Химия твердого топлива, 2022, № 6, стр. 42-50
СРАВНИТЕЛЬНЫЙ АНАЛИЗ ПЕРЕРАБОТКИ РАЗЛИЧНЫХ ВИДОВ БИОМАССЫ В СИНТЕЗ-ГАЗ МЕТОДОМ ДВУХСТАДИЙНОЙ ПИРОЛИТИЧЕСКОЙ КОНВЕРСИИ
В. М. Зайченко 1, *, В. А. Лавренов 1, **, В. А. Синельщиков 1, ***, Ю. М. Фалеева 1, ****
1 ФГБУН Объединенный институт высоких температур РАН (ОИВТ РАН)
125412 Москва, Россия
* E-mail: zaitch@oivtran.ru
** E-mail: v.a.lavrenov@gmail.com
*** E-mail: sinelshchikov@mail.ru
**** E-mail: faleeva.julia@mail.ru
Поступила в редакцию 13.07.2022
После доработки 15.07.2022
Принята к публикации 03.08.2022
- EDN: BAZALC
- DOI: 10.31857/S0023117722060111
Аннотация
Представлены экспериментальные и расчетные данные по характеристикам синтез-газа, который можно получать методом двухстадийной пиролитической конверсии из различных видов биомассы, относящейся к отходам деревообрабатывающей промышленности и сельскохозяйственного производства, а также к промышленно-бытовым органическим отходам. Разнообразие свойств исследованных видов углеводородного сырья позволило установить влияние характеристик перерабатываемой биомассы на характеристики получаемого синтез-газа (состав, объемный выход, теплота сгорания). Показано, что отношение H2/CO в получаемом синтез-газе можно целенаправленно изменять за счет выбора сырья с соответствующим атомным отношением H/O. В качестве параметра, определяющего энергетическую эффективность процесса двухстадийной пиролитической конверсии биомассы в синтез-газ, предлагается использовать содержание летучих продуктов в перерабатываемом сырье, рассчитанное на сухое беззольное состояние. Установлен диапазон содержания летучих продуктов, соответствующий максимальным значениям степени энергетической конверсии.
Интерес к исследованиям, направленным на разработку и совершенствование технологий использования биомассы в энергетических целях, связан со стремлением к улучшению экологической обстановки за счет уменьшения негативного влияния топливно-энергетического сектора экономики на окружающую среду. Поскольку сжигание биомассы, являющейся возобновляемым углеводородным ресурсом, считается нейтральным с точки зрения выбросов двуокиси углерода, то использование любых биотоплив на ее основе автоматически приводит к уменьшению вредных выбросов в расчете на единицу выработанной мощности. Кроме того, биомасса является достаточно универсальным видом энергетического сырья, которое может быть использовано как в качестве твердого топлива для прямого сжигания, так и для получения жидкого и газообразного топлив [1, 2].
Технологии, применяемые для улучшения потребительских свойств биомассы как твердого топлива, направлены на повышение ее объемной плотности, теплоты сгорания и гидрофобности. Для повышения плотности используются брикетрование и пеллетизация исходного сырья [3]. Увеличение теплоты сгорания твердого биотоплива и придание ему гидрофобных свойств достигаются за счет сухого и влажного пиролиза, называемых, соответственно, торрефикацией [4] и гидротермальной карбонизацией [5]. Получаемый в результате применения этих методов биоуголь по своим характеристикам приближается к ископаемым углям, что дает возможность сжигать его в пылеугольных котлах без их существенной модификации и снижения мощности [6].
