Химия твердого топлива, 2020, № 2, стр. 61-65
ДВУХСТАДИЙНАЯ ТЕРМИЧЕСКАЯ КОНВЕРСИЯ СОЛОМЫ И БАГАССЫ САХАРНОГО ТРОСТНИКА С ПОЛУЧЕНИЕМ СИНТЕЗ-ГАЗА
В. М. Зайченко 1, *, А. Ю. Крылова 1, **, Ю. М. Фалеева 1, ***
1 ФГБУН Объединенный институт высоких температур РАН (ОИВТ РАН)
125412 Москва, Россия
* E-mail: zaitch@oivtran.ru
** E-mail: aykrylova@yandex.ru
*** E-mail: faleeva.julia@mail.ru
Поступила в редакцию 04.10.2019
После доработки 11.10.2019
Принята к публикации 25.11.2019
Аннотация
Изучены особенности получения синтез-газа двухстадийной термической конверсией сельскохозяйственных отходов растительного происхождения (соломы и багассы сахарного тростника). Установлено, что метод позволяет получать 1.21–1.24 м3 синтез-газа из 1 кг исходного сырья. Теплота сгорания полученного газа составляет 10.6–11.0 МДж/м3, выход биоугля – 26.46–29.90% от исходной массы сырья.
Одна из важнейших задач современности – это использование новых эффективных источников энергии, поскольку ресурсы ископаемого топлива не безграничны. В этой связи актуально использование возобновляемых источников энергии, доступных повсеместно. К таким источникам относится, в частности, биомасса (прежде всего, отходы растительного и животного происхождения, твердые бытовые отходы).
Сельскохозяйственные отходы, которые образуются ежегодно в больших количествах, являются одним из основных источников биомассы. Растениеводство – ведущая отрасль сельского хозяйства в России. Производство зерновых культур связано с образованием значительного количества отходов в виде стерни и соломы, которые остаются на полях после сбора урожая. Стерня представляет собой нескошенные нижние части стебля и корни. Скошенная масса обмолачивается и разделяется на зерно и солому. Утилизация послеуборочных остатков связана с дополнительными финансовыми и временными затратами, а также требует специальных технологий. В России данная проблема традиционно решается методом простого сжигания. Исследования показали, что сжигание стерни и соломы приводит к уничтожению полезной почвенной микрофлоры и запасов гумуса, приводит к изменению физико-химических свойств и механической структуры почвы. При сжигании стерни и соломы с каждого гектара земли теряется до 4 т органического вещества и до 30 кг азота [1]. Кроме того, при сжигании этих отходов в атмосферу выбрасывается значительное количество сажи, которая представляет собой аэрозольную смесь мелких частиц, образующихся при неполном сгорании биомассы [2]. Установлено, что сажа удерживает в несколько сотен раз больше тепла, чем CO2. Поступая в атмосферу, она поглощает солнечную энергию и излучает инфракрасную радиацию, что приводит к усилению эффекта изменения климата Арктики [3]. Сажа, оседающая на арктический снег и лед, снижает их отражающую способность и ускоряет таяние. Помимо влияния на изменение климата сажа оказывает негативное воздействие на здоровье человека [2]. Также стоит отметить, что сжигание послеуборочных остатков является нарушением федеральных законов “Об охране окружающей среды” и “Об охране атмосферного воздуха” [4, 5]. Согласно пункту 218 Правил противопожарного режима в Российской Федерации: “Запрещается выжигание сухой травянистой растительности, стерни, пожнивных остатков (за исключением рисовой соломы) на землях сельскохозяйственного назначения и землях запаса, разведение костров на полях” [6].
