Химия твердого топлива, 2021, № 5, стр. 38-44
ВЛИЯНИЕ СПОСОБА ПОЛУЧЕНИЯ БИОУГЛЯ ИЗ ТОРФА И ОПИЛА НА ЕГО СОСТАВ И ТЕПЛОФИЗИЧЕСКИЕ ХАРАКТЕРИСТИКИ
К. О. Крысанова 1, *, А. Ю. Крылова 1, **, Я. Д. Пудова 2, ***, М. В. Куликова 1, ****
1 ФГБУН Ордена Трудового Красного Знамени Институт нефтехимического синтеза имени А.В. Топчиева РАН (ИНХС РАН)
119991 Москва, Россия
2 ФГБУН Объединенный институт высоких температур РАН (ОИВТ РАН)
125412 Москва, Россия
* E-mail: k_krysanova@ips.ac.ru
** E-mail: aykrylova@yandex.ru
*** E-mail: pudova.y.d@mail.ru
**** E-mail: m_kulikova@ips.ac.ru
Поступила в редакцию 17.02.2021
После доработки 19.04.2021
Принята к публикации 02.06.2021
Аннотация
Изучено влияние температуры гидротермальной карбонизациии торрефакции на свойства биоугля, полученного из опила и торфа. Установлено, что для обоих процессов с повышением температуры снижается выход биоугля, возрастают степень деоксигенации, количество углерода в биоугле и его теплотворные способности. В процессе термической обработки биомассы обоими способами полностью разрушаются гемицеллюлозы и частично целлюлоза, вследствие чего в биоугле преобладает лигнин. При этом гидротермальная карбонизация оказывает большее воздействие на сырье, о чем свидетельствует большая степень разрушения целлюлозы в сырье, а также более высокие теплотворные способности получаемого биоугля.
ВВЕДЕНИЕ
Начало XXI века ознаменовалось бурным развитием технологий переработки вторичной биомассы – различных органических отходов, прежде всего отходов сельского хозяйства (соломы, рисовой и подсолнечной шелухи, багассы и т.д.), а также деревообрабатывающей промышленности (опил) и торфа. Этот всплеск объясняется необходимостью утилизации постоянно возрастающих многотонных отходов и жесткими требованиями к снижению выбросов оксидов углерода. Для переработки биомассы широко используются термические методы (сжигание, газификация, пиролиз и т.п.). Хорошо известно, что топливо, полученное из биомассы, в отличие от ископаемого, не нарушает общий баланс углекислого газа в атмосфере, что в будущем позволит сдерживать интенсивный рост концентрации СО2.
Перспективными методами переработки биомассы являются торрефакция и гидротермальная карбонизация (ГТК), использующиеся как способы облагораживания биомассы с целью улучшения условий ее хранения и транспортировки, а также теплотехнических характеристик. Особенностью этих процессов являются мягкие условия, что позволяет благоприятно влияет на общую экономику термической обработки.
Торрефакция – низкотемпературный пиролиз, протекающий при температурах от 200 до 300°С, используется в основном для обуглероживания растительного сырья (в частности, топливных пеллет) [1]. Как и все виды пиролиза, процесс протекает в анаэробных условиях при давлении чуть выше атмосферного. Однако для реализации процесса требуется предварительная сушка сырья до 10–15%-ной влажности, что является затруднительным с экономической точки зрения, учитывая высокую изначальную влажность биомассы, которая может достигать 80 и даже 90%.
Гидротермальная карбонизация – современный способ облагораживания различных видов биомассы, направленный на достижение теплотехнических показателей, сравнимых с характеристиками бурых углей [2]. Процесс протекает при температурах от 180 до 280°С в присутствии воды и без доступа воздуха [3]. Основным преимуществом гидротермальной карбонизации в отличие от торрефакции является возможность перерабатывать биомассу, имеющую высокую влажность, в том числе осадки сточных вод и отходы животноводства [4].
