Кинетика и катализ, 2021, T. 62, № 6, стр. 803-810
Каталитическая активность в полном окислении пропана продуктов автоклавного термолиза [Co(NH3)5Cl][PtCl4], их морфология и фазовый состав
Е. Н. Тупикова a, *, И. А. Платонов a, О. С. Бондарева a, Д. С. Хабарова a
a Самарский национальный исследовательский университет им. акад. С.П. Королева
443086 Самара, Московское шоссе, 34, Россия
* E-mail: nil-6ssau@mail.ru
Поступила в редакцию 25.06.2021
После доработки 03.08.2021
Принята к публикации 03.08.2021
Аннотация
В гидротермальных условиях из двойного комплекса [Co(NH3)5Cl][PtCl4] получены каталитические фазы, содержащие высокодисперсные частицы металлической
платины на крупных частицах смешанного оксида кобальта. Химический и фазовый состав,
а также морфология образующихся частиц определены методами оптико-эмиссионной спектрометрии
с индуктивно-связанной плазмой, рентгеновского энергодисперсионного и рентгенофазового
анализа и сканирующей электронной микроскопии. Каталитические фазы были нанесены в
автоклавных условиях на металлические носители из сплавов Х18Н10Т и Х20Н80 в виде
стружки или блока из “металлорезины”. Катализаторы продемонстрировали значительную
активность в модельной реакции полного окисления пропана.
Графический
реферат
ВВЕДЕНИЕ
В настоящее время активно ведутся работы, направленные на получение и исследование многокомпонентных каталитических систем, включающих благородный и цветной металл [1–7]. Такие системы широко изучаются в процессах очистки водорода от примеси угарного газа [8, 9], разложения пероксида водорода [10], окисления спиртов [11, 12] и CO [13].
Как правило, нанесенные катализаторы получают методом пропитки, предусматривающим сорбцию пористым носителем соединения-предшественника из раствора и последующую термическую обработку, приводящую к формированию активной фазы. Удобными соединениями-предшественниками являются двойные комплексные соли (ДКС) благородных и цветных металлов, в результате термолиза которых в зависимости от условий образуются различные продукты [14]. Однако процесс приготовления катализаторов методом пропитки длительный, многостадийный и требует применения материалов с большой сорбционной емкостью. К недостаткам можно также отнести образование побочных токсичных газообразных продуктов, что требует проведения дополнительных природоохранных мероприятий.
Получение каталитических фаз из соединений-предшественников в гидротермальных условиях в автоклавах дает возможность избежать указанных недостатков. Известно, что в автоклавных условиях некоторые простые комплексы платиновых металлов превращаются в дисперсные металлические фазы [15, 16]. При внесении в раствор какого-либо твердого материала, способного выполнять функцию носителя катализатора, происходит одновременное формирование каталитических фаз и осаждение их на поверхность, что упрощает процесс и сокращает время приготовления катализатора. При этом в качестве носителя можно использовать сорбционно инертные материалы, такие как металлы и их сплавы, что позволяет изготавливать термостабильные, механически прочные катализаторы практически любой геометрической формы [17–20]. Полученные таким образом катализаторы [21] с различными комбинациями платиновых металлов являются весьма эффективными в процессах полного окисления органических соединений и гидрирования ненасыщенных углеводородов.
Однако в процессе выделения твердой фазы из раствора, включающем стадию гомогенного формирования зародышей, которые служат центрами кристаллизации, и гетерогенную стадию роста частиц, возможно появление довольно крупных агломератов платиновых металлов. Сочетание в исходном соединении платинового и цветного металла при их одновременном превращении в автоклавных условиях может привести к образованию многофазного порошка, состоящего из металлической платины и оксидов цветного металла, выступающих в качестве “микрореактора”, стенки которого будут ограничивать рост платиновых частиц. Оксиды цветных металлов в составе получаемого из этих соединений катализатора могут играть роль структурообразующего или активирующего промотора. Необходим поиск и исследование подходящих для этих целей комплексных соединений.
