Химия твердого топлива, 2022, № 5, стр. 60-72
ЭФФЕКТИВНОСТЬ ПРОИЗВОДСТВА ДРЕВЕСНОГО ГРАНУЛИРОВАННОГО ТОПЛИВА
В. К. Любов 1, *, А. Н. Попов 1, **, П. Д. Алексеев 1, ***
1 ФГАОУ ВО Северный (Арктический) федеральный университет имени М.В. Ломоносова
(САФУ имени М.В. Ломоносова)
163002 Архангельск, Россия
* E-mail: v.lubov@narfu.ru
** E-mail: a.n.popov@narfu.ru
*** E-mail: alecseevpavel@gmail.com
Поступила в редакцию 07.04.2022
После доработки 07.04.2022
Принята к публикации 08.06.2022
- EDN: MGQVVP
- DOI: 10.31857/S0023117722050073
Аннотация
Проведено комплексное исследование промышленной линии гранулирования побочных продуктов лесопильного производства. Определены энергетическая эффективность ее работы, воздействие на окружающую среду и затраты электроэнергии на основное и вспомогательное оборудование. Предложены рекомендации по снижению удельных расходов топлива, электроэнергии и выбросов вредных ингредиентов при производстве гранулированного биотоплива.
Во многих странах мира для уменьшения воздействия “парниковых” газов на климат планеты активно проводится замена ископаемых топлив биотопливом. Важным шагом на пути активизации работ, направленных на снижение выбросов “парниковых” газов, явилось принятие в 1997 г. Киотского протокола к Рамочной конвенции ООН по предотвращению глобального изменения климата. Положения Киотского протокола получили дальнейшее развитие в Парижском соглашении по сдерживанию климатических изменений, которое подписали более 170 стран. Одним из ключевых положений данного соглашения является долгосрочный план по скорейшему снижению выбросов парниковых газов и достижению баланса, между возникающими в результате деятельности человека парниковыми газами, и их поглощением морями, почвой и лесами – ко второй половине ХХI века. Таким образом, намечен переход к безуглеродной экономике [1, 2] и экологически чистой и ресурсосберегающей энергетике [3, 4], что полностью соответствует приоритетным направлениям Стратегии научно-технологического развития РФ [5].
В технологическом цикле предприятий лесопромышленного комплекса образуется значительное количество побочных продуктов заготовки, обработки и переработки древесины, однако они относятся к трудносжигаемым топливам. Перспективное направление их облагораживания – гранулирование. Наша страна располагает огромным сырьевым потенциалом для производства прессованного биотоплива [6].
В ООО “Регион-Лес” на протяжении ряда лет успешно ведутся работы по комплексному повышению эффективности использования древесного сырья. Так, в 2018 г. был открыт лесопильный комплекс в Шенкурском районе Архангельской области, в состав которого в 2019 г. вошел новый завод по производству древесных гранул из побочных продуктов лесопильного производства, который обеспечил выпуск гранул диаметром 6 мм.
Цель данной работы – комплексное исследование эффективности производства древесного гранулированного топлива и разработка рекомендаций по снижению удельных расходов энергоресурсов и выбросов вредных ингредиентов.
ОБЪЕКТ ИССЛЕДОВАНИЯ
Завод по производству древесных гранул оборудован одной производственной линией и представляет собой автоматизированное производство, обеспечивающее совмещение различных технологических процессов (рис. 1) при изменении параметров исходного сырья и топлива, погодных и климатических условий, параметров работы оборудования и т.д. При этом в качестве сырья используются опилки и щепа, полученная в результате измельчения остатков лесопиления, непригодных для применения в качестве пиломатериалов.
Для получения теплового агента и последующей сушки измельченного сырья применяются отходы лесопильного производства: кора и щепа. При относительной влажности коры более 50% используется смесь коры со щепой, соотношение данных компонентов в топливной смеси устанавливается опытным путем.
Производственный участок, где установлены топливный бункер, стокерный приемник древесного сырья, оборудованный четырьмя гидростанциями, и теплогенератор с искроуловителем имеет “полуоткрытую” компоновку, т.е. оборудован только крышей. Из древесного топлива с помощью дискового сепаратора СД-7Ш отделяется крупная фракция и далее топливо по скребковому наклонному транспортеру МТ589-73 подается в шахтный дозатор с гидравлическим толкателем ДШГТ-1190, который обеспечивает его дозированную подачу на наклонно-переталкивающую решетку теплогенератора, имеющую 11 рядов колосников.
Теплогенератор имеет модульную конструкцию камерного типа и включает в себя топку с подвижной колосниковой решеткой, камеру догорания, куда подается третичный воздух, смесительную камеру и трубу аварийного дымоудаления. В топочной камере реализована ступенчатая схема сжигания кородревесного топлива. С целью уменьшения потерь тепла в окружающую среду теплогенератор имеет воздушную “рубашку” охлаждения, для подачи воздуха в которую установлен центробежный вентилятор.
Для получения продуктов сгорания с заданной температурой смесительная камера оснащена воздуховодами и вентиляторами, при этом регулирование количества воздуха подаваемого в дымовые газы обеспечивается с помощью частотных преобразователей. Температура на выходе из смесительной камеры поддерживается автоматически с пульта управления теплогенератора. Дымовые газы поступают в искроуловитель динамического типа, состоящий из двух вертикальных циклонов с зольниками, где улавливаются золовые частицы и частицы недогоревшего топлива. Далее газы поступают в сушильный барабан, при вращении которого происходит перемешивание древесного материала с горячими газами. При этом происходит испарение влаги, тем самым достигается относительная влажность материала на выходе из сушилки 10–13%.