Биоуголь, полученный как торрефакцией, так и гидротермальной карбонизацией, отличается высокими теплотехническими показателями и гидрофобностью. Последнее положительно влияет на условия хранения и транспортировку получаемого топлива, что делает его пригодным для длительных перевозок и экспорта.
В настоящей работе представлены результаты исследования по влиянию температуры на состав и свойства биоугля, полученного торрефакцией и гидротермальной карбонизацией древесных опилок и низинного торфа.
ЭКСПЕРИМЕНТАЛЬНАЯ ЧАСТЬ
В качестве сырья для получения биоугля были использованы низинный торф и опилки деревьев лиственных пород, предварительно высушенные в сушильном шкафу при 105°С до влажности 5 ± 0.5%. В табл. 1 представлены теплотехнические характеристики сырья.
Таблица 1.
Теплотехнические характеристики исследуемого сырья
Сырье | Зольность, % | Элементный состав, мас. % | Теплота сгорания, МДж/кг | |||||
---|---|---|---|---|---|---|---|---|
C | H | N | S | O | низшая | высшая | ||
Торф | 25.5 | 27.28 | 3.31 | 1.57 | 0.25 | 42.09 | 8.09 | 8.84 |
Опилки | 0.54 | 48.78 | 5.85 | 0.11 | 0.25 | 44.47 | 17.74 | 19.06 |
Принципиальная схема лабораторной установки для изучения гидротермальной карбонизации представлена на рис. 1.
Рис. 1.
Схема лабораторной установки для осуществления процесса гидротермальной карбонизации опила: 1 – реактор, 2 – муфельная печь, 3 – датчик давления, 4 – термопара, 5 – считывающее устройство, 6 – ЛАТР, 7 – вентиль.
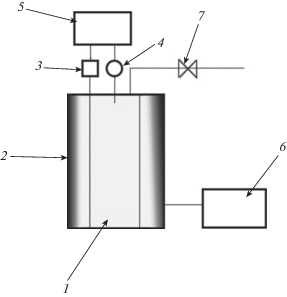
Перед началом эксперимента 30 г сырья смешивали с водой в пропорции 1:5 (по объему) и загружали в реактор, который продували азотом для создания инертной среды. Реактор нагревали до заданной температуры (190–230°С), выдерживали в изотермическом режиме 4 ч и охлаждали. Полученный твердый остаток (биоуголь-карбонизат) отфильтровывали и высушивали до постоянной массы.
Принципиальная схема лабораторной установки для исследования процесса торрефакции представлена на рис. 2.
Рис. 2.
Схема лабораторной установки для исследования процесса торрефакции: 1 – трубчатая печь, 2 – электронный регулятор, 3 – цилиндрический реактор, 4 – чаша с материалом, 5 – термометр.
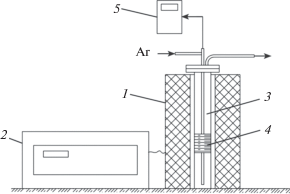
В чашу реактора помещали сырье массой 9 г. Реактор продували азотом для создания инертной среды, нагревали до заданной температуры со скоростью 10 град./мин, выдерживали в изотермическом режиме 1 ч и охлаждали. Полученный биоуголь (торрефикат) взвешивался и собирался для дальнейших исследований.
Зольность веществ определяли по ГОСТ 11022-95.
Элементный анализ проводили на приборе Vario MICRO Cube, предназначенном для одновременного определения элементов C, H, N и S в образцах.