Технологии получения жидкого и газообразного топлив из биомассы основаны на использовании процессов газификации и пиролиза [7–9]. При газификации, являющейся автотермическим процессом, конверсия биомассы проводится в среде газифицирующего агента. При воздушной и паровоздушной газификации теплота сгорания получаемого газа обычно не превышает 7 МДж/нм3. Использование кислорода в качестве газифицирующего агента позволяет существенно увеличить теплоту сгорания получаемого газа, но требует дополнительных затрат на его получение. Недостатком технологий, основанных на использовании пиролиза (аллотермический процесс), является относительно низкая степень конверсии исходного сырья в газообразное состояние, обусловленная наличием значительной доли пиролизной жидкости в конечных продуктах. Кроме того, присутствие конденсирующейся фракции в газе, получаемом с помощью различных термических методов конверсии биомассы, существенно ограничивает возможности его дальнейшего использования и требует применения специальных методов очистки [10]. От этого недостатка свободен метод двухстадийной пиролитический конверсии биомассы, первоначально предложенный в [11] для переработки древесины и исследованный в [12, 13] применительно к другим видам биомассы. Процесс переработки исходного сырья указанным методом состоит из двух стадий, проводимых в различных зонах реактора, пространственно разделенных между собой. Летучие продукты, образовавшиеся на первой стадии при нагреве исходного сырья в зоне пиролиза, на второй стадии переработки поступают в зону крекинга, в которой они фильтруются через пористую углеродную среду при температуре порядка 1000°С. Такой подход позволяет достигать высокой степени конверсии исходного сырья в синтез-газ за счет гетерогенного крекинга как неконденсирующихся, так и конденсирующихся летучих продуктов пиролиза при их взаимодействии с нагретой углеродной поверхностью. В результате полученный газ содержит незначительное количество жидкой фракции, что существенно расширяет возможности его дальнейшего использования без предварительной очистки [14]. Одновременно обеспечивается достаточно высокое значение теплоты сгорания получаемого газа за счет уменьшения в нем доли негорючих составляющих (например, азота, являющегося неотъемлемым компонентом газовой смеси, получаемой при воздушной и паровоздушной газификации). Указанная технология была реализована на пилотной установке производительностью 5–6 кг/ч по древесной биомассе и позволяла получать около 7 м3/ч синтез-газа с суммарным содержанием Н2 и СО, превышающем 90 об. %, и высшей теплотой сгорания на уровне 11.5 МДж/м3 [15].
Следует отметить, что подход, связанный с пространственным разделением зон пиролиза и газификации, используется в так называемых многоступенчатых газификаторах [16]. В частности, в [17, 18] он был успешно применен с целью уменьшения содержания смол в получаемом газе. В газификаторах, исследованных в работах [17, 18], первая стадия аналогична первой стадии в методе двухстадийной пиролитической конверсии. Однако на второй стадии требуемая температура в зоне крекинга достигалась за счет сжигания части летучих продуктов пиролиза. Подача в зону крекинга воздуха, необходимого для сжигания, приводила к наличию большого количества азота в получаемом газе и, соответственно, снижению его теплоты сгорания до 6.5 МДж/м3.
Цель работы – демонстрация возможности использования метода двухстадийной пиролитической конверсии применительно к широкому кругу видов биомассы и установление закономерностей, связывающих свойства перерабатываемого углеводородного сырья с характеристиками как самого процесса переработки, так и получаемого синтез-газа.
ЭКСПЕРИМЕНТАЛЬНАЯ УСТАНОВКА И МЕТОДИКА ПРОВЕДЕНИЯ ЭКСПЕРИМЕНТОВ
Исследования процесса двухстадийной пиролитической конверсии биомассы проводились на лабораторной установке, аналогичной использованной авторами в предыдущих работах [12, 13]. Принципиальная схема установки представлена на рис. 1.
Рис. 1.
Схема установки: 1 – двухсекционная печь, 2 – зона пиролиза, 3 –зона крекинга летучих продуктов пиролиза, 4 – холодильник, 5 – газосчетчик барабанный, 6 – газгольдер, 7 – газовый анализатор.
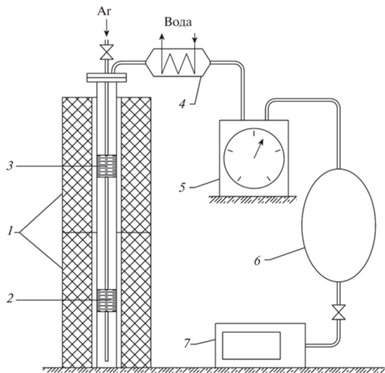
Реактор, представлявший собой металлическую трубу диаметром 37 мм и длиной 850 мм, помещался в двухсекционную печь с независимыми нагревателями. В зоне пиролиза и расположенной над ней зоне крекинга устанавливались тигли, плотно прилегавшие к стенкам реактора. Тигель, расположенный в зоне крекинга, имел газопроницаемое перфорированное дно. В тигель, расположенный в зоне пиролиза, помещалась перерабатываемая биомасса. Тигель, расположенный в зоне крекинга, наполнялся биоуглем, полученным путем пиролиза древесины. Объем зоны крекинга, заполненной биоуглем, выбирался таким образом, чтобы при выбранной скорости нагрева перерабатываемого сырья время взаимодействия летучих продуктов пиролиза с биоуглем составляло несколько секунд. Согласно [12, 19], этого времени было достаточно для полной конверсии конденсирующихся летучих продуктов в газовую фазу, о чем свидетельствовало отсутствие жидкой фракции в водоохлаждаемом холодильнике, установленном на выходе из реактора.