До сушильного барабана древесное сырье проходит дисковый и магнитный сепараторы и молотковую дробилку (рис. 1). Измельченное сырье при помощи пневмотранспорта, циклона и шлюзового перегрузчика направляется в бункер-распределитель, из которого шнековым дозатором подается в смесительный участок газохода перед одноходовой сушилкой барабанного типа, где теплоноситель подхватывает влажное сырье и транспортирует его в сушилку. Длина сушилки составляет 11.7 м, а диаметр – 2.86 м. Из сушильного барабана древесное сырье вместе с влажными газами по трубопроводу попадают в циклон СК-ЦМ-34-2200, где сырье отделяется от сушильного агента, который с помощью дымососа выбрасывается в атмосферу через дымовую трубу диаметром 0.8 м и высотой 14 м.
Высушенное сырье из нижней части циклона шлюзовым перегрузчиком направляется в аэросепаратор через приставку-влагомер. Датчик влагомера производит зондирование древесного материала радиоволнами метрового диапазона и определяет его диэлектрическую проницаемость, на основании которой вычисляется влажность. Значение которой определяет необходимость корректировки режимов сушки.
В аэросепараторе обеспечивается удаление из высушенного материала крупных частиц. После чего древесный материал направляется в дробильную камеру молотковой дробилки ДМ 2 × 37, оборудованной сетками. Под воздействием ударной нагрузки материал разрушается, все частицы, имеющие размер меньше отверстий сит, удаляются из дробильной камеры с помощью системы пневмотранспорта и направляются в циклон СК-ЦН-34-1200. Из циклона мелкодисперсное древесное сырье с помощью шлюзового затвора и скребкового транспортера подается в бункер-ворошитель. Мелкие частицы древесины и пыль, не уловленные в циклоне, осаждаются в аспирационном рукавном фильтре.
Из бункера-ворошителя мелкодисперсный материал с помощью шнекового дозатора подается в смеситель шнекового типа, после чего гомогенизированный материал направляется в пресс-гранулятор фирмы Munch. В рабочей камере пресса мелкодисперсный древесный материал продавливается через радиальные отверстия матрицы с помощью прижимающих роликов, что приводит к формированию гранул. Выходящие из отверстий матрицы гранулы обламываются с помощью ножа, падают вниз и выводятся из пресс–гранулятора.
На выходе из пресса гранулы имеют высокую температуру, поэтому они направляются с помощью скребкового транспортера и элеватора в воздушную охладительную установку, в которой происходят физико-химические изменения, в результате которых гранулы приобретают необходимую прочность. Поток воздуха от охладителя вместе с древесной пылью поступает в аспирационный рукавный фильтр, где пыль осаждается.
Охлажденные пеллеты поступают на вибросито, которое имеет ячейки диаметром 3.1 мм и электропривод. С помощью вибросита отделяется несгранулированный материал, который по линии пневмотранспорта поступает в циклон СК-ЦН-34-1400, где осаждается и с помощью шлюзового затвора и скребкового транспортера направляется в бункер-ворошитель пресса для повторной переработки. Мелкая древесная пыль, не уловленная в циклоне, осаждается в аспирационном рукавном фильтре. К сожалению, возврат древесной пыли, уловленной в рукавных фильтрах, в производственный процесс не производится.
Топливные гранулы после вибросита при помощи элеватора направляются в бункер готовой продукции для дальнейшей фасовки в биг-бэги и отправки на склад.
МАТЕРИАЛЫ И МЕТОДЫ ИССЛЕДОВАНИЯ
Экспериментальные исследования проводились в соответствии с требованиями, предъявляемыми к промышленно-эксплуатационным испытаниям второй категории сложности [7]. Для определения состава продуктов сгорания использовался газоанализатор “Testo-350 XL”. Теплотехнические характеристики топлива, исходного сырья и готовых гранул определяли согласно ГОСТ Р 54186-2010, ГОСТ Р 54211-2010, ГОСТ Р 54185-2010 и ГОСТ Р 54191-2010, а удельную теплоту сгорания – с помощью калориметра IKA C 2000 basicVersion 2 с жидкостным криотермостатом LOIP FT-216-25 в соответствии с ISO 1928. Исследования гранулометрических составов топлива, исходного сырья, древесных гранул и очаговых остатков проводились с помощью анализаторов: “029” и АS 200 Control в соответствии с ГОСТ Р 54188-2010, ГОСТ Р 54189-2010. Механическая прочность и истираемость гранулированного топлива определялись в соответствии со стандартом EN 15210-1 с использованием тестера NHP 100. Определение полей скоростей и расходов газов и воздуха выполнялось с помощью пневмометрической трубки, крыльчатого анемометра и микроманометра прецизионного прибора “Testo-435”. Результаты исследования полей скоростей использовались для определения концентрации твердых частиц в газах. При этом применялся метод внутренней фильтрации [8], для реализации которого использовались аспирационная установка “ОП-442 ТЦ”, пылезаборная трубка, фильтровальные патроны и др.
Температуры наружных поверхностей оборудования линии гранулирования определялись с помощью пирометра и тепловизора “Testo 885-2”. Расход топлива определялся по уравнению обратного теплового баланса. Обработка экспериментальных данных проводилась с помощью многомодульного программно-методического комплекса [9]. Твердые частицы, уловленные из потока отработанного сушильного агента, исследовались на электронном растровом микроскопе Zeiss SIGMA VP с целью определения их структуры, размера, формы и количественного состава, входящих элементов.
