Химия твердого топлива, 2022, № 5, стр. 52-59
О ТЕНДЕНЦИЯХ РАСПРЕДЕЛЕНИЯ ЗОЛООБРАЗУЮЩИХ ЭЛЕМЕНТОВ И ЭЛЕМЕНТОВ-ПРИМЕСЕЙ В ПРОДУКТАХ СЖИГАНИЯ УГЛЕЙ КАА-ХЕМСКОГО МЕСТОРОЖДЕНИЯ
Н. Н. Янчат 1, *, Л. Х. Тас-оол 1, **
1 ФГБУН Тувинский институт комплексного освоения природных ресурсов СО РАН
667007 Кызыл, Россия
* E-mail: janchat62@mail.ru
** E-mail: tasool51@mail.ru
Поступила в редакцию 22.02.2022
После доработки 12.04.2022
Принята к публикации 08.06.2022
- EDN: MCCBQH
- DOI: 10.31857/S0023117722050103
Аннотация
Изучено распределение золообразующих элементов и элементов-примесей в золошлаках (ЗШ), золоуносах каахемского угля путем анализа значений коэффициентов обогащения продуктов сжигания исследованными элементами, ${\text{КО}}_{i}^{{\text{П}}}$. Рассмотрено изменение вещественного состава золы угля в золошлаковых отходах ТЭЦ, котельных и печей. Показано, что ЗШПеч и ЗШТЭЦ в сравнении с углем значительно обогащен Zn, Sb, Cr (до девятикратного!): ${\text{КО}}_{{{\text{Zn}}}}^{{{\text{ЗШ Печ}}}} = 8.9$; ${\text{КО}}_{{{\text{Sb}}}}^{{{\text{ЗШ Печ}}}} = 6.5$; ${\text{КО}}_{{{\text{Cr}}}}^{{{\text{ЗШ Печ}}}}$ = 2.9; ${\text{КО}}_{{{\text{Cr}}}}^{{{\text{ЗШ ТЭЦ}}}} = 6.3$, в то же время в ЗШКот обогащен Sb, V, Sr, Cr в пределах 10–70%, их ${\text{КО}}_{i}^{{{\text{ЗШ Кот}}}}$ = 1.7, 1.2 и 1.1 соответственно. В топках котельных и печей уголь сгорает с большим недожогом – кокса в ЗШКот 17%, в ЗШПеч 10%, что обусловлено вторичным науглероживанием поверхности золошлакового остатка продуктами термодеструкции угля.
ВВЕДЕНИЕ
Угленосность Каа-Хемского каменноугольного месторождения Улуг-Хемского бассейна связана с отложениями эрбекской свиты среднеюрского возраста, в свите содержится один повсеместно распространенный основной угольный пласт 2.2-Улуг (М = 0.85–12.0 м, преобладает 3–6 м) и пять относительно выдержанных сопутствующих пластов с рабочей мощностью 1.0–2.2 м на разрозненных участках с протяженностью 0.22–1.2 км, последние расположены выше пласта Улуг [1]; при добыче угля отрабатываются все пласты. Органическое вещество пласта Улуг сложено на 95% мацералами группы витринита (Vt), доля мацералов группы инертинита (I) 2%, группы липтинита (L) 3%; в углях сопутствующих пластов содержание мацералов Vt 82–88%, Sv 1–6%, I 5–11%, L 1–6% [1, 2].
Каахемский уголь используется в Республике Тыва для выработки электрической и тепловой энергии. Качественный показатель продукции угольного разреза Каа-Хемский согласно ТУ 032031-001-00164799-01: марка угля Г, ГЖ, размер кусков 0–300 мм, ${{A}^{d}}{\text{ }} \leqslant {\text{19}}{\text{.3\% }}$ (преобладает 10–15), $W_{i}^{r}{\text{ }} \leqslant {\text{8}}{\text{.1\% }}$, ${{V}^{{daf}}}{\text{ 46}}{\text{.0\% ,}}$ $Q_{i}^{r}{\text{ 6500}}$ ккал/кг, $S_{t}^{d}{\text{ }} \leqslant 0.9\% $, ${\text{C}}{{{\text{l}}}^{d}}{\text{ }} \leqslant {\text{0}}{\text{.6\% ,}}$ $A{{s}^{d}}{\text{ }} \leqslant {\text{0}}{\text{.02\% }}$, минеральные примеси <2.5%.