По данным Росстата, последние несколько лет производство пшеницы в России превышает 60% от общего валового сбора всех зерновых культур. В 2017 г. посевная площадь под озимую пшеницу составила около 15 млн га земли, под яровую пшеницу – 13 млн га земли. При этом урожайность озимой и яровой пшеницы после доработки составила 85.9 млн т [7]. Соотношение массы зерна и массы соломы у озимой пшеницы составляет примерно 1:1.5, у яровой пшеницы – 1:1.3 [8]. Основываясь на данных об урожайности, нетрудно посчитать, что за 2017 г. образовалось около 98 млн т пшеничной соломы. Энергетический потенциал соломы 14 МДж на 1 кг сухой массы. Для сравнения, объем добычи бурого угля в Канско-Ачинском бассейне в 2017 г. составил 38.35 млн т [9]. Теплота сгорания бурого угля 11 МДж/кг, в брикетах – 13–25 МДж/кг. Таким образом, на полях ежегодно сжигается ресурс, по объему сопоставимый с добычей угля в одном из крупнейших буроугольных бассейнов России. Однако следует отметить, что использование соломы в качестве энергетического топлива связано с рядом трудностей, обусловленных, в частности, ее низкой насыпной плотностью и высокой влажностью. Стоит отметить, что также существуют соломенные котлы, предназначенные для отопления сжиганием целых тюков соломы.
Наряду с растительными остатками от производства зерновых культур, сельскохозяйственные отходы включают в себя побочные продукты промышленной обработки сельскохозяйственной продукции. К таким отходам относится багасса – волокнистая часть сахарного тростника, остающаяся после прессования стеблей и извлечения сахаросодержащего сока. Ежегодное мировое производство сахарного тростника составляет 1.6 млрд т, в результате чего образуется несколько сотен миллионов тонн багассы [10]. Бразилия является крупнейшим производителем сахарного тростника в мире с годовым объемом производства 690 млн т [11]. В среднем на 100 т измельченного тростника производится около 30 т влажных отходов (около 50% влажности) в год. Таким образом, на каждые 3 кг измельченного тростника приходится 1 кг багассы [12]. ЮАР является крупнейшим в Африке производителем сахарного тростника, где ежегодно производится около 3.3 млн т сырой багассы. В развитых странах (США, Бразилия, Индия) багассу используют в промышленности для производства этанола второго поколения. Но в большинстве случаев стратегия по управлению отходами в странах-производителях сахара отсутствует, и багассу складируют на территориях сахарных заводов, занимая полезные площади. Утилизацию багассы обычно проводят методом прямого сжигания в печах для выработки тепла и энергии для собственного потребления сахарных предприятий.
Сжигание багассы (как и соломы) в энергетических целях сопряжено с рядом трудностей. Целесообразным способом использования различных видов биомассы для энергетических целей является переработка исходного сырья в энергетический высококалорийный газ, а затем его использование в качестве топлива.
Существующие методы термической конверсии биомассы, такие как газификация и пиролиз, не позволяют получить газ, который может быть использован в электропроводящем оборудовании. Производимый по данным технологиям газ содержит жидкую фракцию, что недопустимо при использовании в газопоршневых установках. Техническими условиями на эксплуатацию газопоршневых двигателей максимальное содержание смол в газовом топливе лимитировано 50 мг/м3. Использование схем с очисткой газа от жидкой фракции перед подачей в газопоршневую электростанцию требует значительного усложнении и удорожания процесса.
В настоящей работе для утилизации соломы и багассы сахарного тростника с получением синтез-газа использован метод двухстадийной термической конверсии биомассы, разработанный в Объединенном институте высоких температур (ОИВТ) РАН [13]. Сущность метода заключается в том, что процесс разделен на два этапа. На первой стадии перерабатываемое сырье подвергается пиролизу с получением биоугля и парогазовой смеси (ПГС), представляющей собой смесь летучих продуктов пиролиза и неконденсируемых газов. Вторая стадия – газификация при 1000°C полученного на первой стадии биоугля под воздействием ПГС как окислителя с образованием водорода и окиси углерода. В отличие от традиционного процесса газификации, данный метод термохимической конверсии не требует подвода извне окислительного агента: газификация биоугля осуществляется с использованием окислителя, полученного in situ, т.е. внутри процесса. Таким образом, двухстадийная термическая конверсия соответствует принципам зеленой химии, согласно которым следует минимизировать отходы и подачу дополнительных реагентов и материалов в технологический цикл. Получаемый по разрабатываемой технологии газ содержит малое количество жидкой фазы (не более 30–40 мг/м3). Преимущество этой технологии заключается в высокой степени конверсии исходного сырья в синтез-газ и возможности использования полученного газа в качестве топлива для энергопроизводящего оборудования.
