Химия твердого топлива, 2021, № 6, стр. 14-21
КОНВЕРСИЯ ТОПЛИВНЫХ КОМПОЗИЦИЙ, СОСТОЯЩИХ ИЗ ТОРФА И РАПСОВОГО МАСЛА, В ГЕНЕРАТОРНЫЙ ГАЗ
М. В. Белоногов 1, *, А. С. Зайцев 1, **, Р. И. Егоров 1, ***
1 ФГАОУ ВО “Национальный исследовательский Томский политехнический университет”
634028 Томск, Россия
* E-mail: 42maxim@mail.ru
** E-mail: alexzaitsev@tpu.ru
*** E-mail: rommel@tpu.ru
Поступила в редакцию 09.02.2021
После доработки 13.04.2021
Принята к публикации 02.06.2021
Аннотация
Рассмотрены особенности аллотермической конверсии топливной смеси, состоящей из торфа и рапсового масла, под действием мощного потока видимого света. Показано, что смесь, содержащая 65 вес. % рапсового масла, может быть сконвертирована при атмосферном давлении в генераторный газ, в котором соотношение парциальных объемов горючих и негорючих компонентов превосходит единицу. Проанализированы температурные режимы конверсии топлива с различным содержанием рапсового масла. Показано, что длительность высокотемпературного (более 700°С) участка конверсии топлива максимальна, когда доля рапсового масла достигает 65 вес. %.
ВВЕДЕНИЕ
Использование в промышленности низкосортных ископаемых топлив (торфа и бурого угля) становится все более популярным в последние десятилетия [1]. С одной стороны, это обусловлено ростом цен на традиционные топлива [2] (каменные угли, продукты нефтепереработки, природный газ) вследствие сокращения легко извлекаемых запасов таких топлив, а с другой – стремлением ряда государств (в том числе и РФ) к созданию в плане энергетики регионов [3] c опорой на местные ресурсы. Огромные залежи торфа на территории России позволяют, при правильной организации процесса, перекрыть потребности объектов промышленности и энергетики в топливе, сэкономив энергетические угли и снизив стоимость единицы производимой тепловой энергии. Стоит отметить, что внедрение торфа как такового в промышленные цепочки теплогенерации потребует существенных переделок топочных агрегатов уже существующих и будущих котельных [4], оптимизированных под сжигание разных типов угля, мазута и природного газа. Оптимальным способом избежать этих весьма существенных капитальных затрат является предварительная конверсия низкосортного топлива в генераторный газ с последующим его сжиганием в унифицированных топках с газовым питанием. Технологии термохимической переработки торфов (пиролиз, а также различные методы газификации) известны уже давно. В ряде работ описываются методики автотермической [5] и аллотермической [6] газификации торфа, методики пиролиза с использованием как нагрева от сторонних источников, так и за счет сжигания самого торфа.
Использование смесевых композиций различных топлив для повышения эффективности процессов термохимической конверсии применяется достаточно давно [7], например подача воды (водяного пара) в нагреваемую угольную шихту позволяет задействовать паро-углеродные реакции для стимуляции выработки СО и подавления избыточного горения топлива. Использование смесей угля и нефтепродуктов позволяет получить необходимый баланс водорода и углерода в составе полученного газа [7, 8]. Однако применительно к газификации торфа добавление чего-то отличного от воды не получило распространения. При этом, с одной стороны, массовая негорючая примесь повышает затраты энергии на конверсию единицы массы смеси, а с другой – повышает стоимость топливной смеси. Определение оптимальной, с точки зрения энергетики генераторного газа, композиции может оказаться удобным путем для массового освоения всех тех залежей торфа, которые ежегодно горят в силу природных и антропогенных причин, нанося вред экологии городских агломераций [9].
Вопрос экологической безопасности используемых компонентов – один из основополагающих при внедрении топливной смеси в промышленный цикл. Нефтепродукты (и отходы нефтяного происхождения) являются достаточно проблемным компонентом при массовом применении топливной смеси как с точки зрения их хранения, так и с точки зрения состава синтез-газа. При термохимической конверсии, как и при тривиальном сжигании, смесей на основе нефтепродуктов [10] производится достаточно большое количество вредных газов (диоксида серы, сероводорода и его производных). Использование горючих жидкостей растительного происхождения (различных смесей эфиров и прочих ароматических соединений) позволяет существенно улучшить экологические показатели топливной смеси и полученных из нее газов, а также получить практически неисчерпаемый источник углеводородного топлива, воспроизводство запасов которого происходит за счет энергии Солнца, с достаточно коротким циклом воспроизводства [11].
