Кинетика и катализ, 2022, T. 63, № 2, стр. 249-257
Получение спиртов и олефинов из CO и H2 на кобальтовом катализаторе при высоком давлении и циркуляции газа
И. Н. Зубков a, В. Н. Соромотин a, А. П. Савостьянов a, С. А. Митченко a, Р. Е. Яковенко a, *
a Южно-Российский государственный политехнический университет (НПИ) имени М.И. Платова
346128 Новочеркасск, ул. Просвещения, 132, Россия
* E-mail: jakovenko39@gmail.com
Поступила в редакцию 25.06.2021
После доработки 23.08.2021
Принята к публикации 11.09.2021
- EDN: VOWKVW
- DOI: 10.31857/S0453881122020162
Аннотация
Представлены результаты исследования синтеза продуктов из CO и H2 в условиях среднего и высокого давления в режиме циркуляции газа на нанесенном промышленном катализаторе Со–Al2O3/SiO2. Обнаружено, что повышение давления с 2.0 до 8.0 МПа приводит к увеличению количества образующихся спиртов и олефинов синтеза в 10.5 и 2.0 раза соответственно. Определено, что получаемые в синтезе спирты не являются продуктами гидратации олефинов. Подтвержден нетипичный для синтеза Фишера–Тропша эффект возрастания селективности по продуктам С5+ с повышением температуры при высоком давлении в режиме рециркуляции газа.
ВВЕДЕНИЕ
Синтез Фишера–Тропша (ФТ) – каталитический процесс получения из CO и H2 широкого набора продуктов: от метана до длинноцепочечных углеводородов (церезинов) и олефинов, а также кислородсодержащих соединений [1, 2]. В настоящее время церезины применяются как компоненты пластичных смазок, изоляционных материалов, в качестве флегматизатора, в косметической продукции, как сырье при изготовлении изопарафиновых масел и др. [3]. Олефины – важнейшие компоненты, используемые в процессах получения поверхностно-активных веществ, поли-α-олефиновых масел, полимерной, косметической и медицинской продукции [4]. Высшие спирты, содержащие от 6 до 22 атомов углерода в цепи, широко используют в промышленности для производства пластификаторов, растворителей и присадок к топливам.
Промышленный синтез указанных продуктов осуществляют из СО и Н2 на кобальтовых и железных катализаторах при среднем давлении [5]. Кобальтовые катализаторы характеризуются большей селективностью в отношении углеводородов линейного строения, меньшей активностью в реакциях водяного газа и Белла–Будуара [6], в то время как железные более селективны в реакциях образования олефинов [7, 8]. В настоящее время для получения высших спиртов из смесей СО и Н2 предлагаются катализаторы на основе Rh [9] и Мо [10], модифицированные катализаторы синтеза метанола [11], а также Со- [12] и Fe-катализаторы [13] процесса ФТ.
Ранее [14, 15] мы обнаружили, что в реакциях образования углеводородов из СО и Н2 на промышленном катализаторе Со–Al2O3/SiO2 при повышенном давлении (6.0 МПа) и циркуляции газа увеличивается доля олефинов в составе продуктов с одновременным ростом селективности по углеводородам С5+ и С35+. Дальнейшее повышение давления может привести к изменению распределения состава в сторону требуемых продуктов. Целью настоящей работы является исследование закономерностей синтеза продуктов в условиях высокого давления (8.0 МПа) в режиме рециркуляции газа на катализаторе Со–Al2O3/SiO2.
ЭКСПЕРИМЕНТАЛЬНАЯ ЧАСТЬ
Исследования процесса ФТ выполнены с использованием катализатора Со–Al2O3/SiO2, разработанного для селективного синтеза восков [16], технология приготовления которого отработана в промышленных условиях [17]. Катализатор получали методом пропитки пористого носителя – силикагеля марки КСКГ производства ООО “Салаватский катализаторный завод” – водным раствором нитрата кобальта (концентрация 55 мас. %) и промотора (нитрата алюминия) в течение 0.5 ч при температуре 80°С. Гранулы сушили по 4 ч при температурах 80 и 100–140°С, затем прокаливали 4 ч при 400°С. Катализатор содержит 20 мас. % Co и 1 мас. % промотирующей добавки оксида алюминия, характеризуется незначительным взаимодействием активного металла с носителем и имеет средний размер частиц кобальта 8–9 нм [18], который принято считать оптимальным для обеспечения высокой производительности в синтезе углеводородов из СО и Н2 [19].