Перед началом эксперимента реактор и весь газовый тракт продувались аргоном для обеспечения инертной газовой среды. В начале эксперимента зона крекинга нагревалась до температуры 1000°C и поддерживалась при этой температуре в процессе всего эксперимента. Затем установка еще раз продувалась аргоном, после чего нагревалась зона пиролиза до 1000°C со скоростью 7°C/мин. Выходящая из реактора газовая смесь направлялась в холодильник, затем поступала в барабанный счетчик с жидкостным затвором и собиралась в газгольдере. При достижении в зоне пиролиза температуры 1000°C установка еще раз продувалась аргоном для того, чтобы вся образовавшаяся в реакторе смесь газов поступила в газгольдер. После этого состав газовой смеси определялся с помощью анализатора газа MRU Vario Plus Industrial. Результаты измерений состава и объемного выхода газа пересчитывались таким образом, чтобы исключить объемную долю аргона. На основе полученных данных определялся объемный выход синтез-газа $~V_{{{\text{exp}}}}^{{sg}}$, отнесенный к единице массы органической составляющей образца, и рассчитывалась высшая теплота сгорания $Q_{H}^{{sg}}$ полученного газа:
(1)
$\begin{gathered} Q_{H}^{{sg}} = (12.75~{{V}_{{{{{\text{H}}}_{2}}}}} + 12.62~{{V}_{{{\text{CO}}}}} + \\ \, + 39.82~{{V}_{{{\text{C}}{{{\text{H}}}_{4}}}}}){\text{/}}100\,\,[{\text{МДж/н}}{{{\text{м}}}^{3}}], \\ \end{gathered} $В качестве сырья для получения синтез-газа использовались различные виды биомассы: древесные опилки, кора различных пород деревьев, торф, лузга подсолнечника, отходы переработки кофе, иловый осадок коммунальных сточных вод и осадок сточных вод целлюлозно-бумажного комбината. При необходимости сырьевой материал измельчался, так что максимальный размер его частиц не превышал 5 мм. Перед проведением экспериментов образцы высушивались при температуре 105°C до влажности менее 1%. Измерения проводились с помощью анализатора влажности Ohaus-MB45. Элементный состав биомассы определялся с помощью HCNS-анализатора Vario MACRO Cube. Зольность A и содержание летучих продуктов Mvp определялись с помощью термоанализатора SDT Q600. Высшая теплота сгорания биомассы рассчитывалась по формуле Менделеева [20] на основе данных элементного анализа:
где CC, CH, CS и CO – содержание углерода, водорода, серы и кислорода в сырье, мас. %.РЕЗУЛЬТАТЫ И ОБСУЖДЕНИЕ
Характеристики видов биомассы, рассмотренных в данной работе, приведены в табл. 1. Из диаграммы Ван-Кревелена, построенной на основе данных элементного анализа и приведенной на рис. 2, видно, что для рассмотренных видов биомассы атомное отношение водород/углерод и кислород/углерод лежит в диапазоне 1.3–1.8 и 0.2–0.7 соответственно. Отметим, что кора березы характеризуется наибольшим содержанием водорода и наименьшим – кислорода. Достаточно большой диапазон изменения относительного содержания водорода и кислорода давал основание рассчитывать на то, что использование метода двухстадийной пиролитической конверсии для переработки рассмотренных видов биомассы позволит получить синтез-газ с различным объемным отношением H2 к CO.
Таблица 1.