ОБСУЖДЕНИЕ РЕЗУЛЬТАТОВ
При проведении комплексного исследования эффективности работы завода по производству древесных гранул в топку теплогенератора подавалось древесное топливо, в составе которого преобладала щепа (~68%), доля коры составляла ~7.8%, а опилок – 24.2%. Во всех опытах сжигаемое древесное топливо имело высокую степень неоднородности гранулометрического состава (средний коэффициент полидисперсности n = 1.547, а коэффициент, характеризующий крупность состава b = 2.019 × 10–7), результаты исследования которого приведены на рис. 2.
Рис. 2.
Изменение фракционного состава древесного материала в процессе гранулирования и работы теплогенератора: 1 – исходное сырье до дискового сепаратора; 2 – сырье, отсеянное в аэросепараторе; 3 – сырье после сушилки и аэросепаратора; 4 – мелкодисперсный древесный материал перед прессом-гранулятором; 5 – древесные гранулы; 6 – топливо для теплогенератора; 7 – шлак из топки.
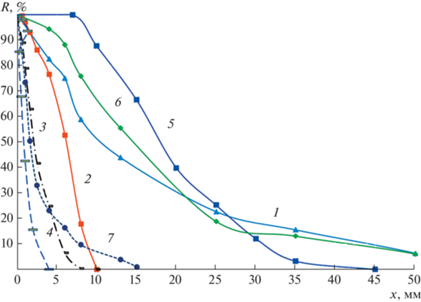
Влажность древесного топлива на рабочую массу при проведении исследований составляла 43.55%; зольность – 0.55%; а низшая теплота сгорания $Q_{i}^{r}$ = 9.553 МДж/кг. Данные теплотехнические и гранулометрические характеристики древесного топлива приемлемы для используемого теплогенератора.
Проба исходного сырья была отобрана из стокерного приемника до дискового сепаратора, ее гранулометрический состав был неоднородный (n = 1.035; b = 3.982 × 10–5), интегральная зерновая характеристика приведена на рис. 2. Необходимо учитывать, что дисковый сепаратор повышает степень однородности гранулометрического состава исходного сырья и его тонкость. Теплотехнические характеристики исходного древесного сырья и сырья после барабанной сушилки приведены в табл. 1.
Таблица 1.
Некоторые результаты энергетического обследования линий гранулирования
Показатель | Опыт № 1 | Опыт № 2 | Опыт № 3 |
---|---|---|---|
Производительность теплогенератора, Q, МВт | 1.96 | 1.98 | 1.97 |
Потери тепла: с химнедожогом, q3, % | 1.12 | 0.93 | 1.13 |
с мехнедожогом, q4, % | 0.09 | 0.09 | 0.09 |
в окружающую среду, q5, % | 6.23 | 6.06 | 6.10 |
со шлаком, q6, % | 0.03 | 0.03 | 0.03 |
Полный расход биотоплива, В, т/ч | 0.982 | 0.965 | 0.983 |
Эмиссия NOx, мг/МДж | 75 | 68 | 80 |
Эмиссия СO, мг/МДж | 168 | 163 | 175 |
КПД брутто теплогенератора с учетом искроуловителя, ηтг, % | 92.54 | 92.89 | 92.66 |
Температура газов перед сушилкой, ϑс.а, °С | 255 | 353 | 341 |
Избыток воздуха в сушильном агенте, αс.а | 9.29 | 8.02 | 9.04 |
Избыток воздуха в газах за сушилкой, αух | 9.44 | 8.17 | 9.19 |
Влажность сырья до и после сушилки, $W_{t}^{r}$, % | 54.14/13.20 | 54.14/12.20 | 54.14/12.30 |
Зольность сырья до и после сушилки, Аd, % | 0.34/0.36 | 0.34/0.36 | 0.34/0.36 |
Выход летучих до и после сушилки, Vdaf, % | 84.50/84.28 | 84.50/84.25 | 84.50/84.25 |
Низшая теплота сгорания сырья до и после сушилки, $Q_{i}^{r}$, МДж/кг | 7.316/15.877 | 7.316/16.091 | 7.316/16.070 |
Температура газов после пылеуловителя, ϑпу, °С | 76 | 77 | 76.5 |
Удельный расход условного топлива на 1 т гранул, в, кг | 272.1 | 218.9 | 225.4 |
Влажность древесных гранул, $W_{t}^{r}$, % | 7.40 | ||
Зольность гранул на сухую массу, Аd, % | 0.37 | ||
Выход летучих веществ на горючую массу, Vdaf, % | 84.25 | ||
Кажущаяся плотность, ρк, г/см3 | 1.15 | ||
Насыпная плотность, ρнас, г/см3 | 0.64 | ||
Механическая прочность, DU, % | 98.51 | ||
Низшая теплота сгорания гранул, $Q_{i}^{r}$, МДж/кг | 17.342 |
Процесс сушки исходного древесного сырья может сопровождаться выходом летучих веществ из наиболее мелких фракций, что может приводить к потере части горючих веществ и создавать угрозу воспламенения высушиваемого материала. В исследованных режимах работы сушильной установки потери горючих веществ имели минимальные значения, так как содержание летучих веществ на горючую массу изменялось очень незначительно (табл. 1). С позиций пожарной безопасности для всех режимов работы сушильной установки температура газов на входе не должна превышать 400°С.
