Химия твердого топлива, 2022, № 4, стр. 40-44
ГАЗИФИКАЦИЯ БИОУГЛЯ, ПОЛУЧЕННОГО ГИДРОТЕРМАЛЬНОЙ КАРБОНИЗАЦИЕЙ ТОРФА
М. В. Куликова 1, *, К. О. Крысанова 1, **, А. Ю. Крылова 1, ***, А. Б. Куликов 1, ****, П. К. Муравский 1, *****, А. Н. Салиев 2, ******, В. Б. Ильин 2, *******, А. А. Савостьянов 2, ********, Р. Е. Яковенко 2
1 ФГБУН Ордена Трудового Красного Знамени Институт нефтехимического синтеза имени А.В. Топчиева РАН (ИНХС РАН)
119991 Москва, Россия
2 ФГБОУ ВО “Южно-Российский государственный политехнический университет (НПИ) имени М.И. Платова” (ЮРГПУ (НПИ))
346428 Новочеркасск, Россия
* E-mail: m_kulikova@ips.ac.ru
** E-mail: kristinakrysanova@gmail.com
*** E-mail: aykrylova@yandex.ru
**** E-mail: akulikov@ips.ac.ru
***** E-mail: muravsky@ips.ac.ru
****** E-mail: saliev.aleksei@yandex.ru
******* E-mail: ilyin07@gmail.com
******** E-mail: and1982.82@mail.ru
Поступила в редакцию 10.12.2021
После доработки 26.01.2022
Принята к публикации 30.03.2022
- EDN: DXUBNP
- DOI: 10.31857/S0023117722040053
Аннотация
Изучено влияние теплофизических характеристик биоуглей, полученных гидротермальной карбонизацией торфа на выход и состав генераторного газа в процессе его паровоздушной газификации. Установлено, что увеличение температуры гидротермальной обработки торфа способствует не только росту выхода газа, но и повышению его качественных характеристик, а именно теплотворных способностей. Длительная обработка сырья (50 ч) торфа при гидротермальной карбонизации приводила к слишком глубокой деоксигенации сырья и отрицательно сказывалась на качестве полученного генераторного газа.
В настоящее время в России основным видом топлива для производства тепловой и электрической энергии является уголь, доля которого в общем энергобалансе страны достигает 70% [1]. Однако угольные ТЭС представляют собой крупные источники выбросов в атмосферу парниковых газов, в частности углекислого. Одним из способов улучшения экологической ситуации в области энергетики можно рассматривать использование СО2-нейтрального энергетического топлива, например торфа.
Торф относится к возобновляемым энергетическим ресурсам большого масштаба: ежегодно в мире образуется несколько миллиардов тонн торфа [2]. По запасам торфа Россия занимает первое место в мире, обладая почти 200 млрд т [3]. Использование торфа для решения проблем энергетики имеет огромное значение.
В качестве одного из перспективных направлений его применения можно рассматривать газификацию – процесс, направленный на производство горючих газов различного состава и назначения. По сравнению с прямым сжиганием газификация позволяет получать чистое газообразное топливо с более высокими показателями качества, которое можно использовать как в паровых котлах, так и в камерах сгорания газотурбинных установок. Будучи, как и уголь, твердым энергетическим топливом, торф обладает рядом преимуществ: он дешевле (тонна хорошего угля стоит вдвое больше, чем тонна торфа), чище (например, в каменном угле содержится 1–3% серы, а в торфе она практически отсутствует), золу, образующуюся после сжигания торфа, проще и безопаснее утилизировать, чем угольный шлак.
В середине прошлого века в нашей стране торф был довольно широко вовлечен в энергетические процессы, как за счет его прямого сжигания, так и производстве энергетических газов [4, 5]. С развитием нефтегазовой отрасли все предприятия, генерирующие энергию, были переведены на жидкое и газообразное топливо и газификацию торфа перестали использовать [6].
В настоящее время вновь возник интерес к газификации торфа как одному из методов распределенной энергетики, предпологающего вовлечение местного сырья для производства тепла и электроэнергии. Однако развитие этого способа наталкивается на ряд экономических причин, одна из которых – довольно низкая теплотворная способность торфа (в среднем 12–17 МДж/кг), близкая к показателю бурого угля. Низкое качество торфа как энергетического топлива связано в основном с высоким содержанием в нем кислорода (до 30% и выше) [7].
