Кинетика и катализ, 2021, T. 62, № 6, стр. 811-820
Причины быстрой дезактивации кобальтового катализатора в условиях высокопроизводительного синтеза углеводородов С19+ по Фишеру–Тропшу
В. Н. Соромотин a, Р. Е. Яковенко a, А. В. Медведев a, С. А. Митченко a, *
a Южно-Российский государственный политехнический университет (НПИ) имени М.И. Платова
346128 Новочеркасск, ул. Просвещения, 132, Россия
* E-mail: samit_rpt@mail.ru
Поступила в редакцию 15.06.2021
После доработки 30.07.2021
Принята к публикации 31.07.2021
Аннотация
Представлены результаты исследования дезактивации промышленного катализатора Со–Al2O3/SiO2 в условиях высокопроизводительного синтеза длинноцепочечных углеводородов по Фишеру–Тропшу
при высоком давлении (6 МПа). Показано, что повышение температуры синтеза приводит
к уменьшению скорости дезактивации катализатора. Установлено незначительное влияние
термической агломерации частиц кобальта и зауглероживания поверхности катализатора
на его активность в изученных условиях. Обнаружена корреляция между скоростью дезактивации
катализатора и селективностью по углеводородам С19+, указывающая на блокирование центров роста цепи синтезируемыми восками, что является
основной причиной быстрой потери активности катализатора.
Графический реферат
ВВЕДЕНИЕ
Синтез Фишера–Тропша (СФТ) предоставляет уникальную возможность производства сверхчистого дизельного и реактивного топлива, бензина, а также смазочных материалов из альтернативного нефти сырья, такого как растительная биомасса, бытовые отходы, попутный нефтяной или природный газ и др. [1]. Применение СФТ в химической промышленности в последние годы явно возрождается в связи с постоянно растущим спросом на чистое транспортное топливо, а также повышением ответственности за сжигание ископаемых углеводородов, негативно воздействующих на окружающую среду. СФТ – это универсальный промышленный путь конверсии синтез-газа, смеси CO и H2, на разных катализаторах в зависимости от целевого продукта. Обычно применяются катализаторы на основе железа или кобальта. Катализатор в виде наночастиц кобальта, нанесенных на SiO2 и промотированный 1% Al2O3 (Co–Al2O3/SiO2) демонстрирует высокую производительность по воскам (углеводородам С19+) или синтетическому дизельному топливу с дополнительным преимуществом ультранизкого содержания серы, азота и ароматических углеводородов [2–4]. Учитывая, что кобальтовые катализаторы относительно дорогостоящие, увеличение их срока службы позволит уменьшить эксплуатационные затраты процесса СФТ.
Дезактивация катализатора является основным препятствием для продолжительного и высокопроизводительного синтеза углеводородов. Выделяют несколько основных путей дезактивации кобальтовых катализаторов СФТ: а) термическая агломерация частиц кобальта (спекание) [5]; б) осаждение аморфного (сажа) или кристаллического (графит) углерода на поверхность катализатора (зауглероживание) [6]; в) образование трудновосстанавливаемых соединений кобальта с носителем (за счет сильного взаимодействия металл–носитель) [7]; г) окисление активного металла [8]; д) отравление катализатора (соединениями серы или азота) [9]. Перечисленные пути являются необратимыми и требуют регенерации катализатора или его замены. Сообщалось [10, 11] о торможении диффузии реагентов к активным центрам катализатора через слой покрывающих их продуктов синтеза. Это снижает производительность катализатора из-за уменьшения конверсии оксида углерода и селективности процесса по углеводородам С5+. В другом исследовании [12] высказывалось схожее предположение, что при температуре 220°C для core–shell (“ядро–оболочка”) кобальтового катализатора ускоренная дезактивация вызвана образованием восков, ограничивающих массоперенос реагентов к активным центрам, однако экспериментальных доказательств такого предположения не получено.
В литературе [6, 8, 10, 13] обычно анализируют влияние технологических параметров (температура, давление, нагрузка на катализатор, состав синтез-газа) на путь и скорость дезактивации, однако данных по дезактивации катализаторов при повышенных (6.0 МПа и более) давлениях мало. В настоящей работе изучена дезактивация кобальтового катализатора, показавшего высокую активность и производительность по тяжелым воскам при давлении 6.0 МПа с использованием циркуляции отработавшего синтез-газа [11].