Балансовые опыты, основные результаты трех из которых приведены в табл. 1, были проведены в диапазоне изменения производительности линии гранулирования по готовому продукту от 1.17 до 1.43 т/ч, что значительно меньше паспортной для пресса-гранулятора (2.5 т/ч). Полный расход древесного топлива на теплогенератор в исследованном диапазоне нагрузок составлял 0.965–0.983 т/ч.
Температура газов перед сушильной установкой составляла 255–353°С, что ниже рекомендуемого значения. Это снижает экономические показатели процесса сушки и линии гранулирования в целом [10].
Энергетическое обследование показало, что распределение воздушных потоков в теплогенераторе является не оптимальным. Недостаточная подача первичного воздуха и чрезмерная подача вторичного воздуха в топку и третичного воздуха в камеру догорания уменьшили время пребывания продуктов горения в активном топочном объеме, что вызвало повышенную генерацию оксида углерода и, как следствие, увеличение потерь тепла с химическим недожогом топлива.
Учитывая отсутствие поверхностей нагрева в топке теплогенератора, процесс горения влажного древесного топлива при коэффициенте избытка воздуха αт = 2.14–2.19 сопровождался достаточно низким образованием оксидов азота (табл. 1). Расчетный расход воздуха в камеру смешения теплогенератора составлял 3077–6596 нм3/ч, а присосы холодного воздуха в газоход имели значения, близкие к нормативным [11]. Оптимизация подачи первичного и вторичного воздуха откроет дополнительные возможности по снижению выбросов оксидов азота и угарного газа.
В сушильной установке барабанного типа влажность исходного сырья снижалась с 54.14% до 12.2–13.2%, при этом количество испаренной влаги с 1 кг сырья составляло 0.466–0.472 кг/кг. Количество сушильного агента на 1 кг высушиваемого сырья изменялось в диапазоне 4.677–7.369 кг/кг, а количество испаренной влаги 1049.2–1311.2 кг/ч. Объемный расход отработанного сушильного агента с учетом испаренной влаги в исследованном диапазоне производительности установки составлял 19 075–21 940 нм3/ч. Расчетный расход отработанного сушильного агента хорошо согласуется с результатами экспериментальных замеров. Расход тепла, уносимого с уходящим из установки сушильным агентом (без учета водяных паров), составлял 315–392 Мкал/ч. В процессе сушки материала температура сушильного агента на выходе из барабана снижалась до 79–83°С.
Высушенное сырье отработанным сушильным агентом транспортируется в циклонный пылеуловитель, где отделяется от газовой среды. Учитывая, что на газоходах и корпусе дымососа тепловая изоляция отсутствует, температура отработанного сушильного агента перед дымовой трубой снижалась на 12.2–13.7°С, при температуре наружного воздуха минус 9–10°С. Таким образом, отсутствие тепловой изоляция на газоходах и корпусе дымососа снижало естественную тягу дымовой трубы, ухудшало условия рассеивания отработанных газов и, соответственно, увеличивало затраты электроэнергии на тягу. Статическое давление газов в газоходе перед дымовой трубой составляло 170 Па, что говорит о том, что дымосос работает под давлением.
Анализ гранулометрического состава высушенного сырья (рис. 2) свидетельствует о том, что степень его однородности повышается (n = 1.433), что объясняется тремя факторами: отделением крупной фракции с помощью дискового сепаратора и аэросепаратора, измельчением сырья в мельнице дробления сырого материала и уносом наиболее тонкой фракции в дымовую трубу. Воздушная сепарация позволяет отделить от высушенного сырья преимущественно частицы с размером 4.0 мм и более (рис. 2). Коэффициенты, определяющие гранулометрический состав аэроотсева, имели следующие значения: n = 2.089; b = = 1.044 × 10–8.
В процессе сушки происходит незначительное увеличение зольности сырья за счет летучей золы, вносимой сушильным агентом в материал, при этом зольность готового продукта на сухую массу незначительно увеличилась с 0.34 до 0.37%.
КПД брутто теплогенератора с искроуловителем динамического типа изменялся в диапазоне 92.54–92.89%. При определении КПД брутто теплогенератора учитывались потери тепла от химического и механического недожога, с физической теплотой шлака и провала, а также потери тепла в окружающую среду от стенок теплогенератора, газоходов и искроуловителя ($q_{5}^{*}$ ≈ 6.0% при номинальной мощности) (ηтг = 100 – q3 – q4 – q6 – $q_{5}^{*}$).
Концентрация твердой фазы в отработанном сушильном агенте после циклонного пылеуловителя при производительности теплогенератора 1.95 МВт составляла 49.7 мг/нм3. Исследования, выполненные с помощью электронного растрового микроскопа Zeiss SIGMA VP, показали, что спектр размеров частиц, выбрасываемых в атмосферный воздух через дымовую трубу, очень широк – от самых маленьких до частиц с эквивалентным размером до 400 мкм (рис. 3,а). Изучение элементного состава уносимых частиц позволило сделать вывод, что в них доминируют мелкодисперсные древесные частицы, выносимые из барабанной сушилки, которые не смог отсепарировать циклонный пылеуловитель СК-ЦМ-34-2200. Отчетливо видны волокнистая структура образца и трахеиды (рис. 3,б), которые являются основным элементом древесины хвойных пород, и на поверхности трахеид – окаймленные поры.
Рис. 3.
Микроскопические исследования частиц уноса: массив уловленных частиц (а); древесные частицы (б).