Известным способом деоксигенирования биомассы считается гидротермальная карбонизация (ГТК), или “холодное обугливание”. Гидротермальная карбонизация – процесс получения биоугля при температуре 180–220°C и давлении до 25 атм в присутствии воды без доступа воздуха [8]. При ГТК практически весь углерод сырья остается в целевом продукте и образуется минимальное количество углеродсодержащих газов (в основном двуокиси углерода или метана), процесс имеет почти 100%-ную углеродную эффективность.
Гидротермальная карбонизация используется для “облагораживания” всех видов биомассы, используемой в качестве энергетического топлива. ГТК позволяет повысить теплотворную способность материала и понизить его гигроскопичность, что оказывает благотворное влияние на качество топлива, его хранение и транспортировку. Термически обработанная биомасса обладает большей теплотворной способностью, что при его газификации позволяет изменить состав генераторных газов и повысить их калорийность.
Цель настоящей работы – изучение особенности паровоздушной газификации биоугля, полученного гидротермальной карбонизацией торфа.
ЭКСПЕРИМЕНТАЛЬНАЯ ЧАСТЬ
В качестве сырья был использован комплексный верховой торф месторождения Боровское Новгородской области. Тип торфа – сфагновый. Степень разложения 23%. Ботанический состав торфа (%) – это сфагнум балтийский 45, сфагнум бурый 35, сфагнум магелланский 10, пушица 10.
Гидротермальную карбонизацию торфа проводили в стальном автоклаве объемом 500 мл при 190–220°С. В аппарат помещали 20 г торфа и 80 г дистиллированной воды, после чего смесь нагревали до требуемой температуры и выдерживали в изотермическом режиме в течение 10–50 ч. Далее реактор охлаждали до комнатной температуры. В результате реакции образовывалась водно-биоугольная суспензия. Биоуголь отделяли от воды фильтрацией и сушили на воздухе до воздушно-сухого состояния. Полученный биоуголь представлял собой мелкодисперсный порошок темно-коричневого цвета.
Для оценки ГТК использовали следующие показатели: массовый выход (%) – отношение количества биоугля (г) к количеству использованного сырья (г); углеродный выход (“углеродная эффективность”, %) – отношение количества углерода, содержащегося в полученном биоугле (г), к количеству углерода в использованном сырье (г); энергетический выход (%) – отношение теплотворной способности полученного биоугля (МДж/кг) к теплотворной способности использованного сырья (МДж/кг).
Укрупненную партию биоугля готовили в стальном аппарате объемом 10 л. В аппарат помещали 1 кг торфа и 4 л деминерализованной воды, после чего смесь нагревали до необходимой температуры и выдерживали в изотермическом режиме в течение 10 ч. Далее реактор охлаждали до комнатной температуры. Биоуголь отделяли от воды фильтрацией и сушили на воздухе до воздушно-сухого состояния.
Газификацию биоугля проводили в газогенераторе обращенного типа с прямоточной подачей углеродного сырья и газифицирующих агентов, схема которого представлена на рис. 1. Из бункера 29 шнеком 33 в газогенератор 34 дозировали порошок биоугля. В качестве газифицирующих агентов применяли паровоздушную смесь, которую готовили с помощью расходомеров 15, 16.
Рис. 1.
Схема установки газификации биомассы. 1–3 – газовые баллоны; 4–6 – редукторы; 7, 41 – регуляторы давления; 8–13, 39 – запорные вентили; 14 – бак для воды; 15–17 – расходомеры; 18 – испаритель; 19–21 – термопары; 22, 23 – нагревательные элементы; 24, 25 – регуляторы температуры; 26–28 – обратные клапаны; 29 – бункер загрузки биомассы; 30, 31 – холодильники; 32 – редуктор; 33 – шнековое загрузочное устройство; 34 – газогенератор; 35 – изоляция; 36 – бункер золы; 37, 37а – краны; 38 – сепаратор-холодильник; 40 – манометр; 42 – газовый счетчик; 43 – блок управления.