Изучение поведения двойных комплексов [Ni(NH3)6][PtCl4] и [Cr(NH3)5Cl][PtCl4] в гидротермальных условиях [22, 23] показало, что из комплексов образуется пористая матрица оксидов цветного металла, включающая частицы металлической платины.
Целью настоящей работы было получение каталитических фаз на металлических структурированных носителях путем гидротермального разложения комплекса тетрахлороплатинат(II) хлоропентаамминкобальта(III) [Cо(NH3)5Cl][PtCl4], исследование их химического и фазового состава, морфологии и каталитической активности в модельной реакции полного окисления пропана.
ЭКСПЕРИМЕНТАЛЬНАЯ ЧАСТЬ
Синтез соединения
Комплексы K2[PtCl4], [Co(NH3)5Cl]Cl2 синтезировали из платиновой черни (99.99%) и Co(NO3)2 ⋅ 6H2O (х. ч.) по известным методикам [24, 25].
Двойной комплекс тетрахлороплатината(II) хлоропентаамминкобальта(III) получали реакцией ионного обмена путем сливания растворов хлороплатината калия и 2% избытка хлорида хлоропентамминкобальта(III). Выпавший осадок отфильтровывали, промывали дистиллированной водой и сушили на воздухе при комнатной температуре. ИК-спектры синтезированных комплексов регистрировали на ИК-Фурье спектрометре NICOLET iS50 (“Thermo Fisher Scientific”, США). ИК-спектр [Co(NH3)5Cl][PtCl4]: 3193 (ν (NH3)); 1575 (δa (NH3)); 1299, 1319 (δs (NH3)); 822 (ρr(NH3)). Содержание металлов (мас. %) по результатам оптико-эмиссионной спектрометрии с индуктивно связанной плазмой: Co – 11.4 (расчет – 11.4); Pt – 38.3 (расчет – 37.7).
Автоклавный термолиз
Для исследования химического и фазового состава, а также морфологии частиц, образующихся при автоклавном термолизе двойного комплекса, получали порошкообразные продукты. Для этого во фторопластовый вкладыш наливали раствор двойного комплекса [Cо(NH3)5Cl][PtCl4] и добавляли 0.01 М KOH до pH 8–9. Концентрация комплексной соли в растворе не превышала 0.7 ммоль/л. Для приготовления катализаторов в раствор комплекса вносили соответствующий металлический структурированный носитель. Массу комплекса рассчитывали так, чтобы масса платины составляла 0.1% от массы носителя. Проводили деаэрацию раствора путем вакуумирования в течение 1 ч и последующего насыщения азотом. Автоклав герметизировали, нагревали при постоянном вращении до 190°C и выдерживали при данной температуре 150 мин. После охлаждения автоклав вскрывали, полученные порошкообразные продукты или нанесенный катализатор отфильтровывали, промывали дистиллированной водой и сушили при комнатной температуре.
Металлические носители
Носители для катализаторов были изготовлены из нержавеющей стали марки Х18Н10Т (нс) или нихрома (нх) марки Х20Н80 в виде блоков цилиндрической формы высотой 20 мм и диаметром 9 мм путем холодного прессования специальным образом уложенной проволочной спирали. Объемная доля пустот в полученном таким образом материале, так называемой “металлорезине” (МР) [26], была равна 0.8. Таким же образом использовали дробленую стружку, полученную на токарном станке, из нержавеющей стали той же марки.
Для увеличения поверхности металлического материала и лучшего сцепления с ней наносимых каталитических фаз создавали дополнительный оксидный слой путем окисления на воздухе при температуре 450 (нс) или 700°С (нх) в течение 4 ч [27, 28].
Физико-химические методы исследования продуктов автоклавного термолиза
В физико-химических исследованиях применяли порошкообразные продукты термолиза двойной комплексной соли, предполагая, что химический и фазовый состав продуктов не зависит от того, формируются они в объеме жидкой фазы или на поверхности носителя.