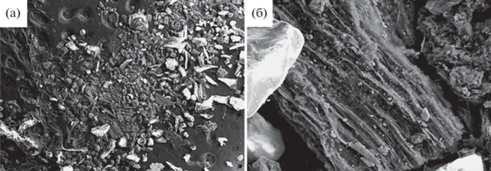
Анализ условий тепловой работы теплогенератора и сушильной установки показал, что потери тепла с уходящими газами, если использовать при их определении подход, принятый для котельных установок, составляют 15.37–17.17% (c учетом энтальпии водяных паров, выделившихся при сушке сырья). Величина данной потери повышается с уменьшением температуры сушильного агента перед барабанной сушилкой ввиду значительного увеличения его объема. В качестве балансового сечения использовалось сечение газохода после циклонного пылеотделителя, где коэффициент избытка воздуха изменялся в диапазоне αц.п = = 8.25–9.52.
Очень низкий уровень потери тепла с механической неполнотой сгорания (табл. 1) объясняется маленькой зольностью древесного топлива и низким содержанием горючих веществ в летучей золе и шлаке ($С_{{{\text{ун}}}}^{{\text{г}}}$ = 4.19–4.21%; $С_{{{\text{шл + пр}}}}^{{\text{г}}}$ = 4.62–4.75%). Результаты исследования гранулометрического состава летучей золы (рис. 4), уловленной в искроуловителе, показали, что она имеет высокую степень полидисперсности (n = 0.821) и очень тонкодисперсный фракционный состав (b = 2.631 × 10–2), при этом доминируют частицы размером менее 250 мкм, массовая доля которых составляет более 96%. Данный гранулометрический состав летучей золы косвенно свидетельствует о хорошей сепарационной способности камеры догорания и высокой степени очистки газов в динамическом искроуловителе.
Рис. 4.
Гранулометрический состава летучей золы и древесной пыли: 1 – зола, уловленная искроуловителем; 2, 3, 4 – древесная пыль, уловленная рукавными фильтрами аспирационных линий: 2 – охладительной установки; 3 – системы пневмотранспорта высушенного материала после мельницы; 4 – несгранулированного материала.
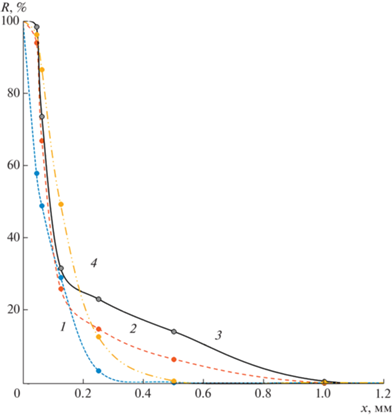
Исследования распределения горючих веществ по фракциям в летучей золе показали, что максимальное содержание горючих имеют частицы с размером 250 мкм и более (рис. 5). Однако их массовая доля в летучей золе мала, поэтому определяющее влияние на величину механического недожога топлива оказывает содержание горючих веществ в частицах менее 45 мкм.
Рис. 5.
Содержание горючих веществ в летучей золе теплогенератора: по фракциям (столбцы с заливкой – левая ось ординат); с учетом массовых долей различных фракций (столбцы без заливки – правая ось ординат).
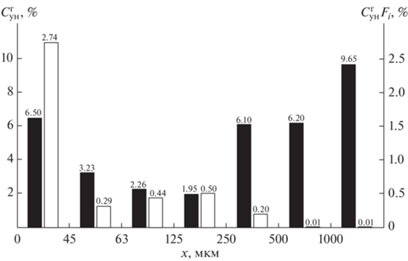
Результаты исследования гранулометрического состава усредненной пробы шлака (рис. 2), отобранной из разных зон камеры сгорания, показали, что он имеет полифракционный (n = 0.852), мелкодисперсный (b = 1.131 × 10–3) гранулометрический состав. Исследования распределения горючих веществ по фракциям показали, что максимальное содержание горючих имеют частицы шлака с размером 2.5 мм и более (рис. 6). Однако их массовая доля в шлаке не велика, поэтому определяющее влияние на величину механического недожога топлива оказывает содержание горючих веществ в частицах шлака менее 1.0 мм.
Рис. 6.
Содержание горючих веществ в шлаке теплогенератора: по фракциям (столбцы с заливкой – левая ось ординат); с учетом массовых долей различных фракций (столбцы без заливки – правая ось ординат).
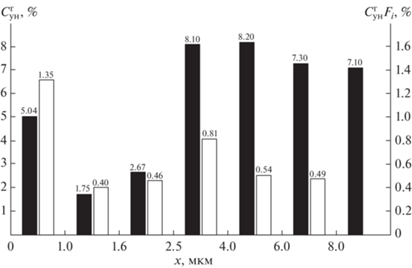
Большие значения потери тепла в окружающую среду для теплогенератора с искроуловителем и газоходами (табл. 1) объясняются “полуоткрытой” компоновкой данного производственного участка, а также отсутствием тепловой изоляции на газоходах, температура газов в которых составляла 255–353°С. Кроме того, обмуровка и изоляция ограждающих конструкций теплогенератора во многих участках не обеспечивала выполнение требований правил. Результаты замеров температур наружных поверхностей ограждающих конструкций показали, что для теплогенератора (рис. 7,а) температура в некоторых зонах достигает 81°С, для искроуловителя 170°С, а для газоходов более 300°С (рис. 7,б).
Рис. 7.
Тепловизионная съемка: левой стены теплогенератора (а); задней стены смесительной камеры и газохода сушильного агента (б); смесительной камеры барабанной сушилки (в).