Характеристики исходного сырья
Исходное сырье | Доля ле-тучих, мас. % на daf | Зольность, мас. % на сухое сос-тояние | Элементный состав, мас. % на daf | Высшая теп-лота сгорания, МДж/кг на daf | ||||
---|---|---|---|---|---|---|---|---|
Mvp | A | С | H | N | O | S | $Q_{H}^{b}$ | |
Древесные опилки (ДО) | 82.04 | 0.5 | 49.15 | 5.93 | 0.10 | 44.82 | – | 19.20 |
Кора березы (КБ) | 91.41 | 0.47 | 67.80 | 9.96 | 0.67 | 21.51 | 0.06 | 33.12 |
Кора осины (КО) | 87.77 | 1.51 | 54.26 | 8.06 | 1.06 | 36.43 | 0.19 | 24.54 |
Кора сосны (КС) | 67.88 | 2.18 | 55.68 | 6.33 | 0.28 | 37.62 | 0.09 | 22.71 |
Кора ели (КЕ) | 69.04 | 4.39 | 54.11 | 6.09 | 0.54 | 39.02 | 0.25 | 21.74 |
Кора клена (КК) | 76.39 | 7.58 | 49.43 | 6.86 | 0.91 | 42.73 | 0.08 | 20.7 |
Кора тополя (КТ) | 79.93 | 7.76 | 50.11 | 6.78 | 0.65 | 42.41 | 0.05 | 20.87 |
Торфяные пеллеты (ТП) | 64.1 | 3.3 | 55.7 | 6.9 | 1.7 | 35.7 | <0.05 | 23.6 |
Лузга подсолнечника (ЛП) | 74.9 | 2.5 | 51.38 | 6.26 | 0.72 | 41.64 | – | 20.72 |
Шелуха кофе (ШК) | 81.54 | 7.74 | 48.93 | 6.21 | 1.64 | 43.01 | 0.22 | 19.70 |
Пергаментная оболочка кофе (ПОК) | 79.18 | 1.61 | 50.78 | 6.29 | 0.36 | 42.53 | 0.03 | 20.46 |
Осадок сточных вод (ОСВ) | 81.7 | 25.18 | 48.22 | 6.92 | 8.50 | 35.2 | 1.16 | 21.3 |
Скоп (Ск) | 85.12 | 10.71 | 52.02 | 6.56 | 0.09 | 40.81 | 0.52 | 21.46 |
Рис. 2.
Диаграмма Ван Кревелена для исследованных видов биомассы: древесные опилки – ДО, кора березы – КБ, кора осины – КО, кора сосны – КС, кора ели – КЕ, кора клена – КК, кора тополя – КТ, торфяные пеллеты – ТП, лузга подсолнечника – ЛП, шелуха кофе – ШК, пергаментная оболочка кофе – ПОК, иловый осадок коммунальных сточных вод – ОСВ, скоп (волокно, собираемое из сточных вод целлюлозно-бумажного комбината) – Ск.
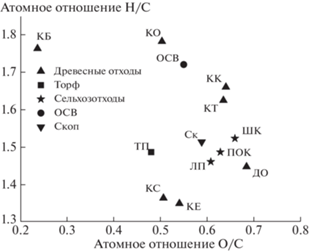
Для качественной оценки состава и объемного выхода синтез-газа можно предположить, что при использовании указанного метода переработки в результате гетерогенного крекинга летучих продуктов пиролиза на поверхности биоугля весь водород и кислород, содержащиеся в перерабатываемом сырье, конвертируются в молекулярный водород и окись углерода. Подтверждением допустимости такого предположения является, во-первых, отсутствие жидкой фракции в холодильнике на выходе из реактора, и, во-вторых, приведенный в табл. 2 экспериментальный состав газа, полученного в результате переработки рассмотренных видов биомассы. Как видно из табл. 2, суммарное содержание водорода и окиси углерода в синтез-газе превышает 90 об. %.
Таблица 2.