На Кызылской ТЭЦ рядовой уголь измельчают до размеров <2.5 мм, высушивают и сжигают в котлах БКЗ-75-39ФБ (тепловая мощность 60.13 МВт, производительность пара 75 т/ч), температура топочной камеры в ядре горения угля 1270–1300°С, на выходе из топки 950–1000°С, в уходящих газах 130°С. Основная часть мелкодисперсного золоуноса (~90%) улавливается в батарейных циклонах БЦ-56–224, шлак и грубодисперсный золоунос осыпается в шлакосборник. В котельных (Барнаульский котлоэнергетический завод [3]) и бытовых печах уголь сжигается в товарном виде без измельчения. По данным мэрии г. Кызыл, в 2021 г. общее количество объектов, использующих уголь для отопления жилых/нежилых зданий и помещений, составило 24 484, в том числе 18 521 индивидуальных дома, 89 водогрейных котельных с ручной топкой (КВр) с мощностью от 0.1 до 0.93 МВт и 5874 кооперативов, обществ, организаций.
Золоотвал ТЭЦ и золошлаковые отходы (ЗШО) котельных и печей, вывезенные на свалки, под воздействием ветра, жары, дождя, талых вод становятся источниками техногенного загрязнения окружающей среды. В золоотвале ТЭЦ накоплено ~250 тыс. тонн ЗШО, в настоящее время они не находят дальнейшего применения, хотя до 1993 г. местные организации выкупали ~1/3 от годового объема отходов (~34.5 тыс. т) для использования в строительстве одноэтажных сооружений (дома, гаражи, бани и др.). Между тем известно, что золошлак ТЭЦ г. Кызыл является перспективным сырьем для производства керамических стеновых материалов и зольных кирпичей [4, 5], микросферы золоуноса могут быть использованы в качестве наполнителей композитов при изготовлении тепло-, звукоизоляционных материалов и конструкций [6].
В работе проведен сравнительный анализ содержаний макроэлементов и элементов-примесей каахемских углей в золошлаках ТЭЦ, котельных и печей. Изучение структурно-вещественного и химического состава золоуносов и золошлаков имеет важное значение для понимания превращений минеральных компонентов в процессах окислительной деструкции угля, для выявления возможностей снижения негативного воздействия ЗШО на окружающую среду за счет их вторичного использования в производстве строительных и др. материалов.
МАТЕРИАЛЫ И МЕТОДЫ ИССЛЕДОВАНИЯ
Объекты исследования – рядовой уголь Каа-Хемского месторождения (n = 2, отобран на угольном разрезе), золоунос (n = 2) и золошлак (n = 2) Кызылской ТЭЦ, золошлак котельных водогрейных (n = 2), золошлак бытовых печей (n = 2). Золоунос (ЗУ) – частицы золы тонкодисперсные, уносимые дымовыми газами из пространства топочной камеры, шлак (Ш) – частицы золы агрегированные, сплавленные, полидисперсные; золошлак (ЗШ) содержит частицы шлака и крупнодисперсного золоуноса. Абсолютное большинство котельных и все домашние печи в г. Кызыл не оборудованы системами улавливания золоуноса. Пробоподготовка угля и золошлаковых продуктов выполнена согласно ГОСТу 10742-71.
Зольность угля определена по ГОСТу 11022-95 (ИСО 1171-97) при (815 ± 10)°С в условиях медленного ступенчатого повышения температуры печи (скорость 3 град/мин) для минимизации потерь микроэлементов. Потери при прокаливании (п.п.п.) золы угля, золоуноса и золошлака определены по ГОСТу 5382-2019 при (1000 ± 10)°С.
Содержания породообразующих оксидов в золе и продуктах сжигания угля (SiO2, CaO, Fe2O3, Al2O3, MgO, Na2O, K2O, TiO2, MnO, SO3, P2O5, а также Sr, Ba, Zr) определены на рентгенофлуоресцентном анализаторе СРМ-25. Содержания оксидных форм элементов-спутников кальция (SrO, BaO, ZrO2) определены расчетным путем из содержания элемента в породе с использованием коэффициента пересчета [7]. Содержание общей серы определено на спектрометре Bruker S4 Pioneer. Содержания микроэлементов в золе угля, ЗУ, ЗШ определены на масс-спектрометре ISP-MS. Анализы выполнены в ИГХ СО РАН им. А.П. Виноградова.
Состав породообразующих минералов в прозрачных шлифах угля изучен на поляризационном микроскопе ПОЛАМ Л-213М. Структура поверхности образца (золоунос, золошлак), приклеенного на двусторонний углеродный скотч, исследована на сканирующем электронном микроскопе TM-1000 HITACHI. Гранулометрический состав образца описан в соответствии с классификацией осадочных пород по Л.Б. Рухину [8], мм: грубозернистые (2–1), крупнозернистые (1.0–0.5), среднезернистые (0.5–0.25), мелкозернистые (0.25–0.10), тонкозернистые (0.1–0.05), алевритовые (0.05–0.005), пелитовые (<0.005).