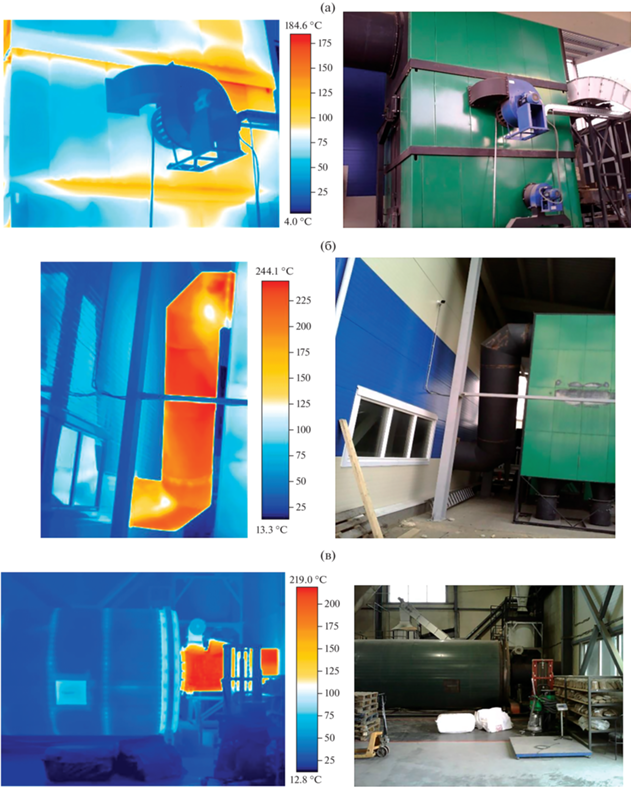
Для других элементов сушильной линии потери тепла в окружающую среду составили: барабанная сушилка q5 = 0.7%, циклонный пылеотделитель с аэросепаратором и газоходами в пределах цеха – 1.27 + 0.74 = 2.01%. Необходимо учитывать, что перед барабанной сушилкой газоход подвода сушильного агента и смесительный участок изоляции не имеют и температура их стенок составляет 250–350°С (рис. 7,в). Для исключения возможных погрешностей, возникающих при реализации относительного метода, была произведена тепловизионная съемка всех элементов обследуемой линии.
При проведении балансовых опытов КПД брутто теплогенератора и сушильной установки (с учетом смесительной камеры, искроуловителя, аэросепаратора, циклонного пылеотделителя и соединительных газоходов), если использовать при его определении подход, принятый для котельных установок, изменялся в диапазоне от 75.37 до 77.52%. Если при определении КПД брутто установки считать полезно используемой теплотой – теплоту, затраченную на нагрев древесного сырья и испарение из него влаги, а подведенной теплотой – располагаемую теплоту древесного топлива, поступающего в топку теплогенератора с учетом его расхода, то тогда КПД брутто такой установки находится в диапазоне 34.13–42.76%.
Удельный расход условного топлива на выработку 1 т гранул при проведении балансовых опытов изменялся в диапазоне 218.9–272.1 кг. С увеличением температуры сушильного агента и производительности установки его величина значительно снижается [10]. Однако режимы эксплуатации сушильных барабанов с температурой газов на входе более 400°С характеризуются высокой пожароопасностью. Результаты первичного обобщения данных, полученных при проведении исследовательских работ на трех предприятиях региона, на двух из которых производят гранулы диаметром 8 мм, приведены на рис. 8. Необходимо отметить, что относительная влажность исходного сырья имела при этом следующие значения 51.35–55.30%. На одном из объектов линии гранулирования были оборудованы теплогенераторами с неподвижными колосниковыми решетками и очень несовершенной системой ввода вторичного воздуха, что вызвало большие потери тепла с химической неполнотой сгорания рис. 8 (данные, обозначенные треугольниками).
Рис. 8.
Влияние температуры сушильного агента на удельный расход условного топлива на выработку 1 т гранул.
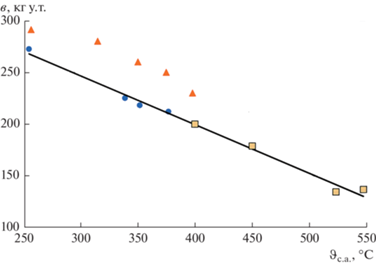
При проведении энергетического обследования максимальная тепловая мощность теплогенератора составляла 1.98 МВт (опыт № 2). Однако конструктивные характеристики теплогенератора и мощность установленных вентиляторов позволяют ему устойчиво работать с теплопроизводительностью более 2 МВт, при условии нормального схода топлива в топливной шахте и теплотехнических характеристиках сжигаемого древесного топлива не хуже, чем имевших место при проведении исследовательских работ (табл. 1).
Мелкие частицы древесной пыли, не уловленные в циклоне СК-ЦН-34-1200, отделяющем высушенное и измельченное сырье, осаждаются в аспирационном рукавном фильтре. Результаты исследования гранулометрического состава данной пыли (рис. 3) показали, что она имеет полидисперсный (n = 1.347), тонкофракционный состав (b = 5.624 × 10–4); при этом в ней доминируют частицы с размером 125 > х ≥ 45 мкм, массовая доля которых составляет более 66%.
Отбор мелкодисперсного древесного материала, идущего в пресс-гранулятор, был выполнен до бункера-ворошителя. Его анализ показал, что древесный материал имеет полидисперсный гранулометрический состав (рис. 2) (n = 1.747; b = = 6.051 × 10–6), при этом доминируют частицы с размером 2000 > х ≥ 250 мкм, массовая доля которых составляет около 73%. Относительная влажность мелкодисперсного древесного сырья перед его увлажнением составляла 11.07%.