Кислород (O, мас. %) определяли из материального баланса:
где C, H, N, S, A – содержание углерода, водорода, азота, серы и золы в пересчете на сухое вещество.Теплотворные способности материалов (высшая и низшая) были рассчитаны по уравнению Менделеева на основе элементного состава:
(3)
$\begin{gathered} {\text{НТС}} = 0.339[{\text{C}}] + 1.256[{\text{H}}] + \\ \, + 0.109[{\text{S}}]--0.109[{\text{O}}]--0.0252[9{\text{H}} + {\text{W}}], \\ \end{gathered} $Для определения структурных компонентов в исходной биомассе и биоуглях применяли следующие методы количественного анализа:
• экстракцию этиловым спиртом (для экстрактивных);
• метод Комаровского – кислотный гидролиз 72%-й серной кислотой (для определения лигнина);
• метод Кюршнера–Хоффера – обработка смесью концентрированной азотной кислоты и этилового спирта в объемном отношении 1 : 4 (для определения целлюлозы);
• метод последовательного гидролиза салициловой и соляной кислотами (для определения гемицеллюлоз).
ОБСУЖДЕНИЕ РЕЗУЛЬТАТОВ
Для исследования были выбраны два типа сырья, распространенного на территории РФ – опилки деревьев лиственных пород и низинный торф. Выбор был обусловлен различным содержанием структурных компонентов в материалах. В составе торфа преобладал лигнин (61%) и практически отсутствовали гемицеллюлозы (0.85%), доля целлюлозы составляла 34.46%, а экстрактивных веществ – 3.4%. Опилки имели более равномерный структурный состав с некоторым преобладанием целлюлозы: 21.81% гемицеллюлоз, 26.83% лигнина, 48.83% целлюлозы, 2.65% экстрактивных веществ. Поскольку условия осуществления гидротермальной карбонизации и торрефакции несколько отличаются, температуру для проведения реакций выбирали из разных температурных интервалов. Однако одна температура (230°С) была все же одинаковой, что позволяет более детально сравнить результаты обеих термообработок.
В табл. 2 данные по влиянию температуры на выход получаемых биоуглей. При использовании обоих способов термообработки наблюдали заметное снижение выхода биоугля при повышении температуры внутри каждого температурного интервала. При повышении температуры с 190 до 230°С выход биоугля, полученного гидротермальной карбонизацией (“карбонизата”) из опилок, снижался с 70 до 58% (на 17%), для торфа на 20%. Выход биоугля, полученного торрефакцией (“торрефиката”) из опилок, при повышении температуры с 230 до 290°С уменьшался на 20%, для торфа всего на 14%. При выбранных условиях термообработки выход карбонизата был заметно ниже выхода торрефиката. Максимальный выход карбонизата был зафиксирован для торфа (86%), а торрефиката – для опилок (93%). При одинаковой температуре (230°С) выход карбонизата из опилок составлял всего 58%, а из торфа 68%, в то время как выход торрефиката из обоих видов сырья в этих условиях превышал 90%. Ранее авторами были получены похожие зависимости для торфа при его обработке как методом торрефикации [5], так и гидротермальной карбонизацией [6]. Уменьшение выходов биоуглей определяется протекающими химическими реакциями в процессах. При торрефакции основными реакциями, влияющими на выходы биоугля, являются дегидратация и декарбоксилирование (элиминирование молекулы диоксида углерода из карбоксильной группы или карбоксилатной группы органических соединений) [7]. Обе реакции влияют не только на выходы биоугля, но и являются основными механизмами деоксигенации сырья. При гидротермальной карбонизации на потерю массы оказывают влияние гораздо больше процессов: термическая деструкция, дегидратация, декарбоксилирование и особенно гидролиз, который заметно усиливается при повышении температуры [8].
Таблица 2.
Влияние температуры ГТК и торрефакции на выход биоугля
Сырье | Обработка | Т, °С | Выход, мас. % |
---|---|---|---|
Торф | ГТК | 190 | 85.87 |
210 | 77.27 | ||
230 | 68.08 | ||
Торрефакция | 230 | 91.38 | |
260 | 85.05 | ||
290 | 78.18 | ||
Опилки | ГТК | 190 | 70.31 |
210 | 66.31 | ||
230 | 57.85 | ||
Торрефакция | 230 | 92.8 | |
260 | 76.34 | ||
290 | 74.31 |
Низкотемпературная термообработка биомассы оказывает заметное влияние на состав полученного материала. Элементный состав биоуглей, полученных при разных температурах в процессах ГТК и торрефакции, представлен в табл. 3.