Размер, морфологию и элементный состав частиц, образующихся в процессе автоклавного термолиза [Co(NH3)5Cl][PtCl4], исследовали на сканирующем электронном микроскопе Vega SB (“Tescan”, Чехия) с энергодисперсионным рентгеновским анализатором INCA Х-act (“Оxford Instruments”, Великобритания) при ускоряющем напряжении 30 кВ.
Рентгенофазовый анализ (РФА) осуществляли на компактном рентгеновском дифрактометре Miniflex II (“Rigaku”, Япония). Основные параметры анализа: сила тока – 15 мА; напряжение – 10 кВ; скорость сканирования – 10 град/мин; материал анода – стандартная рентгеновская трубка CuКα, мощность – 0.45 кВт.
Количественный элементный анализ исходного комплекса и продуктов его термолиза проводили методом оптико-эмиссионной спектрометрии с индуктивно-связанной плазмой (ИСП-ОЭС) на спектрометре PlasmaQuant PQ 9000 (“AnalytikJena”, Германия). Для формирования высокотемпературной плазмы использовали аргон.
Каталитические испытания
Каталитические свойства полученных образцов исследовали в реакции полного окисления пропана в изотермическом реакторе проточного типа в режиме идеального вытеснения. Объем загружаемого катализатора – 1.3 см3. Масса испытуемого катализатора в зависимости от материала и формы носителя была 2–2.5 г. Контроль температуры в реакторе осуществляли хромель-копелевой термопарой, размещенной внутри слоя катализатора. Содержание пропана в смеси с воздухом и азотом составляло 0.04 об. %, соотношение пропана и кислорода соответствовало стехиометрическому, скорость подачи реакционной смеси – 5000 ч–1.
Реакционную смесь анализировали газохроматографическим методом на хроматографе Кристалл 2000М (“Хроматэк”, Россия) с пламенно-ионизационным детектором и стальной насадочной колонкой, заполненной Al2O3. По результатам анализа концентрации пропана в смеси до и после реакции при заданной температуре рассчитывали степень превращения углеводорода.
Для определения воспроизводимости результатов и стабильности работы катализатора проводили 6 циклов каталитических испытаний. В каждом цикле температуру реакции последовательно повышали от 200 до 450°С с шагом в 50°С, при каждой температуре катализатор работал в течение 15–20 мин, после достижения 450°С реактор охлаждали до комнатной температуры.
РЕЗУЛЬТАТЫ И ИХ ОБСУЖДЕНИЕ
Для установления материального баланса процессов, протекающих в автоклавных условиях, по данным ИСП-ОЭС были рассчитаны массы металлов в исходном растворе, в твердом продукте и фильтрате после отделения твердого продукта гидротермального разложения (табл. 1). Результаты показали, что анионная часть комплекса, содержащая платину, подвергается полному превращению, в растворе после реакции платина не обнаруживается. Степень превращения кобальта, входящего в состав катионной части комплекса, составляет около 90%.
Таблица 1.
Материальный баланс процесса гидротермального разложения [Co(NH3)5Cl][PtCl4] по результатам ИСП-ОЭС
Проба | Масса металла, мг | |
---|---|---|
Pt | Co | |
Исходный комплекс | 3.5 ± 0.6 | 1.07 ± 0.05 |
Твердый продукт | 4.0 ± 0.6 | 0.91 ± 0.05 |
Фильтрат после отделения продукта | 0.0 | 0.03 ± 0.05 |
Степень превращения, % | 100 | 85 ± 9 |
В табл. 2 представлены результаты определения состава твердофазного продукта автоклавного термолиза двойного комплекса. Осадок, полученный после автоклавного термолиза, был доведен до постоянной массы прокаливанием при температуре 800°С. Предполагаем, что в этих условиях кобальт образует оксид со смешанными степенями окисления +2 и +3, платина остается в металлическом состоянии. Расчет количества металлов – 0.01 ммоль Pt и 0.007 ммоль Со – показывает, что их содержание в продукте реакции близко к стехиометрическому для комплекса [Co(NH3)5Cl][PtCl4].
Таблица 2.