Цель работы – исследование закономерностей дезактивации катализатора Со–Al2O3/SiO2 в условиях высокого давления (6.0 МПа) в режиме рециркуляции газа.
ЭКСПЕРИМЕНТАЛЬНАЯ ЧАСТЬ
Выбор катализатора
Исследования процесса дезактивации проводили на промотированном оксидом алюминия кобальтовом катализаторе, обозначенном далее Co–Al2O3/SiO2, приготовленном по методике [3, 14] и содержащем 20 мас. % Co и 1 мас. % Al2O3. Для указанного катализатора характерно узкое распределение частиц металла по размерам со средним значением 8–9 нм [3, 15], оптимальным для обеспечения высокой производительности в синтезе конденсированных углеводородов из СО и Н2. Часть приготовленного свежевосстановленного катализатора Co–Al2O3/SiO2 использовали для сравнения в методах просвечивающей электронной микроскопии (ПЭМ) и рентгенофазового анализа (РФА). Зауглероженный катализатор готовили in situ путем осаждения углерода по реакции диспропорционирования СО в трубчатом реакторе с неподвижным слоем при температуре 250°С, давлении 2.0 МПа и объемной скорости газа 500 ч–1 в течении 6 ч.
Каталитические испытания синтеза углеводородов осуществляли проточно-циркуляционным методом в трубчатом реакторе (внутренний диаметр – 16 мм) с неподвижным слоем катализатора (объем загрузки – 15 см3, фракция 2–3 мм с разбавлением кварцем 30 см3) в интервале температур 205–225°С, давлении 6.0 МПа, объемной скорости газа ОСГ = 1000 ч–1, мольном соотношении компонентов синтез-газа Н2/СО = 1.85, кратности циркуляции Кц = 2.2. Для каждого испытания при разных температурах загружали новую порцию катализатора. Перед проведением исследований катализаторы восстанавливали в течение 1 ч в токе Н2 при атмосферном давлении, температуре 400°С и ОСГ = 1000 ч–1. Исследование изменения основных показателей процесса СФТ осуществляли по достижению необходимой температуры в непрерывном режиме в течение 220 ч. Зависимости изменения конверсии СО от времени в потоке при разных температурах представлены в виде нормализованной активности (конверсия СО в текущий момент времени, приведенная к начальной) [13, 16, 17]. Скорость дезактивации катализатора Rcd (%/ч) рассчитывали из наклона графика зависимости нормализованной активности от времени в потоке.
Анализ состава синтез-газа и газообразных продуктов синтеза выполняли методом газо-адсорбционной хроматографии на хроматографе марки Кристалл 5000 (“Хроматэк”, Россия) с детектором по теплопроводности [18]. Продукты синтеза фракционировали, выделяя три фракции в зависимости от температуры кипения: до 180°С ‒ бензиновая фракция (С5‒С10); 180‒330°С ‒ дизельная фракция (С11‒С18); кубовый остаток – парафины С19+. Состав фракции углеводородов С5‒С18 определяли методом капиллярной газожидкостной хромато-масс-спектрометрии на газовом хроматографе GC 7890А с масс-детектором MSD 5975С и капиллярной колонкой HP-5MS (“Agilent”, США). Расчет хроматограмм осуществляли методом внутренней нормализации с использованием калибровочных коэффициентов для углеводородов.
Рентгенофазовый анализ катализаторов проводили с использованием специализированного источника синхротронного излучения “КИСИ-Курчатов” (Россия) с длинами волн 0.0793508 (для отработавшего 100 ч катализатора) и 0.073722 нм (для исходного восстановленного образца), стандарт LaB6. Качественный фазовый состав определяли с помощью PDF-2 [19] в программном комплексе Crystallographica.
Размеры наночастиц металлического кобальта из данных РФА оценивали по уравнению Шеррера: d = Kλ/βcosθ.
Исследования катализатора с помощью ПЭМ выполняли на электронном микроскопе HT7700 (“Hitachi”, Япония). Микрофотографии были получены в режиме передачи изображений (режим формирования изображений в светлом поле) при ускоряющем напряжении 100 кВ.
