Кинетика и катализ, 2022, T. 63, № 5, стр. 676-683
Расширенные возможности анализа нанесенных металлических катализаторов и нанокомпозитов методом динамического рассеяния света
a ФГБУН Институт катализа им. Г.К. Борескова СО РАН
630090 Новосибирск, просп. Акад. Лаврентьева, 5, Россия
b ФГАОУ ВО Новосибирский национальный исследовательский государственный университет
630090 Новосибирск, ул. Пирогова, 1, Россия
* E-mail: ylarichev@gmail.com
Поступила в редакцию 27.12.2021
После доработки 12.04.2022
Принята к публикации 16.04.2022
- EDN: GVWAGI
- DOI: 10.31857/S0453881122050082
Аннотация
Настоящее исследование является продолжением работ по использованию метода динамического светорассеяния (ДРС) для анализа размеров частиц активного компонента в нанесенных катализаторах. Было показано, что предлагаемый подход STS (from solid to sol) также применим для нанесенных катализаторов на основе труднорастворимых носителей и, кроме того, для нанокомпозитов. Установлено, что для анализа методом ДРС достаточно частичного растворения или разрушения носителя с образованием раствора, содержащего искомые наночастицы. Обнаружено, что в определенных условиях в процессе растворения катализатора может наблюдаться эффект вторичной агрегации наночастиц в растворе, препятствующий корректным измерениям. Предложен способ, позволяющий избежать вторичной агрегации частиц при селективном растворении носителя. Продемонстрировано хорошее соответствие между результатами, полученными новым (ДРС) и традиционными (ПЭМ и РФА) методами.
ВВЕДЕНИЕ
Дисперсность активного компонента в нанесенном катализаторе является важным признаком, определяющим активность и стабильность его работы в различных каталитических реакциях [1–4]. Поэтому очень важным является наличие диагностических методов, позволяющих оценивать размеры частиц активного компонента. Для этих задач давно и широко применяются стандартные методы, такие как просвечивающая электронная микроскопия (ПЭМ) и рентгеновская дифрактометрия (РФА) [5–7]. К значимым их недостаткам можно отнести очень высокую стоимость оборудования, наличие высококвалифицированного персонала для его обслуживания, а также заметные временные затраты на получение и обработку данных. Кроме того, у этих методов недостаточно высокая чувствительность, поэтому с их помощью затруднительно анализировать частицы, относящиеся к “хвостам” распределений по размерам, в силу их низкой статистической значимости. Однако такие недооцененные частицы могут содержать существенное количество активного компонента по массе и являться важным маркером начавшегося процесса спекания в силу локальных перегревов в ходе каталитической реакции [8, 9]. Более простые и доступные методы, например хемосорбция СО, не всегда применимы по ряду других причин (поверхностное загрязнение, блокировка пор, эффекты сильного взаимодействия металл–носитель и др.) [5]. Поэтому для некоторых задач и приложений представляет интерес использовать более быстрые, дешевые и доступные способы измерения размеров наночастиц. В настоящее время существует и развивается большое количество различных подходов для определения размеров наночастиц [10–12]. Нам же представляется интересным и перспективным применять для этих целей метод динамического рассеяния света (ДРС) [13, 14]. Ранее в наших работах [15, 16] было показано, как можно адаптировать его для анализа нанесенных катализаторов. Основная идея предложенной методики STS (from solid to sol) заключалась в проведении селективного процесса растворения пористого носителя и получении относительно стабильного раствора, содержащего нанесенные частицы металла практически в неизменном виде [15–17]. Далее полученный раствор анализировали методом ДРС, а найденные размеры частиц имели хорошее соответствие с данными методов ПЭМ и РФА для исходных катализаторов. Однако эффективность предлагаемой методики была проверена только для относительно легкорастворимых оксидных носителей и стабильных наночастиц, состоящих из благородных металлов. Поэтому остается открытым вопрос о возможности ее применения для анализа катализаторов на основе труднорастворимых носителей, например, на основе углерода, а также для менее стабильных наночастиц. С учетом высокой чувствительности ДРС неясно, необходимо ли полностью растворять носитель или для проведения анализа вполне достаточно его частичного растворения или разрушения. Целью настоящей работы является дальнейшее развитие методики STS и расширение ее возможностей применительно к методу ДРС для анализа нанесенных катализаторов и нанокомпозитов.