Характеристики синтез-газа, полученного при двухстадийной пиролитической переработке различных видов биомассы
Исходное сырье | Удельный объемный выход синтез-газа нм3 из кг сырья в расчете на daf | Состав синтез-газа, об. %, эксперимент | Высшая теплота сгорания синтез-газа, МДж/нм3 | Степень энер-гетической конверсии | |||||
---|---|---|---|---|---|---|---|---|---|
эксперимент $V_{{{\text{exp}}}}^{{sg}}$ | расчет $V_{{{\text{cal}}}}^{{sg}}$ | СO2 | CO | H2 | CH4 | N2 | $Q_{H}^{{sg}}$ | Эксперимент η | |
Древесные опилки (ДО) | 1.26 | 1.29 | 1.8 | 45.89 | 49.38 | 2.93 | – | 13.26 | 0.87 |
Кора березы (КБ) | 1.28 | 1.42 | 0.20 | 23.62 | 70.12 | 6.06 | – | 14.33 | 0.55 |
Кора осины (КО) | 1.28 | 1.41 | 0.33 | 30.60 | 65.06 | 4.01 | – | 13.75 | 0.72 |
Кора сосны (КС) | 1.17 | 1.24 | 1.26 | 46.87 | 51.34 | 0.53 | – | 12.67 | 0.65 |
Кора ели (КЕ) | 1.19 | 1.23 | 1.75 | 45.64 | 52.14 | 0.47 | – | 12.59 | 0.69 |
Кора клена (КК) | 1.28 | 1.37 | 1.64 | 47.30 | 50.60 | 0.46 | – | 12.60 | 0.78 |
Кора тополя (КТ) | 1.27 | 1.35 | 1.64 | 46.29 | 51.60 | 0.47 | – | 12.61 | 0.77 |
Торфяные пеллеты (ТП) | 1.25 | 1.27 | – | 41.0 | 49.0 | 1.0 | – | 11.82 | 0.63 |
Лузга подсолнечника (ЛП) | 1.25 | 1.28 | 1.43 | 46.40 | 50.32 | 1.85 | – | 13.01 | 0.78 |
Шелуха кофе (ШК) | 1.36 | 1.30 | 1.08 | 47.39 | 49.95 | 0.52 | 1.06 | 12.56 | 0.87 |
Пергаментная оболочка кофе (ПОК) | 1.26 | 1.30 | 1.39 | 48.26 | 48.4 | 0.88 | 1.07 | 12.61 | 0.77 |
Осадок сточных вод (ОСВ) | 1.32 | 1.27 | 0.2 | 35.7 | 57.4 | 1.0 | 5.7 | 12.22 | 0.76 |
Скоп (Ск) | 1.28 | 1.31 | 0.5 | 46.46 | 52.64 | 0.4 | – | 12.73 | 0.76 |
В рамках высказанного предположения отношение объемных долей H2/CO в синтез-газе будет определяться атомным отношением H/O в исходном сырье. Удельный объемный выход синтез-газа $V_{{{\text{cal}}}}^{{sg}}$ в расчете на кг перерабатываемого сырья, в свою очередь, зависит от суммарного содержания водорода и кислорода в исходном сырье и может быть оценен по формуле:
(3)
$\begin{gathered} V_{{{\text{cal}}}}^{{sg}} = ~22.4~\left( {~\frac{{{{C}_{{\text{H}}}}}}{{{{\mu }_{{{{{\text{H}}}_{2}}}}}}} + \frac{{{{C}_{{\text{O}}}}}}{{{{\mu }_{{\text{O}}}}}}} \right){\text{/}}100 = \\ = 1.4(8{{C}_{{\text{H}}}} + ~{{C}_{{\text{O}}}}){\text{/}}100~\,\,[{\text{н}}{{{\text{м}}}^{{\text{3}}}}{\text{/кг}}], \\ \end{gathered} $Рис. 3.
Зависимость отношения объемных долей H2/CO в синтез-газе от атомного отношения H/O в исходной биомассе: расчет – линия; эксперимент – символы (▲ – ДО, КБ, КО, КС, КЕ, КК, КТ; ★ – ЛП, ШК, ПОК; ■ – ТП; ● – ОСВ; ▼ – Ск).
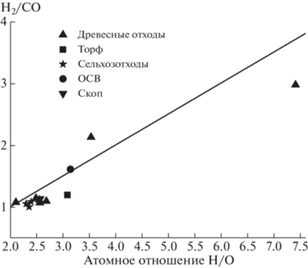
Рис. 4.
Зависимость объема синтез-газа, полученного из кг биомассы в расчете на daf, от величины, пропорциональной суммарному содержанию мольных долей H2 и O в исходной биомассе: расчет – линия; эксперимент – символы (обозначения те же, что и на рис. 3).