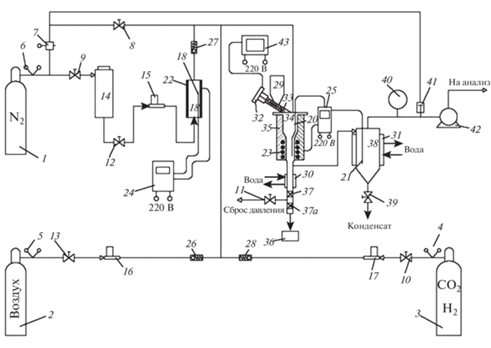
Газификацию осуществляли при давлении 0.1 МПа; температура 850–900°С; расход биоугля – 65 г/ч, пара – 35 и 70 г/ч, коэффициент избытка воздуха 0.3.
Анализ газообразных продуктов газификации проводили на хроматографе “Кристалл 5000” (Хроматэк, Россия), оснащенном детектором по теплопроводности и двумя колонками Haysep R и NaX (молекулярные сита). Первая колонка для определения углеводородов С1–С2 и СО2 (газ-носитель – гелий, 15 мл/мин), вторая – для анализа СО, Н2 и N2 (газ-носитель – аргон, 15 мл/мин). Режим температурно-программируемый со скоростью нагрева 8°C/мин.
Для определения влажности и зольности торфа и полученного из него биоугля был применен термоанализатор SDTQ600, позволяющий проводить синхронный термический анализ, включающий термогравиметрический и дифференциальный термогравиметрический анализы, а также дифференциальную сканирующую калориметрию.
Элементный анализ торфа и полученного из него биоугля проводили на элементном анализаторе Vario MICRO Cube, предназначенном для одновременного определения элементов C, H, N и S в образцах. По данным элементного анализа определяли теплотворную способность материала, используя формулу Менделеева.
Теплотворную способность генераторных газов определяли исходя из их состава, по формуле:
РЕЗУЛЬТАТЫ И ИХ ОБСУЖДЕНИЕ
Для получения биоугля торф подвергали гидротермальной обработке при 190–220°С в течение 10 ч. Массовый выход биоугля, полученный при 190°С, достигал 72% (табл. 1). Углеродная эффективность процесса (доля углерода, оставшегося в твердом материале – биоугле) была довольно высокой и составила 87%. При этом выход летучих веществ заметно (на 10%) снизился по сравнению с аналогичным показателем торфа. Биоуголь содержал на 12% меньше кислорода и на 10% больше углерода, в результате чего его калорийность повысилась на 4 МДж/кг и энергетический выход составил 87%. Неожиданно также возросла зольность биоугля, несмотря на то, что материал 10 ч пребывал в горячей воде. Наблюдаемый эффект можно объяснить наличием в минеральной части торфа трудно растворимых или практически не растворимых в воде соединений и частичной потерей массы материала при его гидротермальной обработке.
Таблица 1.
Влияние условий гидротермальной карбонизации торфа на выход биоугля и его теплотехнические характеристики
Материал | Условие ГТК | Выход, % | Золь- ность, % | Выход летучих веществ, % | Элементный состав, % | Теплотворная спо-собность, МДж/кг | ||||||||
---|---|---|---|---|---|---|---|---|---|---|---|---|---|---|
Т, °С | вре-мя, ч | мас-совый | угле-родный | энерге-тический | С | Н | N | S | O | высшая | низшая | |||
Торф | – | – | – | – | – | 3.88 | 69.5 | 51.79 | 5.91 | 0.93 | Сл. | 37.49 | 20.89 | 19.55 |
Биоуголь | 190 | 10 | 72.5 | 86.7 | 86.8 | 6.78 | 58.2 | 62.00 | 5.31 | 0.93 | Сл. | 24.98 | 24.96 | 23.76 |
220 | 10 | 68.4 | 87.5 | 86.8 | 4.72 | 49.6 | 65.74 | 5.51 | 1.25 | Сл. | 22.78 | 26.72 | 25.47 | |
190 | 50 | 57.3 | 81.6 | 78.7 | 8.94 | 48.2 | 71.18 | 5.55 | 1.4 | 0.27 | 12.66 | 29.75 | 28.49 |
Повышение температуры гидротермальной карбонизации до 220°С привело к некоторому снижению массового выхода биоугля до 68% (табл. 1), однако углеродная эффективность процесса при этом практически не изменилась вследствие увеличения доли углерода в биоугле). Выход летучих веществ снизился еще на 10% и составил 50%. Биоуголь, полученный при 220°С, содержал на 14% меньше кислорода и на 10% больше углерода, чем исходный торф, в результате чего его калорийность повысилась (высшая до 27 МДж/кг, а низшая до 25 МДж/кг). Повышение температуры гидротермальной обработки способствовало некоторому снижению (на 30%) зольности биоугля, что можно объяснить частичным растворением в воде соединений минеральной части торфа.
