Кинетика и катализ, 2022, T. 63, № 6, стр. 695-723
Развитие механохимического метода синтеза слоистых двойных гидроксидов, перспективного для получения адсорбентов и катализаторов
О. Б. Бельская a, *, В. А. Лихолобов b, **
a Центр новых химических технологий ИК СО РАН
644040 Омск, ул. Нефтезаводская, 54, Россия
b ФГБУН ФИЦ Институт катализа им. Г.К. Борескова СО РАН
630090 Новосибирск, просп. Акад. Лаврентьева, 5, Россия
* E-mail: obelska@ihcp.ru
** E-mail: likholobov47@mail.ru
Поступила в редакцию 27.05.2022
После доработки 02.06.2022
Принята к публикации 02.06.2022
- EDN: EWKVIB
- DOI: 10.31857/S0453881122060016
Аннотация
Обобщены результаты исследований в области синтеза и изучения особенностей слоистых двойных гидроксидов (СДГ), полученных с использованием твердофазных реакций. На примере механохимического синтеза MgAl-СДГ проанализировано влияние условий проведения механической активации, состава исходных компонентов на структуру СДГ, формирование и свойства оксидов на их основе. Представлены данные о механохимическом синтезе СДГ, содержащих щелочной металл литий и переходные металлы Ni и Co, и об их каталитических свойствах в реакциях альдольной конденсации фурфурола с ацетоном и аквафазном гидрировании фурфурола.
ВВЕДЕНИЕ
Слоистые двойные гидроксиды (СДГ), аналоги природного минерала гидротальцита состава Mg6Al2(OH)16CO3 ⋅ 4H2O, в настоящее время имеют широкую сферу применения и интенсивно изучаются с точки зрения получения новых композиций и исследования их структуры и свойств [1–7]. СДГ представляют собой класс бруситоподобных11 (рис. 1а) слоистых неорганических материалов [8] и имеют общую формулу [M(II)1 – xM(III)x(OH)2][Am–]x/m ⋅ nH2O, где М – катионы металлов с валентностью (II), обычно Mg2+, и (III), обычно Al3+, А – межслоевой анион с валентностью m; х – молярное отношение М3+/(М2+ + М3+); n – количество молекул воды. СДГ формируются посредством периодического чередования положительно заряженных октаэдрических слоев (М2+, М3+)(ОН)6 и отрицательно заряженных межслоевых галерей, состоящих из компенсирующих заряд анионов А и молекул воды [9] (рис. 1б).
Благодаря развитию синтетических методов удалось заменить катионы Mg2+ рядом двухвалентных катионов (Co2+, Ni2+, Cu2+, Zn2+, Cd2+, Ca2+), а катионы Al3+ – трех- и даже четырехвалентными катионами с близкими ионными радиусами, например, In3+, Ga3+, Au3+, Cr3+, V3+, Ce3+, Sn4+, Zr4+ [10, 11]. Именно структура и состав данного типа материалов определяют основные направления их использования. Поскольку СДГ обладают ионообменными свойствами, их применяют для адсорбционной очистки воды от анионов (галогенидов и оксигалогенидов, фосфатов, сульфатов, хроматов, арсенатов, молибдатов, полисульфидов, гуматов и др.) и радионуклидов [12–15]; в медицине данный тип материалов эффективен для доставки лекарственных препаратов с их контролируемым высвобождением [16–18]. Ряд обзорных работ посвящен использованию СДГ в электро- и фотокатализе [19–21]. Преимущества СДГ при применении в области гетерогенного катализа также обусловлены особенностями строения этого материала. Благодаря возможности сочетания различных катионов в бруситоподобных слоях и способности к анионному обмену можно получать СДГ различного химического состава и широко варьировать их свойства: i) высокая адсорбционная емкость СДГ и формируемых из них смешанных оксидов металлов делают их эффективными носителями для иммобилизации каталитически активных веществ; ii) регулируемая основность поверхности позволяет использовать СДГ и смешанные оксиды на их основе в качестве твердофазных катализаторов основного типа; iii) равномерное распределение разнозарядных катионов в слоях, а также интеркалирование анионов различного состава в межслоевое пространство, дают возможность использовать СДГ в качестве предшественников при синтезе высокодисперсных и стабильных нанесенных катализаторов [22, 23]. Перечисленные особенности СДГ не только приводят к расширению сферы их применения, но и инициируют работы по оптимизации и развитию методов их синтеза.
Для приготовления СДГ были разработаны два основных подхода: жидкофазный (в водных средах) синтез, который в настоящее время является основным (например, соосаждение, гидротермальный синтез др.), и твердофазный (механохимический) синтез [24, 25]. Традиционный метод получения СДГ – соосаждение, включающее медленное добавление растворенных солей катионов металлов к раствору, содержащему вводимый анион, при постоянных pH и температуре с последующим длительным старением, промывкой и фильтрацией образовавшегося осадка. Несмотря на простоту и хорошую воспроизводимость, недостатком данного метода является многостадийность, потребление значительных количеств воды и растворимых солей металлов, образование большого объема щелочных промывных вод. Эти же недостатки отмечаются при реализации других жидкофазных синтезов: метода индуцированного гидролиза, когда происходит реакция между оксидом двухвалентного металла и раствором соли трехвалентного металла, золь-гель метода с использованием алкоксидов и/или ацетилацетонатов металлов, гидротермального метода гомогенного осаждения при термическом гидролизе мочевины в присутствии солей катионов двух- и трехвалентных металлов, при топохимическом синтезе, когда часть катионов бруситоподобного гидроксида окисляется до трехвалентного состояния. В рамках жидкофазных методов также осуществляют синтезы СДГ, связанные с модифицированием предварительно полученного слоистого предшественника посредством анионных обменов или в процессе регидратации прокаленных форм [10, 11]. В целом, результаты исследований в области жидкофазного метода синтеза СДГ и изучению их свойств достаточно подробно обсуждены в недавних обзорах [1–7, 26].
Перспективный и развивающийся метод приготовления СДГ – механохимический, в процессе которого происходит твердофазная реакция между исходными реагентами при механическом на них воздействии [27]. Механохимический подход позволяет значительно ускорить синтез СДГ и снизить количество щелочных промывных вод. Одними из первых публикаций о механохимическом синтезе СДГ были работы [28–31], в которых описан процесс получения MgAl-СДГ без растворителя с использованием “сухого и влажного помола”. Позже данным методом были приготовлены СДГ другого состава, содержащие катионы лития, цинка, кальция, олова, алюминия и др. [32–34]. Также была показана возможность введения в межслоевое пространство СДГ в процессе его механохимического синтеза некоторых неорганических (например, тетраборат лития [35]) и органических (например, аминокислоты, нестероидные противовоспалительные препараты [34, 36, 37]) соединений.
Хотя общее количество публикаций, связанных с механохимическим синтезом СДГ, относительно невелико, внимание к этой перспективной области исследований заметно возросло в течение последних лет (рис. 2). Недавно опубликованы и обзорные работы [24, 38], в которых детально описаны подходы, которые используются при его проведении. Основной объем информации связан с получением MgAl-композиций, однако также приведены данные о механохимическом синтезе СДГ другого состава: LiAl, NiAl, ZnAl, CuAl, CaAl, MgFe, CaFe, CaSn. Cделан акцент на анализ работ, связанных с исследованием процессов интеркалирования различного типа анионов на отдельных стадиях механохимического синтеза, а в качестве основного направления применения СДГ, полученных данным методом, рассмотрены процессы адсорбции анионов, в том числе с целью очистки воды. Кроме того, была реализована адсорбция, сопряженная с фотохимическим разложением органических загрязнителей (на примере метилового оранжевого и метиленового синего), при использовании СДГ, содержащих катионы цинка, кадмия, серебра.
Рис. 2.
Количество опубликованных статей (в год), связанных с механохимическим синтезом слоистых двойных гидроксидов согласно базе данных Web of Science.

Авторам настоящего обзора показалось важным проанализировать новые работы, описать интересные методические решения, а также тенденции, формирующиеся в последнее время не только в области синтеза и изучения особенностей СДГ, полученных с помощью твердофазных реакций, но и в области поиска их возможных приложений. В представленном обзоре также приведены результаты исследований, связанных с механохимическим синтезом СДГ различного состава, которые были выполнены в ЦНХТ ИК СО РАН (ранее ИППУ СО РАН) в течение последних лет. Рассмотрены различные подходы к приготовлению СДГ, включающие стадии механического воздействия, а на примере механохимического синтеза MgAl-СДГ (как наиболее известной и востребованной системы) проанализировано влияние условий проведения механической активации, природы исходных компонентов и соотношения между двух- и трехвалентными металлами на структуру СДГ, формирование и свойства оксидов на их основе. Также представлены данные о механохимическом синтезе СДГ, содержащих щелочной металл литий и переходные металлы Ni и Co, и исследовании их каталитических свойств.
МЕТОДИЧЕСКИЕ ОСНОВЫ МЕХАНОХИМИЧЕСКОГО СИНТЕЗА
При твердофазном механохимическом синтезе химические взаимодействия между реагирующими твердыми фазами инициируются механическим на них воздействием, в результате которого наблюдается аморфизация и разупорядочение кристаллической структуры (пластическая деформация типа сжатия и сдвига, продуцирующая поверхностные дислокации) частиц реагентов [39], что повышает их свободную энергию и способствует образованию из них нового, термодинамически более устойчивого соединения (рис. 3a).
Рис. 3.
Методические основы твердофазного механохимического синтеза СДГ: принципиальные этапы инициирования химического взаимодействия между твердыми фазами в шаровой мельнице при одностадийном синтезе (a); двухстадийный механохимический синтез (вариант I) (б); двухстадийный механохимический синтез (вариант II) [24], адаптировано из <[24] doi.org/10.3390/nano9010080 <Distributed under a Creative Commons Attribution 4.0 License (в). an – ускорение соударения шаров, м с–2; T – температура синтеза; t – продолжительность воздействия.
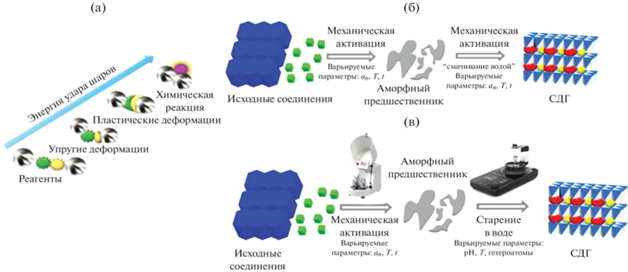
Если первоначально механическое воздействие на исходные реагенты осуществлялось в ступках и было длительным и неэффективным, то в настоящее время для этой цели разработаны специальные устройства, мельницы, в которых функцию мелющих тел выполняют шары определенного диаметра, изготовленные из различных материалов (агат, нитрид кремния, диоксид циркония, хромистая сталь и др.) [40–43]. Наиболее эффективными и удобными в лабораторных исследованиях являются планетарные мельницы, в которых барабаны (размольные стаканы) с мелющими телами (шарами) вращаются вокруг центральной оси и одновременно вокруг собственных осей в противоположном направлении (рис. 4). В этом случае на содержимое размольного стакана, состоящее из измельчаемой массы и мелющих шаров, действует как центробежная сила вращения стаканов вокруг их собственной оси, так и центробежная сила вращающегося опорного (планетарного) диска. Так как направления собственных вращений размольных стаканов и опорного диска противоположны друг к другу, центробежные силы действуют то в одинаковом, то в противоположном направлениях. При этом происходит процесс перекатывания мелющих шаров по внутренней кромке стакана (измельчение осуществляется трением) и затем отрыв и свободное движение шаров и измельчаемого материала через размольный стакан с последующим ударом о противоположную внутреннюю стенку (ударное воздействие). Таким образом, на шары в мельнице действует не только сила тяжести, но и во много раз превосходящая ее центробежная сила, что позволяет интенсифицировать удар шаров о материал. В связи с этим в целом интенсивность энергетического воздействия на частицы твердого вещества в таких мельницах характеризуют величиной ускорения падения (соударения шаров), имеющей размерность м с–2 и обозначаемой далее аn [45].
Основная задача механической активации – “закачивание” в твердое тело энергии путем создания в нем тех дефектов, которые приведут в дальнейшем к химической реакции [44–46]. Часто результатом механической обработки является пластическая деформация материала и связанное с ней образование линейных дефектов – дислокаций, ионных и атомных вакансий, межузельных ионов. Последующая релаксация поля напряжения может сопровождаться процессами выделения тепла, образования новой поверхности, аморфизации твердого вещества и химическими превращениями. Особенность механохимического синтеза заключается в достижении высоких значений коэффициентов диффузии атомов (ионов) компонентов в твердой фазе. В отличие от обычной диффузии, определяемой градиентами концентраций компонентов, этот вид диффузии получил специальное название “деформационного атомного перемешивания”. Следует отметить, что значительное возрастание скорости твердофазного синтеза при механической активации связано не только с образованием дефектов, но и с процессом “подгонки” распределения дефектных частиц по размерам, влияющим на число и площадь межчастичных контактов, в основном и определяющих скорость твердофазной реакции. Таким образом, особенностью механической активации является импульсный (чередование процессов возникновения поля напряжения и его релаксации) и локальный (поле напряжений возникает не во всем объеме твердой частицы, а только на ее контакте с другой частицей или рабочим телом) характер механического воздействия на вещество [44–46].
ОСОБЕННОСТИ МЕХАНОХИМИЧЕСКОГО СИНТЕЗА СДГ
Анализ публикаций, связанных с механохимическим синтезом СДГ [24–43, 47–51], показал, что синтез можно проводить в одну или две стадии. В работе [30] детально описано одностадийное получение MgAl-СДГ (Mg/Al = 2) с использованием в качестве исходных соединений гидроксида магния и кристаллогидратов солей алюминия AlCl3 ⋅ ⋅ 6H2O, Al(NO3)3 ⋅ 9H2O, Al2(SO4)3 ⋅ 18H2O. Одностадийный процесс наиболее простой в реализации, однако к его недостаткам относится низкая кристалличность образующегося СДГ (обусловленная формированием мелких рентгеноаморфных частиц и/или микродеформациями кристаллической решетки). Увеличение времени механической активации или введение дополнительной стадии длительной выдержки механоактивированного образца при повышенной температуре только частично решают эту проблему [47–49]. Из-за наличия у одностадийного процесса этого недостатка предпочтение при механохимическом синтезе СДГ отдается двухстадийному, который, в зависимости от условий проведения второй стадии, может выполняться в двух вариантах: I – “сухой + влажный помолы”; II – “сухой помол + + выдержка в воде” (рис. 3б и 3в).
