Химия твердого топлива, 2020, № 2, стр. 3-11
ТЕРМОРАСТВОРЕНИЕ УГЛЕЙ РЯДА МЕТАМОРФИЗМА В СРЕДЕ ТЕТРАЛИНА И АНТРАЦЕНОВОЙ ФРАКЦИИ СМОЛЫ КОКСОВАНИЯ
П. Н. Кузнецов 1, 2, *, Н. В. Перминов 1, Л. И. Кузнецова 1, Ф.А. Бурюкин 2, **, С. М. Колесникова 1, Е. С. Каменский 1, Н. И. Павленко 1
1 ФГБУН Институт химии и химической технологии СО РАН, ФИЦ КНЦ СО РАН
660036 Красноярск, Россия
2 ФГАОУ ВО Сибирский федеральный университет
660041 Красноярск, Россия
* E-mail: kpn@icct.ru
** E-mail: fbur@mail.ru
Поступила в редакцию 16.09.2019
После доработки 01.10.2019
Принята к публикации 25.11.2019
Аннотация
Сопоставлены показатели термического растворения углей различной степени метаморфизма в водородо-донорном растворителе тетралине и антраценовой фракции смолы коксования каменных углей (АФСК). Установлено, что при 380°С зависимость активности углей от стадии метаморфизма имеет экстремальный характер. В среде тетралина максимальную активность показывали низкометаморфизованные каменные угли марок Д и Г с рыхлой надмолекулярной структурой с большим содержанием фрагментов алифатической природы. Полученный продукт представлял вязко-текучую массу. В жидкофазной среде АФСК высокой активностью отличались среднеметаморфизованные коксующиеся каменные угли марок ГЖ и Ж, содержащие повышенное количество плотноупакованных поликонденсированных ароматических молекул. Процесс протекал селективно с образованием пластичных пекоподобных продуктов с температурой размягчения от 76 до 96°С при незначительном образовании газов и дистиллятных фракций.
ВВЕДЕНИЕ
Производство углеродных материалов и композитов на их основе в значительной степени основано на использовании ароматических соединений и их смесей. Потребности в производных моноциклической ароматики обеспечиваются, в основном, нефтехимическими продуктами (на 90%), а в би- и полициклической ароматике преимущественно (на 95%) компонентами коксохимической смолы – побочного продукта производства металлургического кокса. Большую часть современных высокотехнологичных углеродных материалов и композитов получают с использованием поликонденсированных ароматических углеводородов, которые содержатся в нелетучем остатке каменноугольной смолы – каменноугольном пеке.
Металлургический кокс незаменим при доменной плавке чугуна и стали, выполняет ряд важных функций: источника тепла, восстановителя и компонента, обеспечивающего газопроницаемость шихты. Развитие доменной технологии во всем мире направлено на уменьшение расхода кокса, что связано с его высокой стоимостью, значительными выбросами СО2 при его производстве и ограниченными ресурсами качественных коксующихся углей для коксования [1, 2]. К настоящему времени в доменной технологии достигнуто значительное снижение расхода кокса, что привело к сокращению объема его производства (за исключением Китая) и, как следствие, производства побочного продукта каменноугольной смолы [3].
В перспективе увеличение количества доменных печей с вдуванием в горн пылевидного угля, природного газа и нефтяных фракций (в качестве восстановителей для частичной замены кокса), а также масштабное развитие конкурирующих недоменных процессов получения металла, таких, как прямое восстановительное плавление с использованием водорода и природного газа, Corex-процесса и плавки в электродуговых печах приведет к дальнейшему значительному уменьшению потребности в коксе и, следовательно, объемов производства каменноугольной смолы и пека [2].
Потребности в каменноугольной смоле и пеке, требования к их качеству непрерывно возрастают при получении различных углеродных материалов: угольных электродов, углеграфитовых, конструкционных, полупроводниковых материалов, углеродных волокон, интегральных микросхем, для химического аппарато- и машиностроения, электрохимии, атомной энергетики, авиа- и ракетостроения [4]. В настоящее время пек в основном используется в качестве связующего при приготовлении анодов для электролиза алюминия. Планируемое во многих странах увеличение мощностей производства алюминия приведет к еще большей востребованности пека. В контексте этой проблемы необходимо также подчеркнуть, что масштабное применение конкурирующей недоменной технологии плавки в электродуговых печах, осуществляемой с использованием графитизированных электродов, потребует в перспективе значительного количества пека в качестве связующего для их изготовления.