Исследования методом дифференциальной сканирующей калориметрии (ДСК) проводили с использованием комплекса STA 449F5 (“NETSCH”, Германия), совмещенного с масс-спектрометром QMS 403 Aeolos (ФРГ). Условия эксперимента: реакционный газ ‒ Н2 (5 об. %)‒He, скорость подачи ‒ 50 см3/мин; защитный газ ‒ Не, скорость подачи ‒ 20 см3/мин; навеска образца ‒ 50 мг; скорость нагрева ‒ 10°С/мин в температурном интервале 50‒150°С, термостатирование при 150°С в течение 1 ч, дальнейший нагрев со скоростью 20°С/мин в температурном интервале 150‒800°С.
РЕЗУЛЬТАТЫ И ИХ ОБСУЖДЕНИЕ
Характеристика катализатора
Исходный восстановленный и отработавший 100 ч при температуре 225°С катализаторы были исследованы методами просвечивающей электронной микроскопии (ПЭМ) и рентгенофазового анализа (РФА). Образцы предварительно зауглероженного, а также отработавшего 100 ч при температуре 210°С катализаторов изучены методом ДСК с масс-спектральным анализом метана – продукта гидрирования углерода или гидрогенолиза остаточных продуктов СФТ соответственно.
Микрофотографии ПЭМ для исходного восстановленного и отработавшего 100 ч при температуре 225°С представлены на рис. 1. Наночастицы металлического кобальта равномерно распределены на поверхности, а их размер варьируется в диапазоне от 5 до 15 нм с усредненным значением 8 ± 2 нм. На отработавшем 100 ч катализаторе средний размер частиц (11 ± 3 нм) практически не изменился в пределах экспериментальной погрешности. Эти данные, полученные методом ПЭМ, хорошо согласуются с результатами рентгеновской дифракции с использованием синхронного излучения.
Рис. 1.
Изображения ПЭМ и распределение наночастиц Со0 по размеру для свежевосстановленного (а) и отработавшего 100 ч при температуре 225°С (б) катализаторов.
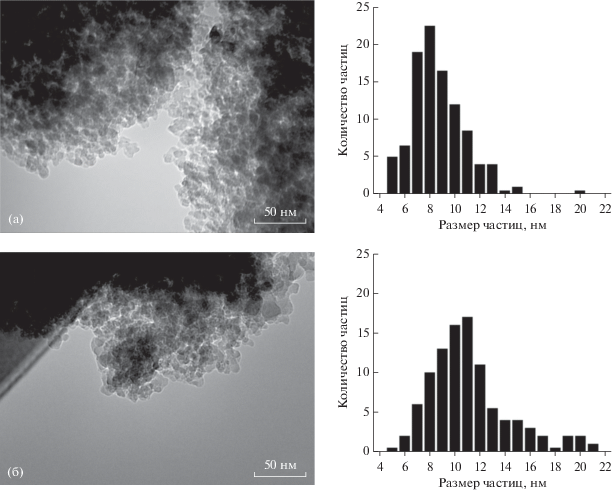
На дифрактограмме восстановленного катализатора (рис. 2, кривая 1) видны фазы металлического кобальта Co0 и оксида CoO с характерными максимумами дифракции в области углов 2θ = = 18°–55°. В структуре катализатора, как исходного восстановленного, так и отработавшего 100 ч при температуре 225°С (рис. 2, кривые 1 и 2), не была зафиксирована фаза кристаллического углерода. Для исходного восстановленного и отработавшего 100 ч образцов определены размеры наночастиц Со0 по уравнению Шеррера, составляющие 11 и 12 нм соответственно.
Рис. 2.
Дифрактограммы катализатора Co–Al2O3/SiO2: 1 – исходный восстановленный (λ = = 0.073722 нм); 2 – отработавший 100 ч при 225°С (λ = = 0.0793508 нм).