В статье представлены результаты исследования двухстадийного пиролиза двух материалов: багассы и соломы. Багасса была предоставлена сахарной компанией Lugazisugarfactory (Кампала, Уганда). Соломенные пеллеты произведены на заводе “Продмаш” (Ростов-на-Дону, Россия). Перед проведением экспериментов образцы двух материалов были высушены при температуре 105 ± 5°C до влажности 0–1%.
На рис. 1 представлена схема экспериментальной установки, реактор которой выполнен из стали 12Х18Н10Т в виде трубы диаметром 37 мм и высотой 850 мм. В зонах пиролиза и газификации установлены чаши, плотно прилегающие к стенкам трубы и имеющие перфорацию в днище для газопроницаемости.
Рис. 1.
Схема лабораторной установки: 1 – двухсекционная печь, 2 – зона пиролиза реактора, 3 – зона газификации реактора, 4 – холодильник, 5 – газосчетчик барабанный, 6 – газгольдер, 7 – газовый анализатор.
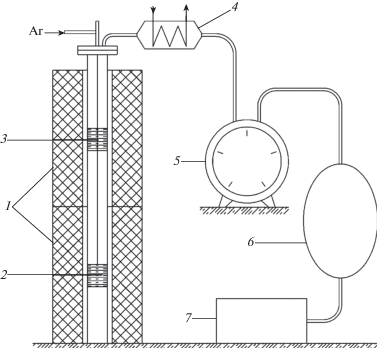
В нижнюю чашу (зона пиролиза) помещалось исходное сырье, в верхнюю (зона газификации) – биоуголь, предварительно прогретый в инертной среде при 1050°C. Реактор размещен в двухсекционной печи, оборудованной двумя автономными нагревателями. Перед экспериментом установку продували аргоном для обеспечения инертной среды. В начале эксперимента зону крекинга нагревали до температуры 1000 ± 5°C, которую поддерживали далее на постоянном уровне. Установку еще раз продували аргоном, поддерживая температуру 105°C в нижней секции. Затем температуру в зоне пиролиза повышали до 1000°C со скоростью 7°C/мин.
Температуру контролировали при помощи термопар. В холодильнике продукты реакции охлаждались и поступали в барабанный счетчик с жидкостным затвором (РГ7000). Состав газовой смеси определяли с помощью анализатора газа Vario Plus Industrial (MRU GmbH, Германия).
В ходе исследований был проведен элементный анализ исходного сырья с использованием элементного анализатора Vario Macro Cube (Elementar Analysensysteme GmbH, Германия). Зольность образцов определяли в соответствии с ГОСТ Р 56881-2016.
В табл. 1 приведены основные теплотехнические характеристики исследуемых материалов в пересчете на сухое состояние: элементный состав, зольность и теплота сгорания.
Таблица 1.
Теплотехнические характеристики исходного сырья
Исходное сырье | Элементный состав и зольность*, % | Теплота сгорания, МДж/кг | |||||
---|---|---|---|---|---|---|---|
C | H | N | S | O** | Ash | $Q_{{{\text{низш}}}}^{{{\text{***}}}}$ | |
Багасса | 41.48 | 5.14 | 0.36 | 0.06 | 51.10 | 1.86 | 13.79 |
Солома | 45.55 | 6.45 | 0.32 | 0.08 | 40.53 | 7.07 | 17.68 |
Как следует из данных, представленных в табл. 1, элементный состав багассы и соломы заметно различается по содержанию кислорода и углерода, которое составляет 51.10 и 41.48% для багассы и 40.53 и 45.55% для соломы соответственно. Количество водорода в багассе и соломе отличалось меньше и было равно 5.14 и 6.45% соответственно. В результате соломенные пеллеты обладали большей теплотой сгорания, несмотря на высокое содержание золы (в 3.8 раза больше, чем у багассы).