Разнонаправленные тенденции производства и потребления коксохимической смолы и пека характерны для многих стран, что требует разработки способов получения заменителей, минуя процесс коксования. Необходимость решения этой задачи диктуется также рядом других факторов, например наличием высокого содержания в коксохимическом пеке канцерогенных веществ [5].
Возможные альтернативные способы получения поликонденсированных ароматических веществ, включая пеки, рассмотрены в обзорных работах [6–8]. В составе коксующихся каменных углей изначально присутствует некоторое количество пластической битумной массы, состоящей из поликонденсированных ароматических углеводородов. Известен способ их извлечения из нагретого угля с помощью центробежно-фуговального аппарата с фильтрующей перегородкой. Однако для переработки таким способом необходимы дефицитные коксующиеся каменные угли с большим содержанием пластической массы.
Перспективным способом получения поликонденсированных ароматических веществ из углей является процесс их термического растворения в среде растворителей. Исследования отечественных и зарубежных авторов показали, что выход продуктов терморастворения определяется как свойствами растворителя, так и угля [9–17]. Растворители, содержащие частично гидрированные ароматические молекулы, такие как тетралин, обычно проявляют высокую эффективность при повышенной температуре благодаря способности насыщать образующиеся при деструкции радикальные частицы водородом. При температуре 400°С максимальные выходы растворимых продуктов в среде тетралина достигались для каменных углей марок Д, Г и Ж [15]. В среде антраценового масла уголь Д показывал низкую активность в сравнении с более метаморфизованными углями Г, Ж и К [16]. Эффективность терморастворения бурых углей увеличивалась в ряду растворителей 1-метилнафталин < < смесь ПАУ > частично гидрированные ПАУ [12]. Авторы [8] для терморастворения использовали суббитуминозный каменный уголь, а в качестве растворителя – техническую метилнафталиновую фракцию смолы коксования. Выход растворимых продуктов достигал 70%. По данным [18], пеки, выделенные из продуктов терморастворения каменного угля в среде антраценовой фракции смолы коксования, по техническим и структурным показателям были близки к промышленным пекам, приготовленным из смеси коксохимического и нефтяного сырья.
Японскими авторами [19–21] разработан процесс терморастворения суббитуминозных и битуминозных углей при 360–380°С в смеси бициклических ароматических углеводородов с получением обеззоленного пластичного угля, получившего название Hyperсoal. Способ получения альтернативных пековых продуктов, разрабатываемый в США [22], базируется на известном процессе SRC-I. В новой технологии используются битуминозные каменные угли, терморастворение ведут в среде антраценового масла при 400°С [23].
В целом следует отметить, что опубликованные данные по эффективности процесса терморастворения с получением полиароматических пекоподобных продуктов определяются множеством факторов. Зависимости показателей терморастворения от свойств углей и растворителей часто противоречивы, что связано со специфичностью взаимодействий растворителя с различными фрагментами ОМУ, химическая и физическая природа которых остается мало изученной.
В статье приведены данные по определению показателей терморастворения углей в зависимости от стадии метаморфизма. В качестве растворителей использовали активный донор водорода тетралин и высокоароматическую антраценовую фракцию смолы коксования углей.
ЭКСПЕРИМЕНТАЛЬНАЯ ЧАСТЬ
Для исследований были отобраны образцы бурого угля Б2 (Латынцевское месторождение Канско-Ачинского бассейна и каменных углей ряда метаморфизма: обогащенный длиннопламенный Д (Касьяновская обогатительная фабрика, разрез Черемховоуголь), газовый Г (Каа-Хемское месторождение, Тыва), газовый жирный ГЖ (Чаданское месторождение, Тыва), жирный Ж (ш. “Чертинская-Коксовая”, Кузбасс), коксовый К (ООО “Участок Коксовый”, Кузбасс) и концентрат смеси углей Ж + К (обогатительная фабрика, г. Белово, Кузбасс). Все угли относятся к витринитовым. Каменные угли марок Г, ГЖ и Ж обладали способностью спекаться, температура размягчения составляла от 350 до 390°С. В опытах использовали измельченные (фракция менее 1 мм) и высушенные в вакуумном шкафу пробы.
В качестве растворителя использовали тетралин технический с содержанием основного вещества 95% и промышленную антраценовую фракцию смолы коксования (АФСК), предоставленную ОАО “Кокс”.