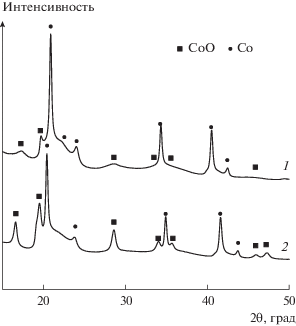
Из рис. 2 видно, что существенного окисления металлического кобальта за 100 ч работы не происходит. Это согласуется с литературными сведениями [8]: для прямого окисления металлического кобальта до его оксида необходимы высокие парциальные давления воды (${{{{P}_{{{{{\text{H}}}_{{\text{2}}}}{\text{O}}}}}} \mathord{\left/ {\vphantom {{{{P}_{{{{{\text{H}}}_{{\text{2}}}}{\text{O}}}}}} {{{P}_{{{{{\text{H}}}_{{\text{2}}}}}}}}}} \right. \kern-0em} {{{P}_{{{{{\text{H}}}_{{\text{2}}}}}}}}}$ = 128), достижимые при значениях конверсии СО свыше 90%. Именно по этой причине в промышленном синтезе углеводородов конверсию ограничивают на уровне 80% [8]. Кроме того, на дифрактограмме отработавшего катализатора не выявлено накопления фазы шпинели силиката кобальта, что также согласуется с литературными данными: для образования соединений кобальта с оксидом кремния требуется парциальное давление воды, на порядок превышающее давление водорода [8], что достижимо лишь при больших конверсиях СО. Как было показано в работе [7], положительные значения свободной энергии Гиббса реакции металлического кобальта с водой и оксидом кремния при уровне конверсии СО ХСО = 66.67% (отвечает отношению парциальных давлений воды и водорода ${{{{P}_{{{{{\text{H}}}_{{\text{2}}}}{\text{O}}}}}} \mathord{\left/ {\vphantom {{{{P}_{{{{{\text{H}}}_{{\text{2}}}}{\text{O}}}}}} {{{P}_{{{{{\text{H}}}_{{\text{2}}}}}}}}}} \right. \kern-0em} {{{P}_{{{{{\text{H}}}_{{\text{2}}}}}}}}}$ = 1) делают термодинамически невыгодным окисление Со0 до СоО и Со2SiO4.
Гидрирование углерода на предварительно зауглероженном катализаторе наблюдали на комплексе ДСК путем регистрации масс-спектрального сигнала m/z = 15, отвечающего метану (рис. 3а). Выделение метана в этом случае начинается при 250°С с максимумом при 350°С и сопровождается экзотермическим эффектом, зарегистрированном при температуре около 400°С (рис. 3б).
Для отработавшего в СФТ при 225°С в течении 100 ч катализатора выделение метана начинается при существенно более низкой температуре (180°С с максимумом при 280°С) и происходит в результате гидрогенолиза накопившихся в ходе СФТ на поверхности катализатора углеводородов. Величина экзотермического эффекта реакции гидрогенолиза существенно меньше, чем таковая для реакции гидрирования углерода. Поэтому на кривой дифференциального термического анализа (ДТА) этого образца указанный эффект не зафиксирован.
Таким образом, в изученных условиях СФТ за первые 100 ч работы катализатора не наблюдается ни существенной агломерации кобальта (данные РФА и ПЭМ), ни его окисления (данные РФА). Также можно исключить заметное зауглероживание поверхности катализатора за 100 ч работы в потоке аморфным (данные ДСК) или кристаллическим углеродом (данные РФА).
Каталитические испытания
В настоящей работе исследование дезактивации проводилось при четырех температурах: 205, 210, 215 и 225°С. В качестве примера на рис. 4 приведено изменения конверсии СО (ХСО, %) от времени в потоке для Co–Al2O3/SiO2 катализатора при 210°С. Можно выделить два периода изменения активности катализатора: быстрое падение конверсии СО в течение первых 50 ч работы (период I), после чего конверсия СО стабилизируется (период II), что характерно для кобальтовых катализаторов СФТ [20].
Рис. 4.
Степень превращения (ХCO, %) от времени в потоке для Co–Al2O3/SiO2-катализатора при Т = = 210°С; P = 6.0 МПа; ОСГ = 1000 ч–1; Кц = 2.2.
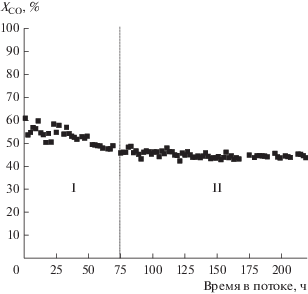
Усредненные по времени в потоке показатели процесса в указанные периоды работы катализатора приведены в табл. 1. Для периода I зафиксированы наибольшие показатели селективности и производительности по конденсированным углеводородам. В периоде II производительность по углеводородам С5+ понизилась на 16% за счет снижения в течение периода I конверсии СО и селективности по углеводородам С5+.
Таблица 1.