ЭКСПЕРИМЕНТАЛЬНАЯ ЧАСТЬ
Приготовление образцов
Для проверки возможностей методики STS было исследовано пять различных нанесенных металлических катализаторов и один образец нанокомпозита:
Ru/SiO2. Образец приготовлен пропиткой по влагоемкости SiO2 с удельной поверхностью 160 м2/г. В качестве предшественника использовано соединение Ru(OH)Cl3. После пропитки и сушки образец восстановливали в токе водорода при 450°С. Содержание рутения в образце составило 5.0 вес. %.
Rh/TiO2. Образец готовили пропиткой по влагоемкости диоксида титана (смесь рутила и анатаза) с удельной поверхностью 120 м2/г. Предшественником был уксуснокислый раствор родия, полученный путем растворения Rh(OH)3 в ледяной уксусной кислоте. После пропитки и сушки образец прокаливали на воздухе при температуре 400°С. Содержание родия в образце – 2.0 вес. %.
Au/C. Образец приготовлен адсорбцией комплекса [Au(NH3)4](NO3)3 на мезопористый углеродный материал типа Сибунит с удельной поверхностью 490 м2/г. После промывки и сушки образец восстанавливали в водороде 300°С. Содержание золота в образце составило 1.4 вес. %.
Ni/SiO2. Образец получали пропиткой по влагоемкости SiO2 с удельной поверхностью 300 м2/г. В качестве предшественника активного компонента использовали нитрат никеля. После пропитки и сушки образец восстановливали в токе водорода при 600°С. Содержание никеля в образце – 10.0 вес. %.
Pd/g-C3N4. Образец был приготовлен пропиткой по влагоемкости графитоподобного нитрида углерода с удельной поверхностью 7 м2/г. В качестве предшественника применяли нитрат палладия. После пропитки и сушки образец восстановливали в спиртовом растворе NaBH4, затем после промывки водой просушивали на воздухе при температуре 110°С. Содержание палладия в образце составило 1.0 вес. %.
Рисовая шелуха. В работе была изучена шелуха риса, выращенного в Краснодарском крае РФ, предварительно измельченная до размера частиц <0.25 мм. Данный природный нанокомпозит содержит 19–25% лигнина, 34–42% целлюлoзу и 17–22% гемицеллюлозы. Остаток (до 20%) приходится на неорганический компонент, который на 95% состоит из кремнезема. Более подробное описание свойств рисовой шелухи приведено в работах [18, 19].
Процедура селективного растворения носителя или матрицы (STS)
Для каждого из образцов способ селективного растворения носителя подбирали индивидуально. Обычно растворение нанесенных катализаторов осуществляли при добавлении навески 0.5 г катализатора к 10 мл 98% серной кислоты, после чего полученную смесь нагревали от 90 до 180°С в зависимости от типа носителя.11 Наибольшая температура нагрева была использована для разрушения углеродного носителя. После охлаждения смеси до комнатной температуры из нее отбирали аликвоту для анализа, которую при необходимости разбавляли серной кислотой, и анализировали методом ДРС. В случае образцов на основе силикагеля вместо серной кислоты применяли 1 М раствор NaOH. В указанных условиях образцы зачастую растворяются лишь частично, но в силу высокой чувствительности метода ДРС этого достаточно для идентификации наноразмерных металлических частиц в полученных растворах. Следует отметить, что образцы нанесенных катализаторов (Rh/TiO2 и Ni/SiO2) непосредственно перед процедурой растворения дополнительно восстановливали водным раствором NaBH4 с последующей промывкой и сушкой.
Рисовую шелуху растворяли в растворе азотной кислоты с добавлением пероксида водорода. К 20 мл азотной кислоты (68%) мелкими порциями при энергичном перемешивании и небольшом нагревании добавлялся 1.0 г рисовой шелухи в виде тонкозернистого порошка. В процессе перемешивания наблюдалось выделение бурого газа (оксиды азота). После прекращения выделения оксидов азота полученную систему доводили до кипения, остужали и затем к ней по каплям добавляли 5 мл 30% раствора H2O2, после чего снова доводили до кипения. Образовавшийся раствор желтого цвета медленно остужали до комнатной температуры. Далее из этого раствора отбирали аликвоту, которую разбавляли дистиллированной водой и анализировали методом ДРС.