Двухстадийный процесс в варианте I использовали в [28] для синтеза MgAl-СДГ, в ходе которого Mg(OH)2 и Al(OH)3 сначала были активированы в режиме “сухого помола” в течение 1 ч, а затем к полученному аморфному веществу добавляли определенное количество воды и выполняли дополнительно “влажный помол” в течение 2 ч для завершения кристаллизации СДГ. Ускорить кристаллизацию СДГ также возможно, если на втором этапе заменить воду солью, содержащей кристаллизационную воду, например, такой как Mg(NO3)2 ⋅ 6H2O [29]. В работе [50] при синтезе CaAlFe-СДГ на первой стадии проводили механическую активацию смеси Ca(OH)2 и Al(OH)3 в течение часа, а затем добавляли Fe(NO)3 ⋅ 9H2O с определенным количеством воды и осуществляли “влажный помол” еще в течение 2 ч. В [32], используя вариант I, синтезировали LiAl-СДГ, в котором LiOH и Al(OH)3 сначала были размолоты в сухом состоянии, а затем во влажном с необходимым количеством воды. В результате был получен LiAl-OH без примесей фаз исходных компонентов. В [51] выполнили аналогичный двухстадийный механохимический синтез MgAl-СДГ с интеркалированным ацетат-ионом. Для этого брусит (Mg(OH)2) и гиббсит (Al(OH)3) сначала подвергали сухой механической активации, а затем к смеси добавляли тетрагидрат ацетата магния для последующего “влажного помола”. C использованием данного подхода удалось получить содержащий четырехвалентный катион Ca(II)Sn(IV)-СДГ, синтез которого невозможен соосаждением или одностадийным механохимическим методом [34]; для этого прекурсоры CaCl2 и SnCl4 ⋅ 6H2O мехактивировали, а затем приливали заданное количество воды и проводили “влажный помол”. Считается, что при такой методике на первой стадии формируется предшественник в аморфном дефектном состоянии, который способен далее на второй стадии мокрого помола трансформироваться (за счет процессов переноса в жидкой фазе анионов и катионов, релаксации дислокаций и “залечивания” дефектов) в кристаллическую фазу СДГ. Однозначно было доказано, что для получения СДГ предварительная стадия “сухого помола” предшественников абсолютно необходима [29], так как добавление воды изначально к смеси Mg(OH)2 и Al(OH)3 на первой стадии помола (одностадийный “мокрый помол”) приводило к сильной адгезии продуктов (образец прочно приклеивался ко дну емкости и поверхности шаров) и неполному протеканию реакции с содержанием в образцах значительного количества непрореагировавших компонентов.
В другой разновидности двухстадийного механохимического синтеза вторая механохимическая стадия “мокрого помола” заменяется непосредственным контактом аморфного продукта механической активации с водой при перемешивании (вариант II). Данный подход “сухой помол + + перемешивание в воде” более технологичен и рассматривается как альтернативный традиционному методу соосаждения для синтеза различных СДГ, но без использования растворов. Например, в [33] для получения высококристалличного ZnAl-СДГ гидрат гидроксида карбоната цинка (Zn4CO3(OH)6 ⋅ H2O) сначала подвергали сухой механической активации с Al(OH)3 для приготовления рентгеноаморфного предшественника, последующий контакт которого с водой привел к образованию целевого СДГ. Отметим, что в этом процессе сырьем служили карбонат цинка и гидроксид алюминия, более дешевые и стабильные, чем растворимые соли, используемые в традиционных методах соосаждения. Ту же процедуру выполняли для синтеза CuAl-СДГ с применением основного карбоната меди и Al(OH)3 в качестве сырья [36]. Следует отметить, что для увеличения эффективности второй стадии возможно использование ультразвуковой обработки суспензии аморфного предшественника СДГ в воде, и с помощью такого подхода были синтезированы CaFe-, CaAl- и ZnAl-СДГ, интеркалированные различными неорганическими анионами, например, галогенидами, азидами и оксоанионами (${\text{CO}}_{3}^{{2 - }},$ ${\text{NO}}_{3}^{ - },$ ${\text{ClO}}_{4}^{ - }$) [52–55].
Следует выделить ряд работ, в которых механической активации на первой стадии подвергали лишь один компонент реакционной смеси – тригидроксид алюминия, который на второй стадии выдерживали в водных растворах солей двухвалентных металлов. Было показано [56], что при высокоэнергетическом воздействии происходило не только изменение размера частиц Al(OH)3, но и перестройка пористого пространства в результате разрушения мелких пор. По мере увеличения интенсивности воздействия наблюдалась аморфизация гиббсита, ослабление связей Al–OH (согласно данным ИК-спектроскопии), что приводило к росту его реакционной способности (снижению температуры дегидроксилирования, облегчению растворения). При получении фазово однородных NiAl-СДГ время механической активации Al(OH)3 составляло 4 ч, а время выдержки трансформировавшегося Al(OH)3 в растворах солей никеля – 3 сут. Такого же принципа подход (с варьированием времени мехактивации, продолжительности и температуры пропитки) был использован для синтеза фазово однородных CoAl-, CuAl-, ZnAl- и MgAl-СДГ [57].
Подводя промежуточный итог этого рассмотрения, можно заключить, что определяющее значение для эффективного получения СДГ механохимическим методом имеет первая стадия – “сухой помол” исходных соединений, тогда как способ выполнения второго этапа может варьироваться – это может быть или “мокрый помол”, или перемешивание, или ультразвуковая обработка в воде.
МЕХАНОХИМИЧЕСКИЙ СИНТЕЗ MgAl-СДГ. ВЛИЯНИЕ СПОСОБА И УСЛОВИЙ ПРОВЕДЕНИЯ МЕХАНОХИМИЧЕСКОЙ АКТИВАЦИИ НА СТРУКТУРУ MgAl-СДГ, ФОРМИРОВАНИЕ И СВОЙСТВА ОКСИДОВ НА ИХ ОСНОВЕ
В качестве исходных соединений при механохимическом синтезе MgAl-СДГ, как правило, применяют смеси, состоящие из Mg(OH)2, Al(OH)3, Na2CO3, NaOH, AlCl3, Al(NO3)3, Al2(SO4)3, MgCl2, Mg(NO3)2 в различных сочетаниях [28–30, 48, 49]. Считается, что при механическом воздействии на соли металлов (в присутствии Mg(OH)2, NaOH, Na2CO3) образуются соответствующие гидроксиды, которые служат прекурсорами при дальнейшем формировании СДГ [58]. Так, AlCl3 в смеси с Mg(OH)2 и NaOH использовали для синтеза СДГ состава Mg0.8Al0.2(OH)2Cl0.2 одностадийным методом, для чего исходные компоненты подвергали механическому воздействию в высокоэнергетической шаровой мельнице (8000M Mixer/Mill, “SPEX”, США, стальные шары) при варьировании времени t от 1 до 20 ч [49]. Было показано, что целевой СДГ как однофазный продукт с высокой степенью кристалличности может быть получен, если длительность механохимической стадии превышает 5 ч. В работе [59] при синтезе MgAl-CO3 двухстадийным методом в варианте II применяли Mg(OH)2 и Al(OH)3, а в качестве источника карбонат-иона – углекислый газ. После обработки в планетарной шаровой мельнице с керамическими шарами в течение 5 ч продукт механической активации гидроксидов переносили в трехгорлую колбу, добавляли воду и через образовавшуюся суспензию с рН 11 пропускали СО2. Последующая стадия старения проходила при 95°С в течение 30 ч. Исследование фазового состава смеси непосредственно после стадии мехактивации показало присутствие интенсивных дифракционных пиков, характерных для Mg(OH)2 и Al(OH)3, и низкоинтенсивного широкого дифракционного пика при 2θ = 11.66°, соответствующего кристаллическим плоскостям d003 MgAl-CO3. Таким образом, на данной стадии компоненты смеси практически не реагируют, и образуется лишь небольшое количество аморфной фазы СДГ, но после взаимодействия их в водной фазе с СО2 и проведения стадии старения идентифицируется единственная и хорошо окристаллизованная фаза MgAl-СДГ.
В [60] при получении MgAl-СДГ из смеси Mg(OH)2, Al(OH)3 и NaHCO3 двухстадийным методом в варианте II была исследована роль отдельных компонентов в механохимическим синтезе. Для этого на первой стадии механическому воздействию (планетарная мельница АГО-II (“Новиц”, Россия), стальные мелющие тела, an = = 200 м с–2, 5 мин) подвергали не только все компоненты одновременно, но и отдельно смеси Mg(OH)2 с NaHCO3 и Al(OH)3 с NaHCO3 с последующим добавлением немехактивированного третьего компонента – Al(OH)3 или Mg(OH)2 соответственно (при сохранении молярного соотношения Mg : Al : HCO3 = 2 : 1 : 0.5), а вторую стадию осуществляли в одинаковых условиях – перемешивали мехактивированную смесь в дистиллированной воде при 90°С в течение 12 ч. Исследование продуктов таким образом проведенных синтезов методом РФА показало, что MgAl-СДГ был единственным продуктом при мехактивации тройной смеси и основным продуктом при мехактивации двойной смеси Mg(OH)2 с NaHCO3 с последующим добавлением Al(OH)3. Однако если мехактивации подвергали смесь Al(OH)3 с NaHCO3 с последующим добавлением Mg(OH)2, то образование MgAl-СДГ практически не происходило, и основной кристаллической фазой в конечном продукте являлся непрореагировавший Mg(OH)2. Эти данные позволили авторам сделать вывод о том, что при синтезе СДГ по варианту II критически необходимой является стадия механохимической аморфизации кристаллитов гидроксида магния с образованием частиц, имеющих структурные дефекты – разупорядоченные бруситовые слои. При дальнейшем (на второй стадии) контакте таких частиц с горячей водой, содержащей катионы Al3+, инициируются процессы переноса, при котором катионы Al3+, замещая катионы Mg2+, переходят в октаэдрические позиции бруситовых слоев, а формирующийся при этом положительный заряд слоев компенсируется анионами ${\text{CO}}_{3}^{{2 - }},$ занимающими межслоевое пространство [60].
Анализ исследований, связанных с двухстадийным механохимическим синтезом СДГ в вариантах I и II показал, что при реализации стадии механической активации (“сухой помол”) возникают неопределенности, обусловленные условиями ее проведения. Проблема заключается в том, что эффективность механохимического воздействия (а в дальнейшем и возможность получения из аморфизированного прекурсора целевой фазы СДГ) во многом определяется характеристиками использующегося оборудования.
Подавляющая часть исследований по механохимии выполнена с применением планетарных мельниц с вертикальной осью вращения, среди которых можно назвать АГО-2, различные модификации мельниц фирмы “Fritsch”, “Retsch” и др. Планетарные мельницы характеризуются двумя главными параметрами: частотами вращения барабанов вокруг своих осей и диска [44]. При выборе условий активации варьируют как частоты вращения и время воздействия, так и соотношение между массой загруженного вещества и массой шаров. Поэтому сопоставление результатов, полученных с использованием различных мельниц – предельно сложная задача из-за множества характеризующих их параметров, а также отсутствия признанных тестовых систем.
Именно различие в устройстве и технических параметрах оборудования для механохимического синтеза привело к тому, что основное количество опубликованных работ связано с выяснением условий синтеза для получения однофазных СДГ определенного состава при применении определенного оборудования [28–30, 48, 49]. Чаще всего в таких работах варьируются не только состав исходных компонентов, взятых для синтеза, но и время механической активации (t), материал и ускорение мелющих тел (an), соотношение масс шаров и реагентов. В [61, 62] MgAl-СДГ получали из коммерческого MgO и Al(OH)3 (Mg : Al = = 2 : 1). Метод синтеза включал стадию мокрого помола (LME 1, “Netzsch”, Германия), обеспечивающую смачивание, деагломерацию, диспергирование твердых частиц в жидкой среде, а также стадию старения при 80°С в течение 24 ч. Было показано, что выбранные условия проведения первой стадии (30°С, 2000 об./мин, 1 ч) не обеспечили полноты превращения реагентов. Поэтому на следующем этапе исследований [63] был сделан акцент на оптимизацию первой стадии для выяснения влияния параметров мехактивации на состав продуктов и определения возможности одностадийного получения СДГ. В мельницу добавляли сухие порошки оксида магния и гидроксида алюминия, смешанные со стехиометрическим количеством воды, и проводили процесс мехактивации с варьированием его условий. Варьировали скорость вращения, t, массу реакционной смеси, температуру обогрева мельницы. Согласно данным РФА, интенсивность линий, характеризующих фазу гидроксида алюминия, заметно уменьшались вследствие его аморфизации при увеличении скорости вращения и времени мехактивации даже при низкой температуре обработки. В то же время реакция гидратации MgO протекала с трудом, и на всех дифрактограммах присутствовали пики MgO, а не ожидаемого Mg(OH)2. Было установлено, что синтез СДГ из данных компонентов возможен только при повышенной температуре синтеза (50°C) и длительном времени воздействия (3 ч), способствующими гидратации MgO.
В исследованиях авторов [64] была детально изучена роль условий проведения первой стадии в двухстадийной схеме “сухой помол + перемешивание в воде” при использовании планетарной мельницы АГО-2С (“Новиц”, Россия). Для получения алюмомагниевого СДГ с карбонатными межслоевыми анионами и мольным соотношением Mg/Al = 3 были заданы значения параметра an = 500 и 1000 м с–2, а t воздействия на смесь реагентов Mg(OH)2, Al(OH)3 и Na2CO3 варьировали в диапазоне 5–90 мин. На втором этапе осуществляли интенсивное перемешивание смеси механоактивированных компонентов в дистиллированной воде при 65°C в течение 2 ч. При любых сочетаниях указанных параметров после первой стадии (механической активации смеси) появления фазы СДГ обнаружено не было (рис. 5а). Однако после контакта продукта механической активации с водой однофазный MgAl-СО3 образовывался лишь в том случае, если первая стадия была проведена в определенных условиях: так, при an = 500 м с–2 формирование однофазного продукта, согласно данным РФА, происходило лишь при времени механохимической активации, превышающем 60 мин. При обработке исходных компонентов при максимально возможном для данного оборудования an = 1000 м с–2 присутствие фазы СДГ (после второй стадии) наблюдалось уже после 5 мин воздействия (рис. 5б), однако t, необходимое для образования единственной кристаллической фазы MgAl-СДГ, составило 30 мин (рис. 5б).
Рис. 5.
Дифрактограммы образцов: после первой стадии механохимического синтеза (мехактивация смеси Al(OH)3, Mg(OH)2 и Na2CO3 при an = 1000 м с–2) (a); после второй стадии перемешивания в воде [64], адаптировано из <[64] doi.org/10.1016/j.jallcom.2021.161902>. <By courtesy of Elsevier> (б).
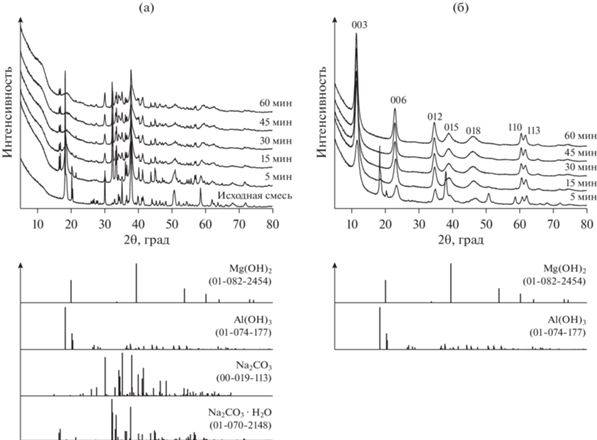
Исследование данных образцов методом СЭМ показало, что время активации влияет на морфологию образующихся продуктов как после первой, так и после второй стадий синтеза СДГ. Так, смесь после механической обработки 5 мин при 1000 м с–2 (MgAl-5/1000) представляла собой преимущественно однородные округлые частицы со средним размером 0.25 мкм (рис. 6а). Контакт этого образца с водой (MgAl-5/1000-H2O) привел к появлению небольших пластин СДГ, расположенных под углом друг к другу (рис. 6б). После увеличения t до 60 мин поверхность образца становилась гладкой (MgAl-60/1000), и далее (MgAl-60/1000-H2O) происходило формирование более крупных пластин СДГ, расположенных параллельно друг другу (рис. 6в, 6г) [64]. Согласно данным РФА, увеличение t первой стадии синтеза способствовало росту размера кристаллитов в готовом MgAl-СДГ (например, Lc возрастала от 7 до 10 нм при изменении t от 5 до 45 мин при an = 1000 м с–2) и повышению термостабильности материала. Так, положение высокотемпературных пиков на дифференциальных профилях термического анализа, соответствующих удалению межслоевой воды, межслоевых анионов и дегидроксилированию слоев [10], смещалось в сторону более высоких температур (примерно на 10°С при увеличении времени первой стадии с 30 до 60 мин) [64]. В то же время следует отметить, что в любых условиях механохимического синтеза СДГ температуры их разложения ниже, чем наблюдаемые для образцов, полученных соосаждением при том же соотношении Mg/Al [65], вследствие более дефектной структуры СДГ, образующихся в условиях механохимического синтеза.