Методики исследований
Исследования основных показателей процесса проводили в трубчатом реакторе (dвн = 16 мм) со стационарным слоем катализатора (15 см3) в проточно-циркуляционном режиме при объемной скорости газа (ОСГ) 1000 ч–1, соотношении Н2/СО = 1.85, давлении 2.0 и 8.0 МПа, в интервале температур 205–225°С. Предварительно катализатор восстанавливали в токе Н2 при ОСГ = = 1000 ч–1 и температуре 400°С [20, 21] в течение 1 ч. Продолжительность непрерывных испытаний для значений каждого технологического параметра составляла 30–60 ч. Активность катализатора синтеза углеводородов оценивали по следующим показателям: конверсия СО, селективность и производительность. Селективность по продуктам рассчитывали, как количество СО, израсходованного на данный продукт, к его общему израсходованному количеству [22].
Анализ синтез-газа и газообразных продуктов синтеза осуществляли методом газо-адсорбционной хроматографии на хроматографе марки Кристалл 5000 (“Хроматэк”, Россия) по методике [20]. Жидкофазные продукты синтеза подвергали фракционированию в зависимости от температуры кипения и определяли групповой состав методом капиллярной газожидкостной хромато-масс-спектрометрии на газовом хроматографе Agilent GC 7890 (“Agilent”, США) с масс-селективным детектором MSD 5975С (“Agilent”, США) и капиллярной колонкой HP-5MS. Анализ бензиновой фракции (Тн. к. = 180°C) проводили путем ввода 1 мкл пробы с разбавлением газом-носителем в соотношении 1 : 500; 2 мкл дизельной фракции (180–330°C) предварительно растворяли в 1 мл дихлорметана и вводили 1 мкл, без разбавления газом-носителем. Для количественного расчета использовали внешний стандарт. Качественное определение компонентов масс-спектрометрическим методом согласуется с результатами работ [23, 24].
ЯМР-анализ водного слоя осуществляли на приборе Avance Neo с магнитом Ascend 300 MHz (“Bruker”, Германия) без ввода дейтерорастворителей. В пробу воды добавляли трет-бутиловый спирт в качестве внутреннего стандарта для количественного расчета.
Углеводороды с поверхности катализатора после синтеза удаляли путем их последовательной экстракции в аппарате Сокслета в течение 1 ч 1,2-диметилбензолом (о-ксилолом) и затем в течение 1 ч н-гептаном.
Морфологию поверхности катализатора изучали на сканирующем электронном микроскопе (СЭМ) Quanta 200 (“FEI Company”, США) с ускоряющим напряжением 30 кВ, оснащенном системой энергодисперсионного анализа для определения элементного состава поверхности образцов.
Рентгенофазовый анализ (РФА) катализаторов проводили с использованием специализированного источника синхротронного излучения “КИСИ-Курчатов” (Россия) с длиной волны 0.793508 Å, стандарт LaB6. Качественный фазовый состав определяли с помощью PDF-2 [25] в программном комплексе Crystallographica.
Размер наночастиц металлического кобальта для характеристической линии со значением 2θ равным 43.6° рассчитывали по уравнению Шеррера [26]:
где d(Co0) – средний размер частиц, нм; K – безразмерный коэффициент формы частицы (K = = 0.89); λ – длина волны рентгеновского излучения, нм; θ – брэгговский угол, рад; β – ширина рефлекса на полувысоте, рад.РЕЗУЛЬТАТЫ И ИХ ОБСУЖДЕНИЕ
Характеристика катализатора
Исходный восстановленный и отработавший при давлении 8.0 МПа катализаторы были исследованы методами сканирующей электронной микроскопии (СЭМ) и рентгенофазового анализа (РФА).
На СЭМ-изображениях (рис. 1) поверхности катализаторов видны четкие межфазные границы агломератов кобальта шарообразной формы размером 2–3 мкм. Ранее было показано [21], что введение оксида алюминия воздействует на степень гетерогенности, форму и ориентацию зерен кристаллитов: при концентрации 0.4–1 мас. % в ходе термообработки образуется большое число однотипных по форме частиц оксидной фазы кобальта, а после их восстановления – частиц металлического кобальта со средним размером 8 нм. На поверхности катализатора после синтеза углеводородов при давлении 8.0 МПа обнаружен углерод, расположение которого совпадает с локализацией агломератов кобальта (рис. 1б). Углерод на поверхности отработавшего катализатора может входить в состав синтезированных углеводородов и/или поверхностной фазы карбида кобальта, а также представлять собой углеродные отложения, образующиеся по реакции диспропорционирования СО.