Усредненные по времени в потоке показатели процесса в зависимости от продолжительности синтеза*
Период работы | Время в потоке, ч | Конверсия СО, % | Селективность, % | GС5+, кг ${\text{м}}_{{{\text{кат}}}}^{{ - 3}}$ ч–1 |
|||
---|---|---|---|---|---|---|---|
CH4 | C2–C4 | C5+ | CO2 | ||||
I | 1–75 | 53.8 | 12.3 | 13.8 | 73.7 | 0.2 | 86.0 |
II | 76–219 | 45.2 | 14.3 | 15.8 | 69.5 | 0.4 | 70.2 |
Групповой и фракционный составы продуктов С5+, полученных в периоды работы I и II, представлены в табл. 2.
Таблица 2.
Состав продуктов, полученных в периоды работы I и II*
Период работы, ч | Продукты | Состав продуктов, мас. % | О/П** | ||
---|---|---|---|---|---|
C5–C10 | C11–С18 | С19+ | |||
I*** | н-Алканы | 10.8 | 26.7 | 49.1 | 0.10 |
изо-Алканы | 0.2 | 0.8 | |||
Алкены | 4.3 | 4.9 | |||
Оксигенаты | 1.6 | 1.6 | |||
Сумма | 16.9 | 34.0 | 49.1 | ||
II*** | н-Алканы | 12.4 | 23.3 | 47.7 | 0.15 |
изо-Алканы | 0.2 | 0.6 | |||
Алкены | 6.1 | 7.0 | |||
Оксигенаты | 1.8 | 0.9 | |||
Сумма | 20.5 | 31.8 | 47.7 |
Фракционный и групповой составы продуктов, полученных в периодах I и II, близки между собой: в периоде II немного увеличилась селективность по бензиновой фракции за счет дизельной фракции и восков. Содержание олефинов в продуктах синтеза тоже несколько возросло (О/П вырос с 0.10 до 0.15), а содержание изо-алканов и оксигенатов существенным образом не изменилось. Оксигенаты представлены преимущественно первичными спиртами с длиной цепи от 4 до 16 атомов углерода.
Данные об изменении состава углеводородов в зависимости от температуры проведения процесса СФТ, приведены в табл. 3.
Таблица 3.
Состав продуктов, полученных при разной температуре СФТ*
Температура, °С | Продукты | Состав продуктов, мас. % | О/П | ||
---|---|---|---|---|---|
C5–C10 | C11–С18 | С19+ | |||
205 | н-Алканы | 7.9 | 17.9 | 69.2 | 0.05 |
изо-Алканы | 0.2 | 0.5 | |||
Алкены | 2.5 | 1.8 | |||
Сумма | 10.6 | 20.2 | 69.2 | ||
210 | н-Алканы | 10.5 | 25.9 | 53.8 | 0.10 |
изо-Алканы | 0.2 | 0.8 | |||
Алкены | 4.2 | 4.7 | |||
Сумма | 14.8 | 31.4 | 53.8 | ||
215 | н-Алканы | 7.0 | 30.7 | 55.2 | 0.07 |
изо-Алканы | 0.2 | 0.9 | |||
Алкены | 1.9 | 3.1 | |||
Сумма | 9.4 | 35.4 | 55.2 | ||
225 | н-Алканы | 7.2 | 30.0 | 51.2 | 0.11 |
изо-Алканы | 0.5 | 0.8 | |||
Алкены | 3.4 | 6.9 | |||
Сумма | 11.1 | 37.7 | 51.2 |
Видно, что подъем температуры приводит к уменьшению селективности по углеводородам С19+, и увеличению выхода фракции С11–С18; соотношение олефин/парафин (О/П) при этом тоже незначительно возрастает. Такой отклик каталитической системы на повышение температуры проведения процесса является типичным для СФТ [11, 15, 21, 22].
Дезактивация катализатора
На рис. 5 приведено сравнение скорости дезактивации катализатора СФТ при разных температурах, выраженное в виде нормализованной активности от времени в потоке. Хорошо видно, что с ростом температуры синтеза скорость дезактивации уменьшается.
Рис. 5.
Зависимость нормализованной активности от продолжительности синтеза при разных температурах.