Рис. 6.
СЭМ-изображения образцов: MgAl-5/1000 (а); MgAl-5/1000-H2O (б); MgAl-60/1000 (в); MgAl-60/1000-H2O (г) [64], адаптировано из <[64] doi.org/10.1016/j.jallcom.2021.161902>. <By courtesy of Elsevier>.
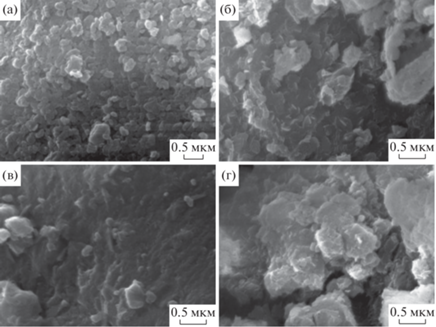
В работе [60] с применением двухстадийного синтеза MgAl-СДГ было показано, что при выборе в качестве исходных компонентов Mg(OH)2, Al(OH)3 и NaHCO3 и проведении первой стадии с использованием планетарной мельницы АГО-2 (стальные мелющие тела, an = 200 м с–2) варьирование t в диапазоне 5–20 мин слабо повлияло на морфологию и структурные параметры конечного СДГ. В то же время была продемонстрирована важность условий проведения второй стадии – выдержки в дистиллированной воде – для формирования структуры MgAl-СДГ. Если изменение температуры в интервале 30–90°С, при которой исследовали процесс “старения”, слабо влияло на структурные параметры СДГ, то время выдержки оказалось более значимым фактором – увеличение времени “старения” мехактивированной смеси от 1 до 12 ч позволило зарегистрировать интенсивные и узкие дифракционные пики конечного продукта.
Важным параметром при проведении механохимического синтеза является материал мелющих тел, определяющий как условия синтеза, так и состав вероятных примесей [66]. Чаще всего для механохимического синтеза СДГ применяют стальные мелющие тела из-за их высокой прочности и возможности использования больших ускорений для увеличения интенсивности воздействия. Однако в этом случае железо является ожидаемой примесью в полученном продукте. В то же время в отдельных работах стальные мелющие тела целенаправленно служили источником одного из компонентов при механохимическом синтезе. Таким образом были получены NiFe- и СоFe-СДГ с хлорид-ионами в межслоевых пространствах [67, 68]. Растворы хлоридов никеля или кобальта подвергали механической активации в шаровой мельнице со стальными шарами в течение 3–6 ч. При этом происходило внедрение ионов Ni2+ или Co2+ в формирующийся оксид железа, а вода являлась источником гидроксид-ионов. Метод не требовал повышенной температуры и регулирования рН, а полученный продукт характеризовался высокой чистотой и кристалличностью и по своим структурным характеристикам был практически идентичен СДГ Ni(Со)Fe–Cl, синтезированным традиционными методами.
Применение керамических мелющих тел (совместно с барабанами, внутренние стенки которых также покрыты керамикой) при проведении механохимической активации позволяет избежать появления примесей соединений железа в образующихся продуктах. Однако керамические материалы не дают возможности осуществлять длительную механическую активацию при высоких ускорениях, поскольку керамические шары достаточно хрупкие и разрушаются. С использованием керамических шаров в [69] было исследовано влияние природы исходных компонентов на фазовый состав образующегося в результате механохимического синтеза продукта. Для этого были выбраны смеси, состоящие из гидроксидов магния и алюминия и карбоната натрия. Во всех экспериментах мольное отношение Mg/Al было постоянным и равным 3. На первом этапе все образцы подвергали механической активации (300 м с–2, 30 мин), а на втором – “старению” в горячей воде. Выбор параметров механической активации определялся условиями, позволяющими проводить синтез без изменения свойств мелющих тел (рис. 7а). Варьирование Al(OH)3/Na2CO3 (2 и 0.5), соотношения между массой шаров и массой навески (mш/mн =20, 40 и 80) позволило получить целевой MgAl-СДГ, однако его максимальное содержание не превысило 70%, и на дифрактограммах всех синтезированных образцов присутствовали дифракционные максимумы фаз исходных компонентов. Наиболее интенсивные рефлексы фазы СДГ наблюдались для образца, приготовленного при соотношении mш/mн = 40 и при Al(OH)3/Na2CO3 = 0.5. Таким образом, применение керамических мелющих тел при механохимической активации дает возможность синтезировать MgAl-СДГ в достаточно мягких условиях (300 м с–2, 30 мин) без загрязнения продукта соединениями железа. Однако помимо основной фазы СДГ во всех изученных образцах присутствовали побочные фазы, относящиеся к непрореагировавшим исходным соединениям, количество которых определялось условиями синтеза (рис. 7а).
Рис. 7.
Дифрактограммы образцов, полученных механохимическим методом. а – Керамические мелющие тела: 1 – исходная смесь Al(OH)3 и Mg(OH)2; 2 – исходная смесь Al(OH)3, Mg(OH)2 и Na2CO3, Al(OH)3/Na2CO3 = 2; 3 – последовательная мехактивация (Al(OH)3 и Mg(OH)2, затем вместе с Na2CO3), Al(OH)3/Na2CO3 = 2; 4 – исходная смесь Al(OH)3, Mg(OH)2 и Na2CO3, Al(OH)3/Na2CO3 = 0.5; 5, 6 – дифрактограммы исходных смесей Al(OH)3, Mg(OH)2, Na2CO3 и Al(OH)3, Mg(OH)2 соответственно; условия мехактивации an = 300 м с–2, t = 30 мин. б – Стальные мелющие тела: 1 – исходная смесь Al(OH)3, Mg(OH)2, Na2CO3, Al(OH)3/Na2CO3 = 0.5; 2 – 400 м с–2, 15 мин, без стадии старения; 3 – 400 м с–2, 15 мин; 4 – 1000 м с–2, 15 мин; 5 – 1000 м с–2, 30 мин [69], адаптировано из <[69] doi.org/10.1134/S0023158418040134>. <By courtesy of Springer Nature >.
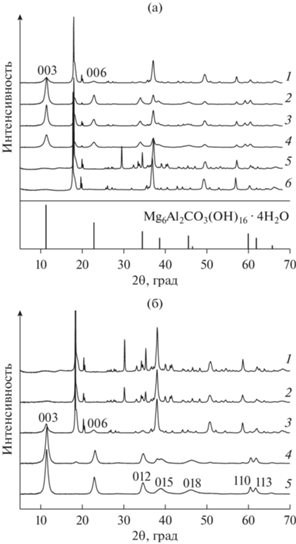
Для получения MgAl-СДГ с использованием стальных мелющих тел механическую активацию проводили в более жестких условиях с тем же составом исходных компонентов (смесь гидроксидов магния и алюминия и карбоната натрия с мольным соотношением Mg/Al = 3 и Al(OH)3/Na2CO3 = 0.5) [69]. Как и в предыдущих исследованиях, синтез СДГ осуществляли в две стадии: на первой стадии выполняли механохимическую активацию (варьируя an и t), а на второй полученный образец подвергали “старению” в течение 2 ч в дистиллированной воде при температуре 65°С при интенсивном перемешивании. Первоначально для механической активации с применением стальных шаров были выбраны относительно мягкие условия: ускорение – 400 м с–2, время активации – 15 мин. Согласно данным РФА (рис. 7б, дифрактограмма 3) в данных условиях реакция прошла неполностью, и наряду с фазой MgAl-СДГ на дифрактограмме присутствовали отчетливые рефлексы, относящиеся к исходным соединениям: гидроксидам магния и алюминия. Использование более жестких условий (an до 1000 м с–2, 15 мин) способствовало значительному возрастанию глубины превращения, и сигналы, характеризующие фазы исходных компонентов, имели низкую интенсивность. Увеличение времени механического воздействия (an = 1000 м с–2, 30 мин) позволило синтезировать однофазный образец MgAl-СДГ [69] (рис. 7б, дифрактограммы 4 и 5).
В рамках механохимического синтеза можно легко варьировать соотношение Mg/Al в составе СДГ, изменяя состав смести реагентов. При этом, согласно данным РФА, значения параметров решетки близки для СДГ, полученных механохимическим методом и методом соосаждения при условии одинакового катионного и анионного состава. Тенденции изменения структурных параметров при варьировании соотношения катионов также сохраняются: с увеличением соотношения Mg/Al возрастают значения параметра решетки с (вследствие уменьшения положительного заряда слоев и силы взаимодействия между слоями и межслоевыми анионами) и параметра решетки а (вследствие повышения доли катионов магния, обладающих бóльшим ионным радиусом по сравнению с катионами алюминия) [70].
Однако морфология поверхности образцов, согласно данным СЭМ, зависит не только от соотношения Mg/Al, но и от метода синтеза. Для MgAl-СДГ с соотношением Mg/Al = 2, полученного механохимическим методом, характерна пластинчатая структура, наблюдается скопление мелких слипшихся частиц (рис. 8а). Для аналогичного образца, синтезированного методом соосаждения, размер пластин намного больше, причем сами они расположены как параллельно, так и под углом друг к другу. Морфология образцов с соотношением Mg/Al = 4, независимо от метода синтеза, характеризуется скоплением пластин, ориентированных в разных направлениях (“розеточная”) (рис. 8б, 8г). При этом размер пластин для образцов, приготовленных методом соосаждения, значительно превышает таковой для MgAl-СДГ, полученных механохимическим методом [70].
Рис. 8.
СЭМ-изображения СДГ, полученных механохимическим методом: MgAl-2-СДГ, Mg/Al = 2 (a); MgAl-4-СДГ, Mg/Al = 4 (б); методом соосаждения: MgAl-2-СДГ, Mg/Al = 2 (в); MgAl-4-СДГ с Mg/Al = 4 (г). an = 1000 м с–2, стальные мелющие тела, t = 30 мин. Старение смеси механоактивированных компонентов в воде при 65°C в течение 2 ч [70], адаптировано из <[70] doi.org/10.1063/1.5122032>. <By courtesy of AIP Publishing>.
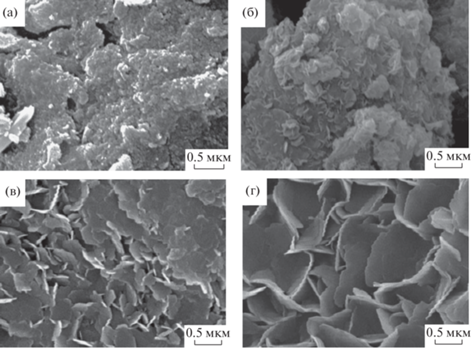
Как отмечалось выше, одним из важнейших направлений применения слоистых двойных гидроксидов является формирование из них (путем термического разложения) смешанных оксидов, характеризующихся высокой удельной поверхностью и оснóвной природой поверхности и представляющих большой интерес для использования в качестве катализаторов оснóвного типа или носителей для нанесенных металлических катализаторов. Приступая к анализу этой области, сразу отметим, что свойства смешанных оксидов (СО), образующихся при прокалке СДГ, существенно зависят от способа синтеза СДГ, и в случае механохимического метода характеризуются более равномерным распределением пор по размерам. Так, было установлено, что если для образцов СО, полученных при разложении MgAl-СДГ-ОН, синтезированных методом соосаждения (далее MgAl-OH-с), характерно бимодальное распределение пор по размерам (с максимумами на кривых распределения пор по размерам (КРПР) 2.6 и 39 нм и 3.1 и 29 нм для соотношений Mg/Al = 2 и 3 соответственно) [69], то для образцов того же химического состава, приготовленных из СДГ, синтезированных механохимическим методом (MgAl-OH-м), КРПР имеют один максимум в области 4–5 нм (рис. 9). В работе [71] СО на основе образцов СДГ, полученных с использованием механической активации, MgAl-CO3-м (an = 1000 м с–2, t = 30 и 60 мин) также показали мономодальное распределение размеров пор по размерам. При этом положение максимума в КРПР смещалось в область меньших значений (от 18 до 15 нм) при увеличении времени активации. В [72] отмечалась даже возможность формирования микропор для ряда СО, образовавшихся при разложении СДГ, синтезированных механохимическим методом.
Рис. 9.
Кривые распределения пор по размерам для MgAl-СДГ с разным соотношением Mg/Al, синтезированных методом соосаждения (с) и механохимическим методом (м): 1 – MgAl-2 (с), 2 – MgAl-3 (с), 3 – MgAl-2 (м), 4 – MgAl-3 (м) [69], адаптировано из <[69] doi.org/10.1134/S0023158418040134>. <By courtesy of Springer Nature >.
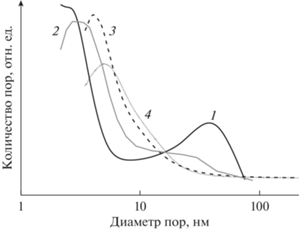
Важные данные о свойствах СО содержатся в работах [69, 73]. Было продемонстрировано, что СО, полученные прокаливанием при 550°C MgAl-СДГ, приготовленных механохимическим методом, как и СО того же состава на основе СДГ, синтезированных соосаждением, обладают “эффектом памяти” и способны к восстановлению слоистой структуры при контакте с водой. При этом происходит формирование так называемой “активированной” формы СДГ с локализацией в межслоевом пространстве анионов ОН– (рис. 10).
Рис. 10.
Схема формирования СО (Mg(Al)O) посредством прокаливания MgAl-СДГ с межслоевыми ${\text{СО}}_{3}^{{2 - }}$-анионами (Mg6Al2(OH)16CO3 · 4H2O) и регидратации СО с образованием активированного MgAl-СДГ с межслоевыми ОН–-анионами (Mg6Al2(OH)16(OH)2 · 4H2O).
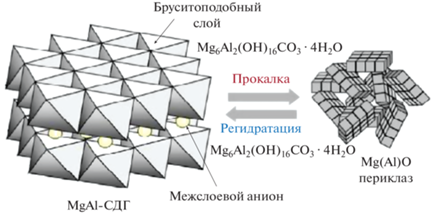
На рис. 11 приведены дифрактограммы, отражающие последовательность структурных превращений MgAl-СДГ, полученных двухстадийным в варианте II механохимическим методом: MgAl-CO3 → → MgAlOx(CO3) → MgAl-OH → MgAlOx(OH), иллюстрирующую возможность формирования двух видов гидроксидной (MgAl-CO3, MgAl-OH) и оксидной (MgAlOx(CO3), MgAlOx(OH)) фаз. Анализ данных РФА образцов, синтезированных механохимическим методом с Mg/Al = 2 и 4, показал, что после прокаливания MgAl-CO3 типичные рефлексы СДГ (003, 006, 013, 015, 018, 110 и 113) исчезали, и наблюдалось образование фазы СО MgAlOx(CO3) с характерными для нее пиками 400 и 440 на рентгенограммах (рис. 11а, кривая 2, рис. 11б, кривая 2) [74]. После контакта этого СО с водой слоистая структура СДГ восстанавливалась при формировании MgAl-OH, а последующее прокаливание позволило получить другой СО – MgAlOx(OH)
Рис. 11.
Дифрактограммы образцов с Mg/Al = 2 (а) и Mg/Al = 4 (б), синтезированных механохимическим методом: 1 – СДГ с анионами ${\text{СО}}_{3}^{{2 - }}$ в межслоевом пространстве (MgAl-CO3); 2 – образец 1, прокаленный при 550°С (MgAlOx(CO3)); 3 – СДГ с анионами OH– в межслоевом пространстве (MgAl-OH); 4 – образец 3, прокаленный при 550°С (MgAlOx(ОН)) [73], адаптировано из <[73] doi.org/10.1016/j.cattod.2019.04.069>. <By courtesy of Elsevier>.