Рис. 1.
Элементное картографирование поверхности катализаторов: а – исходный восстановленный; б – отработавший при 8.0 МПа.
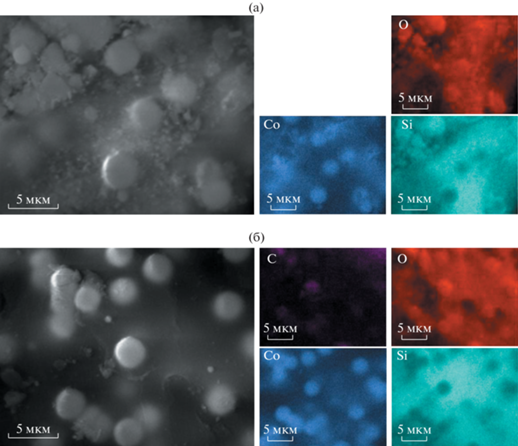
На дифрактограмме восстановленного катализатора (рис. 2, кривая 1) наблюдается присутствие хорошо окристаллизованных фаз металлического кобальта Co0 и оксида CoO с характерными максимумами дифракции в области углов 2θ = 18°–55°. В структуре образца, отработавшего при высоком давлении (рис. 2, кривая 3), идентифицирована кристаллическая фаза карбида кобальта Со2С, что отличает его от катализаторов, отработавших при давлениях 2.0 МПа (рис. 2, кривая 2) и 6.0 МПа [27]. На дифрактограммах как исходного восстановленного, так и отработавших при давлениях 2.0 и 8.0 МПа образцов оксид кремния дает широкое диффузное гало в области малых углов вследствие его рентгеноаморфности. Для этих образцов размеры наночастиц Со0, определенные по уравнению Шеррера, составляют ~10 нм.
Каталитические испытания
Давление 2.0 МПа. Показатели процесса получения углеводородов в зависимости от температуры синтеза в проточно-циркуляционном режиме работы при давлении 2.0 МПа представлены в табл. 1.
Таблица 1.
Показатели процесса в зависимости от температуры синтеза*
Темпера-тура, °С | Н2/СО в рецикле | Конверсия СО, % | Селективность, % | GC5+ | Gолефины | Gоксигенаты | |||
---|---|---|---|---|---|---|---|---|---|
СН4 | С2–С4 | С5+ | СО2 | ||||||
кг ${\text{м}}_{{{\text{кат}}}}^{{ - 3}}$ ч–1 | |||||||||
205 | 1.72 | 26.0 | 17.8 | 10.9 | 69.7 | 1.6 | 43.2 | 2.7 | 0.1 |
215 | 1.63 | 37.6 | 20.2 | 9.4 | 68.8 | 1.6 | 62.1 | 4.8 | 0.1 |
225 | 1.55 | 49.3 | 20.1 | 11.2 | 67.6 | 1.1 | 80.0 | 8.3 | 0.3 |
* Условия процесса: Р = 2.0 МПа; ОСГ = 1000 ч–1; Н2/СО = 1.85; Kц = 2.3. Kц – коэффициент циркуляции: отношение объемного расхода возвратного газа к объемному расходу свежего синтез-газа.
Примечание: GC5+, Gолефины и Gоксигенаты – производительность по углеводородам, олефинам и оксигенатам соответственно.
Установлено, что повышение температуры в диапазоне 205–225°С способствует росту конверсии СО и производительности по углеводородам С5+. Подъем температуры сопровождается незначительным уменьшением селективности образования углеводородов С5+ и увеличением доли газообразных продуктов (углеводородов С1–С4, СО2). Наблюдаемые тенденции изменения селективности при повышении температуры синтеза характерны для процесса получения синтетических углеводородов [28–30] и объясняются различием энергий активации элементарных стадий роста и обрыва углеводородной цепи.
Основными продуктами синтеза (табл. 2) являются насыщенные углеводороды линейного строения, также обнаружено относительно небольшое количество изопарафинов, олефинов и оксигенатов. Подъем температуры способствует изменению фракционного состава продуктов С5+ в сторону углеводородов с более короткой цепью, доля изопарафинов и олефинов немного увеличивается за счет уменьшения селективности по н‑парафинам. Содержание обнаруженных оксигенатов, в основном первичных спиртов, составляет 0.3 мас. % и существенно не изменяется с ростом температуры.