Элементный анализ углей и продуктов осуществляли на анализаторе FlashEATM1112. Особенности молекулярного состава характеризовали по ИК-спектрам, которые снимали на ИК-Фурье спектрометре Bruker Tensor-27 (Красноярский региональный центр коллективного пользования ФИЦ КНЦ СО РАН). Препараты для съемки готовили в матрице KBr.
Параметры пространственной структуры органической массы углей рассчитывали по дифрактограммам, снятым на дифрактометре PANalytical X’Pert PRO в СuKα-излучении. Обработку дифрактограмм и расчет структурных показателей проводили по методике, описанной в [24].
Процесс терморастворения углей осуществляли на установках, оборудованных автоклавами из нержавеющей стали объемом 80 мл и 2 л, при 380°С и автогенном давлении. Продолжительность реакции при заданной температуре составляла 1 ч. В малый автоклав загружали 4 г угля и 8 г растворителя. Автоклавы продували азотом, проверяли на герметичность и помещали в песочную баню, находящуюся в электрической печи и оборудованную устройством для вращения. Интенсивное вращение песочной бани с реакторами (90 об/мин) обеспечивало эффективный теплообмен между теплоносителем песком и автоклавами и безградиентные условия реакции по температуре и концентрации реагирующих веществ.
По окончании реакции и охлаждения содержимое автоклава переносили на фильтр, который затем помещали в аппарат Сокслета для экстракции толуолом. Толуол-нерастворимую часть экстрагировали хинолином по ГОСТ 10200-83. Конверсию органической массы угля определяли по изменению зольности исходного угля и остатка, нерастворимого в хинолине, и по изменению массы продукта после экстракции. Контрольные определения степени превращения осуществляли также экстракцией автоклавного продукта хинолином. Наблюдалась удовлетворительная сходимость показателей, в статье приведены средние значения.
Для получения продуктов в большем количестве, необходимом для исследования их состава, использовали автоклав объемом 2 л, оборудованный механической мешалкой. Загрузка в автоклав составляла 250 г угля и 500 г растворителя. По окончании процесса температуру в автоклаве снижали до 250°С, парогазовые продукты дросселировали через холодильник в приемники газа и конденсата, а содержимое автоклава в расплавленном виде сливали через нижний патрубок в обогреваемый цилиндр-отстойник, где происходило осаждение твердых частиц (минеральных веществ и угольного остатка). После отстаивания, охлаждения и отделения зольной донной части получали обеззоленный пекосодержащий экстракт.
Образующиеся газообразные продукты анализировали хроматографическим методом. Температуру размягчения твердого продукта определяли по ГОСТ 9950-83 (метод “Кольцо и стержень”).
РЕЗУЛЬТАТЫ И ОБСУЖДЕНИЕ
Характеристика растворителей. В работе использовали тетралин квалификации «технический». В соответствии с паспортными данными он содержал 95% основного вещества, 2.7% нафталина, 2.2% декалина и 0.1% других примесей. Химический состав АФСК (мас. %): углерода 87.6; водорода 5.2; азота, кислорода и серы в сумме 7.2. При программированном нагреве выделение летучих веществ начиналось около 150°С, максимальная скорость потери массы наблюдалась при 290–295°С, практически полное улетучивание достигалось при 350°С.
Молекулярный состав АФСК представлен в основном полициклическими ароматическими углеводородами и гетероциклическими соединениями преимущественно с тремя циклами. По данным [25], в составе антраценовой фракции преобладают фенантрен (20–25%), антрацен (5–6%), нафталин и метилнафталины (около 7%), аценафтен (5%), флуорен (2–3%), пирен (4–6%), другие полиядерные ароматические углеводороды (около 40%), способные выступать в качестве активных переносчиков водорода. Молекулы аценафтена и флуорена содержат атомы водорода, расположенные в альфа-положении к ароматическому кольцу, вследствие чего они обладают повышенной реакционной способностью и могут служить источниками водорода. Гетероциклические азотистые соединения представлены преимущественно карбазолом (5–6%), хинолином и его гомологами (0.5%), кислород-содержащие соединения – производными нафтола (2–3%), сернистые – бензтиофеном и его производными. Указанные гетероциклические соединения обладают сольватирующими свойствами по отношению к компонентам реакционной смеси.