Поведение (распределение) элемента в процессе углесжигания охарактеризовано по коэффициенту обогащения (${\text{КО}}_{i}^{{\text{П}}}$), передающему кратность изменения содержания элемента в продукте сжигания в сравнении с его содержанием в исходном угле [9]:
РЕЗУЛЬТАТЫ И ОБСУЖДЕНИЕ
Минеральная примесь угля. Образцы рядовых каахемских углей блестящие и полублестящие, однородные и неяснополосчатые, разбиты трещинами кливажа, в трещинах и на плоскостях скольжения присутствуют тонкие пленки карбонатов и мелкие вкрапления пирита (рис. 1). На наличие карбонатов указывает качественная реакция с 5%-ной HCl (“вскипание” с шипением), пирит определяется визуально по металлическому блеску.
Рис. 1.
Фотоснимок образцов каахемского угля: 1 – плоскости скольжения с пленками карбонатов, 2 – вкрапления пирита.
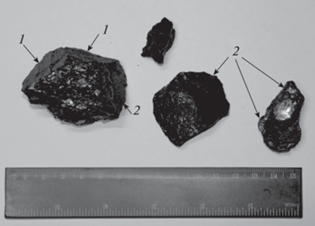
На микрофотографиях шлифов угля в поляризационном микроскопе идентифицируются обломки породообразующих минералов кварца, полевых шпатов, слоистых алюмосиликатов с алевритовой и пелитовой размерностями (рис. 2, а–г). В золе каахемского угля методом рентгенофазового анализа нами ранее [10] были определены, наряду с перечисленными, и такие минералы, как муллит, серицит, монтичеллит, кальцит, ангидрит.
Рис. 2.
Микрофотографии (ПОЛАМ Л-213М) шлифов каахемских углей: обломки породообразующих минералов кварца (1), полевых шпатов (2), слюды (3) с алевритовой (а, в, г) и пелитовой (б) размерностями.
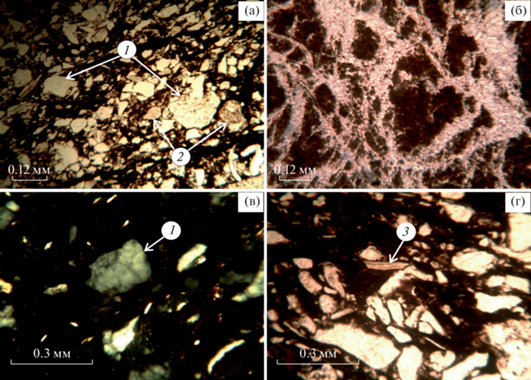
Гранулометрический состав ЗШО. Результаты ситового анализа твердых продуктов сжигания угля в разных топочных устройствах, приведены в табл. 1.
Таблица 1.
Ситовой анализ твердых продуктов сжигания угля Каа-Хемского месторождения
Продукт сжигания | Содержание, мас. % | |||||
---|---|---|---|---|---|---|
размер частиц, мм | ||||||
<0.05 | 0.05–0.1 | 0.1–0.2 | 0.2–0.5 | 0.5–1.0 | >1.0 | |
Золоунос ТЭЦ | 45.1 | 37.4 | 14.3 | 3.2 | 0 | 0 |
Золошлак ТЭЦ | 7.2 | 10.9 | 57.9 | 22.0 | 2.0 | 0 |
Золошлак котельных | 3.3 | 3.1 | 3.0 | 9.0 | 9.2 | 72.4 |
Золошлак печной | 7.3 | 16.2 | 12.2 | 14.7 | 7.7 | 42.0 |
Золошлак на ТЭЦ по окрасу светло-коричневый, содержит ~18% стекловидных образований с размерами в пределах (0.3–1.5) × 7 см, оставшаяся часть в основном мелко-среднезернистая (0.5–0.1, 80%), тонкодисперсных зерен (0.1–0.05 мм) не более 11%, алевритовых (0.05–0.005 мм) менее 7%, крупнодисперсных (1.0–0.5 мм) ~2%, золоунос светло-коричневый, дисперсность преимущественно алевритово(45%)-тонкозернистая (37%), содержание мелкозернистой фракции не более 14%.
Золошлак в котельных темнокрасно-коричневый, в основной массе грубозернистый (>1 мм, 72%), крупнозернистых частиц (1.0–0.5 мм) не более 9%, средне-мелко-тонкозернистых ~15%, алевритовых ~3%. Золошлак печной ярко-коричневый, доля грубозернистых частиц, в сравнении с ЗШ котельных, снижена до 42% при повышении относительного содержания фракции среднезернистой (27%), тонкозернисто-алевритовой (23%). Грубозернистые частицы ЗШ котельных и ЗШ печей углефицированы на 66 и 32% соответственно, что свидетельствует о неполном сгорании угля.
Вещественный состав ЗШО. Электронные снимки изученных образцов (рис. 3 и 4) отображают разнородность продуктов сгорания угля.
Рис. 3.
Микрофотографии (“TM-1000” HITACHI) продуктов сжигания каахемского угля: золоунос ТЭЦ (а), золошлак ТЭЦ (б); золошлак котельных (в), золошлак печей (г).