Таблица 2.
Состав продуктов, полученных при разной температуре синтеза*
Температура, °С | Группа | Содержание, мас. % | Сумма | o/п** | |||
---|---|---|---|---|---|---|---|
C5–C10 | C11–С18 | С19+ | |||||
205 | н-Парафины | 13.7 | 47.4 | 31.6 | 92.7 | 93.4 | 0.07 |
Изопарафины | 0.2 | 0.3 | 0.2 | 0.7 | |||
Олефины | 3.5 | 1.4 | 1,4 | 6.3 | |||
Оксигенаты | 0.3 | 0.0 | 0.0 | 0.3 | |||
Сумма | 17.7 | 49.1 | 33.2 | 100.0 | |||
215 | н-Парафины | 16.4 | 38.2 | 35.5 | 90.1 | 91.8 | 0.08 |
Изопарафины | 0.5 | 0.6 | 0.6 | 1.7 | |||
Олефины | 5.9 | 1.7 | 0.2 | 7.8 | |||
Оксигенаты | 0.2 | 0.0 | 0.0 | 0.2 | |||
Сумма | 23.0 | 40.5 | 36.3 | 100.0 | |||
225 | н-Парафины | 16.7 | 47.9 | 21.3 | 85.9 | 89.2 | 0.12 |
Изопарафины | 0.7 | 1.8 | 0.8 | 3.3 | |||
Олефины | 6.9 | 3.4 | 0.1 | 10.4 | |||
Оксигенаты | 0.3 | 0.1 | 0.0 | 0.4 | |||
Сумма | 24.6 | 53.2 | 22.2 | 100.0 |
Давление 8.0 МПа. Повышение давления процесса синтеза углеводородов с 2.0 до 8.0 МПа оказывает положительное влияние на скорость реакции Фишера–Тропша, селективность и производительность образования углеводородов С5+ (ср. табл. 1 и 3): конверсия СО увеличивается до 77.9%, а производительность по углеводородам С5+ – до 133.0 кг ${\text{м}}_{{{\text{кат}}}}^{{ - 3}}$ ч–1.
Таблица 3.
Показатели процесса в зависимости от температуры синтеза*
Температура, °С | Н2/СО в рецикле | Конверсия СО, % | Селективность, % | GC5+ | Gолефины | Gоксигенаты | |||
---|---|---|---|---|---|---|---|---|---|
СН4 | С2–С4 | С5+ | СО2 | ||||||
кг ${\text{м}}_{{{\text{кат}}}}^{{ - 3}}$ ч–1 | |||||||||
205 | 1.70 | 54.9 | 13.7 | 8.0 | 78.1 | 0.2 | 89.8 | 14.0 | 3.3 |
215 | 1.59 | 66.6 | 12.5 | 8.6 | 78.7 | 0.2 | 109.8 | 21.2 | 4.0 |
225 | 1.41 | 77.9 | 11.4 | 6.8 | 81.5 | 0.3 | 133.0 | 27.9 | 5.6 |
* Условия процесса: Р = 8.0 МПа; ОСГ = 1000 ч–1; Н2/СО = 1.85; Kц = 2.3. Kц – коэффициент циркуляции: отношение объемного расхода возвратного газа к объемному расходу свежего синтез-газа.
Примечание: GC5+, Gолефины и Gоксигенаты – производительность по углеводородам, олефинам и оксигенатам соответственно.
В отличие от результатов исследований при 2.0 МПа, рост температуры при давлении 8.0 МПа сопровождается возрастанием селективности образования углеводородов С5+ и, соответственно, уменьшением доли газообразных продуктов. Подобный “неожиданный отклик” катализатора на повышение температуры наблюдался нами ранее при давлении 6.0 МПа в проточно-циркуляционном режиме [14, 15].
Групповой состав конденсированных неполярных продуктов, полученных при 8.0 МПа, приведен в табл. 4. Как и при давлении 2.0 МПа в продуктах синтеза преобладают углеводороды линейного строения и в незначительных количествах присутствуют изопарафины. При этом выход олефинов С5–С25 увеличивается в 2 раза, а выход первичных спиртов с количеством атомов углерода в цепи от 5 до 16 – на порядок. В водной фазе также обнаружены спирты С1–С4, содержание которых составляет 0.77, 1.1 и 1.83 мас. % при 205, 215 и 225°C соответственно.
Таблица 4.