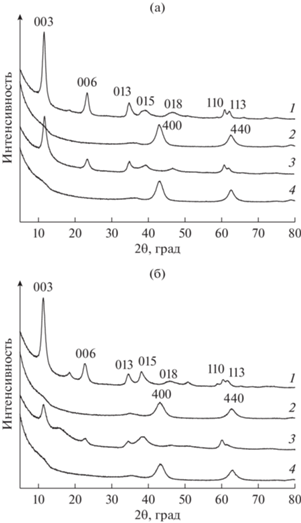
Исследования СДГ, синтезированных механохимическим методом, с использованием электронной микроскопии свидетельствуют, что морфология поверхности частиц СДГ зависит как от соотношения Mg/Al, так и от природы анионов в межслоевом пространстве [73]. В случае MgAl-2-CO3 (Mg/Al = 2) пластины СДГ размером ~0.1 мкм плотно упакованы параллельно друг другу (рис. 12а). При повышении отношения Mg/Al размер пластин несколько увеличивается (~0.2 мкм), и они ориентированы под углом друг к другу (рис. 12б). При замене межслоевых анионов ${\text{CO}}_{3}^{{2 - }}$ на анионы OH– морфология поверхности образцов СДГ изменяется, и из агрегатов мелких пластинчатых частиц формируются “розетки” с гексагональной морфологией, размер которых заметно возрастает при увеличении Mg/Al (рис. 12в, 12г). Последующее прокаливание образцов MgAl-CO3 и MgAl-ОН приводит к оксидным фазам, различающимся своей морфологией. Измерения величины удельной поверхности показали, что для MgAlOx(OH) она больше, чем для MgAlOx(CO3). Так, при Mg/Al = 2 значения удельной поверхности составляли 220 и 160 м2 г–1 для MgAlOx(OH) и MgAlOx(CO3) соответственно. При прокаливании MgAl-CO3 с отношением Mg/Al = 2 и 4 образовавшиеся частицы оксида характеризовались объемом пор 0.45–0.46 см3 г–1 при их среднем диаметре 11 нм. В случае MgAl-ОН с Mg/Al = 2 и 4 были получены оксиды с объемом пор 0.27–0.29 см3 г–1 и средним диаметром 5 нм [73].
Рис. 12.
СЭМ-изображения образцов: MgAl-2-CO3 (а); MgAl-4-CO3, 1000 м с–2, 30 мин (б); MgAl-2-OH (в); MgAl-4-OH (г). Увеличение ×30 000 [73], адаптировано из <[73] doi.org/10.1016/j.cattod.2019.04.069>. <By courtesy of Elsevier>.
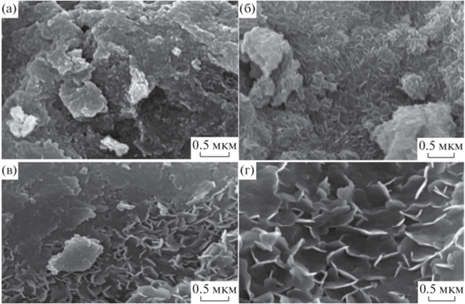
МЕХАНОХИМИЧЕСКИЙ СИНТЕЗ LiAl СЛОИСТЫХ ГИДРОКСИДОВ
LiAl-СДГ представляет собой уникальную форму СДГ, поскольку катион лития является единственным катионом щелочного металла, который может быть встроен в структуру СДГ без ее нарушения (если радиусы катионов Li+, Mg2+ составляют 0.078 нм, то катионный радиус Na+ уже заметно больше и равен 0.098 нм) [75–78]. В структуре LiAl-СДГ катионы Li+ расположены в вакантных октаэдрических позициях в слое Al(OH)3, в котором ионы Al3+ занимают 2/3 октаэдрических позиций [79]. В результате формируются гидроксидные слои с наибольшей плотностью положительного заряда по сравнению с СДГ другого состава. Как следствие, LiAl-СДГ обладают более высокой анионообменной способностью по сравнению с M2+M3+-СДГ. Эта особенность LiAl-СДГ может быть полезной при создании адсорбентов, а также при синтезе катализаторов, когда интеркалированные анионные комплексы металлов являются предшественниками активного компонента [73].
Отметим, что в случае LiAl-СДГ механохимический синтез особенно актуален, поскольку к настоящему времени основным методом получения этого соединения является жидкофазный – гидролиз солей алюминия в присутствии большого избытка раствора карбоната лития, в процессе которого только незначительная часть Li+ встраивается в структуру гидроксида алюминия [80–85]. В некоторых исследованиях при синтезе Li-содержащих СДГ соосаждение дополняли стадией гидротермальной обработки для увеличения полноты реакции между исходными реагентами и кристалличности полученного материала [86–90]. Также описан способ получения LiAl-СДГ при взаимодействии между металлическим Al или AlLi-сплавом и растворами LiOH или LiNO3/NaOH [91, 92]. Все указанные методы сопровождаются образованием большого количества побочных продуктов и/или требуют высоких температур и длительного времени реакции.
Среди работ, использующих при синтезе LiAl-СДГ механическое воздействие, следует отметить [35, 93], в которых механической активации подвергали только один из реагентов – тригидроксид алюминия. В [35] для получения LiAl-СДГ с интеркалированными тетраборат-анионами образец гиббсита Al(OH)3 сначала активировали в течение 2 ч в планетарной мельнице (Pulverisette-7, “FRITSCH”, Германия, шары из диоксида циркония) с варьированием скорости вращения 200, 400, 600 об. мин–1, а затем проводили гидротермальную обработку в водном растворе Li2B4O7 при 95°С в течение 15 ч. Мольное отношение Li/Al/B составляло 1/1.5/2. Была установлена роль первой стадии синтеза: только при скорости вращения 600 об. мин–1 на первой стадии происходила полная реакции между активированным Al(OH)3 и Li2B4O7 с образованием единственной фазы СДГ. В работе [93] на первом этапе Al(OH)3 мехактивировали с постоянной скоростью 450 об. мин–1 в течение 1 ч (планетарная мельница QM3STC, “Nanjing”, Китай, стальные шары), на втором этапе мехактивированный Al(OH)3 помещали в автоклав с раствором LiOH и подвергали гидротермальной обработке в течение 1 ч при варьировании температуры 20–80°С. Данный метод обеспечил формирование частиц LiAl-OH с высокой дисперсностью и правильной гексагональной морфологией, а повышение температуры гидротермальной обработки способствовало росту их кристалличности, и на дифрактограммах наблюдались интенсивные и узкие дифракционные пики, характерные для СДГ. LiAl-СДГ может быть получен и без гидротермальной обработки, если использовать двухстадийный механохимический синтез по варианту I [93], где на первой стадии механической активации подвергали Al(OH)3 в течение 1 ч, затем добавляли LiOH ⋅ H2O и проводили совместную мехактивацию еще в течение 1 ч. Отметим, однако, что в этом случае была получена смесь частиц СДГ различной формы и неоднородных по размерам.
Работы [70, 73, 94–96], связанные с синтезом LiAl-СДГ механохимическим методом, также были направлены на выяснение влияния условий механического воздействия на закономерности образования СДГ, на те текстурные и оснóвные свойства оксидной фазы, которые актуальны с точки зрения возможного применения этих СДГ в качестве носителей и катализаторов оснóвного типа. Так, в [95, 96] был выполнен одностадийный механохимический синтез LiAl-СДГ с использованием порошков кристаллогидрата нитрата лития LiNO3 ⋅ 3H2O и тригидроксида алюминия (смесь нордстрандита и байерита) с атомным отношением Li/Al = 0.5 в условиях механической активации в планетарной мельнице АГО-2 с an стальных мелющих тел 300, 600 и 1000 м с–2, t варьировали от 5 до 60 мин. Исследование фазового состава продуктов механохимического синтеза показало, что независимо от условий процесса основным компонентом являлся LiAl-СДГ (рис. 13). Кроме того, в продуктах присутствовал непрореагировавший тригидроксид алюминия (около 30 мол. % от исходного количества Al(OH)3). Было установлено, что структурные параметры кристаллитов полученного LiAl-СДГ менялись в зависимости от условий механохимического синтеза: так, при увеличении t размеры кристаллитов уменьшались в направлении нормали к слою (Lc). Данный эффект наблюдался уже при an = 300 м с–2 (сокращение размеров от 300 до 270 Å при изменении t с 15 до 30 мин), но в большей степени происходил при an = 600 и 1000 м с–2. В наиболее жестких условиях (1000 м с–2, 30 мин) Lc составлял 85 Å. Наряду с уменьшением размеров Lc при возрастании t и an снижалось количество слоев в одном пакете, рассчитываемое как отношение Lc к величине межплоскостного расстояния базального рефлекса d003, что свидетельствовало о постепенном разрушении отдельных пакетов слоистой фазы. Кроме того, фиксировалось сокращение величины межплоскостного расстояния d003 вследствие удаления части молекул воды из межслоевых пространств в более жестких условиях механохимического синтеза.
Рис. 13.
Дифрактограммы образцов, полученных при механической активации смеси LiNO3 and Al(OH)3 в течение 15 мин и an стальных мелющих тел 300 (1), 600 (2) и 1000 м с–2 (3) [95], адаптировано из <[95] doi.org/10.1016/j.proeng.2015.07.298. <Distributed under a HYPERLINK "https://creativecommons.org/licenses/by/4.0/"Creative Commons Attribution 4.0 License.
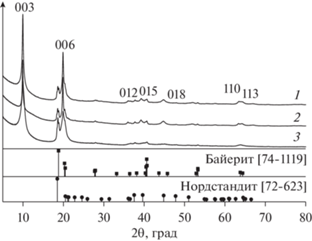
Следует отметить, что полученные LiAl-СДГ обладали повышенной термической стабильностью по сравнению с СДГ другого химического состава, что важно при необходимости сохранения слоистой структуры в условиях высокотемпературных реакций. Результаты термического анализа показали, что если для СДГ с катионными парами ZnAl, NiAl, MgGa, MgAl максимумы высокотемпературных пиков, характеризующих процессы удаления межслоевых анионов и дегидроксилирования слоев СДГ, составляли 180, 330, 410, 450°C соответственно [97], то для LiAl-СДГ (независимо от t и an) это значение было равно 560°C [95].
Выявлено, что условия механохимического синтеза влияют не только на структуру LiAl-СДГ, но и на характеристики полученных при их прокаливании (550°С) алюмолитиевых CO: по мере увеличения t и an происходил рост удельной поверхности соответствующих CO от 100 до 160 м2 г–1 и уменьшение среднего диаметра пор от 15 до 5 нм с их мономодальным распределением по размерам [95]. В работе [96] наряду с исследованием влияния условий активации (t, an) на свойства LiAl-LDH было выполнено варьирование состава исходной смеси и материала мелющих тел. Для смеси Al(OH)3 + Li(NO3) ⋅ 3H2O с соотношением Li/Al = 0.5 и 1 условия механохимической активации были следующие: при использовании стальных шаров an = 1000 м с–2, t = 30 и 60 мин, при использовании керамических шаров an = 300 м с–2, t = 15, 30 и 60 мин. При применении стальных мелющих тел в жестких условиях высоких ускорений одностадийного механохимического синтеза СДГ может быть синтезирован с высоким выходом. Однако все полученные продукты не являлись однофазными и включали кроме фазы СДГ примесь тригидроксида алюминия (6.5 и 2.1 мас. % при Li/Al = 0.5 и 1 соответственно). Кроме того, химический анализ образцов обнаружил присутствие железа, содержание которого увеличивалось от 1.1 до 2.1 мас. % при повышении доли нитрата лития в смеси. В случае смеси Al(OH)3 и LiOH фазовый состав продуктов был аналогичен, однако содержание железа возрастало до 19 мас. %. Механохимический синтез с применением керамических (на основе ZrO2) мелющих тел был выполнен при использовании в качестве исходных соединений тригидроксида алюминия и нитрата лития (Li/Al = 0.5). Было показано, что фаза LiAl-СДГ также являлась основной даже при минимальном времени активации, а содержание циркония в конечном продукте не превышало 0.5 мас. % (рис. 14). Таким образом, в рамках выбранных условий одностадийного механохимического синтеза авторам не удалось получить фазово однородную систему.
Рис. 14.
Дифрактограммы образцов LiAl-СДГ, полученных с использованием керамических мелющих тел при варьировании t активации и an = 300 м с–2 [96], адаптировано из <[96] doi.org/10.1016/j.proeng.2016.07.672. <Distributed under a Creative Commons Attribution 4.0 License.
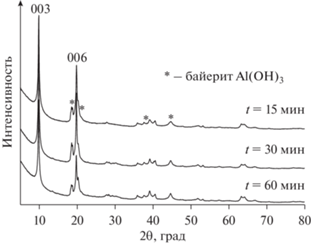
Переход к двухстадийному методу позволил синтезировать однофазный LiAl-СДГ [70, 73, 98] при применении в качестве исходных соединений Al(OH)3 (байерит) и LiNO3 ⋅ 3H2O (Li/Al = = 0.5). На стадии мехактивации были использованы стальные барабаны и стальные мелющие тела, t составляло 30 мин при an = 1000 м с–2. Вторую стадию проводили при интенсивном перемешивании смеси механоактивированных компонентов в дистиллированной воде при 65°C в течение 2 ч. Таким образом были приготовлены LiAl-СДГ, содержащие нитратные анионы в межслоевом пространстве (карбонатные анионы также присутствовали в межслоевом пространстве, так как синтез осуществляли в среде воздуха). На их дифрактограмме (рис. 15а, кривая 1) присутствовали только рефлексы 003, 006 и 110, характерные для слоистой структуры СДГ. Двухстадийный механохимический метод синтеза LiAl-СДГ с межслоевыми карбонатными ионами был выполнен также при использовании трехкомпонентной реакционной смеси Al(OH)3 (гиббсит), LiOH и Na2CO3 с введением карбоната натрия в качестве источника межслоевых карбонат-ионов [70]. Механическую активацию проводили при an = 1000 м с–2 в течение 30 мин при применении стальных мелющих тел. Атомное отношение Li/Al составляло 0.5 при мольном отношении Al(OH)3/Na2CO3 = 0.5. Однако в отличие от описанного выше синтеза (со смесью Al(OH)3 и LiNO3 ⋅ 3H2O) переход к трехкомпонентной смеси (Al(OH)3, LiOH и Na2CO3) не способствовал полному прохождению твердофазной реакции, и фаза непрореагировавшего гидроксида алюминия наблюдалась наряду с целевой фазой СДГ (рис. 15б).
Рис. 15.
а – Дифрактограммы литийсодержащих образцов с Li/Al = 0.5: 1 – СДГ с анионами ${{{\text{NO}}_{3}^{ - }} \mathord{\left/ {\vphantom {{{\text{NO}}_{3}^{ - }} {{\text{CO}}_{3}^{{2 - }}}}} \right. \kern-0em} {{\text{CO}}_{3}^{{2 - }}}}$ в межслоевом пространстве (LiAl-NO3/CO3); 2 – прокаленный образец 1 (LiAlOx-NO3/CO3), 3 – регидратированный образец 2 (СДГ с анионами OH– в межслоевом пространстве, LiAl-OH); 4 – прокаленный образец 3 (LiAlOx-OH). Дополнительные фазы: + – LiAlO2, γ – Al2O3 [73], адаптировано из <[73] doi.org/10.1016/j.cattod.2019.04.069>. <By courtesy of Elsevier>. б – Дифрактограммы LiAl-СДГ, приготовленных двухстадийным механохимическим методом: LiAl-1 – реакционная смесь Al(OH)3 и LiNO3 ⋅ 3H2O; LiAl-2 – реакционная смесь Al(OH)3 + LiOH + Na2CO3; * – фаза Al(OH)3 [70], адаптировано из <[70] doi.org/10.1063/1.5122032>. <By courtesy of AIP Publishing>.