В табл. 2 представлены основные теплотехнические характеристики биоугля, полученного в результате высокотемпературного пиролиза биомассы: элементный состав, зольность, теплота сгорания, выход (отношение массы твердого остатка в зоне пиролиза к массе исходного сырья в пересчете на сухое состояние), углеродная эффективность (количество углерода, перешедшего из сырья в биоуголь) и энергетическая эффективность (отношение теплоты сгорания биоугля к теплоте сгорания сырья, помноженное на выход).
Таблица 2.
Основные теплотехнические характеристики биоугля
Исходное сырье | Элементный анализ и зольность*, % | Теплота сгорания, МДж/кг | Выход, % | УЭ, % | ЭЭ, % | |||||
---|---|---|---|---|---|---|---|---|---|---|
C | H | N | S | O** | Ash | $Q_{{{\text{низш}}}}^{{{\text{***}}}}$ | ||||
Багасса | 90.15 | 0.15 | 0.27 | 0.27 | 2.13 | 7.03 | 30.51 | 26.46 | 57.51 | 58.54 |
Солома | 74.62 | 0.66 | 0.59 | 0.19 | 0.29 | 23.65 | 25.97 | 29.90 | 48.98 | 43.92 |
Можно видеть, что выход биоугля из багассы и соломенных пеллет составляет 26.46 и 29.90% соответственно (табл. 2). Это означает, что при переработке данным методом 1 т багассы или соломенных пеллет будет образовываться 260–300 кг биоугля. Полученный биоуголь можно использовать для газификации. Таким образом, будет организован замкнутый процесс без добавления окислителя и дополнительного биоугля. Как видно из табл. 2, углеродная и энергетическая эффективность термической переработки багассы составляют 57.51 и 58.55%, в то время как для соломы аналогичные показатели равны 48.98 и 43.92% соответственно. Это связано с низким содержанием углерода в биоугле из соломенных пеллет по сравнению с биоуглем, полученным из багассы (74.62 и 90.15% соответственно).
В табл. 3 приведены результаты двухстадийной термической конверсии багассы и соломы: компонентный состав полученного синтез-газа, его выход, теплота сгорания и энергетическая эффективность (ЭЭ) процесса, которая рассчитана как отношение теплоты сгорания газа, полученного из 1 кг исходного сырья, к теплоте сгорания исходного сырья.
Выход синтез-газа, полученный при термической конверсии двух материалов оказался приблизительно одинаковым (табл. 3). Установлено, что полученная смесь газов на 96–98% состоит из водорода и оксида углерода. Однако соотношение этих газов несколько отличается: в синтез-газе, полученном при переработке багассы и соломенных пеллет, отношение H2/CO = 0.93 и 1.20, соответственно, т.е. использование соломы позволяет получать синтез-газ, заметно более богатый водородом (46 и 53% соответственно). Низшие теплоты сгорания синтез-газа, полученного из соломы и багассы, оказались близкими по значению (10.63 и 11.03 МДж/м3 соответственно).
Следует отметить, что энергетическая эффективность двухстадийной термической конверсии багассы приближалась к единице и была существенно выше аналогичного показателя для соломы (табл. 3). Это свидетельствует о том, что почти вся внутренняя энергия багассы при ее переработке данным методом переходит в тепловую энергию синтез-газа.
На рис. 2 показана зависимость выхода синтез-газа, полученного из багассы и соломы, от температуры в зоне пиролиза. Можно видеть, что наибольшая интенсивность газообразования наблюдается в области 250–400°C. Этот интервал соответствует разложению гемицеллюлозы и целлюлозы [14].