Увеличение длительности гидротермальной обработки торфа при 190°С в 5 раз приводило к заметной массовой потере сырья: выход биоугля составил всего 57%, т.е. был более чем на 20% ниже (табл. 1). Однако углеродный выход при этом изменился мало вследствие заметного возрастания в материале доли углерода (до 71%) и резкого падения содержания кислорода (практически вдвое). Несмотря на то что энергетический выход несколько снизился (с 87 до 79%), теплотворная способность материала возросла (высшая до 30 МДж/кг, а низшая до 28 МДж/кг). Следует отметить, что зольность биоугля увеличилась до 9%, что на 24% выше зольности биоугля, полученного при более коротком времени обработки при той же температуре. Наблюдаемый эффект можно объяснить большей потерей массы материала при его более длительной обработке.
Диаграмма Ван-Кревелена для исходного торфа и полученных биоуглей представлена на рис. 2. Можно видеть, что с точки зрения изменения отношений Н/С и О/С наибольшая эффективность гидротермальной карбонизации торфа достигается при более низкой температуре и более длительном времени обработки. При этом значение Н/С для всех изученных биоуглей превышает значение О/С. Такой характер диаграммы позволяет сделать вывод, что извлечение кислорода из материала происходит в основном за счет его удаления вместе с углеродом (за счет образования углеродсодержащих газов СО и СО2), а не с водородом (за счет образования воды) [9].
С целью изучения особенностей газификации биоугля были приготовлены укрупненные партии максимально деоксигенированного торфа, теплотехнические показатели которых соответствовали показателям лабораторных образцов.
Паровоздушную газификацию биоугля проводили при 850–900°С (табл. 2). Наименьшей теплотворной способностью обладал газ, полученный газификацией биоуголя, который был карбонизирован в более мягких условиях (190°С/50 ч). При 850°С был получен генераторный газ с выходом 2.6 м3/кг и теплотворной способностью 3484 кДж/м3. Теплотворная способность была близка к показателям газа, получаемого паровоздушной газификацией торфа, составляющей 3500–4000 кДж/м3 [1]. Однако при паровоздушной газификации торфа отношение Н2/СО обычно не превышает единицы. В случае использования биоугля этот показатель был равен 2.3, т.е. по своему химическому составу такой газ пригоден для использования в качестве сырья при получении метанола и жидких углеводородов по реакции Фишера-Тропша. В сравнении с другими биоуглями он содержал меньшее количество СО, что может быть объяснено высокой степенью декарбоксилирования материала в процессе гидротермальной карбонизации, которая привела к глубокой деоксигинации [10]. Количество кислорода в составе биоугля, полученного при 190°С/50 ч, было вдвое меньше, чем у биоугля, полученного при той же температуре, но меньшем времени обработки.
Таблица 2.