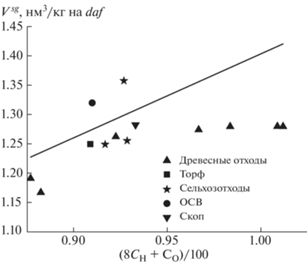
Данные, представленные на рис. 3, свидетельствуют о том, что отношение H2/CO в синтез-газе, получаемом методом двухстадийной пиролитической конверсии, определяется атомным отношением H/O в исходной биомассе. Максимальное значение отношения H2/CO, равное трем, получено при переработке коры березы. Таким образом, за счет выбора перерабатываемого сырья с определенным атомным отношением H/O или использования смесей из биомассы с различным отношением H/O можно в широких пределах изменять соотношение между объемными долями H2 и CO в получаемом синтез-газе. Такая возможность существенно расширяет область его дальнейшего практического использования в качестве сырья для ряда химических технологий, в частности, для производства жидких моторных топлив [23].
Поскольку при двухстадийной пиролитической переработке отсутствует внешний газифицирующий агент, в газовую фазу конвертируются только летучие продукты пиролиза. При организации непрерывного технологического цикла углеродный остаток может использоваться в зоне крекинга, однако его расход за счет взаимодействия с парами воды и двуокисью углерода невелик [15]. Исходя из этого, количественные показатели процесса конверсии фактически определяются содержанием летучих продуктов в перерабатываемом сырье и этот параметр можно взять за основу при систематизации результатов исследований по двухстадийной пиролитической конверсии различных видов биомассы. Как видно из табл. 1, для рассмотренных видов биомассы содержание летучих продуктов изменяется в диапазоне от 64 до 91 мас. %. Так как в процессе пиролиза участвует только органическая составляющая биомассы, то все удельные показатели, рассмотренные ниже, приведены в расчете на сухое беззольное состояние (daf) перерабатываемого сырья.
Важным показателем процесса переработки биомассы в газ, характеризующим его эффективность, является степень энергетической конверсии η, которая определяется как отношение высшей теплоты сгорания синтез-газа, полученного из 1 кг органической массы исходного сырья, $q_{H}^{{sg}} = Q_{H}^{{sg}}{{V}^{{sg}}}$ к высшей теплоте сгорания 1 кг органической массы исходного сырья:
На рис. 5 представлены рассчитанные и измеренные значения степени энергетической конверсии в зависимости от содержания летучих продуктов в исходной биомассе. В обоих случаях для определения η использовалась формула (4). Расчетные значения степени энергетической конверсии были получены путем подстановки в формулу (4) значений высшей теплоты сгорания и удельного объемного выхода синтез-газа, рассчитанных на основе данных элементного анализа исходной биомассы и уже использованного выше предположения о переходе всего водорода и кислорода, содержащихся в ней, в H2 и CO. Экспериментальные значения $\eta $ определены с использованием результатов измерений состава и объемного выхода синтез-газа. Как видно из рис. 5, как рассчитанная, так и измеренная зависимости носят немонотонный характер и качественно согласуются между собой. Максимальное различие между расчетными и экспериментальными значениями η не превышает 8%, что является дополнительным аргументом в пользу предположения, на котором основан расчет. Наибольшие значения степени энергетической конверсии соответствуют видам биомассы с содержанием летучих продуктов пиролиза в окрестности 74–82 мас. %.
Рис. 5.
Экспериментальные и расчетные значения степени энергетической конверсии η в зависимости от содержания летучих в исходной биомассе: эксперимент – залитые символы, расчет – незалитые символы (обозначения те же, что и на рис. 3); линия – аппроксимация расчетных данных.
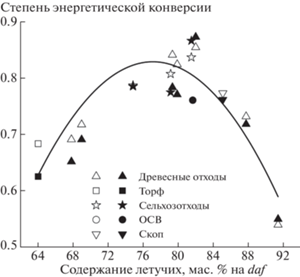
Для объяснения причины немонотонного характера поведения степени энергетической конверсии в зависимости от содержания летучих продуктов пиролиза в исходной биомассе рассмотрим аналогичные зависимости для высшей теплоты сгорания синтез-газа, полученного из 1 кг биомассы в расчете на daf (числитель в формуле (4)), и теплоты сгорания самой биомассы также в расчете на daf (знаменатель в формуле (4)). Из данных, представленных на рис. 6, следует, что для рассмотренных видов биомассы с увеличением содержания летучих продуктов наблюдается увеличение высшей теплоты сгорания синтез-газа $q_{H}^{{sg}}$, полученного из 1 кг перерабатываемой биомассы в расчете на daf.