Характеристика углей. Отобранные образцы углей, за исключением угля Б и Д, обладали коксующими свойствами с толщиной пластического слоя от 10 до 30–33 мм и температурой размягчения от 340 до 380°С. Основные показатели состава образцов углей приведены в табл. 1. Выход летучих веществ изменялся от 19.9 до 45.6%, зольность – от 5.6 до 25.9%. Все угли содержали мало серы, низкометаморфизованные угли отличались повышенным содержанием кислорода.
Таблица 1.
Показатели состава и свойств углей
Уголь | $W_{t}^{r}$, мас. % | Аd, мас. % | Vdaf, мас. % | Элементный состав, мас. % на daf | γ*, мм | ||||
---|---|---|---|---|---|---|---|---|---|
С | Н | N | S | О | |||||
Бурый Б | 30.2 | 7.7 | 44.8 | 72.0 | 5.1 | 1.1 | 0.3 | 21.5 | Нет |
Каменный Д | 11.3 | 18.7 | 45.5 | 76.2 | 5.5 | 1.4 | 0.7 | 16.2 | ” |
Каменный Г | 6.5 | 8.2 | 45.6 | 78.0 | 6.2 | 1.2 | 0.3 | 14.3 | 10 |
Каменный ГЖ | 5.8 | 5.6 | 36.3 | 84.7 | 5.5 | 1.3 | 0.6 | 7.9 | 17–20 |
Каменный Ж | 6.5 | 25.9 | 37.5 | 86.0 | 5.8 | 2.7 | 0.5 | 5.0 | 30–33 |
Каменный К | 1.3 | 6.8 | 19.9 | 90.0 | 4.6 | 2.0 | 0.4 | 3.0 | 13 |
Каменный Ж + К | 4.0 | 10.7 | 33.6 | 86.8 | 5.2 | 8.0 | Н.д. |
На рис. 1 приведены ИК-спектры углей, характеризующие особенности молекулярного состава. Во всех спектрах присутствовали полосы поглощения (п.п.) в области 2950–2750 см–1, 1440–1450 см–1 и 1375 см–1, обусловленные, соответственно, валентными и деформационными колебаниями насыщенных С–Н-связей. Полосы в области 3030, 1600 см–1 и в области 700–900 см–1 относятся к ароматическим структурам. Распределение интенсивностей п.п. в области 700–900 см–1 зависело от типа угля, однако их детальное описание, как и полос в области 1000–1300 см–1, затруднено из-за присутствия в углях силикатных и алюмосиликатных минералов с Si–O- и Al–O-связями. В области 1700–1750 см–1 слабое поглощение обусловлено кислородсодержащими группами (карбонильными, карбоксильными и сложноэфирными). В жирном угле эти структуры слабо проявлялись.
Путем разложения спектров в области 2700–3100 см–1 были определены и сопоставлены следующие показатели молекулярного состава углей и растворителя: индекс ароматичности Har по водороду, т.е. доля ароматического водорода по отношению к суммарному содержанию ароматического и алифатического водорода, соотношение CH3/CH2-групп в молекулах. Индекс Har оценивали по отношению интегральной интенсивности п.п. валентных колебаний ароматических С–Н-связей в области 3100–3000 см–1 (Aar) и алифатических С–Н-связей в области 3000–2800 см–1 (Aal). Соотношение CH3/CH2-групп в молекулах определяли по отношению интенсивностей п.п. при 2960 и 2920 см–1. При оценке указанных показателей учитывали [26], что отношение коэффициента экстинкции для валентных колебаний ароматических С–Н-связей к коэффициенту экстинкции для алифатических С–Н-связей для каменных углей составляет в среднем 0.2, а для С–Н-связей в CH2-группах и в CH3-группах – 0.5. Расчет проводили по уравнениям
(1)
${{H}_{{ar}}} = \frac{{{{A}_{{ar}}}{\text{/}}0.2{{A}_{{al}}}}}{{{\text{1}} + {\text{(}}{{A}_{{ar}}}{\text{/0}}{\text{.2}}{{A}_{{al}}})}} \cdot 100\% ,$(2)
${\text{C}}{{{\text{H}}}_{3}}{\text{/C}}{{{\text{H}}}_{2}} = 0.5({{A}_{{2958\;{\text{c}}{{{\text{m}}}^{{ - 1}}}}}}{\text{/}}{{A}_{{2920\;{\text{c}}{{{\text{m}}}^{{ - 1}}}}}}).$С учетом данных по элементному составу были определены также параметры ароматичности по Брауну-Лэднеру fa [27], которые характеризуют долю углерода, находящегося в ароматических структурах.