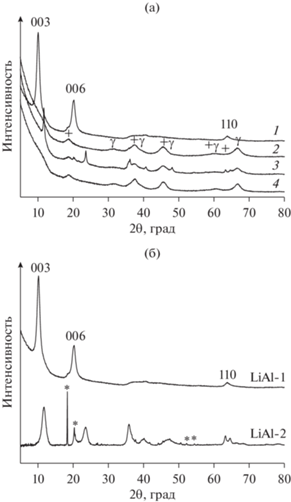
Интересно отметить, что, как и для алюмомагниевых композиций, возможен синтез “активированной” формы LiAl-СДГ (LiAl-OH) с гидроксид-анионами в межслоевом пространстве посредством регидратации СО LiAlOx(NO3/CO3) (полученного прокаливанием LiAl-NO3/CO3 при 550°C) в дистиллированной воде (рис. 15а, кривые 2 и 3), т.е. алюмолитиевые системы также, как описанные выше алюмомагниевые, обладают “эффектом памяти”. При восстановлении слоистой структуры фиксировалось заметное уменьшение межслоевого расстояния d003 с 0.885 до 0.756 нм, характерное при замене карбонатных и нитратных межслоевых анионов на ОН–. При этом, согласно данным СЭМ, происходили заметные изменения в морфологии частиц СДГ в зависимости от состава их межслоевого пространства. Так, для образца LiAl-NO3/CO3 наблюдались плотно упакованные слои округлых частиц, а при формировании LiAl-OH образовывались крупные гексагональные пластины, перекрывающиеся друг с другом в разных направлениях (рис. 16).
Рис. 16.
СЭМ-изображения образцов СДГ: LiAl-NO3/ CO3 (а); LiAl-ОН (б). Увеличение ×30 000 [73], адаптировано из <[73] doi.org/10.1016/j.cattod.2019.04.069>. <By courtesy of Elsevier>.
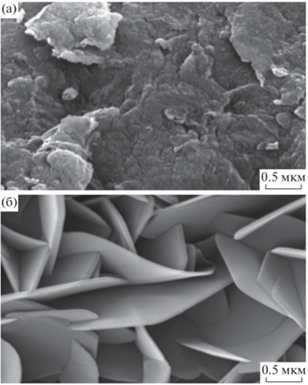
Прокаливание как LiAl-NO3/CO3, так и LiAl-OH при 550°С приводило к исчезновению рефлексов фазы СДГ на дифрактограммах (рис. 15а, кривые 2 и 4) и появлению пиков, относящихся к фазам LiAlOх (основная) и оксида алюминия, близкого по структуре γ-Al2О3. Однако, несмотря на похожий фазовый состав, свойства сформировавшихся оксидных фаз отличались и определялись строением соответствующего гидроксидного предшественника. Так, значения удельной поверхности (147 м2 г–1) и объема пор (0.43 см3 г–1) для оксида, образовавшегося из LiAl-ОН, были выше, чем для оксида, полученного из LiAl-(NO3/CO3) (118 м2 г–1 и 0.35 см3 г–1). Для исследованных смешанных оксидов характерно широкое распределение мезопор по размерам в диапазоне 5–50 нм с максимумом 15 нм для LiAlOx(NO3/CO3) и 13 нм для LiAlOx(OH) [73]. Таким образом, было установлено, что текстурные свойства LiAl смешанных оксидов, как и MgAl-аналогов, можно целенаправленно регулировать, изменяя не только условия проведения механохимической стадии синтеза соответствующих СДГ, но и природу анионов в их межслоевом пространстве.
Важно отметить, что процесс регидратации LiAl-СО с восстановлением структуры СДГ может быть использован для введения анионов в межслоевое пространство [99]. Так, при контакте LiAlOx (полученного прокаливанием LiAl-СДГ при 550°С) с водным раствором Н2[PtCl6] наблюдалось полное извлечение платинового комплекса. При этом на дифрактограммах появлялись рефлексы, соответствующие фазе СДГ, а их низкая интенсивность и уширение свидетельствовали о значительной разупорядоченности структуры синтезированного СДГ в результате взаимодействия с комплексным анионом.
ОСНÓВНЫЕ СВОЙСТВА КАТАЛИЗАТОРОВ НА ОСНОВЕ Mg(Li)Al-СДГ. АКВАФАЗНАЯ АЛЬДОЛЬНАЯ КОНДЕНСАЦИЯ ФУРФУРОЛА С АЦЕТОНОМ
Присутствие магния и лития в составе слоистых двойных гидроксидов, в том числе приготовленных механохимическим методом, придает им оснóвные свойства, что является важным фактором при создании катализаторов с использованием СДГ. В работах [73, 95, 98] оснóвные свойства смешанных оксидов Mg(Li)AlOx, образовавшихся при прокаливании соответствующих СДГ, которые были синтезированы двухстадийным механохимическим методом, изучали с помощью двух подходов (рис. 17). Первый – температурно-программируемая десорбция СО2 – динамический метод, позволяющий определять количество СО2, десорбированного с поверхности при повышении температуры в заданном режиме. Второй – статический метод двойных изотерм [100], в рамках которого изотерму адсорбции СО2, полученную при 0.1 МПа и 30°С, используют для расчета полной емкости образца по этому газу (физически и химически адсорбированный СО2). После этого образец вакуумируют до 1.33 Па при той же температуре в течение 1 ч для удаления физически адсорбированных молекул и получают вторую изотерму. Разность двух изотерм позволяет определить количество хемосорбированного СО2. Так как надежно установлено наличие корреляции между температурой десорбции СО2 и основностью образцов, для дифференциации адсорбционных центров по прочности удерживания СО2 (силе оснóвных центров) стадию вакуумирования проводят при 30, 100 и 200°С. При низкой температуре СО2 десорбируется со слабооснóвных центров (ОН–-группы), при более высокой температуре – с оснóвных центров средней силы (пары Mg2+–O2–) и при максимальной температуре – с сильных оснóвных центров (терминальные анионы O2–, М=О-фрагменты) [101]. Таким образом, при использовании обоих методов общую основность материала оценивали по суммарному количеству десорбированного СО2, а силу оснóвных центров – по количеству СО2, десорбированного при определенной температуре.
Рис. 17.
Кривые ТПД-CO2 (а) и адсорбционная емкость по CO2 (б) для смешанных оксидов на основе Mg(Li)Al-CO3: 1 – MgAlOх, Mg/Al = 2; 2 – MgAlOх, Mg/Al = 4; 3 – LiAlOx [73], адаптировано из <[73] doi.org/10.1016/j.cattod.2019.04.069>. <By courtesy of Elsevier>.
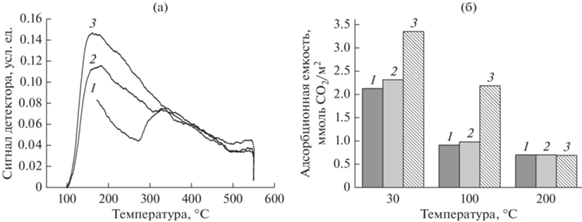
Увеличение отношения Mg/Al и присутствие лития в оксидных фазах, полученных из соответствующих СДГ, увеличивает общую основность согласно результатам обоих методов оценки [73, 95, 98]. Интегрирование профилей TПД-CO2 (рис. 17а) и их моделирование с выделением областей десорбции с максимумами температуры 150–160, 230–250 и 350–400°С позволило не только расположить образцы по росту их основности в ряду MgAlOx-2 < MgAlOx-4 < LiAlOx, но и установить количественные соотношения между оснóвными центрами различной силы [73]. Показано, что для всех исследованных оксидов Mg(Li)AlOx количество CO2, десорбированного в высокотемпературном диапазоне, связанном с сильными оснóвными центрами, практически одинаково для всех образцов и составляет 0.4–0.5 мкмоль м–2. Большее суммарное количество десорбированного СО2 для алюмолитиевых оксидов и алюмомагниевых оксидов с высоким содержанием магния (Mg/Al = 4) обусловлено более высокой концентрацией на поверхности слабых и средней силы оснóвных центров (область десорбции 100–300°С). Эта тенденция наблюдается и при использовании статического метода (рис. 17б). В работе [73] также было продемонстрировано, что основность смешанных оксидов можно регулировать, изменяя состав межслоевого пространства соответствующих СДГ. Образцы оксидов на основе Mg(Li)Al-ОН имели более низкую основность по сравнению с аналогами, полученными из карбонатных предшественников того же катионного состава.
Выраженные оснóвные свойства смешанных оксидов позволяют рассматривать их как твердые оснóвные катализаторы. Для исследования их каталитических свойств была выбрана альдольная конденсация фурфурола с алифатическими кетонами, которая не только служит тестом на оснóвные свойств катализаторов, но и широко используется в органическом синтезе [102–104]. Традиционно реакцию проводят в присутствии щелочей NaOH и KOH и более сложных систем (пирролидин, пролинат цинка, L-лизин, производные пролинтиоамида и ионные жидкости), часто в органических растворителях [105–110]. Очевидными недостатками таких катализаторов являются токсичность, сложность приготовления, нестабильность в водных растворах, невозможность вторичного применения и высокая стоимость. Поэтому создание твердых оснóвных катализаторов представляет собой актуальную задачу, и катализаторы на основе Mg(Li)Al-СДГ имеют большие перспективы использования в этом направлении [111–113].
В [98] в реакции альдольной конденсации между фурфуролом и ацетоном в водной среде был изучен LiAl-СДГ, полученный одностадийным механохимическим методом. Механическую активацию смеси LiNO3 ⋅ 3H2O и Al(OH)3 (Li/Al = = 0.5) осуществляли в планетарной мельнице АГО-2 со стальными мелющими телами (an = 300 и 1000 м с–2, t = 15 и 30 мин). Активность катализаторов на основе синтезированных LiAl-СДГ сравнивали с таковой алюмомагниевых катализаторов основе СДГ, приготовленных соосаждением и имеющих атомные соотношения Mg/Al = 3 и 4. Катализаторами данной реакции являлись СДГ в активированной форме LiAl-ОН и MgAl-ОН, формирующиеся непосредственно в реакционной водной среде в процессе регидратации соответствующих СО (полученных прокалкой при 550°С LiAl-NO3/CO3 и MgAl-CO3). В выбранных условиях аквафазной реакции (мольное отношение фурфурол/ацетон = 0.1, температура – 70°С) альдольная конденсация в присутствии указанных твердых катализаторов протекала в соответствии со схемой 1 , и основными продуктами были 4-(2-фуранил)-4-гидрокси-2-бутанон (1), 4-(2-фуранил)-3-бутен-2-он (2) и 1,5-ди-2-фуранил-1,4-пентадиен-3-он (3). Кроме того, в незначительной степени происходила “самоконденсация” ацетона, поскольку среди продуктов обнаружен 4-гидрокси-4-метил-2-пентанон. В присутствии катализатора LiAlOx-0.5, имеющего наибольшую основность, скорость превращения фурфурола была самой высокой; полное превращение фурфурола наблюдалось через 30 мин реакции с селективным (95 мас. %) образованием соединения 2. Остальные катализаторы также обеспечили практически полное превращение фурфурола (при селективности по 4-(2-фуранил)-3-бутен-2-ону 96–97%), но за большее время. Для наиболее активного из алюмомагниевых систем MgAlOx-4 конверсия фурфурола через 30 мин после начала реакции достигала 80%.
Схема 1 . Альдольная конденсация фурфурола с ацетоном в присутствии оснóвного катализатора [98], адаптировано из < [98] doi.org/10.1515/cse-2017-0003>. <Distributed under a Creative Commons Attribution 3.0 License>.
В [73] в тех же условиях альдольной конденсации фурфурола с ацетоном были испытаны катализаторы на основе Mg(Li)Al-СДГ, полученных двухстадийным механохимическим методом. Исходными соединениями для первой стадии синтеза MgAl-СДГ были Mg(OH)2, Al(OH)3 и Na2CO3 (Mg/Al = 2 и 4, Al(OH)3/Na2CO3 = 0.5), а для синтеза LiAl-СДГ – Al(OH)3 и LiNO3⋅3H2O (Li/Al = = 0.5), t составило 30 мин при an = 1000 м с–2. Вторую стадию проводили при перемешивании смеси механоактивированных компонентов в дистиллированной воде при 65°С в течение 2 ч. Таким образом были приготовлены MgAl-СДГ с карбонат-анионами и LiAl-СДГ с нитрат- и карбонат-анионами в межслоевом пространстве. Перед добавлением в реакционную среду синтезированные СДГ для перевода в соответствующие СО были прокалены при 550°С. Установлено, что активность испытанных катализаторов определялась их основностью и, как и в предыдущем исследовании, литийсодержащий катализатор (LiAl-ОН), формирующийся при регидратации LiAlOx в реакционной водной среде, характеризовался максимальной активностью в альдольной конденсации фурфурола с ацетоном. Его активность была близка к таковой катализатора на основе LiAl-СДГ, приготовленного одностадийным механохимическим синтезом [98]: полная конверсия фурфурола достигалась через 30 мин реакции (рис. 18а). Однако селективность по целевому 4-(2-фуранил)-3-бутен-2-ону для этих образцов отличалась (рис. 18б). Так, Li-содержащий образец, полученный по двухстадийной схеме, имел невысокую селективность по продукту 2 в результате интенсивного процесса “самоконденсации” ацетона вследствие большей основности (неоптимальной для образования соединения 2) (схема 1 ). Для наименее оснóвного алюмомагниевого катализатора (Mg/Al = 2), конверсия фурфурола не превышала 80 мас. % даже через 150 мин после начала реакции (рис. 18а). Кроме того, было показано, что изменение состава межслоевого пространства в Mg(Li)Al-СДГ, использующихся для приготовления катализаторов (например, применение СДГ с гидроксильными анионами в межслоевом пространстве), позволяет дополнительно варьировать основность катализаторов и, следовательно, регулировать их каталитические свойства [73]. Анализируя представленные результаты, можно сделать вывод, что каталитические свойства Li-содержащих катализаторов могут быть настроены под требования конкретной реакции составом LiAl-СДГ и выбором схемы механохимического синтеза, тогда как активность таких каталитических систем превышает активность алюмомагниевых катализаторов, полученных как традиционным способом соосаждения, так и механохимическим методом. В то же время катализаторы на основе MgAl-СДГ, обладая меньшей основностью, могут быть востребованы вследствие их более высокой селективности (в данном случае по отношению к целевому 4-(2-фуранил)-3-бутен-2-ону).
Рис. 18.
Конверсия фурфурола X (а) и селективность S образования 4-(2-фуранил)-3-бутен-2-она (б) в зависимости от времени при аквафазной альдольной конденсации на катализаторах LiAlOx-CO3 (1), MgAlOx-4-CO3 (2) и MgAlOx-2-CO3 (3) [98], адаптировано из <[98] doi.org/10.1515/cse-2017-0003. <Distributed under a Creative Commons Attribution 3.0 License.