Рис. 6.
Зависимость высшей теплоты сгорания $q_{H}^{{sg}}$ синтез-газа, полученного из 1 кг биомассы в расчете на daf, от содержания летучих: эксперимент – залитые символы, расчет – незалитые символы (обозначения те же, что и на рис. 3); линия – аппроксимация расчетных данных.
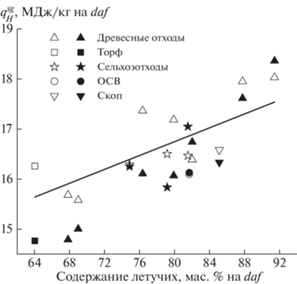
Таким образом, немонотонный характер зависимости, представленной на рис. 5, и наличие на ней экстремума могут быть связаны только с немонотонностью зависимости высшей теплоты сгорания биомассы $Q_{H}^{b}$ от содержания летучих продуктов Mvp. Соответствующая зависимость, построенная на основе данных элементного анализа и результатов измерения содержания летучих, представлена на рис. 7, из которого видно, что указанная зависимость с хорошей степенью точности может быть описана полиномом второй степени (коэффициент детерминации R2 = 0.8), а минимальные значения $Q_{H}^{b}$ соответствуют видам биомассы с содержанием летучих продуктов в диапазоне 74–82 мас. % в расчете на daf.
Рис. 7.
Зависимость высшей теплоты сгорания биомассы в расчете на daf от содержания летучих: эксперимент – залитые символы (обозначения те же, что и на рис. 3), линия – аппроксимация экспериментальных данных.
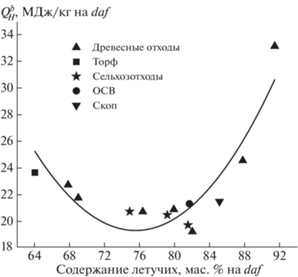
ЗАКЛЮЧЕНИЕ
На основе исследований процесса двухстадийной пиролитической конверсии различных видов биомассы, состава и объемного выхода получаемого синтез-газа показано, что соотношение объемных долей H2/CO в синтез-газе определяется атомным отношением H/O в перерабатываемом сырье. В результате за счет целенаправленного выбора сырья можно получать синтез-газ с заданным соотношением H2/CO и изменять это соотношение в широких пределах, что существенно расширяет возможности дальнейшего использования синтез-газа, в частности для получения компонентов жидких моторных топлив. Степень энергетической конверсии для рассмотренного метода переработки биомассы определяется содержанием летучих продуктов пиролиза в исходном сырье и достигает своего максимального значения на уровне 85% для видов биомассы с содержанием летучих продуктов в области 74–82 мас. % в расчете на daf.
Список литературы
Technologies for Converting Biomass to Useful Energy. Series: Sustainable Energy Developments. V. 4. Editor: Dahlquist E. Boca Raton: CRC Press, Taylor & Francis Group, 2013. 497 p.
Lewandowski W.M., Ryms M., Kosakowski W. // Processes. 2020. V. 8. P. 516. https://doi.org/10.3390/pr8050516
Tumuluru J.S., Wright C.T., Kenney K.L., Hess J.R. A Review on Biomass Densification Technologies for Energy Application. Idaho National Laboratory, 2010. 96 p. https://digital.library.unt.edu/ark:/67531/metadc840657
Nunes L.J.R., Matias J.C.O., Catalão J.P.S. Torrefaction of Biomass for Energy Applications. From Fundamentals to Industrial Scale.Academic Press, 2017. 245 p. https://doi.org/10.1016/C2015-0-04530-0
Libra J.A., Ro K.S., Kammann C., Funke A., Berge N.D., Neubauer Y., Titirici M.M., Fuhner C., Bens O., Kern J., Emmerich K.H. // Biofuels. 2011. V. 2. P. 71. https://doi.org/10.4155/bfs.10.81
Bergman P.C.A., Boersma A.R., Zwart R.W.W., Kiel J.H.A. Torrefaction for Biomass Co-firing in Existing Coal-fired Power Stations “BIOCOAL”. ECN Tech. Report ECN-C–05-013, 2005. 71 p.