Поскольку большинство приготовленных растворов содержало в своем составе агрессивные кислоты, то стандартную процедуру фильтрования через тканевые фильтры не использовали.
Методы исследования
Электронная микроскопия. Снимки просвечивающей электронной микроскопии (ПЭМ) получали на приборе JEM-2010 (“JEOL”, Япония) с максимальным разрешением по решетке 0.14 нм и ускоряющим напряжением 200 кВ. Для расчета распределения частиц по размерам для каждого образца измеряли линейный размер не менее 350 частиц.
Рентгеновская дифрактометрия. Дифракционные измерения проводили с помощью дифрактометра “ARLX’TRA” (“Thermo Fisher Scientific”, США) с использованием CuKα-излучения (длина волны − 1.5418 Å) в интервале углов 2θ от 10°−90° с шагом 0.05°. Время накопления в точке − 5 с. Величины области когерентного рассеяния (ОКР) для нанесенных металлов определяли с помощью формулы Шеррера.
Динамическое рассеяние света (ДРС). Эксперименты по динамическому светорассеянию выполняли с применением спектрометра Photocor (ООО “Фотокор”, Москва, Россия) с цифровым коррелятором (288 каналов). Измерения осуществляли при рассеивающем угле 160° и температуре 24°С. Длина волны лазерного излучения составляла 638 нм. Обработку первичных данных динамического светорассеяния проводили с помощью программы DynaLS [21]. Из полученных автокорреляционных функций рассчитывали распределения по интенсивности. Для определения размеров частиц использовали стандартные величины вязкости и коэффициентов преломления для серной кислоты (26.7 × 10−3 Па с; 1.397), 1 М раствора NaOH (1.116 × 10−3 Па с; 1.343) и воды (8.90 × 10−4 Па с; 1.333) соответственно. Средний размер частиц вычисляли по формуле Стокса−Эйнштейна для сферических частиц [22]:
где D − коэффициент диффузии частицы, Rh − гидродинамический радиус частицы, η − вязкость растворителя, k − постоянная Больцмана.Каждый образец анализировали не менее 5 раз с последующим усреднением полученных результатов. Время накопления для одного измерения составляло 2 мин.
РЕЗУЛЬТАТЫ И ИХ ОБСУЖДЕНИЕ
Все приготовленные образцы нанесенных катализаторов были изучены методами ПЭМ и РФА. В качестве примера на рис. 1a показано изображение ПЭМ для образца Ru/SiO2. На рис. 1б представлена дифрактограмма этого катализатора с характерными для структуры металлического рутения рефлексами. Из полученных данных ПЭМ для всех нанесенных катализаторов были рассчитаны распределения частиц по размерам и определены средние размеры частиц, которые приведены в табл. 1. Также в табл. 1 указаны величины области когерентного рассеяния (ОКР) для металлических частиц, полученные с помощью метода РФА.
Рис. 1.
a − Микрофотография ПЭМ для образца Ru/SiO2; б − данные рентгеновской дифракции для Ru/SiO2. Положения основных рефлексов для структуры металлического Ru (JCPDS 06-0663) показаны штрих-диаграммой.
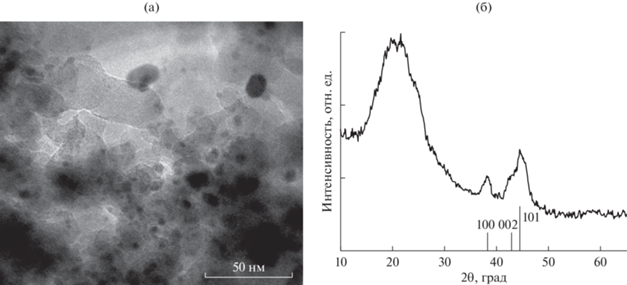
Таблица 1.