Состав продуктов, полученных при разной температуре синтеза*
Температура, °С | Группа | Содержание, мас. % | Сумма | o/п** | |||
---|---|---|---|---|---|---|---|
C5–C10 | C11–С18 | С19+ | |||||
205 | н-Парафины | 12.6 | 25.4 | 41.7 | 79.7 | 80.7 | 0.19 |
Изопарафины | 0.5 | 0.5 | 0.0 | 1.0 | |||
Олефины | 7.4 | 7.3 | 0.9 | 15.6 | |||
Оксигенаты | 2.5 | 1.2 | 0.0 | 3.7 | |||
Сумма | 23.0 | 34.4 | 42.6 | 100.0 | |||
215 | н-Парафины | 20.5 | 24.1 | 31.0 | 75.6 | 77.1 | 0.25 |
Изопарафины | 0.5 | 0.7 | 0.3 | 1.5 | |||
Олефины | 11.3 | 7.1 | 0.9 | 19.3 | |||
Оксигенаты | 2.7 | 0.9 | 0.0 | 3.6 | |||
Сумма | 35.0 | 32.8 | 32.2 | 100.0 | |||
225 | н-Парафины | 17.4 | 22.5 | 33.8 | 73.7 | 74.8 | 0.28 |
Изопарафины | 0.5 | 0.6 | 0.0 | 1.1 | |||
Олефины | 10.7 | 9.5 | 0.8 | 21.0 | |||
Оксигенаты | 3.0 | 1.2 | 0.0 | 4.2 | |||
Сумма | 31.6 | 33.8 | 34.6 | 100.0 |
С повышением температуры от 205 до 225°С доля углеводородов С19+ снижается, селективность по жидким углеводородам C5–С18 увеличивается. Количество спиртов в продуктах синтеза изменяется незначительно (от 3.7 до 4.2 мас. %), а содержание олефинов растет от 15.6 до 21.0 мас. %. Однако с подъемом температуры от 215 до 225°С доля углеводородов С19+ возрастает, а доля углеводородов C5–С18 снижается. Вероятно, зафиксированный результат в режиме работы циркуляции газа вызван обеднением синтез-газа водородом на входе в реактор (табл. 3) при повышении температуры, что оказывает положительное влияние на селективность образования углеводородов С5+. К тому же циркулирующий газ содержит в своем составе, помимо СО и Н2, углеводороды С2+, которые могут способствовать увеличению вероятности роста цепи углеводородов.
Таким образом, повышение давления значительно влияет на селективность образования как высших спиртов, так и олефинов, а повышение температуры – в большей степени на селективность образования олефинов (рис. 3).
Рис. 3.
Содержание спиртов (а) и олефинов (б) в продуктах С5+ синтеза, полученных при разных температурах и давлениях.
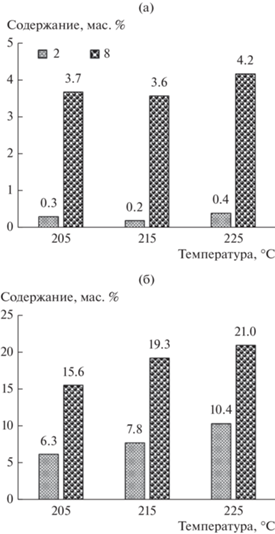
На рис. 4 показано, как меняется селективность образования спиртов и олефинов в зависимости от температуры процесса при давлении 8.0 МПа. Отметим, что длина углеродной цепи синтезированных спиртов при всех рассматриваемых температурах не превышает шестнадцати С-атомов, в то время как длина цепи олефинов – двадцати пяти. Распределение спиртов бимодальное с максимумами C5 и C10, причем бимодальность проявляется более четко с ростом температуры. Распределение олефинов, в отличие от спиртов, унимодальное с максимумом, приходящимся на C7–C8. Селективность образования спиртов и олефинов увеличивается с повышением температуры синтеза.
Рис. 4.
Селективность образования спиртов и олефинов и логарифмическая зависимость массовой доли оксигенатов и олефинов, отнесенной к числу атомов углерода Wn/n (на вставках), от числа углеродных атомов при температурах 205 (а), 215 (б) и 225°С (в).