Примеры разложения ИК-спектров для образцов углей Г, ГЖ, Ж и растворителя АФСК показаны на рис. 2. Полученные численные показатели состава приведены в табл. 2. Видно, что с увеличением стадии углефикации ароматичность углей по Брауну-Лэднеру и индексу ароматичности Нar по водороду увеличивались от 0.64 до 0.71–0.73 и от 0.14 до 0.25–0.26 соответственно. В алифатических фрагментах увеличивалась доля метиленовых групп в сравнении с метильными (отношение СН3/СН2 уменьшалось от 0.21 до 0.12–0.15). Антраценовая фракция АФСК отличалась от углей значительно более высокой ароматичностью и меньшим содержанием метиленовых групп.
Таблица 2.
Показатели молекулярного состава углей и растворителя по данным ИК-спектров
Марка угля | Ароматичность по Брауну-Лэднеру, fa | Индекс ароматичности, Нar | Отношение СН3/СН2 |
---|---|---|---|
Б | 0.64 | 0.14 | 0.21 |
Д | 0.64 | 0.17 | 0.17 |
Г | 0.61 | 0.18 | 0.15 |
ГЖ | 0.71 | 0.26 | 0.12 |
Ж | 0.73 | 0.25 | 0.14 |
Ж + К | 0.71 | 0.20 | 0.15 |
АФСК | 0.96 | 0.90 | 0.25 |
Особенности пространственного строения углей охарактеризованы по данным рентгеновской дифракции в области 2Θ от 7° до 34° и в области от 34° до 52°, обусловленные определенным упорядочением фрагментов органической массы. Широкий рефлекс в области 2Θ от 7° до 34° был разложен на три гауссовых компонента, которые, согласно [24], были отнесены к сравнительно упорядоченной графитоподобной компоненте (Сграф с максимумом при 25°), содержащей упакованные в пачки плоские полиароматические молекулы, и двум малоупорядоченным γ-компонентам, расположенным на периферии (с максимумами при 2Θ около 17°–18° и 8°–11°). Из величины площади под Гауссинами определены относительные содержания соответствующих структур. Полученные данные, приведенные в табл. 3, показывают, что в низкометаморфизованных углях доля неупорядоченных гамма-структур достигала в сумме 70–75%, в угле Ж она уменьшалась до 52%, а доля упорядоченных полиароматических пакетов, соответственно, возрастала до 48%. Доля наименее упорядоченной γ2-компоненты не превышала 13–16%.
Таблица 3.
Состав пространственных структур в углях по данным рентгеновской дифракции
Марка угля | Доля, % | ||
---|---|---|---|
α | γ1 | γ2 | |
Б | 30 | 57 | 13 |
Д | 25 | 63 | 12 |
Г | 36 | 57 | 7 |
ГЖ | 41 | 51 | 8 |
Ж | 48 | 36 | 16 |
Межслоевое расстояние в пакетах графитоподобной компоненты составляло от 3.57 до 3.70 Å. С увеличением степени углефикации число слоев-графенов n в пакетах возрастало от 3.7 в буром угле до 4.4 в жирном, а их диаметр La от 15.1 до 20.1 Å. Малоупорядоченные структуры γ1-компоненты отличались рыхлой упаковкой, среднее расстояние между структурными элементами составляло от 6.1 до 6.8 Å. Можно полагать, что при взаимодействии с растворителем в первую очередь в реакцию могут вовлекаться рыхлые периферийные фрагменты гамма-структур.
Содержание упорядоченной графитоподобной компоненты в определенной степени отражает ароматичность углей. Сопоставление дифракционных данных со степенью ароматичности по Брауну-Лэднеру показывает, что в низкометаморфизованных углях Б и Д только около половины всех ароматических атомов углерода входили в состав пачек графитоподобной компоненты. Остальные находились в составе неупорядоченных и/или малоупорядоченных структур, по-видимому, в форме сильно замещенных и/или малоконденсированных ароматических молекул (моно- и бициклических).
В более метаморфизованном угле Ж основное количество ароматических атомов углерода (около 75%) входило в состав поликонденсированных ароматических молекул и фрагментов, упакованных в пачки графитоподобной компоненты. Наблюдалась определенная корреляция между содержанием упорядоченной графитоподобной компоненты и показателем ароматичности по Брауну-Лэднеру.