Средние размеры для дисперсных частиц металлов по данным методов ПЭМ, РФА и ДРС
Образец | 〈dl〉, нм | 〈dm〉, нм | 〈ОКР〉, нм | 〈d6/5〉, нм | 〈dДРС〉, нм |
---|---|---|---|---|---|
Ru/SiO2 | 3.5 ± 2.1 | 10.3 | 6.2 | 15.4 | 20.0 ± 4.4 |
Rh/TiO2 | 14.5 ± 9.1 | 23.5 | − | 28.4 | 31.1 ± 7.3 |
Au/C | 2.2 ± 1.3 | 3.7 | 16.8 | 5.0 | 17.2 ± 4.8 |
Ni/SiO2 | 5.3 ± 3.8 | 12.1 | 10.8 | 17.5 | 22.9 ± 6.2 |
Pd/g-C3N4 | 5.1 ± 3.6 | 16.0 | − | 20.5 | 23.4 ± 4.1 |
Примечание. 〈dl〉 = ΣNidi/ΣNi − средне-линейный размер частиц, 〈dm〉 = ΣNi$d_{i}^{4}$/ΣNi$d_{i}^{3}$ − средне-массовый размер, 〈d6/5〉 = = ΣNi$d_{i}^{6}$/ΣNi$d_{i}^{5}$ − шестой момент распределения, где ΣNi − число частиц с размерами di по данным ПЭМ. 〈ОКР〉 − размер частиц, определенный из данных РФА по формуле Шеррера; 〈dДРС〉 − размер фракции мелких частиц, определенный из распределений, полученных методом ДРС после усреднения по нескольким измерениям. Прочерки означают, что соответствующие показатели не определяли.
Для всех образцов наблюдаются относительно широкие распределения частиц по размерам. Первый момент распределения или средне-линейный размер частиц (〈dl〉) преимущественно относится к мелким частицам, тогда как более высокие моменты распределений (〈dm〉 и особенно 〈d6/5〉) характеризуют в основном уже крупные частицы (табл. 1). Также следует отметить, что для образца Au/C отмечено существенное расхождение величин 〈dm〉 и 〈ОКР〉, что свидетельствует о бимодальном распределении частиц по размерам (табл. 1). Хотя статистических данных ПЭМ оказалось недостаточно для идентификации небольшого количества крупных частиц, тем не менее, они вносят основной вклад в дифрактограмму, поскольку увеличение размеров частиц приводит к уменьшению ширины линии и, следовательно, к повышению ее интенсивности. Для всех остальных образцов распределения частиц по размерам относительно широкие, но мономодальные.
Далее нанесенные катализаторы растворяли в соответствующих кислотах или щелочах и полученные из них металлсодержащие золи анализировали методом ДРС. Рисунок 2 позволяет сравнить распределение частиц Ru по размерам в катализаторе согласно данным ПЭМ и в золе, образовавшемся после частичного растворения данного образца в растворе щелочи по данным ДРС. Ранее было обнаружено, что крупные фракции (2000 нм и более) могут быть отнесены к частицам пыли и остаточным частицам носителя, тогда как мелкая фракция представляет собой частицы нанесенного металла, перешедшие в раствор в более-менее неизменном виде после растворения носителя [15, 16]. Также было показано, что в силу большей чувствительности ДРС к крупным частицам для корректного сравнения результатов ДРС и ПЭМ необходимо брать величину 〈dДРС〉 и величину шестого момента распределения 〈d6/5〉 соответственно [22, 23]. Для исходного образца Ru/SiO2 и Ru-содержащего раствора, образовавшегося при его растворении, можно отметить хорошее согласие между полученными данными (рис. 2 и табл. 1).
Рис. 2.
a − Распределение частиц Ru по размерам, определенное из данных ПЭМ для образца Ru/SiO2; б − распределение (по интенсивности) частиц по размерам согласно данным ДРС для Ru-содержащего раствора после растворения Ru/SiO2.