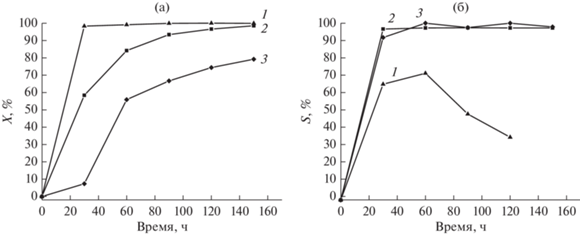
Ni- И Co-СОДЕРЖАЩИЕ СДГ, ПОЛУЧЕННЫЕ МЕХАНОХИМИЧЕСКИМ МЕТОДОМ, И КАТАЛИЗАТОРЫ ГИДРИРОВАНИЯ ФУРФУРОЛА НА ИХ ОСНОВЕ
Как отмечалось выше, структура СДГ позволяет варьировать катионный состав гидроксидных слоев (при условии соблюдения близкого размера катионных радиусов), в том числе вводить катионы переходных металлов (Ni, Co, Zn, Fe, Zr и др.) в состав би- и полиметаллической композиции с обеспечением однородного распределения вводимых металлов на атомном уровне, что увеличивает их устойчивость к агломерации при термообработках и приводит к образованию высокодисперсных частиц, распределенных в оксидной матрице [114]. Анализ опубликованных данных показывает, что использование механохимических методов не только ускоряет синтез таких катализаторов и уменьшает количество сточных вод, но и способствует формированию более дефектных частиц активного металла с повышенной каталитической активностью. Механохимический синтез двух- и трехкомпонентных слоистых гидроксидов описан, например, для MgFeAl- [115], MgNiAl- [116], MgFe- и ZnAl- [117], CoAl- и NiAl-СДГ [118]. Свойства подобных материалов и возможность их получения во многом определяется составом и соотношением исходных соединений, а также условиями механохимического синтеза. Например, в [70] для приготовления NiAl- и CoAl-СДГ применяли двухстадийный механохимический метод по способу II. Условия проведения первой стадии варьировали в зависимости от материала мелющих тел. При использовании керамических и стальных шаров an была 300 и 1000 м с–2 соответственно; t во всех случаях составляло 30 мин, а при варьировании состава исходных соединений атомное отношение металлов M2+/Al в исходных смесях оставалась постоянным и равным 2. На втором этапе механоактивированные компоненты выдерживали в дистиллированной воде при 65°C в течение 2 ч. Применяли 2 типа реакционных смесей: двухкомпонентную Al(OH)3 и Ni(NO3)2 ⋅ 6H2O (или Co(NO3)2 ⋅ 6H2O), в которой атом переходного металла находился в составе соли, и трехкомпонентную Al(OH)3, Ni(OH)2 (или Co(OH)2) и Na2CO3, в которой использовались гидроксиды металлов и карбонат натрия как источник межслоевых ${\text{СО}}_{3}^{{2 - }}$-анионов (мольное отношение Al(OH)3/Na2CO3 составляло 0.5). Согласно данным РФА, образование однофазных NiAl- и CoAl-СДГ происходило только в случае активации трехкомпонентных смесей с применением стальных мелющих тел (рис. 19, образцы Ni(Co)Al-2,3). Уширение и низкая интенсивность пиков, характеризующих фазы СДГ, свидетельствовали о значительной разупорядоченности структуры полученного СДГ. При активации смеси, состоящей из Al(OH)3 и Ni(NO3)2 ⋅ 6H2O (рис. 19, образцы Ni(Co)Al-2), наряду с фазой СДГ присутствовало значительное количество непрореагировавшего гиббсита, и на дифрактограммах наблюдались интенсивные рефлексы данного соединения независимо от материала шаров. CoAl-СДГ из смеси Al(OH)3 и Co(NO3)2 ⋅ 6H2O с заметной примесью гиббсита формировался исключительно в жестких условиях с применением стальных мелющих тел. Важно, что использование гидроксидов металлов (в составе трехкомпонентной смеси) в двухстадийном (способ II) механохимическом синтезе не только привело к формированию однофазных Ni(Co)Al-СДГ (рис. 15, образцы Ni(Co)Al-3), но и помогло избежать их существенного загрязнения железом. Даже в жестких условиях механической активации (1000 м с–2) при применении стальных мелющих тел содержание железа в конечном продукте не превышало 0.5 мас. %.
Рис. 19.
Дифрактограммы NiAl-СДГ (а) и CoAl-СДГ (б), приготовленных двухстадийным механохимическим методом [70], адаптировано из <[70] doi.org/10.1063/1.5122032>. <By courtesy of AIP Publishing>. Ni(Со)Al-1 – мехактивация смеси Al(OH)3 и Ni(или Со)(NO3)2 ⋅ 6H2O, керамические шары; Ni(Со)Al-2 – мехактивация смеси Al(OH)3 и Ni(или Со)(NO3)2 ⋅ 6H2O, стальные шары; Ni(Со)Al-3 – мехактивация смеси Al(OH)3, Ni(или Со)(OH)2 и Na2CO3, стальные шары.
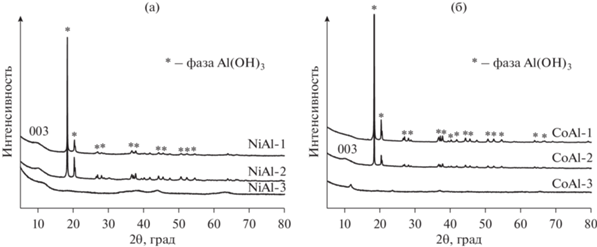
В продолжение данного исследования в [119] трехкомпонентная Al(OH)3, Ni(OH)2 и Na2CO3 и четырехкомпонентная Al(OH)3, Mg(OH)2, Ni(OH)2 и Na2CO3 смеси на основе гидроксидов металлов были использованы для получения NiAl-СДГ с разным соотношением Ni/Al и СДГ с двумя типами двухвалентных катионов NiMgAl-СДГ. Первую стадию двухстадийного механохимического синтеза осуществляли в тех же жестких условиях при an = 1000 м с–2 и t = 30 мин. В двойных NiAl-СДГ мольные соотношение катионов Ni/Al составляло 2, 3 и 4 (образцы NiAl(2, 3, 4)), в тройных NiMgAl-СДГ доля никеля в составе двухвалентных катионов Ni/(Ni + Mg) была равна 0.5 при мольных соотношениях между двух- и трехвалентными катионами (Ni + Mg)/Al = 2, 3 и 4 (образцы 0.5Ni-MgAl(2, 3, 4)). Дифрактограммы таких Ni-содержащих СДГ (полученных в одинаковых условиях механохимической активации, выдержки в воде и сушки), представлены на рис. 20. Из сопоставления дифрактограмм следует, что при синтезе всех образцов фаза СДГ являлась основной, однако по мере увеличения доли двухвалентных катионов росла интенсивность пиков дополнительных фаз, относящихся к исходным непрореагировавшим соединениям. Следует отметить, что в отличие от широких пиков низкой интенсивности, наблюдаемых для NiAl-систем (рис. 20а), тройные системы Ni-MgAl-СДГ характеризуются более интенсивными рефлексами, относящимися к фазе СДГ, что указывает на бóльшую кристалличность образующегося материала. Но, как и для двойных NiAl-систем, на дифрактограммах образцов Ni-MgAl также присутствуют пики, соответствующие фазам исходных компонентов (гидроксидов никеля и алюминия) при увеличении доли двухвалентных катионов.
Рис. 20.
Дифрактограммы образцов. а – NiAl-СДГ: 1 – NiAl(2), 2 – NiAl(3), 3 – NiAl(4); б – Ni-MgAl-СДГ: 1 – 0.5Ni-MgAl(2), 2 – 0.5Ni-MgAl(3), 3 – 0.5Ni-MgAl(4) [119], адаптировано из <[119] doi.org/10.1063/5.0032858>. <By courtesy of AIP Publishing>.

Важный результат, касающийся свойств СДГ, был получен в работе [99]. Показано, что СО, образовавшиеся при прокаливании Mg(Ni, Co)Al-СДГ, не обладают эффектом памяти и, в отличие от алюмомагниевых (литиевых) оксидов, не восстанавливают слоистую структуру при контакте с водными растворами. Так, Mg(Ni,Co)Al-СДГ, приготовленные двухстадийным механохимическим методом (при идентичных условиях синтеза и составе исходных компонентов), были прокалены при 550°С и затем контактировали с водным раствором H2[PtCl6]. При использовании всех вышеописанных смешанных оксидов NiAlОх, CoAlОх и 0.3NiMgAlOx в течение 1 ч происходило полное адсорбционное извлечение из раствора платина-хлоридных комплексов, но слоистая структура при этом не восстанавливалась. На рис. 21 в качестве примера приведены дифрактограммы для Ni-MgAl-системы, демонстрирующие, что рефлексы, характерные для 0.3Ni-MgAl-СДГ, после его прокалки исчезали, а на дифрактограмме этого образца после его контакта с водным раствором (обозначен как [PtCl6]/0.3Ni-MgAl) присутствовали только пики, относящиеся к фазе NiO. Полученная информация важна для понимания деталей синтеза нанесенных катализаторов на основе данных оксидных систем.
Рис. 21.
Дифрактограммы образцов Ni(Mg)Al-СДГ и [PtCl6]/Ni(Mg)AlOx. Адаптировано из <[99] doi.org/10.1063/5.0032741>. <By courtesy of AIP Publishing>, [99].
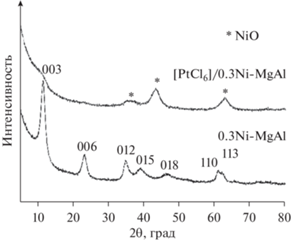
Восстановительная обработка Ni- или Со-содержащих оксидов на основе СДГ приводит к формированию дисперсных частиц этих металлов, активных в каталитических реакциях. И если опубликованные сведения о таких каталитических системах имеются для СДГ, полученных соосаждением [120–122], то информация о возможности механохимического синтеза предшественника никелевого катализатора ограничена. Хорошо известно, что никелевые системы являются эффективными катализаторами гидрирования, активность которых напрямую определяется возможностями диспергирования гидрирующего металла на их поверхности [123, 124]. В [119] представлены данные о свойствах катализаторов на основе Ni-содержащих СДГ, полученных механохимическим методом в реакции аквафазного гидрирования фурфурола. Интерес к этой реакции связан с тем, что фурфурол – это крупнотоннажный продукт переработки биомассы, а продукты его каталитического гидрирования (схема 2 ), такие как тетрагидрофурфуриловый спирт (THFA), фурфуриловый спирт (FA) и тетрагидрофурфурол (THF), широко используются в качестве высокооктановых добавок в моторное топливо, для производства жаропрочных и жидких смол, а также в фармацевтической промышленности и косметологии [123].
Схема 2 . Реакции гидрирования фурфурола [122], адаптировано из <[122] doi.org/10.1016/j.matchemphys. 2020.124091>. <By courtesy of Elsevier >.
В качестве предшественников никелевых катализаторов реакций по схеме 2 были исследованы двух и трехкомпонентные NiAl- и NiMgAl-СДГ (при Ni/(Ni + Mg) = 0.5 и c соотношениями M2+/Al = 2, 3 и 4), полученные двухстадийным (вариант II) механохимическим методом. Их предварительная обработка перед каталитическими экспериментами включала прокаливание при 600°С на воздухе и восстановление при 600°С в водороде, при этом на стадии прокаливания наблюдалось образование фазы СО, а при последующем взаимодействии с водородом происходило частичное восстановление катионов никеля [97, 122]. Аквафазное гидрирование фурфурола в присутствии синтезированных катализаторов проводили при температуре 90°С и давлении 2.0 МПа. Среди биметаллических катализаторов максимальную активность показал образец с меньшим содержанием никеля (Ni/Al = 2) (рис. 22а), вероятно, вследствие более однородного распределения катионов никеля в структуре исходного алюмоникелевого СДГ. Дополнительное диспергирование никеля достигалось при введении катиона магния, и, как следствие, трехкомпонентные системы продемонстрировали повышенную активность (особенно при соотношениях (Ni + Mg)/Al = 3 и 4) (рис. 22б). При применении NiMgAl-катализаторов происходило более глубокое превращение фурфурола с образованием значительного количества (до 70 мас. %) ТГФС [119].
Рис. 22.
Зависимость количества поглощенного водорода от времени для образцов NiAl (a) и Ni-MgAl (б). Условия реакции: 5.0 см3 фурфурола, 100 мл воды, навеска катализатора 0.5 г, температура 90°С, давление 2.0 МПа [119], адаптировано из <[119] doi.org/10.1063/5.0032858>. <By courtesy of AIP Publishing>.
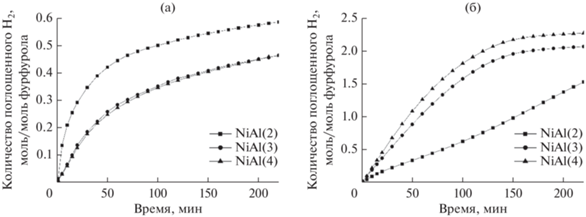
В процессах аквафазного гидрирования фурфурола были исследованы и Co-содержащие катализаторы, синтезированные из CoAl-СДГ (Co/Al = 4), полученного двухстадийным (вариант II) механохимическим методом (в сравнении с приготовленными соосаждением) [125, 126]. Механохимический синтез выполняли с использованием гидроксидов металлов и карбоната натрия (АГО-2С, an = 1000 м с–2, t = 30 мин). Было установлено, что при одинаковом химическом составе CoAl-образцы, синтезированные механохимическим методом, были вдвое активнее, чем полученные соосаждением (конверсия фурфурола составляла 86 и 44 мас. % соответственно). Причиной установленных различий, как показали данные ПЭМ, являлась более высокая дисперсность частиц металлического кобальта, достигаемая при синтезе СДГ-предшественника катализатора механохимическим методом. Важной особенностью всех изученных кобальтовых систем была их высокая селективность (выше 98%) образования фурфурилового спирта (в отличие от никелевых, для которых характерно более глубокое протекание реакции).
ИСПОЛЬЗОВАНИЕ МЕХАНОХИМИЧЕСКОЙ ОБРАБОТКИ ДЛЯ ВВЕДЕНИЯ БЛАГОРОДНОГО МЕТАЛЛА ПРИ СИНТЕЗЕ НАНЕСЕННЫХ КАТАЛИЗАТОРОВ
При традиционных подходах введение активного металла в состав катализатора предполагает применение растворов соединений предшественников с последующими стадиями газо- или жидкофазного восстановления его ионных форм. При использовании СДГ в качестве носителя (предшественника носителя) была показана возможность интеркалирования анионных хлоридных комплексов платины (палладия) в процессе анионного обмена, регидратации смешанных оксидов или на стадии взаимодействия продукта мехактивации с водными растворами соединений активного металла [22, 99, 127, 128]. Однако в [129] было обнаружено, что добавление непосредственно в реакционную смесь AgNO3 (как предшественника частиц металлического серебра, формирующихся при последующем восстановлении находящихся в структуре СДГ катионов Ag+) уже в процессе механохимического синтеза ZnAl-СДГ, без введения какого либо восстановителя, но, возможно, из-за воздействия света, приводило к образованию на поверхности этого СДГ частиц металлического серебра. В развитие этого эффекта было предложено добавлять в реакционную смесь не соединение металла, а порошок металла. Так, в [130] был выполнен синтез Ag/ZnAl-СДГ посредством механической активации элементного серебра и исходных компонентов для получения СДГ, в качестве которых использовали Zn4CO3(OH)6·H2O и Al(OH)3 (Zn/Al = 2, планетарная мельница Pulverisette-7, шары из диоксида циркония, 600 об. мин–1, 2 ч). После стадии мехактивации проводили старение смеси в дистиллированной воде при интенсивном перемешивании в течение 4 ч и вакуумную сушку образца при комнатной температуре. Содержание серебра в синтезированныхх данным методом катализаторах варьировали в диапазоне 1–5 мас. %. В результате механохимически индуцированного взаимодействия между элементарным серебром и СДГ были приготовлены катализаторы, обладающие повышенной фотокаталитической активностью в отношении деградации красителя метилового оранжевого [130]. В тех же условиях синтеза авторы получили Pt/ZnAl-СДГ [131], добавляя в планетарную мельницу вместе с исходными для синтеза СДГ компонентами порошок металлической платины. Содержание платины варьировали в диапазоне 0.5–1.5 мас. %. Дифрактограммы всех образцов содержали набор пиков, типичный для СДГ, а также рефлексы при 39.76°, 46.25° и 67.45°, характерные для ГЦК-решетки металлической платины, причем интенсивность данных рефлексов возрастала при увеличении содержания металла. Синтезированные гибридные катализаторы Pt/ZnAl-СДГ продемонстрировали высокую фотокаталитическую способность в видимом свете в разложении загрязнителя ципрофлоксацина.