В данной работе были рассмотрены особенности аллотермического процесса переработки смеси торфа и рапсового масла (РМ), приготовленной в различных соотношениях компонентов, в генераторный газ. Проанализированы зависимости температуры на поверхности слоя топлива, а также состава генераторного газа от количества РМ в составе смеси. Использование мощного светового потока в качестве источника тепла позволяет обобщить данные результаты в случае использования солнечного света при проектировании промышленных процессов конверсии топливной смеси в генераторный газ.
Приборы и материалы. Использовался торф месторождения “Суховское” Томской области (см. табл. 1), перемолотый с помощью роторной мельницы для большей однородности. В рассматриваемых смесях средний размер частиц не превышал 120 мкм. В качестве горючего жидкого компонента использовалось нерафинированное РМ [12], произведенное ООО “Агроальянс” (Томская обл.).
Таблица 1.
Свойства торфа
Влажность на рабочую массу, % | 9.9 |
Ad, % | 22.8 |
V, % на daf | 74.8 |
Q$_{s}^{a}$,V, МДж/кг | 11.8 |
Элементный состав, % на daf: | |
C | 52.06 |
H | 6.31 |
N | 3.58 |
S | 0.2 |
O | 37.85 |
Физические свойства: | |
λ, Вт/(м К) | 0.26 |
Ср, кДж/(кг К) | 1.88 |
a, cм2/с | 0.0036 |
Топливная смесь приготавливалась непосредственно перед экспериментом, затем перемешивалась в течение 15 мин с помощью низкоскоростного миксера (100–200 об/мин), что позволяло получать смеси с высокой однородностью даже в случае, когда содержание одного из компонентов было довольно малым. Порция топлива представляла собой квазицилиндрический слой массой порядка 0.5–0.6 г и объемом около 0.5 см3. Готовая смесь представляла собой достаточно густую пасту при концентрациях РМ до 45 вес. %. Рост содержания масла до 60–70 вес. % приводит к превращению смеси в густую жидкость (консистенция сметаны) и дальнейшему разжижению при больших концентрациях масла.
Топливо помещалось в герметичную ячейку с оптическим окном сверху и патрубком для откачки газа сбоку, который подключался к входному тракту газоанализатора (см. рис. 1). Ячейка изначально заполнялась воздухом (V ~ 6.5 см3), который расходовался в ходе процесса, а также вытеснялся из камеры продуктами конверсии топлива. Сфокусированный световой поток от галогеновой лампы (450 Вт) заводился в ячейку через окно в верхней грани таким образом, чтобы фокальная плоскость попадала на поверхность топлива. С учетом КПД лампы, в освещенной области радиусом 0.7 мм обеспечивалась интенсивность светового потока порядка 800–810 Вт/см2. Такая интенсивность светового потока позволяет очень быстро разогреть поверхность топлива до температур более 600°С. С учетом коэффициента поглощения топливной смеси (~0.5–0.6) интенсивность входящего теплового потока составляла порядка 400–450 Вт/см2.
Рис. 1.
Схема экспериментального стенда: источник тепловой энергии (лампа, фокусирующая система – Л1 и Л2), ячейка-реактор (Я), газоанализатор (ГА) и термоэлектрический измеритель температуры (900°С).
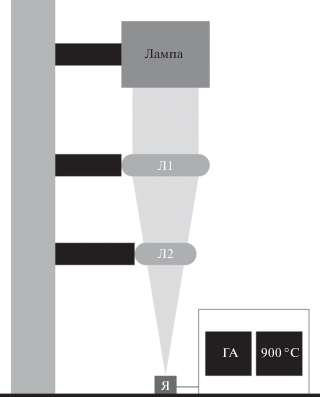
Использованный газоанализатор позволяет контролировать концентрации только фиксированного набора газов (СО, СО2, H2, SO2, NOx, CH4), поэтому процесс испарения эфиров из состава РМ в данном исследовании не контролировался. В тракт газоанализатора были установлены сборник конденсата и дополнительный угольный фильтр, который поглощал основную массу не разложившихся летучих компонентов масла, т.е. в работе рассмотрены особенности процессов термохимической конверсии топлива в оксиды углерода в присутствии массированного испарения летучих компонентов масла. Данный эффект по определению приводит к заметному понижению температуры приповерхностных слоев топлива.