Таблица 3.
Элементный состав биоуглей, полученных низкотемпературной обработкой биомассы при разных температурах
Сырье | Обработка | Т, °С | Элементный анализ, мас. % | |||||
---|---|---|---|---|---|---|---|---|
С | Н | N | S | O | A | |||
Торф | ГТК | 190 | 53.96 | 4.85 | 2.56 | 0.29 | 23.7 | 14.64 |
210 | 55.93 | 5.03 | 2.72 | 0.33 | 19.19 | 16.8 | ||
230 | 56.42 | 3.36 | 1.23 | 0.38 | 11.69 | 26.92 | ||
Торрефакция | 230 | 49.46 | 4.63 | 3.05 | 0.59 | 15.42 | 26.24 | |
260 | 51.12 | 4.44 | 3.05 | 0.39 | 12.04 | 26.04 | ||
290 | 53.95 | 4.02 | 3.16 | 0.38 | 11.09 | 26.49 | ||
Опилки | ГТК | 190 | 57.36 | 5.67 | 0.09 | 0.23 | 36.38 | 0.27 |
210 | 65.09 | 5.22 | 0.1 | 0.22 | 28.84 | 0.53 | ||
230 | 69.73 | 5.54 | 0.12 | 0.24 | 23.05 | 1.32 | ||
Торрефакция | 230 | 54.26 | 6.72 | 0.15 | 0.04 | 38.24 | 0.58 | |
260 | 58.36 | 6.37 | 0.22 | 0.04 | 34.31 | 0.71 | ||
290 | 59.25 | 6.46 | 0.12 | 0.03 | 33.41 | 0.83 |
Гидротермальная обработка опилок при относительно низкой температуре (190°С) привела к увеличению доли углерода в материале до 57%, а повышение температуры до 230°С позволило увеличить ее до 70% (табл. 3). В то же время наблюдалось снижение содержания кислорода в карбонизате почти на 49% в сравнении с исходным сырьем. Обработка торфа гидротермальной карбонизацией при температуре 230°С позволила увеличить количество углерода в биоугле вдвое (с 27 до 56%). Воздействие температуры на торф не оказало значительного влияния на количество углерода в материале: его доля повысилась всего на 5% при повышении температуры с 190 до 230°С. Однако при этом наблюдали весьма заметное уменьшение содержании кислорода: при 190°С почти вдвое, а при 230°С уже в 4 раза.
После торрефакции опилок наибольшим количеством углерода (59%) обладал образец, полученный при 290°С (табл. 3). Количество кислорода в торрефикатах заметно снижалось с повышением температуры: наименьшим значением (24%) обладал образец, полученный при 290°С. Для торфа также наблюдали значительное увеличение углерода в биоугле: оно достигало 54% при 290°С, что вдвое больше, чем у исходного сырья. В этом случае деоксигенация происходила более активно: уже при 230°С содержание кислорода в торрефикате уменьшилось на 60%.
Сравнение двух низкотемпературных способов обработки биомассы позволяет сделать заключение, что карбонизаты содержат больше углерода, а в случае их получения из опилок и значительно меньше кислорода. Однако деоксигенация торфа протекает более интенсивно при торрефакции.
При гидротермальной карбонизации, в отличие от процесса торрефакции, в биоуглях наблюдается снижение зольности, особенно при обработке сырья при низких температурах (табл. 3). Это обусловлено вымыванием минеральных компонентов, попавших в биомассу вместе с грязью в процессе ее сбора. Кроме того, происходит выделение в реакционную воду минеральных компонентов, содержащихся в гемицеллюлозах, при термической деградации последних. (Известно [9], что гемицеллюлозы содержат в своем составе наибольшее количество минеральных компонентов.) Наименьшую зольность (почти в двое меньшую, чем у исходного сырья) демонстрировали карбонизаты, полученные при 190°С. Возрастание зольности при более высоких температурах может быть объяснено большей потерей органической массы и более глубоким разрушением целлюлозы, в матрице которой также могут находиться минеральные компоненты.