Влияние условий паровоздушной газификации биоугля на состав генераторного газа и его теплотехнические характеристики
Условие ГТК | Условие газификации | Выход газа, м3/кг | Состав генераторного газа, % | H2/CO | Теплотворная способность, кДж/м3 | |||||||||
---|---|---|---|---|---|---|---|---|---|---|---|---|---|---|
Т, °С | время, ч | Т,°С | время, мин | расход | СО | Н2 | N2 | CH4 | CO2 | |||||
био-уголь, г/ч | воздух, л/ч | вода, г/ч | ||||||||||||
190 | 10 | 850 | 75 | 65 | 110 | 35 | 2.2 | 12.3 | 17.2 | 45.9 | 2.4 | 22.1 | 1.4 | 4275 |
900 | 90 | 65 | 110 | 70 | 2.1 | 10.7 | 24.9 | 37.9 | 2.6 | 23.9 | 2.3 | 4951 | ||
190 | 50 | 850 | 75 | 54 | 119 | 35 | 2.6 | 7.2 | 16.7 | 48.4 | 2.2 | 25.6 | 2.3 | 3484 |
220 | 10 | 850 | 125 | 65 | 118 | 38 | 2.7 | 8.7 | 20.7 | 41.3 | 4.3 | 25.0 | 2.4 | 4820 |
850 | 125 | 65 | 118 | 76 | 2.8 | 11.4 | 23.2 | 38.8 | 2.6 | 23.9 | 2.0 | 4863 |
Повышение температуры газификации биоугля, полученного при 190°С/10 ч, с 850 до 900°С, а также расхода воды в системе способствовало увеличению доли горючих газов (общая концентрация СО и Н2 выросла с 29 до 36%), что привело к возрастанию теплотворной способности газа до почти 5000 кДж/м3. Отношение Н2/СО при этом оставалось практически неизменным. Биоуголь, полученный в более жестких условиях (220°С/10 ч), при 850°С позволял получать генераторный газ с несколько большим выходом 2.8 м3/кг (табл. 2). В этом случае забалластированный генераторный газ содержал меньше азота (38%) и гораздо больше горючих примесей (общая доля СО и Н2 составляла 37%), что обуславливало его более высокую теплотворную способность (4820 кДж/м3). Отношение Н2/СО в газе превышало величины 2.4. Увеличение подачи воды в зону газификации этого биоугля благоприятно повлияло на течение процесса: увеличился выход газа (до 2.8 м3/кг), возросла доля горючих примесей (до 47.5%, включая метан), отношение Н2/СО составило 2.5, как следствие, теплотворная способность газа увеличилась до 4863 кДж/м3.
Таким образом, при изучении паровоздушной газификации биоуглей, полученных методом гидротермальной карбонизации при различных условиях, было установлено, что длительная обработка сырья (50 ч) приводила к значительному увеличению углерода в материале. Однако полученный генераторный газ был сильно забаластирован и обладал низкими значениями теплотворной способности. Увеличение температуры гидротермальной обработки торфа позволяло не только увеличить выход газа, но и улучшить его теплотворную способность.
Список литературы
Тимофеева С.С., Мингалеева Г.Р. // Изв. ТПУ. Сер. Техника и технологии в энергетике. 2014. Т. 325. № 4. С. 46.
Афанасьев А.Е., Инишева Л.И., Ковалев Н.Г., Константинов В.К., Лисс О.Л., Малик Л.К., Маслов Б.С., Маслов С.Г., Мукина Л.Р., Оспенникова Л.А., Панов В.В., Поздняков А.И., Шаманаев В.А. Концепция охраны и рационального использования торфяных болот России. Под ред. Инишевой Л.И. Томск: ЦНТИ, 2005. 97 с.
Лаптев А.Г., Лаптедульче Н.К., Сергеева Е.С. // Тр. Академэнерго. 2007. № 4. С. 28.
Богданов Н.Н., Ворона Д.А., Глинкер И.С. Газификация фрезерного торфа. М.–Л.: Госэнергиздат, 1959. 120 с.
Коллеров Л.К. Газомоторные установки. М.–Л.: МАЗГИШ, 1951. 240 с.
Никифоров В.А. Разработка торфяных месторождений и механическая переработка торфа. Минск: Высш. шк., 1968. 331 с.
Штин С.М. Гидромеханизированная добыча торфа и производство торфяной продукции энергетического назначения. Под ред. Ялтанца И.М. М.: Изд-во “Горная книга”, 2012. 360 с.
Крылова А.Ю., Зайченко В.М. // ХТТ. 2018. № 2. С. 1. [Solid Fuel Chemistry, 2018. № 2. P. 1. https://doi.org/10.3103/S0361521918020076]https://doi.org/10.7868/S002311771802007X
He C., Giannis A., Wang J-Y. // Energy. 2013. V. 111. P. 257.
Wei Y., Hui W., Meng Z., Jiayu Z., Jie Z., Shengji W. // Bioresource Technol. 2016. V. 205.
Дополнительные материалы отсутствуют.
Инструменты
Химия твердого топлива