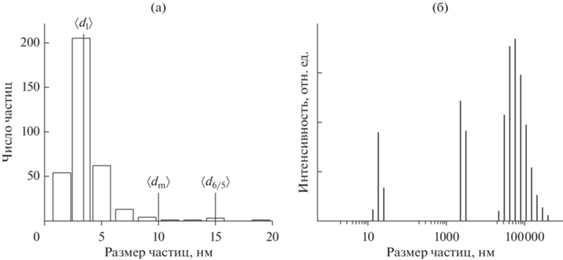
Интересной методической особенностью анализа нанесенных металлических катализаторов методом ДРС является эффект возможной агрегации окисленных наночастиц в растворе, наблюдающейся после растворения носителя. На рис. 3a показано распределение частиц по размерам согласно данным ДРС после растворения носителя в исходном образце Rh/TiO2, приготовленного путем прокалки на воздухе. Как видно из данных для Rh-содержащего раствора, размер частиц мелкой фракции, которая относится к частицам нанесенного металла, существенно сдвинут в сторону бóльших значений, и величина 〈dДРС〉 = 97.1 нм значительно превышает полученную методом ПЭМ величину 〈d6/5〉 =28.4 нм для исходного образца Rh/TiO2 (рис. 3а и табл. 1). С одной стороны, это сильно снижает диагностическую ценность проведенных измерений. С другой стороны, наличие агрегации в растворе может качественно свидетельствовать об окисленности нанесенных частиц металла в катализаторе, что бывает важным в некоторых случаях. Таким образом, при растворении катализаторов, содержащих частично окисленные наночастицы металлов, следует учитывать возможность их агрегации в растворе. Точные причины такого явления до конца не ясны. Согласно литературным данным к основным факторам, негативно влияющим на стабильность металлических наночастиц в растворах и приводящим к их дальнейшей агрегации, можно отнести: уменьшение дзета-потенциала на поверхности частично окисленных частиц; присутствие в растворе ионов металлов, которые могут образоваться при растворении поверхностных оксидов в кислотах, и, в свою очередь, также снижать стабильность наночастиц; адсорбция мелких кластеров на поверхность наночастиц [24–27]. В любом случае, этот эффект препятствует корректным измерениям, и его появление необходимо предотвращать. В ходе проделанных работ обнаружено, что мягкого довосстановления исходных нанесенных катализаторов непосредственно перед процедурой растворения STS обычно хватает для ликвидации поверхностных оксидов и приобретения наночастицами в растворах большей стабильности. Так, довосстановление образца Rh/TiO2 раствором NaBH4 прямо перед процедурой растворения носителя приводит к существенным изменениям в распределениях частиц по размерам согласно данным ДРС (рис. 3а и 3б), а размеры частиц мелкой фракции (〈dДРС〉) хорошо соответствуют величине 〈d6/5〉, определенной методом ПЭМ для исходного катализатора (рис. 3б и табл. 1).
Рис. 3.
a − Распределение (по интенсивности) частиц по размерам согласно данным ДРС для Rh-содержащего раствора, полученного после растворения исходного образца Rh/TiO2; б − распределение (по интенсивности) частиц по размерам согласно данным ДРС для Rh-содержащего раствора, полученного после растворения восстановленного NaBH4 образца Rh/TiO2.
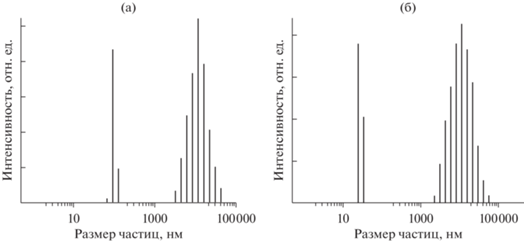
Таким образом, в некоторых случаях возможно существенное расхождение результатов, полученных при использовании ДРС, с данными других методов, обусловленное агрегацией частично окисленных наночастиц в растворе. Поэтому для предотвращения таких расхождений перед процедурой растворения образец необходимо довосстанавливать, например, раствором NaBH4.
На рис. 4 показаны распределения частиц металлов по размерам для остальных нанесенных катализаторов: сверху − согласно данным ПЭМ для исходных образцов (рис. 4а−4в), а снизу – по результатам ДРС для металлсодержащих растворов, полученных после растворения этих катализаторов (рис. 4г−4е). Оказалось, что из всех образцов в довосстановлении нуждался только Ni/SiO2, вероятно, вследствие поверхностного окисления частиц никеля. Интересно отметить, что в случае катализатора Au/C ожидаемо наблюдается расхождение между величинами 〈dДРС〉 и 〈d6/5〉 (рис. 4, табл. 1). Как было показано выше, это связано с тем, что по данным РФА в этом образце имеется небольшое количество крупных частиц, которые никак не представлены в распределении ПЭМ, возможно, в силу их низкого содержания в образце. Между тем, методом ДРС, так же как и РФА, фиксируется присутствие в образце именно крупных частиц золота в силу большей к ним чувствительности. Таким образом, наблюдается определенное согласие между данными РФА и ДРС (табл. 1). В случае же образцов Ni/SiO2 и Pd/g-C3N4 каких-то значимых особенностей нет, можно отметить только хорошее соответствие между величинами 〈d6/5〉 и 〈dДРС〉, найденными для исходных катализаторов и растворов, полученных при их растворении, соответственно.