В случае торрефакции увеличение зольности биоуглей (табл. 3) также обуславливается деградацией структурных компонентов биомассы, что приводит к потере части органической массы и увеличению концентрации минеральных составляющих в материале.
Хорошо известно, что при термическом воздействии на биомассу происходит разрушение ее структурных компонентов, глубина которого зависит от температуры.
Основными структурными компонентами растительной биомассы являются гемицеллюлозы, целлюлоза и лигнин [10]. Целлюлоза (гомополисахарид глюкозы) описывается общей формулой (С6Н10О5)n, она построена из мономерных звеньев – остатков β-глюкопиранозы. Целлюлоза сформирована в линейные цепочки, содержащие до 15 000 молекул глюкозы. Она нерастворима в воде, относительно устойчива к ферментативному разложению и ответственна за волокнистую природу биомассы.
Гемицеллюлозы – нецеллюлозные полисахариды, макромолекулы которых построены из остатков различных моносахаридов (пентоз и гексоз), которые условно их подразделяют на пентозаны (С5Н8О4)n и гексозаны (С6Н10О5)n. Основными гексозанами являются маннаны (глюкоманнан, галактоглюкоманнан). Гемицеллюлозы проявляют более низкую химическую и термическую стабильность, чем целлюлоза. Они содержат боковые цепи, которые делают их частично растворимыми в воде, и имеют важное значение для поглощения растением влаги.
Ароматическая часть биомассы (лигнин) – смесь полимеров родственного строения ароматической (фенольной) природы. Макромолекулы лигнина построены из мономерных звеньев (“фенилпропановых структурных единиц”). Лигнин образует сложную взаимосвязанную структуру – трехмерные сети ароматических компонентов и отвечает за жесткость материала. Он является самым термостабильным среди структурных компонентов биомассы. Лигнин имеет наибольшую теплотворную способность среди полимеров биомассы, поскольку обладает самым высоким содержанием углерода. В отличие от целлюлозы лигнин не может быть деполимеризован на исходные мономеры.
Экстрактивные вещества представляют собой алифатические и ароматические углеводороды, кислоты, терпены, фенолы, смоляные и жирные кислоты, эфирные масла, смолы, жиры, стерины [11]. Состав экстрактивных веществ зависит от природы сырья.
В табл. 4 представлены данные по влиянию температуры на структурные компоненты биомассы.
Таблица 4.
Содержание структурных компонентов и экстрактивные вещества биомассы в биоуглях, полученных низкотемпературной обработкой
Сырье | Обработка | Т, °С | Компонент, мас. % | |||
---|---|---|---|---|---|---|
гемицеллюлоза | целлюлоза | лигнин | экстрактивные вещества | |||
Торф | ГТК | 190 | 0 | 23.90 | 68.76 | 5.80 |
210 | 0 | 17.81 | 75.00 | 6.62 | ||
230 | 0 | 13.97 | 76.77 | 10.81 | ||
Торрефакция | 230 | 0 | 22.67 | 74.54 | 4.16 | |
260 | 0 | 19.77 | 76.28 | 4.68 | ||
290 | 0 | 14.05 | 81.93 | 5.54 | ||
Опилки | ГТК | 190 | 0 | 47.95 | 46.82 | 6.35 |
210 | 0 | 36.54 | 55.33 | 7.25 | ||
230 | 0 | 20.99 | 71.37 | 9.08 | ||
Торрефакция | 230 | 0 | 36.01 | 60.95 | 3.43 | |
260 | 0 | 31.42 | 63.65 | 4.73 | ||
290 | 0 | 27.80 | 65.68 | 7.66 |
Следует отметить, что в процессе обоих типов термообработки биомассы гемицеллюлозы полностью разрушаются (табл. 4). Также частичному разрушению подвергается целлюлоза, степень деградации которой напрямую зависит от температурного воздействия на биомассу. Экстрактивные вещества и лигнин, напротив, имеют тенденцию к накоплению в биоуглях.