Состав порошкообразного продукта гидротермального разложения [Co(NH3)5Cl][PtCl4] по результатам ИСП-ОЭС и согласно расчету
Навес-ка, мг | Масса, мг | Относи-тельная погреш-ность, % | |||
---|---|---|---|---|---|
Pt | Co | Co3O4 (расчет) | общая | ||
2.4 | 2.1 | 0.39 | 0.54 | 2.64 | 10 |
Результаты рентгенофазового анализа порошкообразного продукта гидротермального разложения комплекса подтверждают выводы, сделанные на основании ИСП-ОЭС. Положение линий на рентгенограмме (рис. 1) указывают на наличие двух кристаллических фаз: металлической платины и смешанного оксида кобальта Co3O4.
О размерах и форме частиц, образующихся в процессе гидротермального разложения комплекса, а также распределении металлов по поверхности позволяют судить данные растровой электронной микроскопии, дополненные анализом энергодисперсионных рентгеновских спектров. На электронных изображениях (рис. 2) присутствуют крупные частицы неправильной формы размером в десятки мкм. На их поверхности наблюдаются агломераты сферических частиц размером от 0.6 до 3 мкм. Поверхность сферических частиц неоднородна, на ней имеются дендритные отростки диаметром порядка 100 нм.
Рис. 2.
СЭМ-изображения порошкообразного продукта гидротермального разложения [Co(NH3)5Cl][PtCl4] при увеличении 1000–40 000×.
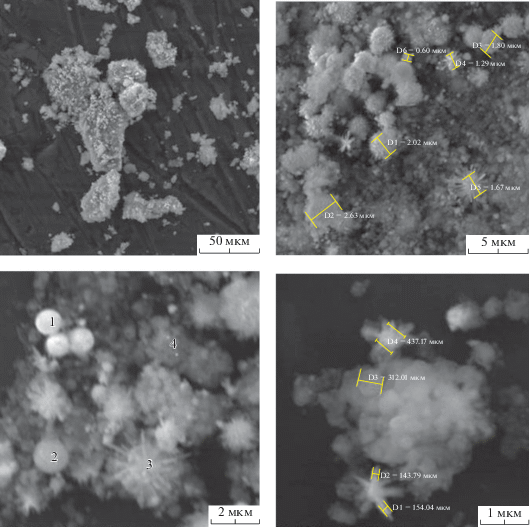
Элементный состав частиц по данным энергодисперсионной рентгеновской спектроскопии представлен в табл. 3. Из спектра вычтены пики, относящиеся к элементам подложки (C, Al). Высокая интенсивность пика кислорода в спектрах обусловлена сигналом от алюминиевой фольги, на которую была нанесена проба. Из общего спектра, полученного в результате сканирования поверхности образца при увеличении 20 000× (рис. 2), следует, что атомное количество обоих металлов в среднем по поверхности практически одинаково, что соответствует данным ИСП-ОЭС и стехиометрии исходного комплекса. Обработка спектров излучения, эмитированного со сферических частиц (обозначены цифрами 1, 2 и 3 на рис. 2), показывает, что атомное содержание платины в несколько раз превышает таковое кобальта, что позволяет идентифицировать их как частицы металлической платины. Основу (точка 4) составляет оксид кобальта. Вывод о характере распределения металлов в продукте гидротермального разложения двойного комплекса подтверждается сравнением изображения во вторичных электронах и карт распределения химических элементов: О, Со и Pt (рис. 3).
Таблица 3.
Результаты энергодисперсионного рентгеновского микроанализа порошкообразного продукта автоклавного термолиза [Co(NH3)5Cl][PtCl4]
Спектр | Содержание элемента, ат. % | ||
---|---|---|---|
O | Co | Pt | |
Общий | 50.09 | 27.53 | 22.38 |
Точка 1 | 69.68 | 3.87 | 26.45 |
Точка 2 | 65.75 | 6.16 | 28.09 |
Точка 3 | 75.00 | 8.00 | 17.00 |
Точка 4 | 82.67 | 14.93 | 2.40 |
Примечание: Спектры получены с участков, обозначенных цифрами 1, 2, 3, 4 на рис. 2.