Терморастворение углей. Показатели процесса терморастворения углей в тетралине приведены в табл. 4, из которой видно, что после реакции доля хинолин-нерастворимой фракции в углемасляной пасте уменьшалась от 33 до 6.4–16.9%. Наиболее высокую способность к терморастворению проявляли низкометаморфизованные каменные угли Д и Г.
Таблица 4.
Показатели терморастворения углей в тетралине в автоклавах объемом 80 мл
Уголь | Состав продукта в расчете на ОМ пасты, мас. % | Отношение хинолин-нерастворимые/ толуол-нерастворимые |
|
---|---|---|---|
толуол-нерастворимые | хинолин-нерастворимые | ||
Б | 26.0 | 16.9 | 0.65 |
Д | 19.0 | 6.4 | 0.34 |
Г | 19.5 | 7.9 | 0.40 |
ГЖ | 22.8 | 12.9 | 0.56 |
Ж | 21.7 | 11.0 | 0.51 |
В жидкофазной среде АФСК наиболее высокую активность показывали среднеметаморфизованные каменные угли ГЖ и Ж (табл. 5). В полученных продуктах доля веществ, нерастворимых в хинолине, уменьшалась до 9–12%. Более метаморфизованные, как и менее метаморфизованные, угли растворялись значительно хуже.
Таблица 5.
Показатели терморастворения углей в АФСК в автоклавах объемом 80 мл
Уголь | Состав продукта в расчете на ОМ пасты, мас. % | Отношение хинолин-нерастворимые/ толуол-нерастворимые | |
---|---|---|---|
толуол-нерастворимые | хинолин-нерастворимые | ||
Б | 32 | 20 | 0.6 |
Д | 27 | 19 | 0.7 |
Г | 26 | 17 | 0.7 |
ГЖ | 23 | 12 | 0.5 |
Ж | 28 | 9 | 0.3 |
К | 29 | 27 | 0.9 |
Ж + К | 28 | 20 | 0.7 |
На рис. 3 величины конверсии углей, полученные при терморастворении в тетралине и АФСК, сопоставлены в графическом виде в зависимости от стадии метаморфизма. Приведенный рисунок показывает экстремальный характер зависимости: в среде донора водорода тетралина максимальной активностью отличались низкометаморфизованные каменные угли Д и Г, а в среде АФСК – среднеметаморфизованные угли ГЖ и Ж. Добавление Н-донорного тетралина (20%) к АФСК приводило к значительному синергетическому эффекту с величиной конверсии до 95%.
Рис. 3.
Сопоставление величины конверсии углей в среде тетралина и АФСК в зависимости от содержания углерода в углях.
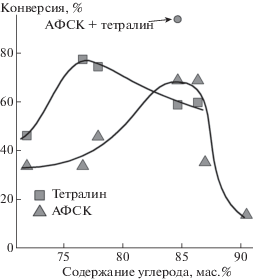
На примере наиболее активного угля ГЖ в опытах с 2-литровым автоклавом был определен материальный баланс процесса терморастворения (табл. 6). Основной продукт терморастворения в среде АФСК представлял при комнатной температуре твердую пластичную пекоподобную массу. Продукт, полученный в тех же условиях в среде тетралина, представлял вязко-жидкую массу.
Таблица 6.
Массовый баланс процесса получения пекосодержащих продуктов в процессе терморастворения угля ГЖ в растворителях (автоклав 2 л, 380°С)
Показатель | Растворитель | |
---|---|---|
АФСК | тетралин | |
Загружено в реактор, г: | ||
сухой уголь | 300 | 400 |
АФСК | 600 | – |
тетралин | – | 800 |
Всего: | 900 | 1200 |
Температура реакции, °С | 380 | 380 |
Рабочее давление, МПа | 1.1 | 3.6 |
Время реакции, ч | 1 | 1 |
Получено, г: | ||
пекосодержащий продукт | 865 | 1150 |
газы | 2.5 | 7.6 |
конденсат | 7.1 | 25 |
Всего | 874.6 | 1182.6 |
Потери: г | 25.4 | 17.4 |
% | 2.8 | 1.5 |
Массовый баланс, % | 97.2 | 98.5 |
В принятых условиях терморастворения образовывалось лишь незначительное количество дистиллятной фракции и газа. В составе образующегося газа преобладал СО2 с небольшим количеством СО, в меньшем количестве присутствовали Н2, Н2S и углеводороды С1–С3 (табл. 7). Потери составляли не более 3%, что связано с налипанием вязкой массы на стенках реактора, отводящих трубках и соединительной арматуре.