Протекания гидролиза, ключевой реакции гидротермальной карбонизации, проясняют большую деградацию целлюлозы в этом процессе ввиду разрушения межкомпонентных связей, удерживающих ее в сырье. В условиях ГТК вода приобретает необычные свойства [12]: повышение температуры приводит к снижению ее диэлектрической постоянной и к существенному увеличению константы диссоциации. Как следствие, в реакционной среде значительно повышается концентрация ионов гидроксония – катализатора гидролиза. Под воздействием воды разрываются связи (в основном бета-(1–4)-гликозидные) простых и сложных эфиров гемицеллюлоз и целлюлозы. В результате образуется большое число продуктов, в том числе растворимые олигомеры, что объясняет большее образование экстрактивных веществ в сравнении с торрефакцией, при которой гидролиз не протекает. Кроме того, диэлектрическая проницаемость воды уменьшается при температурах проведения реакции гидротермальной карбонизации так, что она действует, скорее, как неполярный растворитель.
Лигнин, как наиболее термостабильное вещество, подвергается меньшей деструкции. Как уже было сказано выше, при увеличении температур протекания реакций процентное соотношение лигнина в полученном материале возрастает, что свидетельствует о малой деструкции лигнина и разрушении целлюлозы и гемицеллюлоз. Процентное возрастание лигнина в биоуглях определяет повышение топливных характеристик полученных материалов. Биоугли, полученные торрефакцией, обладали меньшим количеством лигнина, что объясняется более высокими температурами проведения реакции, поскольку небольшая часть лигнина реагирует при температуре 260°C с высвобождением фенола и фенольных производных, что также приводит к увеличению экстрактивных веществ в биоуглях, полученных торрефакцией при 290°C.
В табл. 5 приведены величины теплотворных способностей биоуглей, полученных низкотемпературной термообработкой биомассы.
Таблица 5.
Теплотворные способности биоуглей, полученных низкотемпературной обработкой биомассы
Сырье | Обработка | Т, °С | Теплотворная способность, МДж/кг | |
---|---|---|---|---|
высшая | низшая | |||
Торф | ГТК | 190 | 21.83 | 20.73 |
210 | 23.22 | 22.08 | ||
230 | 22.11 | 21.35 | ||
Торрефакция | 230 | 20.96 | 19.91 | |
260 | 21.64 | 20.63 | ||
290 | 22.17 | 21.26 | ||
Опилки | ГТК | 190 | 22.62 | 17.74 |
210 | 25.50 | 21.34 | ||
230 | 28.11 | 24.32 | ||
Торрефакция | 230 | 22.67 | 21.15 | |
260 | 24.04 | 22.60 | ||
290 | 24.56 | 23.10 |
Как и следовало ожидать, усиление температурного воздействие на сырье приводило к увеличению доли углерода в связи с деоксигенацией материала, что положительно влияло на высшую (ВТС) и низшую (НТС) теплотворные способности полученных биоуглей (табл. 5). При повышении температуры гидротермальной карбонизации опилок с 190 до 230°С теплотворные способности заметно возрастали: на 24% ВТС и на 27% НТС. Самые высокие значения этих показателей (НТС = 28 МДж/кг, ВТС = 24 МДж/кг) наблюдали для карбонизата, полученного из опилок при 230°C. Однако теплотворные способности карбонизата, полученного из торфа при 230°C, имели довольно низкие значения (НТС = = 22 МДж/кг, ВТС = 21 МДж/кг), что, вероятно, объясняется значительным возрастанием зольности в этом биоугле.
В случае торрефакции опилок повышение температуры приводило к меньшему увеличению теплотворных способностей биоугля: значения ВТС и НТС возросли всего на 8 единиц (табл. 5). Усиление температурного воздействия на торф, как и на опилки, оказывало незначительное повышение теплотворных способностей (на 6–7%). В общем, торрефикаты отличались несколько меньшей калорийностью, чем карбонизаты, полученные из того же вида биомассы.