Газовая смесь, прошедшая угольный фильтр, дополнительно очищалась PFTE-фильтром (размер пор ~0.45 мкм) и прокачивалась через датчики газоанализатора. На данном этапе она имела температуру порядка 25°С, т.е. ее химический состав был достаточно стабилен.
Температура нагреваемой поверхности топлива контролировалась с помощью тепловизора Testo 885–2, предварительно откалиброванного по показаниям малоинерционных термопар для данного материала. При проведении тепловизионных измерений стекло на окне камеры реактора убиралось.
ОБСУЖДЕНИЕ РЕЗУЛЬТАТОВ
Изменение температуры поверхности со временем для различных видов топливной смеси представлено на рис. 2. Видно, что сразу после включения нагрева происходит резкий рост температуры в освещенной области до величин порядка 800°С. В зависимости от состава топливной смеси длительность такого высокотемпературного состояния составляет от 45 с (порошок торфа с влажностью от 9.9 до 16–20 вес. %) до 3.5–4.0 мин (смесь, содержащая 65 вес. % РМ). Таким образом, можно отметить, что добавление РМ приводит к такому изменению теплофизических параметров смеси (а также интегральных термокинетических параметров процессов разложения и окисления компонентов топлива), что продолжительность именно высокотемпературной конверсии увеличивается более чем в 5 раз (при той же интенсивности нагрева). Первоначальный скачок температуры до величин ~700°С можно объяснить вкладом тепловых эффектов окисления компонентов топлива. Выход зависимости в дальнейшем в стационарное состояние отражает уровень температур, обеспечиваемый, собственно, нагревом от внешнего источника.
Рис. 2.
Зависимости температур в центре пятна светового нагрева от времени для различных концентраций РМ в смеси.
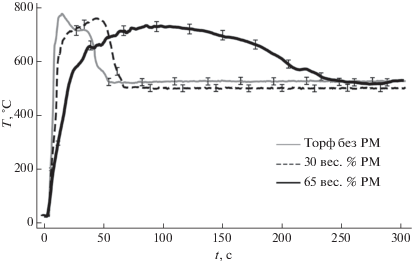
С ростом содержания РМ происходит небольшое снижение пиковых температур, что очевидно обусловлено как ростом тепловых эффектов испарения летучих компонентов РМ, так и изменениями теплоемкости смеси. Однако малость этого спада показывает, что температурный режим конверсии топлива остается практически неизменным.
Дальнейшее наращивание содержания РМ приводит к быстрому исчезновению высокотемпературной области на зависимости температуры поверхности топлива, т.е. уже при содержании РМ на уровне ~70 вес. % испарение компонентов РМ приводит к существенному снижению концентрации кислорода вблизи поверхности топливной смеси, что практически полностью подавляет процессы окисления топлива.
С учетом того, что РМ довольно прозрачное для видимого света и не может быть нагрето до нужных температур потоком видимого света за указанный временной интервал, можно заключить, что присутствие торфа также обеспечивает высокий коэффициент поглощения света смесью. С другой стороны, тепловой эффект окисления торфа позволяет поддерживать температуру в области конверсии на 200–250°С выше той, что обеспечивается тепловым потоком от внешнего источника. И даже при содержании торфа ~35 вес. % тепловой эффект его окисления достаточен для прогрева большого объема РМ, окружающего частички торфа.
Анализ состава получаемой газовой смеси позволяет оценить динамику процесса термического разложения компонентов топливной смеси, окисления горючего кислородом, изначально содержащимся в ячейке; а также сделать приблизительную оценку масс полученных газов. На рис. 3 показаны нормированные зависимости концентраций базовых продуктов термохимической конверсии углеводородной топливной смеси. Все кривые нормированы на максимальные значения концентраций, что позволяет отобразить на одном графике несколько кривых с сильно различающимися величинами пиковых концентраций. Такой подход позволяет наглядно продемонстрировать различия динамики газогенерации для компонентов смеси.