Таблица 7.
Выход и состав газообразных продуктов в процессе терморастворения углей в тетралине и АФСК (автоклав 2 л, 380°С)
Уголь, растворитель | Рраб, МПа | Выход газа, мас. % | Состав газа, об. % | |||
---|---|---|---|---|---|---|
CO2 + СО | H2S | H2 | С1–С3 | |||
ГЖ + АФСК (1:2) | 1.4 | 0.3 | 52.6 | 21.6 | 14.7 | 11.1 |
ГЖ + тетралин (1:2) | 3.6 | 0.6 | 69.5 | 9.8 | 13.1 | 7.6 |
Характеристики состава и свойств обеззоленных пекоподобных продуктов, полученных при терморастворении углей Г, ГЖ и Ж в среде АФСК, приведены в табл. 8. Продукт содержал 26–28 мас. % толуол-нерастворимых веществ, 3–8 мас. % хинолин-нерастворимых, углерода 89.2–89.9%, водорода 5.4–5.5%, серы 0.6–0.8%, кислорода 2.2–3.2%, азота от 1.4 до 1.9%.
Таблица 8.
Элементный состав обеззоленных пекосодержащих продуктов, полученных в среде АФСК
Уголь | Групповой состав, мас. % | Элементный состав, мас. % | Тразм, °С | |||||
---|---|---|---|---|---|---|---|---|
нерастворимые в толуоле | нерастворимые в хинолине | С | Н | N | S | Odif | ||
Г | 28 | 8 | 89.2 | 5.5 | 1.4 | 0.7 | 3.2 | 96 |
ГЖ | 27 | 7 | 89.8 | 5.5 | 1.4 | 0.8 | 2.5 | 76 |
Ж | 26 | 3 | 89.9 | 5.4 | 1.9 | 0.6 | 2.2 | 81 |
Пластичная масса продукта имела температуру размягчения от 76 до 96°С. ИК-спектры показывали высокую ароматичность. Параметр Брауна-Лэднера для продукта, полученного из угля ГЖ, составлял 0.90, индекс ароматичности Нar 0.72, что близко к соответствующим значениям 0.88 и 0.69, вычисленным из аддитивного вклада угля и растворителя. Это может указывать на сохранение основных структурных элементов угля при переходе их в раствор без существенного участия процессов глубокой термической деструкции. Учитывая, что газообразные продукты содержали преимущественно СО2 при незначительном количестве других газов и дистиллята, можно полагать, что в среде АФСК пекоподобные продукты образовывались, в основном, за счет нарушения межмолекулярной ассоциации и сольволизной деполимеризации наиболее слабых мостиковых С–О- и С–С-связей между полиароматическими фрагментами.
ЗАКЛЮЧЕНИЕ
Реакционная способность углей при терморастворении как в среде донора водорода тетралина, так и в жидкофазной среде антраценовой фракции смолы коксования находится в экстремальной зависимости от стадии углефикации.
В среде тетралина наиболее высокую активность проявляли низкометаморфизованные каменные угли – длиннопламенный и газовый – с рыхлой надмолекулярной структурой, содержащей значительное количество алифатических и кислородных соединений.
В среде полифункционального ароматического растворителя АФСК наиболее высокая степень растворения достигалась для коксующихся углей ГЖ и Ж средней стадии метаморфизма, имеющих невысокую температуру размягчения и содержащих плотноупакованные поликонденсированные ароматические молекулы и повышенное количество пластической массы.
Жидкофазный процесс терморастворения в среде АФСК при температуре 380°С характеризуется высокой селективностью в образовании пекоподобного пластичного продукта с температурой размягчения 76–96°С. Выход газов не превышал 0.3%, светлых дистиллятов 1.0%. Образование пекоподобного продукта происходит, в основном, за счет нарушения межмолекулярной ассоциации ОМУ и сольволизного расщепления наиболее слабых мостиковых С–С- и С–О-сшивок между крупными полиароматическими фрагментами.