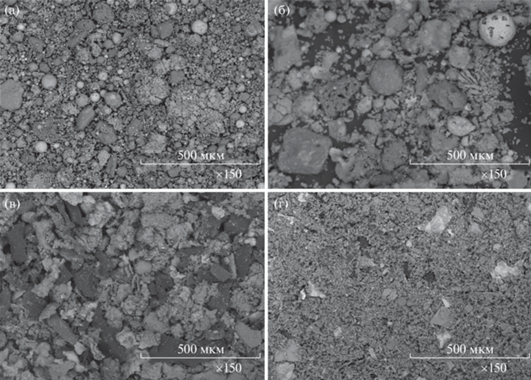
Рис. 4.
Микрофотографии (“TM-1000” HITACHI с ЭДС Bruker) и спектры частиц в продуктах сжигания угля: золоунос ТЭЦ (а), (б); золошлак котельных (в), (г); золошлак печей (д), (е).
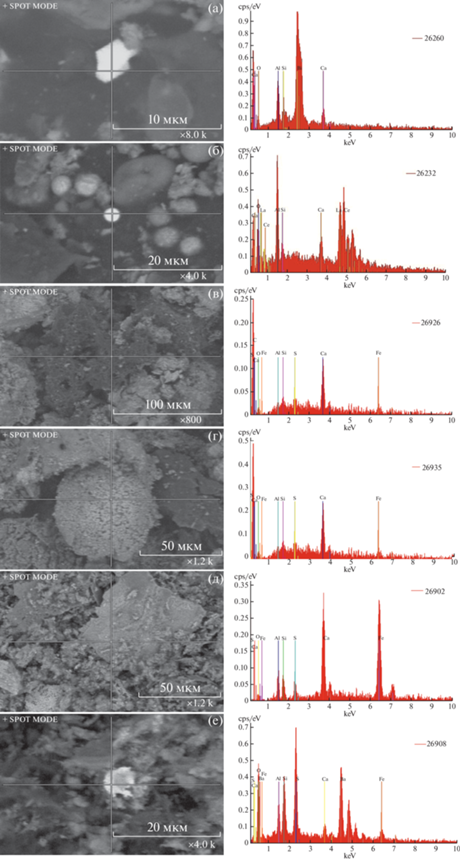
Золоуносы ТЭЦ (рис. 3, а) состоят из технических образований, большую часть которых представляют однородные микросферы алюмосиликатного состава Si (21–35%), Al (10–23%) с гладкой поверхностью и с размерами 1.5–75.1 мкм, присутствуют осколки микросфер, а также рыхлые и пористые образования с налипшими минеральными частицами. К примеру, висмут-содержащее зерно имеет состав Bi–73%, Ca–9%, O–9%, Al–7%, Si–2% (рис. 4, а), в составе цериевой редкоземельной частицы Ce (34%), La (32%), O (14%), Al (12%), Ca (5%), Si (3%) (рис. 4, б). В этих данных, подтверждающих ранние наблюдения [11] о присутствии в ЗУ ТЭЦ алюмосиликатных микросфер с содержаниями Si (25–33%) и Al (9–22%), содержатся новые дополняющие сведения о наличии отдельных зерен микроэлементов.
В образцах золошлаков ТЭЦ (рис. 3, б) преобладают плоские темные стекловидные частицы с матовым блеском, присутствуют пластинчатые, губчатые и комковатые образования с размерами 45–300 мкм, деформированные микросферулы с рельефной поверхностью (50–150 мкм), в полостях встречаются малые микросферы. Состав микросферул: Fe (30–69%), Ca (9–43%) и Si (4–35%). В силикатных частицах с содержаниями Si 8–54% и Al 8–24% присутствует Ca (6–14%) или Fe (9–16%) и элементы-примеси Mn, Ti, Na, K, S (<4%).
Золошлак котельных (рис. 3, в) сложен большей частью из темно-серых плотных крупиц и пористых губчатых образований с размерами, варьирующими в пределах 25–300 мкм, присутствуют частицы с размерами <25 мкм. Темные пористо-губчатые образования (рис. 4, в) сформированы из термически преобразованного угля (кокс, полукокс) с составом С (74%), Fe (6%), Ca (5%), Si (2%), Al (2%), S (1%), O (10%). Плотные серые округленные образования (5–221 мкм) содержат железо (5–73%) и/или кальций (6–59%), так частица с размером 62 мкм (рис. 4, г) имеет состав Fe (64%), Al (9%), Si (8%), Ca (6%), Mg (3%), O (10%).