Рис. 3.
Изображение порошкообразного продукта гидротермального разложения [Co(NH3)5Cl][PtCl4] во вторичных электронах (а) и карты распределения О (б), Со (в) и Pt (г).
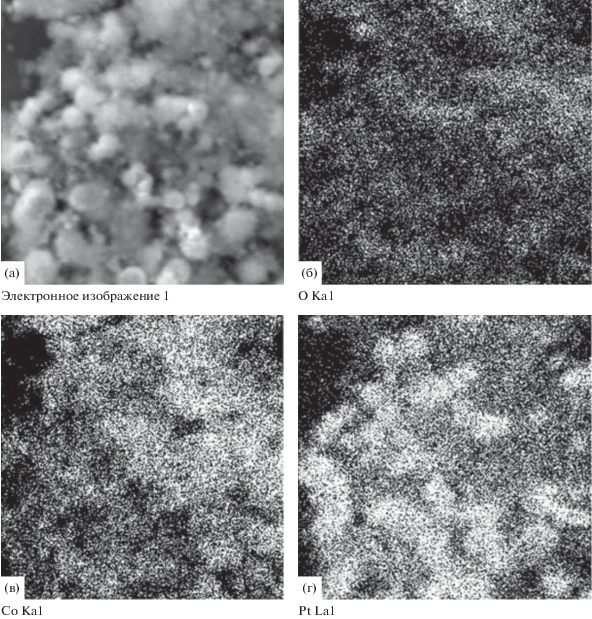
Можно предполагать, что в гидротермальных условиях превращению подвергается в первую очередь катионная часть комплекса, содержащая аммиакат кобальта. Происходит гидролиз [Co(NH3)5Cl]2+ и частичное восстановление кобальта до Со+2, формируются достаточно крупные частицы смешанного оксида кобальта Со3О4. Образующийся свободный аммиак восстанавливает [PtCl4]2– до металлической платины, которая в виде сферических частиц осаждается на поверхности частиц оксида кобальта.
В табл. 4 представлены результаты каталитических испытаний в реакции полного окисления пропана образцов катализаторов, полученных из двойного комплекса [Co(NH3)5Cl][PtCl4]. Также для сравнения были изучены катализаторы, приготовленные аналогичным способом из комплекса платины [Pt(NH3)4]Cl2. Навеска комплексной соли, взятой для синтеза катализатора, во всех экспериментах содержала 0.1% платины от массы носителя. Носители катализаторов отличались как материалом (нержавеющая сталь или нихром), так и формой (дробленая стружка или сформированный из проволочной спирали блок “металлорезина”).
Таблица 4.
Результаты каталитических испытаний в реакции окисления пропана
Катализатор | Носитель (материал/ форма) |
Степень превращения пропана, % | ||||
---|---|---|---|---|---|---|
200°С | 250°С | 300°С | 350°С | 400°С | ||
Pt/Co3O4 | Нс/стружка | 2.11 | 12.09 | 46.58 | 78.51 | 90.58 |
Нс/МР | 1.52 | 5.47 | 21.87 | 65.30 | 90.03 | |
Нх/МР | 5.38 | 13.46 | 66.31 | 95.91 | 99.99 | |
Pt | Нс/стружка | 2.15 | 34.82 | 90.17 | 94.78 | 96.60 |
Нс/МР | 2.14 | 5.70 | 29.60 | 87.64 | 98.60 |
Предлагаемый способ синтеза катализаторов не может обеспечить полное осаждение каталитически активного компонента на носитель, поскольку разложение комплекса возможно не только на поверхности носителя, но и на стенках автоклава и в объеме раствора. Для катализаторов, полученных из двойного комплекса, также наблюдается частичное осыпание каталитического слоя после сушки образцов из-за худшего сцепления частиц оксида с металлической поверхностью. Таким образом, содержание каталитического компонента должно быть меньше рассчитанного (0.1 мас. % по платине). Результаты проведенных каталитических испытаний позволяют оценить целесообразность применения двойного платина-кобальтового комплекса в качестве соединения-предшественника в гидротермальном синтезе катализаторов на структурированных металлических носителях в сравнении с использованием для этих целей простого аммиачного комплекса платины.
