурого угля по сравнению с его измельчением в ШБМ является:
снижение минеральных компонент в легкой фракции (плотность ≤1400 м3/кг);
увеличение доли компонентов, связанных с органической частью угля (СaO, MgO), в тяжелой фракции;
снижение доли компонентов внешней породы (SiO2, Al2O3) в тяжелой фракции и, соответственно, их увеличение в легкой;
снижение доли соединений железа в тяжелой фракции и их увеличение в плотности, характерной для угольно-минеральных сростков (плотность ≤1800 м3/кг).
Учитывая, что дезинтегратор обладает более эффективным раскрытием органоминеральных сростков, можно предположить, что при измельчении в дезинтеграторе происходит отделение части компонент, связанных с органической массой угля, и, соответственно, насыщение тяжелой фракции обособленными минеральными примесями. Это приводит к увеличению доли органической составляющей и снижению минеральных веществ в легкой фракции. Снижение доли компонент внешней породы угля (SiO2, Al2O3) в тяжелой фракции и их увеличение в легкой связано, в первую очередь, с перераспределением доли СaO, MgO в соответствующих фракциях.
Изменение в составе тяжелой фракции, а именно после измельчения в дезинтергаторе, сопровождается уменьшением содержания соединений железа и уменьшением доли органической составляющей. Это означает, что более крупные и тяжелые фракции, содержащие в своем составе в основном минеральные компоненты, а также незначительную долю органических соединений, измельчаются в дезинтеграторе таким образом, что в основном отделяются железосодержащие соединения и органическая составляющая угля.
В табл. 3 представлены результаты исследований по распределению минеральных компонент в разных фракциях по плотности с использованием рентгеноспектрального флуоресцентного анализа (РФА) для проб экибастузского угля. Полученные результаты представлены в виде содержания основных компонентов минеральной части.
Таблица 3.
Распределение минеральных компонентов (%) по фракциям экибастузского угля
Способ измельчения | Плотность, м3/кг | SiO2 | Al2O3 | Fe2O3 | MgO | CaO | Зольность, % |
---|---|---|---|---|---|---|---|
ШБМ | ≤1400 | 65.0 | 19.8 | 1.9 | 0.4 | 5.7 | 8.5 |
≤1600 | 63.4 | 21.6 | 2.1 | 0.5 | 4.3 | 15.9 | |
≤1800 | 62.6 | 23.8 | 1.4 | 0.6 | 1.8 | 27.6 | |
≤2280 | 61.8 | 25.8 | 2.0 | 0.6 | 1.7 | 52.0 | |
≤2860 | 53.1 | 28.0 | 6.5 | 1.8 | 4.9 | 78.8 | |
Дезинтегратор | ≤1400 | 54.6 | 20.5 | 3.0 | 1.4 | 5.7 | 5.1 |
≤1600 | 58.2 | 22.2 | 3.3 | 1.2 | 5.3 | 12.8 | |
≤1800 | 60.5 | 24.8 | 3.5 | 0.7 | 1.4 | 29.5 | |
≤2280 | 62.0 | 25.3 | 4.8 | 0.7 | 1.4 | 49.9 | |
≤2860 | 62.8 | 26.0 | 5.2 | 1.4 | 3.3 | 81.4 |
Следствием измельчения экибастузского угля в дезинтеграторе является:
снижение количества минеральных веществ в легкой фракции;
снижение доли компонент внешней породы угля (SiO2) в легкой фракции и увеличение их в тяжелой.
Распределение по плотности минеральных компонент экибастузского угля после измельчения в дезинтеграторе показывает, что не наблюдается характерного для исследованных углей насыщения тяжелой фракции CaO и даже имеется противоположная тенденция, это связано с прочностью связи минеральных компонент с угольным веществом.
Измельчение в дезинтеграторе экибастузского угля привело к снижению количества минеральных веществ в легкой фракции и увеличению доли компонент внешней породы угля (SiO2) в тяжелой фракции и, соответственно, их снижению в легкой. Это может означать, что дезинтегратор, обладая более эффективным раскрытием органоминеральных сростков, позволяет лучше отделить кремнийсодержащие минералы и обогатить фракцию плотностью >2280 кг/м3, соответствующую обособленным минеральным примесям.
Изменения в распределении железосодержащих соединений, которые содержатся как во внешней породе угля, так и в минеральной части, связанной с органической массой, не имеют значительных изменений и связаны как с отделением вместе с органической составляющей, так и с перераспределением долей других компонент. Незначительное влияние вида измельчения на перераспределения железа можно видеть и по размерным фракциям.