Золошлак печной (рис. 3, г) сложен из частиц с размерами (10–150 мкм) по окрасу красных, черных/темных, светло-серых с металлическим блеском, рыхлых образований (<10 мкм) и минеральных зерен. Светло-серые зерна кальций-железо-содержащих частиц имеют состав Ca (17–44%), Fe (15–40%), S (4–18%), O (20–46%), Si (3–11%) и Al (2–9%); состав темно-серых кремнийсодержащих частиц Si (25–31%), Fe (14–17%), Al (8–15%), С (2–22%), Ca (2–3%), K (2–3%), Mg (1–3%), O (29–41%), Ti (0–2%), S (0–2%), Na (0–2%). Светло-серые частицы с металлическим блеском железистые, Fe (30–77%); на рис. 4, д показан состав одного из таких зерен с размером 62 мкм: Fe (46%), Ca (21%), Si (10%), Al (9%), S (6%) и O (8%. Состав барий-содержащей частицы (5.7 мкм) Ba (45%), O (26%), Fe (11%), S (9%) Si (5%), Al (2%), Ca (2%) (рис. 4, е).
Химический состав золы и твердых отходов сжигания рядового каахемского угля приведен в табл. 2 и 3. Уголь низкозольный (Ad 6.4%), зола угля железисто-кальциево-кремнистая: Fe2O3 (32%), CaO (23%), SiO2 (19%).
Таблица 2.
Химический состав угля Каа-Хемского месторождения, в твердых продуктах его сжигания и коэффициенты их обогащения
Компо-нент | Среднее содержание, мас. % | Коэффициент обогащения (${\text{КО}}_{i}^{{\text{П}}}$) | ||||||||
---|---|---|---|---|---|---|---|---|---|---|
уголь (n = 2) | зола (n = 2) | ЗУТЭЦ (n = 2) | ЗШТЭЦ (n = 2) | ЗШКот | ЗШПеч | ${\text{КО}}_{i}^{{{\text{ЗУ ТЭЦ}}}}$ | ${\text{КО}}_{i}^{{{\text{ЗШ ТЭЦ}}}}$ | ${\text{КО}}_{i}^{{{\text{ЗШ Кот}}}}$ | ${\text{КО}}_{i}^{{{\text{ЗШ Печ}}}}$ | |
SiO2 | 1.20 | 18.52 | 33.10 | 39.56 | 15.45 | 26.75 | 1.76 | 2.10 | 0.82 | 1.42 |
Al2O3 | 0.50 | 7.81 | 11.17 | 8.73 | 9.72 | 13.13 | 1.42 | 1.11 | 1.23 | 1.67 |
Fe2O3 | 2.02 | 31.91 | 23.48 | 22.52 | 28.84 | 21.64 | 0.74 | 0.71 | 0.91 | 0.68 |
CaO | 1.44 | 22.58 | 22.56 | 17.48 | 32.11 | 21.70 | 1.00 | 0.77 | 1.42 | 0.96 |
MgO | 0.48 | 7.57 | 5.74 | 3.29 | 7.35 | 6.14 | 0.76 | 0.44 | 0.98 | 0.82 |
TiO2 | 0.03 | 0.48 | 0.59 | 0.52 | 0.45 | 0.66 | 1.20 | 1.06 | 0.92 | 1.34 |
MnO | 0.03 | 0.49 | 0.32 | 0.42 | 0.22 | 0.27 | 0.66 | 0.87 | 0.46 | 0.56 |
Na2O | 0.04 | 0.70 | 0.70 | 1.05 | 0.97 | 1.50 | 1.00 | 1.51 | 1.39 | 2.15 |
K2O | 0.03 | 0.50 | 0.92 | 0.76 | 0.45 | 1.09 | 1.80 | 1.49 | 0.88 | 2.14 |
P2O5 | 0.003 | 0.05 | 0.05 | 0.14 | 0.08 | 0.28 | 0.96 | 2.68 | 1.53 | 5.36 |
BaO | 0.01 | 0.21 | 0.14 | 0.09 | 0.32 | 0.30 | 0.67 | 0.43 | 1.54 | 1.45 |
SrO | 0.02 | 0.35 | 0.24 | 0.13 | 0.39 | 0.33 | 0.68 | 0.37 | 1.10 | 0.93 |
ZrO2 | 0.002 | 0.03 | 0.02 | 0.02 | 0.02 | 0.02 | 0.76 | 0.76 | 0.76 | 0.76 |
SO3 | 0.56 | 8.80 | 0.97 | 5.29 | 3.63 | 6.19 | 0.11 | 0.61 | 0.42 | 0.71 |
Сумма | 100.00 | 100.00 | 100.00 | 100.00 | 100.00 | |||||
П.п.п. | 2.82 | 1.57 | 3.97 | 17.21 | 10.18 | |||||
Ad | 6.39 |
Таблица 3.