Анализ данных показывает, что катализаторы начинают работать при 200°С. При температуре 400°С наблюдается практически полное превращение пропана на образцах. В присутствии платина-кобальтовых катализаторов на блочном носителе из нержавеющей стали конверсия углеводорода сопоставима с таковой для монометаллического платинового катализатора, полученного аналогичным способом.
Активность образца Pt/Co3O4 на стружке из нержавеющей стали при температурах 250–300°С значительно ниже (12.09 и 46.58%), чем таковая платинового катализатора (34.82 и 90.17%). Однако при температуре 400°С пропан превращается практически полностью (90.58%). Отсутствие положительного влияния оксида кобальта на активность катализатора при низких температурах можно объяснить его более компактным состоянием, что можно наблюдать на электронных изображениях порошкообразного продукта (рис. 2, 3) и, предположительно, меньшей, по сравнению с платиной, поверхностью. Кроме того, оксиды цветных металлов, в том числе Со3О4, проявляют каталитические свойства в реакциях полного окисления углеводородов и СО при более высоких температурах, чем металлы платиновой группы [29]. Существенное увеличение конверсии пропана при 400°С предположительно связано с проявлением каталитического действия оксида кобальта.
Наблюдаемые значения конверсии пропана на платина-кобальтовых катализаторах сохраняются постоянными в течение 6 циклов работы в интервале температур 200–450°С и последующего охлаждения, тогда как активность платиновых образцов снижается уже после второго цикла из-за возможной миграции металлических частиц и их агломерации [22]. Можно предполагать, что добавление оксида кобальта в катализатор стабилизирует дисперсное состояние платины.
Сравнивая каталитические свойства платина-кобальтовых катализаторов, нанесенных на различные носители, отмечено, что образец на “металлорезине” из нихрома более активный, чем на носителях из нержавеющей стали. Разница в величинах степени превращения составляет 20–60%. Материал носителя, вероятно, влияет на прочность сцепления частиц катализатора с поверхностью носителя. Требуются дополнительные исследования в этом направлении.
ЗАКЛЮЧЕНИЕ
В работе впервые показана возможность получения многокомпонентных дисперсных фаз реакцией разложения двойного комплекса [Co(NH3)5Cl][PtCl4] в водных растворах при повышенных температурах. По результатам физико-химических исследований установлено, что образующиеся фазы состоят из смешанного оксида кобальта Со3О4 и осажденных на его поверхности сферических частиц металлической платины.
С использованием двойного комплекса в качестве соединения-предшественника в гидротермальных условиях приготовлены катализаторы, нанесенные на металлические носители из сплавов Х18Н10Т и Х20Н80 в виде дробленой стружки или блока из “металлорезины”. Показано, что в модельной реакции полного окисления пропана катализаторы проявляют высокую и стабильную активность при низком содержании платины, зависящую, в том числе, от материала и формы металлического носителя.
Таким образом, исследованное в работе комплексное соединение перспективно в качестве соединения-предшественника для синтеза каталитически активных фаз с использованием автоклавных технологий.
Список литературы
Гринберг В.А., Кулова Т.Л., Майорова Н.А., Доброхотова Ж.В., Пасынский А.А., Скундин А.М., Хазова О.А. // Электрохимия. 2007. Т. 43. № 1. С. 77.
Тарасевич М.Р., Кузов А.В., Клюев А.Л., Титова В.Н. // Альтернативная энергетика и экология. 2007. Т. 46. № 2. С. 113.
Богдановская В.А., Тарасевич М.Р., Кузнецова Л.Н., Жутаева Г.В., Лозовая О.В. // Электрохимия. 2010. Т. 46. № 8. С. 985.
Богдановская В.А., Тарасевич М.Р. // Электрохимия. 2011.Т. 47. № 4. С. 404.