После пресс-гранулятора готовые гранулы поступают на скребковый транспортер и далее элеватором подаются в колонну охлаждения. Режим работы которой оказывает сильное влияние на их прочностные свойства [12]. Поток воздуха от охладителя вместе с древесной пылью поступает через аспирационную трассу в рукавный фильтр, где пыль осаждается и выводится из технологического процесса. Результаты исследования гранулометрического состава данной пыли (рис. 3) показали, что она имеет полидисперсный (n = 1.175), тонкофракционный состав (b = 2.102 × 10–3); при этом в ней доминируют частицы с размером 125 > х ≥ 45 мкм, массовая доля которых составляет более 67%.
Мелкодисперсная пыль, не уловленная циклоном СК-ЦН-34-1400 линии отделения несгранулированного материала, транспортирующим агентом направляется в рукавные фильтры. Результаты исследования гранулометрического состава данной пыли (рис. 3) показали, что она имеет полидисперсный (n = 1.428), тонкофракционный состав (b = 4.129 × 10–4); при этом в ней доминируют частицы с размером 250 > х ≥ 63 мкм, массовая доля которых составляет более 73%.
Топливные гранулы после вибросита при помощи элеватора перемещаются в бункер готовой продукции для дальнейшей фасовки в биг-бэги. Исследование гранулометрического состава древесных гранул показало (рис. 2), что они имеют довольно однородный гранулометрический состав (n = 4.338), (b = 1.248 × 10–19). В гранулах преобладают пеллеты длиной 7.0 ≤ L < 25 мм, доля которых составляет более 87 мас. %. Содержание крошки составляет менее 1%, что соответствует требованиям действующих стандартов. По теплотехническим показателям и механической прочности произведенные древесные гранулы соответствуют требованиям российских и европейских стандартов.
При проведении комплексного энергетического обследования был выполнен анализ количества электроэнергии, потребляемой для производства древесных гранул. Расчет мощности, потребляемой каждым элементом технологической схемы, проводился в соответствии с рекомендациями [13]. При этом каждые 10–14 мин фиксировались все параметры, характеризующие работу электрооборудования и выводимые на мониторы пульта управления. В дальнейшем проводились обработка полученных данных и определение средних значений потребляемой мощности.
Напряжение в электросети в соответствии с данными, выводимыми на монитор, в среднем составляло 210 В, что свидетельствует о существенных потерях напряжения в сети. В ходе проведения энергообследования был выполнен анализ потребляемой мощности оборудованием каждого производственного участка, при этом результаты итогового обобщения для электрооборудования всего завода приведены на рис. 9. Полученные результаты позволили сделать вывод, что удельный расход электроэнергии на производство 1 т гранул при температуре наружного воздуха минус 9–10°С составил 262.7 кВт⋅ч.
Рис. 9.
Потребляемая мощность электрооборудованием завода по производству древесных гранул: 1, 2, 3, 4 – гидростанции № 1 – № 4, 5 – транспортер L-образный, 6 – сепаратор дисковый, 7 – транспортер скребковый, 8 – питатель двухшнековый, 9 – магнитный сепаратор, 10 – дробилка сырого материала, 11 – вентилятор, 12 – шлюзовый перегрузчик, 13 – бункер распределитель, 14 – дозатор шнековый, 15 – сушильный барабан, 16 – дымосос, 17 – шлюзовый перегрузчик 1, 18 – дробилка сухого материала, 19 – вентилятор, 20 – шлюзовой перегрузчик 2, 21 – транспортер скребковый, 22 – бункер-распределитель, 23 – дозатор шнековый, 24 – смеситель, 25 – пресс-гранулятор, 26 – транспортер скребковый, 27 – элеватор 1, 28 – колонна охлаждения, 29 – элеватор 2, 30 – вентилятор охлаждения, 31 – шлюзовый перегрузчик 3, 32 – вентилятор несгранулированного остатка, 33 – шлюзовой перегрузчик 4.
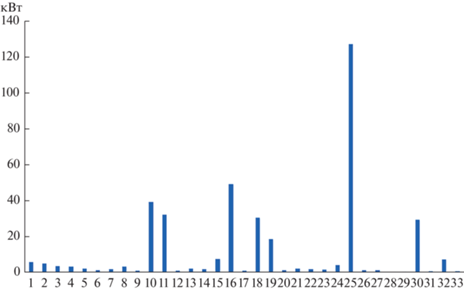
Исходя из результатов энергообследования основными потребителями электроэнергии в технологическом цикле завода являются электродвигатели следующего оборудования: пресса-гранулятора, дымососа, молотковой дробилки для измельчения сырого древесного материала, вентилятора системы транспортировки измельченного сырого материала, молотковой дробилки для измельчения сухого древесного материала, вентиляторов охладительной установки и систем транспортировки измельченного сухого материала и несгранулированного сырья, барабанной сушилки.
ЗАКЛЮЧЕНИЕ
Эффективность работы сушильной установки определяется температурой газов на ее входе, чем выше данная температура, тем меньше расход топлива и затраты электроэнергии на производство древесных гранул. Однако повышение температуры сушильного агента увеличивает пожароопасность установки. Компромиссным решением для сушильных установок данного типа являются режимы их работы с температурой агента на входе до 400°С, которые позволят при приемлемых удельных затратах топлива и электроэнергии обеспечить пожаробезопасность установки.