Содержание микроэлементов в каахемских углях, твердых продуктах их сжигания и коэффициенты обогащения продуктов по элементам
Компо-нент | Среднее содержание, г/т | Коэффициент обогащения (${\text{КО}}_{i}^{{\text{П}}}$) | ||||||||
---|---|---|---|---|---|---|---|---|---|---|
уголь (n = 2) | зола (n = 2) | ЗУТЭЦ (n = 2) | ЗШТЭЦ (n = 2) | ЗШКот | ЗШПеч | ${\text{КО}}_{i}^{{{\text{ЗУ ТЭЦ}}}}$ | ${\text{КО}}_{i}^{{{\text{ЗШ ТЭЦ}}}}$ | ${\text{КО}}_{i}^{{{\text{ЗШ Кот}}}}$ | ${\text{КО}}_{i}^{{{\text{ЗШ Печ}}}}$ | |
Be | 0.14 | 2.22 | 3.11 | 2.00 | 1.54 | 3.38 | 1.39 | 0.89 | 0.69 | 1.51 |
Sc | 0.35 | 5.34 | 9.05 | 9.00 | 5.59 | 7.45 | 1.67 | 1.66 | 1.03 | 1.37 |
V | 2.69 | 41.50 | 67.00 | 65.00 | 49.00 | 95.50 | 1.59 | 1.55 | 1.16 | 2.27 |
Cr | 1.82 | 28.00 | 59.00 | 180.00 | 30.00 | 82.00 | 2.08 | 6.34 | 1.06 | 2.89 |
Co | 0.92 | 14.45 | 18.50 | 11.50 | 10.35 | 37.50 | 1.28 | 0.79 | 0.72 | 2.59 |
Ni | 2.17 | 33.25 | 3.05 | 40.00 | 13.90 | 39.00 | 0.09 | 1.18 | 0.41 | 1.15 |
Cu | 3.89 | 60.50 | 46.00 | 35.00 | 59.50 | 133.50 | 0.75 | 0.57 | 0.98 | 2.19 |
Zn | 4.53 | 70.50 | 49.50 | 55.00 | 65.50 | 629.00 | 0.70 | 0.78 | 0.92 | 8.88 |
Ga | 0.83 | 12.75 | 9.05 | 16.00 | 12.45 | 16.40 | 0.70 | 1.24 | 0.96 | 1.27 |
Ge | 0.19 | 3.06 | 1.71 | 1.50 | 1.92 | 11.20 | 0.56 | 0.49 | 0.63 | 3.68 |
Rb | 0.46 | 7.00 | 20.45 | – | 3.89 | 16.70 | 2.86 | – | 0.54 | 2.33 |
Y | 1.19 | 18.40 | 20.50 | 20.00 | 17.30 | 24.00 | 1.10 | 1.07 | 0.93 | 1.29 |
Nb | 0.61 | 9.45 | 10.50 | 12.50 | 8.00 | 11.80 | 1.10 | 1.31 | 0.84 | 1.24 |
Mo | 0.24 | 3.77 | 2.02 | 3.00 | 3.07 | 8.05 | 0.53 | 0.79 | 0.81 | 2.12 |
Sn | 0.21 | 3.31 | 1.79 | 2.00 | 2.53 | 8.35 | 0.53 | 0.60 | 0.75 | 2.48 |
Sb | 0.34 | 5.48 | 8.39 | – | 9.05 | 35.00 | 1.56 | – | 1.68 | 6.51 |
La | 1.39 | 21.50 | 22.50 | 40.00 | 22.00 | 30.50 | 1.04 | 1.84 | 1.01 | 1.40 |
Ce | 3.04 | 47.00 | 44.50 | 80.00 | 45.50 | 62.00 | 0.94 | 1.68 | 0.96 | 1.30 |
Yb | 0.13 | 2.03 | 2.20 | 2.50 | 1.92 | 2.48 | 1.07 | 1.22 | 0.93 | 1.20 |
Hf | 0.34 | 5.22 | 4.59 | 5.00 | 4.08 | 4.54 | 0.87 | 0.95 | 0.77 | 0.86 |
Pb | 0.93 | 14.35 | 12.40 | 15.00 | 5.59 | 93.00 | 0.85 | 1.03 | 0.38 | 6.39 |
Bi | 0.04 | 0.68 | 0.28 | – | 0.14 | 0.98 | 0.41 | – | 0.20 | 1.43 |
Примечание. Прочерк – содержание элемента ниже предела обнаружения. |
Золошлак и золоунос угля на ТЭЦ кремнисто-железисто-кальциевый SiO2 (40 и 33%), Fe2O3 (23 и 23%), CaO (17 и 23% соответственно). Золошлак печной, подобно ЗУТЭЦ и ЗШТЭЦ, кремнисто-железисто-кальциевый SiO2 (27%), Fe2O3 (22%), CaO (22%). Золошлак котельных по составу кальциево-железисто-кремнистый CaO (32%), Fe2O3 (29%), SiO2 (15%), что достаточно близко к составу золы угля.