Вследствие больших ионных радиусов катионов Pt2+ (0.085 нм) или Ag+ (0.113 нм) они не могут встроиться в структуру СДГ посредством изоморфного обмена с Zn2+ (0.083 нм) или Al3+ (0.057 нм). С использованием методов СЭМ и РФА было установлено, что присутствие этих металлов в виде частиц на поверхности кристаллитов СДГ не оказывало существенного влияния на морфологию и структуру ZnAl-СДГ. В то же время наблюдалось взаимодействие металл–носитель, отражающееся (согласно данным РФЭС) в переносе заряда между Pt (или Ag) и СДГ c увеличением электронной плотности на металле. Анализ данных электронной микроскопии и карт распределения элементов в композитах Pt(Ag)/ZnAl-СДГ показал высокую дисперсность и однородное распределение наночастиц платины и серебра [130, 131], что очень важно для обеспечения необходимой поверхностной концентрации и однородности активных центров М/СДГ-катализаторов.
ЗАКЛЮЧЕНИЕ
В представленном обзоре приведены результаты исследований, связанных с применением экологически чистого, отвечающего направлению “зеленой химии” механохимического метода для синтеза востребованных соединений – слоистых двойных гидроксидов. Показано, что структура и чистота получаемого продукта определяются целым рядом условий и, в зависимости от выбора этих условий, могут целенаправленно варьироваться. Результат синтеза зависит не только от элементного и фазового состава исходных соединений, но и выбранной последовательности стадий процесса, условий осуществления механического воздействия, протекания стадий диффузии и кристаллизации.
В целом, любая схема проведения механохимического синтеза включает два процесса – активацию и диффузию. При механической активации в результате сильного удара шаров по частицам исходных соединений в них возникают искажения кристаллической решетки и дислокации, происходит увеличение внутренней и поверхностной энергии, рост площади реагирующей поверхности. Эффективность этой стадии зависит от параметров механического воздействия, а также от химических свойств обрабатываемых соединений и морфологии их кристаллов. Так как скорость процесса диффузии атомов (ионов) реагирующих компонентов в твердой фазе медленнее, чем процесса активации (пластической деформации), она является определяющей в синтезе СДГ, что особенно важно при получении гетероатомных СДГ. Несмотря на близкие структурные параметры, СДГ, приготовленные механохимическим методом, отличаются морфологией поверхности, а оксиды на их основе характеризуются меньшим средним размером пор и их большей однородностью. В рамках двухстадийной схемы механохимического синтеза вторая стадия (при различных приемах ее реализации) благоприятна для введения органических и неорганических анионов в состав СДГ.
Повышение энергоэффективности и экологичности механохимическего синтеза, наряду с возможностью уменьшения загрязнения продуктов механической активации (что достигается, например, посредством проведения футеровки мельничных барабанов) делают данный метод весьма привлекательным и зачастую конкурентоспособным в сравнении с жидкофазными. Это одна из причин увеличения количества исследований, связанных с механохимическим синтезом СДГ различного состава, и содержащих информацию о роли химического состава исходных соединений и условий проведения каждой стадии синтеза. Однако сфера применения СДГ, полученных данным методом, до сих пор ограничена и, как правило, связана с адсорбционной очисткой воды от органических и неорганических соединений. В то же время, как показывают результаты выполненного обзорного исследования, специфические свойства СДГ, формирующиеся при механохимическом синтезе, зачастую обусловлены высокой химической активностью их поверхности, что является важным фактором для проявления ими необходимых свойств как катализаторов или как носителей для каталитически активных компонентов, и что в последнее время находит отражение в интенсификации фундаментальных и прикладных исследований в этой области (см., например, появившиеся в 2022 г. публикации по целенаправленному синтезу и изучению различных по составу СДГ как катализаторов [132–134]).
Список литературы
Sharma R., Arizaga G.C., Saini A.K., Shandilya P. // Sust. Mater. Technol. 2021. V. 29. P. 00319. https://doi.org/10.1016/j.susmat.2021.e00319
Zhang Y., Xu H., Lu S. // RSC Advances. 2021. V. 11. I. 39. P. 24254. https://doi.org/10.1039/d1ra03289e
Mittal J. // J. Env. Manag. 2021. V. 295. P. 113017. https://doi.org/10.1016/j.jenvman.2021.113017
Lee S.-B., Ko E.-H., Park J.Y., Oh J.-M. // Nanomaterials. 2021. V. 11. P. 1153. https://doi.org/10.3390/nano11051153
Jijoe P.S., Yashas S.R., Shivaraju H.P. // Env. Chem. Lett. 2021. V. 19. P. 2643. https://doi.org/10.1007/s10311-021-01200-3
Santamaria L., Vicente M.A., Korili S.A., Gil A. // J. Env. Chem. Eng. 2020. V. 8. P. 104577. https://doi.org/10.1016/j.jece.2020.104577
Chaillot D., Bennici S., Brendle J. // Env. Sci. Pollut. Res. 2021. V. 28. P. 24375. https://doi.org/10.1007/s11356-020-08498-6
Jochym P.T., Oles A.M., Parlinski K., Łazewski J., Piekarz P., Sterniket M. // J. Phys.: Condens. Matter. 2010. V. 22. P. 445403. https://doi.org/10.1088/0953-8984/22/44/445403
Yan K., Liu Y., Lu Y., Chaib J., Sunet L. // Catal. Sci. Technol. 2017. V. 7. P. 1622. https://doi.org/10.1039/C7CY00274B
Cavani F., Trifiro F., Vaccary A. // Catal. Today. 1991. V. 11. P. 173.
Tian R., Liang R., Wei M., Evans D.G., Duan X. // Struct. Bond. 2017. V. 172. P. 65.
Mishra G., Dash B., Pandey S. // Appl. Clay Sci. 2018. V. 153. P. 172. https://doi.org/10.1016/j.clay.2017.12.021
Theiss F.L., Ayoko G.A., Frost R.L. // J. Colloid Interface Sci. 2013. V. 402. P. 114. https://doi.org/10.1016/j.jcis.2013.03.051
Gu P., Zhang S., Li X., Wang X., Wen T., Jehan R., Alsaedi A., Hayat T., Wang X. // Env. Pollut. 2018. V. 240. P. 493. https://doi.org/10.1016/j.envpol.2018.04.136
Theiss F.L., Couperthwaite S.J., Ayoko G.A., Frost R.L. // J. Colloid Interface Sci. 2014. V. 417. P. 356. https://doi.org/10.1016/j.jcis.2013.11.040
Rives V., Arco M., Martín C. // Appl. Clay Sci. 2014. V. 88–89. P. 239. https://doi.org/10.1016/j.clay.2013.12.002
Kuthati Y., Kankala R.K., Lee C. // Appl. Clay Sci. 2015. V. 112. P. 100. https://doi.org/10.1016/j.clay.2015.04.018
Bi X., Zhang H., Dou L. // Pharmaceutics. 2014. V. 6. № 2. P. 298.
Sun H., Heo Y.-J., Park J.-H., Rhee K.Y., Park S.-J. // Nanotechnol. Rev. 2020. V. 9. № 1. P. 1381. https://doi.org/10.1515/ntrev-2020-0102
Zhou D., Li P., Lin X., McKinley A., Kuang Y., Liu W., Lin W.-F., Sun X., Duan X. // Chem. Soc. Rev. 2021. V. 50. № 15. P. 8790. https://doi.org/10.1039/d1cs00186h
Ng S.-F., Lau M.Y.L., Ong W.-J. // Solar RRL. 2021. V. 5. № 6. P. 2000535. https://doi.org/10.1002/solr.202000535
Бельская О.Б., Степанова Л.Н., Леонтьева Н.Н., Казаков М.О., Гуляева Т.И., Черепанова С.В., Лавренов А.В., Лихолобов В.А. // Химия в интересах устойчивого развития. 2013. Т. 21. № 1. С. 37. (Belskaya O.B., Stepanova L.N., Leontyeva N.N., Kazakov M.O., Gulyaeva T.I., Cherepanova S.V., Lavrenov A.V., Likholobov V.A. // Chemistry for Sustainable Development. 2013. V. 21. № 1. P. 29.)
Бельская О.Б., Лихолобов В.А. // Российский химический журнал. 2018. Т. LXIII. № 1–2. С. 24. (Belskaya O.B., Likholobov V.A. // Russ. J. Gen. Chem. 2020. V. 90. № 3. P. 495. https://doi.org/10.1134/s107036322003026310.1134/s1070363220030263)https://doi.org/10.6060/rcj.2018621-2.3
Qu J., Sha L., Wu C., Zhang Q. // Nanomaterials. 2019. V. 9. P. 80. https://doi.org/10.3390/nano9010080
Mittal J. // J. Env. Manag. 2021. V. 295. P. 113017. https://doi.org/10.1016/j.jenvman.2021.113017
Daniel S., Thomas S. Layered double hydroxides: fundamentals to applications / Layered Double Hydroxide Polymer Nanocomposites, Eds. S. Thomas and S. Daniel. Woodhead Publishing Series in Composites Science and Engineering. Elsevier Science, 2020. P. 1. https://doi.org/10.1016/b978-0-08-101903-0.00001-5
McCormick P.G., Froes F.H. // JOM. 1998. V. 50. P. 61.
Tongamp W., Zhang Q., Saito F. // J. Mater. Sci. 2007. V. 42. P. 9210. https://doi.org/10.1007/s10853-007-1866-5
Tongamp W., Zhang Q., Saito F. // Powder Technol. 2008. V. 185. P. 43. https://doi.org/10.1016/j.powtec.2007.09.013
Isupov V.P., Chupakhina L.E., Mitrofanova R.P. // J. Mater. Synth. Process. 2000. V. 8. P. 251. https://doi.org/10.1023/A:1011376513081
Хуснутдинов В.Р., Исупов В.П. // Химия в интересах устойчив. развития. 2009. Т. 17. С. 439. (Khusnutdinov V.R., Isupov V.P. // Chem. Sustain. Dev. 2009. V. 17. № 4. P. 439.)
Qu J., He X., Wang B., Zhong L., Wan L., Li X., Song S., Zhang Q. // Appl. Clay Sci. 2016. V. 120. P. 24. https://doi.org/10.1016/j.clay.2015.11.017
Qu J., He X., Chen M., Huang P., Zhang Q., Liu X. // J. Solid State Chem. 2017. V. 250. P 1. https://doi.org/10.1016/j.jssc.2017.03.013
Ferencz Z., Szabados M., Ádok-Sipiczki M., Kukovecz Á., Kónya Z., Sipos P., Pálinkó I. // J. Mater. Sci. 2014. V. 49. P. 8478. https://doi.org/10.1007/s10853-014-8558-8
Qu J., Li X., Lei Z., Li Z., Chen M., Zhang Q. // J. Am. Ceram. Soc. 2016. V. 99. P. 1151. https://doi.org/10.1111/jace.14196
Qu J., He X., Chen M., Hu H., Zhang Q., Liu X. // Mater. Chem. Phys. 2017. V. 191. P. 173. https://doi.org/10.1016/j.matchemphys.2017.01.055
Conterosito E., Van Beek W., Palin L., Croce G., Perioli L., Viterbo D., Gatti G., Milanesio M. // Cryst. Growth Des. 2013. V. 13. P. 1162. https://doi.org/10.1021/cg301505e
Intasa-ard S., Imwiset K., Bureekaew S., Ogawa M. // Dalton Trans. 2018. V. 47. P. 2896. https://doi.org/10.1039/c7dt03736h
Xu C., De S., Balu A.M., Ojedad M., Luqueet R. // Chem. Commun. 2015. V. 51. P. 6698. https://doi.org/10.1039/C4CC09876E
Ay A.N., Zümreoglu-Karan B., Mafra L. // Zeitschrift fuer Anorganische und Allgemeine Chemie. 2009. V. 635. № 9–10. P. 1470. https://doi.org/10.1002/zaac.200801287
Zeng M., Huo X., Liu S., Li S., Li X. // Appl. Surf. Sci. 2014. V. 292. P. 1059. https://doi.org/10.1016/j.apsusc.2013.12.093
Zhang X., Li S. // Appl. Surf. Sci. 2013. V. 274. P. 158. https://doi.org/10.1016/j.apsusc.2013.03.003
Zhang X., Qi F., Li S., Wei S., Zhou J. // Appl. Surf. Sci. 2012. V. 259. P. 245. https://doi.org/10.1016/j.apsusc.2012.07.026
Болдырев В.В. // Успехи химии. 2006. Т. 75. № 3. С. 203. (Boldyrev V.V. // Russ. Chem. Rev. 2006. V. 75. P. 177. )https://doi.org/10.1070/RC2006v075n03ABEH001205
Ю.Г. Широков. Механохимия. Теоретические основы. Иваново, 2015. УДК 544.46.:001.8. 214 с.
Молчанов В.В., Буянов Р.А. // Успехи химии. 2000. Т. 69. № 5. С. 476. (Molchanov V.V., Buyanov R.A. // Russ. Chem. Rev. 2000. V. 69. P. 435. )https://doi.org/10.1070/RC2000v069n05ABEH000555
Qu J., Zhang Q., Li X., He X., Song S. // Appl. Clay Sci. 2016. V. 119. P. 185. https://doi.org/10.1016/j.clay.2015.10.018
Fahami A., Beall G.W. // Mater. Lett. 2016. V. 165. P. 192. https://doi.org/10.1016/j.matlet.2015.11.132
Fahami A., Beall G.W. // J. Solid State Chem. 2016. V. 233. P. 422. https://doi.org/10.1016/j.jssc.2015.11.006
Zhu R., Yan L., Song W., Ma Z., Jia R., Sun S. // Mater. Express. 2021. V. 11. № 4. P. 524. https://doi.org/10.1166/mex.2021.1951
Kuramoto K., Intasa-Ard S.G., Bureekaew S., Ogawa M. // J. Solid State Chem. 2017. V. 253. P. 147. https://doi.org/10.1016/j.jssc.2017.05.039
Szabados M., Konya Z., Kukovecz A., Sipos P., Palinko I. // J. Solid State Chem. 2019. V. 272. P. 227. https://doi.org/10.1016/j.jssc.2019.02.020
Szabados M., Varga G., Konya Z., Kukovecz A., Carlson S., Sipos P., Palinko I. // Ultrason. Sonochem. 2018. V. 40. Part A. P. 853. https://doi.org/10.1016/j.ultsonch.2017.08.041
Szabados M., Mészáros R., Erdei S., Kónya Z., Kukovecz Á., Sipos P., Pálinkó I. // Ultrason. Sonochem. 2016. V. 31. P. 409–416. https://doi.org/10.1016/j.ultsonch.2016.01.026
Szabados M., Bús C., Adok-Sipiczki M., Kónya Z., Kukovecz Á., Sipos P., Pálinkó I. // Particuology. 2016. V. 27. P. 29. https://doi.org/10.1016/j.partic.2016.01.006
Alex T.C., Kumar R., Roy S.K., Mehrotra S.P. // Powder Technol. 2014. V. 264. P. 105. https://doi.org/10.1016/j.powtec.2014.05.028
Szabados M., Ádám A. A., Kása Z., Baán K., Mucsi R., Sápi A., Kónya Z., Kukovecz Á., Sipos P. // Materials 2021. V. 14. P. 4880. https://doi.org/10.3390/ma14174880
Jensen N.D., Bjerring M., Nielsen U.G. // Solid State Nucl. Magn. Reson. 2016. V. 78. P. 9. https://doi.org/10.1016/j.ssnmr.2016.06.001
Jiang Y., Yang Z., Su Q., Chen L., Wu J., Meng J. // Materials. 2020. V. 13. № 22. P. 5223. https://doi.org/10.3390/ma13225223
Yu H.-B., Liu H.-R., Liu G.-L., Gao H. // Materials in Environmental Engineering, Proceedings of the Annual International Conference on Materials Science and Environmental Engineering, 4th, Chengdu, China, Dec. 16–18, 2016. 2017. P. 137. https://doi.org/10.1515/9783110516623-014
Labuschagné F.J.W.J., Wiid A., Venter H.P., Gevers B.R., Leuteritz A. // Green Chem. Lett. Rev. 2018. V. 11. P. 18. https://doi.org/10.1080/17518253.2018.1426791
Barnard B.A., Labuschagne F.J.W.J. // Crystals. 2020. V. 10. P. 954. https://doi.org/10.3390/cryst10100954
Barnard B.A., Labuschagné F.J.W.J. // Crystals. 2021. V. 11. № 3. P. 276. https://doi.org/10.3390/cryst11030276
Stepanova L.N., Kobzar E.O., Leont’eva N.N., Gulyaeva T.I., Vasilevich A.V., Babenko A.V., Serkova A.N., Salanov A.N., Belskaya O.B. // J. Alloys Compd. 2021. V. 890. P. 161902. https://doi.org/10.1016/j.jallcom.2021.161902
He J., Wei M., Li B., Kang Y., Evans D.G., Duan X. // Struct. Bond. 2006. V. 119. P. 89.