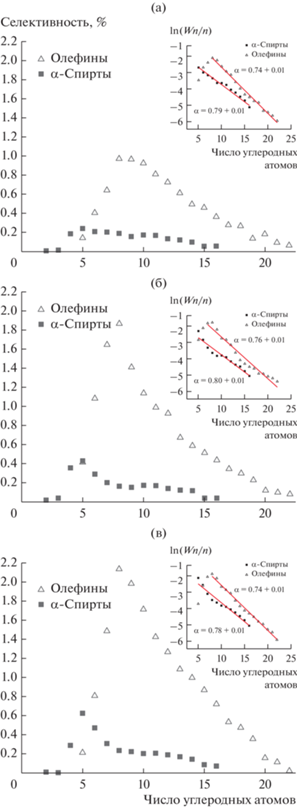
Различный характер распределения этих продуктов – унимодальность в случае олефинов и бимодальность для спиртов, а также ограничение длины их цепей 25 и 16 атомами углерода соответственно свидетельствуют о том, что образующиеся в реакции спирты не являются продуктами гидратации олефинов.
Возрастание селективности по олефинам и спиртам, очевидно, является следствием комбинации двух факторов – увеличения давления и применения режима рециркуляции. Действительно, повышение давления с 2.0 до 8.0 МПа приводит к росту скорости реакции синтеза Фишера–Тропша и, соответственно, к большей конверсии синтез-газа за один проход. Разбавление свежего синтез-газа хвостовыми газами в рецикле заметно уменьшает соотношение Н2/СО на входе в реактор. Пониженное парциальное давление водорода способствует увеличению вклада в обрыв цепи реакции β-гидридного элиминирования с образованием олефинов. С другой стороны, рост конверсии СО ведет к повышению парциального давления воды в реакционной зоне, что также увеличивает селективность образования олефинов за счет ингибирования гидрирования последних [31]. Указанные эффекты более ярко проявляются с подъемом температуры (табл. 2 и 4).
Считается [32, 33], что образование спиртов в условиях реакции синтеза ФТ на кобальтовых катализаторах происходит на границе раздела фаз металлического кобальта и его карбида, Со0/Со2С. Инициирование и рост цепи протекают на наночастицах Со0 с образованием поверхностных частиц Со–CxHy, и именно реакция обрыва цепи определяет состав образующихся продуктов [33, 34]. В случае обрыва цепи путем β-гидридного элиминирования или гидрогенолиза соединений Со–CxHy продуктами являются олефины или парафины соответственно. Карбид кобальта способен ассоциативно адсорбировать СО с последующим его внедрением в растущую на соседней фазе Со0 углеводородную цепь Со–CxHy по связи кобальт–углерод [33, 35]. Это приводит к появлению ацильных частиц Со–(СО)–CxHy, дальнейшее восстановление которых водородом до Со–СН(ОН) –CxHy и последующим гидрогенолизом дает первичные спирты. Таким образом, процессы образования спиртов конкурируют с реакциями получения углеводородов, и для этого необходима фаза Со2С, находящаяся в непосредственной близости к металлическому Со0. Например, в работе [36] было показано, что промотирование кобальта оксидом лантана способствует формированию фазы Со2С, а увеличение соотношения Со2С/Со повышает селективность по спиртам. Схожий эффект был обнаружен при использовании в качестве промотора марганца [37], который облегчает диссоциацию и диспропорционирование CO на поверхности катализатора и усложняет адсорбцию H2, создавая на поверхности среду, обогащенную углеродом и обедненную водородом. В свою очередь, это приводит к превращению металлической фазы Co0 в Co2C, а в условиях реакции – к образованию наночастиц Co–Co2C. В нашем случае такой же эффект может достигаться сочетанием высокого общего давления и рециркуляции газа: оба фактора ведут к заметному обеднению синтез-газа водородом. Повышенная концентрация СО на поверхности катализатора облегчает протекание реакции диспропорционирования и формирование фазы карбида кобальта, что согласуется с данными рентгенофазового анализа (рис. 2). С другой стороны, высокое парциальное давление СО благоприятствует внедрению СО в адсорбированные частицы СНx [38, 39], что приводит к увеличению селективности по высшим спиртам.
ЗАКЛЮЧЕНИЕ
На высокопроизводительном катализаторе Со–Al2O3/SiO2 исследованы закономерности синтеза оксигенатов и олефинов в условиях высокого давления (8.0 МПа) в режиме рециркуляции газа. Установлено, что:
– высокое давление и рециркуляция газа способствуют формированию фазы карбида кобальта, что приводит к интенсификации образования высших первичных спиртов;
– повышение давления в условиях рециркуляция газа одновременно благоприятно сказывается на селективности образования в отношении олефинов;
– подтвержден ранее обнаруженный при осуществлении процесса ФТ при повышенном давлении синтез-газа необычный эффект снижения селективности образования по газообразным углеводородам С1–С4 с подъемом температуры синтеза.