Basu P. Biomass Gasification, Pyrolysis, and Torrefaction. Practical Design and Theory. 2nd ed. Elsevier, 2013. 530 p.
Molino A., Larocca V., Chianese S., Musmarra D. // Energies. 2018. V. 11. P. 811. https://doi.org/10.3390/en11040811
Bahng M.K., Mukarakate C., Robichaud D.J, Nimlos M.R. // Anal. Chem.Acta. 2009. V. 651. P. 117. https://doi.org/10.1016/j.aca.2009.08.016
Rios M.L.V., González A.M., Lora E.E.S., Almazándel Olmo O.A. // Biomass and Bioenergy. 2018. V. 108. P. 345. https://doi.org/10.1016/j.biombioe.2017.12.002
Chembukulam S.K., Dandge A.S., Kovilur N.L., Seshagiri R.K., Vaidyeswaran R. // Ind. Eng. Chem. Prod. Res. Dev. 1981. V. 20. P. 714.
Батенин В.М., Зайченко В.М., Косов В.Ф., Синельщиков В.А. // ДАН. 2012. Т. 446. № 2. С. 179. [Bate-nin V.M., Zaichenko V.M., Kosov V.F., Sinel’shchikov V.A. // Dokl. Chem. 2012. V. 446. P. 196. https://doi.org/10.1134/S0012500812090030]
Лавренов В.А., Ларина О.М., Синельщиков В.А., Сычев Г.А. // ТВТ. 2016. Т. 54. № 6. С. 950. [Lavre-nov V.A., Larina O.M., Sinelshchikov V.A., Sytchev G.A. // High Temp. 2016. V. 54. P. 892. https://doi.org/10.1134/S0018151X16060092]https://doi.org/10.7868/S0040364416060090
Зайченко В.М., Лавренов В.А., Синельщиков В.А. Альтернативная энергетика и экология. 2016. № 23–2. С. 42. https://doi.org/10.15518/isjaee.2016.23-24.029-042
Ivanin O.A., Zaichenko V.M., Sytchev G.A, Sinel-shchikov V.A., Lavrenov V.A., Larina O.M. Chapter 2. Two-Stage Pyrolytic Conversion of Biomass. In: Gasi-fication. Editors Silva V., Tuna C.E. IntechOpen. 2021. 22 p. http://doi.org/10.5772/intechopen.96670
Heidenreich S., Foscolo P.U. // Prog. Energy and Comb. Sci. 2015. V. 46. P. 72. https://doi.org/10.1016/j.pecs.2014.06.002
Brandt P., Larsen E., Henriksen U. // Energy & Fuels. 2000. V. 14. P. 816. https://doi.org/10.1021/ef990182m
Henriksen U., Ahrenfeldt J., Jensen T.K., Gøbel B., Bentzen J.D., Hindsgaul C., Sørensen L.H. // Energy. 2006. V. 31. P. 1542. https://doi.org/10.1016/j.energy.2005.05.031
Kosov V.V., Kosov V.F., Zaichenko V.M. // Chem. Eng. Trans. 2015. V. 43. P. 457. https://doi.org/10.3303/CET1543077
Энергетическое топливо СССР: (ископаемые угли, горючие сланцы, торф, мазут и горючий газ). Справочник. М.: Энергия, 1979. 128 с.
Faleeva Y.M., Zaichenko V.M. // J. Phys.: Conf. Ser. 2020. 1683:052017. https://doi.org/10.1088/1742-6596/1683/5/052017
Зайченко В.М., Сычев Г.А., Фалеева Ю.М. // Кокс и химия. 2019. № 11. С. 50. [Zaichenko V.M., Sytchev G.A., Faleeva Y.M. // Coke and Chemistry. 2019. V. 62. № 11. P. 539. https://doi.org/10.3103/S1068364X19110085]
Wang L., Weller C.L., Jones D.D., Hanna M.A. // Biomass and Bioenergy. 2008. V. 32. P. 573. https://doi.org/10.1016/j.biombioe.2007.12.007
Дополнительные материалы отсутствуют.
Инструменты
Химия твердого топлива