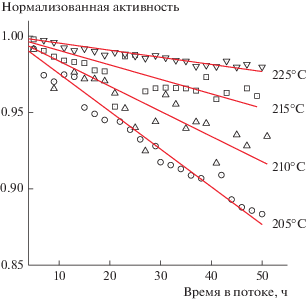
По мнению многих авторов [5, 6, 13, 23, 24], зауглероживание поверхности катализатора и спекание частиц активного металла – наиболее существенные причины, приводящие к снижению активности катализатора в СФТ. Учитывая, что процесс спекания ускоряется с повышением температуры СФТ [13, 23], следовало ожидать наибольший его вклад в дезактивацию катализатора при максимальной в нашем исследовании температуре 225°С, что противоречит приведенным на рис. 5 результатам. Кроме того, на микрографиях ПЭМ не наблюдается существенного укрупнения наночастиц кобальта (средний размер 8 ± 2 против 11 ± 3 нм для, соответственно, исходного восстановленного катализатора и отработавшего 100 ч при 225°С образца). Столь незначительное укрупнение наночастиц кобальта не сказывается заметным образом на активности катализатора (см., например, [13, 25]). Указанные факты свидетельствует о несущественном вкладе спекания частиц металла в потерю активности на протяжении периода I (рис. 4). Данные, полученные методами ДТА (рис. 3), позволяют исключить зауглероживание катализатора в качестве основной причины его дезактивации за первые 100 ч в потоке.
Ранее было предположено [10–12], что при относительно низких температурах и, соответственно, высокой вероятности роста цепи, дезактивация может осуществляться путем блокирования активной поверхности катализатора синтезированными восками. Повышение температуры должно уменьшить вероятность роста цепи и сместить селективность в сторону образования углеводородов с более короткой цепью и, как следствие, понизить скорость дезактивации [11]. Для проверки гипотезы были определены зависимости скорости дезактивации катализатора от температуры процесса (рис. 6а) и селективности образования углеводородов С19+, S(C19+) (рис. 6б).
Рис. 6.
Зависимость скорости дезактивации катализатора Rcd от температуры процесса (а) и селективности по углеводородам С19+, S(C19+) (б).
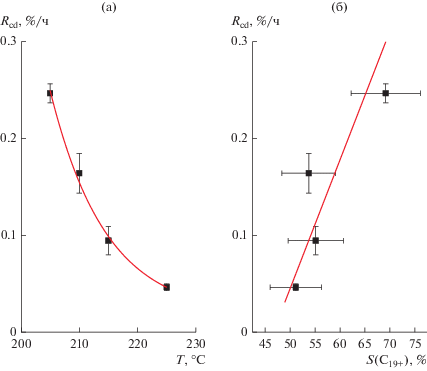
Действительно, повышение температуры синтеза приводит к снижению скорости дезактивации катализатора. При этом имеет место линейная корреляция скорости дезактивации с селективностью образования углеводородов С19+. Это подтверждает гипотезу о блокировании активных центров роста цепи синтезированными тяжелыми восками как основную причину быстрой потери активности кобальтового катализатора в условиях высокопроизводительного синтеза длинноцепочечных углеводородов.
ЗАКЛЮЧЕНИЕ
В работе исследованы закономерности дезактивации катализатора Со–Al2O3/SiO2 в условиях высокопроизводительного синтеза тяжелых восков при давлении 6.0 МПа в режиме рециркуляции газа. Полученные экспериментальные данные позволяют заключить, что наблюдаемое быстрое падение активности катализатора в первые двое суток его работы не связано ни с термической агломерацией частиц активного металла, ни с зауглероживанием поверхности катализатора. Обнаружена корреляция скорости дезактивации катализатора с селективностью образования углеводородов С19+. Этот факт позволяет заключить, что в рассмотренных условиях СФТ высокая селективность и производительность по тяжелым воскам приводят к блокировке активных центров роста цепи катализатора синтезированными продуктами, что препятствует диффузии к ним реагентов и снижает конверсию СО.
Список литературы
Martinelli M., Gnanamani M.K., LeViness S., Jacobs G., Shafer W.D. // Appl. Catal. A: General. 2020. V. 608. № 117740.
Van de Loosdrecht J., Botes F., Ciobica I., Ferreira A., Gibson P., Moodley D., Saib A., Visagie J., Weststrate C.J., Niemantsverdriet J. / Comprehensive Inorganic Chemistry II: from elements to applications.Amstrdam: Elsevier. 2013. P. 525.
Savost’yanov A.P., Yakovenko R.E., Sulima S.I., Bakun V.G., Narochnyi G.B., Chernyshev V.M., Mitchenko S.A. // Catal. Today. 2017. V. 279. P. 107.