Результаты проведенного исследования дают основание полагать, что дальнейшая модификация катализатора и условий процесса (изменение кратности циркуляции газа, давления и др.) позволит получать высшие спирты и олефины с еще большей селективностью.
Список литературы
Dry M.E. // Catal. Today. 2002. V. 71. P. 227.
Storch H., Golumbic N., Anderson R. THE FISCHER-TROPSCH AND RELATED SYNTHESES. Including a Summary of Theoretical and Applied Contact Catalysis. N.Y.–London, 1951. Сторч Г., Голамбик Н., Андерсон Р. Синтез углеводородов из окиси углерода и водорода. М.: Издательство иностранной литературы, 1954. 516 с.
Кунгурова О.А., Штерцер Н.В., Чермашенцева Г.К., Сименцова И.И., Хасин А.А. // Катализ в промышленности. Т. 16. № 4. С. 57. (Kungurova O.A., Shtertser N.V., Chermashentseva G.K., Simentsova I.I., Khassin A.A. // Catal. Indust. 2017. V. 9. № 1. P. 23.)
Голубь Ф.С., Болотов В.А., Пармон В.Н. // Катализ в промышленности. 2020. Т. 20. №. 6. С. 433.
Khodakov A.Y., Chu W., Fongarland P. // Chem. Rev. 2007. V. 107. P. 1692.
Davis B.H // Indust. Eng. Chem. Res. 2007. V. 46. P. 8938.
Gao X., Zhang J., Chen N., Ma Q., Fan S., Zhao T., Tsubaki N. // Chin. J. Catal. 2016. V. 37. P. 510.
Guo X., Guo L., Cui Y., Vitidsant T., Reubroycharoen P., Liu G., Wu J., Yoneyama Y., Yang G., Tsubaki N. // Catal. Today. 2021. V. 375. P. 290.
Abdelsayed V., Shekhawat D., Poston J.A., Spivey J.J. // Catal. Today. 2013. V. 207. P. 65.
Zaman S.F., Pasupulety N., Al-Zahrani A.A., Daous M.A., Al-Shahrani S.S., Driss H., Petrov L.A., Smith K.J. // Appl. Catal. A: General. 2017. V. 532. P. 133.
Heracleous E., Liakakou E.T., Lappas A.A., Lemonidou A.A. // Appl. Catal. A: General. 2013. V. 455. P. 145.
Pei Y., Liu J., Zhao Y., Ding Y., Liu T., Dong W., Zhu H., Su H., Yan L., Li J., Li W.X. // ACS Catal. 2015. V. 5. P. 3620.
Zhang X., Li Z., Guo Q., Zheng H., Xie K. // Fuel Proces. Technol. 2010. V. 91. P. 379.
Savost'yanov A.P., Yakovenko R.E., Narochnyi G.B., Sulima S.I., Bakun V.G., Soromotin V.N., Mitchenko S.A. // Catal. Commun. 2017. V. 99. P. 25.
Savost’yanov A.P., Narochnyi G.B., Yakovenko R.E., Mitchenko S.A., Zubkov I.N. // Petrol. Chem. 2018. V. 58. P. 76.
Савостьянов А.П., Яковенко Р.Е., Нарочный Г.Б., Бакун В.Г., Сулима С.И., Якуба Э.С., Митченко С.А. // Кинетика и катализ. 2017. Т. 58. № 1. С. 86. (Savost’yanov A.P., Yakovenko R.E., Narochnyi G.B., Bakun V.G., Sulima S.I., Yakuba E.S., Mitchenko S.A. // Kinet. Catal. 2017. V. 58. P. 81.)
Нарочный Г.Б., Яковенко Р.Е., Савостьянов А.П., Бакун В.Г. // Катализ в промышленности. 2016. № 1. С. 37. (Narochnyi G.B., Yakovenko R.E., Savost’yanov A.P., Bakun V.G. // Catal. Indust. 2016. V. 8. P. 139.)
Savost’yanov A.P., Yakovenko R.E., Sulima S.I., Bakun V.G., Narochnyi G.B., Chernyshev V.M., Mitchenko S.A. // Catal. Today. 2017. V. 279. P. 107.