Рис. 4.
Распределения частиц нанесенных металлов по размерам по данным ПЭМ для образцов Au/C (a), Ni/SiO2 (б) и Pd/g-C3N4 (в); распределения частиц по размерам по данным ДРС (распределения по интенсивности) для металлсодержащих золей, полученных при растворении Au/C (г), Ni/SiO2 (д) и Pd/g-C3N4 (е).
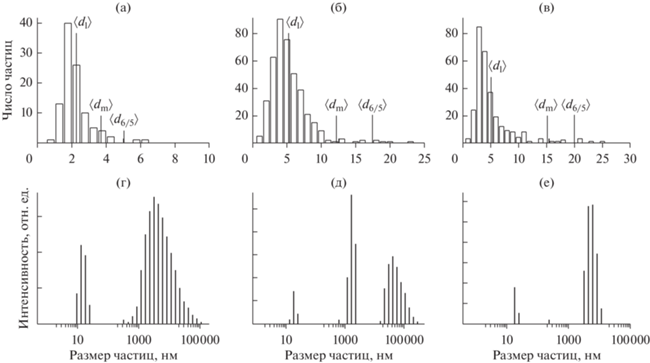
Наконец, последний пример − это применение методики STS для определения размеров частиц кремнезема в рисовой шелухе. Рисовая шелуха представляет собой природный биокомпозит, содержащий лигнин, целлюлозу и нанодисперсные частицы кремнезема. Размеры частиц кремнезема в рисовой шелухе были определены нами ранее методом малоуглового рентгеновского рассеяния (МУРР), причем как в исходной целлюлозной матрице, так и после ее растворения [19, 28]. Поэтому представляло интерес сопоставить полученные ранее данные с результатами ДРС (рис. 5). В окислительной среде при нагреве целлюлоза и лигнин разрушаются, и в растворе остаются только дисперсные частицы кремнезема. Рис. 5а позволяет сравнить размеры частиц кремнеземного золя, приготовленного путем растворения рисовой шелухи, найденные методами МУРР (рис. 5а) и ДРС (рис. 5б). Средний размер частиц кремнезема по данным ДРС составляет 33.2 ± 8.4 нм. Эта величина в общем довольно неплохо согласуется с размерами частиц крупной фракции (20−30 нм) в ранее полученном распределении по данным МУРР. С учетом того, что рисовая шелуха − это природный материал, в целом можно отметить хорошее согласие между разными методами исследования (рис. 5). Таким образом, метод ДРС и методику STS можно применять для определения размера наночастиц не только в нанесенных катализаторах, но и нанокомпозитах.
Рис. 5.
a − Объемное распределение частиц по размерам для кремнеземсодержащего золя из рисовой шелухи по данным МУРР согласно результатам нашей предыдущей работы [28]; б − распределение (по интенсивности) частиц по размерам для кремнеземсодержащего золя из рисовой шелухи по данным ДРС.
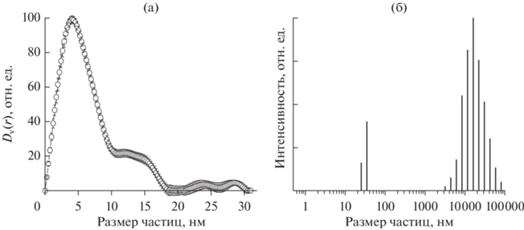
ЗАКЛЮЧЕНИЕ
Изучены возможности использования методики STS для анализа нанесенных катализаторов на основе труднорастворимых носителей и нанокомпозитов методом ДРС. Найдены относительно простые и универсальные условия, обеспечивающие растворение или разложение различных типов пористых носителей. Показано, что для эффективного анализа методом ДРС достаточно лишь частичного растворения или разрушения носителя. Обнаружено, что в ряде случаев может наблюдаться эффект вторичной агрегации наночастиц в растворе, который существенно искажает полученные результаты. Продемонстрировано, что предобработка катализаторов NaBH4 позволяет предотвратить этот негативный эффект, возникающий при растворении нанесенных катализаторов. На примере различных образцов показано хорошее соответствие между данными о размерах частиц для исходных катализаторов и нанокомпозитов, с одной стороны, и для приготовленных из этих образцов растворов − с другой.