Рис. 3.
Динамика производства компонентов синтез-газа, получаемого при газификации сухого торфа (а), (б) и смеси торфа с РМ в соотношении 35 : 65 (в), (г). Нормировочные коэффициенты для концентраций указаны на рисунках.
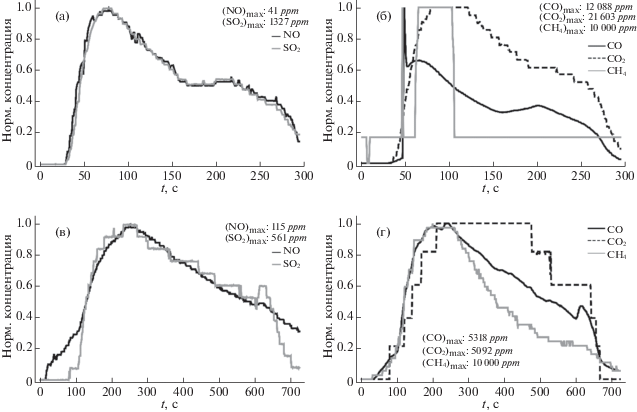
Стоит отметить, что при добавлении РМ начинает меняться содержание вредных примесей (оксиды серы и азота). Максимальные наблюдаемые концентрации диоксида серы (рис. 3,а,в) снижаются в 2–2.5 раза, что несколько ниже снижения доли торфа в смеси (до 35 вес. %). При этом наблюдается почти 3-кратный рост производства оксидов азота. Это происходит вследствие того, что длительность высокотемпературного участка процесса конверсии значительно увеличилась, а следовательно, увеличился общий выход реакций окисления. При этом форма зависимостей концентраций данных газов от времени практически идентична для чистого торфа и хорошо совпадает для смеси (после 100 с нагрева). С учетом зависимостей, представленных на рис. 2, можно сделать вывод, что эти различия в значительной степени обуславливает более медленный нагрев топливной смеси с большим количеством РМ.
Динамика производства метана и оксидов углерода демонстрирует существенные различия между процессами конверсии торфа и смеси торфа с РМ. Общая интенсивность газогенерации (без учета испарения летучих компонентов масла) с добавлением РМ падает более чем в 2 раза преимущественно за счет сокращения производства диоксида углерода; меняется динамика образования оксидов углерода, а также соотношение пиковых концентраций СО и СО2 – с 1 : 2 до 1 : 1, причем интегральный выход СО начинает превосходить выход СО2.
Выработка метана демонстрирует тот же пиковый уровень, но с существенными различиями в деталях динамики процесса. Метан может образовываться двумя путями: при разложении высокомолекулярных летучих компонентов торфа и при разложении компонентов РМ. Причем, судя по росту интегральной выработки метана, производительность второго канала оказывается заметно больше, чем у первого (так как массовая доля торфа падает пропорционально концентрации РМ).
Из рис. 3 можно заключить, что добавление РМ привело к падению общей производительности реакции полного окисления углерода в 4 раза (преимущественно из-за снижения парциальной концентрации кислорода у поверхности топлива за счет его вытеснения испаряющимися летучими компонентами масла, но также и за счет роста температуры смеси). При этом общий выход СО снизился только в 2.3 раза. Начальный скачок концентрации СО при старте конверсии торфа обусловлен скачком температуры до 800°С, причем последующий спад температуры приводил к быстрому падению выработки СО. Расширение высокотемпературного участка нагрева смеси позволяет повысить эффективность производства моноксида углерода.
Общая длительность процесса газогенерации для фиксированной массы топлива (порядка 0.5 г) увеличивается более чем в 2 раза при добавлении РМ. При этом длительность высокотемпературного участка составляет от четверти до трети всего времени газогенерации.