Borg Ø., Dietzel P.D.C., Spjelkavik A.I., Tveten E.Z., Walmsley J.C., Diplas S., Eri S., Holmen A., Rytter E. // J. Catal. 2008. V. 259. P. 161.
Яковенко Р.Е., Зубков И.Н., Нарочный Г.Б., Папета О.П., Денисов О.Д., Савостьянов А.П. // Кинетика и катализ. 2020. Т. 61. № 2. С. 278. (Yakovenko R.E., Zubkov I.N., Narochniy G.B., Papeta O.P., Denisov O.D., Savost’yanov A.P. // Kinet. Catal. 2020. V. 61. P. 310.)
Сулима С.И., Бакун В.Г., Яковенко Р.Е., Шабельская Н.П., Салиев А.Н., Нарочный Г.Б., Савостьянов А.П. // Кинетика и катализ. 2018. Т. 59. № 2. С. 240. (Sulima S.I., Bakun V.G., Yakovenko R.E., Shabel’skaya N.P., Saliev A.N., Narochnyi G.B., Savost’yanov A.P. // Kinet. Catal. 2018. V. 59. P. 218.)
Yakovenko R.E., Savost’yanov A.P., Narochniy G.B., Soromotin V.N., Zubkov I.N., Papeta O.P., Svetogorov R.D., Mitchenko S.A. // Catal. Sci. Technol. 2020. V. 10. P. 7613.
Shafer W.D., Gnanamani M.K., Graham U.M., Yang J., Masuku C.M., Jacobs G., Davis B.H. // Catalysts. 2019. V. 9. P. 259.
Kasht A., Hussain R., Ghouri M., Blank J., Elbashir N.O. // Amer. J. Anal. Chem. 2015. V. 6. P. 659.
PDF-2. The powder diffraction file TM. International Center for Diffraction Data (ICDD). PDF-2 Release 2012. web site: www.icdd.com (2014).
Young R.A. The Rietveld Method. Oxford University Press, 1995. 298 p.
Савостьянов А.П., Яковенко Р.Е., Нарочный Г.Б., Зубков И.Н., Сулима С.И., Соромотин В.Н., Митченко С.А. // Нефтехимия. 2018. Т. 58. № 1. С. 80. (Savost’yanov A.P., Yakovenko R.E., Narochnyi G.B., Zubkov I.N., Sulima S.I., Soromotin V.N., Mitchenko S.A. // Petrol. Chem. 2018. V. 60. P. 81.)
Todic B., Ma W., Jacobs G., Davis B.H., Bukur D.B. // J. Catal. 2014. V. 311. P. 325.
Niu C. Xia M., Chen C., Ma Z., Jia L., Hou B., Li D. // Appl. Catal. A: General. 2020. V. 601. P. 117630.
Rytter E., Tsakoumis N.E., Holmen A. // Catal. Today. 2016. V. 261. P. 3.
Okoye-Chine C.G., Moyo M., Liu X., Hildebrandt D. // Fuel Proces. Technol. 2019. V. 192. P. 105.
Ao M., Pham G.H., Sunarso J., Tade M.O., Liu S. // ACS Catalysis. 2018. V. 8. P. 7025.
Luk H.T., Mondelli C., Ferré D.C., Stewart J.A., Pérez-Ramírez J. // Chem. Soc. Rev. 2017. V. 46. P. 1358.
Bhatelia T., Li C., Sun Y., Hazewinkel P., Burke N., Sage V. // Fuel Proces. Technol. 2017. V. 125. P. 277.
Wang B., Liang D., Guan Z., Li D., Zhang R. // J. Phys. Chem. 2020. V. 124. P. 5749.
Lebarbier V.M., Mei D., Kim D.H., Andersen A., Male J.L., Holladay J.E., Rousseau R., Wang Y. // J. Phys. Chem. C. 2011. V. 115. P. 17440.
Zhao Z., Lu W., Yang R., Zhu H., Dong W., Sun F., Jiang Z., Lyu Y., Liu T., Du H., Ding Y. // ACS Catalysis. 2018. V. 8. P. 228.
Mahdavi V., Peyrovi M.H., Islami M., Mehr J.Y. // Appl. Catal. A: General. 2005. V. 281. P. 259.
Han S.J., Park G., Lee Y.-J., Jun K.-W., Kim S.K., Kim Y.T., Kwa G. // Mol. Catal. 2019. V. 475. P. 110481.
Дополнительные материалы отсутствуют.
Инструменты
Кинетика и катализ