Myoungki M., Hasuck K. // Int. J. Hydrogen Energy. 2016. V. 41. P. 17557.
Duanghathai K., Sirapath Y., Supatini S., Mali H. // Int. J. Hydrogen Energy. 2018. V. 43. P. 5133.
Шикина Н.В., Яшник С.А., Гаврилова А.А., Николаева О.А., Довлитова Л.С., Ищенко А.В., Исмагилов З.Р. // Кинетика и катализ. 2020. Т. 61. № 5. С. 725.
Потемкин Д.И., Конищева М.В., Задесенец А.В., Снытников П.В., Филатов Е.Ю., Коренев С.В., Собянин В.А. // Кинетика и катализ. 2018. Т. 59. № 4. С. 499.
Potemkin D.I., Filatov E.Yu., Zadesenets A.V., Rogozhnikov V.N., Gerasimov E.Yu., Snytnikov P.V., Korenev S.V., Sobyanin V.A. // Mater. Lett. 2019. V. 236. P. 109.
Домонов Д.П., Печенюк С.И., Гостева А.Н. // Журн. физ. химии. 2014. Т. 88. № 6. С. 926.
Печенюк С.И., Семушина Ю.П., Кузьмич Л.Ф., Иванов Ю.В. // Журн. физ. химии. 2016. Т. 90. № 1. С. 22.
Николаев С.А., Цодиков М.В., Чистяков А.В., Чистякова П.А., Эзжеленко Д.И., Кротова И.Н. // Кинетика и катализ. 2020. Т. 61. № 6. С. 864.
Олексенко Л.П., Луценко Л.В. // Журн. физ. химии. 2013. Т. 87. № 2. С. 200.
Печенюк С.И., Домонов Д.П. // Журн. структурной химии. 2011. № 2. С. 419.
Belousov O.V., Sirotina A.V., Belousova N.V., Fesik E.V., Borisov R.V., Malchikov G.D. // Журн. СФУ. Серия: Техника и технологии. 2014. Т. 7. № 2. С. 138.
Борисов Р.В., Белоусов О.В. // Журн. СФУ. Серия: Химия. 2014. Т. 7. № 3. С. 331.
Субботин А.Н., Гудков Б.С., Воробьева М.П., Голосман Е.З., Якерсон В.И., Кустов Л.М. // Катализ в промышленности. 2005. № 6. С. 52.
Тарасов А.Л., Кустов Л.М. // Катализ в промышленности. 2012. № 6. С.7.
Мальцева Н.В., Постов А.Ю., Лаврищева С.А., Киршин А.И. // Известия СПбГТИ (ТУ). 2016. № 32. С. 28.
Кириллов В.А., Шигаров А.Б., Кузин Н.А., Киреенков В.В., Брайко А.С., Бурцев Н.В. // Катализ в промышленности. 2019. Т. 19. № 5. С. 351.
Тупикова Е.Н. Дис. … канд. хим. наук. Самара: СГАУ, 2003.
Хабарова Д.С., Тупикова Е.Н. / Теоретические и практические вопросы интеграции химической науки, технологии и образования. Материалы конференции. Улан-Удэ: ВСГУТУ, 2016. С. 219.
Тупикова Е.Н., Платонов И.А., Хабарова Д.С. // Кинетика и катализ. 2019. Т. 60. № 3. С. 388.
Синтез комплексных соединений металлов платиновой группы. Под ред. Черняева И.И. Москва: Наука, 1964. С. 9.
Руководство по неорганическому синтезу. Под ред. Брауэра Г. Т. 5. Москва: Мир, 1985. С. 1780.
Чегодаев Д.Е. Конструирование рабочих органов машин и оборудования из упругопористого материала МР. Самара: НПЦ “Авиатор”, 1994. С. 15.
Пaт. 2101082 PФ, 1998.
Пaт. 2175264 PФ, 2001.
Пател Ч., Бхатт Н., Паланки С. // Катализ в промышленности. 2020. № 4. С. 286.
Дополнительные материалы отсутствуют.
Инструменты
Кинетика и катализ