ВЫВОДЫ
Разделение угольной пыли бурого угля на фракции по размерам, проведение для полученных фракций РФА впервые позволило получить сравнительный анализ перераспределения минеральных компонент по размерным фракциям угольной пыли бурого угля при измельчении на дезинтеграторе и шаробарабанной мельнице. Данный анализ показал, что при измельчении в дезинтеграторе по сравнению с ШБМ наблюдается обогащение мелкой фракции компонентами минеральной части, связанными с органической массой угля (кальцийсодержащие минералы) и железосодержащими минералами.
Результаты анализа проб бурого угля разной плотности показали, что измельчение в дезинтеграторе приводит к снижению доли легкой фракции с плотностью <1400 кг/м3, увеличению доли компонентов связанных с органической массой угля (СaO, MgO), и снижению доли компонентов внешней породы угля (SiO2, Al2O3) в тяжелой фракции с плотностью >2280 кг/м3, а также уменьшению содержания железосодержащих минералов и уменьшение доли органической составляющей в тяжелой фракции, по сравнению с измельчением в ШБМ.
Результаты лабораторных исследований проб экибастузского угля после измельчения в дезинтеграторе и ШБМ показали незначительное влияние способа измельчения на перераспределение минеральных компонент как по размерным фракциям, так и по плотности.
Список литературы
Чернецкий М.Ю., Бурдуков А.П. // ФГВ. 2016. Т. 52. № 3. С. 79. [Combustion, Explosion, and Shock Waves, 2016, vol. 52, no. 3, p. 326. DOI: 10.1134/S0010508216030114].https://doi.org/10.15372/FGV20160311
Welham N.J., Chapman P.G. // Fuel Proc. Technol. 2000. V. 68. P. 75.
Burdukov A.P. // Appl. Thermal Eng. 2015. V. 7. P. 174.
Юсупов Т.С., Бурдуков А.П. // ХТТ. 2013. № 4. С. 16. [Solid Fuel Chemistry, 2013, vol. 47, no 4, p. 206. DOI: 10.3103/S0361521913040149]https://doi.org/10.7868/S0023117713040142
Burdukov A.P., Popov V.I., Yusupov T.S., Chernetskiy M.Yu., and Hanjalic K. // Fuel. 2014. V. 122 P. 103.
Чернецкий М.Ю., Кузнецов В.А., Бурдуков А.П., Бутаков Е.Б. // ХТТ. 2018. № 1. С. 32. / [Solid Fuel Chemistry, 2018, vol. 52, no. 1, p. 30. https://doi.org/10.3103/S0361521918010020]https://doi.org/10.7868/S0023117718010073
Шарловская М.С., Пугач Л.И., Лисицин В.В., Скерко Н.Н. // Теплоэнергетика. 1973. № 8. С. 44.
Алехнович А.Н., Талова В.М., Богомолов В.В., Гладков В.Е. // Теплоэнергетика. 2001. № 5. С. 55. [Thermal Engineering, 2001, vol. 48, no. 5. p. 401. https://doi.org/10.1134/S0040601512060018]10.1134/S0040601512060018
Казакова О.А., Заворин А.С., Казаков А.В. // Изв. Томского политехн. ун-та. Инжиниринг георесурсов. 2011. Т. 318. № 4. С. 49.
Заворин А.С., Буваков К.В., Гладков В.Е., Красильникова Л.Г. // Изв. Томского политехн. ун-та. Технические науки. 2006. Т. 309. № 4. С. 123.
Карманова Н.Г., Карманов Н.С. // Матер. VII Всерос. конф. по рентгеноспектральному анализу. 19–23 сентября 2011 г., Новосибирск, 2011. 180 с.
Карякин С.К., Заворин А.С., Блохин П.И., Мурсалимова С.М. // Вопросы сжигания топлив в парогенераторах. Межвуз. сб., Барнаул: АлПИ, 1981. С. 41.
Серант Ф.А., Шарловская М.С., Лисицын В.В., Остапенко В.Е., Константиновна Н.В. // Теплоэнергетика. 1983. № 5. С. 58.
Лебедев Б.В., Заворин А.С. // Изв. Томского политехн. ун-та. 2009. Т. 315. № 4. С. 15.
Дополнительные материалы отсутствуют.
Инструменты
Химия твердого топлива