Содержание недожога (кокс/полукокс) в ЗУТЭЦ 1.6%, а в золошлаках ТЭЦ, золошлаках печей и котельных – 4.0, 10 и 17% соответственно. Полагаем, что существенный рост доли кокса в ЗШПеч и ЗШКот обусловлен вторичным науглероживанием поверхности золошлакового остатка продуктами термодеструкции угля; известно [12], что в условиях пиролиза каахемского угля, когда выделяемые газы удерживались в зоне реактора в помощью вентиля, выход коксового остатка повышался с 60 до 73%. Неполнота сгорания угля, очевидно, обусловлена с его специфическими особенностями: уголь пласта “Улуг” имеет низкую температуру перехода в пластическое состояние, при пластометрическом анализе пробы под давлением уголь размягчается при 250–310°С с интервалом температуры пластичности 120–190°С, толщина пластометрического слоя y > 25 мм [2]. Согласно сертификату соответствия качества угля № РОСС RU.ТУ. Н03145 (Кемеровский центр экспертизы угля, 22.01.2018 г), при испытании пробы каахемского угля в дилатометре Одибер-Арну без давления груза температура начала перехода в пластичное состояние ~350°С, интервал пластичности ∆Т 115°С, толщина пластометрического слоя y = 17 мм, выход “летучих” веществ 46–48%.
Для оценки поведения элементов-примесей в процессах сжигания угля рассмотрим результаты сравнительного анализа коэффициентов обогащения продуктов горения (${\text{КО}}_{i}^{{\text{П}}}$) по элементам (табл. 3).
В золошлаковые продукты ТЭЦ микроэлементы Sc, V, Y, Zr переходят в приблизительно равных количествах (${\text{КО}}_{i}^{{{\text{ЗУ ТЭЦ}}}}$ ≈ ${\text{КО}}_{i}^{{{\text{ЗШ ТЭЦ}}}}$). В ЗШТЭЦ и ЗУТЭЦ в сравнении с углем значительно увеличено содержание Cr (${\text{КО}}_{i}^{{{\text{ЗШ ТЭЦ}}}}$ = 6.3; ${\text{КО}}_{i}^{{{\text{ЗУ ТЭЦ}}}}$ = = 2.1). Элементы Be, Co, Rb, Sb переходят преимущественно в ЗУТЭЦ (${\text{К}}{{{\text{О}}}_{i}}$ = 1.39, 1.28, 2.86, 1.56 соответственно), а Ni, Ga, Ce – в ЗШТЭЦ (КОi = = 1.18, 1.24, 1.68). Коэффициент обогащения золоуноса и золошлака по Cu, Zn, Ge, Mo, Sn, Hf, Bi меньше единицы (КОi < 1), поэтому можно ожидать, что в условиях пылеугольного сжигания последние элементы образуют газообразные соединения, конденсирующиеся на выносимых из трубы золоуносах.
В золошлаке печном содержание Sb и Zn в сравнении с углем увеличено многократно, почти в 7 и 9 раз, кратность превышения концентрации для V, Cr, Co, Cu, Ge, Rb, Mo, Sn варьирует в пределах 2.1–3.7.
Золошлак котельных по отношению к углю обогащен элементами-примесями Sb, V, Cr, Sr (${\text{КО}}_{i}^{{{\text{ЗШ Кот}}}}$ в пределах от 1.1 до 1.7) без изменения содержаний Sc, Cu, Ga, La, Ce (${\text{КО}}_{i}^{{{\text{ЗШ Кот}}}} \approx 1$), обеднен Be, Co, Ni, Zn, Ge, Rb, Y, Nb, Mo, Sn, Yb, Hf, Pb, Bi (${\text{КО}}_{i}^{{{\text{ЗШ Кот}}}} < 0.93$). Одним из факторов, определяющих снижение содержания перечисленных микроэлементов в ЗШКот, может быть конденсация/сорбция продуктов их термических превращений на поверхности хлопьев “сажи” с последующим выносом в воздушную атмосферу. Содержание сажи, осевшей на снеговой покров, в промышленной зоне г. Кызыл достигает 73% от массы пылевой фракции снега, вблизи застроек с печным отоплением 63% [13]. Образование хлопьев сажи обусловлено высоким содержанием битумов в исходном топливе, согласно данным [12] выход каменноугольной смолы и пирогенетической воды в каахемском спекающемся угле ГЖ достигает 13%.
ЗАКЛЮЧЕНИЕ
Получены предварительные данные о распределениях макроэлементов и микроэлементов каахемского спекающегося угля в золошлаковых продуктах котлоагрегатов ТЭЦ, котельных и печей. Исходный (рабочий) уголь низкозольный (Ad 6.4%), зола железисто(32%)-кальциево(23%)-кремнистая(19%). Состав ЗШКот близок к золе угля – кальцево(32%)-железисто(29%)-кремнистый(15%). ЗШПеч, подобно ЗУТЭЦ и ЗШТЭЦ, кремнисто-железисто-кальциевый SiO2 (27%), Fe2O3 (22%), CaO (22%).