Оценка масс полученных газов может быть сделана исходя из номинальной производительности насоса газоанализатора (ранее калиброванной с помощью меточного расходомера). Интегрируя концентрационные зависимости по всей длительности процесса, можно заключить, что из торфа получается порядка 30 мг представленных газов, а из смеси – порядка 25 мг. Полная масса продуктов конверсии, оцененная взвешиванием камеры с образцом до и после процесса, составляла менее 0.1 г. Разница между приведенными числами определяется массами не регистрируемых газоанализатором газов – водяного пара, сложных продуктов пиролиза торфа и РМ, испаренных летучих компонентов РМ (преимущественно эфиров).
На рис. 4 показана зависимость средних объ-емов ежесекундной выработки рассматриваемых газов от количества РМ в составе смеси. Оценка объемов была получена из соответствующих зависимостей концентраций газов с учетом производительности насоса газоанализатора. С ростом концентрации РМ происходит очевидное снижение концентраций всех газов, кроме метана и оксидов азота. Данный факт, очевидно, демонстрирует вклад процесса разложения сложных углеводородов из состава масла с выделением простейших предельных углеводородов и азотистых соединений.
Одним из важнейших результатов исследования является очевидный рост соотношения СО и СО2 в составе газообразных продуктов переработки смеси (рис. 4). При конверсии торфа без примеси масла это соотношение равно 4 : 1 в пользу диоксида углерода. С ростом доли РМ в составе смеси соотношение меняется – вплоть до равного 1 : 1. Такое соотношение оксидов углерода, с учетом присутствия метана, позволяет при атмосферном давлении получать генераторный газ с достаточно высокой для практического использования теплотворной способностью. На рис. 5,а показано отношение объемов горючих и негорючих компонентов в составе продуктов конверсии топливной смеси. Видно, что, когда массовая доля РМ превосходит 50 вес. %, наблюдается заметный рост производства горючих компонентов газовой смеси. Однако когда доля масла становится более 65 вес. %, резкое снижение температуры топлива приводит к сокращению производства регистрируемых газов.
Рис. 5.
Соотношение объемов горючих и негорючих компонентов синтез-газа (а), а также длительность процесса активной газогенерации (б) в зависимости от концентрации РМ.

На рис. 5,б показана зависимость длительности процесса активной газогенерации (момент начала и окончания отмечались по превышению концентраций оксидов углерода порога в 100 ppm). Видно, что при низких концентрациях РМ в составе топливной смеси длительность газогенерации составляла порядка 300 с. Однако при росте доли масла свыше 50 вес. % наблюдался резкий рост длительности процесса (до 800–1000 с) и далее резкий спад длительности газогенерации, когда доля РМ превышает 65 вес. %.
Как было отмечено, процесс газогенерации при разогреве масло-торфяной смеси мощным световым потоком разделяется на два принципиально различных канала – испарение летучих компонентов масла (преимущественно метиловые эфиры жирных кислот) и термохимическая конверсия смеси торфа и масла с производством смеси оксидов углерода, простейших предельных углеводородов и водяного пара с небольшой примесью газообразных оксидов (SO2, NO и др.). С ростом доли масла в составе смеси происходит очевидный рост производительности первого канала. Оценки масс произведенных газов (как разница измеренной массы порции топлива до и после процесса) показывают, что из чистого торфа выделяется в среднем на 20% больше газов, чем из смеси торфа и РМ (65 вес. %). При более высоких концентрациях РМ масса газообразных продуктов достигает в 10–12 раз меньших величин. Промежуточные концентрации РМ позволяют получить заметно меньший по массе выход газов, чем для чистого торфа. Данный факт неплохо коррелирует с анализом динамики состава газов (см. рис. 4) – при малых концентрациях РМ наблюдается спад производства продуктов термохимической конверсии топлива, при этом испарение летучих еще достаточно невелико. С ростом концентрации РМ растет испарение, а также меняется режим термохимического разложения топлива (рост выработки метана). Это приводит к тому, что общее изменение массы топливной смеси с 65 вес.% масла практически достигает величин, наблюдавшихся при окислении торфа.
Таким образом, при быстром нагреве топливной смеси в воздушной атмосфере (при давлении в 1 атм.) до температур порядка 800°С образуется смесь оксидов углерода, метана и метиловых эфиров жирных кислот, состав которой сильно зависит от массовой доли РМ в составе смеси. Показано наличие пороговой концентрации (~65 вес. %) РМ, при которой достигается локальный максимум эффективности газогенерации, соответствующий максимуму содержания горючих газов (эфиры, метан и СО).