Определяющее влияние на экологические показатели линии гранулирования оказывает эффективность работы теплогенератора. Однако не оптимальный воздушный режим работы теплогенератора, отсутствие в полном объеме средств контроля теплового и воздушного режима, а также состава уходящих газов приводят к повышенной генерации угарного газа, существенным потерям тепла с химнедожогом топлива и повышенным затратам электроэнергии на тягу.
Большие значения потерь тепла в окружающую среду для теплогенератора с искроуловителем и газоходами вызваны “полуоткрытой” компоновкой данного производственного участка, а также отсутствием тепловой изоляции на газоходах. Кроме этого, обмуровка и изоляция ограждающих конструкций теплогенератора на многих участках не соответствуют требованиям действующих норм. Данные обстоятельства приводят также к снижению естественной тяги дымовой трубы, ухудшению условий рассеивания отработанных газов, конденсации водяных паров на стенках, осаждению на них мелкодисперсных древесных частиц, и, соответственно, увеличивают затраты электроэнергии на тягу, снижают жизненный цикл оборудования.
Удельный расход условного топлива на выработку 1 т гранул при проведении балансовых опытов изменялся в диапазоне 218.9–272.1 кг. С увеличением температуры сушильного агента и производительности установки его величина снижается. Имеются значительные резервы для снижения удельного расхода энергии на выработку единицы продукции.
Результаты исследования гранулометрического состава пыли, уловленной в рукавных фильтрах линий пневмотранспорта: древесного сырья, измельченного в молотковой дробилке сухого дробления; охлаждения готовых гранул; несгранулированного сырья, показали, что она имеет полидисперсный, тонкофракционный состав. При этом в древесной пыли двух первых линий пневмотранспорта доминируют частицы с размером 125> х >45 мкм, массовая доля которых составляет 66–67%. В соответствии с расчетами, выполненными по методике [14], древесная пыль всех трех линий пневмотранспорта относится к IV группе взрывоопасности, при этом критерии взрываемости имеют очень высокие значения 9.39–9.40. При эксплуатации оборудования завода необходимо обеспечить условия, исключающие возможность ее возгорания и взрывов. Кроме этого, данная древесная пыль оказывает негативное влияние на органы дыхания человека.
КПД процесса размола в мельницах и дробилках, особенно при измельчении влажных материалов, имеет очень маленькие значения, так как чрезвычайно велики затраты энергии на упругое деформирование влажного материала. Исходя из этого, при проектировании заводов по производству древесных гранул необходимо стремиться минимизировать количество древесного сырья, направляемого в молотковые дробилки сырого дробления, за счет предварительной классификации древесного сырья по размерам частиц. Реализация данного мероприятия позволяет значительно уменьшить удельный расход электроэнергии на выработку гранул.
Список литературы
Кокорин А.О. Экономическая политика. 2016. Т. 11. № 1. С. 157. [Economic Policy, 2016, vol. 11, no. 1, p. 157. https://doi.org/10.18288/1994-5124-2016-1-10]
Макаров И.А., Чен Х., Пальцев С.В. // Вопросы экономики. 2018. № 8. С. 70. [Voprosy Ekonomiki, 2018, no. 8, p. 70. https://doi.org/https://doi.org/10.32609/0042-8736-2018-4-76-94]10.32609/0042-8736-2018-4-76-94
Grigorev I., Khitrov E., Kalistratov A., Bozhbov V., Iva-nov V. // Geoconference on water resources. Forest, marine and ocean ecosystems. 2014. vol. 14. p. 407. https://doi.org/10.5593/SGEM2014/B32/S14.055
Соловьянов А.А. // Энергетическая политика. 2017. № 1. С. 56.
Трубников Г.В. // Вестник РАН. 2018. Т. 88. № 4. С. 291.
Степанов В.И., Мезина Н.А. // Вестник Российского экономического университета имени Г.В. Плеханова. 2012. № 3 (45). С. 83.
Трембовля В.И., Фингер Е.Д., Авдеева А.А. Теплотехнические испытания котельных установок. М.: Энергоатомиздат, 1991. 416 с.
Сборник методик по определению концентраций загрязняющих веществ в промышленных выбросах. Л.: Гидрометеоиздат, 1987. 140 с.
Любов В.К., Дьячков В.А. // Вторая Российская национальная конференция по теплообмену. 1998. Т. 3. С. 225.
Любов В.К. // Экология и промышленность России. 2018. Т. 22. № 7. С. 33. [Ecology and Industry of Russia, 2018, vol. 22, no. 7, p. 33. https://doi.org/https://doi.org/10.18412/1816-0395-2018-7-33-39]10.18412/1816-0395-2018-7-33-39
Кузнецов Н.В., Митор В.В. Тепловой расчет котельных агрегатов. Нормативный метод. М.: Энергия, 1973. 296 с.
Попов А.Н. Совершенствование процесса производства древесных гранул и их энергетического использования: Автореф. дис. канд. техн. наук. Архангельск: САФУ, 2017. 20 с.
Нейман Л.Р., Демирчян К.С. Теоретические основы электротехники. Т. 1; Учебник для электротехнических специальностей вузов. М.–Л.: Энергоиздат, 1981. 533 с.
РД 153-34.1-03.352-99. Правила взрывобезопасности топливоподачи и установок для приготовления и сжигания пылевидного топлива. М., 2000. 23 с.
Дополнительные материалы отсутствуют.
Инструменты
Химия твердого топлива