Yakovenko R.E., Savost’yanov A.P., Narochniy G.B., Soromotin V.N., Zubkov I.N., Papeta O.P., Svetogorov R.D., Mitchenko S.A. // Catal. Sci. Technol. 2020. V. 10. № 22. P. 7613.
Claeys M., Dry M.E., Steen E.V., Berge P., Booyens S., Crous R., Helden P., Labuschagne J., Moodley D., Saib A. // Amer. Chem. Soc. Catals. 2015. V. 5. № 2. P. 841.
Keyvanloo K., Fisher M.J., Hecker W.C., Lancee R.J., Jacobs G., Bartholomew C.H. // J. Catal. 2015. V. 327. P. 33.
Jiang Z., Zhao Y., Huang C., Song Y., Li D., Liu Z., Liu Z. // Fuel. 2018. V. 226. P. 213.
Wolf M., Gibson E.K., Olivier E.J., Neethling J.H., Catlow C.R.A., Fischer N., Claeys M. // Amer. Chem. Soc. Catal. 2019. V. 9. № 6. P. 4902.
Ma W., Jacobs G., Shafer W.D., Pendyala V.R.R., Xiao Q., Hu Y., Davis B.H. // Catal. Lett. 2016. V. 146. № 7. P. 1204.
Pölmann F., Kern C., Röbler S., Jess A. // Catal. Sci. Technol. 2016. V. 6. P. 6593.
Savost’yanov A.P., Yakovenko R.E., Narochniy G.B., Sulima S.I., Bakun V.G., Soromotin V.N., Mitchenko S.A. // Catal. Commun. 2017. V. 99. P. 25.
Jinglin Y., Xuejin F., Yuebing X., Xiaohao L. // Catal. Sci. Technol. 2020. V. 10. № 4. P. 1182.
Rahmati M., Safdari M., Fletcher T., Argyle M., Bartholomew C.H. // Chem. Rev. 2020. V. 120. № 10. P. 4455.
Яковенко Р.Е., Зубков И.Н., Нарочный Г.Б., Папета О.П., Денисов О.Д., Савостьянов А.П. // Кинетика и катализ. 2020. Т. 61. № 2. С. 278.
Митченко С.А., Савостьянов А.П., Нарочный Г.Б., Яковенко Р.Е., Бакун В.Г., Сулима С.И., Якуба Э.О. // Кинетика и катализ. 2017. Т. 58. № 1. С. 86.
Moodley D., loosdrecht J., Saib A., Overett M., Datye A., Niemantsverdriet J. // Appl. Catal. A: General. 2009. V. 354. № 1–2. P. 102.
Choudhury H., Cheng X., Afzal S., Prakash A.V., Tatarchuk B.J., Elbashir N.O. // Catal. Today. 2020. V. 343. P. 112.
Savost'yanov A.P., Eliseev O.L., Yakovenko R.E., Narochniy G.B., Maslakov K.I., Zubkov I.N., Soromotin V.N., Kozakov A.T., Nicolskii A.V., Mitchenko S.A. // Catal. Lett. 2020. V. 150. № 7. P. 1932.
PDF-2. The powder diffraction file TM. International Center for Diffraction Data (ICDD). 2012. URL: www.icdd.com.
Loosdrecht J., Balzhinimaev B., Dalmon J., Niemantsverdriet J., Tsybulya S., Saib A., Berge P., Visagie J. // Catal. Today. 2007. V. 123. № 1–4. P. 293.
Todic B., Ma W., Jacobs G., Davis B.H., Bukur D.B. // J. Catal. 2014. V. 311. P. 325.
Rytter E., Tsakoumis N.E., Holmen A. // Catal. Today. 2016. V. 261. P. 3.
Moodley D., Claeys M., van Steen E., van Helden P., Kistamurthy D., Weststrate K.-J., Niemantsverdriet H., Saib A., Erasmus W., van de Loosdrecht J. // Catal. Today. 2020. V. 342. P. 59.
Weststrate C.J., Ciobica I.M., Saib A.M., Moodley D., Niemantsverdriet J. // Catal. Today. 2014. V. 228. P. 106.
Bian G.-Z., Fujishita N., Mochizuki T., Ning W.-S., Yamada M. // Appl. Catal. A: General. 2003. V. 252. № 2. P. 251.
Дополнительные материалы отсутствуют.
Инструменты
Кинетика и катализ