ЗАКЛЮЧЕНИЕ
Получение биоуглей из отходов растительного происхождения и условно возобновляемых ресурсов, таких как торф, – перспективное направление в альтернативной энергетике в настоящее время. Процессы торрефакции и гидротермальной карбонизации – это подающее большие надежды термические методы переработки растительной биомассы в высококачественное энергетическое сырье, пригодное для топливных целей.
При осуществлении обоих процессов термообработки температура играет определяющую роль и непосредственно влияет на теплотехнические характеристики, состав и выход получаемых биоуглей. При использовании торрефакции биоуголь образуется с большим выходом. Однако он обладает меньшей теплотворной способностью, чем биоуголь, полученный методом гидротермальной карбонизации. В обоих случаях значительно меняется элементный состав сырья: с повышением температуры усиливаются карбонизация и деоксигенация материала. В случае использования гидротермальной карбонизации имеет место снижение зольности, что объясняется растворением части минеральных компонентов в реакционной воде.
При термическом воздействии на биомассу происходит полное разрушение наиболее нестабильных компонентов биомасс – гемицеллюлоз. Доля целлюлозы в биоугле снижается с повышением температуры термообработки, что свидетельствует о ее частичном разрушении. В случае гидротермальной карбонизации этот эффект проявляется в большей степени. Доли лигнина и экстрактивных веществ, напротив, возрастают при усилении термического воздействия. В случае лигнина это обуславливается его большей термической стабильностью по сравнению с целлюлозой и гемицеллюлозами.
Сравнение двух видов низкотемпературной термообработки биомассы с получением биоугля позволяет сделать вывод, что гидротермальная карбонизация оказывает более глубокое воздействие на сырье, о чем свидетельствуют не только более высокие теплотворные способности биоугля, но и большая степень разрушения целлюлозы в сырье.
Список литературы
Matali S., Abdrahman N., Idris S., Yaacob N., Alias A. // Proc. Engng. 2016. V. 148. P. 671.
Reza M. Hydrothermal carbonization of lignocellulosic biomass. Ph.D. thesis. 2013.
Wilk M., Magdziarz A. // Energy. 2017. V. 140. P. 1292.
Zhai Y., Peng C., Xu B., Wang T., Li C., Zeng G., Zhu Y. // Energy. 2017. V. 127. P. 167.
Зайченко В.М., Крылова А.Ю., Крысанов О.Н., Крысанова К.О., Сычев Г.А. // ХТТ. 2018. № 2. С. 14. [Solid Fuel Chemistry, 2018. V. 52. № 2. P. 70. https://doi.org/10.3103/S0361521918020143]
Зайченко В.М., Крылова А.Ю., Крысанова К.О., Сычев Г.А. // ХТТ. 2018. № 6. С. 30. [Solid Fuel Chemistry, 2018. V. 52. № 6. P. 370. https://doi.org/10.3103/S0361521918020143]
Zhai Y.// Renewable Sustainable Energy Rev. 2018. V. 90. P. 223.
Prins M., Ptasinski K., Janssen F.J.J.G. // J. Anal. Appl. Pyrolysis. 2006. V. 77. P. 35.
Sevilla M., Fuertes A.// Carbon. 2009. V. 47. P. 2281.
Peterson A.A., Vogel F., Lachance R.P., Froling M., Antal M.J., Tester J.W. // Energy Environ Sci. 2008. V. 1. P. 32.
Оболенская А.В., Щеголев В.П., Аким Г.Л., Аким Э.Л. Практические работы по химии древесины и целлюлозы: учебное пособие для вузов. М.: Лесн. пром-сть, 1965. 414 с.
Funke A., Ziegler F. // Biofuels, Bioproducts&Biorefining. 2010. V. 4. P. 160.
Дополнительные материалы отсутствуют.
Инструменты
Химия твердого топлива