ЗУТЭЦ состоит преимущественно из однородных алюмосиликатных микросфер, имеются и рыхлые и пористые образования с вкраплениями Bi-, Ce-, La-содержащих частиц. В ЗШТЭЦ присутствуют куски плоских стекловидных масс (18%), деформированные алюмосиликатные микросферулы с содержаниями Ca (6–14%) или Fe (9–16%) и элементов Mn, Ti, Na, K, S (<4%). ЗШКот сложен плотными частицами и пористыми губчатыми образованиями с включениями частичек кокса, в последних среднее содержание C ~74%, Fe ~6%, Ca ~5%. ЗШПеч однородный, с минеральными зеренами Ca-, Fe-, Si-, Al-, Mg-, Ba-, K-, Na-, S-, O-содержащих частиц.
Уголь в котельных КВр сжигается с большим недожогом, в ЗШКот доля кокса достигает 17%, многие микроэлементы (Be, Co, Ni, Zn, Ge, Rb, Y, Nb, Mo, Sn, Yb, Hf, Pb, Bi) содержатся в меньших концентрациях, чем в угле. Очевидно, газообразные соединения перечисленных элементов выносятся в атмосферу с дымовыми газами.
Список литературы
Лебедев Н.И. Угли Тувы: Состояние и перспективы освоения сырьевой базы. Кызыл.: ТувИКОПР СО РАН. 2007. 180 с.
Угольная база России. Т. III. Угольные бассейны и месторождения Восточной Сибири. Южная часть. M.: ООО “Геоинформцентр”, 2002. 304 с.
Барнаульский котлоэнергетический завод. [Электронный ресурс]: https://bkez.ru/catalog/vodogreinye-kotly/vodogreinye-kotly-kvr/
Кара-Сал Б.К., Сат Д.Х. Особенности свойств золосодержащих керамических масс // Сборник материалов международной научно-практической конференции, посвященной 20-летнему юбилею Тувинского государственного университета. Кызыл: ФГБОУ ВПО. 2015. С. 184.
Шоева Т.Е., Каминский Ю.Д., Дадар А.К.Х. Методика производства и технические характеристики зольных кирпичей // Вестник ТувГУ № 3. Технические и физико-математические науки. Кызыл: ФГБОУ ВПО. 2013. № 3 (18). С. 59.
Тасоол Л.Х., Янчат Н.Н., Чоксум Ж.Э. Алюмосиликатные микросферы зольных уносов теплоэлектростанции г. Кызыла // Вестник ТувГУ № 3. Технические и физико-математические науки. Кызыл: ФГБОУ ВПО. 2012. № 3 (14). С. 33.
Скляров Е.В., Гладкочуб Д.П., Донская Т.В., Иванов А.В., Летникова Е.Ф., Миронов А.Г., Бараш И.Г., Буланов В.А., Сизых А.И. Интерпретация геохимических данных: Учебное пособие / Под ред. Е.В. Склярова. М: Интернет Инжиниринг, 2001. 288 с.
Pухин Л.Б. Основы литологии. 3-е изд. Л.: Недра, 1969. 703 с.
Шпирт М.Я., Рашевский В.В. Микроэлементы горючих ископаемых (сер. “Библиотека горного инженера”. Т. 5. Кн. 4). М.: Кучково поле, 2010. 384 с.
Янчат Н.Н., Тас-оол Л.Х. // ХТТ. 2008. № 4. С. 54. [Solid Fuel Chemistry, 2008, vol. 42, no. 4, p. 241. https://doi.org/10.3103/S0361521908040101]
Тас-оол Л.Х., Янчат Н.Н., Аракчаа К.Д. // ХТТ. 2012. № 5. С. 46. [Solid Fuel Chemistry, 2012, vol. 46, no. 5, p. 322. https://doi.org/10.3103/S0361521912050126]
Монгуш Г.Р., Чульдум К.К., Гарынцева Н.В., Кузнецов Б.Н. Влияние удержания летучих веществ в зоне пиролиза углей Каа-Хемского и Межегейского месторождения на компонентный состав каменноугольной смолы. // Журнал Сиб. фед. ун-та. Сер. Химия. Красноярск.: СФУ, 2020. № 13 (4). С. 606. https://doi.org/10.17516/1998-2836-0209
Тас-оол Л.Х., Хомушку Б.Г., Чупикова С.А., Янчат Н.Н. Геохимические аспекты загрязнения окружающей среды г. Кызыла пылевыми частицами дымовых выбросов // Геоэкология. Инженерная геология. Гидрогеология. Геокриология. 2016. № 6. С. 531.
Дополнительные материалы отсутствуют.
Инструменты
Химия твердого топлива