Рис. 2.
Выход синтез-газа в зависимости от температуры в зоне пиролиза при двухстадийной термической конверсии багассы (1), соломы (2).
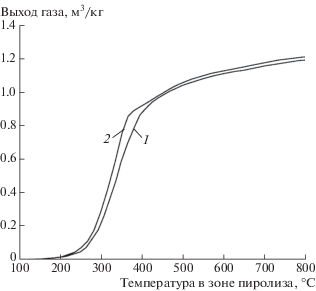
Таким образом, переработка методом двухстадийной термической конверсии соломы или багассы сахарного тростника позволяет получать более 1.2 м3 синтез-газа, на 96–98% состоящего из водорода и окиси углерода, с теплотворной способностью около 11 МДж/м3. Полученный синтез-газ можно использовать как для выработки электроэнергии, так и для получения жидких химических веществ преимущественно топливного назначения.
Несмотря на различные климатические зоны произрастания таких сельскохозяйственных культур, как пшеница и сахарный тростник, они имеют одно важное сходство: их растительные остатки являются распространенными и дешевыми органическими отходами. Предложенный метод их утилизации с точки зрения экономики и влияния на природное равновесие наиболее выгодный и безопасный по отношению к прямому сжиганию на полях.
Список литературы
Сельскохозяйственные сжигания в России: регулирование, мониторинг и подходы к их сокращению // Bellona. 2017. Интернет ресурс: bellona.ru.
Evans M., Kholod N., Kuklinski T., Denysenko A., Smith S.J., Staniszewski A., Hao W.M., Liu L., Bond T.C. // Atmos. Environ. 2017. V. 163. P. 9. https://doi.org/10.1016/j.atmosenv.2017.05.026
Морозова И.А., Игнатьева Ю.С. Пилотные оценки выбросов черного углерода в арктической зоне российской федерации // 2017. Интернет ресурс: nii-atmosphere.ru.
Федеральный закон от 10.01.2002 № 7-ФЗ “Об охране окружающей среды”.
Федеральный закон от 04.05.1999 № 96-ФЗ “Об охране атмосферного воздуха”.
Постановление Правительства РФ от 25.05.2012 N 390 “О противопожарном режиме”.
Россия в цифрах. 2018 // Крат. стат. сб. М.: Росстат, 2018. 102 с.
Михалев С.С., Хохлов Н.Ф., Лазарев Н.Н. Кормопроизводство с основами земледелия. М.: НИЦ ИНФРА-М, 2015. Гл. 10.3. 352 с.
Таразанов И.Г. //Уголь. 2018. № 3. С. 58. https://doi.org/10.18796/0041-5790-2018-3-58-73
Ray R.C., Ramachandran S. Bioethanol Production from Food Crops. Academic Press, 2019. Ch. 10. 460 p.
David G.F., Justo O.R., Perez V.H., Garcia-Perez M. // J. Anal. Appl. Pyrolysis. 2018. V. 133. P. 246. /https://doi.org/10.1016/j.jaap.2018.03.004
Anukam A., Mamphweli S., Reddy P., Meyer E., Okoh O. // Renewable Sustainable Energy Rev. 2016. V. 66. P. 775. https://doi.org/10.1016/j.rser.2016.08.046
Батенин В.М., Бессмертных А.В., Зайченко В.М., Косов В.Ф., Синельщиков В.А. // Теплоэнергетика. 2010. № 11. С. 36–42 [Thermal Engineering, 2010, vol. 57, no. 11, pp. 946–952] DOI: 10.1134/S0040601510110066].
Yang H., Yan R., Chen H., Lee D.H., Zheng C. // Fuel. 2007. V. 86. P. 1781. https://doi.org/10.1016/j.fuel.2006.12.013
Дополнительные материалы отсутствуют.
Инструменты
Химия твердого топлива