Зырянов В.В. // Успехи химии. 2008. Т. 77. № 2. С. 107. (Zyryanov V.V. // Russ. Chem. Rev. 2008. V. 77. № 2. P. 105. )https://doi.org/10.1070/RC2008v077n02ABEH003709
Iwasaki T., Shimizu K., Nakamura H., Watano S. // Mater. Lett. 2012. V. 68. P. 406.
Iwasaki T., Yoshii H., Nakamura H., Watano S. // Appl. Clay Sci. 2012. V. 58. P. 120. https://doi.org/10.1016/j.clay.2012.01.024
Степанова Л.Н., Бельская О.Б., Василевич А.В., Леонтьева Н.Н., Бакланова О.Н., Лихолобов В.А. // Кинетика и катализ. 2018. Т. 59. № 4. С. 506. [Для англ. версии. Stepanova L.N., Belskaya O.B., Vasilevich A.V., Leont’eva N.N., Baklanova O.N., Likholobov V.A. // Kinetics and Catalysis. 2018. V. 59. № 4. P. 521. DOI 10.1134/S0023158418040134]https://doi.org/10.1134/S0453881118040135
Stepanova L.N., Belskaya O.B., Vasilevich A.V., Leont’eva N.N., Salanov A.N., Likholobov V.A. // AIP Conference Proceedings. 2019. V. 2141. P. 020013-020013-6. https://doi.org/10.1063/1.5122032
Stepanova L.N., Kobzar E.O., Leont’eva N.N., Gulyaeva T.I., Vasilevich A.V., Babenko A.V., Serkova A.N., Salanov A.N., Belskaya O.B. // J. Alloys Compd. 2021. V. 890. P. 161902. https://doi.org/10.1016/j.jallcom.2021.161902
Коваль Л.М., Гойворонская Ю.И., Потуданская М.Н., Боженкова Г.С., Паукштис Е.А. // Кинетика и катализ. 2009. Т. 83. № 5. С. 856.
Stepanova L.N., Belskaya O.B., Vasilevich A.V., Gulyaeva T.I., Leont’eva N.N., Serkova A.N., Salanov A.N., Likholobov V.A. // Catal. Today. 2020. № 357. P. 638. https://doi.org/10.1016/j.cattod.2019.04.069
Cherepanova S.V., Leontʹeva N.N., Arbuzov A.B., Drozdov V.A., Belskaya O.B., Antonicheva N.V. // J. Solid State Chem. 2015. V. 225. P. 417. https://doi.org/10.1016/j.jssc.2015.01.022
Chisem C., Jones W. // J. Mater. Chem. 1994. V. 4. P. 1737.
Besserguenev A.V., Fogg A.M., Francis R.J., Price S.J., O’Hare D., Isupov V.P., Tolochko B.P. // Chem. Mater. 1997. V. 9. P. 241.
Kozlova S.G., Gabuda S.P., Isupov V.P., Chupakhina L.E. // J. Struct. Chem. 2003. V. 44. № 2. P. 198.
Shumaker J.L., Crofcheck C., Tackett S.A., Santillan-Jimenez E., Morgan T., Ji Y., Crocker M., Toops TJ. // Appl. Catal. B: Env. 2008. V. 82. № 1–2. P. 120. https://doi.org/10.1016/j.apcatb.2008.01.010
Britto S., Kamath P.V. // Inorg. Chem. 2011. V. 50. P. 5619.
Kameda T., Shinmyou T., Yoshioka T. // Mater. Chem. Phys. 2016. V. 177. P. 8. https://doi.org/10.1016/j.matchemphys.2016.04.015
Cai J., Zhao X., Zhang Y., Zhang Q., Pan B. // J. Colloid Interface Sci. 2018. V. 509. P. 353. https://doi.org/10.1016/j.jcis.2017.09.038
Liu Y.T., Wang M.K., Chen T.Y., Chiang P.N., Huang P.M., Lee J.F. // Env. Sci. Technol. 2006. V. 40. № 24. P. 7784. https://doi.org/10.1021/es061530j
Isupov V.P., Chupakhina L.E., Tarasov K.A., Shestakova N.Y. // Chem. Sust. Dev. 2007. V. 15. P. 63.
Wang C.J., O’Hare D. // J. Mater. Chem. 2012. V. 22. P. 23064.
Liu Y.T., Chen T.Y., Wang M.K., Huang P.M., Chiang P.N., Lee J.F. // Appl. Clay Sci. 2010. V. 48. P. 485. https://doi.org/10.1016/j.clay.2010.02.011
Li H., Guan X., Yang L., Liu S., Zhang J., Guo Y. // J. Wuhan Univ. Technol. Mat. Sci. Edit. 2017. V. 32. № 5. P. 1101. https://doi.org/10.1007/s11595-017-1717-4
Bunekar N., Tsai T.-Y., Yu Y.-Z. // Mater Today Proc. 2016. V. 3. P. 1415.
Wei J., Gao Z., Song Y., Yang W., Wang J., Li Z., Mann T., Zhang M., Liu L. // Mater. Chem. Phys. 2013. V. 139. P. 395. https://doi.org/10.1016/j.matchemphys.2012.12.005
Zhou J., Cheng Y., Yu J., Liu G. // J. Mater. Chem. 2011. V. 21. P. 19353.
Kang H., Leoni M., He H., Huang G., Yang X. // Eur. J. Inorg. Chem. 2012 V. 24. P. 3859. https://doi.org/10.1002/ejic.201200174
Wang S.-L., Lin C.-H., Yan Y.-Y., Wang M.K. // Appl. Clay Sci. 2013. V. 72. P. 191.
Zhang Y., Liu J., Li Y., Yu M., Li S., Xue B. // J. Coat. Technol. Res. 2015. V. 12. P. 595.
Zhang F., Hou W. // Solid State Sci. 2018. V. 79. P. 93. https://doi.org/10.1016/j.solidstatesciences.2018.03.007
Menzheres L.T., Kotsupalo N.P., Mamylova E.V. // J. Mater. Synth. Process. 1999. V. 7. P. 239.
Belskaya O.B., Baklanova O.N., Leont’eva N.N., Gulyaeva T.I., Likholobov V.A. // Procedia Engineering. 2015. V. 113. P. 91. https://doi.org/10.1016/j.proeng.2015.07.298
Stepanova L.N., Belskaya O.B., Baklanova O.N., Vasilevich A.V., Likholobov V.A. // Procedia Engineering. 2016. V. 152. P. 672. https://doi.org/10.1016/j.proeng.2016.07.672
Belskaya O.B., Leont’eva N.N., Gulyaeva T.I., Cherepanova S.V., Talzi V.P., Drozdov V.A., Likholobov V.A. // Russ. Chem. Bull. 2013. V. 62. P. 2349.
Stepanova L.N., Mironenko R.M., Belskaya O.B., Likholobov V.A. // Catal. Sustain. Energy. 2017. V. 4. P. 8. https://doi.org/10.1515/cse-2017-0003
Stepanova L.N., Kobzar E.O., Leont’eva N.N., Belskaya O.B. // AIP Conference Proceedings. 2020. № 2301. P. 02003-1–02003-6. https://doi.org/10.1063/5.0032741
Nam S.S., Kim H.K., Ishan G., Choiane M.J., Lee K.W. // Appl. Catal. A: Gen. 1999. V. 179. P. 155. https://doi.org/10.1016/S0926-860X(98)00322-6
Di Cosimo J.I., D’ıez V.K., Xu MIglesia E., Apestegu’ıa C.R. // J. Catal. 1998. V. 178. P. 499. https://doi.org/10.1006/jcat.1998.2161
Fakhfakh N., Cognet P., Cabassud M., Lucchese Y., Días de Los Ríos M. // Chem. Eng. Process. 2008. V. 47. P. 349.
Bessonov I.V., Kopitsyna M.N., Nelyub V.A. // Russ. J. Gen. Chem. 2014. V. 84. P. 2439.
Faba L., Díaz E., Ordóñez S. // ChemSusChem. 2014. V. 7. P. 2816.
Chimni S.S., Mahajan D. // Tetrahedron. 2005. V. 61. P. 5019.
Fernandez-Lopez R., Kofoed J., Machuqueiro M., Darbre T. // Eur. J. Org. Chem. 2005. P. 5268.
Zhang Y., Wang M.G., Liang J., Shang Z.C. // Lett. Org. Chem. 2010. V. 7. P. 27.
Wang B., Liu X., Liu L., Chang W., Li J. // Eur. J. Org. Chem. 2010. P. 5951.
Zhou S., Liu L., Wang B., Ma M., Xu F., Sun R. // Synth. Commun. 2012. V. 42. P. 1384.
Müller T., Djanashvili K., Arends I.W.C.E., Peters J.A., Hanefeld U. // Chem. Commun. 2013. V. 49. P. 361.
Hora L., Kikhtyanin O., Čapek L., Bortnovskiy O., Kubička D. // Catal. Today. 2015. V. 241. P. 221.
Sels B.F., De Vos D.E., Jacobs P.A. // Catal. Rev. 2001. V. 43. P. 443.
Li C., Wei M., Evans D.G., Duan X. // Catal. Today. 2015. V. 247. P. 163. https://doi.org/10.1016/j.cattod.2014.05.032
Long X., Wang Z., Xiao S., An Y., Yang S. // Mater. Today. 2016. V. 19. P. 213. https://doi.org/10.1016/j.mattod.2015.10.006
Zhang F., Du N., Li H., Liang X., Hou W. // RSC Adv. 2014. V. 4. P. 46823. https://doi.org/10.1039/c4ra07553f
Du W., Zheng L., Li X., Fu J., Lu X., Hou Z. // Appl. Clay Sci. 2016. V. 123. P. 166. https://doi.org/10.1016/j.clay.2016.01.032
Jia C., Zhang X., Li S. // Chin. J. Chem. 2012. V. 30. P. 277. https://doi.org/10.1002/cjoc.201180476
Teodorescu F., Slabu A.I., Pavel O.D., Zăvoianu R. // Catal. Commun. 2020. V. 133. P. 105829. https://doi.org/10.1016/j.catcom.2019.105829
Kobzar E.O., Stepanova L.N., Leont’eva N.N., Belskaya O.B. // AIP Conference Proceedings. 2020. № 2301. P. 030010-1. https://doi.org/10.1063/5.0032858
Sulmonetti T.P., Pang S.H., Claure M.T., Lee S., Cullen D.A., Agrawal P.K., Jones C.W. // Appl. Catal. A: Gen. 2016. V. 517. P. 187.
Meng X., Yang Y., Chen L., Xu M., Zhang X., Wei M. // ACS Catal. 2019. V. 9. P. 4226.
Stepanova L.N., Belskaya O.B., Leont’eva N.N., Kobzar E.O., Salanov A.N., Gulyaeva T.I., Trenikhin M.V., Likholobov V.A. // Mater. Chem. Phys. 2021. № 263. P. 124091. https://doi.org/10.1016/j.matchemphys.2020.124091
Смирнов А.А., Шилов И.Н., Алексеева М.В., Селищева С.А., Яковлев В.А. / // Катализ в промышленности. 2017. Т. 17. № 6. С. 517. https://doi.org/ (Smirnov A.A., Shilov I.N., Alekseeva M.V., Selishcheva S.A., Yakovlev V.A. // Kataliz v promyshlennosti. 2017. V. 17. № 6. P. 517. https://doi.org/10.1134/s207005041803009110.1134/s2070050418030091)https://doi.org/10.18412/1816-0387-2017-6-517-526
Meng X., Yang Y., Chen L., Xu M., Zhang X., Wei M. // ACS Catal. 2019. V. 9. P. 4226. https://doi.org/10.1021/acscatal.9b00238
Кобзарь Е.О., Степанова Л.Н., Бельская О.Б. // IV Российский конгресс по катализу: Сборник тезисов докладов. 20–25 сентября 2021 г., Казань, Россия, 2021. С. 467. ISBN978-5-906376-37-4.
Kobzar E.O., Stepanova L.N., Vasilevich A.V., Belskaya O.B. // Catalyst Design: From Molecular to Industrial Level: abstracts of 6th International School-Conference on Catalysis for Young Scientists, May 16–19, 2021, Novosibirsk, Russia, 2021. C. 43. ISBN9785906376336.
Бельская О.Б., Гуляева Т.И., Леонтьева Н.Н., Зайковский В.И., Ларина Т.В., Киреева Т.В., Доронин В.П., Лихолобов В.А. // Кинетика и катализ. 2011. Т. 52. № 6. С. 899. (Belskaya O.B., Gulyaeva T.I., Leont’eva N.N., Zaikovskii V.I., Larina T.V., Kireeva T.V., Doronin V.P., Likholobov V.A. // Kinet. Catal. 2011. V. 52. № 6. P. 876. )https://doi.org/10.1134/S0023158411060036
Belskaya O.B., Zaikovskii V.I., Gulyaeva T.I., Talsi V.P., Trubina S.V., Kvashnina K.O., Nizovskii A.I., Kalinkin A.V., Bukhtiyarov V.I., Likholobov V.A. // J. Catal. 2020. V. 392. P. 108. https://doi.org/10.1016/j.jcat.2020.09.021
Baláž M., Daneu N., Bala’žová L., Dutková E., Tka’čiková L’., Briančin J., Vargová M., Bala’žová M., Zorkovská A, Baláž P. // Adv. Powder Technol. 2017. V. 28. № 12. P. 3307. https://doi.org/10.1016/j.apt.2017.09
Li Z., Zhang Q., Liu X., Wu L., Hu H., Zhao Y. // J. Mater. Sci. 2018. V. 53. № 18. P. 12795.
Li Z., Chen M., Hu H., Zhang Q., Tao D. // J. Solid State Chem. 2020. V. 290. P. 121594. https://doi.org/10.1016/j.jssc.2020.121594
Rahman A., Pullabhotla R.V.S. // Bull. Chem. React. Eng. Catal. 2022. V. 17. № 1. P. 163. https://doi.org/10.9767/bcrec.17.1.12195.163-193
Zăvoianu R., Cruceanu A., Pavel O.D., Bradu C., Florea M., Bîrjega R. // Catalysts. 2022. V. 12. № 2. P. 145. https://doi.org/10.3390/catal12020145
Seliverstov E.S., Golovin S.N., Lebedeva O.E. // Front. Chem. Eng. 2022. V. 4. article 86761509. https://doi.org/10.3389/fceng.2022.867615
Дополнительные материалы отсутствуют.
Инструменты
Кинетика и катализ