Список литературы
Sun B., Wu F., Zhang Q., Chu X., Wang Z., Huang X., Li J., Yao C., Zhou N., Shen J. // J. Colloid Interface Sci. 2021. V. 584. P. 505.
Haruta M. // Catal. Today. 1997. V. 36. P. 153.
Shimura K., Fujitani T. // Mol. Catal. 2021. V. 509. P. 111623.
Antolini E. // Appl. Catal. B: Env. 2016. V. 181. P. 298.
Bergeret G., Gallezot P. / Handbook of Heterogeneous Catalysis. Wiley−Weinheim−Chichester: Wiley-VCH, 2008. P. 738.
Matyi R.J., Schwartz L.H., Butt J.B. // Catal. Rev. 1987. V. 29. P. 41.
Gogate M.R. // Appl. Catal. A: Gen. 2016. V. 514. P. 203.
Hughes R. Deactivation of Catalyst. New York: Academic Press, 1984.
Hansen T.W., Delariva A.T., Challa S.R., Datye A.K. // Acc. Chem. Res. 2013. V. 46(8). P. 1720.
Wimmer A., Urstoeger A., Hinke T., Aust M., Altmann P.J., Schuster M. // Anal. Chim. Acta. 2021. V. 1150. P. 238198.
Yakovlev I.V., Yakushkin S.S., Kazakova M.A., Trukhan S.N., Volkova Z.N., Gerashchenko A.P., Andreev A.S., Ishchenko A.V., Martyanov O.N., Lapina O.B., D’Espinose de Lacaillerie J.-B. // Phys. Chem. Chem. Phys. 2021. V. 23. P. 2723.
Geiss O., Cascio C., Gilliland D., Franchini F., Barrero-Moreno J. // J. Chromatogr. A. 2013. V. 1321 P. 100.
Bhattacharjee S. // J. Controlled Release. 2016. V. 235. P. 337.
Souza T.G.F., Ciminelli V.S.T., Mohallem N.D.S. // J. Phys. Conf. Ser. 2016. V. 733. 012039.
Larichev Yu.V. // Chem. Papers. 2021. V. 75(5). P. 2059.
Ларичев Ю.В. // Кинетика и катализ. 2021. Т. 62. № 4. С. 483.
Larichev Yu.V. // Nano-Struct. Nano-Objects. 2021. V. 25. P. 100647.
Yeletsky P.M., Yakovlev V.A., Mel’gunov M.S., Parmon V.N. // Micropor. Mesopor. Mater. 2009. V. 121. P. 34.
Larichev Yu.V., Yeletsky P.M., Yakovlev V.A. // J. Phys. Chem. Solids. 2015. V. 87. P. 58. http://www.sciencedirect.com/science/article/pii/ S0022369715300305 - cor1mailto:ylarichev@gmail.com.
Кузнецов П.Н., Перминов Н.В., Кузнецова Л.И., Бурюкин Ф.А., Колесникова С.М., Каменский Е.С., Павленко Н.И. // Химия твердого топлива. 2020. № 2. С. 3.
Soft Scientific, DynaLS - software for data analysis in Photon Correlation Spectroscopy, http://www.softscientific.com/science/WhitePapers/dynals1/dynals100.htm
Hassan P.A., Rana S., Verma G. // Langmuir. 2015. V. 31. P. 3.
Thomas J.C. // J. Colloid Interface Sci. 1987. V. 117. P. 187.
Pradhan S., Hedberg J., Blomberg E., Wold S., Wallinder I.O. // J. Nanopart. Res. 2016. V. 18. P. 285.
Tseng K.H., Lin Y.H., Tien D.C., Ku H.C., Stobinski L. // Micro Nano Lett. 2018. V. 13. № 11. P. 1545.
Pradhan S., Hedberg J., Rosenqvist J., Jonsson C.M., Wold S., Blomberg E., Wallinder I.O. // PLOS ONE. 2018. V. 13. № 2. P. e0192553.
Mateos H., Picca R.A., Mallardi A., Dell’Aglio M., De Giacomo A., Cioffi N., Palazzo G. // Appl. Sci. 2020. V. 10. P. 4169.
Ларичев Ю.В. // Кинетика и катализ 2021. Т. 62. № 6. С. 782.
Дополнительные материалы отсутствуют.
Инструменты
Кинетика и катализ