Тепловой режим процесса конверсии топлива сильно зависит от концентрации РМ. Если при нагреве торфа максимум теплового эффекта его окисления соответствует началу нагрева (свыше 500°С), то при нагреве торфо-масляной смеси тепловой эффект окисления растягивается по времени. Это значит, что общая температура порции топливной смеси будет достигать более высоких температур к концу процесса с соответствующим ростом производительности всех протекающих химических реакций.
Использование мощного светового потока видимого диапазона для нагрева топлива позволяет организовать процесс промышленной конверсии подобных топливных смесей под действием сфокусированного солнечного света, т.е. осуществить процесс пиролиза и газификации топлива за счет возобновляемых источников энергии. Такое применение солнечной энергии выглядит заметно более удобным как с точки зрения накопления и хранения продуктов, так и с точки зрения эффективности использования солнечного света, чем использование фотовольтаических систем прямого преобразования солнечного света в электричество.
При использовании частично возобновляемого топлива (РМ составляет 2/3 массы смеси) процесс конверсии за счет солнечного света выглядит достаточно привлекательным. Использование торфа (огромные и мало востребованные залежи которого имеются в России) позволяет предполагать как низкую стоимость, так и длительный жизненный цикл технологий, основанных на предложенном подходе.
ЗАКЛЮЧЕНИЕ
Смесь торфа с РМ (65 вес. %) под действием мощного светового потока (800 Вт/см2) может быть преобразована в генераторный газ с высоким содержанием горючих компонентов (более 50% по объему) при атмосферном давлении. Термохимическая конверсия такой топливной смеси происходит с максимальным задействованием теплового эффекта окисления топлива, что выражается в двух-трехкратном увеличении длительности высокотемпературного участка конверсии в сравнении с тем, что наблюдалось для смесей с другим содержанием РМ. Выход газообразных продуктов конверсии такой смеси составляет не менее 80% от массы продуктов переработки сухого торфа, тогда как смеси торфа и РМ в других пропорциях обеспечивают гораздо менее эффективную газогенерацию. Данный процесс потенциально позволяет реализовать промышленную конверсию смесей торфа и быстро возобновляемых ресурсов (горючих растительных масел) за счет энергии сфокусированного солнечного света.
Список литературы
Tchapda A.H., Pisupati S.V. // Energies. 2014. V. 7, P. 1098.
Васильева Ю.П. // Вестн.экономики и менеджмента. 2016. № 1. С. 7.
Воронцов А.В. // Вестн. университета (Государственный университет управления). 2014. № 14. С. 115.
Алексеенко С.В., Мальцев Л.И., Богомолов А.Р., Чернецкий М.Ю., Кравченко И.В., Кравченко А.И., Лапин Д.А., Шевырёв С.А., Лырщиков С.Ю. // Изв. Томск. политехн. ун-та. Инжиниринг георесурсов. 2017. № 12. С. 16.
Дубинин А.М., Тупоногов В.Г., Рыжков А.Ф., Каграманов Ю.А., Лабинцев Е.С. // Изв. Томск. политехн. ун-та. Инжиниринг георесурсов. 2015. № 3. С. 50.
Zaitsev A.S., Taburchinov R.I., Ozerova I.P., Pereira A.O., Egorov R.I. // Appl. Sci. (Switzerland). 2020. V. 10. № 126665.
Вершинина К.Ю., Дорохов В.В., Няшина Г.С., Романов Д.С. // ХТТ. 2019. № 5. С. 44.
Donald B.A., Jack D.H. // AIChE Journal. 1976. V. 22. P. 625.
Пелех М.Т., Крейтор В.П. // Проблемы управления рисками в техносфере. 2009. № 4. С. 36.
Зайцев А.С., Ткаченко П.П., Белоногов М.В., Егоров Р. И. // Кокс и химия. 2018. № 7. С. 43.
Осьмак А.А., Серёгин А.А. // Восточно-европейский журнал передовых технологий. 2014. № 8. С. 57.
ГОСТ Р 53457-2009 Масло рапсовое. Технические условия. М.: Стандартинформ, 2011. 21 с.
Дополнительные материалы отсутствуют.
Инструменты
Химия твердого топлива