Список литературы
How is Steel Produced? // World Coal Association. 2016. https://www.worldcoal.org/coal/uses-coal/how-steel-produced (Accessed: 20.02.2017).
Tiwari H.P., Saxena V.K. Industrial perspective of the coke making technologies // New Trends in Coal Conversion: Combustion, Gasification, Emissions, and Coking / Ed. by I. Suarez-Ruiz, M Diez., F. Rubiera. Publisher: Woodhead Publishing, 2018. P. 203.
Snape C.E. Liquid Fuels and Chemical Feedstocks // Coal in the 21st Century: Energy Needs, Chemicals and Environmental Controls / Ed by R.E. Hester, R.M. Harrison. London: The Royal Society of Chemistry, 2017. P. 173.
Бейлина Н.Ю., Петрович Н.И., Селезнев А.Н., Свиридов А.А. // ХТТ. 2005. № 4. С. 54.
Sidorov O.F. // Coke and Chemistry. 2013. V. 56. № 2. P. 63. https://doi.org/10.3103/S1068364X13020063
Кузнецов П.Н., Кузнецова Л.И., Бурюкин Ф.А, Маракушина Е.Н., Фризоргер В.К. // ХТТ. 2015. № 4. С. 16. doi.org/ [Solid Fuel Chemistry, 2015, vol. 49, no. 4, p. 213. DOI:doi.org/10.3103/S0361521915040059]https://doi.org/10.7868/S0023117715040052
Андрейков Е.И. // Химия в интересах устойчивого развития. 2016. Т. 24. С. 317.
Rahman M., Pudasainee D., Gupta R. // Fuel Proc. Tech. 2017. V. 158. P. 35.
Станкевич В.В., Демидова А.И., Рогайлин М.И., Фарберов И.Л., Сенина О.Е. // ХТТ. 1976. № 5. С. 108.
Griffith J.M., Clifford C.E., Rudnick L.R., Schobert H.H. // Energy and Fuels. 2009. V. 23. P. 4553.
Derbyshire F.J., Whitehurst D.D. // Fuel. 1981. V. 60. P. 655.
Rahman M., Samanta A., Gupta R. // Fuel Proc. Tech. 2013. V. 115. P. 88.
Sakimoto N., Koyano K., Takanohashi T. // Energy Fuels. 2013. V. 27. № 11. P. 6594.
Shui H., Zhao W., Shan C., Shui T., Pan C., Wang Z., Lei Z., RenS., Kang S. // Fuel Proc. Tech. 2014. V. 118. P. 64.
Дьякова М.К., Мелентьева Н.В. // Журн. прикл. химии. 1943. Т. ХVI. № 7–8. С. 296.
Забавин В.И. Каменные и бурые угли. М.: Наука, 1964. 195 с.
Shui H., Zhou Y., Li H., Wang Z., Lei Z., Ren S., Pan C., Wang W. // Fuel. 2013. V. 108. P. 385.
Kuznetsov P.N., Kamenskiy E.S., Kuznetsova L.I. // Energy and Fuels. 2017. V. 31. P. 5402.
Yoshida T., Li C., Takanohashi T., Matsuda A., Saito I. // Fuel Proc. Tech. 2004. V. 86. P. 61.
Hamaguchi M., Okuyama N., ShishidoT., Sakai K., Komatsu N., Kikuchi N., Inoue T., Koide J., Kasahara H. // Light Metals. 2012. P. 1219.
Takanohashi T., Shishido T., Saito I. // Energy Fuels. 2008. V. 22. P. 1779.
Andrews R., Rantell T., Jacques D., Hower J., Gardner J., Amick M. // Fuel. 2010. V. 89. P. 2640.
Stansberry P.G., Zondlo J.W., Wombles R.H. // Light Metals. 2001. P. 581.
Скрипченко Г.Б. // ХТТ. 2009. № 6. С. 7 [Solid Fuel Chemistry, 2009, vol. 43, no. 6, p. 333. DOI:doi.org/10.3103/S0361521909060019]
Павлович О.Н. Состав, свойства и перспективы переработки каменноугольной смолы: Учебное пособие. Екатеринбург: ГОУ ВПО УГТУ-УПИ, 2006. 41 с.
Solomon P., Carangelo R. // Fuel. 1988. V. 67. C. 949.
Brown J.K., Ladner W.R. // Fuel. 1960. V. 39. P. 87.
Дополнительные материалы отсутствуют.
Инструменты
Химия твердого топлива